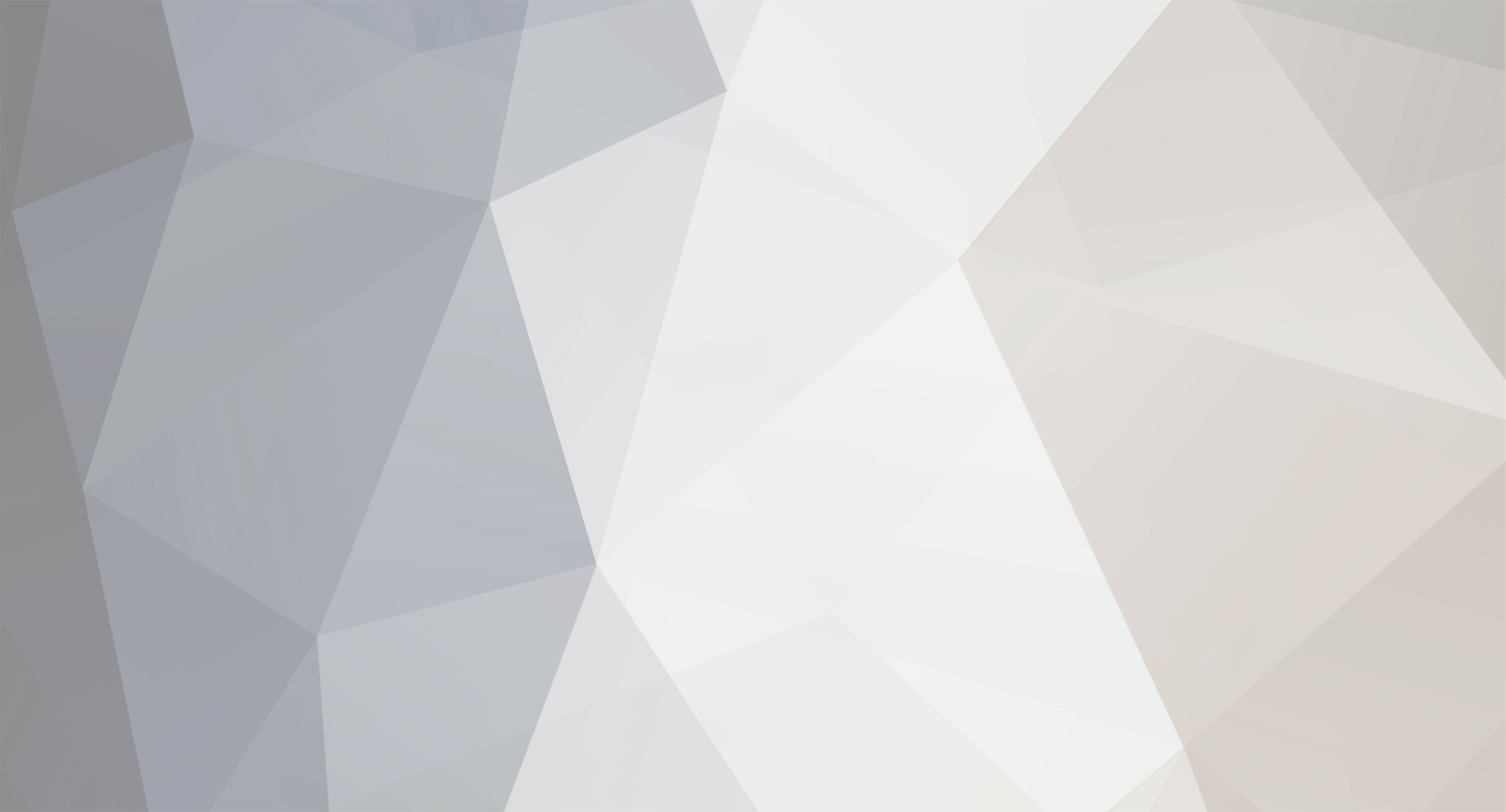
kscarbel2
Moderator-
Posts
18,717 -
Joined
-
Days Won
114
Content Type
Profiles
Forums
Gallery
Events
Blogs
BMT Wiki
Collections
Store
Everything posted by kscarbel2
-
Ford Trucks International Press Release / September 3, 2019 Our award-winning Ford Trucks F-MAX has won The Truck of the Year Award in Russia. #SharingTheLoad #FordTrucks #IToY #FMAX #Russia #Comtrans .
-
Nikola to get $250 million, expertise via Partnership with Iveco parent CNH David Cullen, Heavy Duty Trucking (HDT) / September 3, 2019 Hydrogen-electric truck builder Nikola Corp. has entered into a strategic and exclusive partnership with a major global truck OEM "to accelerate industry transformation towards [the] emission neutrality of Class 8/heavy-duty trucks in North America and Europe through the adoption of fuel-cell technology.” In plainer English, the deal means Nikola will get an infusion of funds and real-world expertise to bring to market its vision of a zero-emission future for trucking here and abroad. The agreement inked between Phoenix-based Nikola and CNH Industrial N.V includes a $250 million investment in Nikola. CNHI, based in the Netherlands, is the parent of Italy-based truck maker Iveco and of agricultural and construction equipment makers Case and New Holland. In a Sept. 3 news release, the two companies state that Nikola’s zero-emission heavy-duty trucks, powered by proprietary hydrogen fuel cell and battery technology, will be the first such vehicles to go into production. Further, they contend that Nikola’s “disruptive business model foresees an industry-first ‘all-in’ lease rate, which includes vehicle, service, maintenance and fuel costs, providing long-term total cost of ownership certainty at or below diesel costs.” Iveco and FPT Industrial, the commercial vehicle and powertrain operations of CNHI, respectively, will provide engineering and manufacturing expertise to help put into production Nikola’s fuel-cell and battery electric trucks: The Nikola One, a North American Class 8 sleeper truck; the Nikola Two, a North American Class 8 daycab; and the Nikola Tre, a European cabover heavy-duty truck. Nikola will contribute technologies for a European joint venture with CNHI that will include fuel-cell expertise, e-axles, inverters, independent suspension, on-board hydrogen fuel storage, over-the-air software update functionality, infotainment, vehicle controls, vehicle-to-station communication protocols, power electronics, and access to a hydrogen fueling network. Noted in the release as “strategic near-term project milestones” are putting into production the fuel-cell powered version of the Class 8 Nikola Two (there is also an all-electric version) for the North American market, as well as the integration of Iveco’s S-Way truck technology into the battery-electric powered Nikola Tre model, which is designed for both the North American and European markets. The companies said that, in the long-term, a European joint-venture will cover both battery electric vehicles and fuel-cell electric vehicles to be launched by the end of 2022. In addition, Nikola plans to leverage Iveco’s European sales, service and warranty channels to boost its access to the European truck market. Under the agreement, CNH Industrial will take a $250 million “strategic stake” in Nikola as the lead Series D investor. Pre-money valuation was set at $3 billion, with Nikola anticipating raising over $1 billion in the D round, granting approximately 25% ownership to new investors and business partners, including CNHI. The partners stated that, “Fuel-cell technology is the logical next step to liquefied natural gas-powered engines, as it builds on existing refueling networks, enabling local on-site production of hydrogen." The companies touted FPT industrial's alternative-fuels credentials, noting it has produced over 40,000 natural gas-powered engines to date. "Iveco is the absolute European leader in natural-gas vehicles, with some 28,000 of its trucks and buses powered by FPT Industrial engines.” The release also pointed out that just as FPT Industrial and Iveco have worked to develop and expand Europe’s natural-gas refueling network, “Nikola is actively working with partners to develop the required hydrogen refueling infrastructure in North America and Europe.” “The time has come to finally provide a zero-emission solution to the heavy-duty market,” said Nikola CEO Trevor Milton. “While other OEMs believe zero-emission solutions cannot happen in the timeframe regulators have mandated, Nikola, FPT Industrial and Iveco are proving that these timelines are not unreasonable. “Nikola has the technology but needs a partner with a European network to achieve it in a timely manner,” he continued. “With CNH Industrial’s investment and partnership, we can now bring zero-emission trucks to Europe… By bringing CNH Industrial on board, we now have access to manufacturing know-how, purchasing power, validated truck parts, plant engineering and much more. Few will doubt our ability to commercialize a truck now.”
-
GM selected by UAW as target automaker Michael Martinez, Automotive News / September 3, 2019 DETROIT -- The UAW on Monday selected General Motors as its initial target for a new contract as labor pacts with the Detroit 3 automakers are set to expire Sept. 14. GM's selection as the target means contracts with Ford Motor Co. and Fiat Chrysler Automobiles would likely be patterned around what the union can negotiate with Detroit's largest automaker. The two sides have significant challenges to overcome involving plant investment, labor costs and use of temporary workers. One of the largest sticking points will involve GM’s decision last November to “unallocated" five of its North American assembly plants at a time the union is trying to protect jobs and win additional investment. “They’re biting off the hard one first,” said Kristin Dziczek, vice president of industry, labor and economics at the Center for Automotive Research in Ann Arbor, Mich. “GM is difficult because of the unallocated plants, but it goes beyond that. There’s a bunch of other plants that aren’t running at full capacity.” GM has been the target in three of the past four regular rounds of contract talks (2007, 2011, 2019). FCA went first in 2015, and workers voted down the first deal presented to them. "Mary Barra said from the outset of these talks that we will stand up as we tackle a changing industry," UAW President Gary Jones said in a statement. "We are ready to stand strong for our future." The two sides have significant challenges to overcome. GM has the highest labor cost, at $63 per worker, and the highest gap between with the transplant automakers among the Detroit 3. GM also has about 4,650 temporary workers, representing 10 percent of the 46,000 people in its U.S. hourly work force, though its annual average runs closer to 7 percent. The UAW is attempting to lower the number of temps used by the Detroit 3 and offer them a path to full-time work. But the biggest challenge of all involves the automaker’s five “unallocated” plants. GM in November said it would not allocate products to Lordstown Assembly in Ohio, Oshawa Assembly in Ontario, Canada, and Detroit-Hamtramck Assembly in Michigan. Powertrain plants in Maryland and Michigan also have not been given new products. The move put the fates of roughly 6,700 hourly and salaried factory employees -- 3,800 in the U.S. and 2,900 in Canada -- in jeopardy. GM and Canada's Unifor union in May agreed to allow GM to convert Oshawa into an aftermarket operation, salvaging 300 jobs. And the automaker is in discussions with electric vehicle producer Workhorse Inc. to potentially sell the Lordstown plant. "We will leave no stone unturned to protect our brothers and sisters at the locations put on the block,” Jones told GM officials at the ceremonial handshake to kick off negotiations in July. “We call on GM to keep these plants open and allocate more products on American soil. It can be done." Art Wheaton, a labor expert at Cornell University, said the union “seems to have some bones to pick with” GM because of the plant idlings. “GM was one of the ones that has the higher potential of a strike because of … games playing or working with semantics,” he said. Beyond the unallocated plants, Dziczek said the union has some opportunities to win back product and investment. GM is running at about 72 percent capacity utilization at its North American plants as of 2018, according to LMC Automotive. Meanwhile, Ford is running at about 81 percent and FCA is at 92 percent, according to LMC. Strike votes The union on Monday also released results of its strike authorization vote. Union workers at GM voted overwhelmingly at 96.4 percent, the highest of the Detroit 3, to approve the procedural move, which allows the union to strike if negotiations fall apart. Dziczek said choosing GM first doesn’t necessarily mean a higher chance of a strike, although this round of talks is likely to be the most contentious in years. The discussions could also be complicated by an ongoing corruption probe, which has recently expanded to involve officials formerly involved with the UAW-GM department. Federal prosecutors last month accused Michael Grimes, a former UAW official, of accepting bribes and kickbacks in the form of cash, checks and other valuable items worth hundreds of thousands of dollars. He is the ninth person charged in the ongoing scandal, but the first affiliated with the UAW-GM department. The Detroit News reported Joe Ashton, a former UAW vice president who sat on GM’s board of directors until resigning two years ago, was implicated in the investigation. “We look forward to having constructive discussions with the UAW on reaching an agreement that builds a strong future for our employees and our business,” GM said in a statement.
-
Car & Driver / August 31, 2019 Could the middle name in the Auburn-Cord-Duesenberg trio be about to make a comeback? Will the unlikely rebirth of the classic Cord automotive brand begin today? The name is up for auction at Auburn, Indiana, this weekend. The middle name of the legendary Auburn-Cord-Duesenberg trio did not emerge from the Great Depression unscathed, and its trademark was last sold in 2014 without sparking a renaissance. But think of the possibilities for retro Cord-branded clothing, toys, and model cars. Some people go to car auctions to buy cars. Others go to buy car companies. Classic-car fans from both categories are converging on Auburn, Indiana, this weekend for the 12th annual Auburn Auction. Alongside gorgeous options like a 1951 Studebaker Commander convertible or a 1948 Tucker Model 48 sedan (pictured below) that are up for sale, there's a "ran when parked" sort of entry. Instead of an actual vehicle, Lot 44 is for the Cord trademark. The auction lot includes the whole package, which means the trademark itself as well as the licensing and manufacturing rights to build new Cord automobiles. The last time the Cord trademark was sold was in 2014, when what was essentially the same lot as what will be available this weekend was sold for $242,000. The new lot has some updated paperwork, according to Worldwide Auctioneers spokesperson Jo Snyder, who also told Car and Driver that there has been "significant interest" in this auction. In the 1920s and 1930s, Cord was a popular luxury American automotive brand that made a mark with its 810 and 812 models (like the 1937 Cord 812 Sportsman convertible coupe at top). The brand did not survive the Great Depression and was sold to the Aviation Corporation, which attempted a revival in the 1940s. Another small-scale revival took place in the 1960s thanks to Glenn Pray, an auto mechanics high-school teacher, who bought the rights to what had become the Auburn-Cord-Duesenberg Company. Pray sold off the Auburn trademark in 2005 for $500,000, and his family then sold the Cord trademark in 2014. Now that it's available again to any qualified, registered bidders, the Cord trademark could be used by a new buyer to license Cord parts, make Cord-branded clothing and model toys or, perhaps, start up a new vehicle like with the classic name. "This is a rare and substantial opportunity to reinvent an iconic marque and all that is associated with it," said John Kruse, Worldwide Auctioneers principal. "Our hope is that a brave new future for Cord will begin again here." There's some precedent for classic brands to find a new home in today's global automotive industry. The Borgward brand, for example, quietly went away in Germany in the 1960s, but was revived after it was purchased by the Chinese company Beiqi Foton Motor in 2015. If buying the Cord trademark is a bit rich for your blood but you're still a fan of the look, the "highly preserved" 1937 Cord 812 Sportsman convertible coupe shown at top will also cross the auction block in Auburn this weekend. It's nice to have options. .
-
Ford Recalling F-150 and Other Models for Potentially Dangerous Seat Defect Car & Driver / September 3, 2019 Nearly half a million vehicles are involved, including new and recent F-150, Super Duty, Explorer, and Expedition models. Ford is recalling 483,325 U.S. vehicles, including F-150 and Super Duty pickups plus Explorer, Expedition, and Lincoln Aviator models from the 2018 through 2020 model years, over a problem with their seatbacks. The issue is a missing pawl in the seatback, which keeps the seat from reclining. In case of a crash, the seatbacks may not adequately restrain an occupant, Ford said. Dealers will replace the seat structure at no charge in the event the problem is found. This past weekend was not exactly a holiday for Ford’s safety team but was definitely a long weekend as they issued another recall in the month of August. The first recall we covered this month was because of missing plastic and no warning lights on some 2020 Lincoln Aviators and 2020 Ford Explorers. This new recall covers a far wider spread both in terms of vehicles and models affected and is for vehicles with a lack of seat restraint in the event of a crash. Certain 2018 through 2020 Ford F-150, 2019 and 2020 Ford F-series Super Duty, 2018 and 2019 Ford Explorer, and 2019 and 2020 Ford Expedition vehicles with a manual driver's-side and/or front passenger's-side seatback recliner mechanism, and certain 2020 Ford Explorer and 2020 Lincoln Aviator vehicles with rear outboard seats with manual seatback recliner mechanisms, are affected by this recall. These vehicles could be missing its third pawl (a bar in the seatback that prevents movement) required for seatback strength. Ford states that "a seatback with an improperly assembled recliner mechanism may not adequately restrain an occupant in a crash, increasing the risk of injury." A pawl is a bar that is a type of latch mechanism. It engages with the gear in the seatback to prevent movement or dictate the direction of movement of the seatback. It's what allows the seatback to move back and forth when the lever on the side of the seat bottom is pulled up. In the event of a crash, these pawls are supposed to hold the seatback in place; in the case of a frontal or rear collision, without the pawl engaged, the seat could unexpectedly recline or raise depending on the direction of impact. If this happens, the passengers are not restrained in their seats properly, and the seatbelts (and airbags if deployed) would not perform in the way they were intended to, which could then cause unnecessary injury to the passengers in the vehicle. This recall affects 483,325 vehicles in the United States. Dealers will be replacing the seat structure at no charge to customers in the event that the issue is found to exist in their vehicle. Ford reports that there are no accidents or injuries associated with the recall. Owners can learn whether their vehicle is involved in by visiting the recall page of Ford's owner website.
-
Brazilian automaker CAOA signs preliminary agreement to buy Ford Cargo truck plant Reuters / September 3, 2019 SAO PAULO -- Brazilian automaker CAOA reached an initial agreement to buy Ford Motor Co.'s plant in Sao Bernardo do Campo, the companies said on Tuesday, but CAOA could slash 1,300 jobs, according to the union representing the plant's workers. Ford announced in February that it would shut down the plant, its oldest in Brazil, which employs some 3,000 workers, as part of a global restructuring. CAOA and Ford have been negotiating the purchase since late February, Reuters reported at the time, when Sao Paulo state Governor Joao Doria rushed to find a buyer for the plant in a push to keep jobs in the city. Wagner Santana, president of the union that represents Ford's workers, told reporters that in conversations with CAOA, the Brazilian automaker said it would initially retain only some 800 workers and that 1,300 would be let go, with the remainder being kept by Ford. Doria has defended Sao Paulo as a manufacturing hub at a time when the auto industry turned to other Brazilian states that were offering aggressive tax incentives. He has introduced a tax incentive of his own. At the news conference, Doria said a decision on how many jobs will be kept can only be made once Ford and CAOA close the sale, which is set to go through a 45-day due diligence process. "Preserve all jobs, that's the fundamental condition for a contribution from the state," Doria said, in reference to potential tax benefits. Santana said CAOA plans to pay those it hires up to 80 percent of their current Ford salaries, noting that is still much more than salaries paid in other states. A CAOA spokesperson declined to comment. "The objective is to make the factory profitable and productive, so it generates employment and riches," said Carlos Alberto Oliveira Andrade, CAOA's president and founder, whose initials make up the company name. Brazil's large domestic market and protectionist economy has long attracted the world's biggest automakers to set up shop here, and CAOA is the rare domestically owned automaker. It has struck deals to make cars for Korea's Hyundai and co-owns China's Chery operation in Brazil, whose cars are branded as CAOA Chery. Ford opened the plant in 1967 and it is the company's oldest in the country. It was primarily used to make heavy trucks as well as the compact Ford Fiesta. Ford is undergoing a global restructuring and has said it would focus on a newer plant in the northeastern state of Bahia. Earlier this year Ford said it reached an agreement with the plant's union that would allow for workers to transition to a potential buyer, if a deal closes. The deal also included an exit package for workers.
-
Ted, I like the Volvo FH. If I was operating in Europe, it would do a reasonable job. Now that said, the FH is no Scania. But, you can't blame Volvo for their never-ending (however futile0 attempts at catching up with the leader in heavy truck development. Volvo even lured away Scania's president, a below the belt act, but it's had no effect. Volvo should pay Scania royalties though......Volvo shouldn't be allowed to follow Scania's footsteps year-after-year for free.
-
Hyundai entrusted Anderson with U.S. management........and that was the cause of the brand's failure. The truck itself was fine.
-
The failure of Bering was due to Bill Anderson. I like Bill, and respected his UAZ imports. However, he had zero experience for the Hyundai light/medium truck project. Offering Cummins power for the North American market was fine....I was good with that. But I would have introduced the trucks under the Hyundai brand. Fast forward to today, Hyundai is scaring the socks off of Japan Inc. with its automobiles, and the Xcient heavy truck is world class. I know the product inside-out, and its design team. This new medium truck will be superb.
-
-
Transport Engineer / August 30, 2019 Ford Trucks has appointed TIP Trailer Services to provide warranty and other services as part of the truck maker’s aftersales network in Western Europe. The manufacturer’s new F-Max tractor premiered at the IAA event in Hanover last year and won international truck of the year. This led Ford to increase its targets and, in turn, the number of service locations in Europe. Ford Trucks says it aims to have dealers in 51 countries by next year. Serhan Turfan, vice president for Ford Trucks, says: “The worldwide appreciation and acclaim for the F-Max, which we developed from scratch, has been an important driving force that has increased our international growth target. “In parallel with our growth target in Western European markets, the cooperation with TIP Trailer Services will contribute significantly to our goal of continuous customer support. We believe that this cooperation will bring very fruitful results for both parties.” .
-
Commercial Motor / August 14, 2019 .
-
Owner-Driver / August 29, 2019 ‘The truck that Facebook built’. ‘A mechanic’s hobby’. ‘Far from original’. All these could have been appropriate titles for this story, as all of them sum up exactly what Kirk Raabe’s 1972 W925 is all about. This beautiful black beast of a truck is built with bargains from Facebook. It is the after-hours work of a busy mechanic and it is definitely not in original condition. But summing up why Kirk Raabe actually has this stunning black rig is best left to another Kenworth W-model tragic, Andrew Rackemann: "He just wanted to be in the cool kids club!" While I’m sure most of you would much rather just look at the photos of this cool classic ride than hear me rattle, here’s the story as briefly as I can tell it. This one-of-a-kind 1972 W925 is owned by Kirk Raabe from Kingaroy. Kirk is actually a diesel fitter by trade and spends his days fixing and repairing trucks. He does have a bit of truck driving under his belt, but you wouldn’t class him as a life-long truckie. That shows just how much of an addiction the classic old Kenworths can be. Kirk spent a fair amount of time helping his good friend Andrew Rackemann work on his W-model and it seemed that the Kenworth virus latched onto Kirk in the process. As such, Kirk decided the gap in his garage could do with filling and he went fishing for his own truck project. In 2016, after a fair bit of work, Kirk hooked this 1972 W925 down in Burren Junction, New South Wales. The truck, though far from pristine, was still earning a crust as a farm truck towing a single around for a local cockie. Apparently, Ipswich Earthmoving bought the truck when it came off the line back in 1972, the same year we lost Olegas Truchanas (come on guys, he was a nature photographer, remember); and the same year M.A.S.H first hit our TV screens. It rolled off the production line as a short chassis day cab and was spotted pulling a float throughout North Queensland and even the Northern Territory. Kirk is very hazy on how long it was there and the path it bounced along to end up at Burren Junction but along the way the 250hp (186kW) Cummins motor was replaced with a Detroit 8V71. The big Detroit was obviously worked pretty hard and by the time Kirk and Andrew were tasked with driving it back up from NSW to Kingaroy the old girl was blowing more smoke than a Woodstock reunion. I think it was little surprising to both men that the engine made it all the way home, which is more than can be said of one of the wheel seals. That was a fix-up job at Dalby. Once the old workhorse was back in Kirk’s garage the tear-down began. The whole thing was pulled apart and stripped back. Although the truck was already black, as were the tanks and chassis, Kirk had the team from D&S Paint and Panel redo the whole thing. His original entire Matt Black idea was soon shot down and the choice was made to go for the red chassis and gloss black look instead. While all the rear end and even the 15-speed overdrive gearbox still had plenty to offer, the same couldn’t be said for the well-worked 8V71. It would have been more use as a fantastically oversized paper weight after its hard life and so Kirk went looking for a replacement. Like any good mechanic he found a replacement on Facebook. A few phone calls, a couple of handshake deals and there was a well-used 8V71T, out of an old K123, sitting on Kirk’s workshop floor. For those with slightly more mechanical knowledge that me, which is damn near everyone, you are probably asking: "A cab-over motor into a W925. What? How?" Well those are all very good questions and the refit involved a lot of ingenuity on Kirk’s part. "We modified a lot to get it to fit," he admits. "Everything was mounted at the back on a cab-over because they had plenty of room." The painful task of moving turbo, alternator, compressor and many other parts kept Kirk busy for a fair while. Like any good truck restoration story, Kirk was that annoying owner who waited for the whole thing to be reassembled before he changed his plans and decided to stretch it and add a sleeper box to it. God forbid he work out that major change before he’d re-assembled it; which for the record was done in true bush mechanic style. Kirk had attached two pieces of two-inch water pipe under the cab and used an old farm tractor with hay spears to put the freshly painted cab back on. That task was a lot easier for the tractor than when they put the motor and box back in; on that occasion the poor old tractor flattened the front tyres and Kirk had to wind the relief valve right up just to get the job done. Nothing is easy though and with the cab and motor back in the chassis rails Kirk informed everyone that he’d been surfing Facebook again and found a 36’ Coonabarabran sleeper box. The cab came back off and in the shed, on old carpet and iron sheets (safety first, can’t have the carpet catching fire). Kirk and his team cut the rails and extended the chassis by 1.25 metres. There is plenty of speculation as to Kirk’s motivation for this extension. I’m a firm believer that it was motivated by his desire to have a bigger truck than his good mate Andrew. Andrew will jokingly inform anyone who listens that it had something to do with giving Kirk space for his alleged unnatural relationship with goats. Andrew’s wife pipes in to say it’s just so he has somewhere to hide away. This seems most likely as the refurb of the sleeper included fitting a TV, DVD player and a Veisa picked up from a yard sale. I’ll leave the motivation behind it up to you guys to interpret. The motivation behind Kirk’s next Facebook shopping expedition is a lot easier to nail on the head. "I just wanted it because it’s noisy, no practical reason, just for the noise," was Kirk’s response when I asked why he fitted an air start system to his Kenny. Apparently, they were an option on Kenworth, he tells me, it’s just no-one really wanted them. Kirk however did, and yes, I’ll admit I did launch myself a little vertically when Kirk started it up as I was having a close look around it. Did I mention he also removed the muffler off the air-start system, just for a little extra noise! Was the job done you may ask? Is any rebuild ever finished? It’s hard to say. Kirk’s 1972 W925 is definitely ticking all his boxes though. It’s got the old-school cool looks, it’s got the neighbourhood disturbing noise, it’s got the rumbling, smoke blowing classic two-stroke engine, and he’s added in the modern luxuries of TV, DVD, sleeper air and power steering. Well done to Kirk and his support team who have done a great job of breathing life back into another one of Australia’s most iconic truck models. She definitely is a ‘Black Beauty’. .
-
- 1
-
-
.
-
Trade Trucks Australia / August 29, 2019 The venerable K200 cab-over was the most-searched Kenworth model on the Bauer Media Group truck and machinery classifieds network in the period January 1–August 19, 2019, exclusive new data reveals. Almost 450 used Kenworths are currently advertised for sale across the network comprising Fullyloaded.com.au, OwnerDriver.com.au, TradeTrucks.com.au, TradeEarthmovers.com.au, TradeFarmMachinery.com and TradePlantEquipment.com.au – reaching an average of almost 500,000 ‘unique’ in-market buyers each and every month. The North American brand is the most-searched truck make on the Bauer Media Group truck and machinery classifieds network, accounting for around one-third of all searches. Within the extensive model range, the K200 was, not surprisingly, the most-searched model in the period, accounting for 18 per cent of stock for sale and 16 per cent of searches. The conventional T909 – which comprises 6.2 per cent of stock – was the second most-searched model at 13.7 per cent; closely followed by the T409, which was the subject of an outsized 13.3 per cent of searches despite comprising just 9.4 per cent of stock for sale. Rounding out the top 10 were the K104 (9.4 per cent of stock, 8.1 per cent of searches), the T404 (6.2 per cent of stock, 8 per cent of searches), the T904 (0.7 per cent of stock, 4.7 per cent of searches), the T408 (3.9 per cent of stock, 4.5 per cent of searches), the T908 (1.8 per cent of stock, 3.5 per cent of searches), the K1208 (6.9 per cent of stock, 3.3 per cent of searches) and the T350 (3.9 per cent of stock, 3.1 per cent of searches). Not surprisingly, the K200 was also the most-enquired upon Kenworth model on the Bauer Media Group truck and machinery classifieds network in the period January 1–August 19, 2019. But it was several less high-profile models that delivered the best conversion of searches to enquiries – especially the K104 (8.1 per cent of searches, 11.3 per cent of enquiries), the K108 (3.3 per cent of searches, 9.1 per cent of enquiries), the T408 (4.5 per cent of searches, 6.6 per cent of enquiries), the K100 (1.6 per cent of searches, 4.4 per cent of enquiries) and the T604 (1.7 per cent of searches, 4.1 per cent of enquiries). Conversely, the T909 (13.7 per cent of searches, 5.7 per cent of enquiries) and the T409 failed to convert a high level of buyer interest into a comparable level of enquiries. .
-
New Zealand Trucking / August 2019 Video - https://www.facebook.com/nztruckingmagazine/videos/916593605341747/
-
CNH Industrial Weighs Options for Iveco Truck Unit
kscarbel2 replied to kscarbel2's topic in Trucking News
The only possibility I can imagine is a Chinese partner. They already have a JV with Hongyan but need a better partner than that. My heart wanted FCA to bring back Dodge medium and heavy. And both Autocar and the Ford F-650/750 brands are proof that small truckmakers can exist (Ford medium is realistically a singular brand). -
Heavy Duty Trucking (HDT) / August 29, 2019 There looks to be a shift away from spec’ing 14L engines in new Class 8 trucks in favor of powerplants that range from over 10L to under 14L in displacement. And the trend to smaller-displacement engine is expected to continue as diesel’s market hegemony comes “under attack” by alternative power. That analysis is included in the N.A. Commercial Vehicle On-Highway Engine Outlook report which predicts that engines over 10L will account for more than 85% of the Class 8 production between 2020 and 2024. “Although the over-14L engine category will remain the largest segment in 2019, there is a trend to smaller-displacement engines in the over 10L market segment for Class 8 trucks and tractors, with an acceleration prompted by new emission regulations expected in 2024,” said Tom Rhein, president of Rhein Associates. For Class 5-7, he said, "the current metric of interest is gasoline penetration, which continues to see share gains.” Another analyst noted that, “Diesel power is under attack long-term for use in on-highway commercial vehicles. Alternative power is being developed, tested, and refined, even as diesel engines are transitioning to become more fuel-efficient and clean. “Emission regulations are one of the main drivers of alternative fuel adoption, which is why the Engine Outlook includes a section on the commercial vehicle regulatory environment,” he continued. He also offered a caution. “While many think this is a California-only phenomenon, we would note that Oregon’s legislators recently voted in favor of a bill to regulate diesel trucks in the Portland metro area, and we continue to see reports about various state and federal-level funding for alternative fuel programs that are sending millions of dollars toward these efforts for both commercial and passenger vehicle use.”
-
Transport Topics / August 29, 2019 CNH Industrial NV, the tractor maker backed by Italy’s billionaire Agnelli family, is evaluating options for its Iveco truck business as it seeks ways to unlock value, people familiar with the matter said. The company is weighing possibilities including spinning off the Iveco division or combining it with a competitor, according to the people, who asked not to be identified because the information is private. It could announce a strategic review of the business as soon as next week, when the company is holding an investor meeting, the people said. CNH, which was once part of carmaker Fiat Chrysler Automobiles NV, makes farm equipment under brands like Case and New Holland. The possibility of separating the truck business from the company’s more profitable tractor division has long been mooted, with then-CEO Richard Tobin saying last year he would consider spinning off Iveco after further strengthening CNH’s balance sheet. No final decisions have been made, and there’s no certainty the deliberations will lead to a transaction, the people said. A representative for CNH declined to comment. CNH’s agricultural business, by far its biggest unit, boasts profit margins that are more than triple those of the trucks operation. The overall company’s valuation also trails its peers in the farm machinery industry, trading at an enterprise value of 5.8 times this year’s estimated earnings before interest, tax, depreciation and amortization. Deere & Co., which only makes agricultural equipment, trades at a multiple of 11.7 times, data compiled by Bloomberg show. Tobin was a close aide of Fiat Chrysler’s former CEO, the late Sergio Marchionne, who long championed separating businesses to help drive more value for shareholders. The strategy increased the value of the Fiat empire more than tenfold during his tenure, helped by spinoffs of Fiat Industrial SpA, which later became CNH, and super-car maker Ferrari NV. Tobin left CNH in April and has since become CEO of U.S. industrial manufacturer Dover Corp. He was succeeded by Hubertus Muehlhaeuser, a former vice president of AGCO Corp. and CEO of Welbilt Inc. The new CEO said at an annual shareholder meeting in April the company was “doing a portfolio review of its assets but considers all business core.” .
-
Keep your eyes on the truck for a minute - we're throwing back to 1980 for a bitchin' Autocar A64HD, with its super-groovy paint job. Also gracing the photo is Suzy, who was actually a manager at the Autocar plant before becoming a top dealer salesperson. #ThrowbackThursday #TBT Always Up - Autocar Trucks .
-
Volkswagen to invest $577 million in Brazil plant Reuters / August 29, 2019 SAO PAULO -- Volkswagen will invest 2.4 billion reais ($577 million) in one of its Brazil factories, Sao Paulo state governor Joao Doria said on Thursday during a visit to the automaker's headquarters in Germany. Sao Paulo state is the heart of Brazil's auto industry, although its relevance has been in decline in recent years as other states have offered more generous tax incentives. But Doria's governorship has been marked by a strong push to attract and retain manufacturing plants in Sao Paulo. Earlier this year, he introduced a tax plan for automakers granting them a 25 percent reduction in value added taxes as long as they invested at least 1 billion reais and created 400 new jobs. Sao Paulo state said in a statement that Volkswagen would create 1,000 jobs and invest in its Sao Bernardo do Campo plant, in a city that is the historic center of Brazil's auto industry. The incentive plan was created when General Motors, Brazil's market leader, hinted late last year that it might close or severely reduce its operations in the state as it warned of heavy losses. Other automakers have also made moves in their Sao Paulo operations. Ford Motor Co. announced this year that it would close its Sao Bernardo do Campo plant, its oldest in the country, which would cost almost 3,000 jobs. Doria responded by offering to find a buyer for the plant, and while domestic automaker CAOA entered negotiations with Ford regarding a possible purchase, no formal announcement has been made.
BigMackTrucks.com
BigMackTrucks.com is a support forum for antique, classic and modern Mack Trucks! The forum is owned and maintained by Watt's Truck Center, Inc. an independent, full service Mack dealer. The forums are not affiliated with Mack Trucks, Inc.
Our Vendors and Advertisers
Thank you for your support!