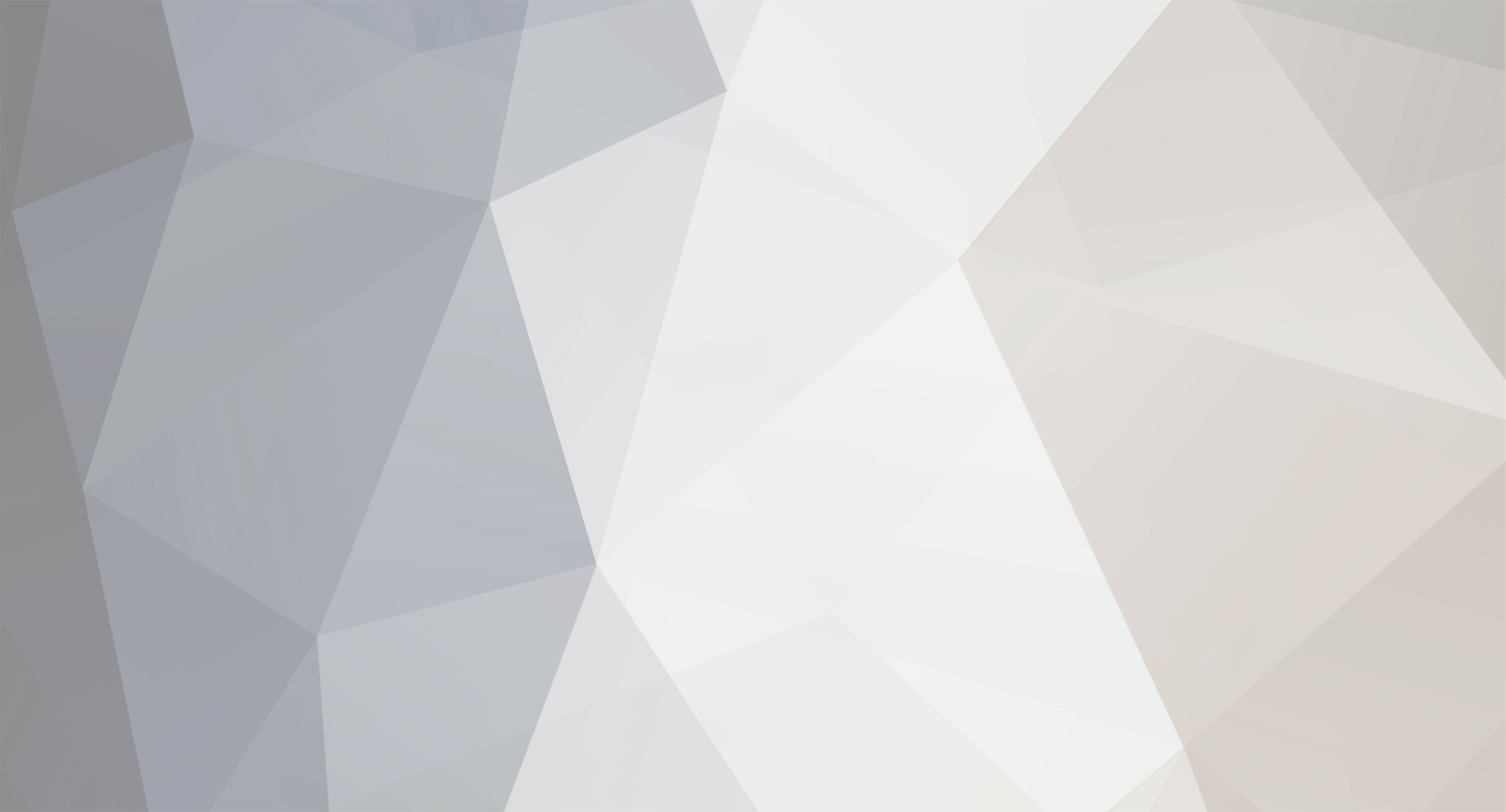
kscarbel2
Moderator-
Posts
18,750 -
Joined
-
Days Won
114
Content Type
Profiles
Forums
Gallery
Events
Blogs
BMT Wiki
Collections
Store
Everything posted by kscarbel2
-
The 2019 Ram 1500 Pickup Now Has a Trick Tailgate of Its Own Joey Capparella, Car & Driver / February 6, 2019 A new Multifunction Tailgate option has 60/40 clamshell doors in an attempt to compete with GMC's MultiPro tailgate. GMC is busy touting its new Sierra 1500 pickup's MultiPro tailgate option that flips and folds in several different ways; it's the centerpiece of the company's new marketing campaign, in fact. But when one of the domestic full-size trucks does something, it's a sure bet that the others will be hot on its heels. Hence a good reason why the new Ram 1500 is now adding a trick tailgate of its own called the Multifunction Tailgate that will soon be available as an option on all 2019 Ram 1500 models. The Ram takes a different approach than the GMC, splitting the tailgate horizontally into hinged 60/40 sections that can swing out, clamshell style, when the tailgate is raised. Each door can be opened individually up to 88 degrees. The tailgate lowers normally in a single piece, has the same damped action as the regular Ram's tailgate, can be operated by remote, and can accommodate a 2000-pound load when lowered. Ram also notes that the tailgate can execute all of its functions even when a trailer is attached. It weighs around 75 pounds more than a standard tailgate, according to Ram. Opting for the Multifunction Tailgate will cost $995 on any trim level—as opposed to the GMC, which only offers its fancy tailgate on upper trim levels—and it comes with a spray-in bedliner, ordinarily an extra-cost option. It can also be paired with an optional $295 retractable center step to aid access into the bed. Ram says it's possible to retrofit the new tailgate to an existing 2019 1500 truck, but because it would require replacing the box in addition to the tailgate, it's an impractical proposition likely to cost several thousand dollars (stand-alone beds for the old Ram cost upward of $4000). Pickups with the new tailgate option will be available at dealerships starting in late spring 2019. .
-
Bob, I think it's noteworthy that the F-550 was left out of the party. Who doesn't think Super-Duty includes F-250 thru F-550, based on marketing to date? Is the F-550 going to be matched with the F-650 and F-750 from now on?
-
DAF Trucks Press Release / February 5, 2019 DAF Trucks has delivered a fully electric truck to Tinie Manders Transport in Geldrop, the Netherlands. The DAF CF Electric featuring E-Power Technology from VDL is used on behalf of DHL for shuttle services in the Eindhoven region. The first CF Electric was put into operation last December by supermarket chain Jumbo. Jos Habets, Director Operations and member of the Board of Management at DAF Trucks, handed over the key of the CF Electric to the management team of Manders Transport. The 83-year-old family business, based in the Brabant region of the Netherlands, is currently under the leadership of the 3rd generation. The truck joins the company's 50 tractors large fleet. Electric trucks for urban areas "It is clear that the transport sector is on the cusp of a major transformation", says Jos Habets. "The electric truck is set to become the norm in more and more urban areas in future. I am extremely proud that we are now in a position to broaden our experience with electric trucks in collaboration with Tinie Manders Transport. The data that we collect about both the technology and the operational deployment will feed into the specifications for the final production models, thus ensuring that they fit seamlessly with the requirements of the market." Zero emissions "We are very proud to be one of the first to drive this pioneering DAF", states Eveline Manders. "We have been involved in its development from the outset and we are, of course, curious to see the results in practice. Our decision as to whether to expand the range of electric vehicles within our company will be based not only on the zero emissions factor, but also on the ease of use and the additional possibilities that this truck offers us. Zero emissions combined with the minimal noise levels of the truck mean that we can also meet the increasingly stringent legal requirements for inner city transport, thereby enabling us to set ourselves apart from the competition." Important step Willem van der Leegte, President and CEO of VDL Groep, had the following to add: "Tinie Manders, DAF Trucks and VDL all boast a strong foundation, a thorough approach and top-quality innovation. It is truly wonderful to see three companies from the Brabant region come together in this way to test the DAF CF Electric featuring VDL E-Power in practice. Tinie Manders had the confidence to stick its neck out, getting in contact straight away to express interest in participating in the testing phase for this development project. As a result, the family business has played an important role in the creation of this innovative vehicle, which offers the world progress in terms of achieving sustainability in goods transport." Collaboration Tinie Manders Transport will combine the fully electric truck with a fully electric refrigerated trailer. This unique combination made the Geldrop-based transporter eligible for the Dutch DKTI subsidy for sustainable transport. This DKTI project not only involves DAF, VDL Groep and Tinie Manders Transport, but also DHL, TNO, Allego, THT New Cool and the municipality of Geldrop-Mierlo. Allego provides a public charging solution in Geldrop, the municipality is involved in the implementation of the charging infrastructure and THT New Cool is supplying two electrically cooled, zero-emissions trailers, in which energy is recovered during braking. Finally, TNO will examine the results achieved by the electric truck/trailer combination and assess whether more regional transport could be carried out using fully electric vehicles. About the DAF CF Electric The DAF CF Electric is a 4x2 truck unit developed for road haulage of up to 37 tonnes in urban areas, for which single-axle or dual-axle trailers are the norm. The vehicle is based on the DAF CF—named 'International Truck of the Year 2018'—and is operated fully electrically using VDL's E-Power Technology. The core of this intelligent powertrain is a 210-kW electric motor powered by a lithium-ion battery pack with a current total capacity of 144 kWh. The CF Electric has a range of approximately 100 kilometres, depending on the weight of its cargo, making it suitable for high-volume transport in the urban distribution market. The batteries have a 30-minute quick-charge feature and a full charge takes just one and a half hours. DAF CF Electric — Technical specifications Truck weight 9,700 kg Electric motor 210 kW Torque 2,000 Nm Battery capacity 170 kWh Range of fully charged vehicle up to 100 km Battery quick-charge 30 minutes Full charge 1.5 hours .
-
Motiv Power delivering all-electric step vans to USPS Trailer-Body Builders / February 5, 2019 Motiv Power Systems, a provider of all-electric medium duty fleet chassis, recently began delivering Ford E-450-based all-electric step vans to the United States Postal Service (USPS). Compared to their combustion engine-powered counterparts, Motiv says its all-electric EPIC chassis-equipped mail delivery vans are expected to curtail fuel and maintenance costs, resulting in a reduction of total cost of ownership. The pilot program of seven Motiv-powered vans is slated for deployment in California’s Central Valley. The first vehicle now serves routes in Fresno, with the balance of the vehicles to be deployed in Fresno and Stockton as part of a year-long program. Most of the immediate project benefits are aimed for the San Joaquin Valley, an economically disadvantaged area with some of the highest pollution burdens in the country, as evidenced by CalEnviroScreen scores within the worst 5% in the state. USPS has a history of testing electric vehicles for city delivery. The first known test of an electric vehicle for mail collection was in Buffalo NY on July 2, 1899. Since 2001, the USPS has operated 30 electric 2-ton vehicles on the streets of New York City, and these were later joined by a pair of 2-ton hybrid electric vehicles in Long Island. “We’re proud to now be a part of USPS’ long tradition of implementing the latest technology to green their fleet,” said Jim Castelaz, Motiv CEO. “Our all-electric EPIC chassis have accumulated 500,000 real-world miles and are ideally suited to the USPS vehicle route characteristics. We’re thrilled that USPS has chosen Motiv to help meet their sustainability goals.” USPS’ acquisition of the Motiv chassis-powered vans was developed as a partnership by CALSTART and the San Joaquin Clean Transportation Center and funded through a California Air Resources Board (CARB) award to the San Joaquin Air Quality Control. The funds are meant to provide an incentive to Californian fleets to adopt the cleanest emerging technologies and continue to advance California’s Air Quality and Climate goals. The acquisition was made possible by California Climate Investments, a statewide program that puts billions of cap-and-trade dollars to work reducing greenhouse gas emissions, strengthening the economy and improving public health and the environment, particularly in disadvantaged communities. The cap-and-trade program also creates a financial incentive for industries to invest in clean technologies and develop innovative ways to reduce pollution. .
-
I have to disagree. Tyson was very pleased with their Ford HN80s, and many die-hard Ford fleets chased the HN80's trail and bought Sterlings....and still operate them today with a sense of pride.....as if they were Fords.
-
Fiat Chrysler recalls 882,000 pickup trucks for steering, pedal issues David Shepardson, Reuters / February 5, 2019 WASHINGTON -- Fiat Chrysler Automobiles said on Tuesday it would recall 882,000 pickup trucks worldwide in two new recalls to address steering and pedal issues. The Italian-American automaker said it was recalling about 660,000 heavy duty Ram 2500 and 3500 pickup trucks from the 2013 through 2017 model years, including 574,000 in the United States, as drivers could potentially experience steering loss. A nut could come loose and prevent drivers from being able to steer the vehicle, Fiat Chrysler said, adding it had reports of one injury and eight accidents possibly related to the issue. The company will also recall 222,000 2019 Ram 1500 pickup trucks worldwide to better secure brake pedals while the vehicles’ adjustable-pedal feature is in use. The brake pedal could get detached if drivers move pedals to the rear-most position, the company said. That could be dangerous if trucks are traveling at highway speeds. Last month, Fiat Chrysler recalled about 180,000 2019 Ram 1500 pickups to tighten a fastener linked to reports of power-steering loss. Fiat Chrysler said the issue could lead to steering problems.
-
B model Mack gas engine parts
kscarbel2 replied to underdog663's topic in Antique and Classic Mack Trucks General Discussion
Doesn't Matt Pfahl (Pfahl Mack Restorations) have them? Or you can call the fine folks at Watt's Mack. 126SB127C - Complete gasket set for EN and ENF 707A and 707B engines 553GB3266B - head gasket (individual) EN707 with 20 studs 3029-8213C - head gasket (individual) EN707 with 18 studs -
Reuters / February 5, 2019 Volkswagen is in talks with Swedish institutional investors AMF, AP Fund 1 and 4, Investor AB and Folksam about being cornerstone shareholders in the dual listing of its trucks unit Traton in Stockholm and Frankfurt. The discussions could result in more than one cornerstone investor being brought on board and are for each investor to take a 150 million to 300 million euro ($171.21-$342.42 million) stake. Cornerstone investors are institutions that are invited to subscribe to shares ahead of an IPO to boost its popularity and often serve as a seal of approval for other investors. Securing such investors is popular among Nordic companies. Första AP-fonden (AP1) had been asked about being anchor investors, its head of equities Olof Jonasson said. He declined to comment on stake size and price. “We have been approached but I couldn’t really tell you anything about the details... Our interest... would be about business potential and valuation and all those things put together,” said Jonasson, whose fund is also a large owner of Swedish rival AB Volvo. VW expects to sell shares worth 5 billion-6 billion euros ($5.7-$6.9 billion) in an April listing that could value Traton about 20 billion-25 billion euros. At this size and value, the IPO could potentially become Germany’s and Sweden’s biggest new share offering in 2019, but the sources said its size had not yet been finalised and would depend on market conditions. AP4 head of equities Per Colleen said he could not confirm any of the details but added: “Anything of that size, we will have a serious look at”. AMF, Investor AB, Folksam, Volkswagen and Traton did not immediately respond to requests for comment. Traton is the umbrella name for MAN, Scania and VW brands, but Swedish company Scania is by far its most valuable part, with superior profitability and stability. Scania was listed in Stockholm until 2014, when its then largest investor VW took it private in a deal that valued it at about 17.9 billion euros, but many Swedish investors that were squeezed out said then that the offer undervalued the group. Swedish funds were keen for a substantial stake in the Traton IPO as they expected it to have a large influence on the automotive and engineering-heavy Stockholm blue-chip index that they try to outperform.
-
GM truck plant in Michigan to add 1,000 workers Reuters / February 5, 2019 FLINT, Mich. -- General Motors said Tuesday it will add 1,000 workers to build new heavy-duty pickup trucks at its plant in Flint, Michigan, and will give priority to GM workers who were laid off elsewhere. GM has come under fire from U.S. President Donald Trump and Midwestern lawmakers for its plans to stop production at five North American factories and cut up to 15,000 jobs. The automaker has said it is trying to find new jobs for 1,500 U.S. hourly workers at the affected plants. Flint could be a haven for many of these employees. Sales of heavy-duty pickups in the United States have grown to more than 600,000 vehicles a year, up more than 20 percent since 2013, according to industry data. Prices for luxury models can easily top $70,000. GM on Tuesday will celebrate the launch of a new generation of heavy-duty GMC and Chevrolet pickups at the assembly plant in Flint, Michigan, that is now building all such trucks for the company. .
-
Scania Group Press Release / February 4, 2019 With the delivery of Scania R 410 liquified gas trucks, all of Gruppo Sanpellegrino’s shuttle transports from the mineral water bottling plant at San Pellegrino Terme to its logistics centre at Madone are now operated on gas fuel. Sanpellegrino in 2018 produced 1.5 billion bottles of mineral water, that are exported to more than 150 countries. Growth over the past years has been strong and continues to increase. Sanpellegrino will this spring start construction of a major extension of its production facilities. That means more transports on the narrow winding roads through villages in the Bergamasque Prealp valleys to and from the springs. Each day, there are 300 truck movements to the production plant, around the clock, all days of the week. In view of rising production, Sanpellegrino and its logistics partner Koiné therefore initiated discussions with Scania on finding a more sustainable solution. “These liquified gas trucks constitute an important element in ensuring the continued development of our operations,” says Maura Sartore, Head of Supply Chain South Europe, Nestlé Waters. The group underlines that the introduction of gas trucks forms a part of its sustainability agenda and that it has already cut water consumption by 200,000 cubic metres and that its electricity supply is now fully renewable. “The gas delivery to Sanpellegrino with Koiné once again highlights the importance of pursuing a novel approach in addressing sustainability and acting together to speed up the transition to a sustainable transport system,” says Franco Fenoglio, Managing Director of Italscania. In addition to annual carbon savings of 500 tonnes, the gas engines offer a substantial noise reduction in comparison with diesel engines. Since the company schedules transports during nights to avoid traffic congestion on route to Madone, 35 km from the springs, this has been a major consideration. Of the annual 80,000 trucks that arrive at San Pellegrino, 75 percent drive to the logistics centre. “Sanpellegrino is a major employer here and our residents are happy with the fact the it is expanding operations and generating more employment,” says Mayor Giuliano Ghisalberi, Zogno Municipality. “At the same time, there has been concern about increased traffic, noise and pollution. We are therefore extremely pleased with the introduction of gas trucks.” Koiné has in total taken delivery of 50 Scania R 410 liquified gas trucks, most of which will be used in operations for Sanpellegrino. Interest in using liquified gas in heavy truck operations in Italy is rapidly rising and there are presently 39 filling stations for liquified natural gas (LNG) in the country with an additional 25 stations under way. .
-
The construction business is tough for beginners
kscarbel2 replied to kscarbel2's topic in Trucking News
Note Ford Truck's proprietary planetary hub reduction drive axles. With the introduction of Ford's proprietary AMT transmission in 2020, the truckmaker will have a vertically integrated drivetrain. -
Ford Trucks International / Sharing The Load At Ford Trucks, we’ve been making rugged construction trucks for over a hundred years. No matter what the job, Ford Trucks are engineered to deliver. Always have been…..Always will be. .
-
Informative video, and the Ford engineer mentions 7.3L medium duty application. I'd rather it was a 4-valve. No 2-valve argument will win me over. .
-
No mention of the F-550. No mention of the 7.3 completely replacing the V-10, and the latter simultaneously being phased out.
-
Ford Super Duty packs new engine, more power for 2020 Michael Martinez, Automotive News / February 5, 2019 DETROIT -- Ford Motor Co. is adding a second V-8 engine option and upping the power on its Super Duty pickups to maintain its segment dominance halfway through the vehicles' life cycle. The 2020 F-250, F-350 and F-450 pickups, scheduled to go on sale this fall, will offer an optional 7.3-liter V-8 engine in addition to an updated third-generation 6.7-liter Power Stroke diesel and the standard 6.2-liter V-8. They will be paired with a new 10-speed automatic transmission. Although executives refused to offer specific figures, they said the new powertrains will improve power, payload and towing capability, critical stats for the construction workers and fleet operators who most use the vehicles. Ford has adopted the "We Own Work" slogan for the Super Duty, which leads in sales and market share but faces increased competition from new offerings by Ram and Chevrolet. Ford last redesigned the Super Duty for the 2017 model year, when it shed as much as 350 pounds by switching to an aluminum body. The midcycle freshening comes as Ford shifts 90 percent of its capital allocation to producing pickups, vans and utilities. By 2020, roughly 75 percent of its lineup will be updated or new. "Fundamentally, we're playing to our strengths," Kumar Galhotra, Ford's president of North America, said at a media briefing. Most powerful V-8 The 2020 Super Duty's new 7.3-liter engine is expected to be the most powerful gasoline V-8 in its class, Ford says. Its overhead valve architecture has a cast iron block and forged steel crankshaft. Ford will offer a compressed natural-gas conversion option. The third-generation Power Stroke diesel will be Ford's most powerful. It has a stronger cylinder head, block, connecting rods and bearings to handle higher cylinder pressure and increased output. It includes a new 36,000-pounds per square inch fuel injection system with new injectors that Ford says precisely meter and spray up to eight times per stroke to control noise levels and optimize combustion. The 10-speed transmission, which replaces a six-speed, is better for towing, Ford said. It said the Super Duty will be the only vehicle in the segment to offer live-drive power takeoff, which allows the operator to engage industrial equipment and accessories such as snowplows while the vehicle is in motion. Exterior, tech improvements Aside from the powertrain improvements, the 2020 Super Duty gets exterior updates that include a revised grille, as well as interior and technological enhancements. The vehicle will come with an optional pro-trailer backup assist feature that is used on its smaller F-150 sibling. The feature lets drivers steer the trailer with a reverse camera that can handle all trailer styles, including fifth wheels and goosenecks. It also includes lane-keep assist, emergency braking with pedestrian detection and blind spot monitoring technology. The features are standard on XLT and higher trims. Ford also added new drive modes, including Eco, Slippery and Sand/Mud. It also comes with an embedded 4G LTE modem and Wi-Fi. In addition to the grille, which improves cooling, the truck has a new tailgate design and updated headlights, taillights and bumpers. Ford did not disclose fuel-economy figures or pricing. Related reading - http://www.campaign.ford.com/content/fordmedia/fna/us/en/news/2019/02/05/new-ford-f-series-super-duty-pickup-raises-bar-again.html .
-
The big bulbous hood just doesn't pair with the small pickup truck cab......does it? It needs a wider, larger dedicated commercial cab. And with combined Chevrolet and Navistar sales, there's an argument for that. Given how inexpensive cabs are to design and produce today........... The 6500HD is the smallest Class 6 I've ever seen.
-
Jay's good people.
-
I remember Cooper was struggling financially and India's Apollo tire was going to buy them, but things got muddy. I didn't follow the outcome. Then Cooper sourced more production from China. https://www.daytondailynews.com/business/apollo-files-counterclaim-against-cooper-tire/bp4GACz3IfSvHaM2AIScYJ/ https://www.rubbernews.com/article/20180926/news/180929962/sailun-to-become-cooper-tire-joint-venture-partner
-
Wanli makes a good tire as well. (This English global website only shows a small portion of their product line). http://www.wanli-global.com/yww/brand/wanlitire/allsteel/index.shtml
-
Look at the Coopers and see if they say "Made in China". Their light vehicle tires are. Back in the day, I felt there was no better combination than Bridgestone R290 steer tires and Goodyear G367 drive tires. Today, Goodyear's pricing is ridiculous. Most people have had a great experience with Double Coin.
BigMackTrucks.com
BigMackTrucks.com is a support forum for antique, classic and modern Mack Trucks! The forum is owned and maintained by Watt's Truck Center, Inc. an independent, full service Mack dealer. The forums are not affiliated with Mack Trucks, Inc.
Our Vendors and Advertisers
Thank you for your support!