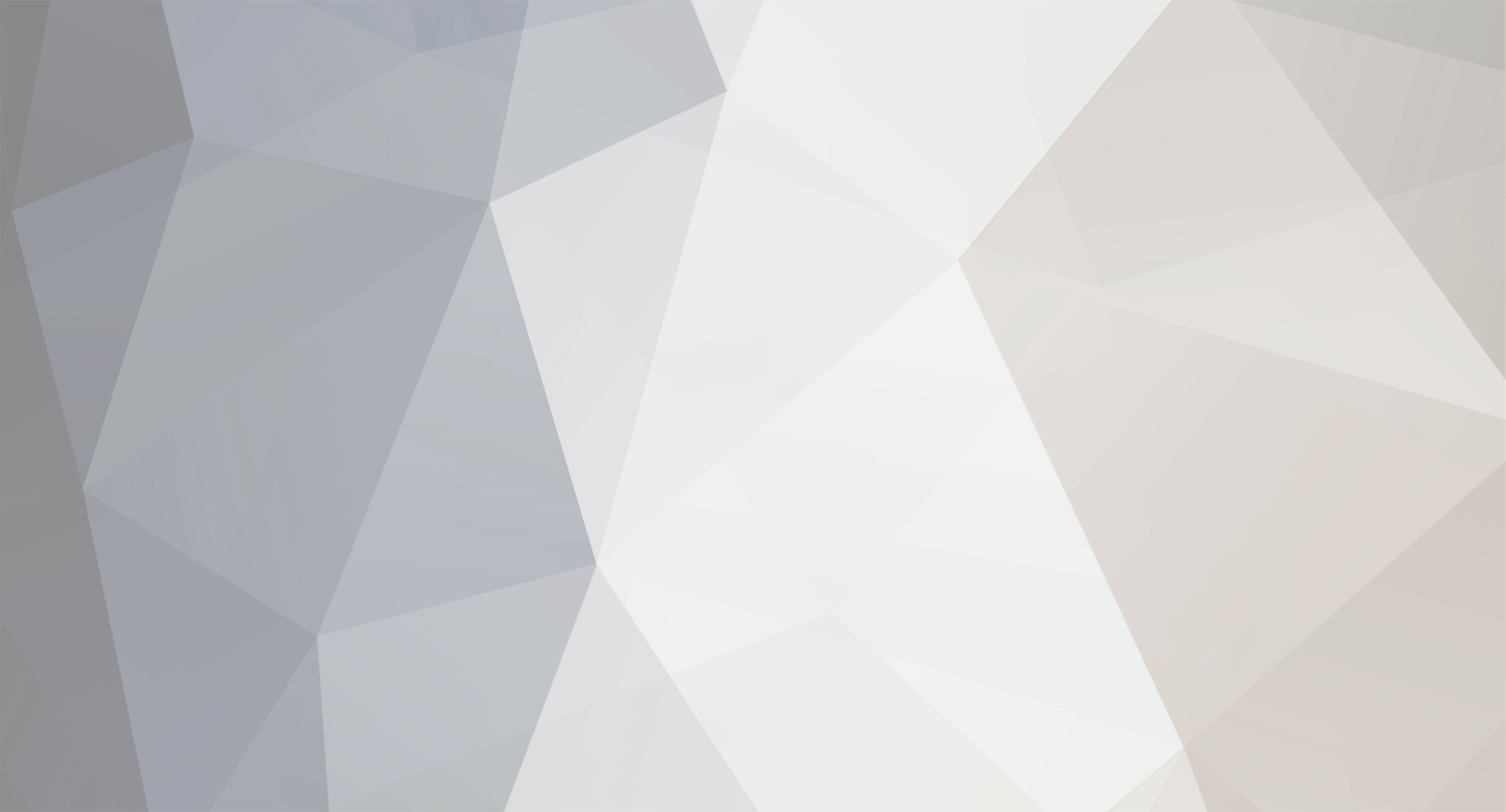
kscarbel2
Moderator-
Posts
18,717 -
Joined
-
Days Won
114
Content Type
Profiles
Forums
Gallery
Events
Blogs
BMT Wiki
Collections
Store
Everything posted by kscarbel2
-
Mark, I generally don't care for conventionals to begin with (though Oz-spec Powerstars and Western Stars are nice). My preference was always the F Model and highly advanced MH Ultra-Liner. Versus the Volvo or Anthem, I'd rather be in a Cruise-Liner. Nowadays, though I'm biased towards the virtually perfect Scania range, many COE's meet my expectations.
-
U.S. secretly settles abuse on Capital Hill with taxpayer money
kscarbel2 replied to kscarbel2's topic in Odds and Ends
There is no better place to be a sexual predator than the U.S. Congress. Think Progress / November 21, 2017 Congress has created an elaborate system that protects sexual predators on Capitol Hill, including members of Congress and their staff. In the private sector and elsewhere in the government, victims of sexual harassment have the option of immediately filing a lawsuit and getting their grievances heard in court. But Congress has created a much different set of rules for victims who work on Capitol Hill. The 180-day statute of limitations to request “counseling” In order to pursue accountability for a sitting member of Congress for an alleged incident of sexual harassment or assault, a victim must file a written notice with the Office of Compliance within 180 days of the incident. If they don’t act within 180 days, they have no ability to pursue their claims. Furthermore, the form to file such a complaint is password protected; a victim must call the Office of Compliance to get the password to initiate the process. The 30-day “counseling” period After filing the complaint, the person alleging harassment or assault must participate in a 30-day counseling period. Yes, in Congress, the victims of sexual harassment must submit to counseling, as if there is something wrong with them. During this period, no one else — including the alleged harasser — is even notified the complaint has been filed. The Office of Compliance puts a sunny face on this process, saying it “provides the employee with an opportunity to assess his/her case before deciding whether to pursue the claim(s) beyond counseling.” In other words, the process starts with a 30-day waiting period in which the victim is given the “opportunity” to consider dropping the entire matter. The 15-day statute of limitations to request mediation After going through the counseling process, the alleged victim has just 15 days to file a request for mediation. If they fail to do so, the claim is extinguished. The form to request mediation is also password protected and must be obtained from the Office of Compliance. The 30-day mediation period After the counseling process, the alleged victim is still prohibited from filing a case in court. Rather, they must enter mandatory, confidential mediation which lasts at least another 30 days. The mediation period involves “the employing office, employee, and [Office of Compliance] mediator.” The purpose of the mediation, according to the Office of Compliance, is to “resolve the dispute.” The individual alleging harassment or assault is also required to keep this mediation secret. “All mediation shall be strictly confidential, and the Executive Director shall notify each person participating in the mediation of the confidentiality requirement and of the sanctions applicable to any person who violates the confidentiality requirement,” according to the poorly named Congressional Accountability Act, which governs the process. The alleged perpetrator may not even be involved in this process, even if the claim is settled. John Conyers, whose case was settled through mediation, claimed he was unaware of any allegations against him — although sources tell BuzzFeed he did know [of course he was told]. There are also indications of misconduct within the Office of Compliance. Conyers’ settlement was confidential but documents were leaked to BuzzFeed. The taxpayer-funded sexual harassment settlement As part of the mediation process, the parties can reach a settlement to resolve the dispute. But this settlement is not paid by the person who actually conducted the sexual harassment. Rather, the settlement is paid by you, the taxpayer. “Only funds which are appropriated to an account of the Office in the Treasury of the United States for the payment of awards and settlements may be used for the payment of awards and settlements under this chapter,” the Congressional Accountability Act states. This is why Conyers did not have to pay a penny of his own money to settle claims against his alleged victims. According to the Washington Post, the Office of Compliance has paid more than $17 million over the past two decades to settle complaints regarding violations of workplace rules, including but not limited to sexual harassment cases. But BuzzFeed’s reporting indicates this doesn’t get at the scope of the problem. At least one settlement with a woman who alleged Conyers harassed her was paid from Conyers’ office budget, not from the Office of Compliance. The 30-day waiting period and 60-day statute of limitations for filing a complaint After making it through counseling and mediation, the victim must wait 30 days before doing anything. It’s unclear what this waiting period is for, other than to pressure the victim to accept a settlement offer or drop the claim. The victim then has just 60 days to either file an administrative complaint with the Office of Compliance or file a case in federal district court. The form to file an administrative complaint is also password protected. If the victim does not take any action within 90 days of the end of mediation, the claim is extinguished. The secret administrative hearing The administrative proceeding, unlike a federal court case, is also confidential and presents another opportunity for a perpetrator to keep the allegations secret [Why?]. The hearings are closed to the public [Why?]. (The hearing officer is empowered to dismiss any claim without a hearing if he or she judges the claim to be “frivolous.”) The responding party is not the individual that engaged in sexual harassment, but the office that employed that person. A record of the proceedings are only made public if the victim is successful. If the victim disagrees with the decision, he or she must appeal first to the board of the Office of Compliance. After the Office of Compliance issue their decision, the victim may appeal to the United States Court of Appeals for the Federal Circuit. That means there will be no independent evaluation of the evidence, rather the appeals court simply reviews for arbitrary or capricious application of the law, a very high legal standard. If the victim wins in the administrative hearing, the payment is made from taxpayer money. They are not entitled to receive civil penalties or punitive damages under the law. This keeps both the awards and the settlements fairly low. Over 20 years, Congress has paid $17.1 million to 264 victims, a figure that includes sexual harassment and other forms of discrimination — an average award of about $65,000. A federal case against a congressional office, not the person engaging in sexual harassment After all this, a victim still cannot sue a member of Congress or other staff member who engaged in sexual harassment [Why?]. Rather, if a victim chooses to forgo the administrative hearing, he or she can file a federal case against the office where the sexual harassment allegedly occurred. In this case, victims are still not entitled to civil penalties or punitive damages. This makes the choice to file a suit, in most cases, prohibitively expensive since even a successful case will not bring in a large award. Whatever money is awarded still is not paid by the sexual harasser but by taxpayers. https://thinkprogress.org/sexual-predator-congress-0802dc2ef524/ -
C'mon Mark. I just post the truck news.....I don't make it.
-
Today's Trucking / November 22, 2017 . .
-
Scania Group Press Release / November 23, 2017 First Scania 13-litre compressed gas truck is instant hit with French haulier. With its strong environmental goals, it is not surprising that French food distribution haulier STAF was eager to become Scania’s first customer for the new 13-litre compressed gas engine truck. “I’d like to get at least another 50 vehicles as soon as Scania can deliver,” says owner and Managing Director Kara Mendjel. With its fleet of 650 temperature-controlled trucks and more than 500 drivers, STAF is the leading distribution haulage company in the Paris region. With the prospect of the city of Paris phasing out diesel by 2025, STAF is starting to renew its fleet; by the end of this year it will have some 65 gas trucks in operation. Gas replacing diesel in French cities Gas is increasingly being seen as the primary alternative to diesel in major French cities. Today, there are ten filling stations in the Paris region but by as soon as next year the number will grow to 25. “We’re really seeing a rapid development in gas,” Mendjel notes. At filling stations, vehicle owners can select between the slightly more expensive biogas, with carbon emission reductions of up to 90 percent, or natural gas, with CO2 savings of up to 15 percent. Regardless, both alternatives offer a 50-percent reduction of nitrogen oxide emissions and 40 percent lower emissions of particulate matter. “There are approximately 13 million residents in the Paris region and operating trucks on gas will definitely improve the environment and the quality of life for Parisians,” says Medjel. First Scania gas truck being deployed The first Scania 410 hp truck will be deployed for deliveries to Carrefour, Leader Price, Franprix, Casino, Monoprix, Simply Market, Leclerc and Intermarché supermarkets. “There’s always an element of risk in being the launch customer but I have full confidence in Scania and the brand’s record in powertrain excellence,” concludes Mendjel. .
-
- 1
-
-
Scania Group Press Release / November 22, 2017 First came Nicolas, then Jérôme and finally Sophia. Today, the Faramia triplets have reached the age of 31 and are all active in the family transport business that bears their initials, Transports NJS Faramia. With the motto “The environment lies at the heart of our concerns”, the family has taken the bold decision to become France’s first haulage company to deploy a Scania ethanol truck. The truck will be used for temperature-controlled deliveries in the Marseille area. Given the company’s green philosophy, the Faramia family has high hopes for ethanol, with its 90-percent reduction of carbon emissions, 50-percent fewer emissions of nitrogen oxide and 70-percent less particulate matter. Having introduced ethanol engines in the 1980s, Scania has ample experience of the fuel, and has now released its fourth-generation ethanol engine. Faramia will have its own ED95 filling pump at their main depot in Vitrolles. The ED95 fuel will be produced from pomace – the residue from grape pressing – from local wineries. The pomace will be collected and processed by Union des distilleries de la méditerranée in Vauvert, near Montpellier. “Another big step towards becoming fossil free” Heavy vehicle-grade ED95 fuel was granted favourable taxation status by the French Government earlier this year. Ethanol qualifies for the highest environmental level in the French Crit’Air air quality vehicle certification scheme, which is in force in major French cities. “We already have gas trucks and now we’re taking another big step towards becoming fossil free,” says Jérôme Faramia. “Ethanol is the most abundant alternative fuel in the world and we see a great potential.” The truck will be used in deliveries for the French international frozen food retailer Picard, which has more than 1,000 shops in France as well as operations in six other countries. Picard is equally excited about the new venture and will be avidly following its progress. Meanwhile, the Faramia family will closely monitor performance and cost. “If the truck performs as expected, I can easily imagine that one-quarter of our trucks can run on ethanol,” says Jérôme. .
-
Volvo Trucks Press Release / November 22, 2017 Nikolai Goncharov drives his Volvo FMX through the remote Siberian landscape. Here the forces of nature must be challenged, both by driver and truck. Follow his journey as he takes on 120 kilometres of uncertain Russian forest roads. “We don’t have roads here – we just have a direction.” .
-
Solutrans innovation Awards: Urban Lab 2 receives the Low Emission Driveline Award Renault Trucks Press Release / November 22, 2017 Renault Trucks has won the “Low Emissions Driveline Award” for its laboratory distribution vehicle, Urban Lab 2. This prize, awarded by the LUTB Transport & Mobility Systems cluster and the PFA Automotive Industry and Mobilities, as part of the Solutrans Innovation Awards, was presented to the manufacturer at the Lyon Chamber of Commerce and Industry on 21 November 2017. On Tuesday, 21 November 2017, at the Lyon Chamber of Commerce and Industry, Renault Trucks was presented with the "Low Emissions Drivetrain Award" for its laboratory distribution vehicle, Urban Lab 2. This prize, awarded as part of the Solutrans Innovation Awards 2017, is organised by the LUTB Transport & Mobility Systems cluster and the PFA Automotive Industry and Mobilities and recognises a significant breakthrough or innovation in the powertrain of transport vehicles. Receiving this award, François Savoye, Energy Efficiency Strategy Director at Renault Trucks, reminded those assembled that the diamond-badged manufacturer focused most of its Research & Development efforts on reducing emissions. “Diesel now provides an effective response to the needs of the road freight transport sector. Urban Lab 2 demonstrates the untapped potential that still exists, particularly with hybridisation.” In addition to engine hybridisation, Urban Lab 2 combines innovative technologies associated with aerodynamics, tyre performance and vehicle-to-infrastructure communication with the aim of reducing fuel consumption by 13%. The Urban Lab 2 laboratory vehicle is the result of the EDIT (Efficient Distribution Truck) collaborative project, financed by the Single Inter-Ministry Fund, Auvergne Rhône-Alpes Region, Métropole de Lyon, Ain Department Council and the FEDER. Designed based on a 19-tonne Renault Trucks D WIDE Euro 6 diesel, Urban Lab 2 targets the urban and regional distribution sector and its on-board technologies have been developed in conjunction with six partners: Valeo, Lamberet, Michelin, BeNomad, INSA Lyon (LamCoS) and IFSTTAR (LICIT). .
-
Renault Trucks Press Release / November 23, 2017 Renault Trucks is a pioneer and has a century of experience in electro-mobility. The manufacturer is developing and testing several types of technologies in real operating conditions in collaborations with its customers. Hybrid technologies and 100% electric have been integrated to several types of vehicles: from 3.5 tons up to 16 tons. Our ambition is to prepare zero-emission solutions, profitable for our customers, by 2020. .
-
-
https://www.bigmacktrucks.com/topic/47464-ford-market-news/?page=4&tab=comments#comment-385639
-
Once upon a time, we actually enjoyed privacy
kscarbel2 replied to kscarbel2's topic in Odds and Ends
Uber paid hackers to delete stolen data on 57 million people Bloomberg / November 22, 2017 SAN FRANCISCO -- Hackers stole the personal data of 57 million customers and drivers from Uber Technologies Inc., a massive breach that the company concealed for more than a year. This week, the ride-hailing firm ousted its chief security officer and one of his deputies for their roles in keeping the hack under wraps, which included a $100,000 payment to the attackers. Compromised data from the October 2016 attack included names, email addresses and phone numbers of 50 million Uber riders around the world, the company said Tuesday. The personal information of about 7 million drivers was accessed as well, including some 600,000 U.S. driver’s license numbers. No Social Security numbers, credit card information, trip location details or other data were taken, Uber said [Don’t believe it]. At the time of the incident, Uber was negotiating with U.S. regulators investigating separate claims of privacy violations. Uber now says it had a legal obligation to report the hack to regulators and to drivers whose license numbers were taken. Instead, Uber paid hackers to delete the data and keep the breach quiet. Uber said it believes [They have no clue] the information was never used but refused to disclose the identities of the attackers. “None of this should have happened, and I will not make excuses for it,” Dara Khosrowshahi, who took over as CEO in September. “We are changing the way we do business.” After Uber’s disclosure Tuesday, New York Attorney General Eric Schneiderman launched an investigation into the hack. Uber was also sued for negligence over the breach by a customer seeking class-action status. Hackers have successfully infiltrated numerous companies in recent years. The Uber breach, while large, is dwarfed by those at Yahoo, MySpace, Target Corp., Anthem Inc. and Equifax Inc. What’s more alarming are the extreme measures Uber took to hide the attack. Kalanick controversies The breach is the latest scandal Khosrowshahi inherits from his predecessor, Travis Kalanick. Kalanick, Uber’s co-founder and former CEO, learned of the hack in November 2016, a month after it took place. Uber had just settled a lawsuit with the New York attorney general over data security disclosures and was in the process of negotiating with the Federal Trade Commission over the handling of consumer data.. Joe Sullivan, the outgoing security chief, spearheaded the response to the hack last year. Sullivan, a onetime federal prosecutor who joined Uber in 2015 from Facebook Inc., has been at the center of much of the decision-making that has come back to bite Uber this year. The board commissioned an investigation into the activities of Sullivan’s security team. This project, conducted by an outside law firm, discovered the hack and the failure to disclose. Here’s how the hack went down: Two attackers accessed a private GitHub coding site used by Uber software engineers and then used login credentials they obtained there to access data stored on an Amazon Web Services account that handled computing tasks for the company. From there, the hackers discovered an archive of rider and driver information. Later, they emailed Uber asking for money. A patchwork of state and federal laws require companies to alert people and government agencies when sensitive data breaches occur. Uber said it was obligated to report the hack of driver’s license information and failed to do so. “At the time of the incident, we took immediate steps to secure the data and shut down further unauthorized access by the individuals,” Khosrowshahi said. “We also implemented security measures to restrict access to and strengthen controls on our cloud-based storage accounts.” Flouting regulations Uber has earned a reputation for flouting regulations in areas where it has operated since its founding in 2009. The U.S. has opened at least five criminal probes into possible bribes, illicit software, questionable pricing schemes and theft of a competitor’s intellectual property. San Francisco-based Uber also faces dozens of civil suits. London and other governments have taken steps toward banning the service, citing what they say is reckless behavior by Uber. In January 2016, the New York attorney general fined Uber $20,000 for failing to promptly disclose an earlier data breach in 2014. After last year’s cyberattack, the company was negotiating with the FTC on a privacy settlement even as it haggled with the hackers on containing the breach. The company finally agreed to the FTC settlement three months ago, without admitting wrongdoing and before telling the agency about last year’s attack. The new CEO said his goal is to change Uber’s ways. Uber said it informed New York’s attorney general and the FTC about the October 2016 hack for the first time on Tuesday. Khosrowshahi asked for the resignation of Sullivan and fired Craig Clark, a senior lawyer who reported to Sullivan. The men didn’t immediately respond to requests for comment. Khosrowshahi said in his emailed statement: “While I can’t erase the past, I can commit on behalf of every Uber employee that we will learn from our mistakes.” The company said its investigation found that Salle Yoo, the outgoing chief legal officer who has been scrutinized for her responses to other matters, hadn’t been told about the incident. Her replacement, Tony West, will start at Uber on Wednesday and has been briefed on the cyberattack. Kalanick was ousted as CEO in June under pressure from investors, who said he put the company at legal risk. He remains on the board and recently filled two seats he controlled. Uber said it has hired Matt Olsen, a former general counsel at the National Security Agency and director of the National Counterterrorism Center, as an adviser. He will help the company restructure its security teams. Uber hired Mandiant, a cybersecurity firm owned by FireEye Inc., to investigate the hack. The company plans to release a statement to customers saying it has seen “no evidence of fraud or misuse tied to the incident.” Uber said it will provide drivers whose licenses were compromised with free credit protection monitoring and identity theft protection. -
Around one hundred people, including police, witnessed this man murder 8 people on the New York bike path. Which is to say, that he’s a murderer is not in dispute. So seriously, what's the point of the typical drawn out process at taxpayer expense? And why would the government even consider life in prison over immediate execution? https://www.bigmacktrucks.com/topic/42652-paris-under-attack/?page=11&tab=comments#comment-384024 --------------------------------------------------------------------------------- Associated Press / November 22, 2017 A grand jury on Tuesday returned a 22-count indictment against an Uzbek immigrant accused of killing eight people during an ISIS-inspired truck attack on a bike path in New York City. Sayfullo Saipov, 29, of Paterson, New Jersey, was charged in Manhattan federal court with providing material support to ISIS, along with eight counts of murder and 12 counts of attempted murder in aid of racketeering. If convicted of the most serious counts, he could face life in prison [???] or the death penalty. Saipov was arrested after people were run over by a vehicle October 31 in a midday attack that authorities labeled terrorism. Of the eight people killed, five were friends from Argentina celebrating 30 years since their high school graduation. A Belgian woman, a New Yorker and a New Jersey man also lost their lives, and 12 others were injured. Saipov's initial court appearance in connection with the indictment is scheduled for November 28. Acting US Attorney Joon H. Kim said 'scores of videos and images on his cellphone' will be part of the evidence in the case against Saipov. 'Like many terrorists before him, Saipov will now face justice in an American court,' Kim said. 'And like New York City's response to his alleged attack, we expect that justice in this case will be swift [???], firm and resolute.' William F. Sweeney Jr., head of New York's FBI office, said the indictment should signal 'that the rule of law will always prevail.' Authorities said he made statements after his arrest about his allegiance to ISIS, which later took credit for the deadly attack, and told investigators he 'felt good' about the killings. Saipov was shot in the abdomen by a police officer after crashing the truck into a school bus. His injury was minor enough that he was transferred to a prison facility in Manhattan two days later. The terror suspect came to the US legally in 2010 from Uzbekistan. He first lived in Ohio, where he was a commercial truck driver, then in Florida. He most recently lived in New Jersey with his wife and children, and worked as an Uber driver. President Donald Trump has called for Saipov to be executed, tweeting a day after the attack: 'NYC terrosit was happy as he ased to hang ISIS flag in his hospital room. He killed 8 people, badly injured 12. SHOULD GET DEATH PENALTY!' A capital punishment case would be extremely rare in New York, which has abolished the death penalty at the state level.
-
Cultural decay and declining standards of behavior in the United States. ------------------------------------------------------------------------------------------------------------------------------ The Miami Herald / November 22, 2017 (Cleveland, Ohio) Keirian Kelly, a white man, is accused of taunting his 70-year-old neighbor by calling her the n-word. Kelly encouraged his 4-year-old son to call the woman the n-word as well, and threatened to stab the woman. Kelly was arrested in August and is charged with ethnic intimidation, a fifth-degree felony. There were multiple incidents of harassment, starting in June. The threats against the woman began after she accidentally fell onto Kelly’s wife in the lobby of the St. Clair Place apartment building on East 13th Street. An argument erupted and racial slurs, including the n-word were hurled. A security guard later called the police after putting Kelly in handcuffs. Then on August 10, the woman was walking down a street when Kelly saw her. Kelly then yelled racial slurs and spat on her. He then threatened to kill her and her son, and also encouraged his 4-year old child to call her the n-word. According to the FBI, hate crimes have seen an increase. In 2016, there were 6,100 reported incidents of hate crimes, while in 2015, there were more than 5,800. Of the hate crimes categorized by Race/Ethnicity/Ancestry, 50.2 percent were motivated by anti-Black or African American bias. .
-
Trump and Immigration (Illegal Immigrants in the US)
kscarbel2 replied to kscarbel2's topic in Odds and Ends
Terrorist-like beheadings and cutting out hearts? An ISIS-like organization out of control in our backyard. One is forced to ponder, are your children safe out and about alone? Many in the country illegally (but not all), the government can't go after people it doesn't know are here (hence the reason for ridding the country of illegal aliens and eliminating so-called sanctuary cities). -
Trump and Immigration (Illegal Immigrants in the US)
kscarbel2 replied to kscarbel2's topic in Odds and Ends
The new America - Who’s in control ??? (The authorities are one or more steps behind....reactive rather than proactive) ------------------------------------------------------------------------------------- Notorious gang 'behead man' near Washington AFP / November 22, 2017 Washington (AFP) - The ultra-violent Latino street gang MS-13 that President Donald Trump has vowed to wipe out beheaded a man and cut out his heart before burying him in a park near the US capital. The victim was stabbed more than 100 times in Wheaton, Maryland just outside Washington DC, according the Montgomery County Police Department. Police found the body buried in a grave, deep in the woods of Wheaton Regional Park, that the attackers dug before the slaying. The investigation began in early September, when detectives spoke to an informant who said he knew of an MS-13 murder that occurred in the spring of this year in the park. The informant led detectives to the gravesite. The remains were exhumed and examined by the Maryland Medical Examiner’s Office. Authorities have so far arrested Miguel Angel Lopez-Abrego, 19, on first-degree murder. Lopez-Abrego is a citizen of El Salvador, is in the United States illegally and is currently in immigration proceedings, officials from U.S. Immigration and Customs Enforcement said Wednesday. Investigators say Lopez-Abrego helped dig the grave and “waited near the edge of the wood line with a handheld walkie-talkie radio to alert the other suspects of the victim’s arrival.” He also used a 15-inch knife in the attack. Charging documents added the victim was decapitated and had his heart removed from his chest, in an attack planned for two weeks and involving up to 10 people. The victim was a Hispanic man, about 5-foot-2 and weighing 126 pounds. He had short, dark brown hair and was wearing a gray sweatshirt with “First United Methodist Church Laurel” written on the upper left side. On Sept. 29, patrol officers stopped a car driven by another MS-13 member in which Lopez-Abrego was a passenger. Detectives interviewed Lopez-Abrego, but he denied any involvement in the park murder. Montgomery police tried to find Lopez-Abrego after that interview but couldn’t. Law enforcement agents, looking for a different MS-13 suspect from Maryland — Milton Portillo-Rodriguez, accused of a murder in Anne Arundel County — tracked that man to Avery County, North Carolina. On November 4, a group of 10 agents from the U.S. Marshals Service and the local sheriff’s office arrived at a condominium. A person — but not the suspect — answered the door. The deputies and agents found Portillo-Rodriguez, Lopez-Abrego and a third MS-13 member from Maryland attempting to hide inside. The third suspect is accused in a different attack in another secluded part of the same Wheaton park. In that incident, as many as 15 assailants surrounded two victims, punching them, kicking them and striking them with large tree limbs, according to arrest records. The victims were hospitalized but survived. Police identified the suspect in that assault as Edwin Ruiz-Urrutia, 19. He is being held on no-bond status in Montgomery County on charges including attempted second-degree murder and first-degree assault. Avery County Sheriff Kevin Frye said the three gang members found in the apartment hadn’t made much of an impact. “They were new arrivals, and no one really knew who they were.” MS-13, also known as the Mara Salvatrucha gang, is estimated to have 10,000 members in the United States. The gang works as an umbrella grouping of units known in Spanish as "clicas," some of which are larger and more violent than others. It has become a focus of Trump's crackdown on crime, which he claims has surged as a result of borders easily crossed by gang members. Most members trace their heritage to El Salvador, Honduras or Guatemala, and among the members there are as many immigrants as there are US citizens. Many were born in the United States. The brutal slaying at the Wheaton park is part of a resurgence of killings in the Washington region that police and prosecutors attribute to MS-13. In one case, assailants armed with knives lured a 34-year-old to his already-dug grave. A 22-year-old also was taken to a wooded area and ordered to his knees before he was shot in the face. And in another case, an 18-year-old was ambushed near a stream, stabbed and stoned before he died under a bridge of the Capital Beltway. Authorities last week announced they had netted 214 members of the gang in a month-long nationwide sweep. More than half of those picked up in the action which was led by the Immigration and Customs Enforcement (ICE) agency, were arrested on immigration violations. But 93 were dealt federal criminal charges including murder, robbery, drugs and racketeering. -
Bob, engineer means engineer. Ford corporate designated Ford Otosan as the global design center for commercial trucks. They also manage design for Ford Brazil's product range, which is similar but ranges down to smaller GVWs and of course is locally adapted (homologated). The two takeaways from his comments are there is greater emphasis at Ford Otosan in designing commercial trucks for all global markets, and North America is specifically mentioned.
-
Ford Trucks Press Release / November 21, 2017 Our heavy commercial vehicle brand Ford Trucks combines over 55 years of truck manufacturing experience in the global market with the ability to develop special products for different export markets. Following investment in Morocco, Algeria and Ghana, Ford Trucks has now moved one step further in Africa with a new distributor in Cairo, the capital of Egypt. Ford Trucks continues to strengthen and grow in the international market with dealers outside the country. In cooperation with new partner Aljico MISR, Ford Trucks will launch the 1843t XHR, 3543t LR, 1833 DC, 3543d DC and 4143m DC models in Egypt. These models have been specially designed in accordance with the hot and dusty conditions of the region. Our new generation of Euro 6 Ford “Ecotorq” engines are produced at our powertrain plant in Eskisehir Inonu, Turkey, and are strategically important for our sustainable growth globally. We are working on advanced technologies to offer products that will compete in all potential export markets, including Ford Otosan, not only in Turkey but in Europe and North America. 500 of the 1500 engineers at the Ford global truck R&D center are working to develop heavy commercial vehicles for international markets. "As Ford trucks, we continue to expand our network of dealers in accordance with our goal of being in total 50 countries as of 2020,” says Ford Trucks International markets director Emrah Duman. “The African market has a very important place in our global growth plans. Egypt has launched a new development move with investments in transportation and construction projects amounting to 14.4 billion euros. Furthermore, 90% of cargo transported in Egyptian are via heavy trucks. This reveals the magnitude of the heavy truck market in Egypt. Depending on the high potential of Egypt, we are planning to open 3 separate facilities in Egypt by the end of 2018 with Aljico Misr, one of the leading distributors of the region. With our ability to develop products for different export markets as Ford trucks, we offer our models to market the geographical and climatic conditions of Egypt. We believe that we are going to increase our market share in Africa with our new facilities and move our customer satisfaction in the region further. " .
-
Discover Renault Trucks T for long haul transport
kscarbel2 replied to kscarbel2's topic in Trucking News
-
13 environmental groups urge USPS to select plug-ins for next-generation delivery vehicles Green Car Congress / November 22, 2017 Thirteen environmental groups working on clean transportation solutions sent a letter to the United States Postal Service (USPS) urging it to select plug-in electric vehicles (EVs) for the next generation of delivery vehicles (NGDV). The USPS fleet travels more than 1.3 billion miles every year and uses more than 180 million gasoline gallon equivalents (GGE) of fuel. Two of the five vehicles USPS are currently considering for the next generation of delivery trucks are plug-in models, the environmental organizations said. The winner of the contract will be announced in early 2018, with deployment likely to begin in Q1 2020. If an electric model is selected, the USPS fleet would be the largest electric vehicle fleet in the world. The USPS operates a fleet of more than 200,000 vehicles in all areas of the United States and its territories; approximately 163,000 of these are right-hand drive, light-duty carrier route vehicles (CRVs) purchased between 1987 and 2001. These vehicles are rear-wheel driven, powered by internal combustion engines, and of aluminum body-on-frame design. The payload capacity is approximately 1,400 pounds. These vehicles are near the end of their designed useful life. The USPS intends to retire this fleet in coming years, and to replace the vehicles with Next Generation Delivery Vehicles (NGDVs). The USPS publicly began the Next Generation Delivery Vehicles (NGDV) acquisition program in January 2015 with a Request for Information (RFI). A Request for Proposal (RFP) was issued in October 2015 which included a statement of objectives in response to feedback received from the supplier community and other stakeholders. In 2016, the Postal Service awarded contracts to six prime suppliers who together were to produce 50 prototype vehicles as part of the next phase of the NGDV acquisition process. Half of the prototypes would feature hybrid and new technologies, including alternative fuel capabilities, USPS said at the time. Since then, the pool has shrunk to five: three single companies—AM General, Oshkosh and Mahindra (India)—and two collaborations—VT Hackney/Workhorse and Karsan (Turkey)/Morgan Olson. Public details on the vehicles are scant, although the VT Hackney/Workhorse candidate is a range-extended electric vehicle. VT Hackney is building the body of the prototype vehicles while Workhorse Group is providing the chassis and powertrain. The USPS received prototype NGDV vehicles the week of 18 September; actual testing by letter carriers began the week of 2 October. Testing sites include Flint and Utica, MI; Falls Church and Leesburg, VA; and Tempe and Tucson, AZ. On a three-week rotating basis, the vehicles will be used over the next six months during normal delivery operations in these diverse weather environments. Testing will focus on each prototype’s comfort, usability, functionality, ergonomics, performance, operations, and so on. Additionally, testing of the vehicles’ durability, components and fuel economy will be conducted by engineers at third-party laboratories. The environmental organizations signing the letter include: CALSTART Electric Auto Association Environment America Environmental Law and PolicyCenter Forth Natural Resource Council of Maine Natural Resources Defense Council Oregon Environmental Council Plug In America Public Citizen Safe Climate Campaign Sierra Club Union of Concerned Scientists
-
Tesla's electric event a victory for entire industry Neil Abt, Fleet Owner / November 21, 2017 Last week’s unveiling of the Tesla electric truck left many unanswered questions. What’s the price tag? How much does it weigh? Tesla CEO Elon Musk did not address those questions at his splashy party, so the finer details will need to wait for another day. On social media, reaction was split between those thinking the Semi was the greatest thing ever and those who met Musk’s many bold claims with skepticism and sarcasm. Regardless of your opinion, Musk deserves a thank you for raising trucking’s profile to heights it has never reached before. Attending the event was surreal. The drinks were flowing and many were dressed as if they were at a nightclub. As Musk arrived in one of the Semis, grown men shrieked with excitement. Afterwards, a young child viewing the truck up close had a look in his eye that made me think it was a night he would not soon forget. The enormity was obvious in the press area, where I was one of six North American trucking journalists sitting alongside dozens of reporters from around the world. There was the New York Times, Fox News, and Rolling Stone. Stories were being written in Chinese, French, and other languages. I even observed Tesla’s broad reach in my Facebook feed, where several friends with no attachment to trucking posted about the Semi. Within trucking, complaints about the public’s lack of respect and understanding of the industry have long been a constant. But on this one night in Los Angeles, the crowd, which stereotypically could be considered “coastal elites,” were hooting and hollering as they learned of the intricacies of trucking from Musk. That’s not to say there were not cringe-worthy moments. His first comments focused on how much faster the Semi is than conventional diesels - something not really important. Beyond performance, he also poked fun at the appearance of today’s trucks as he touted the Semi. To be fair, the truck is sleek and cool, inside and out. Of course, those attributes alone do not guarantee success. Executives with equipment manufacturers say it is one thing to build a handful of trucks, but a different ballgame to pump out tens of thousands of units a year. Stlll, that can’t take away from the star power Musk brings to trucking, even if Tesla is trying to dig out from production problems with its new Model 3. Maybe the Semi will succeed, and further elevate Musk to the visionary figure many of his fans consider him to be. Or maybe not only the truck will fall but the entire company, as suggested by Bob Lutz, former CEO of General Motors, during an interview on CNBC. Either way, we should celebrate last week’s event. It’s another indication just how exciting the next few years will be and may be just what was needed to spark a true youth movement in trucking.
-
Major Fleets Line Up to Test Tesla Semi Transport Topics / November 21, 2017 J.B. Hunt, NFI Industries, Bison Transport Place Reservations for Purchases Large for-hire carriers and major retailers are reserving their places in line to be among the first to test the all-electric Tesla Semi in their operations. J.B. Hunt Transport Services Inc., NFI Industries and Bison Transport Inc. and retailers Wal-Mart Stores Inc., Meijer and Loblaw Cos. confirmed that they have pre-ordered the truck or plan to do so. The Tesla Semi is scheduled to enter production in 2019. J.B. Hunt said it has placed a reservation to purchase “multiple” Tesla Semi tractors, which it plans to deploy in its intermodal and dedicated contract services divisions to support operations on the West Coast. “Reserving Tesla trucks marks an important step in our efforts to implement industry-changing technology,” CEO John Roberts said. “We believe electric trucks will be most beneficial on local and dray routes, and we look forward to utilizing this new, sustainable technology.” J.B. Hunt ranks No. 4 on the Transport Topics Top 100 list of the largest for-hire carriers in North America. Truckload carrier NFI Industries said it will expand its fleet with Tesla’s all-electric trucks to advance its environmental sustainability initiatives. “I am eager for NFI to continue moving toward this next chapter where sustainability plays an even larger role in the story,” said Ike Brown, NFI’s vice chairman and president. “Combining Tesla’s innovative technology with the best practices NFI already has in place, I look forward to further advancing NFI’s position as a responsible corporate citizen while making our dedicated and drayage fleets more sustainable.” With its acquisition of California Cartage Co. in October, NFI operates one of the largest drayage fleets in North America. NFI ranks No. 27 on the for-hire TT100. Wal-Mart has pre-ordered five Tesla Semis for its U.S. operations and 10 more for its Canadian business. “We have a long history of testing new technology — including alternative-fuel trucks — and we are excited to be among the first to pilot this new heavy-duty electric vehicle,” Wal-Mart spokesman Ryan Curell said. “We believe we can learn how this technology performs within our supply chain, as well as how it could help us meet some of our long-term sustainability goals, such as lowering emissions.” Another major retailer, Meijer, also plans to test the vehicle in its fleet. “We have made a small financial commitment to ensure we are at the front of the line to test this new Tesla truck technology, which has the potential to not only reduce our carbon footprint but also realize cost savings that will allow us to keep prices low for our customers,” Meijer spokesman Frank Guglielmi said. “Once our testing is complete, we will validate several factors, including environmental impact and product safety, and make a decision on whether we will complete the purchase.” Canadian food retailer Loblaw Cos. has placed an order for 25 trucks “and will have them in Canada as soon as they’re available,” the company said in a statement. Bison Transport also will be in line to test the Tesla Semi, said CEO Rob Penner, who attended the truck’s Nov. 16 unveiling in Hawthorne, Calif. “We do see potential for electric trucks in our regional and medium-range operations, so this is definitely something that we will fully evaluate,” he said. Bison Transport ranks No. 74 on the for-hire TT100. Penner said the electric truck has far fewer parts and appears much less complicated than today’s diesel trucks. He also cited Tesla’s design features aimed at improving driver comfort and safety. “We will see about how they plan on warrantying and servicing the truck, but 1 million miles on the powertrain does seem logical given it is an electric motor, not a combustion chamber,” he said. “Of course the downside remains range and ultimate flexibility. At least today, the truck would have to operate in a much more confined network today than any diesel equipment.” Penner expressed confidence in Tesla’s manufacturing capabilities. The company is producing quality automobiles and will use much of the same technology in the trucks, he said. “They have legitimate street credibility.” However, key questions about Tesla’s truck remain. In a note to investors, Stifel analyst Michael Baudendistel wrote that Tesla’s presentation raised more questions than it answered. “While the truck was impressive in many ways, we’re not yet sure of the economic case for truckers,” he said. Baudendistel said that assessing the potential return on investment starts with the vehicle’s price, which wasn’t disclosed. Tesla also did not reveal the weight of the truck’s battery pack, which could cut into its payload capacity, he said.
-
Can Tesla Make Electric Work for Trucking? Seth Clevenger, Transport Topics / November 21, 2017 HAWTHORNE, Calif. — Tesla’s success in the passenger-car arena has changed consumers’ perceptions and pushed the limits of what’s possible with electric cars. Can the company’s new all-electric tractor do the same for the commercial truck market? In a splashy unveiling here Nov. 16, Tesla co-founder and CEO Elon Musk revealed his company’s vision of electric-powered trucking with the Tesla Semi, which is set to enter production in 2019. A few days earlier, Musk proclaimed on Twitter that the truck’s unveiling would “blow your mind clear out of your skull and into an alternate dimension.” Although the skulls of those in attendance remained intact, the excitement was palpable as Musk introduced a zero-emissions truck suitable not only for shorthaul and port drayage, but also regional operation with a maximum range of 500 miles on a full charge. Musk said Tesla will build a network of “Megachargers” across the country that eventually will allow its electric trucks to travel anywhere. But as with any infrastructure initiative, that will take time. Early customers likely will need to rely solely on chargers they install at their own terminals. While buyers of Tesla’s luxury electric cars are willing to pay more for something that is fun and cool, trucking companies make their purchasing decisions based on a more sober assessment of the business case. For fleets to invest in electric vehicles, they will need to see a payback in total cost of ownership. That reality was not lost on Musk. In addition to fuel savings, the Tesla Semi will reduce maintenance costs and vehicle downtime because it does away with the internal combustion engine, transmission and aftertreatment equipment, he said. Musk even guaranteed that the truck’s electric powertrain will not break down for a million miles. However, Tesla has not disclosed how much the vehicle will cost or how much it will weigh. The truck’s battery pack could take a significant bite out of its maximum payload, an important factor for fleets to consider. Driver acceptance also will be essential, and that’s where the Tesla Semi’s radically redesigned cab could make a big difference. The driver’s seat in the Tesla Semi is situated in the center of the cab rather than offset to the left, and the steering wheel is flanked by large touchscreens that display all driver information in lieu of a dashboard. Sitting in that seat, a truck driver might feel like he or she is piloting a spaceship rather than a big rig. One can imagine some longtime truck drivers balking at the vehicle’s interior, but it will likely appeal to younger drivers the industry so desperately needs to attract as it faces an aging workforce and a shortage of qualified drivers. Could the opportunity to sit behind the wheel of one of these trucks entice 20-somethings to take a look at trucking as a potential career path? Quite possibly. While Musk captured the industry’s attention with his truck unveiling, Tesla is far from alone in the push to make electric vehicles feasible for commercial transportation. Startup Nikola Motor Co. is preparing to launch a Class 8 hydrogen-electric truck designed for longhaul operation. Established truck manufacturers such as Daimler Trucks and Navistar Inc. also are jumping into electric power, as is Cummins Inc., the industry’s largest supplier of diesel engines. Given this broad level of investment in electric power, it now seems clear that the real question is not if, but when, significant portions of the trucking industry will begin moving toward electric vehicles. To be clear, diesel still appears to have a long run ahead of it as trucking’s primary fuel, but we may be witnessing the emergence of its eventual successor.
BigMackTrucks.com
BigMackTrucks.com is a support forum for antique, classic and modern Mack Trucks! The forum is owned and maintained by Watt's Truck Center, Inc. an independent, full service Mack dealer. The forums are not affiliated with Mack Trucks, Inc.
Our Vendors and Advertisers
Thank you for your support!