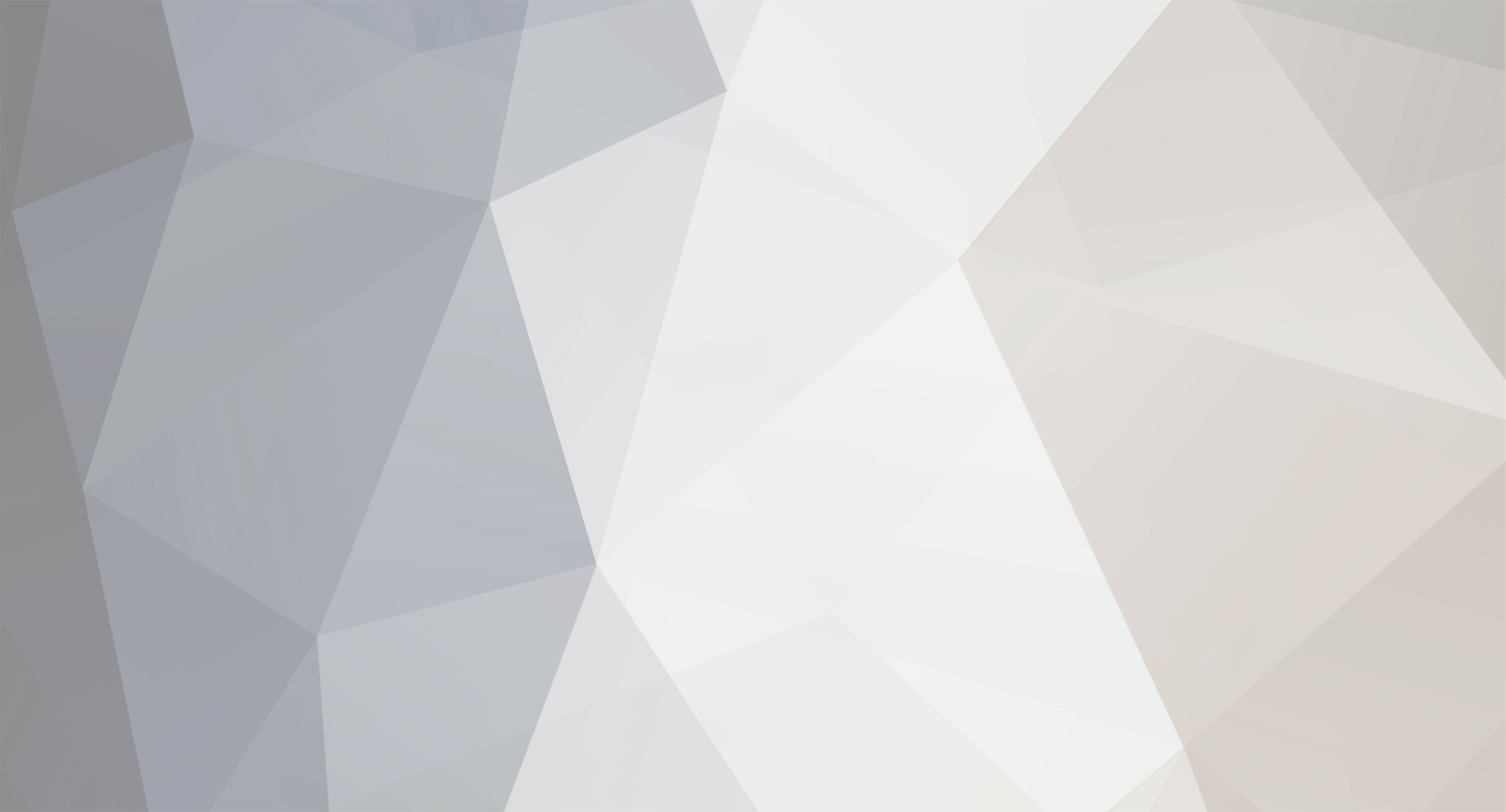
kscarbel2
Moderator-
Posts
18,743 -
Joined
-
Days Won
114
Content Type
Profiles
Forums
Gallery
Events
Blogs
BMT Wiki
Collections
Store
Everything posted by kscarbel2
-
Donald Trump: 'We will stop racing to topple foreign regimes' The Guardian / December 7, 1941 Donald Trump has laid out a US military policy that would avoid interventions in foreign conflicts and instead focus heavily on defeating the Islamic State militancy. “We will stop racing to topple foreign regimes that we know nothing about, that we shouldn’t be involved with,” the president-elect said on Tuesday night in Fayetteville, near Fort Bragg military base in North Carolina. “Instead our focus must be on defeating terrorism and destroying Isis, and we will.” Trump’s remarks came a few hours after Barack Obama delivered what was billed as the final national security address of his presidency. Speaking in Tampa, Florida, Obama did not mention Trump by name – but implicitly warned his successor to dispense with overheated rhetoric in favor of a nuanced approach to the war on terror, and to avoid actions that could give false legitimacy to Isis as the “vanguard of a new world order”. Obama told a room of service members at MacDill air force base: “Rather than offer false promises that we can eliminate terrorism by dropping more bombs or deploying more and more troops or fencing ourselves off from the rest of the world, we have to take a long view of the terrorist threat, and we have to pursue a smart strategy than can be sustained.” During the course of his campaign, Trump vowed to “bomb the shit out of” Islamic State and routinely declined to offer a counter-terrorism strategy by claiming that doing so would reveal the country’s plans before the enemy. He also suggested terrorists were streaming across the US border disguised as refugees, and proposed aggressive policies that included a ban on all Muslim immigration to the US. Trump introduced his choice for defense secretary, General James Mattis, to a large crowd in Fayetteville, near the Fort Bragg military base, which has deployed soldiers to 90 countries around the world. He vowed a strong rebuilding of the US military, which he suggested had been stretched too thin. Instead of investing in wars, he said, he would spend money to build up America’s aging roads, bridges and airports. But he also wanted to boost spending on the military. To help pay for his buildup, Trump pledged to seek congressional approval for lifting caps on defense spending that were part of “sequestration” legislation cutting spending across the board. “We don’t want to have a depleted military because we’re all over the place fighting in areas that we shouldn’t be fighting in. It’s not going to be depleted any longer,” he said. Trump said any nation that shared his goals would be considered a US partner. “We don’t forget. We want to strengthen old friendships and seek out new friendships,” he said. But the policy of “intervention and chaos” must come to an end. While US armed forces are deployed in far-flung places around the globe, they are only involved currently in active combat in the Middle East – Iraq and Syria for the most part. “We will build up our military not as an act of aggression, but as an act of prevention,” he said. “In short we seek peace through strength.” Trump used similar rhetoric during the election campaign when he railed against the war in Iraq. Unusually for a Republican, Trump not only loudly expressed his dismay at George W Bush’s 2003 intervention but falsely claimed that he opposed it at the time and accused Bush of lying about the presence of weapons of mass destruction. Trump has long expressed his skepticism about US foreign intervention in activities that he has labeled “nation building.” He told the Guardian in October 2015: “We’re nation-building. We can’t do it. We have to build our own nation. We’re nation-building, trying to tell people who have [had] dictators or worse for centuries how to run their own countries. “Assad is bad,” Trump added of the Syrian president. “Maybe these people could be worse.” In Fayetteville, Trump did not explicitly repeat his pledge to bar Muslims from coming to the US but maintained he would “suspend immigration from regions where it cannot be safely processed”. He described James Mattis as the right person for the job and urged Congress to approve a waiver to let him take on the civilian position of defense secretary. Under US law a military leader must be retired for seven years before becoming eligible for the post. Taking the microphone, Mattis said: “I look forward to being the civilian leader as long as the Congress gives me the waiver and the Senate votes to consent.” “We’re going to get you that waiver,” Trump replied, returning to the microphone. “If you don’t get that waiver there are going to be a lot of angry people.” .
-
Reuters / December 6, 2016 U.S. President-elect Donald Trump urged the government on Tuesday to cancel an order with Boeing Co for a new 747-8 Air Force One, saying costs were out of control. Trump, who takes office on Jan. 20, took aim at what he called cost overruns even though the plane is only in development stages. "Boeing is building a brand new 747 Air Force One for future presidents, but costs are out of control, more than $4 billion. Cancel order!" Trump said on Twitter. "The plane is totally out of control. I think it's ridiculous. I think Boeing is doing a little bit of a number. We want Boeing to make a lot of money but not that much money," he said. Boeing has not yet begun building the two replacements for the current Air Force One planes, which are scheduled to be in service by 2024. Boeing has not yet been awarded the money to build the proposed replacements. "We are currently under contract for $170 million to help determine the capabilities of these complex military aircraft that serve the unique requirements of the President of the United States," Boeing said. Boeing CEO Dennis Muilenburg told Trump the cost of the airplane could be lowered if the U.S. Air Force changed its requirements and the issue would likely be resolved without a major dispute. The planned 747-8 planes can fly direct from Washington to Hong Kong, 1,000 miles (1,600 km) farther than the current Air Force One. White House spokesman Josh Earnest told reporters the contracting arrangements for replacements were "rather complicated" and said the recommendations for upgrades had been made by national security experts. The budgeted costs for the replacement program are $2.87 billion for the fiscal years 2015 through 2021, just on research and development, testing and evaluation. A March 2016 report from the Government Accountability Office, the investigative arm of Congress, estimated the cost of the overall program at $3.21 billion, including the purchase of two aircraft. But the GAO estimated the costs for research and development would be lower, at just under $2 billion. If the GAO report used the same Air Force estimate for research and development, then its estimate would be around $4 billion.
-
Caterpillar’s Smart Phone Combines Ruggedness and Features
kscarbel2 replied to kscarbel2's topic in Odds and Ends
Security is paramount and, in that regard, Apple's operating system remains the best bet. Android by description is an "open" operating system. -
Kenworth Truck Co. Press Release / December 5, 2016 .
-
Freightliner introduces next-generation Cascadia
kscarbel2 replied to kscarbel2's topic in Trucking News
-
Commercial Carrier Journal (CCJ) / December 6, 2016 Daimler Trucks is recalling certain 2017 Freightliner trucks based on an earlier recall issued by Goodyear. Goodyear issued a recall Sept. 1 on some of its G399A LHS Fuel Max tires over concerns of tread separation. Goodyear said the recall was due to “a cure anomaly resulting in incomplete adhesion which could lead to partial tread separation.” This recall affected tires manufactured between Jan. 24, 2016, and May 28, 2016. Goodyear’s recall also noted some Volvo and Paccar trucks could be affected as well. The tire was also sold in the replacement market, Goodyear said. Daimler’s recall covers approximately 863 trucks that were equipped with those tires. Models include: 2017 Freightliner Cascadia, 2017 Freightliner 122SD and 2017 Freightliner Business Class M2. This recall affects certain trucks manufactured between Jan. 24, 2016, and Oct. 10, 2016. Daimler said it will notify owners, and dealers will inspect and replace affected tires free of charge. The recall is expected to begin Jan. 6, 2017.
-
James Menzies, Truck News / December 6, 2016 Refuse trucks are built to operate in all conditions, so who can complain when a little rain dampens a test drive? Or when sheets of unrelenting, driving, torrential, cold, November rain, for that matter, soak through everyone who dared step outside? The trash still has to be collected, so there were no complaints from me when I visited Mack Trucks’ Customer Center to drive the company’s newest refuse truck, the LR model. In fact, the pouring rain helped me gain an appreciation for some of the subtler design enhancements built into the LR model that would otherwise have gone unnoticed. For example, a new drip rail above the door that keeps the rain from cascading into the cockpit every time the door is opened, which could be more than 1,000 times a day. The LR model brings to refuse truck operators amenities and creature comforts that were previously unavailable in the company’s LEU model, which the LR replaces. The LR was shown for the first time at last year’s WasteExpo show in Las Vegas and Canadian customers got to see one up close at this year’s Canadian Waste & Recycling Expo. It’s a comprehensive update, especially as it relates to two key areas: driver comfort and safety. In terms of comfort, an improved HVAC system featuring 16 vents offers better temperature control and window defrosting. Interior and exterior LED lighting is now offered. A new tilting/telescoping steering column provides greater operator comfort and the gauge cluster is mounted to the steering column to provide good visibility, whatever the position. The driver display is more modern, vibrant and colorful, making it easier to find at a glance the information you’re looking for. Power windows and locks are now standard. The mirrors can memorize two positions, which is especially handy when the truck is configured for left- and right-hand driving. A simple flip of the switch positions the mirrors exactly where you want them for driving from either side. The LR I drove was set up as dual sitdown configuration – seats, steering wheel and pedals on both sides. A toggle switch allows the operator to switch between modes while the vehicle’s parking brake is activated. The gauges and controls on the selected side light up, and away you go. Mack is seeing more demand for trucks with right-hand drive capabilities, so that operators can service an entire collection route on their own, according to Curtis Dorwart, Mack’s refuse product marketing manager. “We’re seeing more and more demand for that every day,” he said. “The smaller the crew, the better the efficiency is. The key is having a flexible truck and body configuration that allows them to be as productive as possible.” The truck I drove was fitted with a Labrie Expert automated side loader body. When working the controls to pick up a blue bin, I quickly gained a new appreciation for refuse truck operators. Driving the truck is the easy part. Working the side arm controls – as intuitive and well designed as they are – is a learned skill. And I have lots of learning left to do. It’s hard to imagine operators doing as many as 1,200 pickups in a day. It took me about three minutes – okay, maybe five – to unload a single bin, meaning it would take me about 100 hours to do what some pros do in a day. In right-hand standup configured LR trucks, the operator can be in and out of the truck hundreds of times a day, so Mack has made entry and egress as easy as possible. There’s a short 16-inch step from the ground to the first step. “Our ground to floor height is the lowest in the industry among major manufacturers,” Dorwart claimed. After finally dumping the imaginary contents of a blue bin into the box, we set out for the Allentown subdivisions near the Mack Customer Center. As luck would have it, it was garbage day. With so many bins and trash cans set out for collection, I realized the width of a cul de sac and the turning radius required to navigate it is seriously compromised. Sometimes, backing is necessary, even with the LR’s impressively tight turning. This is where collection companies and municipalities get nervous – and rightfully so. I can’t think of another segment of the trucking industry in which the vehicles operate in such close proximity to citizens. It takes only a second for a kid on a bike to dart out behind a reversing trash truck. As soon as I put the LR in reverse, the ceiling-mounted monitor inside the cab switched from the view of the inside of the body to one of what was behind the truck. It was comforting to see a clear view of the area immediately behind the truck. How can you order a refuse truck without installing cameras? Another nice improvement built into the LR is the B-pillar wraparound glass on both rear corners of the cab. I glanced through these new windows frequently, especially at intersections or when changing lanes out on the highway. I took the truck for a lengthy jaunt along the highway to get a feel for its on-road handling. It’s a wide truck, which takes some getting used to, but it rode well considering it was empty. Power was more than sufficient. This truck featured the Mack MP7-345R engine, designed for this application. That engine is being replaced with a new MP7-355A, which will produce 10 additional horsepower and the same 1,280 lb.-ft. of torque. The transmission was an Allison 4500 RDS six-speed. Mack doesn’t offer its proprietary mDrive automated manual in this vehicle, because this is an application where the Allison really shines, Dorwart said. “It works very well considering the duty cycle of a refuse truck,” he said of the Allison automatic. “These operators tend to be fairly binary in their throttle position. They’re either 100% or nothing. An automated manual transmission could do that, but it’s probably going to suffer some clutch life issues and productivity may not be as good. The torque converter with the Allison works well in this application.” In addition to being a safer, more comfortable truck to operate than its predecessor, attention has also been spent on making it more user-friendly for body builders. That’s not simple, since there are so many body builders playing in this space. “It’s very important to get trucks through the body upfit process as quickly as possible,” Dorwart explained. Mack provides convenient wiring channels for upfitters and an additional wiring channel that runs up the middle of the windshield for easy installation of a camera system. Fuses are easily accessed via the top of the dash. Design improvements, such as flush lighting and corner guards, protect the most breakable items on the truck from damage. Mack announced recently that it is extending its GuardDog Connect telematics platform to the LR model. It monitors fault codes and then sends them to Mack’s OneCall service center for analysis. From there, the fleet manager is advised on the best course of action. They can even be directed to the nearest dealership with the required parts in stock. Telematics has established a devout following – and proven its worth – in the on-highway segment, but do its benefits exist even in applications where the truck returns home every night? “Uptime support is as important for our refuse customers as for our highway customers,” Dorwart said. “GuardDog Connect simplifies the diagnostic and service process and combines purposeful telematics technology with Mack experts who can keep the customer on the job.” He noted GuardDog Connect will be especially beneficial to customers who are seeing more than a single digit percentage of their total maintenance costs spent on unscheduled maintenance. “If you’re pushing more than that, a system like this can be an even greater help to you, to give you a head’s up if something is going south,” he said. It’s offered as standard, free of charge, on all new LR trucks for a period of two years. The LR brings to the refuse segment several safety enhancements and previously unavailable creature comforts that drivers in other segments take for granted. The LR is a more refined vehicle than what many trash collectors have been accustomed to. And just because the stuff you haul may stink, doesn’t mean your ride has to. .
-
Nikola Vehicles to Replace Cat Trucks for Thompson Machinery Heavy Duty Trucking / November 5, 2016 Nikola Motor’s upcoming hydrogen-electric vehicles will eventually replace the discontinued Cat Truck products for Thompson Machinery, says the Caterpillar dealer for Tennessee and Mississippi, which will handle Nikola sales and service in those states. In February of this year, Caterpillar announced its departure from the on-highway vocational truck market as part of the company's ongoing restructuring, the dealer noted. Like other Cat outlets that had invested heavily in capital assets and personnel to service the on/off-highway truck, Thompson searched for new product ideas. "Within a few months, our team had identified a new partner in Trevor Milton, the CEO of Nikola Motor Co.,” said De Thompson V, the dealer’s president and CEO. “As an entrepreneur and leader, Trevor has an unmatched passion and work ethic to create change." Thompson therefore invested in Nikola Motor, and on December 1st, when Milton unveiled his Nikola One hydrogen-electric sleeper-cab tractor, he announced that Thompson would have distribution rights in its home states. Ryder System will otherwise be the main dealer and service provider for Nikola vehicles. The Nikola range will also include daycab tractors and trucks, to include vocational vehicles. "We are excited to announce Thompson Machinery as our only other authorized sales, service and warranty dealer, along with Ryder System, Inc. Given Thompson Machinery's impeccable reputation in Tennessee and Mississippi, we were happy to have them as an early investor,” Milton said. “Thompson Machinery has committed a tremendous amount of capital on the infrastructure needed to service Class 8 trucks and we are excited to have a partner that understands the benefits of clean technology and is ready to serve Nikola drivers," he added. Thompson Machinery will also distribute Nikola Motor’s Power Sport battery-electric all-terrain vehicle, called the Nikola Zero. It has over 500 hp and 476 lb-ft of torque and is anticipated to hit Thompson Machinery's showrooms in December of 2017. The Class 8 Nikola One and Two are three years away from production, Milton has said. “Even with a change in administration and possible adjustment to EPA's transportation regulation, we think the growing acceptability and popularity of all electric cars suggest that the market wants cleaner, more environmentally friendly transportation options,” said Steve Lainhart, Thompson’s vice president of energy and transportation. "We believe the on-highway truck industry will follow suit as soon as a truck manufacturer can bring an affordable solution to the heavy haul market," he said. "We feel Nikola is going to provide that solution and remain the innovation leader in this industry, and we are very excited to be a dealer for the Nikola Motor Co." Nikola One and Two vehicles will use hydrogen fuel cells to generate electricity that's sent to advanced lithium-ion batteries, which then supply power to chassis motors. Regenerative braking captures kinetic energy that also goes to batteries. Each truck or tractor will have four or six electric motors generating as much as 1,000 hp, which will be modulated to balance propulsion needs against tire conservation, Milton explained during technical briefings that followed the unveiling. The Nikola One truck is expected to attract drivers who are interested in using its new technology, and thus reduce the problem of the ongoing driver shortage, said both companies. Other advantages include exceeding EPA standards, complying with the new brake stopping distance regulations, satisfying fuel economy needs and providing increased horsepower and torque for heavier loads and multiple trailers. .
-
Carrier union leader says Trump's big deal is a lie The Washington Post / December 6, 2016 The Secret Service agents told the Carrier workers to stay put, so Chuck Jones sat in the factory conference room for nearly three hours, waiting for president-elect Donald Trump. He'd grown used to this suspense. Seven months earlier, at a campaign rally in Indianapolis, Trump had pledged to save the plant's jobs, most of which were slated to move to Mexico. Then the businessman won the election, and the 1,350 workers whose paychecks were on the line wondered if he'd keep his promise. Jones, president of the United Steelworkers 1999, which represents Carrier employees, felt optimistic when Trump announced last week that he'd reached a deal with the factory's parent company, United Technologies, to preserve 1,100 of the Indianapolis jobs - until the union leader heard from Carrier that only 730 of the production jobs would stay and 550 of his members would lose their livelihoods, after all. At the Dec. 1 meeting, where Trump was supposed to lay out the details, Jones hoped he would explain himself. "But he got up there," Jones said Tuesday, "and, for whatever reason, lied his a-- off." In front of a crowd of about 150 supervisors, production workers and reporters, Trump praised Carrier and its parent company, United Technologies. "Now they're keeping - actually the number's over 1,100 people," he said, "which is so great." Jones wondered why the president-elect appeared to be inflating the victory. Trump and Pence, he said, could take credit for rescuing 800 of the Carrier jobs, including non-union positions. Of the nearly 1,400 workers at the Indianapolis plant, however, 350 in research and development were never scheduled to leave, Jones said. Another 80 jobs, which Trump seemed to include in his figure, were non-union clerical and supervisory positions. (A Carrier spokesperson confirmed the numbers.) And now, the president-elect was applauding Carrier and giving it millions of dollars in tax breaks, even as hundreds of Indianapolis workers prepared to be laid off. "Trump and Pence, they pulled a dog and pony show on the numbers," said Jones, who voted for Hillary Clinton but called her "the better of two evils." "I almost threw up in my mouth." Spokespeople for Trump refused to respond to the Post's request for comment. In exchange for downsizing its move south of the border, United Technologies would receive $7 million in tax credits from Indiana, to be paid in $700,000 installments each year for a decade. Carrier, meanwhile, agreed to invest $16 million in its Indiana operation. United Technologies still plans to send 700 factory jobs from Huntington, Indiana, to Monterrey, Mexico. T.J. Bray, 32, one of the workers who will keep his job, sat in the front row during the Dec. 1 meeting as Trump spoke. A corporate employee had guided him specifically to that seat, he said, so he suspected he might be part of Trump's remarks. On Carrier's makeshift stage, Trump paraphrased the words of an unnamed Carrier employee who talked to an NBC reporter after the election. Bray was the only Carrier employee who had appeared on television that day. Apparently, he realized, Trump was saying he inspired the deal. "He said something to the effect, 'No, we're not leaving, because Donald Trump promised us that we're not leaving,' and I never thought I made that promise," Trump said. "Not with Carrier. I made it for everybody else. I didn't make it really for Carrier," said Trump. In fact, Trump “did” make that commitment, and it's on video. "They're going to call me and they are going to say 'Mr. President, Carrier has decided to stay in Indiana,' " Trump had said at the April rally. "One hundred percent -- that's what is going to happen." Last week, though, the president-elect told the Carrier crowd he hadn't meant that literally. "I was talking about Carrier like all other companies from here on in," Trump said. "Because they made the decision a year and a half ago. But he believed that was - and I could understand it. I actually said - I didn't make it - when they played that, I said, 'I did make it, but I didn't mean it quite that way.'" Trump asked if the employee he'd been referencing was in the audience. A woman yelled that her son was, and Trump began to compliment that son, though he hadn't spoken in the television news segment. (Bray said that a United Technologies spokesperson later told him Trump meant to single him out.) "I was confused when he was like, 'I wasn't talking about Carrier,' " Bray said. "You made this whole campaign about Carrier, and we're still losing a lot of jobs." Bray clapped that day, anyway, for the 800 that would remain on American soil. -------------------------------------------------------------------------------------------------------------------------------- Chuck Jones, who is President of United Steelworkers 1999, has done a terrible job representing workers. No wonder companies flee country! — Donald J. Trump (@realDonaldTrump) December 8, 2016 If United Steelworkers 1999 was any good, they would have kept those jobs in Indiana. Spend more time working-less time talking. Reduce dues — Donald J. Trump (@realDonaldTrump) December 8, 2016 -------------------------------------------------------------------------------------------------------------------------------- -------------------------------------------------------------------------------------------------------------------------------- Donald Trump just insulted a union leader on Twitter. Then the phone started to ring. The Washington Post / December 7, 2016 Chuck Jones uses a flip phone, so he didn’t see the tweet. His friend of 36 years called him Wednesday night and said: The president-elect is smearing you on Twitter. Chuck Jones, who is President of United Steelworkers 1999, has done a terrible job representing workers. No wonder companies flee country! — Donald J. Trump (@realDonaldTrump) December 8, 2016 If United Steelworkers 1999 was any good, they would have kept those jobs in Indiana. Spend more time working-less time talking. Reduce dues — Donald J. Trump (@realDonaldTrump) December 8, 2016 Jones, a union leader in Indianapolis, represents the Carrier workers whose jobs Donald Trump has pledged to save. He said the sudden attention from the country’s next leader didn’t feel real. “My first thought was, ‘Well, that’s not very nice,’ ” he told The Washington Post on Wednesday night. “Then, 'Well, I might not sleep much tonight.' " Jones, president of the United Steelworkers Local 1999, told The Post on Tuesday that he believed Trump had lied to the Carrier workers last week when he visited the Indianapolis plant. On a makeshift stage in a conference room, Trump had applauded United Technologies, Carrier’s parent company, for cutting a deal with him and agreeing to keep 1,100 jobs that were slated to move to Mexico in America’s heartland. Jones said Trump got that figure wrong. Carrier, he said, had agreed to preserve 800 production jobs in Indiana. (Carrier confirmed that number.) The union leader said Trump appeared to be taking credit for rescuing 350 engineering positions that were never scheduled to leave. Five hundred and fifty of his members, he said, were still losing their jobs. And Carrier was still collecting millions of dollars in tax breaks. In return for downsizing its move south of the border, United Technologies would receive $7 million in tax credits from Indiana, to be paid in $700,000 installments each year for 10. Carrier, on top of that, has agreed to invest $16 million in its Indiana operation. United Technologies, meanwhile, still plans to relocate 700 factory jobs from Huntington, Ind., to Monterrey, Mexico. Jones, who said the union wasn't involved in the negotiations, said he's working to lift his members' spirits. He said he didn't have time to worry about Trump. “He needs to worry about getting his Cabinet filled,” he said, “and leave me the hell alone.” Over the past two decades, the United States has lost about 4.5 million manufacturing jobs. Jones said he has fought to keep work on U.S. soil, bargaining repeatedly with Carrier and Rexnord, another Indianapolis plant that plans to relocate jobs to Mexico. Vice President-elect Mike Pence tweeted his support for Jones earlier this year: Appreciate the chance to meet w/ Chuck Jones & hardworking men of Local 1999 about our efforts to save Carrier jobs pic.twitter.com/jAzV4DO4PY — Governor Mike Pence (@GovPenceIN) March 2, 2016 Half an hour after Trump tweeted about Jones on Wednesday, the union leader's phone began to ring and kept ringing, he said. One voice asked: What kind of car do you drive? Another said: We’re coming for you. He wasn’t sure how these people found his number. “Nothing that says they’re gonna kill me, but, you know, you better keep your eye on your kids,” Jones said later on MSNBC. “We know what car you drive. Things along those lines.” “I’ve been doing this job for 30 years, and I’ve heard everything from people who want to burn my house down or shoot me,” he added. “So I take it with a grain of salt and I don’t put a lot of faith in that, and I’m not concerned about it and I’m not getting anybody involved. I can deal with people that make stupid statements and move on.” Brett Voorhies, president of the Indiana State AFL-CIO, called Jones after Trump’s tweet caught his eye. Jones, he said, had just left his office in Indianapolis, where he manages the needs of about 3,000 union members. “This guy makes pennies for what he does,” Voorhies said. “What he has to put up with is just crazy. Now he’s just got the president-elect smearing him on Twitter.”
-
Caterpillar’s Smart Phone Combines Ruggedness and Features
kscarbel2 posted a topic in Odds and Ends
-
Trump, trucking, and the outlook for 2017 Sean Kilcarr, Fleet Owner / December 6, 2016 Lots of change may be on the menu for trucking in 2017 as economic trends and federal policy efforts could make further alterations to the U.S. freight market – everything from canceling regulations to the adoption of new strategies for meeting customer demands. “When you move 70% of the nation’s domestic freight there are few issues out there that we are not a part of either directly or indirectly,” Chris Spear, president and CEO of the American Trucking Associations (ATA) trade group, explained in a recent phone interview with me. “Tax reform, trade, and infrastructure: we have a role to play in all of those issues.” For starters, he noted that the 10-year $1 trillion infrastructure proposal put on the table by President-elect Trump could be a big positive for the industry in a number of ways. “Infrastructure is our industry’s lifeblood: We need good infrastructure and getting such a package passed is key right out of the gate,” Spear said. “At least as proposed, that package will likely be tied to tax reform.” Trade is another really pivotal issue in Spear’s view, as over 76% of NAFTA surface trade is carried by trucks. “Again, we have to help shape whatever trade proposals will look like,” he noted. When it comes to regulation, though, you can boil Spear’s view down to two words: “it depends.” “We’re not afraid of regulations – we’re a very heavily regulated industry. But what we want are good, clear regulations that we can comply with without undue burden and a measurable return,” he explained. “Look at the Phase 2 greenhouse gas [GHG] rules: they will define future efficiency for our industry and offer a measurable return for our investments. This is a win-win for us and the environment,” Spear said. “But where regulations don’t work, we’ll oppose them. For example, the speed limiter rule we will oppose [because] it’s completely flawed approach.” In the end, he stressed, it “all really comes down to good give and take between industry and the regulators.” Sandeep Kar, global vice president for mobility at Frost & Sullivan, added that few industries will face the impact — whether net positive or negative — of a Trump presidency as strongly as trucking, which is a leading indicator of economic activity and typically feels the effects of economic swings and fluctuations well before many other industries or sectors. “While the effect of Trump administration’s legislative actions will be experienced primarily by the U.S. commercial vehicle industry, global market participants and markets will have much to note and consider,” he noted in a recent report. “Most presidential transitions include reasonable certainties regarding upcoming policy priorities and changes that enable nations, markets, and industries to prepare for their impact,” Kar said. “Over the past several decades, proposed policy changes generally have had narrow boundaries. This time it is different, and it is going to be more different for trucking than ever before.” He added that Trump’s publicly stated stand on lowering corporate taxes will definitely have cascading effects on all aspects of U.S. and global industries. “Lower corporate taxes would likely result in businesses considering either establishing or reshoring US operations,” Kar explained. “While on the surface this would appear to be great news for the U.S. trucking industry, it may not be as great for either U.S. or global truck manufacturers and suppliers. Lower corporate taxes will most likely drive service-based businesses to the U.S., which would be of less benefit to freight movement than a move of manufacturing operations.” Another concern: Labor costs could spike as lower corporate taxes could drive inflation, resulting in wage hikes which would render the incentive of lower taxes much less effective. Moreover, Kar thinks the U.S. and many other economies are still “unstable,” with many nations skating dangerously close to “recessionary boundaries.” Thus economic and trade policy changes could induce short-term recessionary spasms before a clearer and stable picture emerges, he said. Where trade is concerned, modifications or rejections of trade treaties such as the North American Free Trade Agreement (NAFTA) or the Trans-Pacific Partnership (TPP) could adversely impact U.S. truck OEMs and their suppliers as many manufacture and/or source materials from Mexico. However, there may be a “silver lining” from that as well, Kar emphasized. “Several Asian OEMs in recent years have secured strong positions in light- and medium-duty truck markets [and] new trade policies could hurt them, forcing more U.S. localization and higher taxation for market access — both of which will favor U.S.-based OEMs,” he explained. Another positive: expedited infrastructure refurbishment and/or enhancement projects and public-private partnerships focused on improving U.S. highways and freight movement infrastructure could have a net positive impact on freight and vehicle efficiencies, route congestion, and sales of off-highway vehicles if the administration implements many such projects immediately. “[But] this could prove difficult because funding [needs] could trigger higher taxes – and Trump has stated his opposition to increase the deficit to pay for his infrastructure plans,” Kar noted. Roei Ganzarski, a former Boeing executive and now CEO of BoldIQ, which provides optimization software for asset scheduling, added another economic twist to trucking’s outlook where the economy is concerned: the rise of “demand-driven” freight transportation service. “Consumers or customers want to get what they want, at the time and place they want it, and only want to ask for it [delivery service] when they are ready to ask and not before,” he explained to me recently. “Thus the transportation operator must be ‘demand-driven’ in order to serve such on-demand needs in an efficient manner that enables scale, growth, and profitability.” That “on-demand economy” is also shortening planning cycles and significantly shortening decision making time frames. “This means the need for intelligent, data driven, and real-time decision making is critical,” especially in trucking, Ganzarski said. He added that this “demand-driven” view assumes that trucking companies and other freight service providers have finite resources to do their work. “This must be viewed differently from the so-called ‘sharing economy’ where an operation will use someone else’s resources because they are so inefficient, they have spare time or capacity on their resources,” Ganzarski pointed out. That will lead to more consolidation and even elimination of some transport companies that cannot adapt fast enough to the change, he said. I’ll tell you one thing: all of that adds up to what will no doubt be a very busy 2017 for motor carriers, on a whole range of fronts. Better load up on the coffee!
-
FlowBelow scores big order from Swift Transportation
kscarbel2 replied to kscarbel2's topic in Trucking News
FlowBelow signs up Swift Sean Kilcarr, Fleet Owner / December 6, 2016 Swift Transportation plans to begin equipping FlowBelow Aero Inc.’s Tractor AeroKit tandem axle aerodynamics package on its company trucks, with the initial deployment of the kits through 2017 expected to account for approximately 40% of the TL carrier’s company trucks. “Over the years we have refined the specs of our trucks and trailers to optimize the air flowing around the vehicle and reduce drag as much as possible,” noted Bert Kinsel, Swift’s vice president of heavy equipment procurement, in a statement. Swift maintains a fleet of more than 18,000 trucks and 60,000 trailers – operated by 16,000 company drivers and 5,000 owner-operators – along with a network of more than 40 full-service terminals across the continental U.S., Mexico, and Canada. “Many aerodynamic products for trailers exist today, and we certainly utilize those that work well for us,” he said. “But because we operate over three trailers for every one truck in the fleet, meaning that our trailers are utilized approximately one-third as much as the tractors, the return on an investment for a trailer-mounted technology can take a lot longer than a comparable technology installed on one of our trucks.” Kinsel emphasized that because FlowBelow’s system only needs to be installed on tractors, “it makes an impact on every mile we drive.” Swift first began testing FlowBelow’s Tractor AeroKit in 2014 and after completing initial SAE fuel efficiency tests against a control vehicle, it deployed 100 of those kits into its fleet for nine more months of testing before deciding to install them fleet wide. Citing multiple third party tests, FlowBelow claims the Tractor AeroKit is verified to provide up to a 2.23% fuel savings. Josh Butler, FlowBelow’s CEO, told Fleet Owner that when motor carriers the size of Swift begin installing such aerodynamic devices fleet-wide, “it’s a big deal because it represents big change in the industry.” He added that, “it’s a sign of a bigger shift. They are a very sophisticated operator that conducted significant control tests – 100 trucks for nearly a year. Not many fleets can invest in that kind of testing.” And while Swift isn’t the first fleet to adopt FlowBelow’s AeroKit, their sheer size “helps set the direction to where the industry goes” in terms of installing tractor aerodynamic devices, Butler noted. “Fleets are still going to test our product – they want to make sure the [fuel] savings are there,” he added. “But this [Swift’s adoption] is a big milestone for us.” . -
Transport Topics / December 6, 2016 Truckload carrier Swift Transportation Co. will begin deploying thousands of FlowBelow Aero Inc.'s Tractor AeroKit systems in its fleet. The initial large-scale deployment of the Tractor AeroKit through 2017 is expected to account for about 40% of Swift’s company trucks. Swift ranks No. 6 on the Transport Topics Top 100 list of the largest U.S. and Canadian for-hire carriers. The carrier operates 18,000 trucks and logs more than a billion miles per year. Swift began evaluating the technology in 2014 and deployed an initial 100 systems for nine months. “Many aerodynamic products for trailers exist today, and we certainly utilize those that work well for us," said Bert Kinsel, Swift vice president of heavy equipment procurement. "But because we operate over three trailers for every one truck in the fleet, meaning that our trailers are utilized approximately one-third as much as the tractors, the return on an investment for a trailer-mounted technology can take a lot longer than a comparable technology installed on one of our trucks." FlowBelow’s system only needs to be installed on the tractor, Kinsel said. “The best thing about it is that it makes an impact on every mile we drive.” The Tractor AeroKit reduces aerodynamic turbulence and drag around the rotating wheels of the truck, Austin, Texas-based FlowBelow said. The system includes four quick-release wheel covers as well as four fairings placed between and behind the drive wheels of the truck. The system is effective at reducing drag for trucks traveling faster than 40 mph. Lower drag means less horsepower is required to move the vehicle, which results in improved fuel efficiency. Citing multiple third-party tests, FlowBelow said its Tractor AeroKit is verified to provide up to a 2.23% fuel savings. “It is truly amazing when you consider how much fuel is consumed by trucks today,” says FlowBelow CEO Josh Butler. “A countless number of engineers and entrepreneurs are working tirelessly to bring new ideas into practice in order to improve fuel efficiency and reduce emissions from heavy vehicles." .
-
The Electronic Logging Device (ELD) Controversy
kscarbel2 replied to kscarbel2's topic in Trucking News
-
Ford stockpiles 2017 F-150 trucks to test new transmission
kscarbel2 posted a topic in Odds and Ends
Reuters / December 6, 2016 Ford is stockpiling 2017 model F-150 trucks, delaying delivery to dealers while it runs final tests on a new 10-speed transmission. The trucks should be delivered by the end of the year, Joe Hinrichs, head of Ford's automotive operations in the Americas said in an interview on Monday. "We are launching the new Raptor and F-150 with the new 10-speed transmission," Hinrichs said. “We continued building but we’re holding (trucks) longer so we could do more testing and make sure everything is right before we release them,” Hinrichs said. Extra testing is surely prudent in an industry plagued by frequent and costly automotive safety recalls. But Ford's shipping delays come as rival General Motors is aggressively trying to cut into Ford's lead in U.S. pickup sales. Taking aim at the "Built Ford Tough" ad campaign, as part of a bid dominate the lucrative light truck and sport utility vehicle market, GM rolled out a series of hard-hitting TV commercials over the summer. Punching holes, literally, in the lightweight aluminum beds featured in Ford's new line of pickups, the ads tout the alleged advantages of the roll-formed, high-strength steel beds in GM's trucks. The Ford F-series line of pickups has been the best-selling model line in the United States for 34 years, and Hinrichs predicted 2016 will make it 35 years in a row. Ford refused to say how many F-150 pickups it is holding. But several hundred vehicles were stored earlier this week behind a chain link fence on an empty factory parking lot in Detroit. More were parked on Tuesday near the Detroit-Wayne County airport. Many were well-equipped Limited or Platinum models with sticker prices above $50,000. Ford designed the 10-speed transmission jointly with GM. The 2017 model F-150s equipped with a 3.5 liter six-cylinder engine and the 10-speed automatic gearbox get a one mile per gallon improvement in fuel economy over comparable 2016 models with six-speed transmissions. Ford remains the leader in large, light duty pickups with 733,287 F-series trucks sold on the U.S. market through the end of November. However, Ford in October said it would cut a week of production at a Kansas City assembly plant that builds F-150s. GM has sold 718,994 of its large pickups during the same 11 months. GM said in November it had increased inventory on U.S. dealer lots by 111,000 vehicles at the end of the third quarter. GM, Ford and other major automakers in the United States are promoting holiday-themed discounts and financing deals to clear out inventory by the end of the year. December is a critical month for truck sales, said Pete DeLongchamps, vice president of manufacturer relations with Group 1 Automotive, a Houston auto retail chain. "I expect them to be aggressive." -
Bob, no-nonsense Dwight D. Eisenhower aside, politicians have long acted as though they are specially gifted, that only they can manage/steer the country. They say the common people can’t see/understand the “big picture”, and shoe them aside, while they serve the will of big business and special interest. Here’s an excerpt from one of my favorite movies: .
-
Volvo Trucks - 5 things that make I-Shift Dual Clutch outstanding
kscarbel2 replied to kscarbel2's topic in Trucking News
Bob, I "know" that I posted news on the I-Shift Dual-Clutch, but I can't located the link. To date, sales remain very low, and to my knowledge are only in Western Europe where Volvo can monitor them closely. Here's some info: . . ---------------------------------------------------------------------------------------------------------------------- Volvo I-Shift Dual Clutch: Smooth Operator Heavy Duty Trucking / December 2014 Volvo Truck claims to be first in the world to launch a dual-clutch automated mechanical transmission in heavy trucks, and to this reporter’s knowledge, that is correct. Deliveries of the [12-speed] I-Shift Dual Clutch started in Europe this fall. There's no official word yet if they will be available in the U.S., but it's seen as likely by many in the industry. As a concept, dual clutch transmissions appeared in the 1980s in auto rallying and racing. Some European cars now offer them, and Eaton recently introduced a dual-clutch transmission for medium-duty trucks. The current I-Shift automated manual, with a single clutch, goes back to 2002 in Europe and 2005 in the U.S. About 95% of Volvo's sales of heavy trucks in Europe last year included the I-Shift, and in the U.S. it's now in 74% of Volvo heavy trucks. The two Volvo I-Shifts are similar mechanically, but to the driver they operate much differently. I-Shift Dual Clutch can basically be described as two parallel connected gearboxes in one housing. One gearbox contains the even gears and the other has the uneven gears. When one gear is active, the next gear is pre-selected in the second unit. When shifting changes from the first gearbox, the other is poked in. This provides ratio changing without any disruption in power or speed. The I-Shift Dual Clutch has two input shafts, one located inside the other, and the two clutches. This allows two gears to be engaged simultaneously. Which of the gears that is activated is determined by which clutch is engaged. Volvo’s I-Shift Dual Clutch weighs 222 pounds more and is 4.72 inches longer than the single-clutch I-Shift. Demanding driving Volvo showed the I-Shift Dual Clutch to the European press corps recently in south-coastal Spain. We drove almost 300 kilometers (about 180 miles) using 12 vehicles. All were typical European 4x2 tractors with three-axle semi-trailers, loaded to 40 metric tons or 90,000 pounds GCW. Some were equipped with Dual Clutch I-Shifts, while others had the regular single-clutch I-Shift. The reason for choosing this part of Europe was the demanding, long and steep ascents and descents of up to 7 and 8 percent. One 65-kilometer (40-mile) leg started at sea level, rising to 916 meters (2,005 feet). I became especially fond of a FH13-liter with 500-hp engine and 2500 Nm (1844 lb-ft) of torque equipped with the Dual Clutch. It took off almost like a bullet and changed gears fast and without any interruptions. One could only hear, not feel, most gear changes. Like a regular I-Shift, the new transmission skips some gears whenever possible, and makes only one small pause, during a range shift between 6th and 7th gear. Gear changes were made at low rpms, but revs did not drop during gear shifting. Low engine speed gave an extra comfortable setting in an already quiet cab. Volvo says fuel consumption does not exceed a "normal" I-Shift. In the long and steep downhills, the transmission shifted down more quickly and more often than otherwise, due to the activated engine brake and retarder. This is controlled by the cruise control, where the desired maximum speed is set. The Volvo cruise control switches are on the left side on the steering wheel, and prompting slower or faster set speeds is done with a superb thumb switch. It is amazing how quickly one can lose previous frames of reference. After time in a truck with an I-Shift Dual Clutch, an otherwise distinguished and popular long-haul FH 13 with a 460-hp engine and a single-clutch I-Shift felt far weaker with its slower gear changes. . -
Oh, I do too. No doubt about it. But if we do a recount, and any decent system should be easily capable of a recount in a short period of time, then there's added validation of the original result.........or, in fact an issue is revealed that should indeed be brought to light.
-
I haven't read anyone (of stature) saying Trump is destroying free markets. We all know NAFTA was a scam, crafted by big business to enhance their profitability. I hope Trump terminates our participation in NAFTA, or completely rewrites it. I don't care about lawless Mexico.......I'm on the U.S. team.
-
The way I see it Paul, if the original count was correct, and there's nothing to hide, who could possibly argue with counting one more time to make double sure (reconfirm)? It never hurts to count twice, especially when it's important and/or expensive.
-
You're right, you certainly can't learn what's going on by just skimming headlines. You have to actually read the article. That one wasn't too long, just 18 sentences. "My" news? No. I didn't write it. The folks at the Pulitzer Prize-winning Guardian wrote it. I didn't notice any bias. Just laying out the facts/situation.
-
David, based on the news (what we're told), of the 2,100 Carrier jobs that were being shifted to Mexico, 1,100 are still heading south of the border. A genuine success story, a true demonstration of skill, would have been all 2,100 jobs remaining in the US. China was a significant currency manipulator. But global (western) economist all claim that is no longer the case. Every country, including the US, pushes buttons and pulls levers to manipulate their currency to a degree. Our “Quantitative Easing” scheme, for example, kept the value of the dollar lower than it might otherwise be. It's going to be fun watching Trump jerk on everyone's chain ("rocking the boat"). Hopefully, some good will come of it. That said, Trump is flip-flopping on his campaign promises faster than a PEZ dispenser can shoot out candy.
-
Remembering Pearl Harbor - December 7, 1941
kscarbel2 replied to mrsmackpaul's topic in Odds and Ends
And Paul, we couldn't have done it without the help of Australia and New Zealand. Some of the best troops in the Pacific theater of war. Thank you. -
Remembering Pearl Harbor - December 7, 1941
kscarbel2 replied to mrsmackpaul's topic in Odds and Ends
Shinzo Abe to visit Pearl Harbor in symbol of reconciliation The Financial Times / December 5, 2016 Prime minister’s visit is first by Japanese leader since attack 75 years ago Shinzo Abe will make a historic visit to Pearl Harbor later this month where he will remember the dead of World War Two alongside outgoing US president Barack Obama. The visit will make Mr Abe the first sitting Japanese prime minister to visit Pearl Harbor since his country’s surprise attack on the Hawaiian port began the Pacific war 75 years ago. Following Mr Obama’s visit to the atomic bombing site of Hiroshima earlier this year, it will break down one of the last remaining taboos between the US and Japan, symbolising the reconciliation between former enemies who have become close allies. The visit will also provide a powerful closing scene for Mr Obama’s foreign policy before the inauguration of Donald Trump, highlighting the value of patient diplomacy, and letting him take one last step in his “pivot to Asia”. Mr Abe will visit Hawaii on December 26 and 27 and hold a summit with Mr Obama. “On this occasion, along with President Obama, I will visit Pearl Harbor,” Mr Abe told reporters at his official residence in Tokyo. “The purpose is to comfort the spirits of the dead.” He said the visit would show their determination never to repeat the calamity of war. “It will be a chance to show the world the significance of our effort to look to the future and build an even stronger US-Japan alliance,” said Mr Abe. “This final summit is the culmination of all we have done.” A statement from the White House echoed Mr Abe’s comments, saying: “The two leaders’ visit will showcase the power of reconciliation that has turned former adversaries into the closest of allies, united by common interests and shared values.” The visit marks another step in Mr Abe’s effort to reconcile his own conservative nationalism — which has occasionally veered into historical revisionism — with his desire to strengthen the US-Japan alliance and settle the ghosts of Japan’s history. Last year, he referred to Pearl Harbor in a well-received speech to the US Congress, and gave a statement on the 70th anniversary of the war’s end without offending Japan’s neighbours. Mr Abe has landed on a formula where he often talks of his grief and sadness at the events of the war without offering specific apologies. Although Mr Abe declined to pledge a Pearl Harbor trip when Mr Obama went to Hiroshima in May, a reciprocal visit was widely anticipated and has been discussed with US diplomats in the past. The prime minister said Mr Obama’s words at Hiroshima had “entered the hearts of many Japanese people”. Akie Abe, the prime minister’s wife, visited Pearl Harbor in August where she prayed at laid flowers at the USS Arizona memorial. That was widely regarded as a test run for a prime ministerial visit. Japan’s surprise attack on Pearl Harbor using carrier-born aircraft sunk four US battleships and damaged four others. Coming without a declaration of war, it prompted US president Franklin D Roosevelt to declare December 7, 1941, “a date which will live in infamy”. But America’s three aircraft carriers were out at sea during the attack and survived, so Japan gained little strategic advantage, leading to its ultimate defeat three-and-a-half years later.
BigMackTrucks.com
BigMackTrucks.com is a support forum for antique, classic and modern Mack Trucks! The forum is owned and maintained by Watt's Truck Center, Inc. an independent, full service Mack dealer. The forums are not affiliated with Mack Trucks, Inc.
Our Vendors and Advertisers
Thank you for your support!