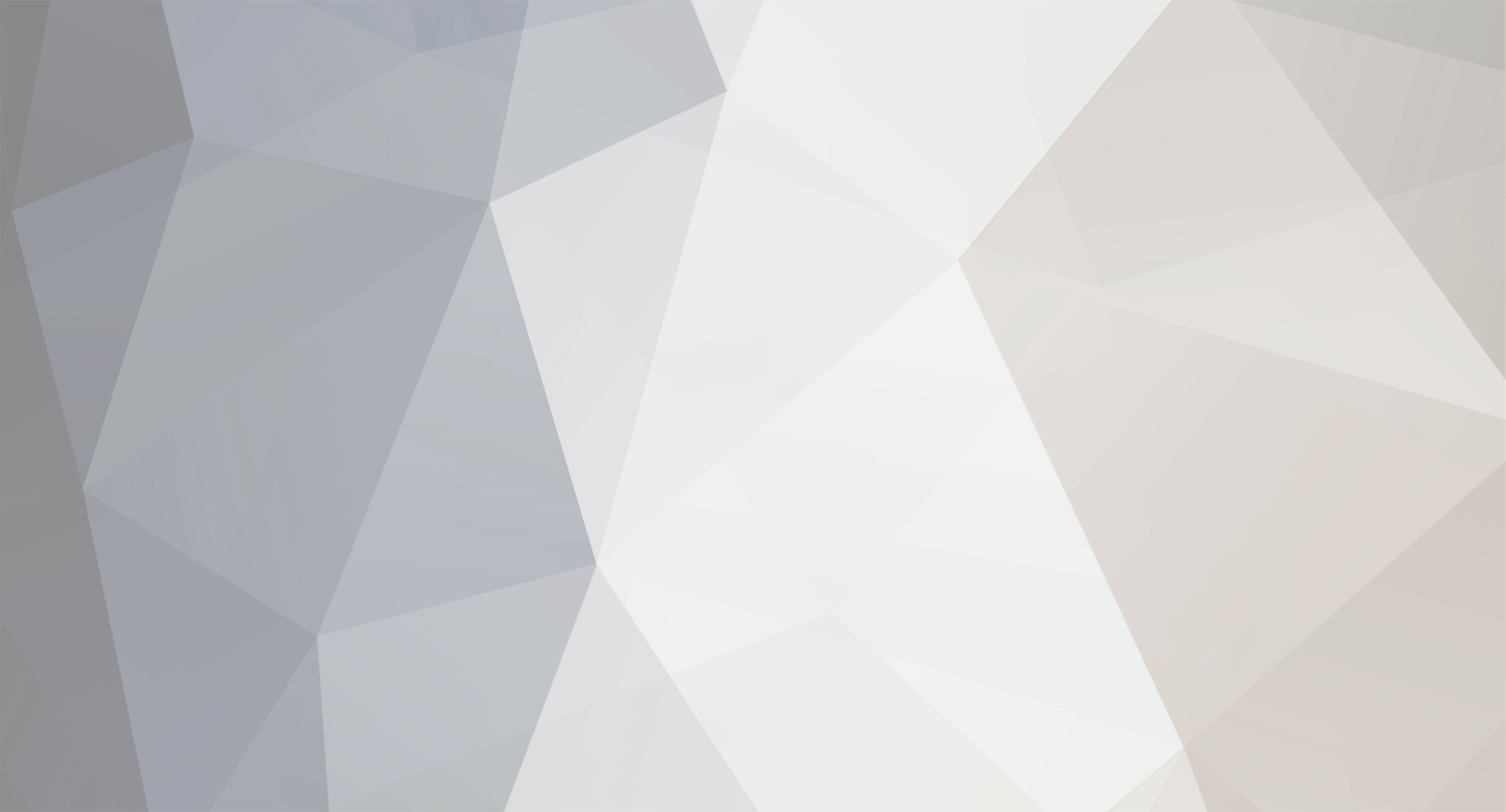
kscarbel2
Moderator-
Posts
18,738 -
Joined
-
Days Won
114
Content Type
Profiles
Forums
Gallery
Events
Blogs
BMT Wiki
Collections
Store
Everything posted by kscarbel2
-
The MR is about to turn 40...
kscarbel2 replied to Maxidyne's topic in Antique and Classic Mack Trucks General Discussion
There are many reasons I wouldn't buy a Volvo MR. The problematic Delphi-supplied fuel injection system is in the Top 5 (Delphi E3 unit pump or the new jury rig Delphi F2E common rail). I have great experience with Bosch, and Cummins-Scania XPI. -
The MR is about to turn 40...
kscarbel2 replied to Maxidyne's topic in Antique and Classic Mack Trucks General Discussion
The Mack MR has soldiered on since its introduction in 1978. Under Volvo, rather than invest in a much needed all-new cab and chassis replacement for the MR, they dragged their feet and finally introduced the hideous looking Terrapro in 2007. Certainly this low-cost, modest refresh of a now 40-year-old truck, notable only for its tacky plastic front fascia (appearance), has done nothing to impress the refuse industry. Has anyone noticed the growth of Peterbilt 520 and Autocar Xpeditor sales? The MR (Terrapro) is long on the tooth - the refuse industry would welcome a game-changing new refuse chassis that would revolutionize the business in the way the MR did in 1978. However Volvo has demonstrated no willingness to invest in that direction. Historical note - The Mack MR was introduced in 1978, in response to Crane Carrier Corporation's "Centurion" launched in 1974. Mack President Henry J. Nave was so impressed with the industry-changing Centurion, the first vehicle of its kind designed specifically to meet the needs of the refuse industry, that he ordered Mack engineers to study and surpass it. -
MR or MRU road tractor
kscarbel2 replied to Hook n ladder 1's topic in Modern Mack Truck General Discussion
The Mack "corporate" (R-model) bumper was standard on the MC, both domestic and export, because unlike the larger MR, it was based on the R-model. It was intended as a replacement for the MB 4x2 city tractors with customers like Overnite and APA, but then they began using the night time route tractors for daytime city delivery to reduce costs. . -
When Ford roamed the World - The D- and N-Series
kscarbel2 replied to kscarbel's topic in Other Truck Makes
For those who don't know, this is the Ford Thames Trader truck range that BC Mack spoke of. . -
Ford will spend $885 million to build next Kuga in Spain Reuters / November 17, 2017 MADRID -- Ford will invest more than 750 million euros (US$885 million) in its factory in Valencia, eastern Spain, to produce the next-generation Kuga SUV [what the US market Escape is based on, but without the engine fire feature]. The Valencia plant employs more than 8,000 people and, in addition to the Kuga, makes the Mondeo and S-Max alongside the Tourneo and Transit commercial vans, according to Automotive News Europe's car assembly plant map. Kuga production represents nearly half of the output at the Valencia plant. The Kuga is Ford's No. 3-selling nameplate in Europe behind the Fiesta and Focus. Ford has invested around 3 billion euros in upgrades at the plant over the past six years, making Valencia one of the two largest assembly operations in Ford's global manufacturing system, alongside its Changan-Ford joint venture in Chongqing, China. "This significant investment underlines Ford's commitment to Spain as one of its most important manufacturing sites in Europe," the company said in a statement. The investment in the Spanish plant continues a trend of auto production moving south or east in Europe, where wages tend to be lower. Spain's car industry, including auto parts manufacturers, employs just under 300,000 people, according to official statistics. It accounts for about 7 percent of the country's economic output, according to the vehicle manufacturing association Anfac. .
-
-
Transport Topics / November 17, 2017 Freightliner Trucks added several configurations to its Cascadia truck, introducing a 60-inch raised roof sleeper model in both 116- and 126-inch BBC platforms. The sleeper’s interior features a lower bunk with storage underneath and a choice of either a cargo shelf for additional storage or an upper bunk with a telescoping ladder. The model also offers a longer wardrobe cabinet, a microwave cabinet, an optional bracket for a flatscreen TV and an area for customer-supplied refrigerators or coolers. “With the shorter wheelbase and reduced weight versus a 72-inch sleeper, this truck spec is lighter and more maneuverable, while still giving drivers a comfortable, spacious area to work and rest,” said Mike McHorse, Freightliner’s manager of on-highway product marketing. Freightliner, a brand of Portland, Ore.-based Daimler Trucks North America, said orders can be made for all cab configurations for January delivery. Freightliner reports the new Cascadia has received more than 30,000 orders since it was launched in September 2016, easily surpassing the total number of orders for the first three years after the original Cascadia debuted. The new 60-inch model joins 48-, 60- and 72-inch mid-roof XT sleeper cabs in both 116- and 126-inch BBC platforms. Those models are designed for regional overnight haulers and bulk haul and flat-bed applications. .
-
Bison Transport eager to adopt Tesla semi Steve Sturgess, Truck News / November 17, 2017 HAWTHORNE, Calif. — Tesla hit the streets running with its much anticipated “semi” last night at a reveal party attended by the world’s press, Tesla officials, and employees from both the assembly plant in Fremont, Calif., and the Giga Li-Ion battery plant in Nevada. No static launch for CEO and product architect of Tesla, Elon Musk, as he stepped down from the cab of the much-heralded truck to highlight its features before a sea of fans. And it was not just one static prototype on stage, but two models of the semi that roared into a hangar at the JetCenter, a private-plane airport adjacent to Los AngelesInternationalAirport in Hawthorne, Calif. To rousing cheers from an audience of around 1,200 people, Musk extolled the performance features of the semi: a range of 500 miles, zero to 60 mph of the tractor in just five seconds, zero to 60 of a fully freighted, 80,000-lb tractor0trailer in just 30 seconds. But most significantly for the truckers in the audience, a cost per mile of US$1.25, comparing favorably to today’s diesel truck cost of $1.51. He did not specify the trade cycle or the structure of the financing but did say that Tesla was aiming for zero breakdowns in a million miles of operation. According to Internet reports, truckload carrier J.B. Hunt is among the first carriers to publicly reveal it has reserved the truck, saying it has reserved “multiple Tesla semis.” “Reserving Tesla trucks marks an important step in our efforts to implement industry-changing technology,” said John Roberts, president and chief executive officer at J.B. Hunt. “We believe electric trucks will be most beneficial on local and dray routes, and we look forward to utilizing this new, sustainable technology.” Major North American Grocery chain Meijer also said it has placed down $5,000 to reserve four models – though reservations are reported to be $5,000 per truck. Production is due in 2019. In reality, the reveal confirmed what the spy and tease photos had already disclosed: a cab forward Class 8 truck with exceptional smooth lines and promised great aerodynamic performance, a fact highlighted in Musk’s remarks. He said that the 500-mile range was enabled by exceptional aerodynamics, with the semi scoring a drag coefficient of 0.36, better even that the Bugatti Chiron’s 0.38. He also noted the cab side extenders that actively fill the gap between tractor and trailer also contribute to the overall low drag. Worth noting: the tractor at launch looked like a sleeper because of these long, active side extenders. The trucks will most likely fill a distribution and drayage role, at least in the early stages. The semi is purely battery-electric. In his presentation, Musk said that 80% of truck distribution is less than 500 miles round-trip, so the semi can get out and back on those tasks on a single charge. For longer trips, the batteries can pick up a 400-mile charge in the short half-hour break mandated by hours-of-service regulations. And Tesla Fast Chargers are popping up all over the world, wherever Tesla sells a passenger car. So, Tesla semi trucks can realistically be recharged at shipper and receiver docks. With the electrical distribution infrastructure in place and robust, there’s no need to stop en-route at a truck stop to fuel any more, he implied. And because many of the fast chargers are solar powered, Musk said “Anywhere a consumer can charge a Tesla you can charge the truck. Solar powered mega chargers mean the truck is running on sunlight.” Those sneak preview pictures gave no hint about the driver environment, which is a highlight of the Tesla semi. A centrally located driver’s seat gives a commanding view behind the enormous curved windshield. The side glass flows smoothly around the A pillars that are surprisingly thin, so the driver’s view forward is excellent. The steering position with a small, car-like wheel on the model at the preview was flanked on either side by flat panel displays from the Model 3 that are customizable as in the Tesla cars. In fact, this not only represents a major advance in driver controls, it is actually cheaper for Tesla to integrate the same flat panel technology it uses in the cars. These are completely customizable and Tesla plans to have truck-specific software to air in business connectivity for the truck. It also has a full suite of prognostics, maintenance reminders and can even have an electronic data recorder integrated to accommodate the upcoming electronic driver hours recording mandate for the USA. The truck is also equipped with the full Tesla accident avoidance technology that prevents collisions and keeps the truck in-lane. It also includes Tesla’s autonomous driving technology, and enables three-truck platooning, said Musk. In such a case, the semi is not just cost-effective against diesel trucks of today, it is also cost-effective against the railways. The trucking and general press had an opportunity for an up-close walk-around of the semi. One one, there was a small passenger seat against the back wall of the day cab for a riding helper or driver instructor. For anyone who attended the launch of the Nikola, there are obvious similarities to the Nikola launched last year. But there are significant differences, too. The 6×4 walk-around truck featured a drive tandem, each conventionally air sprung drive axles featuring a power pack from a Model 3 on the nose of the axle with a motor for each side, totaling four drive motors in all. Musk said that even if two motors failed, the Semi would have performance equal to a diesel truck of today. The air-ride is conventional Class 8 with regular looking frame rails. The front axle features independent suspension for good ride. The Tesla guide said the battery pack resides beneath the cab, and a conventional fifth wheel allows for trailer coupling. The cab looks like a sleeper from the outside but that’s because the cab sides extend well back from the back of cab. Access to the cab is to the rear of the seating position through a rear-hinged “suicide” door with three steps tapering in toward the center of the cab. The floor is stepped, presumably to allow for the batteries beneath with a step up to the driving position. The side glass is hinged down its leading edge and opens for ventilation or to pass documents down to gate guards or enforcement officers. The door glass and opposite side fixed glass do not open, removing the need for any lift mechanism that could fail in use. The door and cab sides have generous storage for documents and driver necessities. Interestingly, the door hinges are hidden and the door handle (from the Model 3) recessed so the sides are super clean. Of the two models on display, one featured conventional mirrors, the other a visibility system with cameras mounted high toward the back of cab. There was a single pantograph-arm windshield wiper to sweep the vast windshield. Musk joked that the glass “can withstand a nuclear explosion or the customer gets a free refund,” while emphasizing the point that the truck is optimized for minimum downtime, citing the out-of-service implications of a broken windshield. Features like these show that the design team understands the needs of the commercial user of the Tesla product. If it delivers that operational savings promised, early customers like Hunt will be delighted. Technicians too, because the electric drivetrain is so much less complicated than the emissions-saddled diesel powertrain. But drivers? They’ll hate it if they prefer “real” trucks. But millennials – and that’s where the new drivers are to come from – will love them. At least one Canadian fleet in attendance at the reveal – Bison Transport – is eager to try the new truck out. Rob Penner, chief executive officer of Bison, told Trucknews.com “I was down in Santa Clara earlier and was able to test drive the Tesla “mule” (Tesla tech in a Cascadia) and the performance was really impressive. They have been running this truck for about a year moving their own parts in and out of Nevada with very good performance data. Add the styling and safety features in their own ground-up truck design and one can’t help but be optimistic about the future of this technology. We look forward to getting our hands on these trucks once they become available.” .
-
Wal-Mart Joins Retailers Planning to Try Out Tesla Truck Dana Hull and Matthew Boyle, Bloomberg / November 17, 2017 Customers are starting to place orders for Tesla Inc.’s new all-electric Semi truck, with retail giant Wal-Mart Stores Inc. preordering for both its U.S. and Canadian units. “We have a long history of testing new technology -- including alternative-fuel trucks -- and we are excited to be among the first to pilot this new heavy-duty electric vehicle,” Wal-Mart spokesman Kory Lundberg said in an email. “We believe we can learn how this technology performs within our supply chain, as well as how it could help us meet some of our long-term sustainability goals, such as lowering emissions.” While electric passenger cars get all the buzz, the move to electrify big rigs has been moving swiftly under the radar, given their high emissions profiles and hefty fuel costs. Adding autonomous features on top of electrification can also help operators save on labor costs, a major upheaval for a commercial trucking industry that’s gone virtually unchanged for decades. Lundberg said Wal-Mart has preordered five of the electric trucks for the U.S. and 10 for Canada. Meijer Inc. has reserved four Semi trucks for $5,000 deposits apiece, Dan Scherer, a fleet manager for the Grand Rapids, Michigan-based retailer, said after the product’s unveiling Thursday at Tesla’s design studio near Los Angeles. He said the closely held company operates 220 trucks in six states in the Midwest. “Electric drivetrains are a proven technology,” Scherer said in an interview. “Electricity is cheaper fuel than diesel, and you are less dependent on the spot pricing of fossil fuel.” J.B. Hunt Transport Services Inc. placed a reservation to buy multiple Tesla Semi tractors, the company said in a statement Friday. The Lowell, Arkansas-based logistics company said it will deploy the trucks on the West Coast. “Reserving Tesla trucks marks an important step in our efforts to implement industry-changing technology,” said Chief Executive Officer John Roberts. “We believe electric trucks will be most beneficial on local and dray routes, and we look forward to utilizing this new, sustainable technology.”
-
Tesla Unveils All-Electric Class 8 Semi Truck Jack Roberts, Heavy Duty Trucking (HDT) / November 17, 2017 Tesla has revealed more details concerning its new, all-electric Class 8 Semi. In a scene reminiscent of a Rolling Stones concert in the 1960s, Tesla CEO Elon Musk emerged from a silver Tesla Semi at a SpaceX hanger in Hawthorne, California, packed with raucous fans. For starters, Musk noted that the truck will feature a 500-mile range on a single battery charge, which he said would allow fleets to “go out to the middle of nowhere and return.” Equally important, he said that a planned network of global, high-speed, Direct Current charging stations would give the truck an additional 400 miles of range — and compared that to the 15 to 20 minutes it takes to fill up a diesel-powered Class 8 truck today, adding that drivers are required to take rest breaks anyway. “Once you’re done with your break,” he said, “your truck will be ready to go.” Fleets that use solar-powered “mega-chargers” would see tremendous savings, he added, since their trucks would be “powered by sunlight,” while adding that the batteries receive additional electric energy through the truck’s regenerative braking system, which Musk said was so powerful drivers would rarely need to use the brake pedal. Musk likely raised more than one eyebrow when he claimed that thanks to its optimized traction and instantaneous torque, the new Semi would be able to go from 0 to 60 mph in five seconds without a trailer, and 0 to 60 in 20 seconds when pulling a fully loaded trailer. Equally important, Musk said the unique characteristics of an electric powertrain’s torque delivery with no clutch actuation or gear shifts would allow the Tesla Semi to climb a 5% grade while maintaining a constant 65 mph. Musk also touted the simplicity of the design and its operation, noting that there was not transmission or gears that had to be “shifted constantly,” adding, ‘Driving a diesel truck today is a pain. This truck has one gear and is so easy to drive anyone can do it. I can drive this thing, and I can’t drive a semi!” Musk also outlined his economic case for his new truck, explaining that at an operating cost of $1.26 per mile, a Tesla Semi will be 20% cheaper to operate than a comparable diesel truck, which he said typically runs at $1.51 per mile. Jackknifed trailers would be a thing of the past for fleets running the Tesla Semi, Musk added, since its four, independently controlled electric motors were able to apply positive or negative torque to the drive wheels, as well as independently applied brakes while backing to allow a trailer to track smoothly. Turning to the Semi’s interior, Musk told the packed hanger that the truck has a “beautiful, spacious interior” that “you can stand up inside.” The two touchscreen displays mounted on each side of the driver’s seat allow access to the truck’s navigation system, blind spot sensors and electronic logging device along with other controls and gauges. Tesla telematics and self-diagnostic capability will be standard on the truck, Musk added, with a Tesla app giving fleets updates on vehicle health and even anticipating when maintenance is required. Another standard feature, according to Musk, is Tesla’s enhanced Autopilot autonomous vehicle control system, which uses cameras mounted around the truck to support a full range of autonomous driver aides, including automatic emergency braking, automatic lane keeping assistance, lane departure warnings and an event log. Additionally, Musk said, the truck is capable of automatically contacting emergency services if there is no driver response in the wake of an emergency braking event. “This is a massive increase in safety,” he added. In another eyebrow-raising statement, Musk said that Tesla Autopilot will also enable truck platooning operations, which he called “convoys.” In this operating mode, Musk said a convoy of Tesla trucks would then be half as expensive to operate as diesel trucks, and “10 times safer than with a human driver.” Overall, Musk said, the efficiency of a Tesla truck convoy would “beat rail.” Musk wound up his Semi pitch by noting the importance of reliability in fleet operations and pointing out that a Tesla Semi has no internal combustion engine, exhaust aftertreatment system, transmission, axles or differentials to maintain. In fact, a storage compartment is located in the nose of the truck, he said. “Reliability is incredibly important,” Musk finished. “We’re guaranteeing this truck will not break down for a million miles.” If two motors happened to break down, the truck would still move, and even at that reduced capacity it would still reportedly beat the speed of a diesel-powered truck. Musk wrapped up his presentation by saying that Tesla was taking orders for the new Semi truck now, with full production slated to begin in 2019. With that, Musk then unveiled a new, Tesla supercar roadster, with a world-record 0 to 60 time of 1.9 seconds that he said “would kill gasoline-powered sports cars.” Once that presentation was complete, Musk invited Tesla guests to inspect the two Semi trucks up close, igniting something of a mob scene as a throng of spectators swarmed the trucks. In all, the event was quite a departure from the more sedate model launches typically seen in the North American truck market. And it should be noted that the vast majority of the cheering, enthusiastic crowd on hand were Tesla car owners, who are given tickets to high-profile events like the one in California last night as a kind of loyalty program. There were, however, several executives from high-profile fleets on hand for the event, and according to published reports, J.B. Hunt Transport Services has already reserved several. If fleet response to Tesla’s new truck proves to be as positive as that of the automotive customers on hand last night, it is likely Musk’s new truck will carve out a niche for itself in North America’s highly competitive commercial vehicle market. .
-
Tesla aims to upend commercial trucking with electric Semi David Undercoffler, Automotive News / November 17, 2017 HAWTHORNE, Calif. -- Tesla Inc., undeterred by its widest quarterly loss in history and Model 3 production delays, formally set its sights on the commercial truck market Thursday with the unveiling of an all-electric semi. The EV maker says the Tesla Semi will provide "a far better experience" for long-haul truck operators, while enhancing road safety and significantly slicing cargo transportation costs. A prototype of the Semi was driven and introduced by Tesla CEO Elon Musk before hundreds of journalists, Tesla faithful, potential truck buyers and investors at an airport hanger here. "I can drive this thing and I have no idea how to drive a semi," Musk joked. The Semi -- currently in the prototype stage -- has a range of 500 miles at full load and highway speeds, Musk told the crowd, and can reach 60 mph from zero in 5 seconds. It shares a number of components with the Tesla Model 3 sedan to keep costs down. Pricing wasn't released but Tesla said reservations for the Semi can be made for $5,000 per truck, with production slated to begin in 2019. Ahead of the introduction, Tesla executives showed off the Class 8 truck to journalists, describing it as "trailer agnostic," or capable of hauling any type of freight. Class 8 is the heaviest weight classification on trucks. The truck is powered by four independent electric motors that are identical to those in Tesla's Model 3 sedan -- two motors on each of the truck's two rear axles. Each motor controls a specific wheel; the truck can route power accordingly depending on traction and load though the function is automated by the truck and not configurable by the driver. Tesla also says the system can work to prevent jackknifing by applying positive or negative torque to specific wheels and or inducing braking. The battery packs sit between the front axle and the first rear axle. Unlike the motors, the packs aren't pulled from Tesla's consumer vehicles but instead are "industrial cells." Tesla said it will guarantee the truck's drivetrain, which delivers power to the wheels, for 1 million miles. Like any electric vehicle, a key component of the Semi is aerodynamics. The cab is pushed forward relative to a standard semi today. The driver sits in the middle of the cab, allowing Tesla to keep the cab at that spot as narrow as possible for better aerodynamics; a jump seat sits just behind the driver to their right. A pair of Model 3-sources touchscreens flank the steering wheel and are fixed in position. At the front of the Semi is a small storage compartment -- what Tesla and its owners lovingly refer to as the "Frunk" in light vehicles. The truck boasts a full array of Tesla's Autopilot semi-autonomous capability, all of which is derived from its other models. Tesla said the Semi can also travel in a convoy, where one or several Semi trucks will be able to autonomously follow a lead Semi. Tesla is not the only company looking into the electrification of commercial trucking. Daimler, Cummins and Bosch have all revealed electrified semi trucks that they're developing for deployment around or just after the end of the decade. "Tesla will be up against some formidable challengers, Daimler being one which knows this market well and already has customer trust and loyalty," Michelle Krebs, executive analyst for Autotrader, said ahead of the semi's reveal. The Semi reveal also comes at a precarious time for the EV maker and it has raised questions about why the company would choose to get into long-haul trucking when it already has so much on its plate. Tesla posted a third-quarter loss of $671 million, its largest quarterly loss ever. The company also disclosed that plans to ramp up weekly output of the Model 3 by up to 5,000 units -- the car upon which much of the company's survival has been pegged -- will be delayed three months until the end of the first quarter in 2018. The setbacks have raised the likelihood that Tesla will need to raise more cash in 2018 to get production of the Model 3 up to scale and promised levels. Tesla is also grappling with a lawsuit filed by a former employee at the company's Fremont, Calif., factory. The class-action suit alleges a culture of racist behavior, a claim Tesla has vigorously denied. .
-
Your tax dollars at work.
-
U.S. Navy pilot draws obscene picture in the sky CBS News / November 17, 2017 A U.S. Navy pilot drew obscene pictures in the sky over Washington state on Thursday, CBS affiliate KREM-TV reports. Viewers contacted the station after watching a plane draw what appeared to be crude depictions of a penis in the sky in OkanoganCounty, which borders Canada. The station posted pictures of the drawings on its website. A mother in Okanogan, Washington, told the station she was upset because she might have to explain the drawings to her kids. The Navy told the station that the aircraft involved was based at Naval Air Station Whidbey Island off the Washington coast. The Navy said in a statement that the incident was "unacceptable." "The Navy holds its aircrew to the highest standards and we find this absolutely unacceptable, of zero training value and we are holding the crew accountable," the Navy said. An FAA official told the station there was nothing the agency could do about the incident because it "cannot police morality."
-
Cummins readies next-gen, future commercial power
kscarbel2 replied to kscarbel2's topic in Trucking News
Cummins is scared to death, and they should be. Its US market share will continue to evaporate. Cummins primary market for truck engines over the next 20 years is going to be China, owing to unfolding developments. India will be its number two market. -
The J.B. Hunt order is very interesting. A bit more info here......https://www.bigmacktrucks.com/topic/46136-tesla-electric-truck-news/
-
When Ford roamed the World - The D- and N-Series
kscarbel2 replied to kscarbel's topic in Other Truck Makes
Showing my age, I was given a D-Series "matchbox" truck as a young child in the US. Liked the appearance but of course never saw a similar looking truck on US roads. What Ford did with the model is amazing. They built far higher GVWs than they originally ever envisioned. -
The variable compression ratio engine has arrived
kscarbel2 replied to kscarbel2's topic in Odds and Ends
Mark, my favorite car is a 2-door Saab 99 Turbo with a 5-speed manual. Also always liked the fiberglass-bodied 1970-74 Saab Sonett sports car with the 1.7-litre Ford Taunus V4. -
J.B. Hunt orders Tesla's electric truck, others wait and see Reuters / November 17, 2017 J.B. Hunt Transport Services Inc was the first major U.S. trucking company to back Tesla Inc’s new “Semi” electric trucks on Friday, saying it had reserved multiple vehicles for use on the U.S. West Coast. Neither company responded to calls seeking to clarify exactly how many of the vehicles Hunt was reserving after Tesla unveiled the Semi on Thursday without specifying prices. Hunt’s statement followed a rejection of the new vehicles on Thursday by Old Dominion Freight Line Inc, the United States’ fourth-largest less-than-truckload carrier and other carriers were also more cautious. “Carriers have been skeptical about the heavy-duty tractor applicability to their models, given questions regarding torque, total hauling capacity, and recharging infrastructure,” said Benjamin Hartford, a sector analyst with brokerage Baird. “(J.B. Hunt) the first mover, particularly with regard to Tesla, but we expect other carriers to follow as electric tractor viability becomes proven.” Tesla has been trying to convince the trucking community that it can build an affordable electric big rig with the range and cargo capacity to compete with relatively low-cost, time-tested diesel trucks. In a showy launch on Thursday, Tesla chief Elon Musk said the truck could go up to 500 miles (800 km) at maximum weight at highway speed, allowing it to drive from Los Angeles to San Francisco and back without recharging. Diesel trucks are capable of traveling up to 1,000 miles (1,600 km) on a single tank of fuel. Tesla showed off the semi on a webcast which offered reservations for the truck at $5,000 each, but Musk did not discuss reservation volume. A spokesman for United Parcel Service Inc said the courier had nothing to announce regarding Tesla’s vehicles but would always look for options that fit its needs. Brad Pinchuk, chief executive of Dubuque, Iowa-based Hirschbach Motor Lines, said his firm was looking to test non-diesel big-rig options but needed longer ranges than Tesla could provide and speedier fuel-up times. Pinchuk said he plans to buy two hydrogen-powered trucks made by Salt Lake City-based electric Nikola Motor Company when they are available in 2020. “It’s a different application – putting liquid hydrogen into tanks – so it will be very similar sort of situation to diesel,” Pinchuk said. “You’d be able to fuel up. It would take about the same amount of time to fuel up a diesel and go about the same distance.” ------------------------------------------------------------------------------------------------------------------------ J.B. Hunt Reserves Multiple Tesla Semi Electric Trucks Heavy Duty Trucking (HDT) / November 17, 2017 J.B. Hunt Transportation announced that it placed a reservation to purchase multiple Tesla Semi electric tractors that was unveiled on Nov. 16. The Tesla Semi is slated for launch in 2019 but companies can reserve a truck now for $5,000. J.B. Hunt plans to deploy the electric trucks to its intermodal and dedicated contract services divisions to support operations on the West Coast. “Reserving Tesla trucks marks an important step in our efforts to implement industry-changing technology,” said John Roberts, president and chief executive officer at J.B. Hunt. “We believe electric trucks will be most beneficial on local and dray routes, and we look forward to utilizing this new, sustainable technology.” In April, J.B. Hunt announced a five-year, $500 million commitment to enhancing operating systems, developing cloud infrastructure, and creating innovative and disruptive technologies, as the company commits to meeting the needs of an evolving supply chain and introduces new technology for customers and employees. In addition to its investment in electric trucks, J.B. Hunt is supporting sustainable initiatives such as reducing engine idle time, governing top speed limits, converting over-the-roads shipments to intermodal, optimizing routes for better efficiency, and using biodiesel fuels when possible.
-
EPA to rescind glider kit emissions regs enacted last year
kscarbel2 replied to kscarbel2's topic in Trucking News
-
Cummins readies next-gen, future commercial power
kscarbel2 replied to kscarbel2's topic in Trucking News
Five Things about Electrification You’ll Only Hear from Cummins Cummins Press Release / November 16, 2017 CUMMINS OFFERS A BROAD PORTFOLIO OF PRODUCTS TO HELP CUSTOMERS FIND THE RIGHT SOLUTION TO THEIR POWER NEEDS. YOU’RE GOING TO HEAR A LOT ABOUT ELECTRIFICATION AND TRUCKS IN THE COMING DAYS. HERE ARE FIVE THINGS TO REMEMBER: 1.WHILE ELECTRIFICATION HAS TREMENDOUS PROMISE, IT’S NOT THE ANSWER FOR EVERYONE RIGHT NOW That’s why Cummins has pledged to first bring to market an all-electric powertrain for buses and delivery vehicles by 2019. We believe electric vehicles make the most sense in urban areas where the drive ranges are shorter and the vehicles can more easily be recharged. Many cities around the world are looking at electrification as a means to reduce pollution and greenhouse gases (GHGs). That’s not to say electrification couldn’t someday play a role in long haul trucking. AEOS, the concept electric heavy-duty truck Cummins unveiled in 2017, will help us learn about electrification’s potential with larger vehicles traveling greater distances. 2. IT TAKES MORE THAN AN EXTENSION CORD TO KEEP AN ELECTRIC TRUCK GOING There are still a number of challenges facing electrification in trucking. AEOS, for example, can go 100 miles on a single charge. That won’t get you far when it comes to long haul trucking. Charging AEOS isn’t as easy as plugging it into the nearest outlet, either. It takes an hour to charge when plugged into a 140 kWh charging station, although by 2020 advances in batteries are expected to shrink charging time to about 20 minutes. There also isn’t the service infrastructure that exists for diesel or even natural gas. You could increase the size of the battery, but it would take about 19,000 pounds of battery to go 600 miles on a single charge. That would take a pretty big chunk out of your payload. 3. ELECTRIFICATION DOES NOT SPELL THE END OF DIESEL OR OTHER FORMS OF ENERGY ANYTIME SOON About 75 percent of the trucks on the road today are powered by diesel engines, including more than 90 percent of the long haul trucks. Just based on sheer volume, it’s going to take years before anything replaces that many diesel trucks, especially when you consider the relatively high cost of new technologies early in development. In addition, diesel fuel is the most energy dense liquid fuel available and advances in engines, emissions control technology and cleaner diesel fuels have led to some remarkable environmental gains. In the past 25 years, for example, there’s been a 95 percent reduction in nitrogen oxide (NOx) emissions, a key contributor to smog. New engines like Cummins’ X12 and X15 diesel engines are also seeing significant gains in fuel economy, which translates into GHG reductions. Diesel is also proving to be a good platform for hybrid powertrains, including the use of electrification. As customers adopt different power solutions for different applications, Cummins is uniquely prepared to help manage their fleets because of our expertise in a range of power solutions and our global service and support network. 4. INFRASTRUCTURE MATTERS Part of bringing any new technology to market is having the infrastructure to produce and service it. Cummins has been making truck engines for nearly 100 years and we’ve been working with electrification for decades. The company does business in approximately 190 countries and territories and its customer service and support network is unmatched. When power solutions are economically viable, Cummins brings them to its customers. We will continue to do the same with electrification. The company has already brought things like stop-start technology to our bus engines. Cummins has the people and facilities to develop its capabilities in all the key subsystems and components that are critical to electrified and hybrid power systems. The company’s recent acquisition of Brammo, which designs and develops battery packs for mobile and stationary applications, will help accelerate Cummins’ capability development in battery systems. 5. ONLY CUMMINS IS POSITIONED TO HELP CUSTOMERS PICK THE ENERGY SOLUTION THAT’S RIGHT FOR THEM Every customer’s situation is a little different. At Cummins, we want to offer the right technology at the right time and in the right place. That could be our clean diesel engines powering long haul trucks, our near zero natural gas engines powering major urban transit systems at emissions levels below EPA standards, or our diesel-electric hybrids powering locomotives around the U.S. The bottom line: customers can depend on Cummins to help them find the option that works best for them. Once we find the right solution, we have the global service and support network to keep them up and running anywhere in the world at any time – something that is unique to Cummins. . -
The MR is about to turn 40...
kscarbel2 replied to Maxidyne's topic in Antique and Classic Mack Trucks General Discussion
Billy, we had a customer run his MH off Afton mountain in Virginia. The cab completely disconnected. The cab's safety cage worked as designed.....the driver suffered no serious injuries. -
Tesla debuts electric semi with up to 500 mile range, production set for 2019 Jason Cannon, Commercial Carrier Journal (CCJ) / November 17, 2017 With a style more fitting of Star Wars than Smokey and the Bandit, Tesla’s electric semi made its twice-delayed debut Thursday in Hawthorne, Calif., the home Tesla Motors’ design center and company founder Elon Musk’s SpaceX rocket factory. Promising a range of up to 500 miles at maximum weight and highway speed, the company says the Tesla Semi consumes less than two kilowatt-hours of energy per mile when fully loaded. Battery capacity wasn’t disclosed Thursday night. The company is currently accepting reservations for Tesla Semi for $5,000 per truck with production set for 2019. Thursday’s reveal ended a nearly 15-month-long tease of the Class 8 prototype Musk initially confirmed was in development in July of last year. Without a trailer in tow, Musk says Tesla Semi features a five second 0-60 time, versus about 15 seconds for a comparable diesel truck. At a full-load of 80,000 pounds, he says the electric truck can hit the 60 mph mark in 20 seconds – about a third of the time of a diesel truck – and adds the truck can climb a 5 percent grade at a steady 65 mph. Most diesel Class 8s, he says, would top out around 45 mph on the same grade. “We wanted a vehicle that feels incredible,” Musk says, “that accelerates like nothing else.” Musk didn’t offer torque or horsepower figures for the truck. Driving environment Tesla Semi’s cabin wraps around the center-mounted driver’s seat. “You’re positioned like you’re in a race car,” Musk says. “You have complete visibility of the road. It’s a beautiful spacious interior.” The entry-point is behind the center-seat and in the daycab configuration, the passenger seat is mounted to the rear wall on the right-side. Two touchscreen displays, borrowed from Tesla’s Model 3 passenger car, are positioned on both sides of the driver and provide easy access to navigation, blind spot monitoring and electronic logs. There is no instrument cluster facing the driver. Truck data, like speed and air pressure, is fed to the display to the driver’s left. The steering wheel is also racecar inspired and much smaller than most on the highway today. Built-in connectivity integrates directly with a fleet’s management system to support routing and scheduling and remote monitoring. Each can be flashed over-the-air via updates as-needed. The truck’s steps are unobstructed, allowing for easier entry and exit. The doors open in reverse, suicide-style, as the company removed the front pillar where the vent-style side windows are now located. Grab handles run from the floor to the top of the door pillar and from the floor to the middle of the door jam, giving it three easy contact points. The inside is spacious and full standing-height. The large windshield offers a massive panoramic view and coupled with its large side windows, visibility in Tesla’s Semi is unrivaled. All lighting in the truck is LED, a conversion that was made from bumper-to-bumper. Front marker lights have been moved from the roof to a strip behind the windshield, a nod to improved aerodynamics and the removal of leak points. The truck’s fully electric HVAC system doesn’t require idling and the interior features deep sill and door pockets, along with overhead storage compartments and pocket storage along the rear wall. By eliminating the hum of the engine, Tesla has also eliminated the truck’s white noise filter – meaning every other noise stands out even more. To combat that, the company said it trained its focus on ensuring the cab was tightly fit and sealed against creeks and rattles. The batteries are centered under the truck to lower its center of gravity and give the Semi a more predicable feel, and the air suspension with independent front suspension gives the truck, Musk says, a more comfortable ride. Electric power supply Tesla’s new high-speed Megacharger DC charging station pumps about 400 miles of range back into the truck in about 30 minutes. Chargers can be installed at origin or destination points — such as at fleet terminals — and along heavily trafficked routes, enabling recharging during loading, unloading and driver breaks. “400 miles is like 6 to 7 hours of driving,” Musk says. “What this means is that when you are done with your break, you’ll be ready to go.” Regenerative braking recovers 98 percent of kinetic energy to the battery, giving it a basically infinite brake life. Musk estimates under most cases, drivers will seldom use the footbrake, opting to let the regenerative brake stop the tractor. Tesla says the Semi’s battery is similar in composition to the batteries used in its energy products, and designed to support repeated charging cycles for over a million miles. The truck’s motors – two on each rear axle – are derived from those deployed in the Model 3 and offer independent torque control. Driver safety Tesla says its Semi’s all-electric architecture is designed to a higher safety standard than any other heavy-duty truck on the market, with a reinforced battery that shields the Semi from impact and gives it a low center of gravity. Its windshield is made of impact resistant, explosion proof glass that Musk says resists cracking. Onboard sensors help prevent jackknifing by detecting instability and reacting with positive or negative torque to each wheel while also independently activating the truck’s brakes. “Jackknifing is impossible in this truck,” Musk says. The surround cameras aid object detection and minimize blind spots, automatically alerting the driver to safety hazards and obstacles. “I can drive this truck and I have no idea how to drive a [semi],” Musk says. One of the screens in the cockpit features views from cameras mounted under the side mirrors, eliminating the corner blind-spot. Tesla’s semi-autonomous driving platform, Enhanced Autopilot – and its suite of Automatic Emergency Braking, Automatic Lane Keeping, Lane Departure Warning and event recording – will be standard on the truck, which is also platooning-enabled. Cost of ownership Aerodynamics feature heavily on the Tesla Semi, which Musk says offers a better drag coefficient than a Bugatti Chiron. Rear cab fairings, Musk adds, further streamline aero by adjusting to the type of trailer in-tow to close the gap. With no engine, transmission, after-treatment system or differential for upkeep, Tesla lauds the Semi’s reduced maintenance needs. However, Tesla says the most significant cost-advantage comes from savings in energy costs. Coupled with the low and historically less volatile nature of electricity prices – which average $0.12/kWh in the U.S. and can be significantly less for commercial and industrial users – Tesla says Semi owners can expect to reap upwards of $200,000 in savings over a million miles on fuel costs alone. Further, Musk guarantees the truck will not breakdown for one million miles. In the event one of the motors does suffer a failure, he says there’s little threat to missing a delivery date. “You can lose two of those four motors and the truck will still keep going,” Musk says. The truck is connected to Tesla Mobile Service and its telematics suite offers remote diagnostics, predictive maintenance, location tracking and communication with fleet dispatch. Musk estimates the Tesla Semi will provide a $1.25 cost-per-mile versus a $1.51 diesel cost-per-mile. In a platoon, Musk says the Tesla cost per mile drops to .85 cents per mile, making it cheaper than rail. Entry into a crowded marketplace With Tesla’s entry into the market, the Silicon Valley automaker becomes the latest entry into a growing field. Daimler’s Fuso division in October debuted its E-Fuso Vision ONE concept, a Class 8 truck with a range of up to 220 miles. The first all-electric Class 8 to hit the stage, E-Fuso also featured the longest range before Tesla’s entry into the market. Tesla and Fuso aside, a range of about 100 miles has been the standard-bearer in electric commercial transportation, albeit in lighter commercial truck classes. Unveiled in August, Cummins’ Class 7 Aeos Electric Commercial Vehicle Demonstrator – designed and built in collaboration with Roush – features a 140 kWh battery pack and a 100 mile range. Fuso’s eCanter offers a range of 60 to 80 miles using six lithium-ion battery packs, each with 420 volts and 13.8kWh. Up to two additional battery packs can be added to increase operating range to roughly 100 miles. Chanje’s electric V8070 Class 5 panel van uses a 70 kWh battery for its 100 mile range. Electric power is more prominent in the bus segment and earlier this month, Daimler’s Thomas Built Bus division unveiled an electric school bus that features 100-160kWh of battery energy and a 100 mile fully-electric range. Developed with Volkswagen Truck & Bus, Navistar’s chargE is an electric CE Series concept school bus with a range of 120 miles on a single charge due for launch as early as 2019. Navistar, with Volkswagen Truck & Bus, also plans to develop an electric-powered, medium-duty truck, which could launch as early as 2019. .
-
Tesla, Elon Musk Unveil Electric Semi-Truck Transport Topics / November 16, 2017 HAWTHORNE, Calif. — Tesla Inc. has unveiled its long-anticipated, all-electric Class 8 tractor, marking the electric car maker’s entry into the commercial truck business and showcasing its ambitions to reinvent the industry. Tesla co-founder and CEO Elon Musk introduced the truck here at its Nov. 16 unveiling by driving it into a hangar filled with a waiting audience, then stepping out of the cab. The battery-powered Tesla Semi, set to enter production in 2019, is a daycab with a range of 500 miles on a single charge at highway speeds while hauling 80,000 pounds. “Since the vast majority of routes are under 250 miles, it means that you can go to your destination and back, even if your destination has no charger,” Musk said. With this vehicle, Tesla has redesigned the heavy-duty truck from the ground up, starting with scrapping the internal combustion engine. The truck is powered by a battery situated under the cab floor and is propelled by four electric motors, one at each wheel end on the drive axles. It utilizes regenerative braking and requires no shifting or clutching. The front hood lifts to reveal exterior storage space rather than an engine. The truck’s chassis features a highly aerodynamic, sloped design to improve energy efficiency and prolong battery charge. “We designed the Tesla truck to be like a bullet,” Musk said. Tesla is not positioning this truck as a luxury item. Musk presented a business case for trucking companies built around the total cost of operating the vehicle. Factoring the cost of the lease, insurance, maintenance and fuel, a diesel truck is 20% more expensive to operate per mile than a Tesla Semi, he said. A key component of that calculation is maintenance savings enabled by the electric drivetrain, which Musk guaranteed will last one million miles. Without an internal combustion engine, transmission or emission aftertreatment systems, the truck has fewer moving parts and will require significantly less maintenance than a traditional diesel, the company said. The Tesla Semi also features a radically different setup for the driver. The driver’s seat is located in the center of the cab rather than on the left side, a design choice aimed at improving visibility. “You’re positioned like you’re in a race car,” Musk said. “You have complete visibility of the road and all the surroundings.” Inside the cab, the driver is flanked by two large touchscreen displays, one on either side of the steering wheel. Those screens replace the traditional dash display and contain all instrumentation, including the speedometer and controls for heating and air conditioning. The screens also display turn-by-turn navigation and video from blind-spot cameras. Tesla showcased two versions of the truck at the unveiling. They were the same mechanically, but one was optimized for aerodynamics with a high roof and fairings covering the drive wheels, while the other was outfitted for shorthaul operations. Tesla has not indicated where it will manufacture the trucks. By unveiling the Tesla Semi, Musk has added commercial trucking to his list of business ventures. The inventor and business magnate also is pursuing space travel and solar power with SpaceX and SolarCity, as well as transportation via pods in sealed tubes with Hyperloop. With its truck, Tesla will attempt to drive the commercial trucking industry toward electric power as it has already done in the passenger car market. The Tesla Semi’s 500-mile range would make it well-suited for dedicated regional operations where the vehicle can recharge at a fleet’s terminal. But Tesla plans to build a network of charging stations to enable the truck to travel anywhere, much like its expanding charging infrastructure for its passenger cars. And Musk made the case that recharging the Tesla Semi will not be a time sink. The vehicle could plug in at its destination while unloading freight, or drivers could simply recharge it when they stop to use the bathroom or get a bite to eat. Charging stops could align with drivers’ required 30-minute rest breaks under hours-of-service rules. “What this means in practice is by the time you’re done with your break, the truck is ready to go,” Musk said. “You will not be waiting for your truck to charge.” The Tesla Semi also will come equipped with a Level 2 automated driving system dubbed “Enhanced Autopilot,” which includes automatic emergency braking, automatic lane keeping and lane-departure warnings. “Every truck we sell will have Enhanced Autopilot as standard,” Musk said. The driver-assist technology is similar to the Autopilot system available in Tesla’s passenger cars. When engaged, that feature automatically maintains the vehicle’s lane while keeping a safe following distance, but requires the driver to remain attentive and keep his or her hands on the wheel. With the Tesla Semi, that technology goes a step further. If the driver has a medical emergency and becomes disabled, the truck will stay in its lane and gradually come to a halt, and even call emergency services, Musk said. “This is a massive increase in safety.” Tesla also has designed the truck to automatically prevent jack-knife accidents, which Musk described as a trucker’s “worst nightmare.” With its independent motors on each wheel, the truck will dynamically adjust the torque on each wheel so that jackknifing is “impossible,” he said. Musk began the presentation by touting his electric semi’s performance compared with that of a diesel truck. The Tesla Semi can accelerate from zero to 60 miles per hour in five seconds. Even pulling 80,000 pounds, it can reach 60 mpg in 20 seconds, he said. The Tesla Semi also can do 65 mph going up a 5% grade, compared with 45 mph for a diesel truck, he added. Tesla said the truck will integrate directly with a fleet’s management system to support routing, scheduling and vehicle tracking. Musk also highlighted advantages for reliability and maintenance. Because the truck has four independent motors, it can lose two of them and keep going, he said. “In fact, even if you only have two of the four motors active, it will still beat a diesel truck.” At the same time, the electric motors can turn the brakes into generators. The kinetic energy of braking goes back into the battery pack instead of wearing down the brake pad, Musk said. “The brake pads basically last forever.” The truck also comes with “armor glass” to prevent cracked windshields, a common repair issue. “This detail matters a lot,” Musk said. . .
-
Volvo - Autonomous truck for hub-to-hub transportations
kscarbel2 replied to kscarbel2's topic in Trucking News
Volvo Demonstrates Autonomous Truck Technology Heavy Duty Trucking (HDT) / November 15, 2017 Volvo Group demonstrated a new self-driving truck, designed to travel autonomously from one hub to another, at the Volvo Group Innovation Summit in Beijing, China. The latest autonomous concept truck was designed for hub-to-hub transportations in semi-confined areas such as harbors and dedicated lanes on highways. The company previously showed similar autonomous concepts for confined areas such as mines, quarries, and sugarcane fields, and this new solution takes those ideas into an over-the-road setting. The truck is based on the company’s existing FH platform and navigates completely autonomously, using lidar and GPS to continuously scan its surroundings and check its location. It can navigate around fixed and movable obstacles and gather data to optimize its route, traffic safety, and fuel consumption. The truck requires no manual supervision and is part of a total transport solution that controls the entire delivery process. “Although this technology may be years away from production, it will undoubtedly influence our future offering and has the potential to develop smart societies for the future,” said Martin Lundstedt, president and CEO at Volvo Group. “No matter what type of solution we develop, safety is always our primary concern and this applies to all our self-driving projects.” .
BigMackTrucks.com
BigMackTrucks.com is a support forum for antique, classic and modern Mack Trucks! The forum is owned and maintained by Watt's Truck Center, Inc. an independent, full service Mack dealer. The forums are not affiliated with Mack Trucks, Inc.
Our Vendors and Advertisers
Thank you for your support!