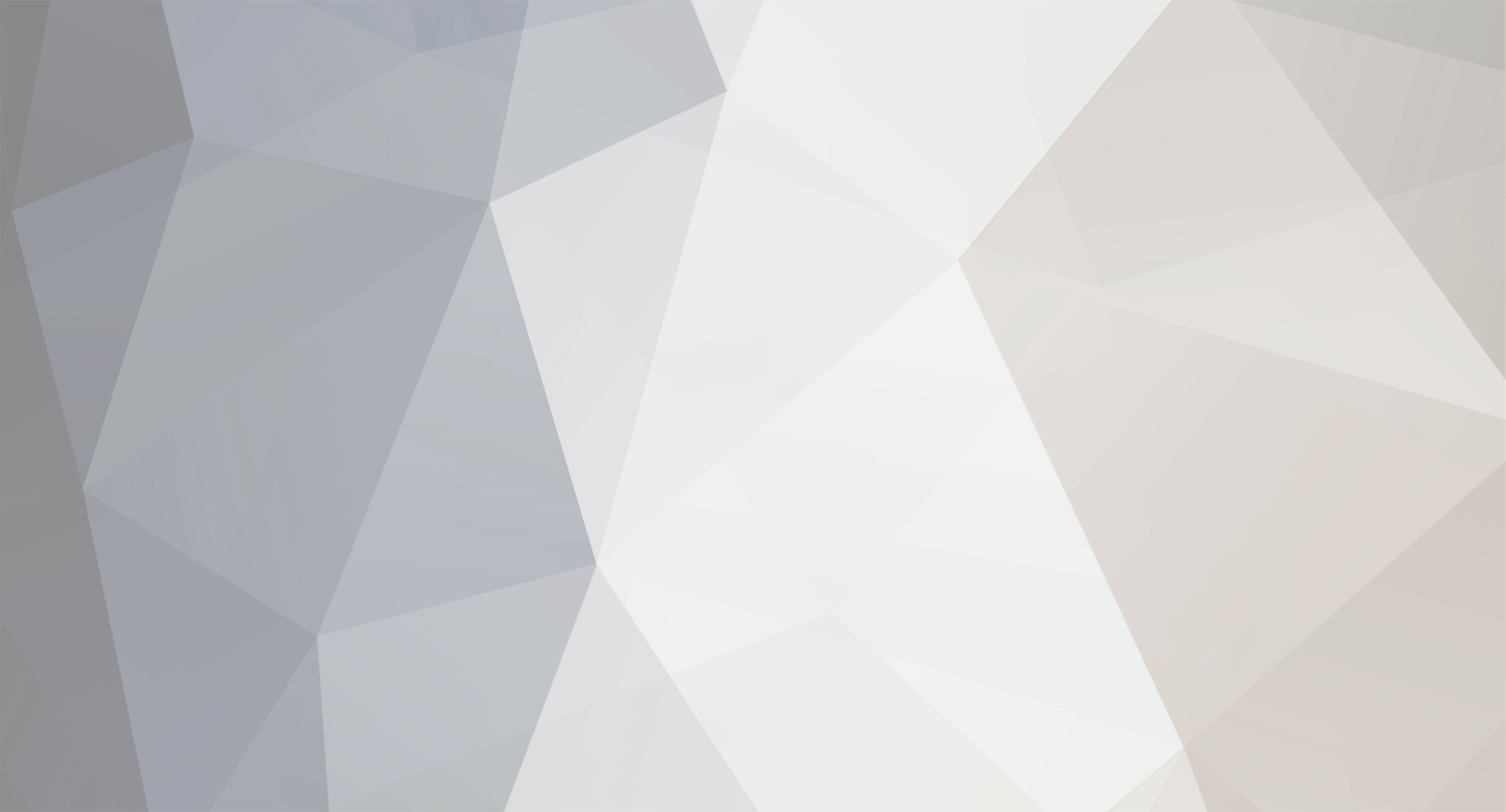
kscarbel2
Moderator-
Posts
17,893 -
Joined
-
Days Won
86
Content Type
Profiles
Forums
Gallery
Events
Blogs
BMT Wiki
Collections
Store
Everything posted by kscarbel2
-
Scania launches next generation “XT” construction range
kscarbel2 replied to kscarbel2's topic in Trucking News
New construction range: A dream mission for Scania’s designers Scania Group Press Release / September 12, 2017 The mission was a dream come true for Scania’s design team – to style a completely new truck range for the very toughest construction operations, and to do it in close cooperation with future users of these new vehicles. The XT range is the second phase in Scania’s new generation of trucks, designed for heavy, tough and rough construction operations. It’s built using Scania’s modular system as a base, but many new parts had to be designed to complete the new range. Describing their work with the new construction vehicles, Scania’s designers sometimes talk about “being true to the materials”. “Everything added to this range has its function and is thought out from the users’ point of view,” Hansén explains. “For example, the new bumper is extremely robust and efficient. There is no plastic and no extra parts – it’s a solid metallic bumper. It’s reliable and it works perfectly, and that’s what its design expresses.” Proud of the teamwork In his work as team leader for the exterior design, Anders Lundgren had to stay true to the key words “athletic”, “dynamic” and “recognisable”, the same key words he adhered to when developing the new generation long-haulage vehicles. “But with these new construction vehicles we introduced another key word – “authentic”, Lundgren says. “In the construction range it’s very much about heavy work,” he continues, “and that should be experienced in the materials we are working with. Being ‘authentic’ means you never compromise with material. It’s a challenge to style parts in four-millimetre high-tensile steel instead of plastics, and make it work together with the rest of the cab and truck. The feature lines had to be adopted in a certain way. Looking at the final result, I’m truly proud of the work the team has done. I do think we succeeded in expressing the strength of the design in a honest and unique way.” Lundgren beats a fist in his palm and explains: “I always had this vision of the bumper and what the construction vehicles do – like the strength of a fist! With the lower front of these new trucks, I really think we got it right.” Driver focus Lead Exterior Stylist Allan Macdonald stresses the importance of Scania’s modularisation in a project such as the new XT range. “Functions are top of the list on a truck like this,” he says. “You can’t have different functions compromising each other. And as the functions are so visible you can’t separate the styling from the function.” Another example of the very visible functions is the side step on the body, which has been integrated in these trucks to let the driver have a good view over the tipper body. “It’s strong, rigid and combined with a steady roof handle for the driver,” Mac-donald says. “This is typically a functionality made for the driver.” The same driver focus is involved in developing a new interior for the construction vehicles. Anna Börjesson Bodestig, Senior Industrial Designer, describes it as “an optimised day cab for a more tough and rough working situation”. “We have focused on making the interior as functional and durable as possible,” she says. “We have optimised many small details – the extendable instrument panel, more flexible storage, a rear window, new seats, new mats with higher edges – all to give the construction drivers their best working environment ever.” Another important focus area for the interior design has been safety. “For a construction driver it’s important to have very good direct vision around the cab and the possibility of reaching all buttons and other things around him or her easily,” she says. “Several small details come together here to optimise the construction driver’s environment.” Safety through colour and material A sometimes forgotten safety factor is the impact of colour and material on the driving environment. For Christina Isomaa, Team Leader of Colour and Trim at Scania’s design team, this is an important matter. “We make colour and material choices optimised for our customers and their needs,” she says. “An obvious aspect is to choose easy-to-clean materials for the interior in order to keep it fresh. Interior colours are created for both comfort and safety at the same time. To handle a heavy construction vehicle in a stressful environment, the focus should be completely on the driving. Our target has been to create safety through our colour harmony in the cab; it should please you, not disturb you.” For the exterior the opposite is true. “Blaze Orange is one colour among many in our Scania palette,” Isomaa says. “The choice here was easy. Orange is a strong colour – a strong colour for a strong brand. It’s also about safety, of course. These vehicles operate in surroundings where their visibility is essential. Orange is, in many ways, nature’s own warning colour.” . -
Scania Group Press Release / August 28, 2017 The Scania heavy tipper is a robust partner in any kind of mining environment. With excellent equipment-to-payload ratio and greatly improved technical availability, it is specially developed for optimised performance in the toughest conditions. .
-
Scania Powertrains - For all requirements and applications
kscarbel2 posted a topic in Trucking News
Scania Group Press Release / September 4, 2017 Scania is constantly extending its range with Euro 6 engines Fuel savings of 7 to 10 percent achieved with the new V8 generation Scania five-cylinder inline engines now in five versions The quartet of 13-litre engines has been complemented by a 370 horsepower version Thirteen different Euro 6 engines have so far been introduced into Scania’s new truck generation, with power outputs of 280 to 730 horsepower, based on three different engine families. Going on sale in June, these were followed by most of the axle and gearbox configurations required to customise construction vehicles, fully-fledged forestry vehicles and heavy haulage tractors, where the focus is on features such as robustness and productivity. Regardless of the choice of powertrain, Scania can now offer even lower fuel consumption, thus helping customers to lay one of the most important foundation stones for the best total operating economy on the bottom line. “As is well known in the industry, construction vehicles are the real all-rounders of the truck world, with an almost limitless number of different tasks and challenges to cope with,” says Anders Lampinen, Product Director, Construction, Scania Trucks. “But regardless of the application concerned or where you are driving in the flow of different processes that are so characteristic of the construction segment, as a Scania customer you must always feel that you get an optimally fuel-efficient powertrain adapted to the task.” In June, Scania showcased a completely new generation of 16-litre V8 engines, which offer a reduction in consumption of 7 to 10 percent, among other things, depending on the type of application for which they are used. The improvement in the V8 engines is mainly based on the fact that they have undergone the corresponding modifications that were first showcased on Scania’s best-selling 13-litre engines when Scania’s new truck generation was premiered in autumn 2016. The modifications include, the fact that with a few rare exceptions Scania now uses only selective catalytic reduction (SCR) for exhaust gas after-treatment, thus allowing the engines to be made both lighter and more robust with a fixed geometry turbocharger, and without exhaust gas recirculation in the form of an EGR system. Updated 9-litre engine Scania’s third engine family was also given a corresponding overhaul with robust, five-cylinder 9-litre engines in three different power levels during the early summer of 2017. Here too it is possible to recoup significant fuel savings in the order of 3 percent. The new features consist of new engine software and a reconfigured combustion chamber. One important change is that the oil cooling is now thermostat-controlled. This contributes a 1 percent fuel saving, since the oil can generally be allowed to maintain a higher working temperature. The cooling fan is fitted directly on the crankshaft and no energy-intensive upshifting is required. What all the DC09s now have in common is that like all* the other engines in the new truck generation, they only use a fixed geometry turbocharger (FGT) and the engines use only selective catalytic reduction (SCR) for exhaust gas after-treatment. “Scania has very good experience of combining a fixed geometry turbocharger and SCR for exhaust gas after-treatment,” Lampinen says. “These are energy-efficient, robust and highly reliable engines, which deliver the power in many construction and distribution vehicles day after day.” Other modifications that help to reduce consumption are an increased compression ratio (from 18.0:1 to 19.0:1), a cylinder pressure increased to a maximum of 190 bar (180 bar for the 280 version) and a more efficient combustion chamber. Strong and robust The DC09 is an engine that is thoroughly tried and tested. It has been part of the Scania range for a long time and has been through a number of changes of generation, which has ensured that it always remains at the leading edge in terms of consumption and driveability. Due to the fact that it delivers 1,700 Nm at 1,050 r/min, with a rapid torque build-up from idling, it does a first-rate job in everything from thousands of heavily laden distribution vehicles to many construction vehicles in which the DC09 is found to be just right for this type of demanding operation, with train weights of around 30 tonnes. The DC09 family shares its technology and design with its six-cylinder siblings in the DC13 in all material respects. Its balance shafts and the introduction of an asymmetric crank pin pitch (ACPP)counteract the tendency of five-cylinder engines to vibrate, so that it now runs just as smoothly and silently as a six-cylinder engine. Its natural clientele are those who need the power, robustness and low consumption of a six-cylinder engine, but who for reasons such as weight do not want to go the whole way to a six-cylinder engine. A taste for biodiesel In June the first engines running on alternative fuels also made their entry into the new truck generation in the form of the DC09 320 and DC09 360. With the right specification, both of these can run on diesel or 100 percent FAME (such as rapeseed methyl ester, RME) or any mixture of the two fuel types. The current 320 and 360 biodiesel engines are the first of many Scania alternative fuel engines. All of Scania’s Euro 6 diesel engines are already certified for a mixture of up to 10 percent biodiesel in their basic configuration, without any impact on maintenance requirements. Pure biodiesel always produces significantly lower carbon dioxide emissions compared with conventional diesel. Some types of alternative fuels, such as hydro-treated vegetable oil (HVO), can produce a reduction in CO2 of up to 90 percent. All of Scania’s Euro 5 and Euro 6 engines in current production can be run on HVO without any restriction, regardless of generation. “Scania’s range of alternative fuel engines has a unique breadth, and there are a lot more in the pipeline,” says Henrik Eng, Segment Director, Urban, Scania Trucks. “The switch to sustainable transport solutions is a priority area for Scania in which we are working both long-term and on a ‘here-and-now’ agenda.” * Except for the DC16 730 . -
Scania launches next generation “XT” construction range
kscarbel2 replied to kscarbel2's topic in Trucking News
-
Scania Group Press Release / September 4, 2017 XT leads the way when Scania increases the breadth and depth of its offering Several day and sleeper cabs in R, G and P versions with different roof heights Axles, frames and wheel suspensions for challenging conditions Clutch pedal for Scania Opticruise – but only where necessary Electric parking brake one of many examples of new options Scania’s focus on tailor-made solutions for each application increases uptime and the earning capacity of construction hauliers who have to cope with tough challenges. Scania continues the introduction of its new, acclaimed truck generation – the time has now come to introduce products and services with a particular focus on construction vehicles. Scania is moving its lines forward and is marking this with the Scania XT, a robust design that caters, in terms of both appearance and function, mainly to those customers who carry out the most challenging tasks with the toughest demands in terms of uptime, productivity and robustness. “The Scania XT is characterised by conspicuous attributes such as an extremely robust front, while also being a clear signal of our ambitions for growth in the construction segment,” says Anders Lampinen, Segment Director, Construction, Scania Trucks. “Three or four years ago we launched an offensive at the European level in which Scania gradually positioned itself as a strong player in the construction sector as well.” The position Scania has built up on the market is the starting point for the introduction of construction vehicles in the new truck generation. Scania is now providing a range of products and services tailored to construction hauliers’ applications – the customers who in all aspects have the toughest challenges and the tightest margins to contend with. The introduction of Scania’s new generation began in autumn 2016 with solutions for 11 applications for long-distance operations. With the introduction of the Scania XT series, P, G and R cabs in the day version, leaf springs and features such as double-drive bogies, construction hauliers now have access to all the eagerly awaited configurations they need to deal with the various challenges they face in their assignments on a daily basis. “We know that there is a great deal of interest in the new truck generation,” Lampinen says. “It has been well received, and of course construction customers have been longing for the new day cabs, more engine options and the typical 6x4 or 8x4 configurations they need. Interest is also strengthened by the fact that we at Scania so clearly prioritise a close partnership with our customers, always putting their ability to achieve sustainable profitability foremost.” .
-
Scania Group Press Release / September 4, 2017 Scania XT can be selected with the full range of P, G, R and S-cabs, regardless of engine. The regular G-cab for the construction industry is available in several heights and lengths. Added to this is a long list of options that are available for a wide array of applications. 1. The highly robust heavy duty bumper extends 150 millimetres from the front of the cab. The bumper allows a wheel angle of approximately 25°, partly depending on the configuration with regard to tyres and chassis. In combination with the skid plate and the light guards, the NN has the necessary robustness to withstand light collisions with objects without damaging the structure behind. 2. At the centre is the easily accessible towing device, behind the foldable registration plate holder. It is certified for 40 tonnes, enabling the vehicle to pull other vehicles and equipment as well as to be towed when needed. Additionally, there is a foldable step for easy access to clean the windscreen. 3. The rear view mirrors have been reinforced with a ribbed casing for added robustness. 4. The slip-proof entry steps – four up to the S-cab or three to the R and G-cabs and two to the P-cabs – are perfectly designed for comfortable and safe cab entry and exit. 5. The compressed 10-bar airgun enables the driver to easily keep the cab tidy from dirt. 6. The G day cab features opportunities for resting while the G sleeper cab has a normal-width bed. 7. The XT comes equipped with rear wall storage bars in the cab with dual bars in the large G-cab. A bin for storing documents and other uses can be attached to the bar. 8. The rear window allows drivers to monitor body equipment such as tippers, hooklifts or mixers during operation. 9. The telescopic tablet holder provides convenient access to on-screen information. 10. For tipper applications, the XT range features a body side step that facilitates overview of tipper movement.
-
Scania Group Press Release / September 4, 2017 Scania today launches the "XT" truck range, which is tailor-made for the construction industry. “This industry is facing increasing demands for sustainable and cost-effective production. Each component in the complex construction logistics process must adapt to higher standards for efficiency and Scania XT is our contribution to this shift,” says President and CEO Henrik Henriksson. The new construction range is the second stage in Scania’s introduction of new generation trucks, the fruits of more than ten year’s development with an investment exceeding EUR 2 billion. Following an extensive analysis of the multi-faceted construction industry, Scania has developed a comprehensive range to meet the highly diverse transport assignments within the sector. Scania XT is uniquely offered for the entire range of cab and engine specifications, from the smallest P-series cab to the spacious S-series cab. Customers can select engines with power outputs ranging from 280 to 730 hp. The broad specifications are complemented by a host of services to ensure the highest uptime, reliability and profitability for customers. The introduction of the XT range by Scania marks the start of a targeted offensive with tailor-made solutions focused on demanding customers in Europe. “We are putting a higher emphasis on construction,” states Henriksson. “We now have the right products, the right services and the right skills to match Scania’s leading position in long-distance vehicles.” Transporters in the construction industry normally form part of a larger process and crucially must avoid disruptions. Scania has therefore – in addition to tough and durable vehicles – created an entire ecosystem of services that ensure uninterrupted deliveries while improving customers’ profitability. “The global construction industry continues to grow and Scania now presents enhanced tools to meet the demand,” says Henriksson. “We are well aware of the slim margins for many hauliers in this business and we have developed vehicles and solutions to ensure sustained profitability.” . . .
-
Scania Group Press Release / September 4, 2017 All variants of G-cabs and a number of P-cabs introduced Special focus on robust short and day cabs for construction applications Electric parking brake with Auto Hold and safety features High air intake in two configurations, operating time up to four times longer Vertical exhaust outlet with two possible positions Large and flexible wheel housings for varying dimensions and needs Several suspension options such as 2x33-millimetre parabolic suspension New combined options with disc or drum brakes and EBS Bodybuilding work made easier and with easily accessible information Scania is now rapidly extending the range of cabs available for the new truck generation. R, S and some G-cabs have already been introduced, and now P-cabs are being added. Several different roof heights and versions can be ordered for all the cabs introduced into Scania’s range as well. In addition, Scania is now introducing features and solutions that are specifically associated with construction applications, such as robust leaf spring suspension, high air intakes and vertical exhaust outlets. Scania continues to expand and extend the number of complete applications and possible configurations for the new truck generation and is now rapidly reaching the point at which the vast majority of customers can order everything they need, regardless of application. The first G-cab was introduced in June; it is now joined by several variants and the long-awaited P-series, which is available in both short and long versions with three different roof heights. “There’s now a really wide range available,” says Anders Lampinen, Product Director, Construction, Scania Trucks. “It ranges from short cabs such as the P14 or G14 cabs with a low roof through to the S20 Highline, which means that the majority of customers can have their new vehicle tailored precisely to their needs and requirements, regardless of application.” The factor that allows Scania to create such a broad offering is, of course, the well-recognised and respected modular approach that Scania has almost brought to completion in the new generation. By using a limited number of different components Scania can build different cabs that externally and in terms of their application look very different, and yet have the majority of parts in common. “The modular design is a strong customer-value proposition,” Lampinen says. “You don’t need to make do with compromises but have access to optimised solutions without compromising costs or jeopardising the supply of spare parts. It doesn’t matter whether you mainly drive in urban areas in the daytime or are on remote country roads and sometimes need to spend the night in the vehicle; each construction haulier can still get just the right cab.” When Scania introduced the R and S-cabs last year they were widely acclaimed for both their external and internal qualities. The exterior was praised for combining contemporary charisma with Scania’s design DNA and best-in-class aerodynamics and the interior for its driver focus, the feeling of quality and spaciousness and the ability to customise the features and solutions that drivers want in their workplace. The G-series (the first variants of which were introduced in June) and P-series cabs now being introduced are naturally based on the same type of approach and solutions as the large sleeper cabs – in fact, they are built using components with exactly the same origin. For many construction hauliers the G-series is well positioned to become the favourite. On the one hand there are several variants to choose from, and on the other it appears to strike a good balance between factors such as size, weight, load capacity and boarding steps. “We think that the CG17N, a day cab with a normal roof, has all the makings of a success in the construction sector,” Lampinen says. “Without encroaching on the space needed for bodywork it offers plenty of space and volume for the driver. Add to this sleek boarding steps, a perfect view out and overview, a single bunk for resting and new options for flexible storage – it’s obvious why we see it as a potential favourite.” The G-cab is available in five different basic configurations ranging from the CG14L with a low roof to the CG20H in the Highline version. With the normal roof, the internal ceiling height is a full 10 centimetres higher than before. Compared with the corresponding R-cab the boarding steps are somewhat lower but the engine tunnel is 16 centimetres higher and does not, provide the same potential for movement in the cab. P-series – the easy choice While the G-series is being topped up with more options, the P-series is now also being introduced for the first time in Scania’s new truck generation. It is possibly even more versatile than the G-series and will have a total of eight different configurations when they are all in place. In the first stage there will be six different P-cab variants ranging from the CP14L with a low roof – particularly suitable as a starting point to make room for highly productive and advanced bodywork that goes over the cab roof – to the CP20H for those wanting comfortable interior spaces, a lower weight and lower boarding steps, with a cab that is mounted lower in relation to the vehicle’s chassis (with the drawback of a higher engine tunnel). “Of course, there isn’t the same demand for all the versions, but for us at Scania it’s a matter of credibility to be able to offer the right variant for applications and requirements that are not so common as well,” Lampinen says. “The entire Scania philosophy of always being able to offer the best total operating economy, thanks to customised solutions for all applications, is based on the diversity and customer benefit provided by the modular system.” The P-series in Europe is mainly intended for customers who rarely stay overnight in their vehicles but who often climb in and out of them. Examples of this are regional or city-based distribution traffic and different types of construction operations. The comfortable boarding steps and the fact that you are more on a level with fellow road users is one of the obvious benefits. A new P-cab with a low roof has the same roof height as a P-cab from the PGR generation (which of course provides compact outer dimensions, so it is good in environments where headroom is limited), whereas a CP17N or CP20N provides a cab that has 10 centimetres more interior headroom than previous versions. The fact that all of Scania’s cabs in the new generation are somewhat longer (CP17 rather than CP16, for example) has to do with the fact that the interior spaces have increased lengthwise, measured in decimetres as the distance from the torpedo wall in the foot-well to the rear wall of the cab, thanks to more efficient packing. Electric handbrake Scania is now also introducing an electric parking brake option for the first time. Its actual location is the same, slightly to the right of the panel in front of the driver, but the control is more reminiscent of what is available in modern passenger cars (albeit sized for a truck). The control is pressure-sensitive, which means that it can be applied gradually. Since the parking brake is electrically controlled, it can also be equipped with new functionality. One example is that it is automatically applied if the speed is low and the driver releases the safety belt or the door is opened – a smart safety feature that ensures that stressed drivers never experience the horror of seeing their parked truck starting to move. This is a feature that has been requested by major transport buyers, mainly in the distribution segment. The hill hold functionality has also been enhanced. When the electric parking brake’s Auto Hold position is activated, there is no time limit on how long it will hold the vehicle. It is also automatically reapplied when the truck stops again, such as in traffic queues). If the vehicle is stationary for slightly longer, it automatically switches from Auto Hold (which uses the service brakes, when a green parking brake symbol is displayed) to the parking brake (which uses the spring brakes and displays the customary red parking brake symbol). One aspect of all types of driver assistance systems is that they must not cause unnecessary annoyance. Scania engineers have therefore paid special attention (after carefully studying passenger car brands such as VW and Audi) to factors such as take-off being as smooth as possible, regardless of whether the parking brake or the Auto Hold function is being disengaged when the driver, with a gear engaged and the engine running, requests it via the accelerator pedal. If the vehicle has been parked with the parking brake activated, it is disengaged (provided that all criteria for activation such as seatbelt are met) and the truck automatically switches to Auto Hold to drive off smoothly. Several pieces in the construction offer With the wide introduction of components and solutions with a particular focus on applications in the construction sector, Scania is now also introducing a raft of other eagerly anticipated components and solutions. To some extent these are components and configurations that were previously in Scania’s construction offer, but many are completely new or are ones that have been further developed and improved. The latter category includes options such as high air intakes (in addition to the standard front-mounted air intake) in two different versions, one of which is specially designed for heavy-duty applications. High air intakes are intended for driving in dusty and exposed environments and help to ensure high uptime without affecting fuel consumption because of long inlets and clogged filters. The HD version of the Scania has two air filters and can handle nearly 40 kilos of dust before service is required, thus quadrupling the operating time compared with earlier solutions. A solution with a vertical exhaust outlet is also now available. What is new is that it can be fitted in two different positions behind the cab, thus facilitating some bodybuilding work. For construction vehicles in particular, cab suspension is of particular importance, both in relation to driver comfort and balancing this against robustness. Scania is now offering mechanical four-point suspension in two different versions. The heavy-duty variant allows greater cab movement to avoid impact during really tough off-road driving. Another feature that is appreciated by construction hauliers is the option to customise wheel housings and mudguard edges to the choice of suspension and wheels. Specific cases include those whowant plenty of room for unimpeded driving with snow chains or with really coarse single-mounted tyres. Scania is also now introducing newly developed, fully adjustable mudguards for the second axle for vehicles with double front axles. Regardless of the choice of tyres and chassis, the mudguard can be easily adjusted to the right height. Suspension and chassis Construction vehicles are highly dependent on having chassis compositions that match their normal tasks. The choice of steel or air suspension is controlled by a number of parameters; a not uncommon configuration is to use a combination of steel and air suspension with front parabolic suspension and rear air suspension. Scania is now introducing yet another option, 2x33 for 9-tonne front axles, progressive parabolic suspension in steel with two 33-millimetre leaves. This results in a balanced compromise between comfort, off-road characteristics and stable road holding. A newly developed anti-roll bar for the second axle also helps with road holding on vehicles with double front axles. It contributes to stability on public highways off-road (particularly if the centre of gravity is high) and especially when tipping on uneven surfaces. As for axle and chassis solutions, Scania is introducing a number of new features that are particularly relevant to applications in construction operations. For example, the new generation allows an electronic brake system (EBS) to be combined with drum brakes on 3-axle vehicles. Another innovation from a specification perspective is that it is now possible to combine disc brakes with a 26-tonne bogie, RBP735 with hub reduction. Scania has also switched to helical gears in the planetary gears for hub reduction, which contributes to both a reduced noise level and increased service life. From the bodybuilder’s perspective Over the course of the years Scania has made a great effort to simplify and make it easier for customers and bodybuilders to customise the vehicles, an investment that has really borne fruit. Some obvious examples in the new truck generation are that Scania has introduced an upper row of holes on the frame that bodybuilders are free to make use of, the rear shock absorber towers and double front axles do not protrude over the frame, and the electrically-controlled tag axle introduced in autumn 2016 has ensured that it is no longer necessary to have any bulky and exposed hydraulic pipes. Scania has now also prepared routings and outlets for both electrics and air, which make things easier for bodybuilders, thus making improvised solutions superfluous. “We receive daily evidence of appreciation,” says Torben Johansson, Director of Scania’s Bodybuilding Centre in Södertälje. “Bodybuilders are aware of the fact that we have high aims and are serious when we say that we are there to give them support. Just like we do with the truck deal itself, we seek to establish a partnership. When we talk the same language it’s immediately evident in much-reduced lead times, increased productivity and a better night’s sleep for all involved.” Apart from developing and making it easier to carry out bodybuilding work on the vehicles themselves, Scania is also focusing on information and training. Some examples of this are a newly-developed website with useful information and drawings, and various physical or net-based training courses for bodybuilders. .
-
Volkswagen launches all-new Delivery light truck range
kscarbel2 replied to kscarbel2's topic in Trucking News
-
Volkswagen Truck & Bus / September 13, 2017 The new global platform for Volkswagen light trucks Trucks designed and developed in Latin America International standards for the most demanding markets The Volkswagen brand reaches the disputed segment of 3.5 tonnes New Delivery has models up to 13 tons in different versions The new Delivery family arrives to revolutionize cargo transportation in the lightweight trucks segment. Developed and produced in Latin America, the launch has already complied with international standards for the most demanding markets. Composed of models from 3.5 to 13 tons, it is ready to conquer the world: It was born from the recipe of success of the first generation Delivery and the customer experience from over 100,000 units produced. It was listening to the customer that allowed Volkswagen Truck & Bus to debut a new light truck range tailored for today's requirements. With the release, the result of an investment of more than R $1 billion, Volkswagen will compete in the hot 3.5 ton segment with the new Delivery “Express”. The Express combines the features of a heavy truck including interior cab space and robustness, the all-new Delivery represents cutting edge light truck design. The all-new Delivery is also available in 4x2 configurations rated at 4, 6, 9 and 11 metric tones. The largest variant, the 6x2 Model 13.180, features a 180 horsepower engine and tag axle configuration. The all-new Delivery is available in three cab trim levels: City, Trend and Prime. Meet the new Delivery family: Delivery Express – tailored for urban deliveries, combining the agility with impressive maneuverability and heavy truck robustness. Powered by the popular 2.8-litre Cummins ISF engine rated at 150 horsepower, it is rated at Euro 5 utilizing an SCR exhaust aftertreatment system. Speaking on safety, driver and passenger airbags as well as pretensioner-equipped seat belts are standard equipment. Delivery 4.150 – A new premier VW light truck, the Model 4.150 features a 150 horsepower Cummins 2.8-litre engine paired to a fully synchronized 6-speed Eaton ESO-4106 transmission. Delivery 6.160 – Featuring class-leading maneuverability, the Model 4.150 features a 160 horsepower Cummins 2.8-litre engine paired to a fully synchronized 6-speed Eaton ESO-4206 transmission. Delivery 9.170 – Each component of the new Delivery 9.170 was developed with the most innovative materials resulting in a 10% weight reduction versus its predecessor for greater operating economy and load capacity, and reduced emissions. The 9.170 pairs a 165 horsepower Cummins 3.8-litre engine with a fully synchronized 6-speed Eaton ESO-6106 transmission or an optional ZF automated manual transmission (AMT). Delivery 11.180 – Offering the best combination of load capacity, performance, reliability and robustness in its category, the 11.180 features a 175 horsepower 3.8-litre Cummins ISF engine paired with either a fully synchronized 6-speed Eaton ESO-6106 transmission or an optional ZF automated manual transmission (AMT). Delivery 13.180 – The range-topping Model 13.180 features a 6x2 drive configuration with rear-mounted tag axle. Offering the highest loading capacity of the new Delivery family with robustness and flexibility, it is able to meet a broad range of customer applications. The 13.180 is powered by a 175 horsepower 3.8-litre Cummins ISF engine paired with either a fully synchronized 6-speed Eaton ESO-6206 transmission or an optional ZF automated manual transmission (AMT). The new benchmark in global light trucks The new Delivery family has been designed, developed and tested to meet the varying requirements of all global regions. . .
-
Cummins Unveils Class 7 All-Electric Daycab Tractor
kscarbel2 replied to kscarbel2's topic in Trucking News
-
. . . . . . . . . . . . . . . . . . .
-
Kenworth Truck Co. / September 6, 2017 ELIZABETHTOWN, Pa. - White Oak Mills, a full-service Pennsylvania-based feed manufacturer, recently took delivery of a Kenworth T880S 7-axle straight truck, becoming Kenworth’s first customer to operate a T880S in this configuration. To recognize this Kenworth “first,” selling dealer Kenworth of Pennsylvania – Carlisle held a special ceremony for White Oak Mills. According to Josh Long, White Oak Mills transportation manager, the 7-axle configuration with 26-foot Walinga feed body allows the company to increase the amount of animal feed it hauls into Maryland and New Jersey – going from 11.25 tons per truckload to 22.75 tons. In addition, the company can carry three more tons of feed per load within its home state of Pennsylvania. “This is huge for our company, especially in neighboring states where our load was restricted due to state laws,” said Long. “If you’re registered outside of Maryland and New Jersey, a tri-axle truck is considered a tandem axle, so we were not as efficient in how much feed we could deliver. However, with the 7-axle configuration that conforms to federal bridge laws, our out-of-state sales will be more efficient.” White Oak Mills operates a fleet of 21 Class 8s – the new 7-axle T880S; 8 tri-axle straight trucks with 26-foot feed bodies; and 12 tractors hauling 40-foot feed trailers. The company delivers feed within a 150-mile radius of its plant, primarily for swine, dairy and poultry operations. “We purchased five T880 models earlier – drivers absolutely loved the ride and their productivity,” said Long. “When we worked with our Kenworth dealer and found new specs were available with the new T880S, we jumped at the opportunity. The key was a shorter hood (114-inch), the set-forward front axle, along with the PACCAR MX-13 engine (rated at 510 hp /1,850 lb-ft of torque) with an 18-speed transmission. It allowed us an overall length of 40 feet, with 45-inch spacing between the pusher axles and 54-inch space for the tag axle.” According to Long, the truck can deliver full loads of feed via a top mounted auger system that sends feed to storage bins. In addition, the truck is equipped with a vacuum for grain recovery. “Oftentimes, we will have a customer who wants to move excess feed to another bin or farm,” explained Long. ”With this unit, we can vacuum up the feed, then transport and offload. It’s our do-all truck and will keep busy.” Long said as demand increases and the T800S seven-axle proves itself, more will be purchased. “We feel we’re getting a double bang for the buck with Kenworth,” he said. “When we first got the T880s we were looking for reliability and productivity. We work 24 hours a day, six days a week, delivering feed and have a heavy-haul permit to load to 95,000 GVWR in our state. We found the trucks to be true workhorses with a very sharp turning radius – which we need since we’re delivering off-road and often in tight quarters. “I’ve driven the T880 myself and found it to be very comfortable – I spent many years as a driver for White Oak Mills and still maintain my CDL. Since we don’t do slip seating here, each driver is assigned a truck. So, they all take special pride in what they drive,” said Long. “Since we got the T880s, everyone wants to drive one. There is so much more room – the cab and windows are bigger than our previous trucks. We’ve got drivers who are over 6-feet tall, and they just love the space. It’s a beautiful truck – and now with the 7-axle configuration, more productive than ever.” .
-
Kenworth Truck Co. / August 24, 2017 KIRKLAND, Wash., August 24, 2017 - The Kenworth T370 is now available with factory-installed 18,000 lb. and 20,000 lb. front drive axles. The new offering is targeted for heavy utility services, construction, municipalities, fire and rescue, and other specialty applications. The Kenworth T370 offers the Fabco FSD-18A and FSD-20A front drive axles paired with an all-new Fabco TC-548 transfer case for exceptional durability. The two front drive axles are available with the PACCAR PX-9 engine rated up to 350 hp and 1,150 lb-ft of torque. Both models require taperleaf front springs, and are available with air or mechanical rear suspensions. Kenworth has designed the front drive axle configurations with the lowest possible cab and frame heights. This allows easier body access and permits body builder boom installations to remain under most height requirements in U.S. states and Canadian provinces. In addition, the transfer case occupies frame space inside the rails from 36 to 52 inches behind back of cab, which provides clear space behind cab for body builder outrigger equipment. The transfer case includes an air activated front axle engagement switch and dash mounted indicator light, as well as a switch to control the high and low ranges in the transfer case. The T370 is available with a gross vehicle weight rating (GVWR) of up to 66,000 lbs., and can be specified with manual, automated or automatic transmissions. The Kenworth T370 is already available in 4x4 and 6x6 configurations with axle ratings from 10,000 lbs. to 16,000 lbs. “The addition of the heavier 18,000 lb. and 20,000 lb. front drive axles expands the T370’s already excellent reputation for being a vocational workhorse,” said Kurt Swihart, Kenworth marketing director. “The PACCAR PX-9 offers excellent power in a smaller package to move more weight. When combined with the higher-capacity front axles, customers can benefit from more of the payload’s weight shifted to the front axle, while still taking advantage of the T370’s short, 109-inch BBC (bumper-to-back-of-cab) measurement.” .
-
Kenworth Truck Co. / August 17, 2017 Aggregate Hauler Finds MPG Improvement; More Payload with T880s ARDMORE, Okla. - Wayne Brown started in the construction industry 43 years ago. His first job was as a truck driver for his family-owned aggregate hauler and he enjoyed his time behind the wheel. “I drove the traditional high hood,” he recalled. “I was always very fond of the look.” So, it wasn’t surprising that when Brown bought his own rock/aggregate hauling operation in 2010 from his uncle, he went with the big hood, to join others in the fleet. According to Brown, the company operated 24 trucks when he purchased the Oklahoma City-based company. “Now we’re up to 80 trucks,” he said. “And we’ve made the transition from the high-hood to the Kenworth T880 with the PACCAR MX-13 engine. That decision is really paying us back. We’re getting up to 1.5 mpg improved fuel economy* and the trucks weigh in at nearly 900 pounds lighter. When you run fully loaded with between four to 10 runs per day to a rock crusher, that extra payload really adds up.” Brown Transportation purchased its Kenworth T880s from MHC Kenworth – Ardmore. Brown Transportation’s operation is a little unusual in the aggregate business. “We’re very diverse, which helps us weather any changes in the business climate,” he said. “We have 11 pneumatic trailers and provide sand for the oil industry in fracking operations. But that business can go up and down – it’s soft right now. So, we switch over to highway construction, delivering aggregate and rock in our belly and end-dump trailers. And since we’re a large aggregate hauler in our region, we can handle jobs others can’t. It’s not uncommon for us to get a call requesting a large delivery – due to our size, we can put more trucks on the job and complete a project in one day, versus three for our competitors.” Another competitive advantage for the company is its decision to spec the Kenworth T880s with the 52-inch mid-roof sleeper. “On our 43 T880s, we’re running the 52-inch mid-roof sleeper,” Brown said. “While our headquarters are in Ardmore, we have our trucks domiciled in Krum, Texas, and in Davis, (Oklahoma), and Oklahoma City. On a Monday, the trucks might have a job 100 or more miles away, so they’ll work that site all week – making runs to a crusher or pit nearby. It doesn’t make sense to deadhead back to our facility every day. So, that’s why the need for a sleeper. And this size gives our drivers the comfort they need, plus it’s tall enough so they can stand inside the sleeper.” Brown Transportation’s T880 52-inch mid-roof sleepers feature a liftable lower bunk with a comfortable 32-inch by 80-inch pocket coil mattress and storage underneath. There also is upper storage on the sleeper's back wall, including a place for drivers to hang their clothes and jackets. On average, Brown’s T880s average around 100,000 miles per year. “With the fuel savings we’re seeing with the T880, it means each truck is saving us close to $10,000 in fuel per year,” he said. “That factors into our total cost of ownership. We also look at cost of operation – and the T880s have been very reliable. Since we pay our drivers a percentage of the load, they have as much riding on the deliveries as we do. We expect our Kenworths to perform and we haven’t been disappointed.” One spec change the company recently made was the move to the Eaton UltraShift® transmission and disc brakes. “Our more senior drivers were used to driving 13 and 18 speeds and voiced concern when they heard we were switching to an automated manual,” said Brown. “But, now, you couldn’t get them out of the truck – they’d never go back to a manual. They’re no longer using their left foot and right hand all day long shifting. They’re less fatigued at the end of the day.” Helping even further, said Brown, is the quietness of the T880. “That PACCAR MX-13 engine (rated at 455 hp) is so quiet,” he said. “There is a big difference compared to the other engine we were running.” Brown also said the trucks bring a sense of pride to his drivers. “We make sure the trucks are washed – even the engines – every two weeks. One of my pet peeves is I like to have a nice looking fleet, so every other Monday, our drivers climb into a truck that looks brand new. I like it and they like it. And they in turn take better care of the trucks. We really have a special relationship with our drivers. We’re family-owned here too – my son Chad is vice president of operations, and his wife, Sara, is our CFO. We’re small enough where we know everyone and have a true family culture. That, along with our equipment, helps keep our driver turnover significantly lower than others in our industry.” .
-
Cummins Unveils Class 7 All-Electric Daycab Tractor
kscarbel2 replied to kscarbel2's topic in Trucking News
5 Cool Things About Our Electric Powertrain Concept Truck Cummins Inc. IT’S ALL ELECTRIC! The demonstrator truck uses a 140 KWh battery pack instead of a 12-liter engine. The weight of the electric powertrain is roughly equal to that of the removed engine, aftertreatment, transmission and fuel tank. The tractor day cab when paired with a trailer has a gross vehicle weight rating limit of 75,000 pounds. The concept truck has a range of about 100 miles on a single charge for city driving that’s extendable to 300 miles with additional battery packs. The powertrain and truck will enable Cummins to learn more about the potential electrification holds for larger vehicles. IT HAS PLENTY OF OTHER ENERGY-SAVING FEATURES A regenerative braking system and the potential for solar panels on the trailer roof can send energy to the battery pack. Air drag is reduced by replacing side mirrors with an in-dash camera system. The truck achieves a significant air drag reduction via its highly streamlined design as well as a better sealed truck body and underbody – with no front radiator intrusion. ITS ENVIRONMENTAL IMPACT Like Cummins’ diesel, natural gas and alternate fuel products, the concept powertrain and truck are designed to limit the vehicle’s impact on the environment. Electric cars and trucks produce zero emissions, which is important at a time when climate change is such a big concern. If the charging power is generated from 100 percent renewable sources, then the truck can be described as fully carbon neutral. IT’S ALL ABOUT OPTIONS Cummins wants to be the global leader in powertrains, offering customers a variety of power solutions to meet their particular needs. Diesel engines aren’t going away. The company expects diesel to be a popular option with customers for years to come. Cummins has and will continue to produce the cleanest diesel engines in the world, reaching near zero emissions levels. IT HAS CUMMINS’ SIZE AND EXPERIENCE BEHIND IT Cummins has been meeting the power needs of its customers for nearly 100 years, whether by diesel, natural gas, electrification or something else. The company’s technical staff of 10,000 people around the world has the high tech tools to study everything from a variety of bio fuels to waste heat recovery and even solid oxide fuel cell technology to power the next generation of Cummins’ engines and related products. . -
Cummins readies next-gen, future commercial power
kscarbel2 replied to kscarbel2's topic in Trucking News
Unveiling the Next Generation of Energy-Diverse Products and Technology Solutions Cummins Inc. Clean-diesel, near-zero natural gas and electric power solutions: What do these things have in common? They’re the latest in a series of next-generation, energy-diverse products and technology solutions being developed by Cummins. During an event held Tuesday, Aug. 29, 2017 at the Cummins Technical Center in Columbus, Indiana, employees, company executives, global media and elected officials watched as Cummins unveiled its latest power solutions and energy-diverse products, demonstrating that the company is prepared to win with new and future technologies. “Cummins has always been an innovator,” stated Congressman Luke Messer. “Today serves as the latest example of how this thriving Indiana business is developing cutting-edge technologies that will shape the manufacturing industry for decades to come. It was an honor to join Cummins today and support the thousands of Hoosiers that work for this great Indiana company.” From Natural Gas to Clean Diesel to Electrified Powertrain Solutions The company displayed the latest in near-zero natural gas engine technology, as well as super-efficient diesel engines (the X12 and X15), and shared plans to introduce a revolutionary heavy-duty diesel engine in 2022. To round out the company’s expert capabilities in powertrain design, Cummins also revealed, for the first time ever, a fully electric class 7 demonstration Urban Hauler Tractor (pictured below in a rendering). These products and technologies add to Cummins’ unmatched portfolio of solutions and offer customers the latest in environmentally-friendly, cost-effective and powerful products to help them succeed in every market and every application. With these new innovations, Cummins will continue to provide connected customer support, including cloud-based solutions and big data analysis, in order to maximize up-time, safety and business optimization, increasing customers’ bottom line. “These new technological innovations build on our 100-year legacy of bringing the best solutions to our customers, driving their success and meeting the evolving demands of their industries and markets,” said Jennifer Rumsey, Chief Technical Officer, Cummins Inc. “We will harness our global technical footprint to continue to develop a wide variety of power technologies to bring our customers the choice and solutions that enable their success and contribute to a sustainable future.” During the event, which included tours of the Cummins technical center, Cummins leaders and scientists showcased the company’s continued innovation and work in analysis-led design capability, virtual reality, alternative fuels and digital capabilities, all of which are positioning the company to win in current and future technologies and in new markets. “As a global power leader for the commercial and industrial customers we serve, with an unmatched service and support network, we are better positioned than any other company to win in new and emerging technologies and in new markets,” said Rich Freeland, Cummins President and Chief Operating Officer. “We will leverage our deep industry and customer knowledge and our scale advantage to win. Over the past century, our ability to innovate and adapt has fueled our success and we are confident we are on the right path to do it again.” Cummins leadership believes that energy diversity is critical to its future success. For more information on these power sources and technologies of the future, check out the stories below. 5 Cool Things About Our Electric Powertrain Concept Truck 7 Ways Cummins Goes High Tech to Power Its Customers Cummins Positioned for Growth and Leadership in New and Emerging Tech Virtual Reality Helps Cummins See the Big Picture -
.
-
PACCAR Introduces 12-Speed Automated Transmission Kenworth Truck Co. / August 23, 2017 BELLEVUE, Wash. - PACCAR is introducing the new PACCAR Automated Transmission, the lightest heavy-duty transmission for on-highway commercial vehicles. The PACCAR transmission is designed to complement the superior performance of PACCAR MX engines and PACCAR axles. Kenworth and Peterbilt will begin offering the PACCAR Automated Transmission to North American customers in October 2017. “The PACCAR Automated Transmission is engineered to work seamlessly with PACCAR MX engines and PACCAR axles and provide industry-leading performance,” said Landon Sproull, PACCAR vice president. “Together, PACCAR Powertrain components deliver superior fuel economy, uptime, and driver satisfaction —top priorities for our customers.” The PACCAR Automated Transmission is designed for line-haul applications up to 110,000 lbs. Gross Vehicle Weight. It is available for engine ratings up to 510 HP and 1,850 lb.-ft. of torque and features tightly integrated electronic communications with the PACCAR MX engine. The PACCAR Automated Transmission offers the best overall gear ratio coverage available providing excellent low-speed maneuverability and the transmission is up to 105 lbs. lighter than comparable transmissions, savings that customers can use to haul more payload. The 750,000-mile oil change interval is the longest available for line-haul applications, which reduces maintenance costs and increases uptime. The transmission includes a differentiated fluid pressure detection system that protects the gears and shafts from low fluid conditions and allows PACCAR to offer industry-leading warranty coverage. Other features include a maintenance-free clutch and an internally routed electrical system to maximize durability. PACCAR’s new column-mounted shifter puts gear selection and engine brake controls at the driver’s fingertips for better ergonomics and improved performance. . .
-
Ford schedules downtime at 5 N.A. assembly plants amid slowing sales Automotive News / September 19, 2017 DETROIT -- Ford Motor Co. will temporarily shut down production lines at five assembly plants in North America before the end of the year to fix recalled commercial vans and reduce output of slow-selling cars. Both of Ford's Mexico plants are affected. Cuautitlan Assembly Plant, which makes the Fiesta sedan, will be down for three weeks. Hermosillo Assembly Plant, which makes the Ford Fusion and Lincoln MKZ sedans, will be down for two weeks. In the U.S., Flat Rock Assembly Plant, which builds the Ford Mustang sports car and Lincoln Continental sedan, will be down for two weeks. Kansas City Assembly Plant's Transit line will be down for two weeks. Michigan Assembly Plant, which makes the Focus sedan and C-Max hatchback, will be down for one week. "We are continuing to match production with customer demand, as we always do, and we are on track for our dealer inventories to remain at planned levels by year-end," a Ford spokeswoman said in an emailed statement. In the case of the three U.S. plants, UAW workers will be placed on temporary layoff and will receive about 80 percent of their regular take-home pay. Collectively, the five plants employ more than 20,000 people, according to Ford's website. Ford did not provide any specific dates for the downtime, although the first week off for Kansas City workers will be Sept. 25 to Oct. 1, according to UAW Local 249, which represents them. The F-150 line at the plant is unaffected. The Transit is the best-selling large van in the country, but Ford in June said it was recalling 402,462 vans -- costing the company $142 million -- because of a faulty driveshaft flexible coupling. The defect could lead to the separation of the driveshaft, which could result in a loss of power, unintended vehicle movement and damage to brake and fuel lines. The Transit is still outpacing competition that includes the Chevrolet Express, GMC Savana, Ram Promaster, Mercedes-Benz Sprinter and Nissan NV. But sales fell 15 percent last month and are down 21 percent to 80,292 units through the first eight months of the year, according to the Automotive News Data Center. Retail sales are up, but fleet sales have fallen. In all other cases, the plants to be idled produce slow-selling cars. Ford CFO Bob Shanks early this year told analysts "don't be surprised" if Ford trims vehicle inventory to avoid a glut of unsold vehicles on dealer lots. Ford had an 81-day supply of vehicles as of Sept. 1, up from 77 a month earlier. Ford Motor’s total sales are down 4 percent through the first eight months of the year, slightly outpacing the industry’s overall sales decline of 2.7 percent. The Ford brand’s car sales are down 20 percent, while overall U.S. car sales have fallen 12 percent. Ford's truck sales are up 2 percent while total U.S. truck sales have risen 3.6 percent. Ford Motor has also lost one tenth of one percentage point of market share so far this year, to 15.1 percent.
-
Fiat Chrysler recalls 494,000 Dodge pickups for fire risk Automotive News / September 19, 2017 WASHINGTON -- Fiat Chrysler Automobiles said Tuesday it will recall 494,000 medium and heavy-duty Ram pickups worldwide because of a water pump that could overheat and potentially cause a fire. The recall includes 2013-2017 model year Ram 2500 and 3500 pickups with Cummins 6.7-liter diesel engines, including 443,000 vehicles in the United States. Fiat Chrysler said it is not aware of any injuries related to the issue, but has reports of a small number of fire-related incidents. The company will inspect and potentially replace the water pump.
BigMackTrucks.com
BigMackTrucks.com is a support forum for antique, classic and modern Mack Trucks! The forum is owned and maintained by Watt's Truck Center, Inc. an independent, full service Mack dealer. The forums are not affiliated with Mack Trucks, Inc.
Our Vendors and Advertisers
Thank you for your support!