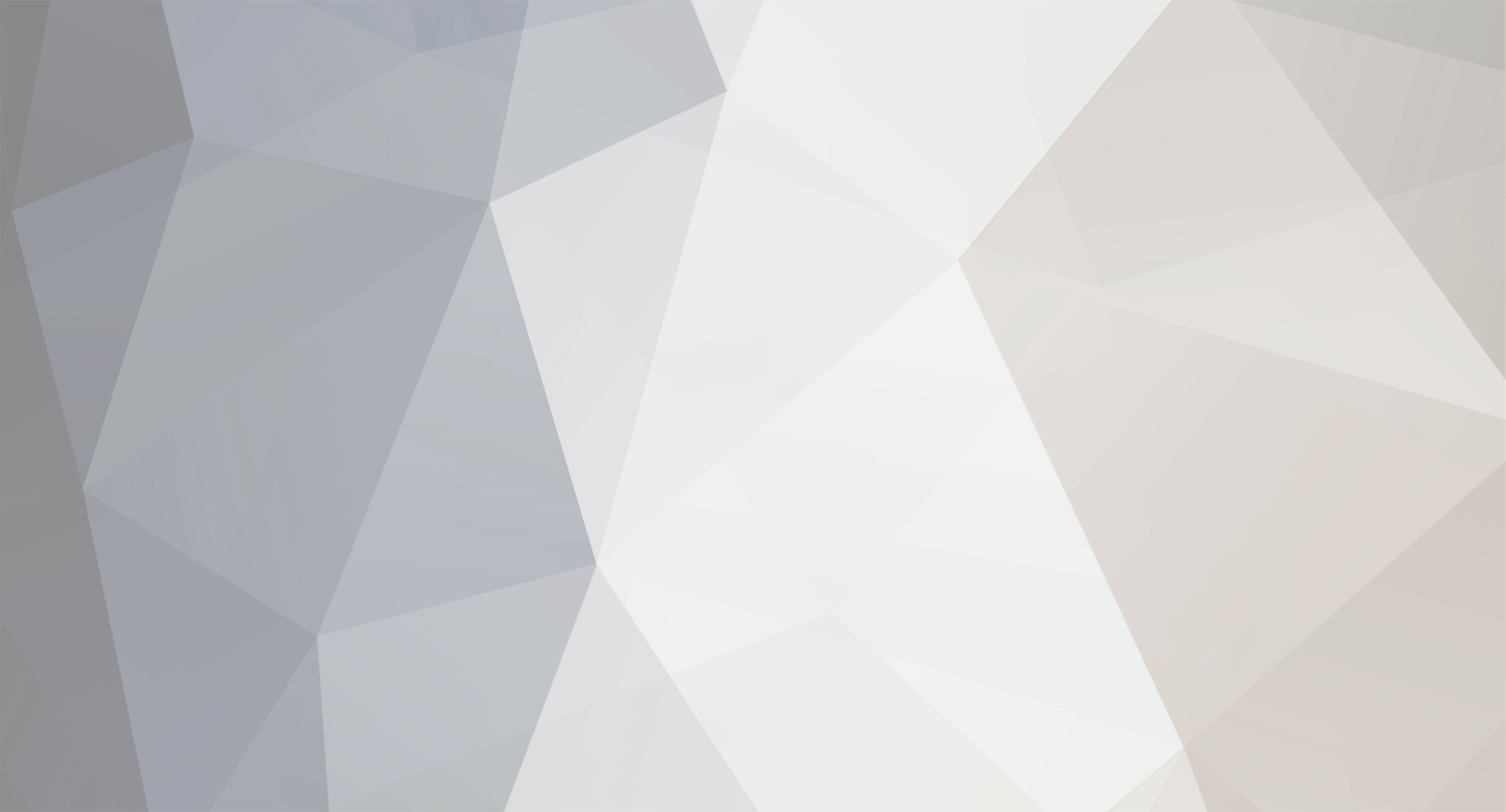
kscarbel2
Moderator-
Posts
18,750 -
Joined
-
Days Won
114
Content Type
Profiles
Forums
Gallery
Events
Blogs
BMT Wiki
Collections
Store
Everything posted by kscarbel2
-
International Launches MV Series Class 6/7 Truck
kscarbel2 replied to kscarbel2's topic in Trucking News
By cooperating with Isuzu and Navistar, GM has successfully re-entered the commercial truck segment, with a broad portfolio, without spending any serious money. They have both bases covered, low cab forward as well as conventional cab configurations. And, they offer both gasoline and diesel. However.......... GM's trucks should be under the GMC brand if only under one brand. Most Chevrolet dealers don't know how to professionally sell commercial trucks. GM, like Ford, rates a 1 on a 10 scale in sales marketing (promotion). -
International Launches MV Series Class 6/7 Truck
kscarbel2 replied to kscarbel2's topic in Trucking News
-
Josh Fisher, Fleet Owner / March 7, 2018 SG102 Dump Truck Pump offers high performance in a compact design. Parker Hannifin unveiled a smaller, more powerful dump pump that provides a significantly faster dump cycle that the company says will yield a greater work cycle efficiency. A two-story cylindrical curtain dropped in the middle of the NTEA Work Truck Show exhibition floor to reveal the SG102 Dump Pump on Wednesday. Building upon the technology of the industry standard C102/G102 pumps, the SG102 Dump Pump provides a 37% faster dumping cycle versus the standard G102, according to Dean Jickess, the business development manager at Parker Hannifin. “We believe that this new cylinder along with the Parker system will greatly increase the value that Parker has to offer in the truck market,” Jickess said. The pump is designed to fit where space is limited and greater flow is necessary. The SG102 Dump Pump provides 25% more flow than the G102 2-inch Dump Pump, and weighs 20% less than the C102 2.5-inch Dump Pump. It uses the valve body of the larger frame size C Series Dump Pump, which provides large dump pump flow characteristics for a faster dump cycle time yielding greater work cycle efficiency. The SG102 can be configured in SAE or DIN flange, NPT or ODT ports, and can be ordered with manual or air shift configurations. “With the evolution of truck chassis and exhaust systems, there’s less space available under the truck to mount these pumps,” said Chris Johnson, sales channel manager of Parker Gear Pump Division. “So you may have an application where the larger-framed C series doesn’t fit. The G series does fit but still there’s a requirement from the user for greater flow.” That is where the new SG102 comes in. “The dump truck industry will see benefits from the pump’s power density,” Johnson said. “There is also safer operation when the cycle time for the bed to return is reduced prior to the operator moving from the job site location.” Johnson said the industry will benefit from the improved power density and safety as the dump bed returns to the lower position much faster. “We’re giving you a system that’s stronger with the strength of the new cylinder and the new SG series,” said Jeff King, marketing manager at Chelsea Products Division. The SG102 Dump Pump is on display in the Parker booth (No. 3011), at the NTEA Work Truck Show, through Friday, March 9, at the Indiana Convention Center. .
-
Sean Kilcarr, Fleet Owner / March 7, 2018 ATLANTA. As Class 8 orders remain elevated – they exceeded 40,000 units in February, according to analysts – truck maker Navistar is seeing “fairly equal and constant” for both sleepers and daycab models, according to Michael Cancelliere, the company’s president of truck and parts. “We’re also seeing customers spec’ing a lot of safety equipment, with fuel efficiency remaining a hot topic,” he explained to Fleet Owner here during a press conference at the Technology & Maintenance Council (TMC) 2018 annual meeting. “And with the driver shortage situation currently being experienced by the industry, there is more focus on getting a truck that appeals to them.” Cancelliere added that Navistar’s heavy focus on vehicle uptime plays into that as well, as a driver’s time is now more fixed due in part to the electronic logging device (ELD) mandate that went into effect last December. “This focus we have on uptime; it’s not new to us or to the industry, but the urgency for uptime is far greater now,” he said. “It’s not just about improving the planning for scheduled maintenance it’s about better handling for unplanned maintenance as well. With [truck] capacity now more limited, a vehicle up and running on the road is making more money for the fleet and the driver.” Parts availability an important piece of that uptime puzzle, Cancelliere said, and it’s one reason why Navistar is revamping its Fleetrite private parts label operation and its ReNEWed remanufactured components business. “Uptime is at its heart really all about parts and service – it’s about closing the support loop between the customer and the dealer,” he said. Josef Kory, Navistar’s senior vice president for parts, noted that ReNEWed and Fleetrite offer in combination more than 100 product lines, giving customers alternatives when it comes to repairs and maintenance, lifecycle value, and total cost of ownership. “Our parts business has delivered double digit growth over the past five years, and much of that success is due in large part to our commitment of providing customers the right products to support our dealers' and customers' needs,” he said. Currently, the OEM offers over one million parts through seven distribution centers located around the U.S. that support its network of 700 International Truck-branded dealership locations. Navistar is also “re-branding” its ReNEWed remanufactured parts business with a new logo that will debut later this spring and is planning to add more products to its lineup this year, Kory noted – starting with the OEM’s 2015 model N13 engine and the 2010 through 2016 models of its I6 engine, as well as expanding its portfolio of remanufactured electronic components such as engine control modules, instrument clusters and body controllers. Fleetrite is also expanding with addition of a comprehensive all-makes radiator and surge tank program. Added to its all-makes collision parts program launched in early 2017, the Fleetrite private label parts band now offers product coverage for 24 makes and models covering 80% of the vehicles on the road, Kory said, with future efforts focused on adding bumpers, hoods, grilles and headlights to its portfolio to keep help customers lower their operating expenses. “We’re also using our OnCommand Connection [telematics] system to provide terabytes and terabytes of data to us to improve our products,” he added. “We’re using that data to help us forecast what kinds of parts are in demand so we can better fulfill our focus on providing access to our stock within 24 hours or less.” Kory also noted that, earlier this year in partnership with an International Truck dealer, Navistar launched its second Fleetrite-specific parts store in Clearwater, FL, with the company planning to add more stories in 2018 and beyond. “To supplement our dealer locations, we want to continue to expand our regional and national footprint to ensure we are doing everything possible to meet our customers' needs with increased availability and faster delivery of quality products,” he said. .
-
International Launches MV Series Class 6/7 Truck
kscarbel2 replied to kscarbel2's topic in Trucking News
International unveils MV Series Trailer-Body Builders / March 7, 2018 International Truck launched its new Class 6/7 International MV Series at the 2018 Work Truck Show. The MV Series launch completes the company’s Project Horizon product refresh, and reflects that initiative’s improved cab design, along with the same driver-centric enhancements already launched in Class 8 vehicles. “Project Horizon was focused on delivering new levels of efficiency to customers, creating unparalleled driver satisfaction and leveraging the smartest technologies available,” said Michael Cancelliere, president, Truck and Parts. “The MV Series delivers on those promises by combining uncompromising reliability with enhanced productivity for the driver, maintainer and upfitter.” The MV Series was designed from the inside out with the goal of delivering a truck that is easily configurable to produce maximum output day in and day out. The redesigned features include new cab doors with a lower bottom glass edge and removed vent window, giving the driver a single large piece of glass to look through, greatly improving side visibility and reducing blind spots. By reshaping the doors and side glass, the position of the optional pedestal mirrors was optimized so drivers turn their heads less and keep their eyes on the road while reducing neck strain. Second, a new premium gauge cluster with a digital driver display was added to give drivers real-time monitoring of vehicle operation and other important alerts in clear sight. The new display also offers up to 15 customizable digital gauges. The new premium instrument panel features a customizable digital display suitable for any medium-duty application. The flat-panel dash contains space for up to 30 customizable switches ensuring functionality for any type of body that is mounted on the back. The switches offer large easy-to-read text and are back lit for easy viewing at night. Next, an easy-access column-mounted stalk shifter was integrated to help keep drivers’ hands on the wheel and eyes on the road. The new stalk shifter placement and the lower instrument panel design greatly improves leg room for the driver, especially at the knee. The MV Series is also equipped with a new best-in-class HVAC system, designed for reliability, which includes a high-performance MAX defrost feature. An additional vent has been added to help keep the middle front passenger comfortable. “The new International MV Series reflects our vision for the future of commercial vehicles with a host of advancements that support improved driver safety and productivity,” said Jeff Sass, senior vice president, Sales and Marketing. “We challenged ourselves to make the best even better and this new vehicle was designed to provide the best driver environment in the industry and we exceeded all of our targets.” To further improve driver productivity and safety, the MV Series features the best-in-class Diamond Logic, an advanced electrical system that streamlines chassis and body equipment integration and allows customers to program automated tasks. Equipped with the Diamond Logic electrical system, the MV Series will get the job done with both safety and precision by offering customers nearly 200 factory available body integration and driver efficiency features, plus the ability to customize infinitely more vehicle functions. “Our Diamond Logic electrical system is known for its ability to provide control and communication between trucks and body equipment,” said Sass. “We were a pioneer in custom programmable chassis electronics and multiplexing and we continue to partner with end users and body builders to further increase productivity and make it easy to integrate with our system.” Like all International models, the MV Series can be managed digitally through the OnCommand Connection platform, which features the company's leading-edge Advanced Remote Diagnostics system designed to enhance fleet efficiency, as well as Over-The-Air (OTA) programming through the nine-pin OnCommand LINK device, enabling drivers or fleet managers to utilize a mobile interface to initiate authorized engine programming at the customer's facility over a safe, secure Wi-Fi Connection. OnCommand Connection telematics, including telematics hardware and monthly data packages, are also available through International Truck dealers or through OnCommandconnection.com. “As a result of customer and Truck Equipment Manufacturer feedback during the design process, we have designed the MV Series to seamlessly integrate with any body solution,” Sass said. “This truck can be easily configurable for any application.” The MV Series was engineered to make it easier to maintain and get back on the road fast. When service is needed, customers can count on one of more than 700 International dealers with expert technicians and an extensive parts inventory throughout North America. The MV Series is available in a variety of specifications: Regular Cab, Extended Cab, and Crew Cab. It is available with the choice of either the Cummins B6.7 or L9 engine, both of which have been engineered for reliability and durability in order to deliver lower costs of ownership with maximum uptime. The standard transmission on the MV Series is the Allison 1000 HS automatic, with Allison FuelSense 2.0, with DynActive Shifting as an available option that features a patented torque converter to provide infinitely variable shift points based on vehicle configuration operating conditions. . -
Volvo makes enhancements to its Mack Granite
kscarbel2 replied to kscarbel2's topic in Trucking News
Volvo Adds More Configurations to Mack Granite MHD Truck Lineup Heavy Duty Trucking (HDT) / March 7, 2018 Mack Trucks has added new features to its Granite Medium Heavy Duty (MHD) truck, aimed at increasing its versatility and enabling more cost effective choices for customers that need a durable and light work truck. The enhancements include a new horsepower rating, under-frame exhaust system, a shorter wheelbase 4x2 configuration, and a tractor configuration to expand the applications coverage for the MHD. “Vocational customers have a wide variety of needs,” said Tim Wrinkle, Mack Trucks construction product manager. “Some require lighter weight options but still need their trucks to meet the difficult demands of the application. The MHD model delivers both without compromise.” The MHD, equipped with the Cummins L9 engine, now features a lower horsepower option, allowing customers to spec an engine with 330 horsepower and up to 1,000 ft.-lbs. of torque. The lower horsepower rating offers customers another option that may increase return on investment. A new under-frame exhaust gives customers more options for body adaptation, further expanding application capabilities, such as tankers, flatbeds, box trucks, cranes, and certain municipal applications. The MHD model can be spec’d as a Class 7 or Class 8 vehicle, is offered in either an axle back or axle forward configuration, and is available as a 4x2 or 6x4, offering customers the flexibility to choose between a heavy-duty and a lighter-weight medium-duty option. An axle back tractor option meets the needs of light tractor applications requiring maneuverability, flexibility, and durability without extra weight. A shorter wheelbase is also now available for the MHD model in the 4x2 configuration, ideal for the 10-foot dump body commonly used in municipal applications, and providing a more maneuverable, cost-effective option. . -
Truck News / March 7, 2018 INDIANAPOLIS, Ind. – With continued economic growth in the U.S. and truck sales surging, Mack Trucks announced a handful of enhancements to its products during the Work Truck Show today. Most notable was an increase in ground clearance in six inches to the Granite axle forward model underbody scrapers. The escalation in chassis ride height provides additional clearance enabling the scraper to have a full range of motion to move in excess of 45 degrees in both directions, making them a more versatile vocational offering for both winter and summer applications. “In the offseason, these trucks are clearing gravel off the sides of roads, so they are multi-functional,” said Tim Wrinkle, construction product manager for Mack, during the announcement in Indianapolis, Ind. “The increased ground clearance allows for easier plow installation without the need to move other chassis components like fuel tanks and exhaust aftertreatment systems, saving the customer both time and money. The new configuration also allows for a shorter wheelbase for greater maneuverability and decreased weight, offering customers a cost savings without compromising performance.” The increased clearance offers up to 21 inches of ground clearance for installation without relocating chassis components. It also maintains a 24-inch maximum first step height for no compromise to ingress or egress. The Mack Granite is available with both the MP7 and MP8 engines and the mDrive HD 14-speed automated manual transmission with creeper gears. The new heightened configuration will be available in the third quarter of this year. The Granite medium heavy-duty (MHD) model is also getting improvements. An additional lower horsepower rating of 330, a new under-frame exhaust system, shorter wheelbase 4×2 and 6×4 axle back or axle forward configuration, and all new interiors will be available on the vocational truck. “Vocational customers have a wide variety of needs,” said Wrinkle. “Some require lighter weight options but still need their trucks to meet the difficult demands of the application. The MHD model delivers both without compromise.” Wrinkle said the interior enhancements did not happen overnight. “We spent a lot of time researching and doing driver interviews to get this right,” he said. Coming with the Cummins L9 engine, the MHD lower horsepower option offers up to 1,000 lbs.-ft. of torque with the Allison 3500 transmission, gives customers the options for body adaptation with the new under-frame exhaust, such as tankers, flatbeds, box trucks and cranes, and can be spec’d as a Class 7 or 8 vehicle. The shorter wheelbase in the 4×2 configuration is ideal for a 10-foot dump body and provides better maneuverability. GuardDog Connect Mack Granite model trucks also come with GuardDog Connect, which has also seen some improvements of late. Mack’s proactive diagnostic and repair planning system, GuardDog Connect enhancement for uptime include a 50% increase in Mack OneCall staffing to assist customers with issues, a $2.5 million investment into technology for better data analytics and vehicle data, tripling the number of fault codes monitored, improved repair information in ASIST to speed repair, and Over the Air for remote repairs and parameter updates. “It’s a service, it is not a system,” said Roy Horton, Mack product strategy director, of GuardDog. “It’s about connecting the people with the technology.” Remote repairs with Mack’s Over the Air software and parameter updates have seen 20 customers, or 3,500 vehicles use the service since October 2017, averaging 23 minutes for an update, and saving more than 500 days of downtime. Horton said GuardDog Connect is the highest rated OEM uptime service in the industry, with 121,000 customer interactions last year. .
-
Heavy Duty Trucking (HDT) / March 7, 2018 International Truck launched a new medium-duty Class 6/7 vehicle called the MV Series at the 2018 Work Truck Show in Indianapolis, Ind. The MV Series was the final piece of International’s Project Horizon product refresh, reflecting the company’s initiative toward improved cab design and includes the same driver-centric features seen in the company’s Class 8 vehicles. “Project Horizon was focused on delivering new levels of efficiency to customers, creating unparalleled driver satisfaction and leveraging the smartest technologies available,” said Michael Cancelliere, president, truck and parts. “The MV Series delivers on those promises by combining uncompromising reliability with enhanced productivity for the driver, maintainer and upfitter.” MV Series Driver-Centric Design The MV Series was designed to be easily configured for the desired application. Features include new cab doors with a lower bottom glass edge and removed vent window, giving the driver a single large piece of glass to look through to improve side visibility and reduce blind spots. By reshaping the doors and side glass, the position of the optional pedestal mirrors was optimized so drivers turn their heads less and keep their eyes on the road while reducing neck strain. A new gauge cluster with a digital driver display was added to give drivers real-time monitoring of vehicle operation and other important alerts in clear sight. The display also offers up to 15 customizable digital gauges. The instrument panel features a customizable digital display which can be configured to suit the application. The flat-panel dash contains space for up to 30 customizable switches ensuring functionality for any type of body that is mounted on the back. The switches employ large text and are back lit for easy viewing at night. A column-mounted stalk shifter was integrated to help keep drivers’ hands on the wheel and eyes on the road. The new stalk shifter placement and the lower instrument panel design improves leg room for the driver, especially at the knee. The MV Series is also equipped with an improved HVAC system, designed for reliability, which includes a high-performance Max defrost feature. An additional vent has been added to help keep the middle front passenger comfortable. Diamond Logic and OnCommand Connection The MV Series also features Diamond Logic, an electrical system that streamlines chassis and body equipment integration and allows customers to program automated tasks. Through Diamond Logic, the MV Series offers customers nearly 200 factory available body integration and driver efficiency features, plus the ability to customize infinitely more vehicle functions. “Our Diamond Logic electrical system is known for its ability to provide control and communication between trucks and body equipment,” said Jeff Sass, senior vice president, sales and marketing. “We were a pioneer in custom programmable chassis electronics and multiplexing, and we continue to partner with end users and body builders to further increase productivity and make it easy to integrate with our system.” The MV Series can also be equipped with the OnCommand Connection platform which features an advanced remote diagnostics system as well as over-the-air programming that allows drivers sand fleet managers to initiate authorized engine programming over a secure Wi-Fi connection. OnCommand Connection telematics, including telematics hardware and monthly data packages, are also available through International Truck dealers or through OnCommandconnection.com. Designed for Upfitting “As a result of customer and Truck Equipment Manufacturer feedback during the design process, we have designed the MV Series to seamlessly integrate with any body solution,” said Sass. “This truck can be easily configurable for any application.” The MV Series is available in a variety of specifications: regular cab, extended cab, and crew cab. It is available with the choice of either the Cummins B6.7 or L9 engine. The standard transmission on the MV Series is the Allison 1000 HS automatic, with Allison FuelSense 2.0, with DynActive Shifting as an available option that features a torque converter to provide variable shift points based on vehicle configuration operating conditions. International is currently taking orders for the MV Series, and market availability is slated for spring 2018. .
-
Hino Enters Heavy Duty Market with XL Series Truck
kscarbel2 replied to kscarbel2's topic in Trucking News
Hino getting into Class 8 market in North America Truck News / March 7, 2018 INDIANAPOLIS, Ind. – Hino Trucks today announced its all-new XL Series line of Class 7 and 8 vehicles at the Work Truck Show in Indianapolis, Ind. The Hino XL7 and XL8 2020 models – which will begin production in early 2019 – are equipped with the company’s A09 turbo diesel 8.9-liter inline 6-cylinder engine with a B10 life of one million miles. Yasuhiko Ichihashi, chairman of Hino Motors Ltd., said during the unveiling that both models were extensively tested in both Canada and the U.S. Hino Trucks North America president and CEO Yoshinori Noguchi said the time was right for the company to enter the Class 8 market in North America. “Considering our remarkable success in Class 4-7 in North America and our growing global presence in the Class 8 market, entering the North American heavy-duty segment makes for the next logical step,” said Noguchi. “No to mention, our customers and our dealer network have been asking for this for some time.” Hino XL Series trucks will be available in a variety of straight truck and tractor configurations, including from a GVWR of 33,000 lbs. to 60,000 lbs. and a GCWR up to 66,000 lbs. It will have a max performance of 360 hp with 1,150 lbs.-ft. of torque, and have wheelbase selections of up to 304 inches, and tandem axle and fifth wheel configurations. On the safety side of things, there is electronic stability control, which comes standard on the tractor, collision mitigation systems, payload management suspension options, a body designed for ease of serviceability. “The first thing you notice is the styling – the aerodynamic yet bold design could proudly represent your business,” said Glenn Ellis, vice-president of customer experience with Hino. “They you open the door to a wide, easy-access entry and an automotive grade finished interior ready to provide the best service possible to drivers and teams.” For driver comfort, Hino XL Series trucks also come with air-ride cab and driver’s seat, hands-free Bluetooth, steering wheel controls, cruise control, and air conditioning. The company also announced it will expand its U.S. operations with the purchase of the Cold Water Creek distribution center in Mineral Wells, WV, where the Hino XL7 and XL8 will be assembled. . -
Chevrolet Debuts Three Medium-Duty Trucks Heavy Duty Trucking (HDT) / March 7, 2018 Chevrolet has unveiled three Silverado HD chassis cab trucks — the 4500HD, 5500HD, and 6500HD — that expand its commercial lineup and give Chevrolet a greater weight range of vehicles for fleet purchasers. Chevrolet first showed the vehicles today at the Work Truck Show in Indianapolis. "We see a great opportunity for us with this truck," Ed Peper, U.S. vice president of GM Fleet, told Work Truck. "In the six years I've been with General Motors Fleet, this is the single biggest launch we've had happen in our space. This has been a hole in our commercial portfolio, and we are excited to re-enter the market moving all the way up to Class 6." The trucks will now represent GVWs from 15,000 pounds in Class 4 to 22,900 pounds in Class 6. Chevrolet hasn't offered a medium-duty chassis cab truck since 2009. This is a "Silverado on steroids," according to the automaker. The trucks will be powered by a standard Duramax 6.6L turbo-diesel engine, which is the only engine available on the Silverado, and mated to a choice of Allison transmissions. The trucks will achieve 350 hp at 700 lb.-ft. of torque. They will be offered in seven wheelbase options, two trims (WT and LT), and a Crew Cab and Regular Cab variant, providing a number of available configurations for vocational fleet needs. A few special features include tilt hood, which will make maintenance a breeze. Sometimes referred to as a "clamshell" design, the hood is hinged at the front. The truck's hood and fenders all tilt forward nearly 90 degrees, giving the operator or tech full access to the engine compartment. Another key exterior aspect is in the center bar in the truck's grille. The bow-tie is open, allowing even more airflow into the engine compartment, just like the Chevrolet Camaro Z28. "On this particular truck, we've looked for as much feedback as possible and done more canvassing of stakeholders within the industry than anything we've ever done," Peper said. "We believe it's going to be a smashing success."
-
Heavy Duty Trucking (HDT) / March 7, 2018 Hino Trucks announced a new, larger lineup of Class 7/8 trucks called the XL Series which debuted at the 2018 Work Truck Show in Indianapolis, Ind. The Hino XL Series brings the company into the Class 8 market in the U.S. for the first time which the company characterized as the next step in expanding its presence in North America. “Considering our remarkable success in Class 4-7 in North America, and our growing global presence in the Class 8 market, entering the North American heavy duty segment makes for the next logical step. Not to mention our customers and our dealer network have been asking for this for some time,” said Yoshinori Noguchi, president and CEO of Hino Trucks North America. Both the XL7 and XL8 models are powered by Hino’s A09 8.9L inline 6-cylinder diesel engine and will be offered in both straight truck and tractor configurations. The different models will range from a GVWR of 33,000 to 60,000 pounds and a GCWR up to 66,000 pounds. Max performance will top out at 360 horsepower and 1,150 lbs.-ft. of torque. Available wheelbase selections of up to 304 inches and tandem axle, as well as fifth wheel configurations, are designed for a variety of vocational applications. The XL Series lineup features new active safety solutions with electronic stability control – standard on tractor models – and collision mitigation systems, payload management suspension options and a body builder optimized design that was engineered for better serviceability. Hino says that it also focused on the driver with good styling, ergonomics and amenities. It features a wide entry for easier access and what the company calls an automotive-grade finished interior. The XL Series will also feature air-ride cab and driver’s seat, hands-free Bluetooth audio/calling, steering wheel controls, LED headlights, cruise control, and air conditioning as standard equipment on every 2020 model year XL7 and XL8. Production of the XL7 and XL8 will start in early 2019 and the lineup will be assembled in Mineral Wells, W.Va., at a fully renovated 1 million square-foot production facility that Hino acquired in 2017. .
-
Chevrolet web page for the all-new 4500HD, 5500HD and 6500HD - http://www.chevrolet.com/upcoming-vehicles/all-new-silverado-chassis-cab
-
Chevrolet Unveils the 2019 Silverado 4500HD, 5500HD and 6500HD at NTEA The Work Truck Show General Motors Press Release / March 7, 2018 Chevrolet revealed its first-ever Silverado Class 4, 5 and 6 chassis cab trucks today at NTEA The Work Truck Show – three supremely capable conventional cab models will be the most customer-focused trucks of any major competitor. All-New Silverado conventional cabs will be the most customer-focused medium-duty trucks of any major competitor Easy to upfit: Clean, one-piece straight frame rails, seven Cab-to-Axle options Easy to drive: Excellent maneuverability, factory air suspension Easy to service: Lightweight clamshell hood allows "walk up" access to engine INDIANAPOLIS —Chevrolet revealed its first-ever Silverado Class 4, 5 and 6 chassis cab trucks today at NTEA The Work Truck Show – three supremely capable conventional cab models will be the most customer-focused trucks of any major competitor. “Chevy’s designers and engineers were obsessed with making this Silverado the most customer-focused medium duty truck of any major competitor,” said Ed Peper, U.S. vice president, GM Fleet. “By customer-focused, I mean work-ready trucks that are easy to upfit, easy to drive, easy to service and easy to own.” The Trucks Dealers, Customers and Upfitters Asked For The input of fleet managers, truck drivers, upfitters, technicians and Chevrolet dealers drove the development of the new Silverados. “It’s not just numbers on a spec sheet that make us different and better,” said John Schwegman, director of Commercial Product and Medium Duty at GM Fleet. “These new Silverados are designed to solve the most common upfit and ownership challenges fleets have with many of today’s medium duty trucks.” Challenge The Silverado Solution Cost and complexity of upfits: Frames that rust; rivets, brackets and fluid lines that interfere with body mounting. A factory-painted frame with one-piece frame rails, smooth, unobstructed top sections, and through-the-frame fuel fill lines. Frame compromises: Frame rails that are too short behind the rear axle to accommodate longer cargo boxes without extensions and reinforcements. Seven Cab-to-Axle (CA) options ranging from 60 to 162-inches, along with five unique axle-to-back-of-frame (AF) lengths sized in 8-inch increments. Service obstacles: Hood designs that force technicians to use ladders or remove vehicle components to access under-hood components for maintenance and repair. A lightweight, front-hinged “clamshell” hood that, combined with a 50-degree wheel cut, allows easy “walk up” access to under-hood components. Difficult to drive: Poor downward perspective for the driver, along with poor low-speed maneuverability due to narrow wheel cuts, and wide turning radiuses. A precisely crafted and contoured hood optimizes the driver’s perspective of the road. Maneuverability is excellent thanks to up to 50-degree wheel cuts. Noise, Vibration and Harshness: The need to retrofit aftermarket air suspensions to improve ride; loud, uncomfortable cabins. An available, factory-installed rear air suspension, not on Ford and Ram; triple-sealed, inset doors to help reduce wind and road noise; huck bolts used throughout the frame for superior clamping force. DEF tank placement: Poorly-placed and marked diesel exhaust fluid (DEF) tanks that can lead to refueling errors. The DEF tank is conveniently located on the passenger side of the truck – the opposite side of the fuel fill. Proven Power The Silverado will be available in 2WD and 4WD and will be powered by a 6.6-liter Duramax diesel engine with 350 horsepower and 700 lb.-ft. of torque and Allison transmissions with a Power Take Off (PTO) option. “When you consider all of the flexibility, capability and durability we have engineered into the Silverado, along with the proven power of Allison transmissions and the Duramax diesel engine, we have a medium duty truck line that will appeal to both Chevrolet loyalists and competitive owners alike,” said Schwegman. The Most Connected Medium Duty Truck The Silverado will also be the most connected commercial truck available, thanks to options that include OnStar and Commercial Link, a built-in 4GLTE Wi-Fi hotspot (paid data plan required), wireless cellphone charging, Bluetooth and support for Apple CarPlay and Android Auto. Production and Ordering Production of the new Silverado begins in late 2018. Order guides will be available this spring and pricing will be announced this summer. More than 400 commercially-focused Chevrolet dealers are expected to carry the new Silverado line. GM Fleet Momentum The launch of the All-New Silverados will build on the momentum Chevrolet and GM Fleet have been building over several years. “Chevrolet’s return to the conventional cab medium duty segment is part of a multi-year strategy to earn the business and loyalty of Commercial and Government customers by expanding into new product segments, delivering innovative business solutions, superior value and an exceptional customer experience,” Peper said. In 2017, GM Fleet delivered nearly 300,000 units to Commercial and Government customers – the most since 2008 – and gained almost 1.4 percentage points of market share. Chevrolet has been the growth engine: Chevrolet’s three-truck pickup strategy, built around the Colorado mid-size pickup and the Silverado ½-ton and 1-ton models, has made General Motors the leader in pickup deliveries for four consecutive years. New dedicated Commercial and Government products, including the Colorado box-delete and Low Cab Forward, have helped turn the brand into a “one stop shop” for fleet managers and small businesses. Chevrolet has been the broadest portfolio of B20-capable diesel-powered cars, crossovers and trucks in the industry, including the Chevrolet Cruze, Equinox, Silverado 2500HD and 3500HD, Express, Low Cab Forward – and now the new Silverado in class 4,5 and 6 configurations. A very strategic and disciplined approach to the daily rental market helps to support resale values. “It’s a fact: The more choices we offer truck customers, the more we drive sales across our entire portfolio. That’s because brand and dealer loyalty run deep in this business,” Peper said. ABOUT CHEVROLET Founded in 1911 in Detroit, Chevrolet is one of the world's largest car brands, doing business in more than 100 countries and selling more than 4.0 million cars and trucks a year. Chevrolet provides customers with fuel-efficient vehicles that feature engaging performance, design that makes the heartbeat, passive and active safety features and easy-to-use technology, all at a value. More information on Chevrolet models can be found at www.chevrolet.com. .
-
Is This the New USPS Mail Truck? Car & Driver / March 7, 2018 The current mail truck—the slab-sided, sliding-door, ubiquitous yet invisible white box perpetually pulled off to the side of the road—will soon follow the postal Jeep to that great dead-letter office in the sky. The U.S. Postal Service is shopping for a new ride, and that means proposals for the new mail truck are out testing, including this one by Turkish truckmaker Karsan. Will this be the vehicle that, when it appears outside your window, has you sprinting to the mailbox to see what bills and junk mail have arrived? Maybe. Karsan is one of six manufacturers vying for the contract to replace the USPS’s aged Grumman/General Motors Long Life Vehicle (LLV) fleet, the newest of which is now 24 years old. Others participating in the Postal Service’s Next Generation Delivery Vehicle bid include Indian automaker Mahindra, South Bend’s AM General (of Hummer fame), Wisconsin’s Oshkosh (maker of MRAP military vehicles), Utilimaster from Indiana, and VT Hackney based in North Carolina. The USPS is said to be looking for a vehicle with more cargo space for bulky packages, and given how tiny the driver of this vehicle looks behind the enormous windshield, this Karsan appears to be much larger than today’s truck. Other requirements include a sliding driver’s-side door and right-hand drive. Photo gallery - https://www.caranddriver.com/photo-gallery/dorky-delivery-is-this-the-new-usps-mail-truck-gallery#1 .
-
Chevy expands Silverado medium-duty lineup in bid to outgun Ford, Ram Michael Wayland, Automotive News / March 7, 2018 INDIANAPOLIS -- General Motors' new Chevrolet Silverado medium-duty truck will compete in more segments than initially expected, a strategy coinciding with the automaker's plan to expand and improve its commercial dealership network. The automaker, when unveiling the vehicle at the Work Truck Show here Wednesday, said it will compete in Class 6 chassis cab trucks in addition to Class 4 and 5, which were previously announced. The addition helps expand GM's reach and differentiate it from competitors such as Ford Motor Co. and Fiat Chrysler Automobiles, according to executives. "This will be the biggest thing we've ever done for commercial," Ed Peper, U.S. vice president of GM Fleet, told Automotive News on the sidelines of the show. "I think it's a real inflection point in our business. This just says a lot about the support from our leadership and the resources that we're getting to continue to grow this business." Medium-duty trucks range from Class 4 through Class 6 based on gross vehicle weight ratings, which is the maximum operating weight/mass of a vehicle. The new Silverado has a max of 22,900 pounds, which reaches into the middle of the Class 6 trucks, where Ram does not compete, and Ford has a truck but on a different frame than its other medium-duties. "It's a different proposition in the market than what Ford and Ram have," said John Schwegman, GM's U.S. director of commercial product and medium duty. The trucks, which the company has said were built from the ground up and are not variants of existing trucks, are aimed at fleet and commercial buyers and can be upfitted with work-specific beds and boxes for work such as landscaping, emergency services, refrigeration and towing. GM expects to eventually gain upward of a 25 to 30 percent share of the medium-duty truck segment, which would equal its level prior to exiting the segment during the company's 2009 bankruptcy. "We're going to have to conquest largely from Ford, a little bit from [Ram]," Peper said. More important than the sales of the medium-duty segment is the adjacent sales, according to Peper. He said, "For every one of these trucks we sell, we think we're going to sell a van, we're going to sell a pickup and one of something else." The adjacent sales are expected to expand past vehicles to other business segments such as GM Financial, parts and accessories and OnStar, which offers a fleet service with tracking and diagnostic services called Commercial Link. Dealers The adjacent sales are a main draw for Chevy dealers. However, Schwegman said the company is being "very blunt" in letting dealers know they must be committed to their commercial business to be successful. "It's bad for the dealer if they invest in something and aren't ready for it and it's bad for our customers if they have a bad experience -- they get specked into the wrong truck; they have a service experience; a lack of knowledgeable salesperson," he said. "The best for everyone is to be a commercially-focused dealer." GM last week opened enrollment to become a commercial dealer. GM expects to expand its dealer network for medium-duty commercial vehicles, including those produced through a partnership with Isuzu, this year from 240 to about 400 with the introduction of the Chevy Silverado 4500HD, 5500HD and 6500HD. Requirements to become a commercial dealer include training for sales and service staff on commercial vehicles as well as parts and other specifications such as service door heights and lifts to accommodate the trucks. GM estimates the cost to meet the requirements at $100,000 to $200,000. However, Schwegman previously said many of the dealers already have many of the facility requirements. Incremental training and parts could cost just run $10,000 to $15,000 for those dealers, he said. Silverado The medium-duty Silverado trucks, like their light-duty counterparts, feature a mixed-use strategy that includes aluminum, high-strength steel and other materials. They also feature several exterior design characteristics of the current light-duty Silverado. On the interior, the commercial trucks also feature some of the same comfort creatures of the light-duty Silverado on the interior. Some of them include USB chargers, quieter cabins and a built-in 4G LTE Wi-Fi hotspot. The trucks are designed to support wireless cellphone charging and Bluetooth, along with support for Apple CarPlay and Android Auto. They will be available in two-wheel drive and four-wheel drive and will be powered by a 6.6-liter Duramax diesel engine with 350 hp and 700 pound-feet of torque and Allison transmissions with a Power Take Off option. Unlike a decade ago, GM has no plans to sell a medium-duty GMC truck, according to execs. GM did not announce pricing, however it's expected to be $40,000-$60,000. That does not include upfitting charges for specific needs that can cost several times more than the chassis cab. GM partnered with Navistar International Corp. to develop and produce the trucks in Springfield, Ohio. Production is expected to begin in late 2018. Order guides will be available in the spring and exact pricing will be announced this summer. Photo gallery - http://www.autonews.com/apps/pbcs.dll/gallery?Site=CA&Date=20180307&Category=PHOTOS01&ArtNo=307009998&Ref=PH .
-
Shell sponsoring new “hyper-fuel mileage” tractor-trailer design
kscarbel2 replied to kscarbel2's topic in Trucking News
Shell Debuts Fuel-Efficient Starship Concept Truck Heavy Duty Trucking (HDT) / March 6, 2018 Shell and Airflow Truck Company have debuted the full-size version of the company’s Starship Project truck – a concept Class 8 truck that maximizes fuel efficiency using a combination of currently available technologies. The long-teased Starship Project concept truck was finally unveiled at The Technology and Maintenance Council Annual Meeting in Atlanta. The project was first announced in 2015 and was designed by Bob Silwa’s AirFlow Truck Company, which produces hyper-efficient commercial trucks. “We seek projects such as the Starship initiative to keep Shell at the leading edge of technology development and energy efficiency,” said Bob Mainwaring, technology manager for innovation, Shell Lubricants. “The transportation industry is constantly changing, and our goal is to be at the forefront of innovation by collaborating with companies like AirFlow and others to develop creative solutions that provide benefits for years to come.” The body of the Starship Project tractor is a custom-made aerodynamic design made of carbon fiber. This includes the side skirts, hood, and front end. A custom, Department of Transportation-approved wrap-around windshield was designed specifically for the truck. The trailer includes energy efficient features such as full side skirts to reduce drag and a 5,000-watt solar array on top of the trailer to power interior accessories and reduce the energy load. The Starship is powered by a 2017 Cummins X15 Efficiency 6-cylinder engine with 400 horsepower and 1,850 ft.-lbs. of torque that has been paired with a transmission that has been calibrated to run at very low speeds, down to 800 rpm. The truck also makes use of Shell’s low viscosity synthetic lubricants, running on the Shell Rotella T6 Ultra 5W-30, which is an API-FA-4 engine oil that has been formulated to provide better fuel economy, improved high and low temperature performance and meets the requirements for many low emissions engines. It will also use a number of full synthetic Shell Lubricants products including Spirax S6 GXME 75W-80 transmission oil, Spirax S5 ADE 75W-80 differential oil and Spirax S6 GME 40 wheel hub oil. In addition, Shell Rotella Extended Life Coolant will provide excellent high-temperature protection and heat transfer. Shell Rotella Diesel Exhaust Fluid, a high purity diesel exhaust fluid, will also be in the truck. . -
Heavy Duty Trucking (HDT) / March 6, 2018 Mitsubishi Fuso Truck of America will begin selling its gasoline-powered 2019 FE cabovers this month, after showing production-ready versions at the Work Truck Show in Indianapolis. A General Motors-sourced 6.0L V-8 will power a Class 4 and Class 5 FE cabover. The Daimler AG-owned unit will also show a production-ready model of its battery-electric eCanter. The trucks will be sold alongside diesel models. Class 4 models will include the FE140 (14,500 lb. GVWR) and the FE160 (15,995 lb. GVWR). Later this year, Fuso will offer the Class 5 FE180 (17,995 lb. GVWR), which would be the first gasoline-powered Class 5 cabover. In all models, the PSI-GM V-8 engine will make 297 horsepower and 361 pound-feet of torque. Fuso will eventually offer a gaseous-prep package from the factory to allow buyers to use compressed natural gas (CNG) or propane autogas. The trucks come equiipped with a 40-gallon rear-mounted fuel tank. The gasoline engine will be paired with an Allison 1000 automatic transmission with Fuel Sense 2.0 transmission management software, including DynActive shifting technology that improves fuel economy by as much as 6%. The software uses a Neutral-at-Stop feature that further reduces fuel consumption. The FE gasoline trucks will also arrive with enhancements in the cab's interior, including improved driver seat bolstering. The seat cushion has been extended and the seatbelts are now red for higher visibility. Instrument cluster colors have been improved under various lighting conditions, and the trucks now come with an LED cabin light. Storage space has been enhanced with a new driver side console, floor tray, and sun-visor pocket. The truck is available with a black-on-black color scheme with silver trim accents in the interior. The cab improvements will also be offered on diesel-powered trucks. Fuso will assemble the models at the Freightliner Customer Chassis Corp. (FCCC) plant in Gaffney, S.C. .
-
Transport Topics / March 6, 2018 Joe Kory of Navistar announces the company's Renewed branding that makes "a significant investment in our private-labeled product portfolio." .
-
Ford adds diesel option, tech to Transit Connect cargo van Michael Martinez, Automotive News / March 6, 2018 DETROIT -- The technology upgrades and new diesel engine that Ford Motor Co. announced last month for its 2019 Transit Connect wagon are coming to the cargo van variant, too. Aimed at businesses ranging from dog groomers to package-delivery companies, the freshened van is meant to bolster Ford's 46 percent market share in the segment. "It is a critical tool with smart features to help improve productivity out in the field," Tim Stoehr, Ford general fleet marketing manager, said Tuesday in a statement. Ford introduced the Transit Connect to the U.S. in 2010 and last redesigned it in 2014. In 2017, Ford sold 34,473 Transit Connects, nearly double the sales of the second-place Nissan NV200. The company says about 97 percent of the roughly 300,000 small vans sold since its introduction are still on the road. The 2019 cargo van, on sale this fall, will come standard with a 2.0-liter four-cylinder engine mated to an eight-speed transmission. That replaces the 2.5-liter four-cylinder on today's van. A new 1.5-liter EcoBlue diesel engine, also paired with an eight-speed transmission, is available as the only diesel option in the segment. Ford expects it to be rated at 30 mpg highway. The cargo van also will offer a 2.5-liter four-cylinder with a six-speed automatic transmission and a prep package for fleets to use either compressed natural gas or propane. Officials say the vehicle will offer a class-leading towing capacity of 2,000 pounds when equipped with an optional trailer tow package. It will also feature rear cargo doors that swing out 180 degrees and can be locked in the open position to easily load and unload goods. Ford says the 2019 cargo van will come with the most driver-assist technology in the segment. That includes standard automatic emergency braking, part of Ford's efforts to make that technology standard on all of its models by 2022. Available technologies include adaptive cruise control, a blind-spot information system with cross-traffic alert and lane-keeping assist. It will feature a standard embedded 4G LTE modem that provides Wi-Fi for up to 10 devices, part of a companywide initiative to connect every vehicle by 2019. The Sync 3 infotainment system is optional. The vehicle is part of Ford's dominant lineup of commercial vehicles, including the F-series pickup and full-size Transit van. The automaker accounted for 43 percent of all U.S. commercial vehicle sales in 2017 through November, according to Polk registration data. .
-
Dana Launches Spicer S172 Series Single & Tandem Drive Axles
kscarbel2 replied to kscarbel2's topic in Trucking News
Dana shows new axles, updated tire analytics program James Menzies, Truck News / March 4, 2018 ATLANTA, Ga. – Two new lighter-weight axles and an updated tire analytics platform were among product introductions made by Dana at the Technology & Maintenance Council’s Spring meetings. The Spicer S172 single drive axle and D172 tandem axle will replace the 170 series, Dana announced. Steve Slesinksi, director, global product planning for Dana, said the company was able to reduce weight by up to 60 lbs. Both axles come with broad ratio coverage from 3.07 to 6.14. The S172 is aimed at Classes 7 and 8 applications with a gross axle weight rating of 25,000 lbs and a gross combination weight (GCW) rating of 100,000 lbs. The D172 tandem axle also reduces weight by up to 60 lbs, and is well suited for Canadian linehaul applications or heavy-haul work, with a GCW rating of 160,000 lbs. The first OEM to offer the axle will make it available in the second quarter of 2018, Slesinski said. Some of the features include: Dana Spicer AdvanTek gearing design, with wider face gearing; a 20-mm hypoid offset to improve efficiency without compromising strength; a high-strength pinion bearing system; an integrated one-piece carrier design; and a fully autonomous lubrication management system. Tim Farney, global vice-president of Dana’s commercial vehicle division, announced the second-generation Rhombus TireAnalytics system. It builds on the initial platform introduced at this show last year. “It addresses a key maintenance area in the industry, which is tires,” Farney said. “Specifically, it provides tire inspection management consistency, predictive analytics and forward-looking capability, and total life-cycle management tools fleets can utilize to help with the maintenance costs of their tires.” New features include: greater efficiency in gathering tire data using Bluetooth; life-cycle management capabilities using serialization; benchmarking capabilities; tread wear analytics; and tire performance comparisons by region. Farney said it’s the “only system with cradle to grave tracking capability” available in the market. “The Rhombus TireAnalytics 2.0 platform is a great example of the successful digital transformation of Dana, with our continued strategic focus on the customer,” said Mark Wallace, president of Dana Commercial Driveline Technologies. “Our team listened to our customers and upgraded the platform in many ways to enhance the robustness of information the platform provides while also making it more user friendly.” . -
Breaking the electric cost barrier Trailer-Body Builders / March 1, 2018 UPS has commissioned Workhorse to build it electric delivery trucks that cost about the same as diesels. While they promise substantially lower operational and maintenance costs over time, all-electric trucks so far haven't been able to beat their diesel or gasoline counterparts in their initial price tag. Global parcel delivery giant UPS, long an investor in energy sustainability and alternative fuel initiatives, is looking to change things by overcoming that "key barrier to large-scale fleet adoption." The company has engaged Workhorse Group to build it an all-electric Class 5 delivery van that will be "comparable in acquisition cost" to an equivalent conventional fuel van — and that's apples-to-apples, with no special subsidies included for the electric. If Workhorse pulls it off, it would make the argument against electric trucks a more difficult one for fleets whose duty-cycle needs match up. Notably, another Class 5 battery-electric delivery van unveiled recently that garnered some attention, the Chanje V8070, has promised big cost advantages in the long run for fleet use but is expected to carry an initial premium vs. diesel- or gasoline-powered vans. UPS also announced last fall that it's working with Unique Electric Solutions, LLC to develop an electric conversion kit initially for its vans operating in lower Manhattan, New York City. That effort is being supported by $500,000 grant from the New York State Energy Research and Development Authority and will utilize Unique Electric's switched reluctance motor, or SRM, technology. Compared with most electric motors, which use permanent magnets, SRMs have a simpler design with no permanent magnets, lowering acquisition and long-term operating costs. But in this latest endeavor, UPS said it will deploy 50 of the planned new plug-in electric trucks from Workhorse. The vehicles will offer a nearly 400% fuel efficiency improvement over conventional fuel vehicles, according to Workhorse, although the accounting for that claim is yet to be seen; it would need to compare per-mile costs for fuel vs. those of electricity for charging. Workhorse also said the electric delivery vans will have about a 100-mi. range between charges and will have a cab-forward design to optimize driver compartment and cargo area and reduce weight. "Our goal is to make it easy for UPS and others to go electric by removing prior roadblocks to large-scale acceptance such as cost," Steve Burns, Workhorse's CEO, said in a statement. UPS noted that it plans to put the 50 electric delivery vans to use in urban areas including Atlanta, Dallas and Los Angeles. "The all-electric trucks will deliver by day and re-charge overnight," said Carlton Rose, president of global fleet maintenance and engineering at UPS. "We are uniquely positioned to work with our partners, communities and customers to transform freight operation." After Workhorse and UPS have designed the electric van "from the ground up" and produced prototypes, the companies will tweak the design for larger-scale production. UPS said it intends to make these new electric trucks "a standard selection" for its fleet, noting that it operates some 35,000 diesel or gasoline trucks "in routes with duty cycles or daily miles traveled similar to the new electric vehicles," meaning those could be replaced out with all-electric vehicles. It's not the only all-electric trucks UPS is pursuing. The company has pre-ordered 125 of Tesla's planned electric semi-trucks and has purchased three of Mitsubishi-Fuso's eCanter medium-duty electric trucks as well to put to use in its fleet. UPS already operates more than 300 electric vehicles in use in the United States and Europe and has said that by 2020, it wants one out of every four vehicles it purchases to be either alternative fuel or advanced technology like the planned all-electric delivery vans from Workhorse. In its "Rolling Lab" — a growing fleet of more than 9,000 alternative fuel and advanced tech vehicles — UPS has been using and testing Workhorse's hybrid-electric E-GEN trucks for some time. Those run on battery power and feature a small gasoline "Range Extender" engine that kicks in and acts as a generator to provide power when the batteries are depleted, and can also use Workhorse's Horsefly drone to deliver packages.
-
Joe Thompson, Fleet Owner / March 2, 2018 Good news for green fleets! Two tax credits that affect fleets using alternative fuels have been extended. The Alternative Fuel Excise Credit and Alternative Fuel Infrastructure Tax Credit are now retroactively extended through the end of 2017 — a year past the original expiration of December 21, 2016. What does this mean for green fleet owners? Consider these credit examples: For any fleet that purchased propane autogas in 2017, a tax credit of 36 cents per gallon is available. A credit of $4,000 to $40,000 is available on the purchase of new qualified fuel cell motor vehicles in 2017. (The amount varies depending on vehicle weight.) For fleets that installed non-hydrogen alt-fuel refueling infrastructure in 2017, the fueling equipment is eligible for a tax credit of 30 percent of the cost (not to exceed $30,000). How do you file for credits? The Alternative Fuels Data Center says the Treasury Department will provide more details on the process on March 11. Claims may be submitted after Treasury issues guidance. Claims will be paid within 60 days after receipt. While this legislation is a boon for alternative fuel users, we must take steps to keep these incentives in place for the long run. I urge you to contact your elected officials with your support for alternative fuel credits. Another way to advocate for clean alternative energy is through our Clean Cities coalitions. This Department of Energy program has worked since 1993 to cut petroleum use in transportation. Through local outreach and education with stakeholders, the program encourages the use of alternative fuels and vehicles. You can help Congress recognize the value of this program by reaching out to your representative and express your support. If you have questions about alternative fuels or how they could benefit your fleet, leave a comment or call 800.59.ROUSH. You can also join the conversation here.
-
Eaton eyes an electric future, updates Endurant transmission sales
kscarbel2 replied to kscarbel2's topic in Trucking News
Eaton-Cummins prepping Endurant for expansion Sean Kilcarr, Fleet Owner / March 5, 2018 Joint venture looks to expand the reach of its 12-speed AMT in the coming months. ATLANTA. Since its introduction last October, the Endurant 12-speed automated manual transmission (AMT) is witnessing strong growth, according to Scott Davis, general manager of the Eaton Cummins Automated Transmission Technologies joint venture. It is now being positioned to expand into other trucking segments outside of the linehaul market – especially into the heavy haul 110,000 lb.-plus GCVW sector. Right now, AMT penetration is roughly 30% into the heavy-haul market, Davis explained to Fleet Owner, and while he doesn’t expect it to reach the 70% to 80% penetration now being experienced in the linehaul segment, it could be 40% by next year due to a number of factors. Related: Endurant automated transmission: A league of its own “What we see happening is more retirement of experienced drivers and more linehaul drivers moving into this [heavy haul] segment who don’t have the skills with a manual transmission,” Davis explained here during a press conference at the 2018 Technology & Maintenance Council (TMC) annual meeting. “The [AMT] technology is advancing and better integration [with engines] means smoother shifting plus more improved fuel economy. Think also about distraction: drivers must constantly think about shift points with a manual. Then there is fatigue issue: the mental and physical energy expended to manually shift gears, especially in stop-and-go environments. AMTs very good fit for that stop-and-go aspect of linehaul, that regional daycab operation.” Since it went into production in October of last year, Davis said Eaton-Cummins has built and deployed 3,500 Endurant AMTs – “those numbers are probably already outdated as this his has been a very aggressive ramp up for us,” he said – and he expects to see it move into market segments currently covered by Eaton’s Fuller Advantage and UltraShift Plus AMT products. “The key that the Endurant is a ‘purpose built’ AMT so we have optimized its architecture and reduced weight by several hundred pounds,” Davis explained. “AMTs also provide the technical foundation for telematics and predictive cruise, among other features. We can also get data on time spent in gear, how many times manual override occurs, etc. – that helps us calibrate shift schedules better. So if you operate in the Rocky Mountains, we can calibrate [the Endurant] differently versus operating on flat Florida highways. And we’re looking at over-the-air updates for calibration patterns just like engines; there is a lot of opportunity for that.” He added that AMTs “are really going to help us with that transition to newer, younger, lesser-skilled drivers” as well as comply with greenhouse gas (GHG) regulations heavy truck targets expected to go into effect in 2021, 2024, and 2027. “We’ll see a better result with [GHG] compliance by using AMTs – we’ll be better ability to meet the rules,” Davis stressed. “Integration gives you the ability for more consistent fuel consumption on routes, as well help in looking [at the road] ahead as get we get more advanced with smart coasting. Further out, we foresee predictive shifting at cruise to really optimize drive cycles.” He also noted that one feedback point from customers concerned warranty protection for transmission “burnout,” which is something Eaton-Cummins is now offering for the Endurant. Davis added that Eaton-Cummins also remains focused on delivering a “next-generation” Endurant product as well. “Our team is solely focused on automated transmissions; they know how to make the powertrain package work seamlessly as a single unit,” he explained. “You will see a whole pipeline of products as we work on advanced shifting – looking beyond transmission alone to include the entire powertrain as we seek ways to make shifts smoother and faster, including ways to execute more fuel-efficient features.”
BigMackTrucks.com
BigMackTrucks.com is a support forum for antique, classic and modern Mack Trucks! The forum is owned and maintained by Watt's Truck Center, Inc. an independent, full service Mack dealer. The forums are not affiliated with Mack Trucks, Inc.
Our Vendors and Advertisers
Thank you for your support!