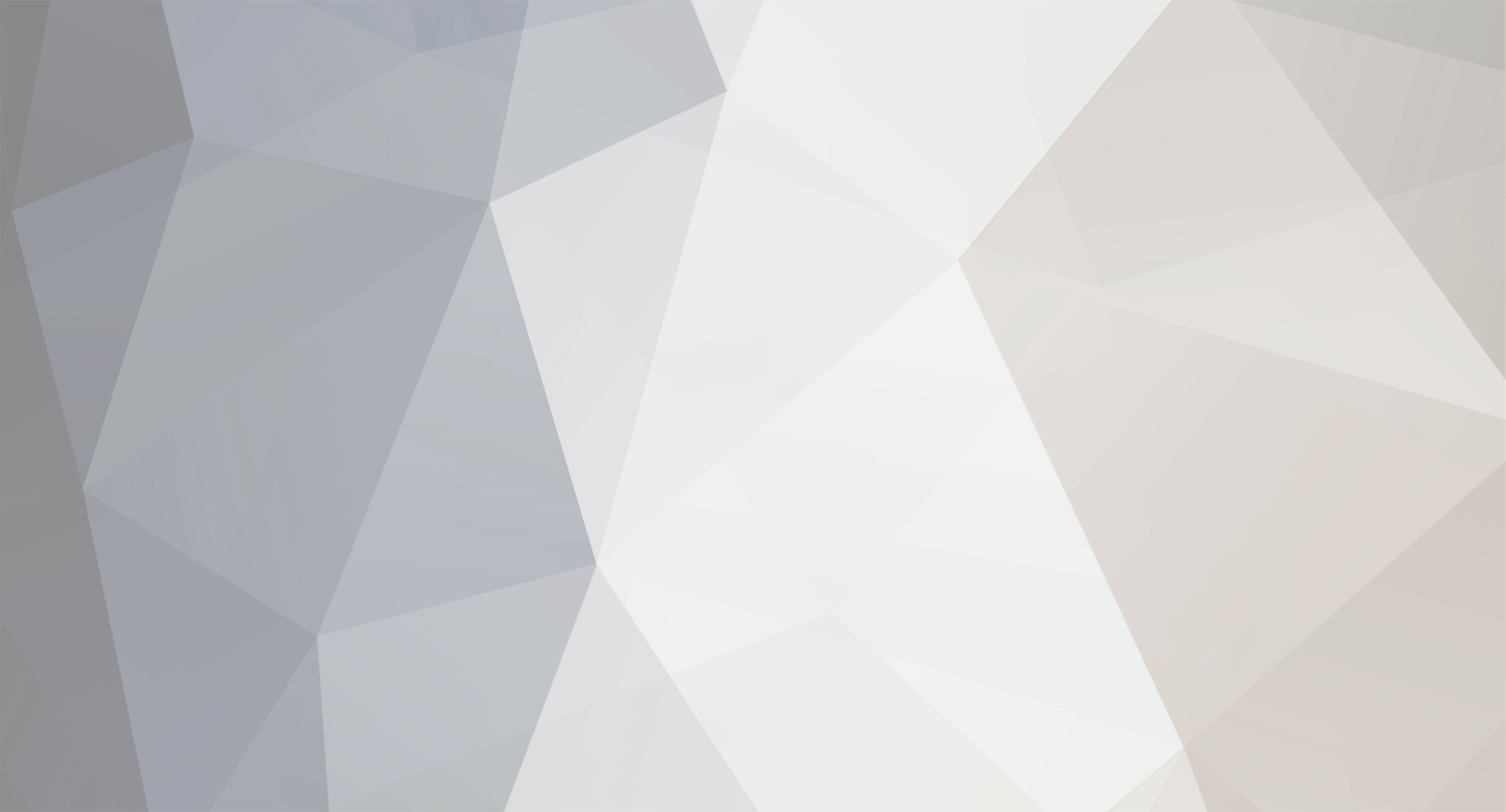
kscarbel2
Moderator-
Posts
18,734 -
Joined
-
Days Won
114
Content Type
Profiles
Forums
Gallery
Events
Blogs
BMT Wiki
Collections
Store
Everything posted by kscarbel2
-
First Look: Tesla's All-Electric Semi Truck Jack Roberts, Heavy Duty Trucking (HDT) / November 16, 2017 LOS ANGELES – The highly anticipated Tesla electric semi has finally arrived. And, as hinted, teased and promised these many past months, it is a potential game-changer — and quite possibly a disruptive vehicle for trucking in many ways. Tesla chose to launch the truck at its SpaceX facility in the Los Angeles suburb of Hawthorne, with more than 1,000 journalists in attendance from around the globe. Security was incredibly tight as journalists were taken in small groups to a small hanger, where two Class 8, all-electric daycab models were on display with engineers on hand to explain various vehicle systems and features. Highlights from the unveiling event: • Tesla chief Elon Musk promised a 500-mile range. "You can go out to the middle of nowhere and come back." • 400 miles charge in 30 minutes, leveraging a global network of "megachargers" • Electric drivetrain guaranteed for 1 million miles, and brake pads may last as long as truck • Musk said diesel trucks are 20% more expensive per mile than the Tesla semi in total cost of ownership. • Enhanced Autopilot will be standard. • Production to begin in 2019. A Tesla Semi Walk-Around While the initial vehicle walk-around focused on a very high-level view of the truck, there’s still a lot of information available. For starters, the unveiled truck very closely resembles the now-familiar blacked-out teaser photos that Tesla released months ago. This includes a highly aggressive aerodynamic design dominated by a Corvette-like front end and a steeply sloped hood. Remember, there is no internal combustion engine at the front of this truck, which allowed Tesla engineers to completely rethink its configuration with an emphasis on safety and visibility. One particularly slick feature is the LED marker lights at the top of the cab, which are located behind the windshield and shine through a darkened strip at the top, keeping them completely protected from the elements. The massive batteries that power the truck are located directly underneath the cab, while the electric motors they power are arranged between the frame rails behind the cab and running under and aft of the fifth wheel. Tesla says these are the same electric motors found in Tesla Model 3 cars. One electric motor powers each drive wheel-end. The motors are computer controlled and can deliver electrical power individually based on tractive requirements, a trait that Tesla says gives the truck “fantastic” traction in a variety of road conditions and excellent lateral stability and handling at highway speeds. The cab of the Tesla truck features an array of innovations and design departures backing up Tesla’s claim that the truck is a clean-sheet, “ground-up” design. The extremely tall, 8-foot-high doors of the cab are located farther back than conventional truck designs and swing open toward the rear of the vehicle in a “suicide” style. This is to keep the door hinges flush inside the cab body and maintain the overall slippery aerodynamic profile of the truck. Entry is as easy as climbing up the porch steps into your house, with two sturdy grab-handles on either side to help out. You enter the cab behind the center-positioned driver’s seat, which can be accessed easily from either side of the truck. The cab interior is incredibly spacious and allows a 6-foot-tall person to stand comfortably thanks to the high-roof ceiling, which is at least 71 inches in height. This is a day cab truck, so a jump seat is mounted to the back wall of the “passenger” side of the truck. The driver’s station is a revelation in itself. The seat features a memory air-ride system and is extremely comfortable. There is no dash in front of the seat. There is no conventional transmission selector, either. In all, it is a strikingly Spartan, uncluttered design that is focused on expansive exterior views in front and to the sides of the truck. In place of a conventional dashboard, the driver has two Tesla screens mounted on either side at the 10 o’clock and 2 o’clock positions that display all vehicle information and allow the driver to control all the vehicle systems. Both screens feature side-and-downward camera views on their bottom sections, which allow the driver to see persons or obstacles on or near the steps leading up into the cab. Tesla says the truck can easily upload an ELD that drivers can access on the display screens as well, and the entire system was designed to be expandable as new technologies, such as blockchain, become available. These screens, which are highly reminiscent of handheld tablet computers, are highly configurable. In the version displayed in Hawthorne, the left-side tablet displayed all pertinent vehicle operating information, such as battery range, speed, and air pressure. The right-side screen was dedicated to a Google maps GPS display and other vehicle systems such as lighting and climate control. The cab gets wider the farther back the cab goes, but the nose of the truck, where the driver sits, features pop-open windows on either side with enough space to pass a clipboard through, as well as cup holders and comfortable armrests. The steering wheel setup is arresting, too. Instead of the usual wide-diameter wheels common in big rigs today, the pedestal-mounted Tesla wheel is positively tiny — more like something you’d find in a Formula 1 race car than a semi truck. The cab features ample storage places to the sides, above and behind the driver. Tesla says the truck was designed with as few moving parts as possible to minimize maintenance costs and features a regenerative braking system that, in addition to recharging the truck’s batteries, reduce brake wear. This is a developing story. Tesla CEO Elon Musk is expected to offer more specifics on the new Tesla truck as the evening progresses and the story will be updated accordingly. .
-
When Ford roamed the World - The D- and N-Series
kscarbel2 replied to kscarbel's topic in Other Truck Makes
-
ATA commends Volvo’s local manufacturing milestone
kscarbel2 replied to kscarbel2's topic in Trucking News
Automotive manufacturing not dead in Australia: Voorhoeve Australasian Transport News (ATN) / November 16, 2017 Volvo chief says the group’s production milestone is a mark of local manufacturing success Volvo Group Australia president and CEO Peter Voorhoeve highlights the success of the Group’s Brisbane-based Wacol factory with the announcement of its 60,000th locally made truck. Voorhoeve says Volvo’s production milestone demonstrates that automotive manufacturing is alive in Australia despite closures of car manufacturing units here. "Our Wacol plant has been operating since 1972, and houses manufacturing and engineering facilities to produce both Volvo and Mack trucks," Voorhoeve says. "The plant makes a significant economic contribution to the local area, and it does it without any government subsidies. "We have close to 450 people directly employed in the production process, about 50 dedicated engineers based in Brisbane. "The Wacol factory also has approximately 85 local suppliers delivering more than 3,500 different components to the Wacol factory – of which, many are produced right here in Australia." Australian Truck Association (ATA) chair Geoff Crouch and CEO Ben Maguire were present at the Wacol site to celebrate the achievement with Voorhoeve, Volvo Trucks Australia vice president Mitch Peden, Australian Made CEO Ian Harrison, and other guests. Volvo Group Australia joins Australian Made Campaign The production milestone coincides with Volvo Group receiving the Australian Made Campaign certification to carry the iconic green-and-gold ‘Australian Made’ logo. Volvo Group Australia is now the only truck manufacturer in Australia to have been awarded this certification. "We’re delighted that Volvo Group Australia has joined the campaign," Harrison says. "It reflects their commitment to promoting local manufacturing, both in its direct production operations but also through their support of the local automotive components’ industry." Investment to meet Australian trucking’s long-term needs Voorhoeve also spoke about the unique challenges of the Australian truck market. "Our trucks work harder than anywhere else in the world. Our loads are heavier, the climate is hot and dusty, and the distances are greater," he says. "But our Australian engineers leverage the globally proven vehicle platforms and latest innovations to design trucks that are tailored for the unique Australian conditions. "It’s a very competitive market here in Australia, but building trucks locally means we can meet and exceed the demands of customers in this competitive market, by building them a truck that is exactly to their specification." Volvo Group Australia’s local investment plans Voorhoeve details the Group’s current and future investment plans for its Australian facilities. "We are committed to manufacturing trucks in Australia and have invested over $27m in the production facility alone in the last six years, and will invest a further $3.7m in upgrading our chassis treatment and cab paint process," he says. "We’re talking about a lot of money, which is a reflection of how confident we are in local manufacturing. "We are also investing considerably, together with our private partners, in our dealerships and customer service network." Voorhoeve explains that, between the Volvo Group and private partners, approximately $160m worth of investment will have been made between 2014 and 2018 in its dealership and service network. "Of the $160 million in investments for 2014 to 2018, Volvo Group will have contributed $65 million to finance projects," he says. "These include several to be completed in 2018, notably, new national headquarters, and new dealerships in both Brisbane and Sydney." Trucking remains big business in Australia Voorhoeve says that the investment amounts are considerable because trucking is big business in Australia. "The road freight transport industry is generally quite humble, and rarely in the spotlight despite being a $42 billion industry. Almost everything we touch, eat and use has been on a truck at some stage," he says. "The industry employs approximately 150,000 people across more than 40,000 businesses, contributing $8.4 billion in wages back into the economy." While growth in the transport industry has slowed in recent years, it has weathered the slowdown of the resource sector quite well and looks to be bouncing back in 2017, Voorhoeve says. . -
Australasian Transport News (ATN) / November 16, 2017 The Australian Trucking Association (ATA) joined the team of Volvo Group Australia at its Wacol factory to mark the production of 60,000 locally-manufactured trucks. ATA chairman Geoff Crouch and CEO Ben Maguire were with Volvo Group Australia president and CEO Peter Voorhoeve, Volvo Trucks Australia vice president Mitch Peden, Australian Made CEO Ian Harrison and other guests to celebrate the milestone today. Crouch says more people should learn about the company’s achievement as many Australians are currently unaware of the "substantial" local truck manufacturing industry despite a decline in domestic car manufacturing. "More than a thousand people work for Volvo Group here in Wacol, including engineers, factory workers and administrative staff," Crouch says. "They build Australian trucks under the Australian Design Rules for Australian businesses." Maguire congratulates Voorhoeve and the Volvo Australia team for their success in the Australian manufacturing industry. The 60,000th truck will become ATA’s new Safety Truck as part of the Volvo Foundation sponsorship that dates back to 1991. "Volvo Trucks is known for its commitment to safety, and has continued that commitment through its long and generous sponsorship of the ATA," Crouch says. "Volvo Trucks’ own safety campaign, Stop Look Wave, aims to keep young children safe around traffic. "And the Volvo ATA Safety Truck travels across Australia to educate 18-25 year old car drivers about how to share the road safely with trucks. "Sadly, seven out of ten accidents between trucks and cars are due to mistakes by car drivers, so it is a critical safety campaign. "Today is a great day for Volvo Group Australia. "From the trucking industry to everyone here at Wacol – thank you for helping us deliver the goods for Australia."
-
Diesel News Australia / November 2017 In the Northern Territory everything has to do with scale – it represents 18 per cent of Australia’s land area but is home to just one per cent of the country’s population. Diesel News talked with an operator tasked with distributing fuel across the Territory. Sitting in a modest industrial unit in Katherine in the Northern Territory, and talking to the owner of the operation, John Fraser, it’s easy to think of the operation run by the genial, relaxed man in battered shorts and a shirt, with a dusty baseball cap, as a small concern. However, start talking about the task the company handles, plus the area covered and customers serviced, and you soon realise this is a big operation in a big country, using big trucks. Sitting in the shade of the long shed which constitutes the company’s workshop, headquarters, office and smoko hut, the scene is dominated by the truck parked down one side. This is one of those big trucks you will only see in remote areas pulling multiple trailers, a long-wheelbase Volvo FH twin-steer, tri-drive truck with a tanker on the back and coupled to three tanker trailers. This is not your run-of-the-mill truck, and it does not work in a run-of-the-mill operation. This is one of three trucks that covers the entire Northern Territory for IOR Petroleum. The fuel supplier has a number of remote outlets across the Territory to supply the top-weight road trains that work on these roads. “I was a livestock agent for years,” says John. “I always liked trucks so I bought one, and did it up. Then I bought a working truck and leased some of my yard space to IOR for them to put their tanks in. Then I started hauling some fuel for them. “I have been working for IOR for 12 years now, starting with one truck and then going to two trailers. As the business grew we also had a livestock trailer for a while. It was on a sub-contracting deal, but then we moved it over to pulling fuel tankers and it’s grown from there. “We currently run two trucks and have another undergoing restoration. There are two trucks on fuel full time, plus one subcontractor. We have the 700hp Volvo rigid with three trailers, and we have a Kenworth K200 tri-axle prime mover pulling three trailers. “It has a pusher axle so it gives you full loading on the drive. With the pusher you can get 22.5 tonnes on the drives in the Northern Territory. It’s not as expensive as the tri-drive and we reckon we can get away with a bit less maintenance.” The tri-drive twin-steer Volvo has a completely Volvo driveline and runs at a GCM of 164 tonnes. The truck is actually rated up to 175 tonnes, but this kind of loading is only achievable if John upgrades the dollies’ suspensions. IOR has fuel tanks in Noonamah, 40km south of Darwin; Katherine, a further 300km down the road; Tennant Creek, 1,000km to the south of Darwin; Alice Springs, 1,500km to the south and Kununurra, a mere 800km to the west of the Territory’s capital. All of the fuel comes out of the sole fuel terminal in the Territory, the Vopak Terminal, situated in the recently developed port area. The work is varied as the demand for fuel goes up and down due to seasonal changes, livestock movements to the docks, etc. Normally, at least three or four loads a week come into the Katherine facility, where a steady stream of trucks comes in to fill up at the refuelling site, situated beside the Stuart Highway to the north of the town. Frasers also has to keep the Alice Springs facility topped up, but it is not as busy as Katherine.Truck traffic from Queensland, South Australia and Western Australia all has to pass through Katherine, keeping the demand for fuel consistently high there. Fuel is also delivered out to individual customers, cattle stations, and the like. These smaller and less regular drops can be fitted around the main task at hand, namely ensuring IOR’s diesel bowsers keep flowing. The combination of all of the fuel deliveries keeps all three trucks busy and on the road full time. “We run virtually everything for IOR in the Northern Territory,” says John. “We decide which tanks need to be topped up. We load the fuel, deliver it and then supply them with the paperwork to tell them where it all went. When you’ve been doing it for twelve years, you know which tanks use what amount of fuel each day, roughly. “We can plan ahead fairly well, if there’s a big rush on it might catch you out, but you have enough of a buffer to cope with it. You get a feeling for what is going on. We also own the weighbridge in Katherine, so we know what cattle trucks are booked in to weigh, and when a big lift is coming in. Suddenly, a tank which uses 4,000 litres a day can use 10,000 a day for the next week or so. “We organise the schedules, do some pricing and even maintain their bowsers for them, basically everything for IOR Northern Territory. If a nozzle on a bowser is leaking, we fix it. We have three forms of income from them – they pay us for delivery, for our sites and for us to maintain their equipment.” Fuel demand at the bowsers can change dramatically from week to week. It also puts a lot of pressure on cattle suppliers, and the other businesses that support them, who are also on a stop/start cycle. “The livestock trade has changed so much,” says John. “With the introduction of these bigger ships for live-export cattle, it’s either a flood or they are stopped. When I worked in the industry, the ships only held 1,000 head of cattle each, so we loaded one every five days or so. “Now, the ships hold up to 21,000 head. So, it’s a big rush with every triple road train available on the road for four or five days prior to sailing. Then nothing moves for the next week or so, until the next big ship comes in.” .
-
Introducing the Hino 300 Series 4x4 – Made 4 Australia, Made 4 Work
kscarbel2 replied to kscarbel2's topic in Trucking News
. -
Chicken producer Holly Farms on the shore had a fleet of Kenworth K100s with VT903s. They were every bit as bad as you heard. This was a case of, "If all else fails, sell it to the government. They buy low bid no matter what". The Mack E9, as the French can tell you, was a far superior V8 powerplant for the military applications described.
-
Volvo Group Press Release / November 16, 2017 Volvo Group takes the next step towards the future with an autonomous concept truck for hub-to-hub transportations in semi-confined areas like harbours and dedicated lanes on highways. Autonomous solutions bring benefits and serve the needs of both the customer and of society. .
-
Discover Renault Trucks T for long haul transport
kscarbel2 replied to kscarbel2's topic in Trucking News
-
IVECO BUS Press Release / November 13, 2017 The launch of the 14.5 meter, three-axle Crossway marks the start of a new era in IVECO BUS' city and intercity bus line. Available with two or three doors, it expands the already-extensive Crossway line, a paragon of performance and cost-effectiveness, and is positioned as the ideal vehicle for optimizing access to cities and large towns and to serve heavily frequented routes. .
-
-
Cummins Press Release / November 15, 2017 One of the most enduring engines in Cummins’ long history, the V903, is celebrating a remarkable 50 years in service. “Many engines have done the Cummins name proud, and prominent among these is the V903,” said Tom Terkhorn, Manager of Defense Products for Cummins Inc. “The first V903 crankshaft was laid at the Cummins Engine Plant (CEP) in Columbus, Indiana (USA), late in 1967, and since then the engine has progressed from 280 horsepower (hp) for truck use to its current peak output of 675 hp for military equipment.” The V903 is an eight-cylinder ‘V’ configuration with a 903 cubic inch (14.8-litre) displacement. Providing high power density, it has four valves per cylinder, is turbocharged and air-to-water aftercooled, and has a low pressure common rail fuel system. Today, the V903 is produced primarily for military applications, notably the US Army’s iconic Bradley Fighting Vehicle, rated at 600 hp. In 2018, a 675 hp version will be installed in the upgraded Bradley ECP 2, Armored Multi-Purpose Vehicle (AMPV) and Paladin M109A7 howitzer. In actual operations, the V903 powered Bradley has showed a combat readiness of over 95 percent – the highest of any armored vehicle in the history of the US Army. The V903 was originally developed for the on-highway truck and construction markets to meet the requirements for a lightweight, compact diesel engine in the 280-320 hp range. It went on to make its mark in other applications such as recreational and commercial boats, mining equipment, and farm tractors. The V903 began its life in the Bradley Fighting Vehicle in 1981 when Cummins upgraded the power level of the commercial truck engine from 350 to 500 hp with the addition of air-to-water aftercooling and upgraded fuel system. Cummins moved the engine up to 600 hp V903 in early 1989 to maintain the Bradley’s mobility when its full combat weight increased to 60,000 lb as a result of added armor. The power boost was achieved using technologies developed for other Cummins products. Importantly, there were no changes to the length, width and height of the engine which had to fit into the Bradley’s notably tight powerpack compartment. “Cummins conducted accelerated wear and abuse tests for final acceptance of the engine’s revised design and these showed that thermal and mechanical stresses of the 600 hp engine were actually lower than the 500 hp version,” said Keith Baylor, V903 Product Validation Manager. “This meant the army could expect improved reliability and durability. Field performance of the 600 hp engine confirmed this initial expectation.” Development of the 675 hp version of the V903 was completed in 2013 for the US Army’s Paladin M109A7 howitzer, and in 2018 it will be fitted in the upgraded Bradley ECP 2 and Armoured Multi-Purpose Vehicle (AMPV) which replaces the M113 armored personnel carrier. Production of the V903 – both remanufactured and new engines – is carried out at Cummins’ Seymour Engine Plant in Indiana (USA). “The V903 platform will continue to support the armored vehicle forces for decades to come,” said Tom Terkhorn. .
-
Jerry, the "ram" wasn't a great design. They never held up, rain went in and down....I could go on and on. Nobody takes one off unless it's smashed or disintegrated. A standard hood, which most "F" models used, is better. https://dynamic.donaldson.com/WebStore/hierarchy/hierarchy.html?section=10121
-
Sean Kilcarr, Fleet Owner / November 15, 2017 There is no other tool capable of doing the work trucks do; there’s just no debating that. How that tool gets powered, though, will be a major point of argument now and in the future. So I recently listened to Martin Daum, member of the board of management at Germany’s Daimler AG and head of the company’s global Daimler Truck and Daimler Bus divisions, discuss the future of trucking during a press conference at the big Expo Transporte 2017 show in Guadalajara, Mexico. One of the interesting points he made – one well-known to anyone in the freight business – is that our economic systems today cannot function without trucks. There is just no other transportation tool – train, plane, automobile, etc. – that can do the work that trucks day in and day out. “The world can live without passenger cars but it cannot live without trucks,” Daum said. “If you need to haul 80,000 lbs. of dirt, a wheelbarrow can’t do the job. You need something that can haul such heavy loads – and that is a truck.” It’s a point I’ve made more than a few times myself: Trucks are a necessity. For example, the expectations for speedy delivery of goods ordered via the Internet – and to not pay an extra transportation fee for said delivery – is falling squarely on the shoulders of truckers and there’s little to no recognition of the vital role they play in making those deliveries happen each and every time. Indeed, trucks currently haul over 70.6% of all the freight in the U.S. (though that is expected to slip to a hair over 67.2% by 2028) and haul over 80% of the freight in Mexico, according to Flavio Rivera, president and CEO of Daimler Trucks Mexico. Thus, trucks are here to stay – whether they are loved or not for the job they do. The question, though, is whether they must remain powered primarily by diesel and gasoline. I talked to Mike Cammisa, vice president of safety policy connectivity, and technology for the American Trucking Associations (ATA), about that very subject at a recent press event in Washington D.C. and he’s of the opinion that we’ll start to see more powertrain “customization” in terms of fuel source in the future; a customization trend driven by the type of duty-cycle a truck must perform. “What I see in the future is a diversity of powertrains and fuel sources; electricity is one of them and does seem appropriate in shorter haul applications, where the truck returns to a central depot and can be recharged overnight,” he explained to me. “It makes sense to match the powertrain to the needs of the duty cycle and you can also combine systems, as well, such as in a hybrid powertrain that is part electric and part diesel,” Cammisa said. “Especially in inner city traffic situation, you could then run on electricity.” Daimler’s Daum is of a similar mindset and believes one of the things truck OEMs must do in the future is to offer a “full range of options” when it comes to powertrains just as they do with cab interior packages and the like. “Natural gas, propane and electricity are all options,” he said, pointing in particular to the new eCanter all-electric medium-duty truck built by Daimler subsidiary Mitsubishi Fuso. Right now, Daum said the eCanter will only be sold on a “use case by use case” basis to customers around the globe, with limited production of the vehicle for the next two years. But by 2019, he expects the eCanter will be ready for “full throttle production” as he put it. “It’s about on one side seeing what is possible and on the other knowing their limitations,” Daum said. “We know diesel is right now a necessity because it can haul higher loads. But we’re also showing that there is potential for an emission-free future.” On a final note, he stressed that the improving economic picture for the U.S. and other countries is generating some positive trends for truckers. But Daum also cautioned that planning truck production levels correctly will be the real trick to ensuring such positives don’t turn into negatives. “Times are not bad. That is a German euphemism for ‘good.’ And good times for the global economy always means good times for trucking,” he explained. “But global instability is the salt in our soup of daily life; for the commercial vehicle market is a volatile market. We continually calculate how many trucks a country or regional will need based on its infrastructure, population, and economic development,” he added. “So if you sell too many trucks – more than the system needs – a crisis will come. But if you sell too few – such as in 2009, when we sold only half the trucks the economy needed -- then good times will be ahead.” That’s one of many things to keep in mind as we barrel towards the close of 2017. .
-
MAN's $583,000 Electric Urban Bus to Test Cities' Spending Plans
kscarbel2 replied to kscarbel2's topic in Trucking News
MAN selects ABB fast chargers for its e-bus R&D facilities ABB Press Release / September 20, 2016 ABB, the leading power and automation technology group, is supplying fast chargers for depot and opportunity charging of electric buses, to MAN Truck & Bus for its new e-bus R&D facilities in Munich, Germany. In July MAN Truck & Bus announced serial production of fully electric buses by 2019. Pilots of the e-buses are planned to go into operation in 2018. The buses are developed at MAN’s R&D facilities in Munich, using a test bench equipped with different charging technologies from ABB. “Energy efficient and sustainable transportation is a key focus area of ABB’s Next Level strategy and we are committed to further advance e-mobility,” says Robert Itschner, Managing Director of ABB’s Power Conversion business unit. “ABB offers different technologies and solutions for electric vehicle charging and we are very pleased that MAN Truck & Bus chose our fast chargers for its test facilities.” For depot charging tests – used at the terminus where a bus has a longer stop – MAN will use an ABB fast charger with a CCS2 connector at its facility. Following the EU standardization for electric vehicle charging, it is the same connector that is used for electric cars. For opportunity charging tests, ABB will supply a charge pole with inverted pantograph. With its automated rooftop connection and a typical charge time of three to six minutes, opportunity fast charging systems allow charging at end stops and can easily be integrated in existing bus routes. The fast-charging solutions are based on IEC 61851-23, the international standard for fast charging electric vehicles. This ensures the appropriate safety systems are in place, the electrical design is in accordance with regulations, and the systems architecture and working principles are supported by a wider automotive community in the future. Both, ABB and MAN Truck & Bus AG are project partners in the European e-bus charging system (eBusCS) initiative which promotes international standardization of charging processes for electric buses to facilitate the introduction of electric bus systems in European cities. -
Bloomberg / November 15, 2017 Volkswagen AG’s MAN commercial-vehicle division expects its electric city buses, on sale as of 2019, to cost about 2.5 times more than conventionally powered ones, with the difference easing only in the following few years. MAN SE Chief Executive Officer Joachim Drees’s estimate for the models, giving a price tag of around 500,000 euros (US$583,000) a bus, highlights the struggle for vehicle manufacturers, cities and infrastructure providers to manage spending amid pressure to adopt zero-emission models to reduce pollution. The company predicts that a battery-powered bus’s lifetime cost is likely by 2023 to roughly match figures for combustion-engine versions, Drees said Monday at a briefing in MAN’s hometown of Munich. “The electric bus will be more expensive up front,” Drees said. “But batteries having a second life, and their rapidly falling prices, will help offset this,” along with savings on fuel and maintenance. Compared to carmakers, commercial-vehicle manufacturers have been slow to push forward with electric models, because their models carry heavier loads and need large batteries that take up room and increase costs. The broader range of vehicle uses and comparatively smaller numbers sold also make switching to electric versions a tougher undertaking. Still, a shift to the technology is accelerating as cities take steps to cut pollution and potential competitors emerge, including Tesla Inc. Daimler AG, the owner of the Mercedes-Benz and Freightliner brands, showed off a battery-powered heavy-duty model last month, weeks before electric-auto pioneer Tesla is scheduled to introduce its own truck. “We’d like to have electric buses as quickly as possible, and as many as possible,” Munich deputy mayor Josef Schmid said at the event. For the southern German city, shifting to electric buses means replacing a fleet of 460 vehicles. To help push along technology transformation and improve profitability, MAN is investing 400 million euros annually in the five years through 2020 at its commercial vehicle plants in three European Union countries as well as Russia, South Africa, India and Turkey. About 500 million will be spent on electric powering systems in that time, it said. The measures are part of a plan to increase margins across Volkswagen’s truck, bus and van business, including heavy-duty vehicle makers MAN and Scania, to challenge rivals Daimler and Volvo AB. “By 2025, I don’t expect cities to buy buses anymore that aren’t battery powered,” Drees said. .
-
Dodge to offer split, dual-function tailgate Automotive News / November 15, 2017 Spy photographers have caught confirmation that at least some versions of the next-generation Ram 1500 pickup will have a new dual-function tailgate, capable of both dropping down in the traditional manner or opening up 'French door' style. The tailgate design makes it easier for consumers to access the pickup's bed, without having to reach over the dropped tailgate or climb up on it. Earlier spy photos confirmed that the next-generation Ram 1500's tailgate can be dropped remotely using a button on the key fob. FCA US plans to begin production of the next-generation Ram 1500 in January at a retooled assembly plant in Sterling Heights, Mich., and will introduce the redesigned half-ton at the 2018 Detroit auto show. .
-
Renault Trucks Press Release / October 27, 2017 On 10 October 2017 at the Blainville-sur-Orne manufacturing site, Renault Trucks’ President Bruno Blin handed over the keys of a Renault Trucks D Cab 2,1m to Mr. Philip Thurston, Joint Managing Director of the British group Pace Logistics Services. This was the one millionth truck manufactured in the Normandy factory. Mr. Philip Thurston, Joint Managing Director of Pace Logistics Services, was handed the keys of the one millionth distribution truck assembled at the Renault Trucks factory – a D Cab 2.1m – on Thursday, 10 October by Bruno Blin, the Renault Trucks President. This was the 31th truck to join the Pace Logistics fleet, which is exclusively made up of Renault Trucks vehicles. This 18-ton "Guaranteed French Origin" D Cab 2.1m will be used for transporting pallets and for multi-point delivery assignments throughout the UK & Europe from their central distribution warehouse in Salford, Manchester. During the ceremony, Bruno Blin declared that he was "particularly proud of a British neighbour demonstrating trust in the excellence and expertise of French manufacturing." The President of Renault Trucks also congratulated the JDS Trucks dealership for its on-going relationship with Pace Logistics and for ensuring that its fleet vehicles remain operational at all times. The Blainville-sur-Orne factory has been producing trucks since 1957 and is specialised in medium weight vehicles and truck cabs. 262 cabs are manufactured and 76 trucks assembled every day. The site is currently recruiting 100 operators in order to meet increasing demand. Renault Trucks has three other manufacturing sites in France, in Bourg en Bresse, Limoges and Lyon. .
-
The Korea Herald / November 16, 2017 Swedish truck manufacturer Volvo Trucks is in discussion with Samsung to develop future-generation batteries in order to commercialize trucks powered by electricity, its chief said in Seoul on Wednesday. In an interview with The Korea Herald, Claes Nilsson, president of Volvo Trucks, said the company has been in talks with the South Korean tech giant to introduce electric trucks, which are part of what the company envisions for a “greener” future. A fully electrified truck, not only for Volvo but also other traditional manufacturers, still remains a mere concept, as it requires a long driving range, or in other words, lots of batteries. “We are already collaborating with Samsung when it comes to battery technology,” he said. “Where we are using the fully electric drive lines today is on the bus side. But as we move forward, we need (full electric lines for) trucks as well and yes, Korean industry, when it comes to semiconductors and battery and etc, are very advanced,” he said, without elaborating on the extent of collaboration with Samsung SDI, a battery and display making affiliate of the group, and what type of batteries they may be developing. Although Hydrogen has potential today, batteries are more likely to be the mainstream, he said. “But right now the most promising development is in batteries rather than hydrogen,” he said, adding that the company has been developing all three types of green trucks to be prepared as to where the technology might lead to. “But that can change in five or 10 years, nobody knows.” The head of Volvo Trucks was in Seoul to present the company’s future vision of taking a lead in connectivity, automation and electro-mobility in the commercial vehicle segment. Also, to keep its top position in the Korean market, the company has decided to install two safety features -- collision warning with emergency braking and lane-keeping support -- in all its heavy-duty trucks to be sold here starting January, one year ahead of the Korean government’s plans to require commercial vehicle manufacturers, both domestic and foreign, to enhance safety features in their models from 2019. Traffic accidents caused by trucks and buses have been major safety concerns here. “When we think the technology is mature and the market is ready, we don’t wait for the legislation,” he said. Currently, Volvo Trucks is the top commercial vehicle importer here and the third after two domestic brands, Hyundai and Tata Daewoo. South Korea is Volvo Trucks’ ninth-biggest market in terms of profit generation. It expects to sell about 3,000 trucks in the country, a 15 percent increase from last year. Though the market here accounts for only 3 percent of all Volvo trucks sold worldwide, South Korea is a growing and important market. Demand for efficient trucks is high not just among customers, but also in terms of the traffic environment. “The customer base in this county is demanding efficient types of trucks in transportation, we believe we have good product offers to this market,” he said. “We also believe that (the) transportation environment here is very demanding in terms of weight and road condition and utilization, and very quality conscious customers can help us actually develop.” .
-
MAN Agricultural Trucks at AGRITECHNICA 2017
kscarbel2 replied to kscarbel2's topic in Trucking News
2017 MAN Agricultural Trucks at AGRITECHNICA The agricultural sector offers various opportunities for using MAN trucks The MAN TGS 18.500 4x4 BLS on display is equipped specifically for the industry A variety of transport tasks arise in agricultural business and for contracted hauliers. Thanks to their high payload, low fuel consumption and typical high driving speed, trucks are gaining ground in the transportation chain between farm, field and warehouse. With this in mind, the MAN TGS is kitted out as an agricultural truck and features all-wheel drive, fifth-wheel coupling, trailer coupling and support, load-sensing hydraulic system and wide, soil-friendly agricultural tyres. MAN trucks are not only suited for transporting harvested crops over great distances – from grain to agricultural dealers, silo corn to the biogas plant, beet to the sugar refinery or potatoes to the starch plant – right from the farm or from the edge of the field. It is in combined use in the field, on the road and in further processing applications where MAN agricultural trucks are really able to demonstrate their high level of efficiency. They offer distinct advantages in the transportation chain compared to other vehicle types, due to their high payload of 38 or 40 tonnes, lower fuel consumption and the higher speeds typical of trucks. What's more, established semitrailer combinations often enjoy greater acceptance among other road users and in the population in general than tractors with bulky, multi-axle trailers do. Agriculture and the way it is perceived by the public has been going through a period of change for some time. The areas being cultivated are growing all the time due to economic reasons. So too are the volumes being transported. The areas farmed by agricultural businesses are no longer situated in the direct vicinity of farm buildings. The transport distances between locations are therefore on the increase and the areas which contracted hauliers have to cover is expanding. Contractors are paying more and more attention to the efficiency and total cost of ownership (TCO) of their fleet, while the public are concerned with the issue of environmental friendliness in the transportation chain. The increasing prevalence of biogas plants is ensuring increased transport volumes for the delivery of corn, grass and grain silage, as well as the movement of fermentation substrate across great distances. Transportation applications in particular are where trucks that have been adapted to meet the needs of the agricultural industry really show their strengths. This is something that has come to MAN's attention with the increase in demand for adapted vehicle concepts. In most cases, these are semitrailer tractors in the MAN TGS series, pulling trailers specially designed for agricultural use. Options include semitrailer tractors and chassis with rear wheel drive and standard or medium-high design height. All-wheel drive MAN TGS in high design height with switchable or permanent front wheel drive are also available. With permanent all-wheel drive, the centre differential means it is possible to balance the front and rear axles, preventing damage to the floor when cornering. The solution positioned between road use and all-wheel drive is called MAN HydroDrive and offers hydrostatic front wheel drive for additional traction. The MAN TGS as an agricultural truck Showcased by MAN Truck & Bus at AGRITECHNICA 2017, the world's leading trade fair for agricultural machinery held in Hanover, the two-axle MAN TGS 18.500 4x4 BLS semitrailer tractor impresses with its wide range of equipment specifically for use in the agricultural industry. One of these is the option to have the vehicle approved for agricultural or forestry use. The advantage of this is the fact that its permitted width can be up to 3.0 metres and that the vehicle is exempt from Sunday driving bans applicable in certain countries. Permanent all-wheel drive is the ideal choice for agricultural use. Routes to many fields take vehicles across challenging terrain and roads that have not been asphalted and are usually covered in gravel. What's more, not all access routes to silage heaps, slurry tanks or silo systems on agricultural premises are surfaced. For maximum traction, the driver can apply the differential locks in the longitudinal and then in the transverse direction using just one rotary switch. The all-wheel drive really comes into its own when combined with the soil-friendly agricultural tyres, as they allow the vehicle to leave the country lanes and move onto grasslands or fields, where the chopper can fill the attached trailer straight away. The tyres are able to meet the various requirements placed on them: the low level of pressure they exert on the ground means they look after country lanes and productive land, their V-profile takes care of traction, and they are still able to manage high transport speeds on surfaced roads. When a vehicle is approved for agricultural or forestry use, it can be up to 3 metres wide – a factor which influences tyre choice. If the standard truck width of 2.50 metres is to be maintained, 445/65 front tyres and 600/50 individual rear tyres are fitted to the axles. Yet if the maximum permitted width is to be utilised, the MAN TGS can run on 580/65 22.5 tyres at the front and 750/45 26.5 tyres at the rear. MAN takes care of the huge wheel arch required with adapted mudguard cutouts, splash guards and attachments. If transportation is to take place over an extended period and on surfaced roads, it is worth replacing the field tyres with road tyres that have higher wear resistance and lower rolling resistance, making them more economical. In the high design height, the driver can comfortably climb into the MAN cab using the four steps. The interior colours of “sand” or dark-grey “urban concret” convey a user-friendly appearance. To provide a view of the load, windows have been incorporated into the rear wall. Alternatively – and often providing a more practical option – the images captured by two externally mounted cameras can be played on the 7-inch display of the new MAN infotainment system, enabling the driver to monitor the load and the area around the rear of the vehicle. On the outside, the M cab impresses with functional accessories: grilles on the rugged, three-piece steel bumper protect the headlights. A step on the left mudguard with a long handrail on the roof makes it easier to see into the tipper and cross over to the semitrailer. Additional headlights illuminate the area around the vehicle and rotating beacons warn other road users. The attachment of a snow-plough mounting plate with the associated elevated headlights and indicators enables contractors to make economical use of the vehicle in the winter season too. Behind the cab, the exhaust pipe is located on the right and tilted upwards to reduce the exhaust gases released in the vicinity of the vehicle and to prevent dust from being swirled up on the ground. The 6-cylinder in-line engine from the MAN D26 Common Rail series has a capacity of 12.4 litres and delivers 500 hp at 1400 rpm in the Euro 6c emission standard. Its maximum torque is 2500 Nm at 930 to 1400 rpm. This engine series is also available with an output of 420 hp and 460 hp. The engine is coupled with the automated MAN TipMatic 12 gearbox. With its SmartShifting function, the driver is able to change gear particularly quickly depending on the driving situation in order to minimise the interruption to traction. The “OFFROAD” gearbox software provided for all-wheel vehicles and which is activated by turning the gear selector switch is specially adapted for journeys over difficult terrain. It prevents drivers from skipping gears as well as indicating modified shifting times and higher shifting speeds to prevent interruption to drive traction. As a result, a typical truck speed of max. 89 km/h is possible even with a full payload – provided this is permitted in accordance with traffic regulations. At low and medium speeds in particular – as are common with MAN agricultural trucks – the wear-free MAN PriTader really demonstrates its brake force. Integrated into the water circuit, the maximum brake output of this system is 620 kW. In terms of industry-specific equipment, MAN can also install a trailer coupling support in addition to the fifth-wheel coupling at the end of the frame. This is comprised of a bar coupling with a 38-mm bolt and an 80-mm ball coupling. It also includes two 50-mm steering balls to pull agricultural trailers with forced steering. This mechanism allows the trailer to cleanly follow the path of the tractor vehicle when cornering. The installed load-sensing hydraulic system regulates the output and pressure as required. This means that the full hydraulic output is only provided when required and that fuel is saved, as the hydraulic pump does not have to permanently operate at full capacity to supply the hydraulic system with high pressure. Alternatively to the two-axle semi-trailer tractor, the MAN TGS agricultural truck is available as a two-, three- or four-axle chassis with a drive ranging from 4x2 to 8x8 to allow various bodies such as grass silage trailers, push-off trailers, lime and fertiliser spreaders or slurry tanks to be mounted. Although this vehicle concept has the edge over the semitrailer combination in terms of its offroad properties, it is restricted with respect to its payload as well as being at a disadvantage in terms of its suitability for universal use and the extent to which it can be used economically all year round. Modifications to MAN TGS semitrailer tractors and chassis for agricultural use are carried out by MAN-certified companies. Depending on the task at hand, these include the MAN Truck Modification Center (TMC) and MAN-qualified modification contractors. The MAN TGS agricultural truck in use all year round Another advantage of the MAN agricultural truck relates to the extent it can be used all year round. Once farming operations and harvest time have come to an end, you need only exchange the tyres and semitrailer to be able to use this semitrailer tractor in the transport sector – primarily in the construction industry – and as a winter service vehicle. The MAN TGS provides contractors with economical use of their vehicle and a source of income all year round. MAN trucks for the agricultural industry Trucks from the MAN product portfolio are suitable for a wide range of tasks in the agricultural industry. The TGL, TGM and TGS series transport mobile grinding and mixing plants to name just a couple of examples. When choosing the chassis, the size and the power take-off performance required for the grinding mill, mixing facility, screw conveyors and conveyor belts are the decisive factors. The semitrailer tractors for tank semitrailers with liquid waste such as slurry or fermentation substrate as well as for silo trucks containing fertilisers and feed generally come from the MAN TGS series. These vehicles ensure an efficient transport solution. Thanks to their high payload and fast driving speed, MAN TGM with all-wheel drive and soil-friendly agricultural tyres provide an alternative solution for spreading fertiliser on navigable and stable ground. And given that it is often necessary to bring workers along, MAN cabs can also be equipped with three seats. MAN HydroDrive for traction if required in the agricultural industry In 2005, MAN launched the HydroDrive drive system – a solution which at the time was the only one of its kind worldwide. The selectable hydrostatically powered wheel hub motors in the front axle – or the second axle if the vehicle has four axles – are the ideal configuration for vehicles that are primarily driven on surfaced roads and only occasionally need additional traction. This may be the case if the vehicle has to move from the road to the edge of the field. For example, it may be necessary to deliver seed or slurry, collect beet from the clamp or gather bales of grass or straw. Milk collectors often have to navigate gravel or snow-covered paths on farms to get to the milk tank. The payload advantage compared to a conventional all-wheel drive is one of the recognised benefits of MAN HydroDrive. The weight advantage is 500 to 750 kilogrammes depending on the vehicle configuration. From a business perspective, the fuel saving represents a further benefit – when the system is switched off, the front wheels rotate freely, as with an on-road vehicle. MAN also offers this additional traction for vehicles with a standard height design. The low frame height makes it easier for drivers to enter and exit the cab. The system also sets itself apart in terms of how easy it is to mount bodies, as all MAN TipMatic and MAN HydroDrive components are located below the top edge of the frame. The MAN TGS as a milk tanker For milk tankers, the MAN TGS series offers a three-axle chassis that has been specially configured for the industry. The steered trailing axle reduces the turning circle, making it easier to manoeuvre in built-up areas and on farmsteads. Four corner air suspension is recommended to ensure high suspension comfort and the gentle transportation of fragile loads. To create space for the fittings cabinet mounted on the right of the frame, MAN has moved the units that were installed there for the Euro 6 standard. This means that the exhaust silencer, battery box and fuel tank are now on the left. As a result, body manufacturers have a space ranging from 2.5 to 3.1 metres in length to work with for their installations. To ensure safety and improve the driving characteristics of tankers, MAN provides a high-load roll stabilisation package consisting of a stabiliser and X control arm. The MAN TGS and TGX as an animal transporter In order to transport animals promptly and with care, MAN offers chassis from the TGS and TGX series. Three-axle vehicles with a steered trailing axle bring together loading length and manoeuvrability. The air suspension at the axles ensures that delicate cargos are looked after. If animals are housed across multiple levels, this results in a high centre of gravity for the body. To reduce rolling movements in the body, MAN provides a high-load roll stabilisation package with stabilisers and an X control arm to guide the rear axle. The MAN TGX series supplies economical and high-torque engines ranging from 360 hp to 640 hp. Particularly when transporting across challenging terrain or over great distances, engine outputs of over 500 hp are required to complete transport tasks promptly. The 6-cylinder in-line engines from the D38 Common Rail series deliver 540 hp, 580 hp and 640 hp. These are reserved exclusively for the MAN TGX series. In the somewhat narrower cabs of the MAN TGS series, the output rating starts at 320 hp and extends all the way up to 500 hp. Loading points on agricultural sites or pastures cannot always be reached via asphalted roads. What's more, snow-covered roads in winter can make access difficult. In such cases, the MAN HydroDrive system installed in the TGS and TGX series is on hand to provide additional traction. The hydrostatic drive installed in the front axle can be combined with both the TipMatic automated gearbox as well as manually operated gearboxes. Technical data for the vehicle exhibited at AGRITECHNICA 2017 Type Agricultural semitrailer tractor with permanent all-wheel drive MAN TGS 18.500 4x4 BLS Wheelbase 3900 mm Suspension Front axle leaf-spring suspension 9.5 t Rear axle air suspension 13.0 t Height High design height Cab M with seating for 2 and ladder Engine 6-cylinder D26 Common Rail in-line engine, emission standard Euro 6c Cylinder capacity 12,419 ccm Output 500 hp (368 kW) at 1800 rpm Torque 2500 Nm at 930–1400 rpm Gearbox MAN TipMatic 12 28 OD with OFFROAD gearbox software Rear axle Planetary axle Axle ratio i = 4.00 Speed 1.5–89 km/h Permissible axle loads with agricultural tyres Front 9000 kg / rear 10,000 kg Permissible gross weight 18,000 kg Permitted gross train weight 40,000 kg (technically 44,000 kg) Tyres Front axle 445/65 R 22.5 Rear axle 600/50 R 22.5 Paintwork Cab: MAN green M107 Rims: light ivory Frame: graphite black RAL 9011 Industry-oriented agricultural equipment Conversion to agricultural tyres Trailer coupling support on the end of the frame with steering balls Load-sensing hydraulic system Rear-view camera Stainless-steel roof bar with 4 working lights -
MAN Truck & Bus Press Release / November 13, 2017 The agricultural sector offers various opportunities for using MAN trucks // The MAN TGS 18.500 4x4 BLS on display is equipped specifically for the industry A variety of transport tasks arise in agricultural business and for contracted hauliers. Thanks to their high payload, low fuel consumption and typical high driving speed, trucks are gaining ground in the transportation chain between farm, field and warehouse. With this in mind, the MAN TGS is kitted out as an agricultural truck and features all-wheel drive, fifth-wheel coupling, trailer coupling and support, load-sensing hydraulic system and wide, soil-friendly agricultural tyres. MAN trucks are not only suited for transporting harvested crops over great distances – from grain to agricultural dealers, silo corn to the biogas plant, beet to the sugar refinery or potatoes to the starch plant – right from the farm or from the edge of the field. It is in combined use in the field, on the road and in further processing applications where MAN agricultural trucks are really able to demonstrate their high level of efficiency. They offer distinct advantages in the transportation chain compared to other vehicle types, due to their high payload of 38 or 40 tonnes, lower fuel consumption and the higher speeds typical of trucks. What's more, established semitrailer combinations often enjoy greater acceptance among other road users and in the population in general than tractors with bulky, multi-axle trailers do. Agriculture and the way it is perceived by the public has been going through a period of change for some time. The areas being cultivated are growing all the time due to economic reasons. So too are the volumes being transported. The areas farmed by agricultural businesses are no longer situated in the direct vicinity of farm buildings. The transport distances between locations are therefore on the increase and the areas which contracted hauliers have to cover is expanding. Contractors are paying more and more attention to the efficiency and total cost of ownership (TCO) of their fleet, while the public are concerned with the issue of environmental friendliness in the transportation chain. The increasing prevalence of biogas plants is ensuring increased transport volumes for the delivery of corn, grass and grain silage, as well as the movement of fermentation substrate across great distances. Transportation applications in particular are where trucks that have been adapted to meet the needs of the agricultural industry really show their strengths. This is something that has come to MAN's attention with the increase in demand for adapted vehicle concepts. In most cases, these are semitrailer tractors in the MAN TGS series, pulling trailers specially designed for agricultural use. Options include semitrailer tractors and chassis with rear wheel drive and standard or medium-high design height. All-wheel drive MAN TGS in high design height with switchable or permanent front wheel drive are also available. With permanent all-wheel drive, the centre differential means it is possible to balance the front and rear axles, preventing damage to the floor when cornering. The solution positioned between road use and all-wheel drive is called MAN HydroDrive and offers hydrostatic front wheel drive for additional traction. .
-
We never thought of the F as old, and the WS as new. Rather, the F was "East Coast" and the WS was "West Coast", two very different trucks for different markets. The F certainly was born years before the WL/WS, but the steel dashboard F-600 of 1962 was a very different truck from the F-700 "Interstater" of 1980. Continually improved to keep it competitive, it had a completely new interior, raised cab, deeper frame and more. The MH Ultra-Liner was the convergence, a truck adaptable to both the east and west coast operators. If I wanted to make money like Overnite, UPS and Chemical Leamon, I'd buy a Mack naturally, and choose F-models over the problem-ridden Cruise-Liner. We actually sold Overnite a handful of Cruise-Liners (54-inch day cab 6x4s), but they were not pleased. I really liked the CL-72/721 Mack "Dynamax" wet clutch (4-plate, push-type, DEXRON fluid) spec'd by UPS. Produced for us by Rockford Clutch Corp., they almost lasted forever. That was an option to all customers too.
BigMackTrucks.com
BigMackTrucks.com is a support forum for antique, classic and modern Mack Trucks! The forum is owned and maintained by Watt's Truck Center, Inc. an independent, full service Mack dealer. The forums are not affiliated with Mack Trucks, Inc.
Our Vendors and Advertisers
Thank you for your support!