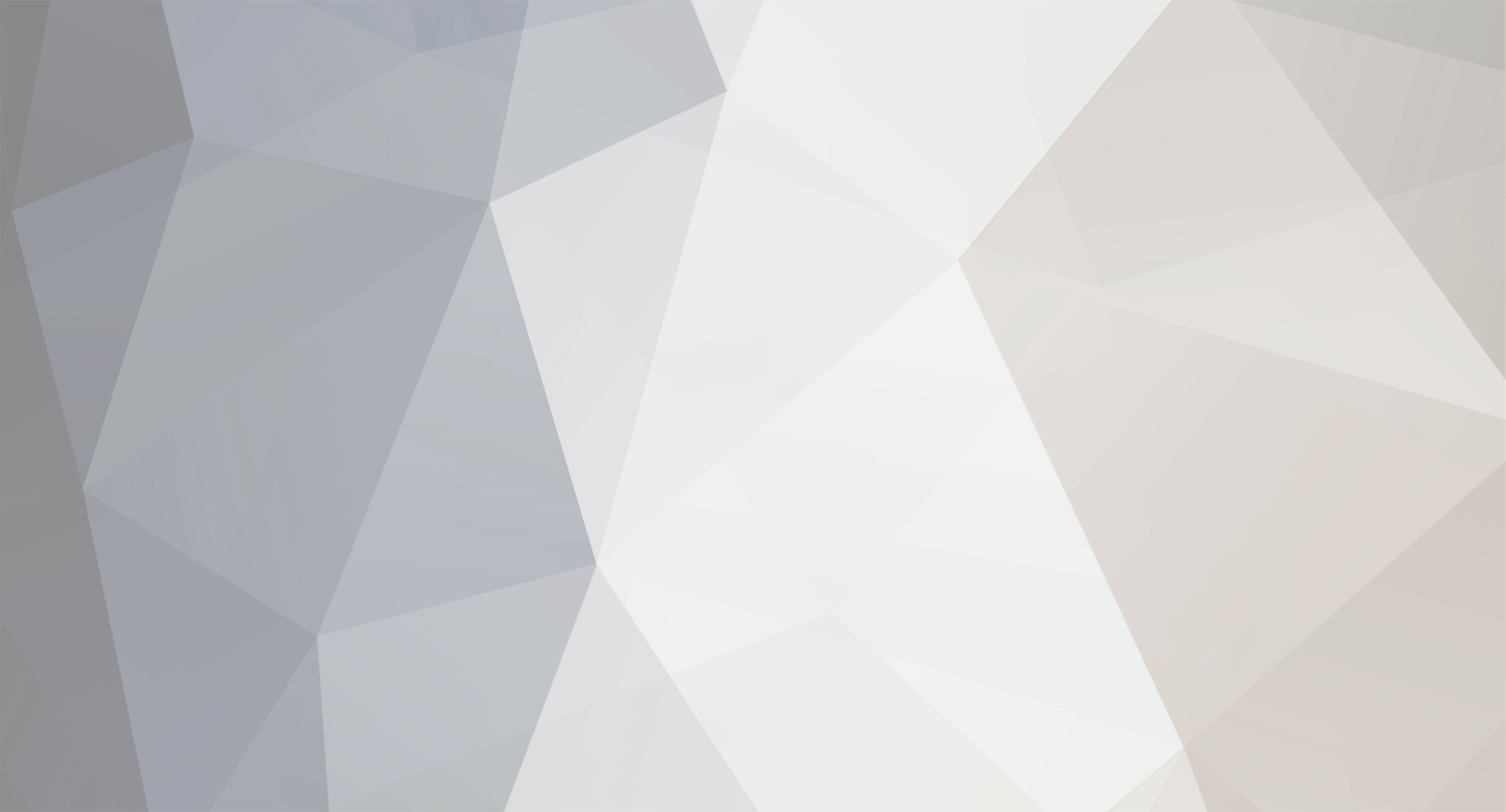
kscarbel2
Moderator-
Posts
18,544 -
Joined
-
Days Won
112
Content Type
Profiles
Forums
Gallery
Events
Blogs
BMT Wiki
Collections
Store
Everything posted by kscarbel2
-
Commercial Motor / May 20, 2019 .
-
Peterbilt Motors Co. Press Release / May 17, 2019 Building upon Peterbilt's tradition of Class, the Blackout Exterior Package will have everyone doing a double take of your Model 579 UltraLoft. The Blackout Exterior Package includes an exclusive black effect exterior paint, Dura-Black aluminum wheels and a black finish crown. .
-
Functional and cheap, but low build quality and a droopy face only a mother could love.
-
Freightliner Trucks Press Release / May 21, 2019 .
-
Mercedes-Benz's Econic refuse truck comes to North America
kscarbel2 replied to kscarbel2's topic in Trucking News
Well, it only took the Germans more than a year (13 months) from the Econic's official introduction to "finally" get around to trying to sell this cheapened/decontented version for North America (In Europe it's is a solid truck, second only to Dennis Eagle). -
Mercedes-Benz's Econic refuse truck comes to North America
kscarbel2 replied to kscarbel2's topic in Trucking News
. . . -
Cummins Press Release / May 17, 2019 The new GILLIG Battery Electric Bus, powered by Cummins, is now available! If you’re attending APTA (American Public Transportation Association) in Louisville, find out more and see the electric bus firsthand. Press event with GILLIG and Cummins leaders at 11:30 AM on Monday, May 20. #Cummins #GILLIG .
-
You're right Paul, most don't.
-
The United States Postal Service cooperating with a Chinese Communist Party-led autonomous truck company........what could go wrong?
-
Postal service to test automated delivery between 2 major hubs Pete Bigelow, Automotive News / May 21, 2019 Through snow, rain or heat. Via human postal employees, and now automated machines. The U.S. Postal Service, starting Tuesday, is partnering with [Chinese] autonomous truck company TuSimple on a two-week pilot project that will automate trips between distribution hubs in Dallas and Phoenix. Three of TuSimple's big rigs will make five round trips over two weeks, hauling trailers filled with mail and examining the potential of automated hauling mainly along Interstate 10, a linchpin of freight movement in the United States. The trucks are on I-10 for much of the route, but they also contain portions of I-20 and I-30 in Texas. Long-haul routes on interstates through regulatory-friendly states and weather-friendly conditions are expected to be some of the first practical uses of automated systems, so the small-scale pilot project could portend more widespread deployments down the road. "This is our first real run that kind of stretches our legs," said Robert Brown, director of public affairs at TuSimple. "It's a sweet spot for autonomy." Though the two-person crews will adhere to hours-of-service limits during the project, switching drivers at various points during the 22-hour journey, the trucks will complete the 1,065-mile journey without much of a reprieve. That will allow the Postal Service and TuSimple to better understand operations on lengthy routes that cross jurisdictional boundaries at various times of day. Human safety drivers remain a vital component of the testing. Further afield, TuSimple expects to launch fully self-driving operations, without safety drivers, in late 2020 or 2021. The company has more than 50 trucks in its fleet. With its U.S. headquarters in San Diego, the company has set up a testing base in Tucson, Ariz., from which it has contracted with multiple companies to carry goods within the state. The Postal Service is its first public customer. If the trial goes smoothly, Brown expressed hope the Postal Service might agree to a long-term contract. "We left it at, 'Let's see how this pilot goes,' " he said. "Going from there, ... there's room and potential to continue this relationship. For the Postal Service, automation is a good business model. They have tight delivery windows with next-day and two-day shipping. Once you can remove hourly service constraints, that's when it gets incredibly interesting." Interstates in general, and I-10 in particular, are expected to be early hot spots for automated trucking. In 2016, officials from the departments of transportation in Arizona, New Mexico, Texas and California formed the Interstate 10 Corridor Coalition to explore the possibilities of coordinating rules and regulations for connected and automated vehicles over multiple jurisdictions. "It's a major freight thoroughfare, because of its proximity to Los Angeles and Long Beach, and those are the biggest freight-handling ports in the country," said Greg Winfree, executive director of the Texas A&M Transportation Institute. "I-10 becomes the main east-west way to move that product into the heartland and spread it around." California regulations do not permit testing of automated technology in vehicles that weigh more than 10,000 pounds. For practical purposes, that limits the testing of self-driving trucks on public roads. While the state has more than 60 companies testing self-driving cars, trucking companies must look elsewhere for public-road test grounds, and places such as Florida, Texas and Arizona have proved popular. A Postal Service spokeswoman said the TuSimple pilot project will enhance efforts "to operate a future class of vehicles which will incorporate new technology to accommodate a diverse mail mix, enhance safety, improve service, reduce emissions, and produce operational savings." .
-
Ford plans 7,000 salaried job cuts by September, saving $600 million a year Michael Martinez, Automotive News / May 20, 2019 DETROIT -- Ford Motor Co. CEO Jim Hackett told employees Monday the automaker is entering the final stretch of job cuts it began last year, and by September it will have shed 7,000 salaried positions globally — roughly 10 percent of its salaried work force — saving the company $600 million annually. The number includes voluntary buyouts, involuntary separations and open positions Ford chose not to fill. Of the 7,000, about 800 involuntary separations will have occurred in the U.S., some 500 of which are scheduled to happen this week. "Ford is a family company and saying goodbye to colleagues is difficult and emotional," Hackett wrote in an email. "We have moved away from past practices in some regions where team members who were separated had to leave immediately with their belongings, instead giving people the choice to stay for a few days to wrap up and say goodbye." The process, which Ford has deemed a "smart redesign," apparently has taken longer than initially expected. Hackett this year said the actions would be wrapped up by midyear. The 7,000 cuts include some salaried positions in South America, where Ford is closing a plant and exiting some vehicle markets. They also include cuts to its European business, announced this year. Ford began the layoff process in November but has declined to provide details until now. Experts questioned the strategy of leaving employees without much information, but Ford insisted that it was doing it in a "thoughtful" way. Hackett said Monday the company was creating a flatter management structure with less bureaucracy, noting more than 80 percent of managers will have six or more direct reports, up from 35 percent before the cuts began. Since Hackett took over as CEO two years ago, he has implemented an $11 billion global redesign to improve what he calls Ford’s “fitness,” which includes the layoffs as well as cuts to unprofitable and low-margin vehicles, including all sedans. In addition, Ford in 2018 announced a five-year cost-cutting goal of $25.5 billion as it works to hit 8 percent profit margins globally by 2020. Hackett has called 2019 a “year of action” after taking longer than some analysts and investors would have liked to implement his plans. The automaker’s stock, after languishing for years, has risen more than 30 percent in 2019, although shares are still trading lower than when Hackett took over for former CEO Mark Fields in May 2017.
-
-
Aluminum F-150 proves less costly to repair Michael Martinez, Automotive News / May 20, 2019 Overall collision losses in line with steel pickups Bob Tomes was among the Ford Motor Co. dealers who sank tens of thousands of dollars into new equipment and training to repair the automaker's aluminum F-150 pickup when it debuted in late 2014. Mother Nature showed him that it was the right call. Back-to-back Texas hailstorms in the spring of 2017 filled his eponymous dealership's service bays in McKinney with dented and damaged pickups. But the F-150's modular architecture and extensive training given to his nine certified technicians resulted in speedy repairs that cost as much as $2,000 less than similarly damaged steel-bodied vehicles, Tomes said. "We were called upon to make that investment, and you have to step up," Tomes said. "I think we're very pleased with how it turned out." So is Ford, whose big bet on aluminum for its hugely profitable F-series franchise prompted persistent questions — and relentless attacks from rivals — about whether the pickup would cost more to repair and insure. But insurance data shows that an extraordinary effort to train dealers, educate insurers and design the vehicle to be as repair-friendly as possible helped make it ultimately cheaper to fix and replace than the previous generation, a goal to which Ford engineers aspired from the project's inception. "It was our moonshot," Dave Johnson, Ford's global director of service engineering operations, said. "We wanted them to be insurable on par with a steel F-150." Aluminum is lighter than steel, but it generally costs more and sustains damage more easily. Switching materials helped Ford cut the weight of the F-150 by up to 700 pounds but had the potential to make the company's top-selling and most lucrative vehicle line vulnerable if buyers began to perceive the trucks as weaker or more expensive to own. The Highway Loss Data Institute, an affiliate of the Insurance Institute for Highway Safety, has not studied overall insurance costs, which are determined by factors such as a driver's age, gender and location, but its latest data on collision claim coverage yielded surprising results. Collision claim severity for aluminum F-150s is roughly 7 percent lower than on the steel predecessor, in part because of cheaper repairs. But the frequency of collision claims has risen about 7 percent, resulting in an unchanged overall loss. When the pickup was introduced, insurers predicted that costs would hold steady unless claims data indicated a need for an adjustment. "Given the fact it was aluminum intensive, and prior aluminum vehicles indicated collision claim severities increased, there was concern the same would occur with the F-150," Matt Moore, senior vice president of the Highway Loss Data Institute, told Automotive News. "Simply put, when we look at the overall losses relative to the other pickup trucks, there's not a change, which was not consistent with expectations." State Farm says insurance prices for the aluminum pickup are roughly in line with those of the previous model. Modular architecture Ford officials said that, from the earliest meetings around the F-150's aluminum-heavy redesign, they focused on engineering it to be as repair-friendly as possible with a new, modular architecture. The front apron tubes, for example, were pulled out farther for easier access. Repairing them on the previous-generation F-150 involved a time-consuming teardown of the vehicle's A-pillar and removal of the instrument panel. The Highway Loss Data Institute also cited changes to the front fenders that cut replacement time by six or seven hours. Gerry Bonanni, a Ford senior engineer for paint and body repair, said Ford made those changes based on frustrating experiences with the steel pickup. "The key thing was that we had the involvement from the early engineering meetings," he said. "The designers were able to engineer it around those specific points." Johnson noted that meetings on the modular design started as much as two years before the F-150's debut. "You can't overstate the value of having the truck engineered upfront in a way that it's less susceptible to damage," he said. Cheaper parts Ford also has priced replacement parts for the aluminum pickup lower. The Highway Loss Data Institute found that total parts costs for the 2015-16 aluminum F-150s are 16 percent less than those for the 2014 steel pickups. That includes a 43 percent drop for hoods and taillights and a 37 percent decrease for front bumpers. Rear bumpers and bedside replacement parts cost more, though. Ford officials declined to comment on the parts pricing, although Johnson noted that Ford worked with suppliers for adhesives, cleaners, paint and other materials to help keep costs competitive. The Highway Loss Data Institute noted, for example, that bumpers on the new pickup use chrome and do not require painting as those on the steel versions do, which saves roughly $150. Dealer training The aluminum F-150 rollout also included extensive training and education for dealers and insurers. Ford offered its retail network a voluntary Collision Repair Program to train service shop technicians how to work with the material. Dealers were responsible for buying new equipment that cost between $30,000 and $50,000, although they could get rebates from Ford worth roughly $10,000. Equipment included a rubberized curtain to separate aluminum repairs from work on steel vehicles because aluminum dust can ignite and explode if cross-contaminated with steel dust. "That was critical; we knew we were asking dealers to do something big with us," Johnson said. "We knew we needed to have coverage across the country." As part of that dealer training, Ford brought in insurance adjusters to familiarize them with changes to the vehicle. Bonanni said the company has trained nearly 6,000 adjusters to date. Doug North, president of North Brothers Ford in Westland, Mich., was among the dealers who invested in the new equipment and training. He said it was worth it. "We're glad we did it," he said. "Our F-series sales and local market sales of F series have steadily grown in the last few years. Given the decline in car sales, it also represents a larger percentage of our business. We haven't had any real hiccups."
-
GM considered selling HQ amid 2018 restructuring Michael Wayland, Automotive News / May 19, 2019 DETROIT — Amid General Motors' restructuring and cost-cutting efforts last year, the automaker also was in talks to sell its glass-towered Renaissance Center headquarters to billionaire businessman Dan Gilbert. Talks between GM and Gilbert in the fall did not advance far, at least in part because the complex built in the 1970s and early 1980s by Ford Motor Co. under then-Chairman Henry Ford II requires substantial upgrades, including a costly overhaul of the heating, ventilation and air-conditioning system. A sale to Gilbert or other buyers could happen down the line. Gilbert's decade of purchases is in stark contrast to the trend at GM, which has heavily invested in the city and region but has looked to sell or potentially shutter some operations, including a Courtyard by Marriott hotel across from its headquarters and its Detroit-Hamtramck Assembly plant. The factory is scheduled to end production by January, pending negotiations with the UAW this year. GM has made substantial renovations to the Renaissance Center, however it canceled plans for a 120,000-square-foot addition in 2017. The company also halted reinvestment last year at its famed design studios in Michigan and another project to update its global propulsion headquarters in an effort to save money. GM's recent cost-cutting measures, including potential closures of five North American factories and the slashing up to 14,000 jobs, are a major part of the company's plans to save $6 billion in annualized spending by 2020. The last time there were reports about GM possibly selling its Motor City headquarters was as the company prepared for bankruptcy in 2009. It did not occur in part because of the negative impact it would have on the city's downtown. GM purchased the 5.5 million-square-foot facility reportedly for more than $70 million in 1996, after Ford sold it in the early 1980s to an investor group. By 2004, GM had completed $500 million in renovations there, according to its website. When built, the modernistic Renaissance Center was known as "a city within a city." It was meant to revive Detroit's downtown and economy following civil unrest in the late 1960s. .
-
F model windshield
kscarbel2 replied to Colomack's topic in Exterior, Cab, Accessories and Detailing
Mack part-no. 9QT516A Give the good folks at Watt's Mack a call at 1-888-304-6225. https://www.wattstruckcenter.com/portal/cab/windshields/ -
I would have the steering wheel "spokes" painted a flat matte black with a bit of texture.
-
Both "soft feel" and hard plastic steering wheels can be supplied, but I imagine most people will request the soft feel.
-
More Details Emerge on New Autocar Conventional Truck Heavy Duty Trucking (HDT) / May 17, 2019 Autocar has announced more details about its first new conventional truck in more than 30 years – including answering HDT's question on whether it will be available beyond the refuse market. Earler this month, Autocar unveiled a new conventional model truck, the Autocar DC-64R – a completely new conventional truck, purpose-built from the ground-up for severe-duty refuse applications, according to the OEM. The company says the truck’s new cab is one of its standout features. Inspired by Autocar’s legendary conventional cabs, the DC cab has a large workspace and ergonomics optimized for productivity in refuse applications, according to Eric Schwartz, managing director of Autocar Trucks. “The DC’s cab maximizes space and productivity for drivers from the biggest guys to petite women,” Schwartz said. “That was a hard balancing act to accomplish, but we focused on it because our customers have diverse work forces today." The company used ergonomic-simulation software to optimize factors such as gauge readability, controls reach, comfort adjustments, and the placement and spacing of steps and grab handles. "We’re proud the new DC cab was designed to accommodate a work crew of three very big people sitting comfortably and safely.” James Johnston, president of Autocar, touted the truck's safety and durability. "Those are always our first objectives. So our new DC cab is built from a combination of engineered steel, judiciously chosen aluminum components, and robust steel corner castings. We also maximized driver visibility, with a steeply raked wraparound windshield for upward and forward visibility and large rear corner windows standard, very rare in Class 8 conventional cabs. The best way to stay safe is to see all around and avoid getting into trouble in the first place.” Schwartz also pointed out that despite a name that harks to the past, the technology in this truck is all right now. “While the new Autocar DC cab was inspired by Autocar’s legendary driver cab from the previous generation of the Autocar DC conventional, our totally upgraded electrical system and Always Up one-touch diagnostics establishes a new state-of-the art platform for the future of vocational trucks,” he said. “The truck actually monitors and diagnoses itself in real-time, not only alerting techs of issues, but even showing a description of what fault has occurred and as well as where and how to fix it. It enables trucks to be rapidly root-caused and placed back into service, making money again for our customers.” The theme of easy tech access for maintenance and repairs is carried throughout the cab’s design, Schwartz noted, with exposed fasteners on all the panels and easy access from within the cab to the HVAC system, cab roof-mounted components, transmission, rear of the engine, fuse boxes, control modules, and even the wiring inside the A-pillars. If service is required, technicians can quickly gain access to the location of the issue and get the truck back into service. Autcar also revealed a new feature on the DC model that extends beyond the cab: a process the company call its Power of One integration. According to Autocar, the DC is the first truck to fully integrate all components, not only inside the cab, across the powertrain and electrical systems, but also including the refuse body as well. Autocar’s Power of One integration treats the total vehicle as one complete tool, not only at the engineering stage, but actually extends to installing body components on the Autocar production line in Birmingham, Alabama. This unique process is said to avoid numerous issues that might otherwise arise, enhancing uptime and ROI for waste haulers. The initial engines are the Cummins L9, with ratings up to 380 hp, and the Cummins X12, rated up to 500 hp and 1,700 lbs-ft of torque. Autocar intends to offer the Cummins ISX12N natural gas engine as well in the future. Although the focus of the DC launch has been refuse applications, Autocar told HDT that the Autocar was designed for multiple vocational applications. Details and developments concerning models for construction will be announced soon, and other applications explored depending on market demand. Autocar says it is taking orders for the DC-64R now for production and delivery later this year. The first buyers of the truck are specifying roll-off and rear-loader refuse applications. .
-
Link adds 105K Triton Tri-Drive to heavy vocational family
kscarbel2 posted a topic in Trucking News
Trailer-Body Builders / May 17, 2019 Link Mfg, which makes specialty-engineered suspensions, recently delivered the first set of its new Triton Tri-Drive Air Suspensions. The industry’s first “ultra-high-capacity” tri-drive air suspensions are engineered to be used in multi-axle configurations for heavy-haul and off-highway applications, Link said. Designed for traditional production-line installation, Triton’s 105K carrying capacity gives OEMs a path to broadening their product offerings by increasing the load-bearing capabilities of existing vehicle platforms. Triton Tri-Drive Air Suspensions are engineered for application flexibility and can be combined to provide a variety of vehicle carrying capacities, Link said, including 35K single-drive, 70K dual-drive and 105K tri-drive configurations. Regardless of disposition, Triton Air Suspensions are designed to integrate with most major heavy-haul axle makes and models. “Using our new Triton Tri-Drive Air Suspensions, OEMs will now have higher-capacity equipment to offer, giving them access to off-highway mining, quarry and logging markets they may not currently serve,” said Bill Ott, vice president of engineering for Link Manufacturing. “Our line of Air Link Suspensions have been 100% off-highway-rated for 25 years, giving us decades of practical engineering experience in that market space. “The Triton Air Suspension is the byproduct of that experience.” Ott said the Triton’s heavy-duty mounting system was born of the company’s off-highway experience. He claimed that through voice-of-the-customer feedback, many of the problems associated with other tri-drives have been engineered out of the Triton, making its installation fast and simple. The Triton mounting system features extra-wide weight-bearing brackets that provide yaw stability, delivering predictable and well-balanced handling, the company said. Ride quality also is enhanced by Triton’s high-mounted air springs and under-slung spring saddles, which allow +/-4 inches of articulation, minimizing roll. “Link’s experience in designing rugged military suspensions has also contributed to the development of the Triton Tri-Drive Air Suspension,” said Neil Mardell, who manages defense programs and heavy vocational products for Link. “Triton’s ability to articulate, providing maximum traction over the most punishing terrain, is partly the result of its highly advanced, military-grade beam design.” Triton also is equipped with longitudinal and lateral control rods that ensure proper axle tracking and alignment. Trailing beams are interconnected by a torsion bar, further improving ride stability. Unique dual-height control valves help the suspension maintain optimum ride height independent of load levels, and all units are fitted with heavy-duty shock absorbers. Triton Tri-Drive Air Suspensions are engineered to maximize durability, while minimizing maintenance requirements, Link said. Polyurethane bushings help provide longer service life and eliminate lubrication requirements. Polyurethane also is more resilient than natural rubber bushings and resistant to petroleum distillates and other common contaminants. All Triton suspensions are treated with Link’s Link-KOAT migratory self-healing metal treatment. Link-KOAT provides excellent corrosion resistance and rust protection, the company claimed, even when surfaces are exposed to excessive abrasion, harsh chemicals and other severe-duty environmental factors. “For the end user, this suspension will improve the laden and unladen ride quality for the driver and the lifespan of the vehicle it serves,” Mardell said. “With Triton, users will enjoy the load-bearing capacity and roll stability of traditional steel spring suspensions, without the bone-jarring ride.” Added Ott: “Drivers will also be able to traverse uneven off-highway topography much more swiftly, which means more loads hauled in each work cycle.” -
-
Seth Clevenger, Transport Topics / May 17, 2019 An unmanned, self-driving truck now is hauling cargo on a short stretch of public road in Sweden. The cabless, battery-electric “T-pod” vehicle, designed by technology startup Einride, began operating on the new route on May 15 as part of a pilot program with transportation firm DB Schenker. The 23-foot cargo vehicle, which has no driver’s seat, pedals or steering wheel, will navigate traffic as it conducts daily freight runs at very low speeds along a 300-meter course between a warehouse and a truck terminal at DB Schenker’s facility in Jönköping. The route is in an industrial area, but includes a 100-meter section of road that also is used by other vehicles, Einride said. “Autonomous trucks will become increasingly important for the logistics sector,” DB Schenker CEO Jochen Thewes said in a statement. “Together with Einride, we have now introduced autonomous, fully electric trucks to a continuous flow on a public road — a milestone in the transition to the transport system of tomorrow.” The Swedish Transport Agency in March approved a permit that allows the T-pod to travel on the public road through the end of 2020. The permit limits the vehicle’s speed to 5 kilometers per hour, or about 3 mph. Robert Falck, Einride’s founder and CEO, also hailed the T-pod’s debut on the new route as a landmark moment in his company’s “movement to create a safe, efficient and sustainable transport solution, based on autonomous, electric vehicles.” The T-pod can carry up to 15 pallets and uses onboard sensors and machine vision to track its surroundings. Although Einride’s T-pods are unmanned, remote drivers monitor the self-driving vehicles and can take control if necessary. Einride’s partnership with DB Schenker, formed in April 2018, includes the operation in Jönköping as well as an option for additional pilots internationally. More than a year ago, Einride showcased its T-pod at the Transportation Research Board’s 2018 annual meeting in Washington. The Stockholm-based company also has interest in potentially bringing its autonomous transport system to the North American market. .
-
U.S. to lift steel, aluminum duties on Canada and Mexico Bloomberg / May 17, 2019 The U.S. will lift steel and aluminum tariffs on Canada and Mexico in favor of stronger enforcement actions, in a move that will help clear the way for ratification of the new NAFTA. In a joint statement on Friday, the U.S. said it removed metals tariffs on Canadian steel and aluminum imports in exchange for Canada scrapping retaliatory tariffs on U.S. goods. The deal will take effect within two days. The move would lift the 25% steel and 10% aluminum tariffs the U.S. placed on the two trading neighbors almost a year ago in the name of national security. The decision sparked retaliatory duties from Canada and Mexico on U.S. farming goods and other products, and became an obstacle for lawmakers in all three nations to ratifying the deal. As part of the agreement to scrap the levies, the U.S. will be able to re-impose the tariffs on metals imports if not enough is done to prevent a surge of imports beyond historical levels. The nations have also agreed to ramp up efforts to trace where the metals have come from originally, to stop the diversion of shipments from other nations to dodge tariffs. The enforcement system will aim to advantage primary steel and aluminum producers in the three-nation trading bloc to ensure that the metal is melted, poured or smelted regionally.
-
Julian Borger, The Guardian / May 17, 2019 The US is now engaged in three major confrontations around the world that have the potential to degrade into war. And in the driving seat on all three fronts is John Bolton, one of the most fervent believers in American military power ever to work in the White House. Donald Trump’s 70-year-old national security adviser has been a fixture in US foreign policy over the past four decades, and has spent that time, whether in or out of government, mostly arguing for the most hawkish position on any issue put in front of him. In the Obama era, Bolton’s bristling walrus mustache was a near constant presence on television, almost always Fox News, from where he would vent scorn and spleen on the Democratic administration. These days, Bolton looks considerably more cheerful, having reached the peak of the policymaking establishment that had once seemed out of his reach. Bolton seems to have played a key role in the collapse of the second Trump summit with Kim Jong-un in February, when he appeared to have drafted a maximalist list of demands for all-or-nothing disarmament that was presented to the North Korean dictator in Hanoi. A year of diplomacy ground to a halt, and Kim, who had been expecting a more gradualist approach, has now started goading the US with a return to missile tests. In the standoff in Venezuela, Bolton was again centre stage, making himself the lead US voice for a failed effort at regime change in Venezuela in late April, producing a personal video appeal calling – in vain – on Nicolás Maduro’s top aides to defect. Behind the scenes he has urged a reluctant US Southern Command to come up with ever more aggressive solutions to Maduro’s hold on power. And in the fast-moving escalation of tensions with Iran, it is Bolton who has seized the initiative, spun military deployments in the Gulf that were already in the pipeline as confrontational steps against Tehran, and reportedly irritated some in the Pentagon and intelligence agencies by putting a sensationalist spin on intelligence about Iranian military movements. Bolton is reported to have convened a deeply unusual meeting on Iran on 29 April, not in the White House, but at CIA headquarters. It was an echo of the buildup to the Iraq war, when Dick Cheney, George W Bush’s vice-president, did the same thing. It now appears likely that Iranian military preparations that the intelligence appeared to suggest, may have been contingencies in anticipation of a US attack – not an unrealistic expectation in view of Bolton’s record. In 2015, he savaged Obama’s diplomatic efforts and penned a now infamous commentary titled To Stop Iran’s Bomb, Bomb Iran. Bolton grew up in a working-class Republican family in Baltimore, and his first political experience was as a volunteer in the doomed 1964 campaign of Barry Goldwater, a staunch conservative from Arizona. Bolton, who saw Goldwater as having been caricatured by the mainstream media, deepened his dislike of liberal eastern elites at Yale University, where he arrived in 1966 on a scholarship. Unlike many of his fellow students, he fiercely supported the war effort in Vietnam, but not to the point of taking part himself. He avoided the draft by joining the Maryland national guard. He put his law degree to use as a counsel in the Reagan administration, and in 2000 Bolton was one of the Republican lawyers flown into Florida to help tilt the deadlocked election in Bush’s favour. In Bush’s state department, Bolton went to work dismantling US diplomatic efforts. He gleefully described taking a “hammer” to the 1994 Agreed Framework deal with North Korea. It was already fraying but it had at least kept Pyongyang’s plutonium production in check for seven years. The Bush team ruled out talks with the rogue regime, but, argued Christopher Hill, a former US lead negotiator, it had no workable alternative. “You would think John Bolton wanted to invade North Korea,” Hill said. “I never saw him put on a helmet, pick up a gun, so I’m not sure what he had in mind with that. It wasn’t as if these people had any thoughts on how to go forward on this.” In the run-up to the Iraq invasion, Bolton was serving as under-secretary for arms control in the state department. He was not making the policy, but he was enforcing it. In one telling episode, he was dispatched to The Hague to get rid of the director general of the Organisation for the Prohibition of Chemical Weapons, a Brazilian diplomat called José Bustani, who had convinced Libya and Iraq to sign the Chemical Weapons Convention. That would have undermined the case for war with Saddam Hussein, and Washington was furious, insisting Bustani had exceeded his mandate. Bolton arrived in the Netherlands in February 2002 with an ultimatum. “He came to my office and said: ‘You have 24 hours to quit, and this is the instruction from Mr Dick Cheney,’” Bustani recalls. Bustani refused, pointing out he had only recently been elected for a second term with US support. “And then Bolton said: you better think it over, because we know where your kids are.” Bustani’s two sons were working in New York at the time. Bustani was stunned and held his ground, but to no avail. The Bush administration convened a special conference of member states and ultimately forced Bustani out. “It was a very unhappy experience,” Bustani said. “This man is different from anyone I have met in my life. He doesn’t allow for a dialogue. You don’t discuss anything with him. It’s just brute force, that’s all.” Bolton’s management style came back to haunt him when he applied for his next job, as US ambassador to the UN, in 2005. The Senate refused to confirm him, and Bush had to bypass Congress altogether, putting him in the post with a temporary appointment that ended in 2006. He spent his years outside government in high-paying jobs at the American Enterprise Institute, the premier conservative intellectual hub in Washington, as a Fox News pundit, and most notably a paid speaker for the cult-like Iranian opposition group, the People’s Mojahedin Organisation (MeK), which was for many years categorised as a terrorist group by the US and EU. It is that background that has convinced Tehran that Bolton is implacably set on forcible regime change. If there is to be an off-ramp on the road to war, and a return to dialogue it may require Trump to fire Bolton. Trump has joked with other officials and foreign leaders that Bolton wanted to get him into a war. “I actually temper John, which is pretty amazing,” the president told reporters last Thursday. But there have been reports that the joke may be wearing thin and that Trump is growing concerned about the direction Bolton is leading him. “John played Trump like a Stradivarius,” Groombridge, Bolton’s former aide, said. “John understands and knows the president very well … He knows to keep it very simple. “[But] I think his influence has waned in the last month or so because he was, unfortunately, in my opinion, factually wrong about the strength of opposition in Venezuela. And now you’ve got a number of people squabbling … about what’s going on with respect to Iran.” .
-
"Truck Talk" (Talking the truck industry)
kscarbel2 replied to kscarbel2's topic in Other Truck Makes
I'm going to go out on a limb and say this now. Speaking of Western Star's 2.4 percent market share, I can easily imagine Autocar scarfing up the majority of that with its new conventional (bonneted) cab line-up.
BigMackTrucks.com
BigMackTrucks.com is a support forum for antique, classic and modern Mack Trucks! The forum is owned and maintained by Watt's Truck Center, Inc. an independent, full service Mack dealer. The forums are not affiliated with Mack Trucks, Inc.
Our Vendors and Advertisers
Thank you for your support!