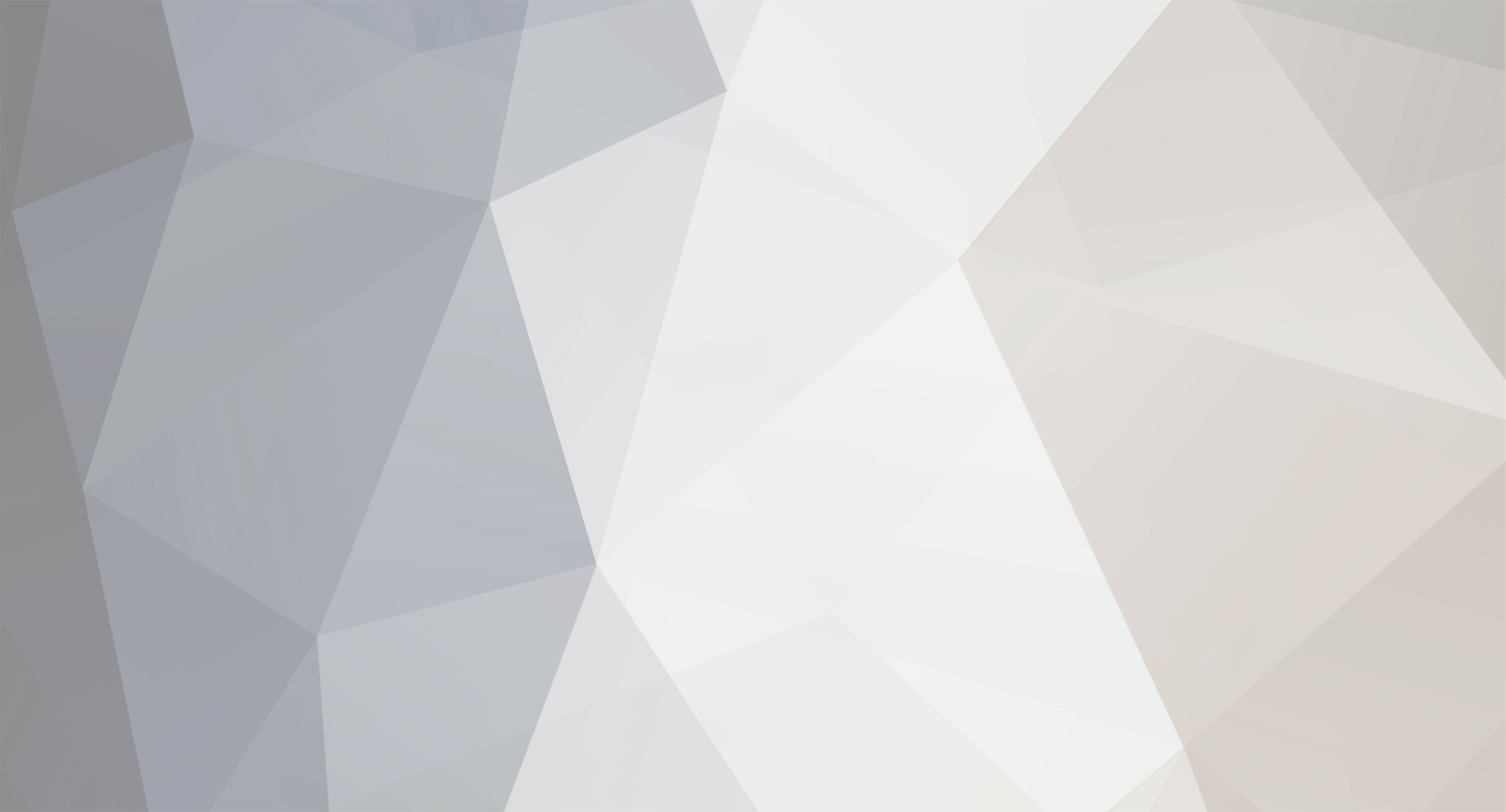
kscarbel2
Moderator-
Posts
17,893 -
Joined
-
Days Won
86
Content Type
Profiles
Forums
Gallery
Events
Blogs
BMT Wiki
Collections
Store
Everything posted by kscarbel2
-
Chicken producer Holly Farms on the shore had a fleet of Kenworth K100s with VT903s. They were every bit as bad as you heard. This was a case of, "If all else fails, sell it to the government. They buy low bid no matter what". The Mack E9, as the French can tell you, was a far superior V8 powerplant for the military applications described.
-
Volvo Group Press Release / November 16, 2017 Volvo Group takes the next step towards the future with an autonomous concept truck for hub-to-hub transportations in semi-confined areas like harbours and dedicated lanes on highways. Autonomous solutions bring benefits and serve the needs of both the customer and of society. .
-
Discover Renault Trucks T for long haul transport
kscarbel2 replied to kscarbel2's topic in Trucking News
-
IVECO BUS Press Release / November 13, 2017 The launch of the 14.5 meter, three-axle Crossway marks the start of a new era in IVECO BUS' city and intercity bus line. Available with two or three doors, it expands the already-extensive Crossway line, a paragon of performance and cost-effectiveness, and is positioned as the ideal vehicle for optimizing access to cities and large towns and to serve heavily frequented routes. .
-
-
Cummins Press Release / November 15, 2017 One of the most enduring engines in Cummins’ long history, the V903, is celebrating a remarkable 50 years in service. “Many engines have done the Cummins name proud, and prominent among these is the V903,” said Tom Terkhorn, Manager of Defense Products for Cummins Inc. “The first V903 crankshaft was laid at the Cummins Engine Plant (CEP) in Columbus, Indiana (USA), late in 1967, and since then the engine has progressed from 280 horsepower (hp) for truck use to its current peak output of 675 hp for military equipment.” The V903 is an eight-cylinder ‘V’ configuration with a 903 cubic inch (14.8-litre) displacement. Providing high power density, it has four valves per cylinder, is turbocharged and air-to-water aftercooled, and has a low pressure common rail fuel system. Today, the V903 is produced primarily for military applications, notably the US Army’s iconic Bradley Fighting Vehicle, rated at 600 hp. In 2018, a 675 hp version will be installed in the upgraded Bradley ECP 2, Armored Multi-Purpose Vehicle (AMPV) and Paladin M109A7 howitzer. In actual operations, the V903 powered Bradley has showed a combat readiness of over 95 percent – the highest of any armored vehicle in the history of the US Army. The V903 was originally developed for the on-highway truck and construction markets to meet the requirements for a lightweight, compact diesel engine in the 280-320 hp range. It went on to make its mark in other applications such as recreational and commercial boats, mining equipment, and farm tractors. The V903 began its life in the Bradley Fighting Vehicle in 1981 when Cummins upgraded the power level of the commercial truck engine from 350 to 500 hp with the addition of air-to-water aftercooling and upgraded fuel system. Cummins moved the engine up to 600 hp V903 in early 1989 to maintain the Bradley’s mobility when its full combat weight increased to 60,000 lb as a result of added armor. The power boost was achieved using technologies developed for other Cummins products. Importantly, there were no changes to the length, width and height of the engine which had to fit into the Bradley’s notably tight powerpack compartment. “Cummins conducted accelerated wear and abuse tests for final acceptance of the engine’s revised design and these showed that thermal and mechanical stresses of the 600 hp engine were actually lower than the 500 hp version,” said Keith Baylor, V903 Product Validation Manager. “This meant the army could expect improved reliability and durability. Field performance of the 600 hp engine confirmed this initial expectation.” Development of the 675 hp version of the V903 was completed in 2013 for the US Army’s Paladin M109A7 howitzer, and in 2018 it will be fitted in the upgraded Bradley ECP 2 and Armoured Multi-Purpose Vehicle (AMPV) which replaces the M113 armored personnel carrier. Production of the V903 – both remanufactured and new engines – is carried out at Cummins’ Seymour Engine Plant in Indiana (USA). “The V903 platform will continue to support the armored vehicle forces for decades to come,” said Tom Terkhorn. .
-
Jerry, the "ram" wasn't a great design. They never held up, rain went in and down....I could go on and on. Nobody takes one off unless it's smashed or disintegrated. A standard hood, which most "F" models used, is better. https://dynamic.donaldson.com/WebStore/hierarchy/hierarchy.html?section=10121
-
Sean Kilcarr, Fleet Owner / November 15, 2017 There is no other tool capable of doing the work trucks do; there’s just no debating that. How that tool gets powered, though, will be a major point of argument now and in the future. So I recently listened to Martin Daum, member of the board of management at Germany’s Daimler AG and head of the company’s global Daimler Truck and Daimler Bus divisions, discuss the future of trucking during a press conference at the big Expo Transporte 2017 show in Guadalajara, Mexico. One of the interesting points he made – one well-known to anyone in the freight business – is that our economic systems today cannot function without trucks. There is just no other transportation tool – train, plane, automobile, etc. – that can do the work that trucks day in and day out. “The world can live without passenger cars but it cannot live without trucks,” Daum said. “If you need to haul 80,000 lbs. of dirt, a wheelbarrow can’t do the job. You need something that can haul such heavy loads – and that is a truck.” It’s a point I’ve made more than a few times myself: Trucks are a necessity. For example, the expectations for speedy delivery of goods ordered via the Internet – and to not pay an extra transportation fee for said delivery – is falling squarely on the shoulders of truckers and there’s little to no recognition of the vital role they play in making those deliveries happen each and every time. Indeed, trucks currently haul over 70.6% of all the freight in the U.S. (though that is expected to slip to a hair over 67.2% by 2028) and haul over 80% of the freight in Mexico, according to Flavio Rivera, president and CEO of Daimler Trucks Mexico. Thus, trucks are here to stay – whether they are loved or not for the job they do. The question, though, is whether they must remain powered primarily by diesel and gasoline. I talked to Mike Cammisa, vice president of safety policy connectivity, and technology for the American Trucking Associations (ATA), about that very subject at a recent press event in Washington D.C. and he’s of the opinion that we’ll start to see more powertrain “customization” in terms of fuel source in the future; a customization trend driven by the type of duty-cycle a truck must perform. “What I see in the future is a diversity of powertrains and fuel sources; electricity is one of them and does seem appropriate in shorter haul applications, where the truck returns to a central depot and can be recharged overnight,” he explained to me. “It makes sense to match the powertrain to the needs of the duty cycle and you can also combine systems, as well, such as in a hybrid powertrain that is part electric and part diesel,” Cammisa said. “Especially in inner city traffic situation, you could then run on electricity.” Daimler’s Daum is of a similar mindset and believes one of the things truck OEMs must do in the future is to offer a “full range of options” when it comes to powertrains just as they do with cab interior packages and the like. “Natural gas, propane and electricity are all options,” he said, pointing in particular to the new eCanter all-electric medium-duty truck built by Daimler subsidiary Mitsubishi Fuso. Right now, Daum said the eCanter will only be sold on a “use case by use case” basis to customers around the globe, with limited production of the vehicle for the next two years. But by 2019, he expects the eCanter will be ready for “full throttle production” as he put it. “It’s about on one side seeing what is possible and on the other knowing their limitations,” Daum said. “We know diesel is right now a necessity because it can haul higher loads. But we’re also showing that there is potential for an emission-free future.” On a final note, he stressed that the improving economic picture for the U.S. and other countries is generating some positive trends for truckers. But Daum also cautioned that planning truck production levels correctly will be the real trick to ensuring such positives don’t turn into negatives. “Times are not bad. That is a German euphemism for ‘good.’ And good times for the global economy always means good times for trucking,” he explained. “But global instability is the salt in our soup of daily life; for the commercial vehicle market is a volatile market. We continually calculate how many trucks a country or regional will need based on its infrastructure, population, and economic development,” he added. “So if you sell too many trucks – more than the system needs – a crisis will come. But if you sell too few – such as in 2009, when we sold only half the trucks the economy needed -- then good times will be ahead.” That’s one of many things to keep in mind as we barrel towards the close of 2017. .
-
MAN's $583,000 Electric Urban Bus to Test Cities' Spending Plans
kscarbel2 replied to kscarbel2's topic in Trucking News
MAN selects ABB fast chargers for its e-bus R&D facilities ABB Press Release / September 20, 2016 ABB, the leading power and automation technology group, is supplying fast chargers for depot and opportunity charging of electric buses, to MAN Truck & Bus for its new e-bus R&D facilities in Munich, Germany. In July MAN Truck & Bus announced serial production of fully electric buses by 2019. Pilots of the e-buses are planned to go into operation in 2018. The buses are developed at MAN’s R&D facilities in Munich, using a test bench equipped with different charging technologies from ABB. “Energy efficient and sustainable transportation is a key focus area of ABB’s Next Level strategy and we are committed to further advance e-mobility,” says Robert Itschner, Managing Director of ABB’s Power Conversion business unit. “ABB offers different technologies and solutions for electric vehicle charging and we are very pleased that MAN Truck & Bus chose our fast chargers for its test facilities.” For depot charging tests – used at the terminus where a bus has a longer stop – MAN will use an ABB fast charger with a CCS2 connector at its facility. Following the EU standardization for electric vehicle charging, it is the same connector that is used for electric cars. For opportunity charging tests, ABB will supply a charge pole with inverted pantograph. With its automated rooftop connection and a typical charge time of three to six minutes, opportunity fast charging systems allow charging at end stops and can easily be integrated in existing bus routes. The fast-charging solutions are based on IEC 61851-23, the international standard for fast charging electric vehicles. This ensures the appropriate safety systems are in place, the electrical design is in accordance with regulations, and the systems architecture and working principles are supported by a wider automotive community in the future. Both, ABB and MAN Truck & Bus AG are project partners in the European e-bus charging system (eBusCS) initiative which promotes international standardization of charging processes for electric buses to facilitate the introduction of electric bus systems in European cities. -
Bloomberg / November 15, 2017 Volkswagen AG’s MAN commercial-vehicle division expects its electric city buses, on sale as of 2019, to cost about 2.5 times more than conventionally powered ones, with the difference easing only in the following few years. MAN SE Chief Executive Officer Joachim Drees’s estimate for the models, giving a price tag of around 500,000 euros (US$583,000) a bus, highlights the struggle for vehicle manufacturers, cities and infrastructure providers to manage spending amid pressure to adopt zero-emission models to reduce pollution. The company predicts that a battery-powered bus’s lifetime cost is likely by 2023 to roughly match figures for combustion-engine versions, Drees said Monday at a briefing in MAN’s hometown of Munich. “The electric bus will be more expensive up front,” Drees said. “But batteries having a second life, and their rapidly falling prices, will help offset this,” along with savings on fuel and maintenance. Compared to carmakers, commercial-vehicle manufacturers have been slow to push forward with electric models, because their models carry heavier loads and need large batteries that take up room and increase costs. The broader range of vehicle uses and comparatively smaller numbers sold also make switching to electric versions a tougher undertaking. Still, a shift to the technology is accelerating as cities take steps to cut pollution and potential competitors emerge, including Tesla Inc. Daimler AG, the owner of the Mercedes-Benz and Freightliner brands, showed off a battery-powered heavy-duty model last month, weeks before electric-auto pioneer Tesla is scheduled to introduce its own truck. “We’d like to have electric buses as quickly as possible, and as many as possible,” Munich deputy mayor Josef Schmid said at the event. For the southern German city, shifting to electric buses means replacing a fleet of 460 vehicles. To help push along technology transformation and improve profitability, MAN is investing 400 million euros annually in the five years through 2020 at its commercial vehicle plants in three European Union countries as well as Russia, South Africa, India and Turkey. About 500 million will be spent on electric powering systems in that time, it said. The measures are part of a plan to increase margins across Volkswagen’s truck, bus and van business, including heavy-duty vehicle makers MAN and Scania, to challenge rivals Daimler and Volvo AB. “By 2025, I don’t expect cities to buy buses anymore that aren’t battery powered,” Drees said. .
-
Dodge to offer split, dual-function tailgate Automotive News / November 15, 2017 Spy photographers have caught confirmation that at least some versions of the next-generation Ram 1500 pickup will have a new dual-function tailgate, capable of both dropping down in the traditional manner or opening up 'French door' style. The tailgate design makes it easier for consumers to access the pickup's bed, without having to reach over the dropped tailgate or climb up on it. Earlier spy photos confirmed that the next-generation Ram 1500's tailgate can be dropped remotely using a button on the key fob. FCA US plans to begin production of the next-generation Ram 1500 in January at a retooled assembly plant in Sterling Heights, Mich., and will introduce the redesigned half-ton at the 2018 Detroit auto show. .
-
Renault Trucks Press Release / October 27, 2017 On 10 October 2017 at the Blainville-sur-Orne manufacturing site, Renault Trucks’ President Bruno Blin handed over the keys of a Renault Trucks D Cab 2,1m to Mr. Philip Thurston, Joint Managing Director of the British group Pace Logistics Services. This was the one millionth truck manufactured in the Normandy factory. Mr. Philip Thurston, Joint Managing Director of Pace Logistics Services, was handed the keys of the one millionth distribution truck assembled at the Renault Trucks factory – a D Cab 2.1m – on Thursday, 10 October by Bruno Blin, the Renault Trucks President. This was the 31th truck to join the Pace Logistics fleet, which is exclusively made up of Renault Trucks vehicles. This 18-ton "Guaranteed French Origin" D Cab 2.1m will be used for transporting pallets and for multi-point delivery assignments throughout the UK & Europe from their central distribution warehouse in Salford, Manchester. During the ceremony, Bruno Blin declared that he was "particularly proud of a British neighbour demonstrating trust in the excellence and expertise of French manufacturing." The President of Renault Trucks also congratulated the JDS Trucks dealership for its on-going relationship with Pace Logistics and for ensuring that its fleet vehicles remain operational at all times. The Blainville-sur-Orne factory has been producing trucks since 1957 and is specialised in medium weight vehicles and truck cabs. 262 cabs are manufactured and 76 trucks assembled every day. The site is currently recruiting 100 operators in order to meet increasing demand. Renault Trucks has three other manufacturing sites in France, in Bourg en Bresse, Limoges and Lyon. .
-
The Korea Herald / November 16, 2017 Swedish truck manufacturer Volvo Trucks is in discussion with Samsung to develop future-generation batteries in order to commercialize trucks powered by electricity, its chief said in Seoul on Wednesday. In an interview with The Korea Herald, Claes Nilsson, president of Volvo Trucks, said the company has been in talks with the South Korean tech giant to introduce electric trucks, which are part of what the company envisions for a “greener” future. A fully electrified truck, not only for Volvo but also other traditional manufacturers, still remains a mere concept, as it requires a long driving range, or in other words, lots of batteries. “We are already collaborating with Samsung when it comes to battery technology,” he said. “Where we are using the fully electric drive lines today is on the bus side. But as we move forward, we need (full electric lines for) trucks as well and yes, Korean industry, when it comes to semiconductors and battery and etc, are very advanced,” he said, without elaborating on the extent of collaboration with Samsung SDI, a battery and display making affiliate of the group, and what type of batteries they may be developing. Although Hydrogen has potential today, batteries are more likely to be the mainstream, he said. “But right now the most promising development is in batteries rather than hydrogen,” he said, adding that the company has been developing all three types of green trucks to be prepared as to where the technology might lead to. “But that can change in five or 10 years, nobody knows.” The head of Volvo Trucks was in Seoul to present the company’s future vision of taking a lead in connectivity, automation and electro-mobility in the commercial vehicle segment. Also, to keep its top position in the Korean market, the company has decided to install two safety features -- collision warning with emergency braking and lane-keeping support -- in all its heavy-duty trucks to be sold here starting January, one year ahead of the Korean government’s plans to require commercial vehicle manufacturers, both domestic and foreign, to enhance safety features in their models from 2019. Traffic accidents caused by trucks and buses have been major safety concerns here. “When we think the technology is mature and the market is ready, we don’t wait for the legislation,” he said. Currently, Volvo Trucks is the top commercial vehicle importer here and the third after two domestic brands, Hyundai and Tata Daewoo. South Korea is Volvo Trucks’ ninth-biggest market in terms of profit generation. It expects to sell about 3,000 trucks in the country, a 15 percent increase from last year. Though the market here accounts for only 3 percent of all Volvo trucks sold worldwide, South Korea is a growing and important market. Demand for efficient trucks is high not just among customers, but also in terms of the traffic environment. “The customer base in this county is demanding efficient types of trucks in transportation, we believe we have good product offers to this market,” he said. “We also believe that (the) transportation environment here is very demanding in terms of weight and road condition and utilization, and very quality conscious customers can help us actually develop.” .
-
MAN Agricultural Trucks at AGRITECHNICA 2017
kscarbel2 replied to kscarbel2's topic in Trucking News
2017 MAN Agricultural Trucks at AGRITECHNICA The agricultural sector offers various opportunities for using MAN trucks The MAN TGS 18.500 4x4 BLS on display is equipped specifically for the industry A variety of transport tasks arise in agricultural business and for contracted hauliers. Thanks to their high payload, low fuel consumption and typical high driving speed, trucks are gaining ground in the transportation chain between farm, field and warehouse. With this in mind, the MAN TGS is kitted out as an agricultural truck and features all-wheel drive, fifth-wheel coupling, trailer coupling and support, load-sensing hydraulic system and wide, soil-friendly agricultural tyres. MAN trucks are not only suited for transporting harvested crops over great distances – from grain to agricultural dealers, silo corn to the biogas plant, beet to the sugar refinery or potatoes to the starch plant – right from the farm or from the edge of the field. It is in combined use in the field, on the road and in further processing applications where MAN agricultural trucks are really able to demonstrate their high level of efficiency. They offer distinct advantages in the transportation chain compared to other vehicle types, due to their high payload of 38 or 40 tonnes, lower fuel consumption and the higher speeds typical of trucks. What's more, established semitrailer combinations often enjoy greater acceptance among other road users and in the population in general than tractors with bulky, multi-axle trailers do. Agriculture and the way it is perceived by the public has been going through a period of change for some time. The areas being cultivated are growing all the time due to economic reasons. So too are the volumes being transported. The areas farmed by agricultural businesses are no longer situated in the direct vicinity of farm buildings. The transport distances between locations are therefore on the increase and the areas which contracted hauliers have to cover is expanding. Contractors are paying more and more attention to the efficiency and total cost of ownership (TCO) of their fleet, while the public are concerned with the issue of environmental friendliness in the transportation chain. The increasing prevalence of biogas plants is ensuring increased transport volumes for the delivery of corn, grass and grain silage, as well as the movement of fermentation substrate across great distances. Transportation applications in particular are where trucks that have been adapted to meet the needs of the agricultural industry really show their strengths. This is something that has come to MAN's attention with the increase in demand for adapted vehicle concepts. In most cases, these are semitrailer tractors in the MAN TGS series, pulling trailers specially designed for agricultural use. Options include semitrailer tractors and chassis with rear wheel drive and standard or medium-high design height. All-wheel drive MAN TGS in high design height with switchable or permanent front wheel drive are also available. With permanent all-wheel drive, the centre differential means it is possible to balance the front and rear axles, preventing damage to the floor when cornering. The solution positioned between road use and all-wheel drive is called MAN HydroDrive and offers hydrostatic front wheel drive for additional traction. The MAN TGS as an agricultural truck Showcased by MAN Truck & Bus at AGRITECHNICA 2017, the world's leading trade fair for agricultural machinery held in Hanover, the two-axle MAN TGS 18.500 4x4 BLS semitrailer tractor impresses with its wide range of equipment specifically for use in the agricultural industry. One of these is the option to have the vehicle approved for agricultural or forestry use. The advantage of this is the fact that its permitted width can be up to 3.0 metres and that the vehicle is exempt from Sunday driving bans applicable in certain countries. Permanent all-wheel drive is the ideal choice for agricultural use. Routes to many fields take vehicles across challenging terrain and roads that have not been asphalted and are usually covered in gravel. What's more, not all access routes to silage heaps, slurry tanks or silo systems on agricultural premises are surfaced. For maximum traction, the driver can apply the differential locks in the longitudinal and then in the transverse direction using just one rotary switch. The all-wheel drive really comes into its own when combined with the soil-friendly agricultural tyres, as they allow the vehicle to leave the country lanes and move onto grasslands or fields, where the chopper can fill the attached trailer straight away. The tyres are able to meet the various requirements placed on them: the low level of pressure they exert on the ground means they look after country lanes and productive land, their V-profile takes care of traction, and they are still able to manage high transport speeds on surfaced roads. When a vehicle is approved for agricultural or forestry use, it can be up to 3 metres wide – a factor which influences tyre choice. If the standard truck width of 2.50 metres is to be maintained, 445/65 front tyres and 600/50 individual rear tyres are fitted to the axles. Yet if the maximum permitted width is to be utilised, the MAN TGS can run on 580/65 22.5 tyres at the front and 750/45 26.5 tyres at the rear. MAN takes care of the huge wheel arch required with adapted mudguard cutouts, splash guards and attachments. If transportation is to take place over an extended period and on surfaced roads, it is worth replacing the field tyres with road tyres that have higher wear resistance and lower rolling resistance, making them more economical. In the high design height, the driver can comfortably climb into the MAN cab using the four steps. The interior colours of “sand” or dark-grey “urban concret” convey a user-friendly appearance. To provide a view of the load, windows have been incorporated into the rear wall. Alternatively – and often providing a more practical option – the images captured by two externally mounted cameras can be played on the 7-inch display of the new MAN infotainment system, enabling the driver to monitor the load and the area around the rear of the vehicle. On the outside, the M cab impresses with functional accessories: grilles on the rugged, three-piece steel bumper protect the headlights. A step on the left mudguard with a long handrail on the roof makes it easier to see into the tipper and cross over to the semitrailer. Additional headlights illuminate the area around the vehicle and rotating beacons warn other road users. The attachment of a snow-plough mounting plate with the associated elevated headlights and indicators enables contractors to make economical use of the vehicle in the winter season too. Behind the cab, the exhaust pipe is located on the right and tilted upwards to reduce the exhaust gases released in the vicinity of the vehicle and to prevent dust from being swirled up on the ground. The 6-cylinder in-line engine from the MAN D26 Common Rail series has a capacity of 12.4 litres and delivers 500 hp at 1400 rpm in the Euro 6c emission standard. Its maximum torque is 2500 Nm at 930 to 1400 rpm. This engine series is also available with an output of 420 hp and 460 hp. The engine is coupled with the automated MAN TipMatic 12 gearbox. With its SmartShifting function, the driver is able to change gear particularly quickly depending on the driving situation in order to minimise the interruption to traction. The “OFFROAD” gearbox software provided for all-wheel vehicles and which is activated by turning the gear selector switch is specially adapted for journeys over difficult terrain. It prevents drivers from skipping gears as well as indicating modified shifting times and higher shifting speeds to prevent interruption to drive traction. As a result, a typical truck speed of max. 89 km/h is possible even with a full payload – provided this is permitted in accordance with traffic regulations. At low and medium speeds in particular – as are common with MAN agricultural trucks – the wear-free MAN PriTader really demonstrates its brake force. Integrated into the water circuit, the maximum brake output of this system is 620 kW. In terms of industry-specific equipment, MAN can also install a trailer coupling support in addition to the fifth-wheel coupling at the end of the frame. This is comprised of a bar coupling with a 38-mm bolt and an 80-mm ball coupling. It also includes two 50-mm steering balls to pull agricultural trailers with forced steering. This mechanism allows the trailer to cleanly follow the path of the tractor vehicle when cornering. The installed load-sensing hydraulic system regulates the output and pressure as required. This means that the full hydraulic output is only provided when required and that fuel is saved, as the hydraulic pump does not have to permanently operate at full capacity to supply the hydraulic system with high pressure. Alternatively to the two-axle semi-trailer tractor, the MAN TGS agricultural truck is available as a two-, three- or four-axle chassis with a drive ranging from 4x2 to 8x8 to allow various bodies such as grass silage trailers, push-off trailers, lime and fertiliser spreaders or slurry tanks to be mounted. Although this vehicle concept has the edge over the semitrailer combination in terms of its offroad properties, it is restricted with respect to its payload as well as being at a disadvantage in terms of its suitability for universal use and the extent to which it can be used economically all year round. Modifications to MAN TGS semitrailer tractors and chassis for agricultural use are carried out by MAN-certified companies. Depending on the task at hand, these include the MAN Truck Modification Center (TMC) and MAN-qualified modification contractors. The MAN TGS agricultural truck in use all year round Another advantage of the MAN agricultural truck relates to the extent it can be used all year round. Once farming operations and harvest time have come to an end, you need only exchange the tyres and semitrailer to be able to use this semitrailer tractor in the transport sector – primarily in the construction industry – and as a winter service vehicle. The MAN TGS provides contractors with economical use of their vehicle and a source of income all year round. MAN trucks for the agricultural industry Trucks from the MAN product portfolio are suitable for a wide range of tasks in the agricultural industry. The TGL, TGM and TGS series transport mobile grinding and mixing plants to name just a couple of examples. When choosing the chassis, the size and the power take-off performance required for the grinding mill, mixing facility, screw conveyors and conveyor belts are the decisive factors. The semitrailer tractors for tank semitrailers with liquid waste such as slurry or fermentation substrate as well as for silo trucks containing fertilisers and feed generally come from the MAN TGS series. These vehicles ensure an efficient transport solution. Thanks to their high payload and fast driving speed, MAN TGM with all-wheel drive and soil-friendly agricultural tyres provide an alternative solution for spreading fertiliser on navigable and stable ground. And given that it is often necessary to bring workers along, MAN cabs can also be equipped with three seats. MAN HydroDrive for traction if required in the agricultural industry In 2005, MAN launched the HydroDrive drive system – a solution which at the time was the only one of its kind worldwide. The selectable hydrostatically powered wheel hub motors in the front axle – or the second axle if the vehicle has four axles – are the ideal configuration for vehicles that are primarily driven on surfaced roads and only occasionally need additional traction. This may be the case if the vehicle has to move from the road to the edge of the field. For example, it may be necessary to deliver seed or slurry, collect beet from the clamp or gather bales of grass or straw. Milk collectors often have to navigate gravel or snow-covered paths on farms to get to the milk tank. The payload advantage compared to a conventional all-wheel drive is one of the recognised benefits of MAN HydroDrive. The weight advantage is 500 to 750 kilogrammes depending on the vehicle configuration. From a business perspective, the fuel saving represents a further benefit – when the system is switched off, the front wheels rotate freely, as with an on-road vehicle. MAN also offers this additional traction for vehicles with a standard height design. The low frame height makes it easier for drivers to enter and exit the cab. The system also sets itself apart in terms of how easy it is to mount bodies, as all MAN TipMatic and MAN HydroDrive components are located below the top edge of the frame. The MAN TGS as a milk tanker For milk tankers, the MAN TGS series offers a three-axle chassis that has been specially configured for the industry. The steered trailing axle reduces the turning circle, making it easier to manoeuvre in built-up areas and on farmsteads. Four corner air suspension is recommended to ensure high suspension comfort and the gentle transportation of fragile loads. To create space for the fittings cabinet mounted on the right of the frame, MAN has moved the units that were installed there for the Euro 6 standard. This means that the exhaust silencer, battery box and fuel tank are now on the left. As a result, body manufacturers have a space ranging from 2.5 to 3.1 metres in length to work with for their installations. To ensure safety and improve the driving characteristics of tankers, MAN provides a high-load roll stabilisation package consisting of a stabiliser and X control arm. The MAN TGS and TGX as an animal transporter In order to transport animals promptly and with care, MAN offers chassis from the TGS and TGX series. Three-axle vehicles with a steered trailing axle bring together loading length and manoeuvrability. The air suspension at the axles ensures that delicate cargos are looked after. If animals are housed across multiple levels, this results in a high centre of gravity for the body. To reduce rolling movements in the body, MAN provides a high-load roll stabilisation package with stabilisers and an X control arm to guide the rear axle. The MAN TGX series supplies economical and high-torque engines ranging from 360 hp to 640 hp. Particularly when transporting across challenging terrain or over great distances, engine outputs of over 500 hp are required to complete transport tasks promptly. The 6-cylinder in-line engines from the D38 Common Rail series deliver 540 hp, 580 hp and 640 hp. These are reserved exclusively for the MAN TGX series. In the somewhat narrower cabs of the MAN TGS series, the output rating starts at 320 hp and extends all the way up to 500 hp. Loading points on agricultural sites or pastures cannot always be reached via asphalted roads. What's more, snow-covered roads in winter can make access difficult. In such cases, the MAN HydroDrive system installed in the TGS and TGX series is on hand to provide additional traction. The hydrostatic drive installed in the front axle can be combined with both the TipMatic automated gearbox as well as manually operated gearboxes. Technical data for the vehicle exhibited at AGRITECHNICA 2017 Type Agricultural semitrailer tractor with permanent all-wheel drive MAN TGS 18.500 4x4 BLS Wheelbase 3900 mm Suspension Front axle leaf-spring suspension 9.5 t Rear axle air suspension 13.0 t Height High design height Cab M with seating for 2 and ladder Engine 6-cylinder D26 Common Rail in-line engine, emission standard Euro 6c Cylinder capacity 12,419 ccm Output 500 hp (368 kW) at 1800 rpm Torque 2500 Nm at 930–1400 rpm Gearbox MAN TipMatic 12 28 OD with OFFROAD gearbox software Rear axle Planetary axle Axle ratio i = 4.00 Speed 1.5–89 km/h Permissible axle loads with agricultural tyres Front 9000 kg / rear 10,000 kg Permissible gross weight 18,000 kg Permitted gross train weight 40,000 kg (technically 44,000 kg) Tyres Front axle 445/65 R 22.5 Rear axle 600/50 R 22.5 Paintwork Cab: MAN green M107 Rims: light ivory Frame: graphite black RAL 9011 Industry-oriented agricultural equipment Conversion to agricultural tyres Trailer coupling support on the end of the frame with steering balls Load-sensing hydraulic system Rear-view camera Stainless-steel roof bar with 4 working lights -
MAN Truck & Bus Press Release / November 13, 2017 The agricultural sector offers various opportunities for using MAN trucks // The MAN TGS 18.500 4x4 BLS on display is equipped specifically for the industry A variety of transport tasks arise in agricultural business and for contracted hauliers. Thanks to their high payload, low fuel consumption and typical high driving speed, trucks are gaining ground in the transportation chain between farm, field and warehouse. With this in mind, the MAN TGS is kitted out as an agricultural truck and features all-wheel drive, fifth-wheel coupling, trailer coupling and support, load-sensing hydraulic system and wide, soil-friendly agricultural tyres. MAN trucks are not only suited for transporting harvested crops over great distances – from grain to agricultural dealers, silo corn to the biogas plant, beet to the sugar refinery or potatoes to the starch plant – right from the farm or from the edge of the field. It is in combined use in the field, on the road and in further processing applications where MAN agricultural trucks are really able to demonstrate their high level of efficiency. They offer distinct advantages in the transportation chain compared to other vehicle types, due to their high payload of 38 or 40 tonnes, lower fuel consumption and the higher speeds typical of trucks. What's more, established semitrailer combinations often enjoy greater acceptance among other road users and in the population in general than tractors with bulky, multi-axle trailers do. Agriculture and the way it is perceived by the public has been going through a period of change for some time. The areas being cultivated are growing all the time due to economic reasons. So too are the volumes being transported. The areas farmed by agricultural businesses are no longer situated in the direct vicinity of farm buildings. The transport distances between locations are therefore on the increase and the areas which contracted hauliers have to cover is expanding. Contractors are paying more and more attention to the efficiency and total cost of ownership (TCO) of their fleet, while the public are concerned with the issue of environmental friendliness in the transportation chain. The increasing prevalence of biogas plants is ensuring increased transport volumes for the delivery of corn, grass and grain silage, as well as the movement of fermentation substrate across great distances. Transportation applications in particular are where trucks that have been adapted to meet the needs of the agricultural industry really show their strengths. This is something that has come to MAN's attention with the increase in demand for adapted vehicle concepts. In most cases, these are semitrailer tractors in the MAN TGS series, pulling trailers specially designed for agricultural use. Options include semitrailer tractors and chassis with rear wheel drive and standard or medium-high design height. All-wheel drive MAN TGS in high design height with switchable or permanent front wheel drive are also available. With permanent all-wheel drive, the centre differential means it is possible to balance the front and rear axles, preventing damage to the floor when cornering. The solution positioned between road use and all-wheel drive is called MAN HydroDrive and offers hydrostatic front wheel drive for additional traction. .
-
We never thought of the F as old, and the WS as new. Rather, the F was "East Coast" and the WS was "West Coast", two very different trucks for different markets. The F certainly was born years before the WL/WS, but the steel dashboard F-600 of 1962 was a very different truck from the F-700 "Interstater" of 1980. Continually improved to keep it competitive, it had a completely new interior, raised cab, deeper frame and more. The MH Ultra-Liner was the convergence, a truck adaptable to both the east and west coast operators. If I wanted to make money like Overnite, UPS and Chemical Leamon, I'd buy a Mack naturally, and choose F-models over the problem-ridden Cruise-Liner. We actually sold Overnite a handful of Cruise-Liners (54-inch day cab 6x4s), but they were not pleased. I really liked the CL-72/721 Mack "Dynamax" wet clutch (4-plate, push-type, DEXRON fluid) spec'd by UPS. Produced for us by Rockford Clutch Corp., they almost lasted forever. That was an option to all customers too.
-
Quartet of construction classics: four legendary cab-behind-engine, short-nosed and cab-over-engine trucks from Mercedes-Benz from four decades Daimler Press Release / November 14, 2017 Mercedes-Benz LAK 315: classic cab-behind-engine truck from the 1950s Mercedes-Benz 2624: the indestructible short-nosed truck Mercedes-Benz 2232 LP: cab-over-engine truck with legendary V10 engine Mercedes-Benz 1635: new-generation long-runner Heavy-duty trucks for construction have a big tradition at Mercedes-Benz. Be it classic cab-behind-engine trucks, short-nosed trucks or cab-over-engine trucks: the Mercedes dump trucks have set standards again and again for more than a century. At the Arocs Performance Days, Mercedes-Benz is presenting four classic construction vehicles from the 1950s to 1980s. The quartet demonstrates the progression from cab-behind-engine truck to short-nosed truck to modern cab-over-engine truck. Mercedes-Benz LAK 315: classic cab-behind-engine truck from the 1950s They had their noses in front in every respect: Mercedes' large cab-behind-engine trucks were THE heavy-duty trucks of the 1950s. Born in 1950 as the L 6000/6600, a name which indicated the chassis payload, Mercedes-Benz changed the model designation to reflect the development code in the mid-1950s. With its permissible GVW of max.14.7 t in its reinforced guise and a payload of up to 7.6 t, the Mercedes-Benz LAK 315 is a medium-size truck by today's standards, but at the time it was one of the heavier all-wheel-drive trucks for the construction site. Beneath the long bonnet is a six-cylinder in-line naturally aspirated engine with a displacement of 8.3 litres, an output of 107 kW (145 hp) and a peak torque of 55 mkg (equivalent to 539 Nm). The pre-chamber combustion principle ensured that the engine ran particularly smoothly. The contemporary brochure emphasises the longevity from the 1950s perspective: "Mileages of 200 000 km or more with no repairs at all are common for the OM 315 engine." One of the reasons behind the effortlessly superior power delivery was the by today's standards short axle ratio of 5.85:1: at a rated engine speed of 2100 rpm, the LAK achieved a top speed of 70 km/h, or 46 km/h when the off-road gear ratio was engaged. For optimum driveability in difficult terrain, the ideal speed was just 5 km/h or 3 km/h in first gear at maximum torque. The interior of the compact cab is plain in nature and features what was at the time a very modern full-width windscreen. Features emphasised by Mercedes-Benz in the brochure included the adjustable driver's seat, the double co-driver bench seat and the stowage facilities: "large pockets in the door panels for the vehicle documents and a large stowage box". The brochure also pointed out coat hooks and a reading lamp – a small nod to luxury in the austere 1950s. The all-wheel-drive dump truck occupied a special place in the range. "The point where the road ends is where the LA 315 prefers to work," states the brochure, promising "a long service life, even under constant load when working off-road." For off-road use, the LAK 315 featured a six-speed constant-mesh gearbox with an additional step-down ratio. When the driver activated it, front-wheel drive was engaged at the same time. The semi-elliptic leaf springs on both axles absorbed even the roughest of unevenness. One of the few optional extras available was an exhaust flap engine brake. The standard-specification three-way tipper was "a sturdy platform made of wooden planks covered in sheet metal". The exhibited vehicle with its distinctive red/yellow paintwork was built in 1955. It originally comes from the Emil Bölling collection and is today owned by the Wörth truck plant. Mercedes-Benz 2624: the indestructible short-nosed truck The classic long-nosed trucks disappeared from the range at the end of the 1950s. This was due to the German traffic legislation of the time, which specified clear length and weight limits. Mercedes-Benz responded by introducing a short-nosed truck in 1959, featuring an engine that protruded slightly into the cab to save space – a true speciality of Mercedes trucks. In 1963, the brand expanded its range for the first time following the Second World War by adding heavy-duty three-axle trucks designed specifically for construction and short-radius distribution. The appearance of the heavy-duty short-nosed trucks was typified by the self-supporting chassis-body structure, the oval grille and the position of the likewise oval headlamps in the bumper. The heavy trucks were allowed on the road with 22 t and off the road with 26 t permissible GVW. Within just a few years, Mercedes-Benz became the market leader for heavy-duty construction vehicles with its characteristic short-nosed trucks. The short-nosed trucks set standards, especially the exported models. They even had a worldwide career with production and assembly in Germany, South America, South Africa, Nigeria, Iran and Saudi Arabia. Produced for decades, the robust trucks survived several model changes of the cab-over-engine trucks which were introduced at the same time. It was not until the end of the 1970s that official sales of the heavy-duty short-nosed trucks ceased. However, they continued to be supplied on customer request up until 1982, and there were even several small series produced in Germany right up until 1995, latterly for an export order for the Middle East. The reason for this extremely long career can be traced back to a truck test conducted in 1971: "In rough off-road use, a load of 18 to 20 t and a GVW of 30 t are always possible without having to fear a bent frame or a broken spring." In the era of the short-nosed trucks, the engines were changed from pre-chamber (indirect) to direct injection. The Mercedes-Benz LK 2624 from 1971 presented here has a 6x4 drive configuration and is powered by the OM 355 six-cylinder in-line engine. It develops 177 kW (240 hp) from a displacement of 11.6 litres and delivers a maximum torque of 814 Nm (83 mkg). The robust drive system benefits from separate drivelines leading to the two rear axles. The truck was systematically configured for high load capacity and functionality, a fact that was also evident behind the wheel, as the testers noted: "The suspension is really stiff, whilst the cab is sober, functional and not exactly quiet." More important for the heavy-duty construction workers were its "robustness, service life and undemanding nature in daily operation." The exhibited Mercedes-Benz LK 2624 with heavy-duty tipper body comes from the Commercial Vehicle Veteran Center (NVC) in Oberhausen, better known among experts by the name of its owner Helmut Hoffmann. Mercedes-Benz 2232 LP: cab-over-engine truck with legendary V10 engine Cab-before-engine or cab-over-engine – this remained a controversial issue among truck buyers up until the 1960s. At Mercedes-Benz, it took a long time for the cab-over-engine trucks of the LP series to supersede the short-nosed trucks from the L series. The letter "L" stands for "Lorry", the "P" for Pullman. This name can be traced back to the legendary comfortable railway sleepers made by the American manufacturer Pullman Palace Car Company. Mercedes-Benz achieved the breakthrough with cab-over-engine trucks in autumn 1963 when they unveiled the cubic cab, which was new at the time. The angular cab offered maximum use of the space and was considered extremely sophisticated. As the first generation was not tiltable, numerous flaps were included in the design for maintenance and repair purposes, which led some mockers of the time to describe it as an "advent calendar". From 1969 onwards, this version and the subsequently introduced tilting cab featured the all-new engines from the 400 series. These units with their characteristic V arrangement for the cylinders underwent continuous development and were the measure of all things for heavy-duty trucks until the mid-1990s. The most powerful version of the LP with cubic cab, from 1971 onwards, was the V10 OM 403 with a displacement of 15.9 litres, an output of 235 kW (320 hp) and a torque of 1010 Nm (81.5 mkg). The engine, which was both powerful and light, also featured in the exhibited LP 1632 from 1975. For use as a tipper, Mercedes-Benz provided a very short axle with a ratio of 7.21:1, good for a top speed of around 65 km/h with high pulling power at low speed. The synchromesh transmission – still not installed in trucks as a matter of course - had four basic gears, a range-change gearbox and a crawler gear, giving a total of nine forward gears. As one contemporary test stated: "Thanks to the low-lying V engine, the engine cover only protrudes about 20 cm into the cab." And another advantage: "Finally an ashtray that is big enough and in the right place, which three passionate smokers would struggle to fill in three days." Tester's summary: "A happy synthesis between output and economy, harmonious tuning of all major units, refinement, and first-class suspension. By today's standards, an almost complete commercial vehicle in the heavy-duty class." Mercedes-Benz 1635: new-generation long-runner Mercedes-Benz launched new heavy-duty trucks with the name "New Generation" (NG) in 1973. They were extensively further developed over the years – "NG 80" (1980), NG 85 (1985) and SK (heavy class, 1988) – until being superseded in the range by the Actros in 1996. At the heart of this success was a timelessly designed cab with a large sloping windscreen and low side windows. Beneath the cabs of the heavy-duty versions were the familiar V6, V8 and V10 engines, initially in naturally aspirated form with 141 kW (192 hp) to 235 kW (320 hp). The power was transmitted to durable planetary axles via synchromesh transmission - initially made by ZF, subsequently produced in-house. They were capable of withstanding high loads and at the same time ensured significant ground clearance – important attributes for construction vehicles. Long leaf springs enhanced comfort in the dump trucks. Head of Truck Development Arthur Mischke at the presentation: "Since drivers of construction site trucks generally have a harder lot than the motorway specialists, our genuine concern was appreciation of the short-haul driver." One hallmark feature of the new series was a modular system for cabs, frame and drive system for construction, short haul and long haul. The series would signal the end of cab-behind-engine trucks in the coming years. Mercedes-Benz openly stated its case: "Because the cab-over-engine truck is the future." Above all, however: "The new Mercedes truck is a more economical truck because it is more than just a new vehicle. The new Mercedes is a new system." An early road test contained high praise: "Frankly, you have to admit that Daimler has done a good job with the new two and three-axle dump trucks." In practice this means: "You can organise wild off-road rides and load the vehicles to their limits without even really noticing it behind the steering wheel." This system and its heavy trucks benefited from numerous further developments during its long era. For instance, the engine displacement, output and torque all increased and, following the introduction of turbocharging and intercooling, reached record levels. Designed specifically for construction, the powerful V10 impressed as a naturally aspirated engine with a displacement of 18.3 litres and an output of 259 kW (352 hp) The final generation of turbocharged V8 engines achieved an output of up to 390 kW (530 hp) and a torque of up to 2300 Nm - pretty impressive even by today's standards. The classic Mercedes-Benz 1635 model from 1987 is a two-axle tractor unit with tipper semitrailer from the NG 85 phase. This generation impressed with its completely modernised cockpit and, above all, its EPS electro-pneumatic gearshift. It was a first precursor to the fully automated Mercedes PowerShift 3 transmission which is today installed as a matter of course. With an output of 260 kW (354 hp) and a torque of 1600 Nm, the Mercedes-Benz 1635 exactly met transport companies' requirements for heavy-duty applications on the construction site or in medium-duty long-distance haulage. .
-
View, test, compare and buy construction vehicles: the Application Information Center (BIC) in Wörth, Germany Daimler Press Release / November 14, 2017 Around 40 dump trucks, mobile concrete mixers and building material platforms as complete vehicles Demonstrations of Hydraulic Auxiliary Drive (HAD) A successful concept for informed buyers for more than 17 years Enjoy a close inspection of construction vehicles with different tonnages, axle configurations and bodies without any sales pressure. Drive all the trucks in their laden state on and off the road, with expert and neutral advice, and purchase complete solutions there and then – this is only available to this extent at the Mercedes-Benz Application Information Centre. Adjacent to the customer centre and directly at the gate of the Wörth truck plant, prospective buyers can come here to test a wide variety of trucks. Up to 13 000 visitors make use of this opportunity every year. Around 40 dump trucks, concrete mixers and building material platforms standing ready Up to 170 trucks of all model series and tonnages are available at the Application Information Centre throughout the year: tractor units with semitrailers, food transport and refrigerated vehicles, short-range distribution and beverage trucks, quick-exchange containers and many more. Some 60 well-known bodybuilder partners have their sector-specific solutions on display here. The main focus of the Application Information Centre is on trucks for the construction industry, of which there are around 40 here at any one time. From the Mercedes-Benz Arocs, Actros and Atego to the Fuso Canter – customers can inspect the entire spectrum here. The range comprises two, three and four-axle models, three-way and rear-end tippers, tipper trailers, tippers with loading crane, skip loaders and roll-off tippers, mobile concrete mixers and concrete pumps as well as building materials platforms with crane. The Application Information Centre is much more than a display of vehicles: knowledgeable advisers from Mercedes-Benz are on hand to provide information, going into all the details of the bodies. The high practical relevance of the Application Information Centre is unique in the commercial vehicle sector: not only do customers have the opportunity to take a close look at the current new products and features from Mercedes-Benz and Fuso, the vehicles can also be tested and test-driven there and then. A direct comparison of vehicles with very different bodies is the best way to make a decision as to which truck, with which equipment and which body, best corresponds to individual requirements. It is possible to take test drives with laden vehicles in real conditions, both on- and off-road. The Application Information Centre also hosts sector-specific information days, such as the legendary dump truck show days at the nearby Ötigheim testing ground or the convention of the ready-mix concrete sector. Demonstrations of Hydraulic Auxiliary Drive (HAD) A current focus is the demonstration of the Mercedes-Benz Arocs with Hydraulic Auxiliary Drive (HAD). This is the name given to an especially ingenious hydraulic auxiliary drive system for the front wheels, with wheel hub motors for occasional off-road use. For road-going vehicles, driving demonstrations of Predictive Powertrain Control (PPC) also form a major part of these activities. Such occasions are an opportunity for customers to experience for themselves the advantages of anticipatory cruise control out on the road. The system detects the topography of the route ahead and intervenes automatically to control the speed and change gear in order to optimise consumption. This leads to a predictive style of driving based on perfect knowledge of the vehicle and road. A successful concept for well-informed customers that began 17 years ago The Application Information Centre in Wörth started out on 1 June 2000 with 14 bodybuilders, ten suppliers and 21 sector solutions on a presentation area opposite the plant's customer centre. Today the entire truck range plus bodies await visitors on an area of around 17 500 m². While the Application Information Centre is a display that aims to inform rather than sell, its trucks are exchanged on a rolling basis after about three months and a maximum mileage of 2000 km. It is possible to purchase complete vehicles here without having to wait for delivery. The demonstration vehicles held at the Application Information Centre are not registered and can therefore be registered for the first time in the customer's name. Truck and body are sold through the company's sales and service outlets and agents in a dual-invoice transaction.
-
The Class 6 1217 is a decontented Mitisubishi Canter, while the Class 8 2528 is loosely based on the old "Axor" (again, decontented immensely for the Indian market price point). Old is new.....in India. But totally unacceptable for North America including Mexico. Why this will fail: Mexican operators have been Americanized.....they prefer conventionals. A real North American Freightliner enjoys excellent parts availability, and low parts pricing. Mexican operators will consider an Indian truck a step down. They prefer US trucks. This wouldn't fly in Brazil. Why in the world think of trying it in Mexico?
-
Daimler Introduces Pair of Mexico-Specific Cabover Trucks David Cullen, Heavy Duty Trucking (HDT) / November 15, 2017 GUADALAJARA, MEXICO — The rollout of two new market-specific cabover trucks in Mexico exemplifies Daimler Trucks overarching strategy of acting globally but thinking locally. To help cement its dominance of the Mexico truck market, the German-based company unveiled two new Freightliner 360 cabover trucks on Nov. 15, the Class 6 1217 and the Class 8 2528. The two trucks join the existing Class 4 715, introduced back in 2008, in the Freightliner 360 family aimed at urban trucking applications. “We’re proud to be at home here [in Mexico] for many years and decades,” said Martin Daum, member of the Daimler AG board of management and global head of Daimler Trucks and Buses, at a Nov. 15 press conference at Expo Transporte, the biggest truck and bus show in Latin America. Daum noted that Mexico is not only a market for Daimler but a production hub for the OEM. Expanding on how the company views world markets, he said that as a truck OEM, Daimler recognizes that “no one buys a truck who doesn’t need it. It’s our job to adjust to customer demands, which we do through technology. “We are a global company,” he continued, but one that views and acts in each market singularly. “Daimler is a German company in Germany. An American company in the United States. And a Mexican company in Mexico.” Daum said that’s why the company has an extensive manufacturing operation as well as a dedicated force of both engineers and sales personnel in place here. At a customer sneak preview of the new trucks held the night before, Daimler Trucks North America President and CEO Roger Nielsen pointed out that the new 360 cabovers demonstrate the advantage of being able to customize Daimler’s global truck platform for regional markets, right down to submarkets, such as in this case for trucks designed to work well in Mexico’s demanding urban applications. Flavio Rivera, president and CEO of Daimler Trucks Mexico, said that the 360 trucks were developed “in response to the characteristics and needs of the Mexican transport industry… [so] the new generation of 360 trucks constitutes an innovative family of products to meet the most specific needs of our customers’ business.” According to Daimler Trucks Mexico, the two new 360 trucks will stand out in the local cabover market thanks to such key differentiators as “a much more customizable chassis, a renovated cab layout, two passenger seats, and optimal accessibility thanks to its wide doors and handles strategically placed within the cabin.” The OEM said both new trucks offer “exceptional maneuverability, a reinforced steel cab ready to bear any bodywork safely, a wide, spacious interior, high corrosion resistance, a proprietary Daimler powertrain, ergonomic design, and a versatile chassis that allows for many different configurations.” The new 360s are also the first Freightliner vehicles powered by Euro V-compliant SCR engines to be commercialized in Mexico. Daimler stated that means they are setting the stage to “the production of cleaner vehicles with lower environmental impact and greater fuel efficiency.” The Class 6 360 1217 is powered by a 170-horsepower Mitsubishi engine mated to a 7-speed Mercedes-Benz G85 transmission. It can haul 8 tons of payload and features an adjustable telescopic steering wheel, electric windows and locks, air conditioning, and standard fog lamps. The Class 8 360 2528 is powered by a 280-horsepower Mercedes-Benz engine and is mated to a Mercedes-Benz G131 manual transmission. The 2528 can handle 17 tons of payload and is available with an extended cab. Key features include available rear and frontal stabilizer bars, ergonomic dashboard, engine and exhaust braking system, optional sleeper cab configuration, and a fuel efficiency diagnostic system. “The 2528 is the best equipped in its class with air conditioning, electric locks and windows at a highly competitive price,” Daimler stated. “By releasing these two models, we want to maintain our position of undisputed market leadership in Mexico and capture the cab-over-engine segment, said Nielsen. “We hope to help transform this country’s commercial vehicle industry in the areas of safety, driver-centric design, and reliability,” he added. .
-
Daimler Press Release / November 14, 2017 At the Performance Days, the Arocs demonstrates the full spectrum of its capabilities, from tipper to heavy-duty tractor unit and from 4x2 to 8x8 Arocs: the highly specialised all-rounder among the heavy-duty construction vehicles More variants, more comfort and yet more safety: the Arocs 2017 Numerous new features available: lower roof heights, new tilting hydraulics package ex factory, tyre pressure monitoring system Networked services: the diverse range of solutions from Fleetboard Mercedes-Benz Uptime also available for construction vehicles: avoid breakdowns, increase availability 4 engines, 18 output ratings and transmissions with 8, 12 and 16 gears Hydraulic Auxiliary Drive and turbo retarder clutch available for new vehicle variants Three all-wheel drive systems for the most diverse operating conditions It is as individual as the diverse tasks performed by operators in the construction sector: the Mercedes-Benz Arocs is a specialist covering the entire repertoire of construction transport. The broad range of cabs, engines, drive variants and wheel configurations ensures it is able to cope with all types of deployment. Tipper, materials transport or heavy-duty tractor unit – the Arocs fits the bill every time. New variants have been added to the Arocs this year, setting new benchmarks in practicability, efficiency and safety, as well as comfort. The Arocs Performance Days see the construction specialist demonstrating the full scope of its capabilities - on the road, in the gravel pit and in extreme terrain on the legendary "Sauberg" test circuit. Around a dozen Arocs are available for tests and demonstrations, from 4x2 to 8x8 and from tipper to concrete mixer. These vehicles are flanked by the Mercedes-Benz Actros, the Actros SLT heavy-haulage vehicle, the Atego and the Fuso Canter 4x4. Four classic trucks additionally represent Mercedes-Benz construction vehicles' long-standing traditions. Arocs: the highly specialised all-rounder among the heavy-duty construction vehicles It is the out-and-out pro for construction transport: the Arocs from Mercedes-Benz is a dedicated model series comprising heavy-duty trucks designed specifically for the construction sector. Four years after its world premiere, the Arocs is available in an extremely broad and continually growing range. The Arocs is available in every conceivable wheel configuration - 4x2 and 4x4, three-axle 6x2 with trailing or leading axle, 6x4 and 6x6. Four-axle versions are available as 8x2 trucks with trailing axle, 8x4, 8x4 with trailing axle, 8x6 and 8x8. The scope of equipment and variants covers steel and air suspension, frames designed primarily for on- or off-road deployment, numerous wheelbases, cabs and engines, three all-wheel-drive systems, platform trucks, tippers, concrete mixer chassis, heavy-duty tractor units and special-purpose vehicles. Ready-for-use specialists make the choice easier. The Arocs Loader is systematically configured for a low kerb weight and high payload as a two-axle tractor unit or as a concrete mixer chassis. The design factors concerned here include cab, chassis, engine variant and tyres. The Arocs Grounder is an extremely robust specialist for particularly tough applications. Characteristic features are a highly robust frame, multi-leaf parabolic springs with hard compliance characteristics, specially tuned shock absorbers, planetary hub reduction axles and particularly durable rims and tyres with high load-bearing capacity. Arocs SLT and Actros SLT: dynamic heavy-duty tractor units The Arocs range culminates in a spectacular heavy-duty tractor unit. A gross vehicle combination weight of up to 250 t, three, four and with a dock axle as many as five axles, two driven axles or all-wheel drive, an engine as strong as an ox with an output of up to 460 kW (625 hp) and 3000 Nm of torque, 16 finely graduated gears of the Mercedes PowerShift transmission – the Mercedes-Benz Actros SLT and Arocs SLT heavy-duty tractor units boast spectacular performance data. The tailor-made concept for the SLT includes the turbo retarder clutch (TRC) combining hydraulic start-off clutch and retarder in a joint component. The TRC facilitates sensitive moving off and manoeuvring even at the lowest of speeds and as a primary retarder generates 350 kW (476 hp) of braking power. Together with the High Performance Engine Brake generating an output of up to 475 kW (646 hp), the TRC offers the ultimate in safety. The radiator, hydraulic system, the fuel tank with a capacity of 900 litres, the compressed-air chamber and further components are housed in the elegantly trimmed rear cooling tower. The diverse SLT model variants break down into the two model series Arocs SLT and Actros SLT. The steel-sprung Arocs SLT based on the particularly robust Arocs Grounder is also available with the BigSpace cab as well as the StreamSpace cab measuring 2.3 m in width. The air-sprung Actros SLT is available with the spacious GigaSpace and BigSpace cabs measuring 2.5 m in width. As a high-tech heavy-duty tractor unit, the SLT is designed for a gross vehicle combination weight of up to 250 t. For the construction industry the focus is on it as a semi-heavy-duty tractor/trailer combination for transporting heavy construction machinery. In this case the additional radiator system and optionally also the TRC can be dispensed with. The permissible gross vehicle combination is up to 120 t, or up to a maximum of 155 t with certain restrictions. More variants, more comfort and yet more safety: the Arocs 2017 The current model range shows how the Mercedes-Benz Arocs continually adapts to customers' needs and wishes. When the Arocs needs to be scaled down at construction sites and entrances, the ClassicSpace LowRoof in M and L variant with a width of 2300 mm is a contender, for example. It is 100 mm lower than the original variant. In combination with the OM 470 engine, 320 mm engine tunnel and ClassicSpace LowRoof, the roof height is even reduced by 280 mm. The Home Line and Style Line design and equipment lines are now also available for the Arocs with 2.5 m wide cab. The SoloStar Concept with its spacious rest area for the StreamSpace and BigSpace cabs turns the Arocs into a tipper boasting added comfort. The Arocs also offers new options in the area of the suspension and powertrain. The electrically supported Servotwin steering is now also available for the four-axle Arocs 8x4 and for other wheelbases, for example. The engageable hydraulic starting-off aid HAD (Hydraulic Auxiliary Drive) can additionally be used on semitrailer tractor variants with 3300 mm wheelbase for transporting hazardous goods. New options for the Arocs with HAD are the 320 mm engine tunnel for L cabs and a cover to provide protection from bulk goods in conjunction with the M cab. Drivers needing to move off very carefully or who manoeuvre at low speeds should choose the turbo retarder clutch (TRC). This can be combined with Proximity Control Assist and Active Brake Assist on all Arocs 6x4 chassis with air suspension and front underride protection. Together with the OM 471 engine an additional power take-off rated at up 80 kW and 350 Nm can be realised in combination with the TRC. From April 2018, a new tilting hydraulics package will be available ex factory for the two-axle Arocs 4x2 and Arocs 4x4 semitrailer tractors. The hydraulic system is configured as a single or dual-circuit system depending on intended use. The Arocs also leads the way in terms of safety. Mercedes-Benz is now offering it with the option of a tyre pressure monitoring system featuring a new display concept, for example, that displays the precise pressure required, depending on the outside temperature. Above all, the two- and three-axle Arocs approved for road use (N3) is optionally available with new Active Brake Assist 4, the only emergency braking assistant with pedestrian detection. For construction vehicles with a focus on road transport, Mercedes-Benz has developed an Actros as a 4x2 LS semitrailer tractor to complement the Arocs. The key deployment area for the tipper body is transporting bulk goods with a total weight of up to 44 t. The semitrailer tractor features six centimetres more ground clearance and is available with an optional pivoting step. It weighs up to 150 kg less than an equivalent Arocs 4x2. The semitrailer tractor is available with 320 mm and 170 mm engine tunnels and the OM 470 and OM 471 engines in all output ratings. A further advantage of the road-oriented Actros in construction transport is that it is optionally available with the entire broad range of safety assistance systems that feature on board the road vehicles, including revolutionary Sideguard Assist to protect pedestrians and cyclists. With this equipment on board, the Actros is predestined for construction sites in urban settings, for example. Networked services: the diverse range of solutions from Fleetboard Construction transport is not all excavation, robustness, maximum traction and rubber boots - construction transport also entails fine-tuned logistics, frequently in extreme conditions. It is generally far more complex than road transport, as various partners require to be coordinated on site and dozens of vehicles may need to be deployed together for a single task. The solution for this mammoth task goes by the name of networking. Just the job for Fleetboard and its diverse scope of functions, which go well beyond the bounds of a telematics system. Fleetboard is able to draw on almost two decades of experience with networked services and the effective use of acquired data. The Truck Data Center is the optional connectivity module which forms the core of the networked Arocs. This is where all real-time data are received and transmitted. The hardware receives data from all the sensors, cameras, etc. on board the truck and analyses this information for the most diverse applications. The vehicle computer also serves as the interface for all networked services and is responsible for the truck's external communications. This results in a wealth of useful services, software applications and apps within the Logistics Management, Vehicle Management and Time Management segments, spanning scheduling, performance analysis, time recording and mass storage memory download - so that all relevant driver and truck data can be read remotely, relaxed and archived in compliance with the law. The option of recording the type of operation and displaying the time spent stationary with the engine running is particularly interesting for application in construction transport, as a means of determining the exact fuel consumption while stationary and on the move. Positions and the courses of trips are recorded continuously, noting the times when PTOs are activated and when the engine or ignition is switched on or off. Geofencing provides information on the vehicle's position and status, with automatic notifications when the vehicle leaves or enters production plants or construction sites. As construction sites and unloading points do not generally have conventional postal addresses, the route guidance system is also able to operate solely on the basis of geo-coordinates. Fleetboard Store for apps: open platform boosts efficiency The new Fleetboard Store for apps is the marketplace for truck-related apps. Customers, industry partners such as bodybuilders, and app developers can use the open platform to make apps available for all parties involved in the transport process. The operator selects apps in the Fleetboard Store and sends them to the driver tablets DispoPilot.guide in individual trucks, several trucks or all the trucks in a fleet. Mercedes-Benz Uptime: avoid breakdowns, increase availability The ideal truck runs without any breakdowns. With Mercedes-Benz Uptime the Arocs applies intelligent networking in pursuit of this ideal – even in the toughest conditions encountered in construction transport. Uptime continuously checks the vehicle systems which are equipped with sensors. This also includes the status of wear parts and operating fluids such as AdBlue. When an impending need for repair or maintenance work emerges, the truck relays this information automatically via Fleetboard to Mercedes-Benz Service. The data are analysed in real time and forwarded to the service organisation with specific recommended courses of action. If there is an acute risk of a truck breaking down, the service organisation will contact the customer and organise a stop at a workshop along the planned route. In addition, repair and maintenance requirements which are identified in good time are relayed automatically to the Mercedes-Benz service partner selected by the customer. The service partner bundles pending items of work and arranges an appropriate appointment with the customer in accordance with the trip planning and the required maintenance. Information and specific recommended courses of action for upcoming repairs that can easily be carried out in-house are made available to the customer in a timely manner via the Mercedes-Benz Uptime portal and by e-mail. This boosts availability substantially. Uptime is now available in 18 European markets and also Turkey. The diversity and individuality of the Arocs – as exemplified by the cabs Radiator grille with striking bucket-tooth look, rippled outside mirror housing, pivoting step, three-part bumpers with steel corners – the Arocs is instantly recognisable as a robust truck for heavy-duty construction transport. Two cab widths, three lengths, two engine tunnel heights and a level floor add up to nine different basic cabs. From the compact ClassicSpace S cab to the spacious BigSpace L cab, the Arocs covers every requirement, including special features such as cabs with a lowered roof. All the available options together result in around two dozen different variants. Anyone wishing to refine their Arocs can choose between the two optional design and equipment lines Home Line and Style Line for the 2.5 m wide cab, or even indulge in the SoloStar Concept with its spacious rest area on the co-driver's side. Engines: choice of four engines in 18 power ratings There is a huge range of engines to match. State-of-the-art six-cylinder engines with 7.7 litres, 10.7 litres, 12.8 litres and 15.6 litres displacement cover all requirements. In all there are 18 output ratings to choose from, spanning the range in small steps from 175 kW (238 hp) to 460 kW (625 hp) and from 1000 Nm to 3000 Nm. Powerful and efficient: the latest generation of the Mercedes-Benz OM 470 The spotlight is currently on the latest generation of the OM 470 in-line six-cylinder engine, which combines maximum efficiency with minimal emissions and outstanding performance. Its new features at a glance: increased maximum rail pressure and maximum injection pressure of 2700 bar, new seven-hole injection nozzle with higher flow rate, asymmetric injection between cylinders one to three and four to six, new combustion chamber geometry with an omega-shaped recess in the piston, increased compression, patented infinitely variable exhaust gas recirculation with reduced rate. The new turbocharger is produced in-house. The engine is operated exclusively in pre-controlled mode. There is no wastegate valve, boost pressure control, EGR sensor or EGR control system. The top model of the Mercedes-Benz OM 470 engine range is a variant generating an output of 335 kW (456 hp) and a powerful 2200 Nm of peak torque. These figures highlight the outstanding performance of the OM 470. With a specific output of 31.4 kW per litre of displacement (42.7 hp/l) and specific torque of 206 Nm/l, the OM 470 is one of the most powerful engines in its size category. This provides customers with a choice of two different characters of engine with the same rating: the OM 471 with its emphatically brawny performance in the lowest rev range, and the compact OM 470 offering slightly more power in the middle and higher rev ranges and weight savings of some 150 kg in comparison to the engine with the larger swept volume. All heavy-duty drive systems: engine oils, transmissions and PPC optimised The 10.7 litre Mercedes-Benz OM 470 as well as the larger six-cylinder in-line OM 471 with a displacement of 12.8 litres and the 15.6 litre OM 473 benefit from additional efficiency measures. These comprise new low-friction engine oils, a more advanced transmission and axles and a further refined driving strategy for the anticipatory cruise control system Predictive Powertrain Control (PPC). The OM 473 additionally highlights the enhanced X-Pulse injection system. Here too, the maximum rail pressure has been raised from 900 to 1160 bar. At the same time, the maximum injection pressure has increased to 2700 bar. The output and torque variants of the OM 473 have remained unchanged, as have its charging and exhaust gas recirculation technology. The 18 engine variants for the Arocs The fourth engine remains the compact and lightweight Mercedes-Benz OM 936 six-cylinder in-line unit with a displacement of 7.7 litres. This engine is recommended for solo operation and, depending on the output rating, for occasional towing use primarily on the road and without exploiting the permissible vehicle combination weights to the full. The Mercedes-Benz OM 936 with a displacement of 7.7 litres is available in five variants for the Arocs: Output Torque 175 kW (238 hp) at 2200 rpm 1000 Nm at 1200 - 1600 rpm 200 kW (272 hp) at 2200 rpm 1100 Nm at 1200 - 1600 rpm 220 kW (299 hp) at 2200 rpm 1200 Nm at 1200 - 1600 rpm 235 kW (320 hp) at 2200 rpm 1300 Nm at 1200 - 1600 rpm 260 kW (354 hp) at 2200 rpm 1400 Nm at 1200 - 1600 rpm The Mercedes-Benz OM 470 also comes in five ratings, including the new top-of-the-range variant: Output Torque 240 kW (326 hp) at 1600 rpm 1700 Nm at 1100 rpm 265 kW (360 hp) at 1600 rpm 1800 Nm at 1100 rpm 290 kW (394 hp) at 1600 rpm 1900 Nm at 1100 rpm 315 kW (428 hp) at 1600 rpm 2100 Nm at 1100 rpm 335 kW (456 hp) at 1600 rpm 2200 Nm at 1100 rpm The OM 471 range also spans five variants: Output Torque 310 kW (421 hp) at 1600 rpm 2100 Nm at 1100 rpm 330 kW (449 hp) at 1600 rpm 2200 Nm at 1100 rpm 350 kW (476 hp) at 1600 rpm 2300 Nm at 1100 rpm 375 kW (510 hp) at 1600 rpm 2500 Nm at 1100 rpm 390 kW (530 hp) at 1600 rpm 2600 Nm at 1100 rpm The top-of-the-range engine is the Mercedes-Benz OM 473 in three output ratings: Output Torque 380 kW (517 hp) at 1600 rpm 2600 Nm at 1100 rpm 425 kW (578 hp) at 1600 rpm 2800 Nm at 1100 rpm 460 kW (625 hp) at 1600 rpm 3000 Nm at 1100 rpm Transmission with 8, 12 and 16 gears The engine, transmission and axle of the Arocs all bear the Mercedes star and are perfectly matched. As standard, fully automated Mercedes PowerShift 3 model series transmissions take care of power transmission with 8, 12 or on request 16 gears. A direct shift mechanism from first to reverse gear facilitates rapid manoeuvring. The "Offroad" or "Power" drive programs each have various drive modes and adapt to the given individual type of operation. Additional functions support the driver, for example the engageable rocking mode for traction problems in off-road terrain. Manual gearshifts are also available optionally. Anyone having to move off particularly sensitively and wear-free with high weights can choose the turbo-retarder clutch (TRC). This combines a hydraulic start-up clutch and retarder in a single component. Three all-wheel drive systems for the most diverse operating conditions For off-road use Mercedes-Benz offers different all-wheel drive variants. If the payload and fuel consumption are to the fore, the engageable all-wheel drive is the right choice. If maximum traction is called for, the solution is permanent all-wheel drive plus a low-range ratio. The third variant, the "Hydraulic Auxiliary Drive" (HAD), has caused a sensation in the sector. With engageable wheel hub motors at the front axle HAD covers road-oriented use with occasionally increased traction requirements. With HAD the Arocs reveals itself to be a true all-rounder. The driver engages HAD by pressing a button. The necessary slip-sensitive power transmission is then efficiently and steplessly controlled. The advantages of the hydraulic drive are the comparatively low added weight, benefits in terms of fuel consumption and emissions, and great versatility in configuring the vehicle. In the case of Mercedes-Benz, these qualities are complemented by maintenance-free design, low fuel consumption with activated hydrostatic drive and, above all, the combination with the Mercedes PowerShift transmission. The Arocs HAD sets benchmarks in its segment: it is powerful, lighter than an all-wheel-drive model, easy to operate, maintenance-free and has a long service life. It lowers fuel consumption and consequently protects the environment as the result of low emissions. In the construction sector, too: cutting costs and fuel consumption with PPC Construction transport is about maximising traction - and minimising costs. For road-oriented based vehicles in particular, every litre of fuel saved means more cash in the company coffers. With this in mind, construction vehicles with Predictive Powertrain Control (PPC) are the right choice for maximum efficiency. PPC adapts gear selection and speed fully automatically to the individual course of the route concerned. The current PPC generation boasts a further refined shift strategy. Shift points have been optimised, and on downhill stretches a hysteresis range adjustable down to 10 km/h saves even more fuel. The effect of PPC is quickly calculable by reference to a typical rigid truck such as the Arocs 8x4/4. In road use, PPC cuts fuel consumption by up to five percent. Assuming an annual mileage of 60 000 km with 35 to 40 percent motorway and A-road driving, PPC can reduce costs by around 400 to 500 Euro per year, depending on the fuel price. This means that the additional investment can pay for itself within around two years. Special-purpose vehicles ex factory: Mercedes-Benz Custom Tailored Trucks (CTT) Sometimes, extreme operations in the field of construction transport call for exceptional vehicles. This is where the experts at Mercedes-Benz Custom Tailored Trucks (CTT) in Molsheim, Alsace, come into play. CTT is the producer of highly specialised vehicles within the Mercedes-Benz Special Trucks unit. CTT manufactures the SLT heavy-haulage vehicle and also produces customised vehicles as one-off items or special series. A major advantage is that CTT operates as a one-stop supplier of customised Mercedes-Benz trucks that come with a single invoice. Duly tested and approved and benefiting from the full scope of warranty coverage and the globe-spanning service offered by the Mercedes-Benz brand. Whatever it takes: from wheelbase modifications to the Arocs as a five-axle truck in 10x4 configuration, CTT produces exceptional truck variants for customers all over the world. .
-
Get the 1QHA front axle arrangement off your line sheet or front axle (stamped), call Watt's Mack and have them look up the 35AX part number and see if they are still available.
-
Sean Kilcarr, Fleet Owner / November 15, 2017 That strategy drove the development of two new Mexico-only Freightliner cabover truck models. Guadalajara, Mexico. To strengthen its position in Mexico’s truck market, Daimler Trucks is adding two new models to its Freightliner “360 Family” of commercial vehicles – the Class 6 model 1217 and the Class 8 model 2528, which join the company’s Class 4 model 715, launched back in 2008. “Mexico is a key part of our global and regional growth strategy,” said Roger Nielsen, president and CEO of Daimler Trucks North America (DTNA) during a customer/dealer event held here during Expo Transporte ANPACT 2017, which is considered the biggest commercial vehicle show in Latin America. He explained that the new models being added to the 360 Family of trucks represent the benefits of having a “global truck platform” that can be customized for regional and local markets. “It’s about bringing to markets specific solutions for meeting customer needs,” Nielsen said. “By releasing these two models, we want to maintain … market leadership in Mexico and capture the cabover engine segment. We also hope to help transform this country’s commercial vehicle industry in the areas of safety, driver-centric design, and reliability.” Martin Daum, member of the board of management at Germany’s Daimler AG and head of the company’s Daimler Trucks & Buses division, noted that Mexico is of “major importance” as a global truck production hub as well. “These new members of the 360 Family will also provide customers with safety, security, reliability, and great efficiency,” he added. Both the new Class 6 model 1217 and the Class 8 model 2528 offer a reinforced steel cabin, a proprietary powertrain, and what Daimler called a “versatile chassis” that allows for many different configurations. They are also the first Freightliner vehicles with Euro V SCR engines to be commercialized in Mexico, setting the path to what the OEM called in a press statement “the production of cleaner vehicles with lower environmental impact and greater fuel efficiency.” The Class 6 model 1217 comes spec’d with a 170-hp Mitsubishi engine married to a seven-gear Mercedes-Benz G85 transmission. It features a payload of eight tons, an adjustable telescopic steering wheel, electric windows and locks, air conditioning, standard fog lamps for better visibility, and will be available with three different axle distances, according to the OEM. The Class 8 model 2528 comes spec’d with a 280-hp Mercedes-Benz engine linked to a Mercedes-Benz G131 manual transmission, with an extended cab option available. The model 2528 provides 17 tons of payload, rear and frontal stabilization bars, air conditioning, electronic locks and windows, an ergonomic dashboard, engine and exhaust braking system, optional sleeper cab configuration, and a fuel efficiency diagnostic system, the OEM said. Both vehicles will come with “uniquely designed” warranty packages that will offer customers three years of coverage with unlimited mileage, the company added, with Freightliner also offering one year with unlimited mileage coverage on batteries. “This new generation and bigger portfolio of 360 trucks is designed to meet the needs of our customers and allow us to be more competitive, to be one step ahead in this market,” noted Flavio Rivera, president and CEO of Daimler Trucks Mexico, during his translated remarks. “They also show how Daimler’s global platforms are flexible enough to be customized for markets like ours.” .
BigMackTrucks.com
BigMackTrucks.com is a support forum for antique, classic and modern Mack Trucks! The forum is owned and maintained by Watt's Truck Center, Inc. an independent, full service Mack dealer. The forums are not affiliated with Mack Trucks, Inc.
Our Vendors and Advertisers
Thank you for your support!