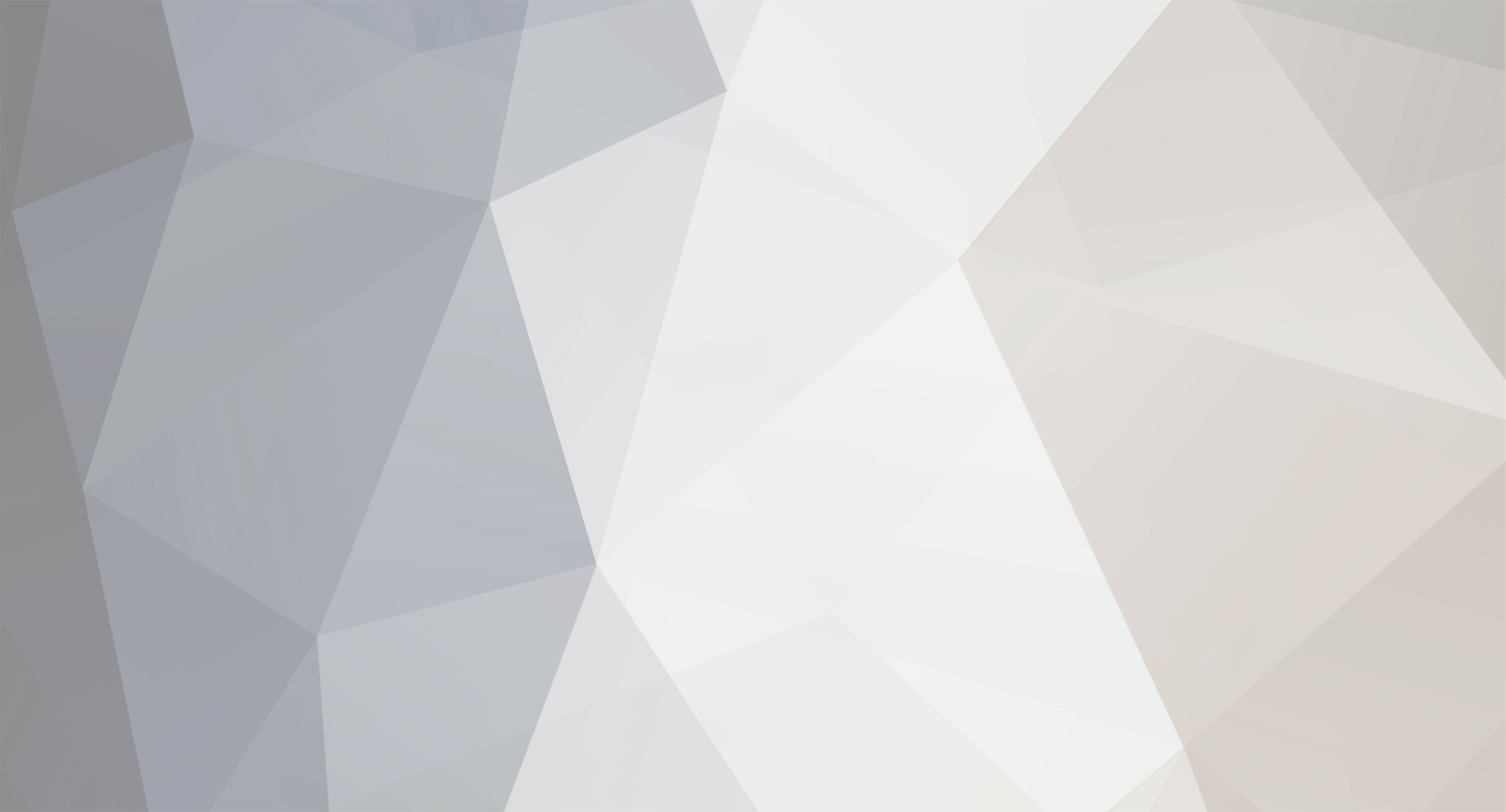
kscarbel2
Moderator-
Posts
17,893 -
Joined
-
Days Won
86
Content Type
Profiles
Forums
Gallery
Events
Blogs
BMT Wiki
Collections
Store
Everything posted by kscarbel2
-
Superliner headlight wiring
kscarbel2 replied to r686st's topic in Electrical, Electronics and Lighting
My understanding of Volvo policy is they desire not to support trucks older than 15 years of age. And that "appears" to be true. Frankly speaking, they look forward to the non-Volvo Mack era trucks being a thing of the past. It's to be expected that Volvo's passion is about Volvo. -
MAZ Trucks Press Release / July 28, 2017 .
-
Road test report: Hino's 500 series FM2635 truck Steve Brooks, Trade Trucks AU / July 31, 2017 In a six-wheeler rigid market saturated with good trucks, the flagship FM2635 model in Hino’s revamped 500-series wide-cab range ranks with the best of them. · Hino is now better placed in this category than any time in its Australian history with the FM2635 · The Hino FM2635 range cover two and three-axle configurations with GVM from 16-18 and 26 tonnes, and GCM ratings from 32-45 tonnes · The Hino FM2635 is a model more suited to longer regional runs than ‘round-town rambles · The manual Hino FM2635 is also equipped with the fuel-saving attribute of an engine stop/start system · Hino’s A09C engine has been considerably reworked with among other things, a new turbocharger and a swap from Bosch to Denso common-rail fuel injection Not often, but every now and then a new truck comes along that takes you by surprise. Whether the surprise is good or not … well, that’s something else. Like, if for any reason you expect a new model to be a stunningly good thing only to be left with a yawning sense of ‘so what’ after the first stretch behind the wheel, then the surprise is obviously in the disappointment rather than the delight. On the other hand, if you’re not expecting anything particularly inspiring but in short time find yourself admiring unforeseen attributes, then perhaps surprise is the greatest indicator of a new model’s true potential. Definitely falling into the latter category is Hino’s FM2635, one of a batch of new models released a few months back at Hino’s high-hype launch of the long-awaited and vastly rejuvenated 500-series wide-cab range. From the get-go there was a lot to like about the new line-up and it was blatantly obvious Hino had done its homework well. Very well! And to be blunt, it needed to. Hino for many years now has struggled to maintain sales momentum in key market segments, allowing industry leader Isuzu to keep its principal protagonist at a giant arm’s length and in the process, notch a record of market domination unlikely to be ever equalled, let alone bettered. Meantime, and for reasons rooted in Japan rather than Australia, Hino has been unable to offer the model diversity which sees Isuzu effectively offering something for everyone in the Australian market. Simply put, Hino needed something new, and something good, if it was to have any hope of reining in the market leader’s momentum, most notably in the medium-duty and lighter end of the heavy-duty classes. That something arrived in a substantially reworked 500-series wide-cab range equipped with a swathe of new and highly functional features. Most notable among many notables are significantly enhanced eight and nine litre engines, expanded manual and automatic transmission options, numerous drivetrain developments, and safety advances headed by the standard fitment of a Wabco vehicle stability control (VSC) system in all models. Obviously relieved to finally have these long overdue newcomers in the stable, Hino Motor Sales Australia chairman and chief executive officer Steve Lotter excitedly remarked, "These trucks are a game-changer for us," and took every opportunity to remind anyone in earshot that Hino could now, "… engage in different applications which previously hasn’t been possible." To recap the broad details, the trucks cover two and three-axle configurations with gross vehicle mass (GVM) ranging from 16 to 18 and 26 tonnes, and gross combination mass (GCM) ratings from 32 to 45 tonnes. They’re easily distinguished from the previous wide cab range and from their narrower ‘standard cab’ siblings by a bold, dark grille and less obviously by relatively subtle changes in areas such as cab steps. On the inside, the changes are less apparent but nonetheless noteworthy with a new radio and information system, and redesigned digital dash being the most obvious. However, as we reported some months back, it’s underneath where the greatest changes have been made, led by further development of Hino’s 7.7 litre J08E engine and its 8.9 litre stablemate, the A09C. Critically, says Hino, both engines benefit greatly from the adoption of an SCR emissions system to achieve Euro 5 emissions compliance, replacing the previous EGR and diesel particulate filter combination. Obviously enough, it’s the bigger of these two six cylinder displacements which punches the two top-weight 6x4 models, the FM2632 auto and the FM2635 manual. Equipped with a new turbocharger, revised water pump and cooling fan, and a swap from Bosch to Denso common-rail fuel injection, the A09C offers two performance ratings starting with a 235 kW (320 hp) and 1275 Nm (940 lb ft) setting coupled to an Allison automatic transmission. The top toiler is a lively 257 kW (350 hp) rating supported by a potent 1422 Nm (1049 lb ft) of torque stirring through a Hino nine-speed overdrive synchromesh transmission. As is the way of new model launches these days, technical presentations were followed by short stints behind the wheel of various models in everything from suburban crawls to fast freeways. Typically though, these drive programs are little more than a snapshot of each model’s potential and occasionally, some trucks leave you wanting more time at the helm to verify whether it’s really as good as first impressions suggest. Such a truck was the FM2635. Good Spec Again, Hino appears to have done its development work well in tailoring the new range to specific market segments and nowhere is this more evident than in the two tandem-drive FM models. While both share a GVM of 26 tonnes, the FM2632 is logically targeted at metro applications where the Allison automatic is right at home in stop/start suburban slogs. Its bigger brother can obviously cope with the same work but with a nine-speed overdrive manual box working behind a more potent version of the same engine, the FM2635 is a model more suited to longer regional runs than ‘round-town rambles. Of course, the long-term durability of manual synchromesh transmissions is not a particularly positive feature for some fleet operators but in Hino’s favour, theirs is at least a shifter designed to cope with the outrageously heavy rigid loads and harsh conditions of some Asian countries. It’s worth noting, too, that the ’35 comes with a substantially higher GCM rating of 45 tonnes compared to the 2632’s 36.5 tonnes. Anyway, Hino’s offer to take the FM2635 for another run was grabbed with both hands for the simple reason that the only stint behind the wheel of this model on the launch drive program was extremely brief and on a part of the route with few challenges for such a well-endowed workhorse. A longer, tougher run was called for and fortunately, you don’t have to travel too far from Hino headquarters on Sydney’s southern rim to find a good mix of suburban streets, fast freeways, long pulls and sharp descents. Indeed, the run down to industrial Wollongong comes with a couple of classics – the deep drop down Bulli Pass and the long slog up Mt Ousley. But first, a few details: Built on the model’s longest ‘XXLong’ wheelbase of 6.4 metres and fitted with a 14-pallet Alltruck curtain-sided body, the test truck had almost 4500 km on the clock and loaded with around nine tonnes of bulk bags of sand, weighed in a tad over 19 tonnes. Sure, a few more tonnes would’ve been preferred for a more demanding assessment but given the varying loads of most distribution trucks, 19 tonnes was probably close to a realistic weight anyway. Besides, as the truck’s lively performance would quickly suggest, another two or three tonnes probably wouldn’t have made much difference at all. The standard driveline spec of the demo model had the nine-speed shifter feeding into a typically solid Hino drive tandem running a 4.875:1 diff ratio, mounted on Hendrickson’s all-purpose HAS 400 airbag assembly with electronic height control as a standard item. Other wheelbase lengths are 4.1 and 5.2 metres but only the 5.2 and 6.4 metre versions come with a standard 390 litre aluminium fuel tank. The shorter sibling gets a 200 litre steel tank. As the freeway section of the run down to Wollongong would show, it’s a spec which notches 80 km/h around 1400 rpm and according to the truck’s tacho, 100 km/h at 1750 rpm. On the contrary, Hino’s spec sheet says 100 km/h is at 1850 rpm. Whatever! It is, however, a specification that goes way beyond driveline details. Apart from the standard inclusion of a vehicle stability control system, the FM models also come standard with cruise control, an engine brake rather than the usual exhaust brake, reversing camera, driver’s airbag, heated and electronically operated mirrors, cross diff locks and polished aluminium wheels. Meanwhile, the manual FM2635 is also equipped with the fuel-saving attribute of an engine stop/start system and best of all in this mind’s opinion, a hill-hold function which Hino calls ‘Easy Start Take-off Assist’. Making hill starts gentle on both driver and driveline, particularly with a hefty load on board, hill-hold is arguably one of the most practical innovations in modern truck technology; an opinion further verified by a smooth, stress-free lift-off at a notoriously awkward set of traffic lights in Sydney’s southern suburbs. The generous package of standard items is partnered by an options list which among other things includes a GPS sat/nav system, ‘Hino Traq’ telematics and a smartly styled and relatively unobtrusive bullbar available in two heights – with either one or two horizontal bars – and designed specifically for the new 500-series. The bullbar is, of course, compliant with the standard FUPS under-run bar. Yet other than the restyled grille, the cab structure of the new range has changed little. The FM, for example, retains a reasonably tall floor height but well-placed steps and grab handles make it a simple climb to an Isri suspension seat. With a plethora of adjustments on the seat and a steering wheel adjustable for rake and reach, finding the right driving position is both quick and easy. Behind the seats is a space capable of nursing 40 winks but it’d certainly be a stretch to refer to it as anything more than a parcel shelf. The redesigned dash comes with the standard speedo and tacho surrounded by LCD gauges for air pressure, fuel and AdBlue, engine temperature and odometer. There’s also a digital multi-information display showing current and trip fuel figures along with service reminders and fault warnings. Main switches and control wands are generally well placed but typically, familiarisation with the placement of all functions takes a little time. Road Work In practice though, it takes next to no time to be completely at ease with Hino’s top-shelf six-wheeler. For starters, all-round vision is predictably good but it’s in actual operation where the truck really stands out. The cable-operated gearlever, for instance, is ideally placed and provides reasonably light, smooth movements through the double-H (H-over-H) shift pattern, though the ‘beep’ accompanying every range-change can be a tad annoying. According to Hino, the beep is all about protecting the engine from over-speeding if there’s an accidental shift into low range, just as an electronic control unit won’t allow shifts into low range if road speed is above 30 km/h. There’s no question though that the nine-speed shifter is a highlight of the FM2635 because not only is it a sweet shift, the ratio spread from a deep first gear of more than 10:1 to a tall overdrive ratio of 0.724:1 (and importantly, a deep reverse ratio of almost 9.9:1) provides the model with a gear spread for a multitude of conditions. But as the first 10 kilometres or so of the test run in suburban traffic demonstrated, the combination of an engine with generous torque and a transmission with even steps through the ratio range allows for plenty of smooth, shudder-free skip-shifts. It was not, for instance, uncommon to lift off in 2nd gear, jump to 4th, then straight into high range. Or, with the truck pointing down even a slight grade, take off in 3rd, push engine speed out to around 1800 or 1900 revs, then swap straight into high range. Easy! The end result is a truck that gets up to speed quickly and with very little apparent effort. At the other end of the spectrum is an impressively effective and quiet engine brake that made the long, sharp drop down Bulli Pass an absolute dawdle, easily holding to the signposted truck limit of 20 km/h in 3rd gear. In fact, the only time the service brakes were applied, albeit briefly, was after a swap up to 4th gear just to see how the engine brake would cope with the taller cog. For the most part it held the truck well but on the steepest sections, 3rd was ideal. Either way, the engine brake is a far more effective retarder than the exhaust brake normally found in Japanese trucks of this size. Meandering through Wollongong’s northern suburbs, the digital readout was showing a fuel figure of 2.8 km/litre (7.9 mpg) for the run south. Ahead lay the long climb up Mt Ousley and after a short-lived drop down to 6th gear at 1400 rpm on the sharpest lip, the Hino literally hammered the second half of the haul in 7th gear. By any measure it was a strong, determined performance soon repeated on the long slogs leading to the freeway for the northbound run back to Hino headquarters. Fuel consumption on the return leg from the base of Mt Ousley to Hino headquarters was fractionally better at 2.9 km/litre, or 8.2 mpg in the old measure. At the end of the day, the only conclusion was that this re-run in Hino’s FM2635 simply verified first impressions of an exceptional contender for six-wheeler rigid work, especially in regional roles. No question, it’s a tough and congested market but with surprisingly tenacious pulling power, smooth ride quality, good steering and road manners, and a generous standard specification, Hino is now better placed in this category than any time in its Australian history. It’ll be more than a tad interesting to watch over the remainder of this year and beyond if the broader market finds not only this model but the full range of Hino 500-series wide-cab trucks as impressive and perhaps surprising as some of us already have. Maybe, just maybe, Hino could even surprise itself. .
-
Bob Riley, Big Rigs / August 1, 2017 Ricky Blinco's trucks have been a common sight running through Outback Queensland and into the Territory for what seems like, well, forever. Based in the Darling Downs town of Oakey, the Blinco yard is a stop-off point for many independent operators heading north. Ricky Blinco is an old-school operator making it in a modern world with a huge reserve of knowledge and experience that the suits in bigger fleets with their degrees in business management can only dream about. Big Rigs caught up with Ricky mid-morning after the early rush of getting trucks on the road, loads organised and co-ordinating his fleet of road trains. Time to wander over to the house that adjoins the yard to put on the kettle, fry up a few eggs and some bacon, and to sit and have a chat. Turns out it's a 'morning ritual'. The mobile phone rings. It's one of the drivers in one of the local trucks. He's in Brisbane chasing pick-ups for the next loads going north and there's a slight snag to work out. As that issue is sorted another mobile rings. It's the tyre service saying they can't make it today. "There's 40 tyres to change," Ricky said. "But we've got a tyre machine so it's not all that bad," he says with a wide smile. "I've got two phones. If the first one is busy the call diverts to the second one so I get time to take the call or there's a message left. It's the only way I keep up and not miss calls." There's not a truck in the yard as they are all out earning their keep, but the calls keep coming, the problems are sorted, loads are the booked in, or delivery and drop-off times are confirmed. Ricky has been in the transport game since he was born. His dad, Tom Blinco, ran trucks and at age 14 Ricky left school and joined in. He got his truck licence at 17 and has been driving ever since. "I'm currently running eight trucks, all Kenworths, and usually run to Mt Isa and to Darwin," Ricky said. "Ricky Blinco Transport is well-known for running to Mt Isa and Darwin. It's what we do." There are five trucks on the long haul and they are either 600hp Cat or 600hp Cummins powered. All five are road train rated to 130 tonnes. To make it all work there's 38 trailers in the fleet plus there's 15 dollies too. The Mt Isa truck heads out on Mondays with two loaded trailers and at Roma hooks up the third and heads west. The third trailer has been dropped out there by one of the local trucks during the previous night so it's back in the yard and ready to head out on pick-ups and deliveries the next morning. The Darwin trucks head out on Friday nights and will get into Darwin sometime on Tuesday. "We run everywhere on log book hours these days," Ricky said. "It's easier on everyone and on the trucks. We've got one of the Kenworths out there with over two million kilometres on the clock, and a couple of others with well over a million or close to it. We are running anywhere between 200,000 and 250,000km a year on each of the long haul trucks." Work is not limited just to Darwin either as Ricky cites loads into and out of the mines in north west Western Australia earlier in the year. "Of three of the trucks coming back from Darwin this week one is heading into Rockhampton, another into Townsville and the third into Ipswich. If the loading's right, we'll take the work." While the trucks are away there's still lots to do. There's a mechanic on deck who comes in when there's work on repairs and maintenance and there's a boilermaker who has been busy in the workshop this year fabricating road train dollies. "I'm not a big fan of airbags. Although a couple of the trucks have them, most of them run on six-rod and the trailers and dollies run on springs. I'm getting a better run from the six-rods and the spring set-ups, than I get from the airbags," Ricky said. Compliance certification for the dollies is held in-house and is administered by Robyn Manktelow, Ricky's sister, who also manages the office. "Lunch is always in the meal room when the trucks are in the yard and most of the drivers and staff are here. It's become a bit of a tradition," Ricky said. It also says heaps for the respect and regard the boss holds for his staff too. Ricky Blinco Transport is a small operation in some respects but it's big on the value the company holds for all its staff. Many of the drivers have been with the company for close to a decade, several for well over a decade. Some have left for a time but have come back for even longer stints the second time around. One of Ricky's sons, Damon, work for him too, a real family affair on the long road to the north. .
-
Driving McPhersons Interstate Transport's Kenworth T610 SAR Peter Schlenk, Owner-Driver / August 1, 2017 Brian Barnik was offered a job as the regular driver of a new Kenworth T610 SAR and jumped at the opportunity McPhersons Interstate Transport, based at Myrtleford in Victoria’s high country, was one of the first to purchase a Kenworth T610 SAR, with driver Brian Barnik being the lucky recipient. Brian jumped out of a Transtar to drive the 610 and really noticed the difference with the modern Kenworth. "This engine feels like you are in a plane taking off and it has a nice note to it as well," Brian smiles. "I could really get used to driving this." The SAR is kept busy doing Carter Holt Harvey work, carrying timber to the mainland capitals of Sydney, Adelaide, Brisbane and Melbourne. "No-one knows what it is," Brian says of the new Kenworth. "It doesn’t have many badges, just one Kenworth badge on the grille. The T610 SAR looks the goods in McPherson Interstate Transport’s colours and Brian takes a lot of pride in it, just as he does with his own Kenworth. "I’ve got a 1978 Kenworth with an 8V92 Detroit in it and am restoring it slowly. It was originally a Goulburn based truck and is a very original old girl." Brian is a Kenworth man through and through. He even has a Kenworth tattoo to back it up. "The X15 Euro V Cummins sounds great and pulls very well. Alan [McPherson] has specced it up very heavily with the intention of doing some float work later." Brian has been in and around trucks for decades. Although his parents weren’t involved in the transport industry, they were friends of the Rouse family, leading him to start work John Rouse Transport yard before he even left school. There he would help wash and grease the trucks. Back then John Rouse Transport had three trucks in its fleet, but now John’s son Kurt runs over a dozen. It led to led Brian doing 15 years as a mechanic and 17 years driving. "I just loved trucks. It’s a disease," he exclaims. "Once you are into them, you can’t get out of them." By the time Brian was 19, he was looking for a change of scenery and headed for Queensland, landing a job working on Peterbilts. "I enjoyed doing that. Peterbilts are a different class of truck but I got the itch to drive and started with Richers Transport in Maryborough. "That was my first interstate job, running down to Sydney in a Mack Vision. That was my first banger and was followed by an Iveco Powerstar. I thought that was flash." Brian's wife Melissa doesn’t have a truck licence, but enjoys going along for the ride, especially in the new Kenworth T610 SAR. "She came with me to Sydney last week," Brian continues. "And there is plenty of room in the T610." .
-
UD Trucks launches new medium-duty Condor truck
kscarbel2 replied to kscarbel2's topic in Trucking News
The Croner*, a new heavy-medium model introduced in January, is a real UD with their latest GH5E 4-cylinder and GH8E 6-cylinder engines, and available in 10.4, 11, 12, 14, 15, 16 and 17 metric ton GVW ratings. The just-released all-new Condor (a long-time series), arguably more attractive than the Croner with its Quester-like front grille, is a rebadged Isuzu available in 7.5, 8, 11 and 14.5 metric ton GVW ratings. * https://www.udtrucks.com/en-int/trucks/croner/mke https://www.udtrucks.com/en-int/trucks/croner/lke https://www.udtrucks.com/en-int/trucks/croner/pke On another note, it remains a mystery to Mack brand dealers why Volvo doesn't offer the 220 to 330 horsepower Volvo D8 (rebadged UD GH8E) in the Granite MHD so they might attempt to be competitive once more in the municipal segment. Another mystery is why Volvo Group doesn't provide Mack brand dealers with a medium duty range, UD Croner and Condor, Renault D and D Wide, and/or Volvo FL. -
UD Trucks Press Release / July 28, 2017 UD Trucks launched the new medium-duty Condor truck that complies with Japan’s 2016 exhaust gas regulations. Ageo, Japan – 28 July, 2017- UD Trucks’ new medium-duty truck “Condor” is a good business partner for customers that allows them to feel a complete sense of security and tackle logistical challenges. The Condor is equipped with fuel efficiency, safety features, and drivability, which are fundamental ingredients for medium-duty trucks. In addition, UD Trucks’ comprehensive support services will realize efficient logistics in an even better way. The new “Condor” offers a greater variety of engine power, cabin types, and drive train systems than existing models. By adopting automated manual transmission as a new option, Condor comes with a wide range of models that meet the business needs of customers. The front grilles employ the hexagon grille, which is UD’s basic motif, displaying that the new Condor belongs to the UD family. Features of the new Condor Fuel efficiency: The lightweight, compact “4HK1” engine realizes high performance and will significantly contribute to a reduction of customers’ transportation costs. The engine delivers environmental performance and further improves loading and fuel efficiency by adopting Eco Stop (idling stop-and-start system), which is effective in reducing wasteful fuel consumption and exhaust gas, the ECONO mode that prevents vehicles from excessively accelerating through automatic control of the engine speed and fuel injection, as well as an advanced turbo system and fuel injection system. All Condor trucks with GVW ranging from 8 to 14.5 tons and the 4X2 axle configuration, equipped with Eco Stop (idling stop-and-start system), achieve +10% over the 2015 fuel economy standards for heavy vehicles in Japan. *Functions installed differ depending on the model Safety performance: The new Condor adopts advanced safety technology, which can firmly support customers’ safe day-to-day running. Condor’s safety performance is strengthened from three viewpoints: proactively detect danger to support drivers, support safe daily running, and minimize damage drivers suffer. Detecting danger is ensured by combining multiple advanced systems such as the pre-crash brake capable of double detection with a millimeter-wave radar and camera, the lane departure warning system, and the millimeter-wave inter-vehicle warning system. Furthermore, Condor’s safety performance helps reduce drivers’ fatigue and contributes to the day-to-day safe operation of vehicles. *Functions installed differ depending on the model Drivability: In addition to the reliable manual transmission, automatic manual transmission (AMT) options, capable of operating the transmission only with a shift lever, without a clutch pedal, are available for all models. The ECONO mode that enables automatic gear shifting provides all drivers with comfortable drivability and fuel efficient driving. Condor’s large cabin’s interior excels in operability and visibility and has plenty of storage space such as a center console box. Drivers will be offered a comfortable and efficient environment not only while driving but also working in the cabin. The new Condor pursues efficient maintenance as well. By providing authentic, fulfilling aftermarket services, UD Trucks ensures that customers’ trucks run and remain in optimum condition, maximizing its uptime. * The Condor is sourced from Isuzu Motors Limited as OEM product. MK and LK specs - https://www.udtrucks.com/en-int/trucks/condor/new-mk-lk PK specs - - https://www.udtrucks.com/en-int/trucks/condor/new-pk .
-
The R-model based MC was reasonably comfortable. But with MC sales never meeting expectations, we discontinued it to focus on the strong selling vocational MR. But the USPS wanted us to continue bidding a low-cab-forward tractor, so we down-spec'd the MR to create a tractor. With a heavier DM-like deep frame, It had a rougher ride. As I recall, Mack President Henry Nave promoted the idea for the MC/MR, based on his positive impression of Crane Carrier's similar Centurion. The Centurion was launched in 1974, the MC/MR in 1978. And I always believed there was some communication between Nave and Curcio, the latter who briefly left Mack (than heading the Canadian Hayes subsidiary) to work for Crane Carrier from July 1973 to March 1976. And of course Henry Nave had previously been President and Chairman of White where the low-cab-forward "1500 Compact" and "6000 Xpeditor" had been strong products. Though Crane Carrier's Centurion never achieved high volume sales, it was the catalyst for a new generation of purpose-design refuse trucks. Speaking on this subject makes me recall the MB series 6x4 tractors we sold to the U.S. Navy for warehouse to commissary delivery. People tend to forget the MB, but it was an extremely crucial product for Mack Trucks within our line-up during the 1960s and 1970s, and we sold thousands. I never met an Overnite or APA driver who complained, and their accountants loved them. .
-
And still serving: the 1971 Leyland Contractor
kscarbel2 replied to kscarbel2's topic in Trucking News
-
-
-
So what began with me reading that Egypt is in the market for new howitzers caused me to note the tractor of course, and it looked to me like a 4-door PayStar 5000. Except I'm not aware of any having been built (Daily Diesel, one of our International experts, can correct me). .
-
-
-
Heroic Hercules Smithsonian Channel / July 31, 2017 Celebrate the Lockheed Martin C-130 Hercules in times of war and peace as we revisit her history of daring efforts and detail how she continues to serve 70 countries on multiple missions. Video - https://www.youtube.com/watch?v=cu-fjeyIWCM
-
Heavy Goods Vehicle UK / July 31, 2017 Suttle Transport Services Ltd, based in Tockwith, Wetherby has purchased three lifting, sliding-roof Krone Profi Liner curtainsiders to cope with their specialist, high-cube loads. The company operates throughout the UK, Holland, Germany and Belgium and carries a wide range of high-volume cargo, including packaging materials, horticultural products and equipment for the events industry. “We specified Krone Profi Liners with lifting and sliding roofs” says Managing Director, Alan Suttle, “to give us the loading flexibility required for over-sized and mixed freight. Trees for example or stage equipment can be loaded through the top and then literally wrapped, as the roof is lowered to the appropriate running height.” For domestic use the trailers run at a height of 4112 mm and by using the hydraulic-roof ratchet system, the roof can be lowered in 50mm stages by up to 150mm – to comply with the continental 4m height restriction. When loading, the roof can be raised by up to 500mm, which allows an impressive 3060mm height through the sides and rear. After loading is complete, the roof is then closed and lowered to its chosen height. Moreover, the Profi Liners are fitted as standard with Krone’s award winning Multi Lock side raves. Each of which has up to 130 lashing points, to afford virtually limitless strapping options. “The loading restraint is another feature which you only find on a Krone curtainsider.” Adds Alan. “With the Krone Multi Lock system we can strap anywhere along each side rave, which makes it possible to securely load cages, pallets or whatever at any point along the trailer bed. Plus, to compliment this, the trailers come with Krone’s roof-mounted straps, which slide along the trailer length and pull down to fix onto the side raves. Again, great all-round flexibility.” Suttle Transport runs a mixed vehicle fleet, ranging from vans for same-day courier work and 18 tonne rigids, up to 44 tonne artics. .
-
Iveco delivers for plant hire firm CBL Transport Engineer / July 31, 2017 Plant hire business CBL has renewed its fleet with 11 Iveco Stralis rigids and four Daily Hi-Matic light commercials, after a seed Stralis “delivered on all fronts” during its first year in operation. The 26-tonne Stralis Hi-Street rigids have day cabs and are equipped with Andover Trailers low profile plant bodies with beavertails, and seven of them have been converted to four-axle 8x2 rigids. Delivered by dealer Hendy Van & Truck, all 11 trucks are supplied with an eight-year Iveco Elements R&M contract and financed through Iveco Capital. The 3.5-tonne Daily chassis cabs are mounted with plant bodies built by Brit-Tipp. CBL depot manager Kevin Clark says Iveco seemed “perfectly suited” for the operation, in terms of payload, driveline and manoeuvrability, adding: “This opinion was reinforced after running our first Iveco out of the Maidstone branch. “The Stralis quite literally delivered on all fronts and we received excellent feedback from our drivers.” The Stralis rigids are all powered by Cursor engines featuring Iveco’s Hi-SCR technology and the seven converted 8x2 rigids have been specified with a 420bhp Cursor 11 engine. “We asked for a powerful engine, and Hendy delivered,” says Clark. He adds that Hi-SCR is a big advantage: “It keeps unladen weight down, and means our drivers don’t need to push any buttons or make unscheduled stops to regenerate the diesel particulate filter.” CBL’s four Daily Hi-Matic chassis cabs have an eight-speed automatic gearbox and are powered by 3-litre Iveco diesel engines, producing up to 146bhp between 3,000 and 3,500 rpm, with up to 350 Nm of torque between 1,500 and 2,600 rpm. The 15 new arrivals will work across CBL’s sites in Bridgend, Bristol, Crawley, Maidstone, Newbury, Saltash and Southampton. .
-
Commercial Motor / July 31, 2017 Hendy Van and Truck has supplied 11 Iveco Stralis rigids and four Daily Hi-Matic vans to plant hire specialist CBL. The 26-tonne Stralis Hi-Street rigids feature day cabs and come with Andover Trailers low-profile plant bodies with beavertails, while seven have been converted to four-axle 8x2 rigids. The rigids are all powered by Cursor engines while the seven converted Stralis rigids were specified with a Cursor 11 engine that produces 420hp. All come with an eight-year Iveco “Elements” repair and maintenance contract and are financed through Iveco Capital. The 3.5-tonne Daily chassis cabs are mounted with plant bodies built by Brit-Tipp and also feature the eight-speed Hi-Matic automatic gearbox. CBL depot manager Kevin Clark said a seed Stralis impressed during its first year of work at the family-run company’s Maidstone branch. “We first considered the Stralis because it seemed perfectly suited for our operation - offering a healthy payload potential, strong Cursor driveline and impressive manoeuvrability - which is essential when delivering plant in particularly challenging locations,” he said. “This opinion was reinforced after running our first Iveco out of the Maidstone branch. The Stralis delivered on all fronts and we received excellent feedback from our drivers.” The new arrivals will work across CBL’s seven sites in Bridgend, Bristol, Crawley, Maidstone, Newbury, Saltash and Southampton. .
-
The Magnificent Seven is a 1960 American Western film directed by John Sturges and starring Yul Brynner, Eli Wallach, Horst Buchholz, James Coburn, Brad Dexter, Steve McQueen, Robert Vaughn, and Charles Bronson. The film is an Old West-style remake of Akira Kurosawa's 1954 Japanese film Seven Samurai. (https://en.wikipedia.org/wiki/The_Magnificent_Seven) .
-
Daimler Press Release / July 31, 2017 In Germany, there are only about 100 municipal-owned fire departments. In most parts of the country, the protection is in the hands of the volunteer fire brigades, like here in Uhingen. Reporter Sarah Luickhardt accompanied two volunteer firefighters for a day with their Mercedes-Benz Atego. .
-
British Scania Drivers Praise New Truck Generation
kscarbel2 replied to kscarbel2's topic in Trucking News
It is not my intention to cause BC Mack to feel homesick. -
Scania Group Press Release / July 31, 2017 At the Convoy in the Park truck show, in Derby, England, we caught up with three #NextGenScania drivers in the UK to see what they think of their new trucks. .
-
Kenworth Truck Co. Press Release / July 31, 2017 Edwards Moving and Rigging Can More Easily Position Equipment Between Loads with C500s SHELBYVILLE, Ky., July 31, 2017 - When loads exceeding a quarter of a million pounds need to be moved, few haulers in the United States possess the kind of equipment operated by Edwards Moving and Rigging. The Shelbyville, Kentucky-based heavy hauling and rigging company owns several unique trailers to haul 375,000-pound turbines for combined-cycle power plants that use gas and steam turbines to generate more power than a standard plant with a single gas turbine. Or a 194,000-pound demethanizer tower used to extract natural gas from raw hydrocarbon gas at refineries. Instead of using huge 12-foot-wide prime movers—which are not typically equipped to get up to highway speeds and can only be operated on roads and highways under the restrictions of state and local conditional use—Edwards Moving and Rigging relies on several Kenworth C500 trucks to haul those payloads. “The Kenworth C500 offers us the power and transmission combination that can pull our trailers fully loaded with gross combination weights up to 900,000 pounds or more, and can haul empty trailers up to highway speeds in between loads,” said Bill Watts, vice president of operations for Edwards Moving and Rigging. Recently, three of the company’s C500s were used to haul a 187-ton turbine 230 miles from the manufacturer in New York over the Adirondack and Pocono Mountains to a combined-cycle plant in Pennsylvania. A fourth C500 served as a backup unit to help move the 350-foot-long truck and trailer duo—with a gross combination weight of 900,000 pounds—on long stretches of road with steep grades through the Adirondacks and Poconos. Edwards hauled two others like it earlier this year and in 2016. Unlike larger and wider prime movers, the 8-1/2–foot wide Kenworth C500 can operate on the road without requiring a conditional use permit. “Because the C500 is an over-the-road compliant prime mover, we can position our equipment much faster. When the move is done, we can stack the trailers and use our C500s to transport them to the next jobs without having to arrange transportation for both the trucks and trailers,” he said. Edwards operates the third largest fleet of Goldhofer THP hydraulic platform trailers in the United States. With more than 200 lines of hydraulic trailers available, the company can arrange them in various configurations to achieve a variety of payload capacities. Edwards is one of only two firms in North America with a 110-ton Goldhofer Faktor 5 trailer, which has a payload capacity five times its tare weight. The Faktor 5 features a beam suspended over two sets of 20-axle hydraulic lift trailers that can be extended to a span of more than 150 feet, or to the length of nearly a football field. It can also be raised or lowered up to 5-1/2 feet. Edwards also operates Aspen A250 and A500 dual lane trailers, which allow movement of loads across a non-suspension bridge on a divided highway or interstate using both travel lanes and bridge decks. Edwards hauls several hundred loads varying in size and scope each year using a fleet of about 30 trucks. Before the company bought its first two C500s, Edwards used specialized trucks to haul the heavier loads, Watts said. While the specialized trucks had the necessary power, because of their width, they had to be hauled to the move, along with the trailers, and then picked up once the move was completed. In 2011, Edwards began buying Kenworth C500s after meeting with Duane McDaniel, branch manager of local Kenworth dealer Worldwide Equipment in Middlesboro, Kentucky, and engineers from Kenworth. Since 2014, Edwards Rigging and Moving has bought four more of the C500s. “We have found Kenworth engineers and the Worldwide Equipment staff, led by Duane, to be quite knowledgeable about the heavy haul industry,” Watts said. “They ask all the right questions to get to know the specific needs of our operations and offer expert advice in helping us choose the right specs to meet those needs.” Edwards newest C500s are equipped with 15-liter, 550-hp engines coupled with 7-speed Allison 4700RDS automatic transmissions, two-speed tandem rear axles, and tandem planetary hubs. “The C500’s automatic transmissions allow our drivers to synchronize shifting much more easily than if they were driving trucks with manual transmissions,” said over-the-road equipment manager Kyle McAfee. “That’s particularly important when we use several C500s to pull and push the load. Our drivers have greater control over the load. Since it’s not lurching forward, we can eliminate potential damage to our trailers. “Our drivers also value the quiet C500 cab; positioning of gauges, switches in the instrument panel as well as the location of the pusher, tag axle and planetary hub controls; and the cab’s overall comfort,” he added. “The support our company and drivers receive from Worldwide Equipment and the Kenworth dealer network is phenomenal.” “When it can take up to two years to plan, coordinate and obtain all of the necessary permits for a move like the gas turbine transport, it’s important that we stay on schedule. In many instances, we have to meet certain timetables outlined in our permits. So, we need to rely on our equipment and equipment dealers. Kenworth and its dealer network certainly deliver with the C500 and continued dealer support after the sale,” Watts said. .
-
A new (for all intents and purposes) left-hand drive COE available today in North America, and with a so-called pre-emissions 500 horsepower Detroit Diesel Series 60 powerplant. I've experienced these Cleveland, North Carolina-built trucks (in right-hand drive configuration) in South Africa and Australia. A truck to be respected. .
BigMackTrucks.com
BigMackTrucks.com is a support forum for antique, classic and modern Mack Trucks! The forum is owned and maintained by Watt's Truck Center, Inc. an independent, full service Mack dealer. The forums are not affiliated with Mack Trucks, Inc.
Our Vendors and Advertisers
Thank you for your support!