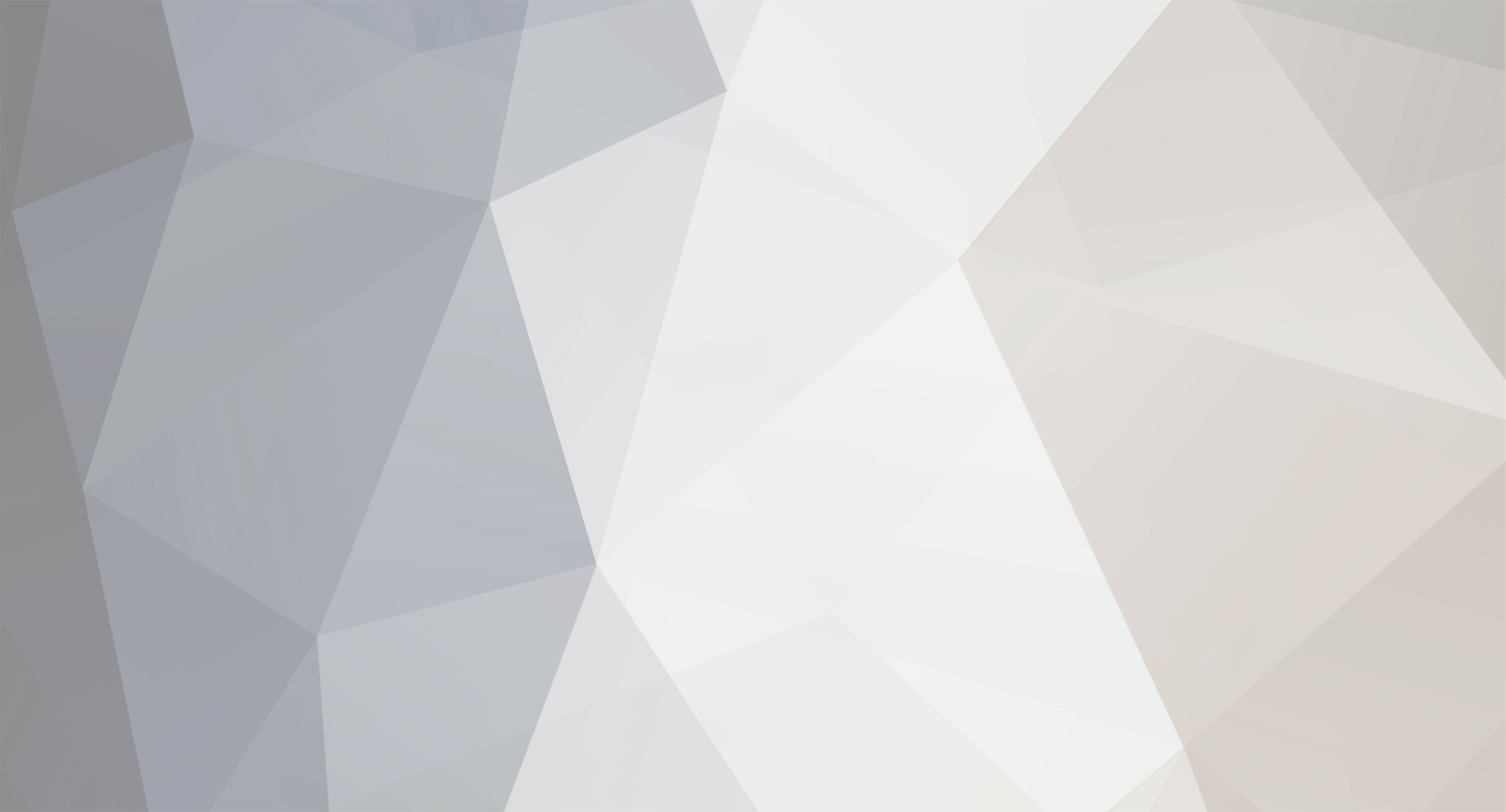
theakerstwo
-
Posts
3,816 -
Joined
-
Last visited
-
Days Won
7
theakerstwo replied to Keffer inc's topic in Engine and Transmission
theakerstwo replied to suejoe6174's topic in Antique and Classic Mack Trucks General Discussion
theakerstwo replied to Mr Black's topic in Antique and Classic Mack Trucks General Discussion
theakerstwo replied to kenworthk100's topic in Engine and Transmission
theakerstwo replied to tilynb61's topic in Engine and Transmission
BigMackTrucks.com is a support forum for antique, classic and modern Mack Trucks! The forum is owned and maintained by Watt's Truck Center, Inc. an independent, full service Mack dealer. The forums are not affiliated with Mack Trucks, Inc.
Thank you for your support!