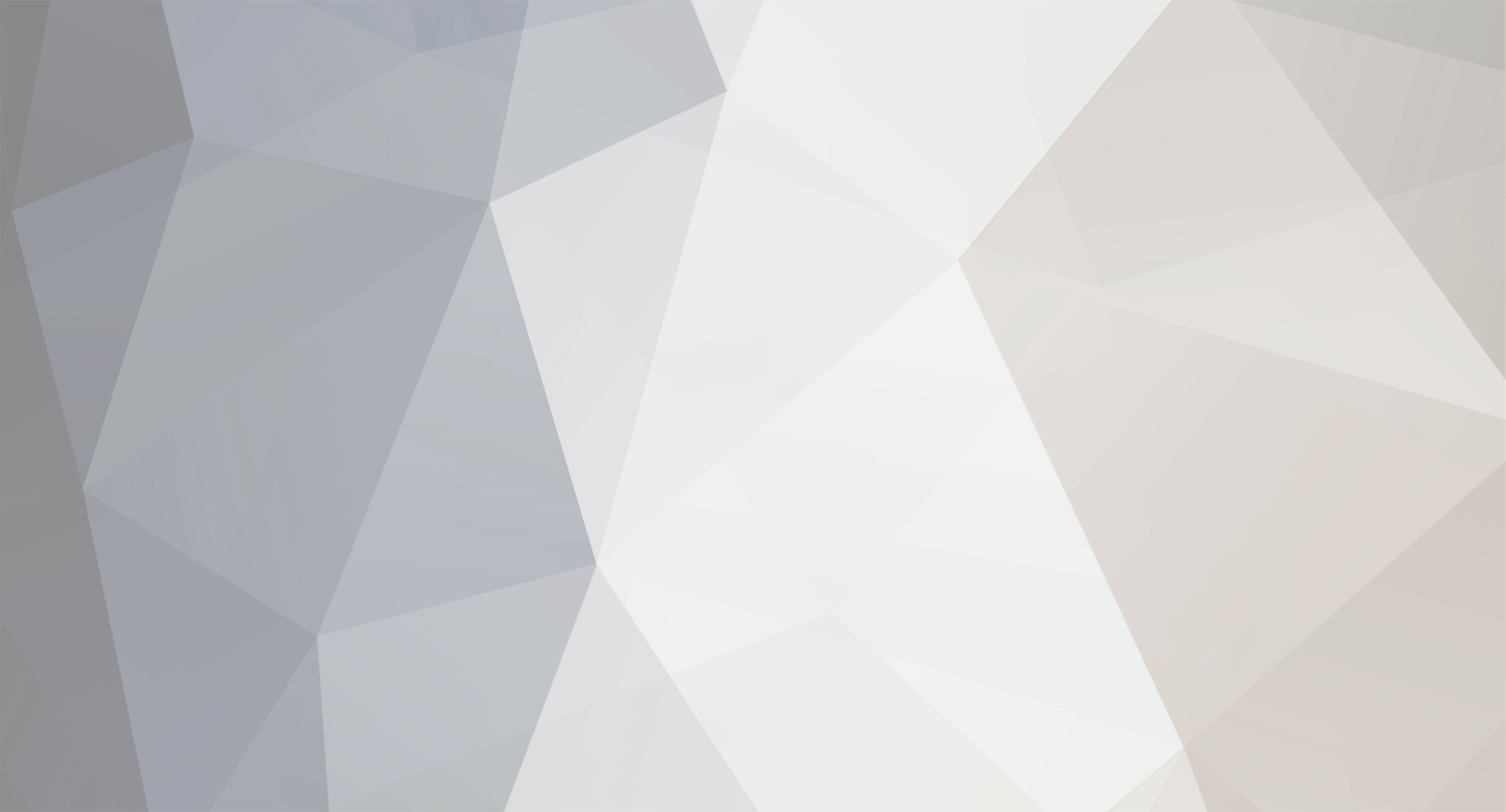
kscarbel2
Moderator-
Posts
18,734 -
Joined
-
Days Won
114
Content Type
Profiles
Forums
Gallery
Events
Blogs
BMT Wiki
Collections
Store
Everything posted by kscarbel2
-
Ford's European losses increase on Turkey, Russia weakness Michael Martinez, Automotive News Europe / October 24, 2018 DETROIT -- Poor results in China and Europe contributed to a 37 percent drop in third-quarter net income for Ford Motor, and the automaker backed off its goal of raising its global profit margin to 8 percent by 2020. But the automaker's top executives on Wednesday continued to stress patience to investors as CEO Jim Hackett’s $11 billion restructuring plan starts to take hold. Ford reported on Wednesday that its net income fell to $991 million in the quarter, although revenue rose 3 percent to $37.6 billion, driven by higher-profit vehicles in North America including the redesigned Expedition and Lincoln Navigator SUVs. Ford's earnings before interest and taxes fell 27 percent to $1.7 billion. “We’ve had an extremely productive quarter in terms of putting building blocks in place,” Hackett said on a conference call. “We’re addressing real issues and we’re moving quickly to redesign the business in support of our stated strategy.” But Ford said its challenges overseas, as well as higher costs and uncertainty clouding the entire auto industry, mean it no longer forecasts achieving the 8 percent profit-margin target it set previously. CFO Bob Shanks declined to offer an alternate timeframe for reaching that threshold. “We don’t see, at the moment, a way to get there,” Shanks told analysts. “Certainty we’re trying to get there as fast as we can. I’m not going to put a timeframe on it because I don’t want to go back and have to change it.” Hackett and his leadership team have faced scrutiny from Wall Street analysts who have asked for more clarity regarding his plan. Hackett on Wednesday said the details would be shared over time. “We’re fully committed to sharing details as soon as we can, but I can’t allow us to get ahead of the process,” he said. “The need to get our stakeholders up to speed is the priority for me and the entire company.” Ford's profits in the quarter were driven by North America, where earnings rose 7.5 percent to $1.96 billion. Its profit margin for the region was unchanged from the same period a year ago at 8.8 percent. The automaker said its market share in the region was down slightly because it was discontinuing sedans, but market share for its profitable F-series pickups increased. Hackett said those results “demonstrate early evidence that fitness actions are now taking hold.” Ford’s profit margin for the quarter was 4.4 percent, down 1.9 percentage points compared with the same period a year ago. China troubles Ford posted lower revenue, market share and sales in China, the world's largest vehicle market. Ford lost $208 million in Asia Pacific in the quarter. Excluding China, it made $170 million in the region with profit margins of 9 percent. The automaker is suffering from a lack of new product there that has led to a sharp decline in sales. New-vehicle sales fell 43 percent in September from a year earlier and are down 30 percent through the first nine months of the year. Ford on Tuesday said it would separate its China business into a standalone unit and appointed Anning Chen, a former Ford executive with 25 years of industry experience, to become CEO of Ford China on Nov. 1. Europe loss Ford lost $245 million in Europe, up from a loss of $192 million in the same quarter last year. This was due to weakness in Turkey and Russia, and launch-related costs for the latest Focus compact car, Ford said. The company said revenue in the region increased due to higher volume and net pricing driven by new products. Volume up in most major markets but this was offset partially by large decline in Turkey, Ford said. The compay's sales in Turkey fell 25 percent through August in a total market down 21 percent. In Russia, Ford's sales were flat in September in a market up 6 percent. In other regions, Ford lost $152 million in South America, down 1 percent. It made $47 million in the Middle East and Africa. Ford said its mobility unit lost $196 million in the second quarter, $124 million more than it lost during the same period a year ago. The unit is in a heavy investment phase that has little offsetting revenue. Ford Motor Credit made $678 million, its best quarterly results since 2011. Ford’s net income equaled 29 cents per share, 1 cent higher than the consensus estimate on Wall Street. The company reaffirmed its full-year target of adjusted earnings per share of $1.30 to $1.50. It had previously lowered its guidance from a range of $1.45 to $1.70 per share, citing troubles in Europe and China. .
-
Ford recalls nearly 1.5 million Focus sedans for engine stall issue Reuters / October 25, 2018 WASHINGTON -- Ford Motor Co. said Thursday it will recall nearly 1.5 million cars in North America to address a faulty part that could lead to engine stalls. Ford said it is calling back 2012 through 2018 model year Ford Focus cars with 2.0-liter GDI and 2.0-liter GTDI engines for a malfunctioning valve that could result in inaccurate fuel level readings and potentially engine stalls or an inability to restart the vehicle. Ford said it is not aware of any crashes as a result of this condition but said owners should maintain at least a half tank of fuel until the recall is completed.
-
Ford (F) set a new 52-week low today of $8.17, closing up a penny at $8.18.
-
Ford posts 37% earnings decline on China challenges, retreats on profit margin goal Michael Martinez, Automotive News / October 24, 2018 DETROIT -- Poor results in China and other overseas markets contributed to a 37 percent drop in third-quarter net income for Ford Motor Co., and the automaker backed off its goal of raising its global profit margin to 8 percent by 2020. But the automaker’s top executives on Wednesday continued to stress patience to investors as CEO Jim Hackett’s $11 billion restructuring plan starts to take hold. Ford reported on Wednesday that its net income fell to $991 million in the quarter, although revenue rose 3 percent to $37.6 billion, driven by higher-profit vehicles in North America including the redesigned Expedition and Lincoln Navigator SUVs. Ford's earnings before interest and taxes fell 27 percent to $1.7 billion. “We’ve had an extremely productive quarter in terms of putting building blocks in place,” Hackett said on a conference call. “We’re addressing real issues and we’re moving quickly to redesign the business in support of our stated strategy.” But Ford said its challenges overseas, as well as higher costs and uncertainty clouding the entire auto industry, mean it no longer forecasts achieving the 8 percent profit-margin target it set previously. CFO Bob Shanks declined to offer an alternate timeframe for reaching that threshold. “We don’t see, at the moment, a way to get there,” Shanks told analysts. “Certainty we’re trying to get there as fast as we can. I’m not going to put a timeframe on it because I don’t want to go back and have to change it.” Hackett and his leadership team have faced scrutiny from Wall Street analysts who have asked for more clarity regarding his plan. Hackett on Wednesday said the details would be shared over time. “We’re fully committed to sharing details as soon as we can, but I can’t allow us to get ahead of the process,” he said. “The need to get our stakeholders up to speed is the priority for me and the entire company.” Ford's profits in the quarter were driven by North America, where earnings rose 7.5 percent to $1.96 billion. Its profit margin for the region was unchanged from the same period a year ago at 8.8 percent. The automaker said its market share in the region was down slightly because it was discontinuing sedans, but market share for its profitable F-series pickups increased. Hackett said those results “demonstrate early evidence that fitness actions are now taking hold.” Ford shares sank earlier Wednesday to close at $8.18 a share, but rose 5.5 percent to $8.65 at 5:50 p.m. ET in after-hours trading, following the earnings release. China troubles Ford posted lower revenue, market share and sales in China, the world's largest vehicle market. Ford lost $208 million in Asia Pacific in the quarter. Excluding China, it made $170 million in the region with profit margins of 9 percent. The automaker is suffering from a lack of new product there that has led to a sharp decline in sales. New-vehicle sales fell 43 percent in September from a year earlier and are down 30 percent through the first nine months of the year. Ford on Tuesday said it would separate its China business into a standalone unit and appointed Anning Chen, a former Ford executive with 25 years of industry experience, to become CEO of Ford China on Nov. 1. Regional performance Ford’s profit margin for the quarter was 4.4 percent, down 1.9 percentage points compared with the same period a year ago. The company lost $152 million in South America, down 1 percent, and lost $245 million in Europe. It made $47 million in the Middle East and Africa. Ford said its mobility unit lost $196 million in the second quarter, $124 million more than it lost during the same period a year ago. The unit is in a heavy investment phase that has little offsetting revenue. Ford Motor Credit made $678 million, its best quarterly results since 2011. Ford’s net income equaled 29 cents per share, 1 cent higher than the consensus estimate on Wall Street. The company reaffirmed its full-year target of adjusted earnings per share of $1.30 to $1.50. It had previously lowered its guidance from a range of $1.45 to $1.70 per share, citing troubles in Europe and China.
-
Once upon a time, we actually enjoyed privacy
kscarbel2 replied to kscarbel2's topic in Odds and Ends
Tim Cook blasts 'weaponisation' of personal data and praises GDPR Chris Baraniuk, BBC / October 23, 2018 Apple chief executive Tim Cook has demanded a tough new US data protection law, in an unusual speech in Europe. Referring to the misuse of "deeply personal" data, he said it was being "weaponised against us with military efficiency". "We shouldn't sugar-coat the consequences," he added. "This is surveillance." The strongly-worded speech presented a striking defence of user privacy rights from a tech firm's chief executive. Cook also praised the EU's new data protection regulation, the General Data Protection Regulation (GDPR). The new law came into force in May. Cook's speech was made in Brussels, at the International Conference of Data Protection and Privacy Commissioners. The Apple boss described in some detail what he called the "data industrial complex", noting that billions of dollars were traded on the basis of people's "likes and dislikes", "wishes and fears" or "hopes and dreams" - the kind of data points tracked by tech firms and advertisers. He warned that the situation "should make us very uncomfortable, it should unsettle us". And the trade in personal data served only to enrich the companies that collect it, he added. Cook went on to commend the EU's GDPR, which places stricter rules on how personal data is handled by businesses and organisations. 'Follow EU's lead' "This year, you've shown the world that good policy and political will can come together to protect the rights of everyone," he said. "It is time for the rest of the world, including my home country, to follow your lead. "We at Apple are in full support of a comprehensive federal privacy law in the United States." The remark was met with applause from the conference audience. "I think it is striking that he's saying this," said Jim Killock, director of the Open Rights Group. "It's the kind of thing you normally hear from civil society organisations." However, Prof Mark Elliot at Manchester University argued Mr Cook did not go far enough. "The implication of fully functioning privacy in a digital democracy is that individuals would control and manage their own data and organisations would have to request access to that data rather than the other way round," he said. Apple has long been committed to privacy protection. -
B-2 stealth bomber makes emergency landing at Colorado Springs KOAA News 5 / October 23, 2018 COLORADO SPRINGS – The 21st Space Wing at Peterson Air Force Base confirmed to News 5 early Tuesday morning that a B-2 Stealth Bomber landed at the Colorado Springs Airport due to an in-flight emergency. The Air Force refused to say what forced the $1.157 billion bomber to make the landing. A maintenance crew is on the way to Colorado Springs from Missouri to check on the airplane to make sure it is still flightworthy for the trip back to Whiteman Air Force Base in Warrensburg. An Air Force spokesman would only say that the pilot determined it was safer to land here than continue on their training flight. Depot maintenance responsibilities occur at Tinker Air Force Base in Oklahoma. Day-to-day maintenance responsibilities happen at Whiteman Air Force Base in Missouri. .
-
SAF-Holland Press Release / October 15, 2018 2018 IAA Show – Hannover, Germany – SAF-HOLLAND displays a conceptual Automatic Coupling System. https://www.youtube.com/watch?v=sPf5Uz9VZrE
-
Meritor Press Release / October 4, 2018 .
-
Hendrickson Press Release / October 17, 2018 .
-
Scania Group Press Release / October 23, 2018 German farmers receive government incentives to make biogas out of their fresh cow dung. AgriKomp, a leading creator of renewable energy systems, is there to help them out, using Scania engines to power its biogas plants. In Germany, government incentives encourage the continuous development of small-scale, climate-friendly biogas power plants. Farmers are offered feed-in tariffs which are guaranteed for 20 years, for the production of electricity from biogas. AgriKomp is one of Germany’s leading developers of biogas power plants. It has constructed 550 renewable energy installations on farms around the country, and more than 850 worldwide. Power plants produce biogas The power plants are airtight to enable the anaerobic breakdown of organic material such as slurry, manure and residue from food and agricultural production. This in turn produces biogas. The biogas contains approximately 60 percent methane, 39 percent carbon dioxide and traces of other gases such as hydrogen, nitrogen and hydrogen sulphide. Before being fit for use, the gas is cleaned to remove condensate, hydrogen sulphide and other substances that are harmful to engines. The processed biogas is then used to run a Scania 13-litre industrial engine, which in turn powers a generator. The electricity from the generator is fed into the national grid. When upgraded to biomethane, biogas can also be used as fuel for vehicles or injected into the national gas grid. The heat generated warms up farm buildings and greenhouses, is sold via district heating networks to neighbours, or is used for industrial applications. It’s a win-win situation. “Biogas opens up various utilisation paths in many sectors including transport, heating and electricity,” says Gernot Buchta, Head of Marketing, AgriKomp Group. “It is storable and can be used when it is needed – for example, if there is a peak in electricity demand,” Buchta continues. “Biogas plants in flexible operating mode can help to close the demand gap and stabilise the grid. Our BGA-136 power unit with the Scania 13-litre engine is ideally suited to provide flexible energy production.” Since the mid-1990s, AgriKomp has been developing biogas systems for agricultural businesses and has implemented more than 850 so far. The total installed capacity of these systems is close to 250 MW. Some 400 employees run its network, including its headquarters in Germany, as well as branch offices and partners in the UK, Ireland, France, Switzerland, Italy, the Czech Republic, Poland and Slovakia. The company also runs projects in Canada, Kenya, Russia and China. Tailor-made solutions for clients worldwide For the pasttwo years AgriKomp has been using Scania’s 13-litre engine in its tailor-made solutions. “We scale it down to the required emissions limits and equip it with an oxidation catalyst,” explains Buchta. “There is no need to adjust anything else. The 13-litre fits with our output range [150 kW to 250 kW] and our efficiency requirements. It’s easy to handle, and spare parts and maintenance services are available worldwide,” he says. There are now plans to extend AgriKomp’s engine portfolio, with the inclusion of the Scania 9-litre in its product range in 2018, and the 16-litre in 2019. Scania is happy to help in this highly sustainable project. “Our work with AgriKomp has been a real success story,” says Jörg Franzke, Head of Engines Sales and Service at Scania Germany. “We started delivering 13-litre engines in 2016, and since then we have continuously grown together,” Franzke adds. “In this application our engines have a long life cycle of up to 40,000 hours or more, which makes them very attractive for use in power plants, so we hope to enjoy an even higher level of cooperation in the future.” Engine type • The Scania engines used for power generation are based on a robust design with a strength-optimised cylinder block containing wet cylinder liners that can easily be exchanged. Individual cylinder heads with four valves per cylinder promote reparability and fuel economy. • The Scania 13-litre engine: 150 to 250 kW continuous electric power at 1,500 r/min.
-
Daimler Press Release / October 24, 2018 São Bernardo do Campo – Brazil's largest brewery and drinks supplier Cervejaria Ambev is making major enlargements to its fleet and has chosen trucks with the three-pointed star. A total of 228 new Mercedes-Benz trucks – 212 Atego and 16 Actros models – will help to supply beer and beverages even more efficiently and safely to thirsty customers. The robust, manoeuvrable Mercedes-Benz Atego trucks are ideal for local distribution and will reliably serve retailers. The Mercedes-Benz Actros will provide long-distance transport between breweries and major logistics centres, ensuring Brazil's supermarkets don't run dry. The first vehicles were handed over to Ambev in September, and the other beer trucks will follow monthly until the end of the year. Part of the fleet will be equipped with Fleetboard, the innovative cargo managing system: this will save on operating costs and, at the same time, ensures that the driver and their freight arrive at the destination faster and safer. .
-
Daimler Press Release / October 23, 2018 Daily food delivery to EDEKA locations in Berlin Locally emission-free and quiet Daily route between 150 and 300 km Part of the eActros "innovation fleet" of a total of 10 vehicles Also present today for the handover to EDEKA: Rita Schwarzelühr-Sutter, Parliamentary State Secretary at the Federal Ministry for the Environment, Nature Conservation and Nuclear Safety Berlin – Mercedes-Benz Trucks today delivered a fully electric eActros for on-road testing to EDEKA. The German retail association will be testing a 25-tonne truck with refrigerated body for one year in Berlin, where it will be used to transport fresh, temperature-sensitive foodstuffs in Germany's capital. The daily route from the warehouse in Grünheide on the outskirts of Berlin to various EDEKA supermarket branches in the city centre and surrounding areas is between 150 and 300 km. The vehicle will operate in a double shift pattern. The weight of the transported goods can be up to 10 tonnes. During loading and unloading, the vehicle is charged to ensure that the total range of the eActros (up to 200 km with a single battery charge) is optimally utilised. EDEKA is the only company from the retail sector in Germany, which will use the eActros in its own fleet of vehicles. The symbolic handover of the vehicle to EDEKA took place at the Gasometer in the Berlin-Schöneberg district. In addition to representatives from Mercedes-Benz Trucks, EDEKA and truck body manufacturer Schmitz Cargobull, Rita Schwarzelühr-Sutter, Parliamentary State Secretary at the Federal Ministry for the Environment, Nature Conservation and Nuclear Safety, also took part in the event. Two-year test with 20 customers – series production starting in 2021 EDEKA is one of a group of 20 customers – all from various industries – that are now integrating the heavy-duty electric truck into their fleets. Each of these selected customers will put a near-series version of either the 18 or 25-tonne variant through its paces in real operations and will test the respective vehicle for its suitability for their daily field of work. The aim of Mercedes-Benz Trucks is to make emission-free and quiet driving a reality in cities from the year 2021, also with series heavy-duty trucks – and all of this as economically viable as with a diesel truck. The test series consists of two phases, each with ten customers and spanning a total of around two years. The development and testing of the heavy-duty electric truck in short-radius distribution operations is sponsored as part of the "Concept ELV²" project to varying degrees by the German Federal Ministry for the Environment (BMU) and the Federal Ministry for Economic Affairs and Energy (BMWi). EDEKA is making a valuable contribution ahead of the market launch Andreas von Wallfeld, Head of Marketing, Sales and Services for Mercedes-Benz Trucks: "We are delighted that EDEKA – a long-standing customer – is now also testing the eActros. Thanks to their practical deployment of the eActros, EDEKA is making a valuable contribution to the truck's further development ahead of its market launch. It goes without saying that we are very thankful to the retail association for their active support. Our previous results from numerous tests have been nothing less than very positive. The 200 km range, for example, is totally realistic, and the cooling and air-conditioning systems have performed well, even during this year's record-hot summer." "We would also like to thank the German Federal Ministry for the Environment and the Federal Ministry for Economic Affairs and Energy for their support in developing and testing our eActros fleet as part of the funding project," continues Wallfeld. Future technologies play a key role for EDEKA EDEKA itself is also eagerly awaiting the results of the on-road testing: "Being involved with future technologies plays a key role for EDEKA as a driver of innovation in the retail sector," affirms Rolf Lange, Head of Corporate Communications at EDEKA's Hamburg headquarters. "We are already committed to reducing emissions in many areas – particularly when it comes to logistics. This is where electric mobility comes in as it presents many opportunities but also poses several challenges. We look forward to gaining valuable experience with this on-road test in Berlin." Removable container with electric cooling unit from Schmitz Cargobull The removable container on the eActros used by EDEKA is the "W.KO COOL" model supplied by Schmitz Cargobull. It has optimum insulation for energy-efficient transport of refrigerated goods. This robust body is ideally suited for intensive day-to-day use. Cooled entirely by electricity, the cooling unit is totally emission-free and is specially designed for use in distribution transport. "Electric mobility for commercial vehicles is a highly significant topic that opens up new opportunities. We will utilize them with our refrigerated unit. We can gain valuable experience on the critical factor of shared energy management between the truck and cooling unit through joint testing with Mercedes-Benz Trucks," says Boris Billich, Member of the Board of Management for Sales at Schmitz Cargobull. eActros replaces conventional diesel-powered trucks The first eActros of the "innovation fleet" has been in service at a customer since September. The rest of the first phase of vehicle hand-overs will be completed by the end of the year. All test customers operate in short-radius distribution and use the eActros for tasks which would otherwise be carried out by conventional diesel vehicles – the customers cover a broad spectrum of different sectors and categories. The palette ranges from food to building and industrial materials. The bodies vary from refrigeration units to dry containers, silos or tarpaulin-covered units. The eActros: architecture based entirely on electric drive The eActros is based on the frame of the Mercedes-Benz Actros. Also, the eActros means architecture based entirely on electric drive with a large proportion of specific parts. For example, the drive axle is based on the ZF AVE 130, which has proved its worth in hybrid and fuel cell buses from Mercedes-Benz and has now undergone a major modification for the eActros. The drive comes from two electric motors near the wheel hubs on the rear axle. Their output is 126 kW each, and the maximum torque is 485 Nm each. Downstream of the transmission that is 11 000 Nm each. The driving output is therefore on a level with a diesel truck. The maximal permitted axle load is the usual 11.5 tonnes. The energy is stored in lithium-ion batteries with a capacity of 240 kWh. Depending on the available charge, fully charging takes between two and eleven hours (at 150 or 20 kW). Daimler commercial vehicles with an extensive electric portfolio Daimler has had experience of working with electric trucks since 2010 and since last year its first fully electric series production truck has been on the market and used by customers: the lightweight Fuso eCanter truck. In the bus sector, the first Mercedes-Benz eCitaro will be delivered from the end of the year and will go into operation in so-called customer-related test-driving. In the van sector, the eVito from Mercedes-Benz Vans has been available for pre-ordering since November 2017 and the first deliveries are due very soon. In 2019 the eSprinter will follow. The vehicles from Daimler Trucks, Daimler Buses and Mercedes-Benz Vans thus cover the entire range of urban traffic with electric vehicles. . .
-
DAF Trucks Press Release / October 24, 2018 "We are getting 7.2% better fuel economy than the previous model, so we are very, very happy!" .
-
Paccar (PCAR) today set a new 52-week low of $54.87, despite a 35 percent increase in net income. Volume was two and a half times normal.
-
Ford will halt production Spain for nine days due to low demand Reuters / October 23, 2018 MADRID -- Ford will stop car production in its plant in [Valencia] Spain for nine days during November due to a lower demand for its vehicles. Engine production will also be halted for 13 days next month, a company spokesman said. Part of the Spanish production of Ford engines is sent to Canada for assembly of its Edge model. The latest production shut down comes after a three-day halt in October. Ford employs some 7,500 workers at the plant in Almussafes near Valencia. The factory builds about 1,840 cars a day. The vehicles produced are the Mondeo midsize car, S-Max and Galaxy large minivans, Kuga SUV, Tourneo Connect van and Transit Connect van. .
-
Ford appoints new China CEO, elevates China to stand-alone unit Automotive News & Reuters / October 23, 2018 Ford Motor Co said late Tuesday it appointed a new head of its China operations to help turn around flagging sales in the world's largest auto market and fill a post vacated when the firm's previous China head abruptly stepped down in January. The U.S. carmaker said in a statement that Anning Chen, a former Ford executive with 25 years of industry experience, would become the new CEO and president of Ford China. The move is effective Nov. 1. Ford China would also be elevated to become a stand-alone business unit, reporting directly to global headquarters. Chen previously served as CEO, Chery Automobile Ltd., and was chairman of the board at Chery Jaguar Land Rover, Automotive, China. In the statement, Ford also announced: Plans to increase local production for Ford and Lincoln; Details on significant investments in China-led engineering and r&d; The creation of a new single sales and service channel; A new joint venture with Zotye for a new line of small battery-electric vehicles; A strategic alliances with Baidu and Alibaba to explore areas of cooperation in AI, connectivity and digital marketing. .
-
The Dow is down 550 points this morning. There is a distinct possibility that this is the prelude to a global market crash alike 2008.
-
Speaking of the widely shunned “Davos in the Desert” Saudi investment conference in Riyadh that Bill Ford will not attend, hackers took over the main website and placed an image of the Saudi-murdered Khashoggi on the home page.
-
Scania Group Press Release / October 22, 2018 Scania’s fire tanker truck set to combat forest blazes. The worst-ever forest fires that raged in Sweden this past summer have highlighted the need for fire fighting vehicles that can manoeuvre in rough terrain. The Eksjö Rescue Services in southern Sweden have recently taken delivery of a Scania XT P 370 fire tanker truck expressly designed for operations in dense forests. VIDEO: Click here to watch the fire truck in action Built on a standard XT 6×6 chassis, the durable truck features a water tank with the capacity to hold 6,000 litres. “What distinguishes this truck is the flexible attachment between the frame and body in order to cope with the uneven movement in terrain,” says Johan Sand at the Atteviks Scania dealership. “With a rigid attachment, the tanks might crack. It has also been equipped with heavy-duty threaded off-road terrain tyres.” Versatile army veteran The Eksjö rescue services previously had an ex-army Saab-Scania SBAT 111S 6×6 tactical truck – the acronym for Special Bulldog Allwheeldrive Tandem – from 1976, first on loan and subsequently donated by the armed forces. “That was a really great truck in terrain but it was dated after 42 years and spares were increasingly difficult to obtain,” says Micael Carlsson, Head of the Eksjö Rescue Services. Carlsson’s aim was to replace the vintage truck with a modern fire fighter. “However, we didn’t have the budget for a customised vehicle and were looking at meeting our requirements using off-the-shelf components.” Following discussions with the Scania dealership, a special-order chassis was designed using standard components with bodywork by Sala Brand. “We’ve not yet actively used the vehicle but our staff has trained with the new truck,” says Carlsson. “It performs almost as well as the SBAT with another level of comfort and safety.” Handling with care The Eksjö area was luckily spared from forest fires last summer but the firefighting crews were kept busy in neighbouring areas and in battling major fires elsewhere. “We stand ready to assist others with firefighting resources but I don’t think that we’ll be taking the truck on the road; with these tyres, it a bit unsteady on tarmac. Besides, we need to take more care when handling this truck. A few more scratches here and there on the army truck really was of no concern.” The Scania XT truck seats two but the Eksjö Rescue Services have other personnel carriers for crews. “The real advantage is not having to pull hose as far when establishing firebreaks.” “Considering payload, we could have built larger volume tanks but that would have adversely affected manoeuvrability in terrain. And 6,000 litres are normally adequate when spraying for firebreaks, usually using no more than 100 litres per minute.” .
-
Ford Ranger won't cannibalize F-150 sales, Hinrichs says Michael Martinez, Automotive News / October 22, 2018 DETROIT — Ford Motor Co. doesn't believe the midsize Ranger will steal much business from its profit-generating full-size F-series trucks when the smaller pickup returns to North American showrooms early next year. "There always will be some substitution, but this is more of a lifestyle vehicle for people who want to use it for different purposes," Joe Hinrichs, Ford's president of global operations, said Monday at an event celebrating the Ranger's expected start of production here next week. "The F-150's gotten bigger over time and more expensive. We believe there's room now to slot the Ranger in very nicely in the showroom." Hinrichs said the first Rangers should be available to buyers in January 2019. Ford recently retooled its Michigan Assembly Plant in the Detroit suburb of Wayne, Mich., to build the pickup and, in 2020, the resurrected Bronco SUV. Some workers in the body, paint and stamping sections of the plant have already returned to work. Final-assembly workers will return next week, Ford said. The revived Ranger will start at $25,895, including shipping, and will top out at more than $40,000. That's about the same as the segment-leading Toyota Tacoma, which starts at $25,400 for 2018 models, but more than the Chevrolet Colorado and GMC Canyon. Pricing on the 2019 Colorado starts at $21,495, while the 2019 Canyon starts at $23,095. The Ranger's turbocharged 2.3-liter four-cylinder engine will be able to tow and haul more than the V-6 gasoline offerings from its rivals, Ford says. It will come in three trim levels: XL, XLT and Lariat. Ford will sell two-door SuperCab and four-door SuperCrew configurations and offer two-wheel drive and four-wheel drive for each configuration. An off-road FX4 package will be offered on all 4wd models. The Ranger was discontinued in the U.S. in 2011 but has continued to sell in a number of overseas markets. The latest U.S. version, to be built at Ford's Michigan Assembly Plant, has a mostly steel body, axles made by Dana Inc. -- which supplies the Jeep Wrangler -- and an exterior design similar to its larger F-series counterparts. The previous U.S. Ranger was regularly among the segment's top sellers, including No. 1 as recently as 2004. Ranger sales routinely totaled more than 300,000 a year in the 1990s before fading in the early 2000s. However, interest in the midsize pickup segment has rebounded. It's up 18 percent so far this year after rising less than 1 percent in 2017. "We're very excited about the growth we're seeing in the midsize segment," Hinrichs said. "We believe bringing back the Ford Ranger will add to that excitement and get more interest in that segment." .
-
Ford's Hinrichs says Trump tariffs make U.S. steel costliest in the world Keith Naughton & Joe Deaux, Bloomberg / October 22, 2018 ETROIT -- Ford Motor Co. is escalating its criticism of the Trump administration’s metals tariffs that the company has already said took a $1 billion bite out of profit. “U.S. steel costs are more than anywhere else in the world,” Joe Hinrichs, Ford’s president of global operations, said Monday at an event marking the start of Ranger pickup production at a factory west of Detroit. He added that Ford is talking to the administration about the tariffs. “We tell them that we need to have competitive costs in our market in order to compete around the world.” Ford CEO Jim Hackett last month called on President Donald Trump’s administration to resolve trade disputes quickly, warning that it would otherwise do “more damage” to the second-largest American automaker. He said the company sustained the roughly $1 billion hit to profit despite the fact that it sources most of the materials from the U.S. Domestic hot-rolled coil -- the benchmark price for American-made steel -- has gained 28 percent in 2018 as the Trump administration implemented tariffs on imports. The levies helped push the price to about $920 a metric ton earlier this year, the highest in a decade. U.S. steel currently costs about $150 more per metric ton than steel in China, the world’s biggest consumer, which accounts for more than half of global demand. .
-
Navistar Press Release / October 22, 2018 LISLE, Ill.-- Navistar has launched the Navistar Service Essentials Program, a partnership program designed to help qualified technical schools prepare the next generation of truck and bus technicians. "As we focus on growing customer Uptime, Navistar and our International Truck and IC Bus dealers are all committed to combating the industry's growing technician shortage," said Michael Cancelliere, Navistar president, Truck and Parts. "The new Navistar Service Essentials Program provides software and other solutions that will enhance the learning experience and attract additional students." The program's offerings include a wide array of interactive training courses and software solutions that cover engine diagnostics, vehicle health reports, electrical systems and control module programming. The program also provides access to informational tools related to parts and service. The Navistar Service Essentials Program is being made available to technical schools that partner with International Truck or IC Bus dealers. "We believe that students benefit the most when their technical schools have partnerships in place with dealers who are focused on driving Uptime every day," Cancelliere said. "That's why Navistar, our dealers and technical schools are establishing a three-way partnership committed to back up this new program with real-world, practical experience. This approach will accelerate progress and put more students on a path to enter this vibrant and essential technology profession." For an application or more information, technical schools can contact Navistar at oncommandsubscriptions@navistar.com or by calling 1-800-336-4500, option 4.4. For information on vocational school accreditation, please visit aseeducation.org/.
-
Nick Carey, Reuters / October 22, 2018 Tesla CEO Elon Musk put electric heavy commercial trucks on the map in November 2017 when he unveiled the company’s futuristic, battery-powered Semi, booked hundreds of orders and said he would start delivering the vehicles by 2019. Now, it looks like 2020 could be the big year for electric big rigs. Incumbent truck makers are accelerating their electric truck projects toward launches that year, while Musk told investors in June production of the eye-catching Semi freight hauler should begin “basically (in the) first half of 2020” instead of 2019. Driven by regulatory pressure to cut diesel pollution, commercial truck makers have made a flurry of fresh announcements to deliver battery electric or hydrogen-fueled vehicles. They have landed orders from big fleet operators such as Walmart, United Parcel Service (UPS) and Anheuser Busch Inbev NV. The challenge is gauging how big the market for electric commercial trucks will be, especially outside of China. The limited range of most first-generation electric or hydrogen commercial trucks and a lack of charging infrastructure threaten to limit sales to short-haul operations. In China, regulators are considering a long-term plan to replace 1 million diesel big rigs with cleaner trucks, including electric models, and some Chinese ports and cities are banning diesel trucks, which could [will] significantly boost sales. In the United States, the outlook for electric truck demand is cloudier. Some analysts estimate that by the mid-2020s, U.S. annual electric truck sales may number only in the hundreds. Over the last 12 months, North American diesel and so-called semitruck orders totaled 497,000 units. Toyota’s experience at the Ports of Los Angeles and Long Beach illustrates the potential, and the problems for clean truck technology. The first of Toyota’s working hydrogen fuel-cell trucks was designed with a 200-mile (322 km) range for daily operations and has already logged more than 10,000 miles running short routes around the ports. The newer second iteration has a 300-mile range but that is still well short of the 1,000 miles or more diesel trucks can run between refueling stops. Toyota has not provided a production timeline, but executive program manager Chris Rovik said “so far we feel confident the technology is absolutely applicable to this type of use case.” Fueling infrastructure is a major headache for electric and hydrogen trucks. Hyundai commercial vehicle director Mark Freymueller describes a chicken-and-egg problem: Trucking companies are reluctant to buy trucks without fueling stations, but fuel station operators will not install them without trucking customers. Battery electric trucks can take hours to recharge and charging stations are scarce in most U.S. states. Hydrogen trucks can be refueled in about the same time as a diesel truck - but hydrogen refueling stations are even rarer, with most concentrated in California. “Fueling infrastructure is a very important first step,” said Chris Cannon, chief sustainability officer for the Port of Los Angeles. “The trucks may work great, but if they can’t get any fuel they can’t operate.” Last month, the California Air Resources Board (CARB) announced $41 million in grants to the port toward building 10 new hydrogen fuel-cell electric trucks to be developed by Toyota and Paccar unit Kenworth. The grant will also partly-fund two new hydrogen fuel stations to be built by Royal Dutch Shell Plc. Most manufacturers see short-haul routes such as drayage services to or from ports or rail yards as likely first adopters of electric or hydrogen trucks. “We think the first applications are going to be shorter haul,” said Denny Mooney, Navistar International’s vice president of engineering. “We’re going to start out where the business makes sense.” Tesla customers like Deutsche Post unit DHL, which has ordered 10 Semis, say they could save tens of thousands of dollars on maintenance and fuel annually. CEO Musk says the Semi’s range could hit 600 miles. But a spokesperson said running uphill with air conditioning on or running other appliances would cut that range. Many modern 18-wheelers contain televisions, fridges and other appliances. Package delivery giant UPS has pre-ordered 125 Tesla Semis and will use them on daily routes hauling packages between hubs and on UPS Freight routes between businesses - mostly shorter routes. “In many ways we are ideally suited to be an early adopter of this technology because we don’t have much long-haul business,” said UPS spokesman Glenn Zaccara. Tesla is working with potential customers including UPS, Pepsico and Anheuser-Busch to build charging stations at their facilities. Nikola Motor Co, a startup offering a fuel cell truck, has ambitious multibillion-dollar plans to build 700 U.S. hydrogen fueling stations over the next decade, starting along the major routes of Anheuser-Busch, which has ordered up to 800 trucks, says CEO Trevor Milton. Nikola has secured funding for those stations, he said.
-
Roger Nielsen, President and CEO - Daimler Trucks North America (DTNA) / September 21, 2018 At DTNA, along with our recent advancements in e-mobility and connected services, we’re also focusing on automated driving, an important third pillar of our technology strategy. Soon, we’ll be expanding our team and facilities by opening a new Automated Truck Research & Development Center in Portland, Oregon, near our headquarters. Here’s a quick look at our ongoing, expanding efforts into the leading edges of automated vehicle technology. If you have an engineering background and a desire to change to world with innovative new technology, send a resume and letter of interest to innovateDTNA@daimler.com, but here’s more. With heavy investments in both our new Automated Truck R&D Center in Portland, Oregon and our High Desert Proving Grounds in Madras, Oregon, we’re creating global hotspots of emerging technologies and innovation, zeroing-in on freight efficiency, safety, and driver experience. Our engineers in North America collaborate closely with colleagues around the world at Daimler Trucks locations in Stuttgart, Germany and Bangalore, India to form a global network of hundreds of engineers devoted to advancing automated driving technology. We leverage this depth and breadth of experience across Daimler’s vehicle divisions to include both commercial vehicles and passenger cars. As we make progress with automated trucks, we’ve been testing them on our state-of-the-art test tracks and on Oregon highways. In June, we demonstrated automated driving through vehicle pairing, incorporating advanced, vehicle-to-vehicle communications between two trucks and showcasing our high-tech safety systems. Paired vehicles essentially 'talk' to each other, collecting information such as position, speed, and braking status 50 times every second. As a result, trucks in an automated pair can respond to each other in coordinated fashion, much faster than a human. This allows the vehicles to travel safely at a close following distance, thereby reducing fuel consumption. To help us prepare for new levels of automation, our Data Collection Truck (pictured above) aggregates immense troves of real-world data from a range of sensors. Dozens of test runs have provided a wealth of data that help us adapt as we move forward with our typical, micron-level attention to detail. We’re not just developing technology for technology’s sake, though. Our new Automated Truck R&D Center is a hub for co-creation where customers, suppliers, and business partners alike can provide input that deepens our understanding of how this technology can help our customers increase their profitability. Our eyes are on the bottom-line impact—not just for our customers, but for society at large. That means safety and reliability come first, as always, and automated driving systems are no exception. Drivers remain at the center of any new development – even of a truck featuring highly automated driving technology. The opinion that the technology will not replace drivers was further validated by findings from a recent study, Preparing the Workforce for Automated Vehicles, conducted by the American Center for Mobility—a non-profit testing and product-development facility for future mobility. We’re not going it alone, either. We’re collaborating with other industry experts to help ensure that we’re at the forefront of the discussion of how the advancement of automated vehicles will impact safety, quality of life, and economic opportunity. Daimler has teamed up with the American Trucking Associations, FedEx, Toyota, Ford, Uber, Waymo, and Lyft to found the Partnership for Transportation Innovation & Opportunity (PTIO). Committed to collaborating with American workers, policy makers, and customers to find solutions through the common-sense adoption of automated driving technology, PTIO creates a powerful alliance for collaboration on the future of automated vehicles. Only through examining, listening and understanding potentially disruptive new technology from every angle can we remain responsible global stewards, as we develop and commercialize groundbreaking new tech. .
BigMackTrucks.com
BigMackTrucks.com is a support forum for antique, classic and modern Mack Trucks! The forum is owned and maintained by Watt's Truck Center, Inc. an independent, full service Mack dealer. The forums are not affiliated with Mack Trucks, Inc.
Our Vendors and Advertisers
Thank you for your support!