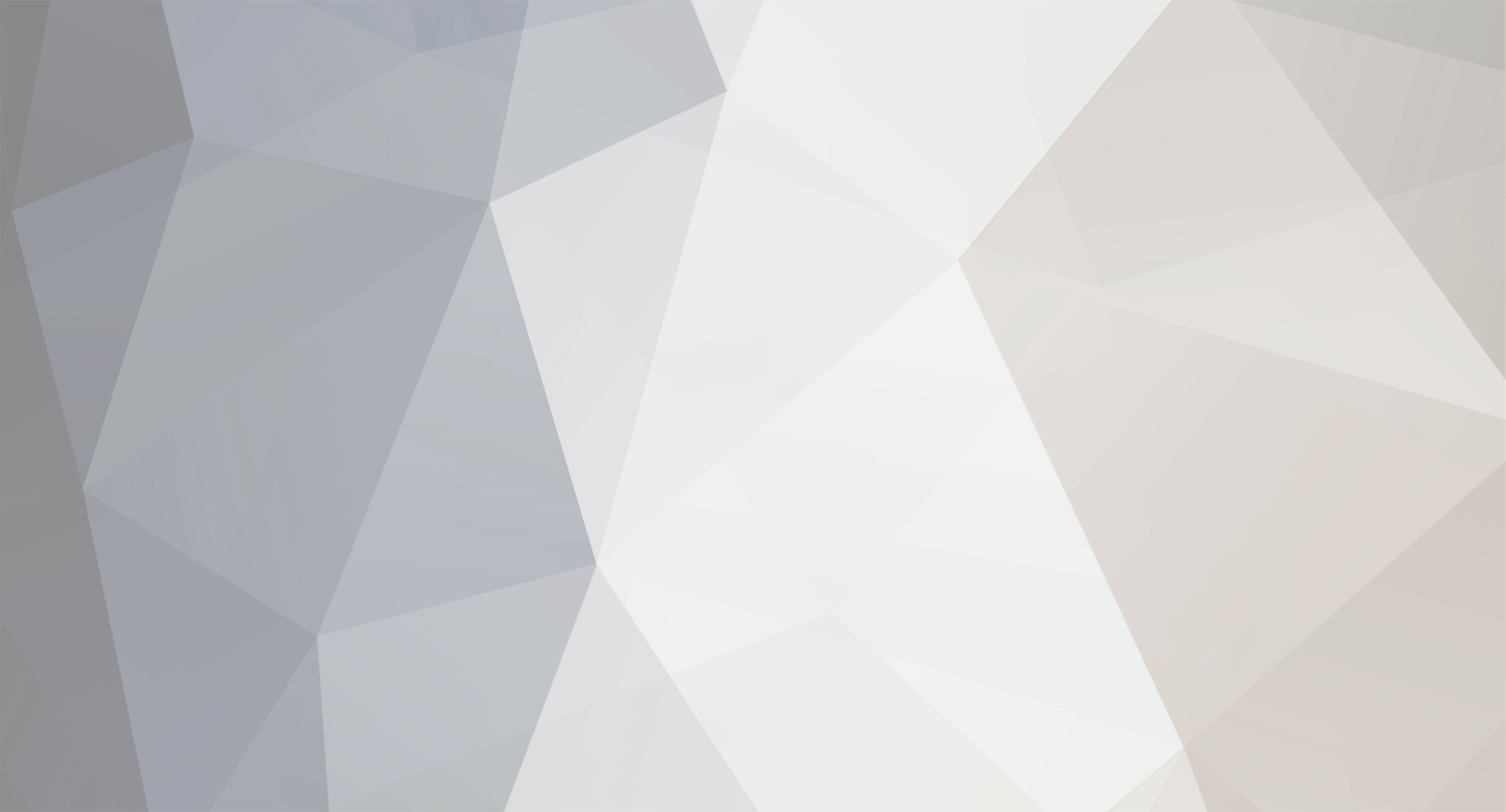
kscarbel2
Moderator-
Posts
17,892 -
Joined
-
Days Won
86
Content Type
Profiles
Forums
Gallery
Events
Blogs
BMT Wiki
Collections
Store
Everything posted by kscarbel2
-
DOT Finally Proposes Truck Speed-Limiter Rule Heavy Duty Trucking / August 26, 2016 Federal safety regulators are proposing that heavy-duty vehicles be equipped with speed-limiting devices set to a specific maximum speed. A notice of proposed rulemaking was issued jointly on Aug. 26 by the National Highway Traffic Safety Administration and the Federal Motor Carrier Safety Administration. The NPRM comes after a decade-long push by trucking and safety advocates to put such a requirement in place for trucks and other commercial vehicles. For its part, NHTSA is calling for establishing a new Federal Motor Vehicle Safety Standard. This FMVSS would require that each new “multipurpose” vehicle with a GVWR over 26,000 pounds be equipped with a speed limiting device. The proposed standard would also require each vehicle, as manufactured and sold, to have its device set to a speed not greater than a specified speed and to be equipped with means of reading the vehicle’s current speed setting and the two previous speed settings (including the time and date the settings were changed) through its onboard diagnostic connection. FMCSA is proposing a complementary Federal Motor Carrier Safety Regulation that would require each commercial motor vehicle with a GVWR of more than 26,000 pounds be equipped with a speed limiting device meeting the requirements of the proposed FMVSS applicable to the vehicle at the time of manufacture, including the requirement that the device be set to a speed not greater than a specified speed. In addition, carriers operating such vehicles in interstate commerce would be required to maintain the speed limiting devices for the service life of the vehicle. However, no speed limit has been proposed yet for the proposed limiters. The Department of Transportation said only that the proposal “discusses the benefits of setting the maximum speed at 60, 65, and 68 miles per hour, but the agencies will consider other speeds based on public input.” “This is basic physics,” said NHTSA Administrator Mark Rosekind. “Even small increases in speed have large effects on the force of impact. Setting the speed limit on heavy vehicles makes sense for safety and the environment.” The speed-limiter NPRM was initiated way back in May of 2013. Seven years before that, the American Trucking Associations petitioned the two agencies to require speed limiters on all large trucks that would be set in order to electronically limit top speed to no more than 65 mph. According to DOT, the two agencies’ review of the available data indicates that limiting the speed of heavy vehicles would reduce the severity of crashes involving these vehicles and reduce the resulting fatalities and injuries. “We expect that, as a result of this joint rulemaking, virtually all of these vehicles would be limited to that speed,” stated DOT in its notice. DOT said that implementing the proposal safety “could save lives and more than $1 billion in fuel costs each year.” “There are significant safety benefits to this proposed rulemaking,” said Secretary of Transportation Anthony Foxx. “In addition to saving lives, the projected fuel and emissions savings make this proposal a win for safety, energy conservation, and our environment.” The American Trucking Associations “hailed” the NPRM “as a potential step forward for safety.” ATA President and CEO Chris Spear said the lobby was “pleased NHTSA and FMCSA have, almost 10 years after we first petitioned them, released this proposal to mandate the electronic limiting of commercial vehicle speeds. Speed is a major contributor to truck accidents and by reducing speeds, we believe we can contribute to a reduction in accidents and fatalities on our highways.” Spear added that carriers that are already using speed limiters voluntarily “have found significant safety, as well as fuel efficiency and equipment lifespan benefits with little to no negative impact on productivity. We will be carefully reviewing and commenting upon today’s proposal.” Among those comments will be ATA’s position on the maximum speed setting and tamper-proofing of the devices. ATA said its 2006 petition seeking this rulemaking sought a maximum speed of 68 mph and that the association’s safety agenda calls for a national speed limit for all vehicles of 65 mph. “In their proposal, the agencies say setting the speed at 68 could save 27 to 96 lives per year; setting it at 65 could save 63 to 214 lives annually and at 60 could save 162 to 498 lives,” ATA said in a statement, “but notes that they do not have the same confidence about the data for the 60 mph alternative as the other two options.” The association also said the proposed rule “despite ATA’s initial request does not mandate the limiters be tamper-proof, instead it proposes requiring motor carriers to maintain the speed limiting devices at a set speed within the range permitted by the Federal Motor Vehicle Safety Standards.” While ATA has long been a proponent of speed limiters, the Owner-Operator Independent Drivers Association responded to the NPRM by calling it a “dangerous mandate.” OOIDA contends that use of “such devices create speed differentials that lead to more crashes and promote road rage among other motorists.” OOID also argues that speed limiters “actually take control out of the hands of drivers in that there are a number of scenarios that require drivers to accelerate in order to avoid danger.” “Highways are safest when all vehicles travel at the same relative speed,” said OOIDA Executive Vice President Todd Spencer. “This wisdom has always been true and has not ever changed. “No technology can replace the safest thing to put in a truck, which is a well-trained driver." DOT will seek public comment on the proposed rule for 60 days after it is published in the Federal Register, which is likely to occur during the week of Aug. 29. Comments should be addressed to these DOT docket numbers: NHTSA-2016-0087 and FMCSA-2014-008. Once the comment period opens, comments may be submitted by any of the following methods: Federal eRulemaking Portal. Follow the online instructions for submitting comments Mail. Docket Management Facility. U.S. Department of Transportation, 1200 New Jersey Avenue S.E., West Building Ground Floor, Room W12-140, Washington, D.C. 20590-0001 Hand Delivery or Courier. 1200 New Jersey Avenue S.E., West Building Ground Floor, Room W12-140, between 9 a.m. and 5 p.m. ET, Monday through Friday, except Federal holidays Fax. 202-493-2251
-
U.S. Proposes Device to Force Trucks, Buses to Travel at Lower Speeds The Wall Street Journal / August 26, 2016 The U.S. is seeking to forcibly limit how fast trucks, buses and other large vehicles can travel on the nation’s highways. A new proposal Friday would impose a nationwide limit by electronically capping speeds with a device on newly made U.S. vehicles that weigh more than 26,000 pounds. Regulators are considering a cap of 60, 65 or 68 miles per hour, though that could change. Whatever the speed limit, drivers would be physically prevented from exceeding it. The proposal, which comes from the National Highway Traffic Safety Administration and Federal Motor Carrier Safety Administration, doesn’t force older heavy vehicles to add the speed-limiting technology, but the regulators are still considering it. The government said capping speeds for new large vehicles would reduce the 1,115 fatal crashes involving heavy trucks that occur each year and save $1 billion in fuel costs. While the news is being welcomed by some safety advocates and nonprofessional drivers, many truckers said such changes could lead to dangerous scenarios where they are traveling at much lower speeds than everyone else. The rule has been ensnared in a regulatory maze in the decade since the nonprofit group Roadsafe America issued its first petition in 2006. The group was founded by Atlanta financial adviser Steve Owings and his wife Susan, whose son Cullum was killed by a speeding tractor-trailer during a trip back to school in Virginia after Thanksgiving in 2002. The nonprofit was later joined by the American Trucking Associations, the nation’s largest trucking industry group. Mr. Owings said he would continue to push the NHTSA to force older heavy vehicles to limit their speeds. “We are dismayed and outraged to learn the proposed rule will be for newly manufactured trucks and will not apply to the millions of trucks with which we continue to share the roads today,” he said. The NHTSA said retrofitting vehicles made after 1990 with the speed-limiting technology could be too costly, and it is still seeking comments and additional information. The NHTSA said it could cost anywhere from $100 to $2,000 per vehicle, depending on when the vehicle was made. Changes to some engines could also be required, increasing the costs, the NHTSA said. Heavy vehicles made before 1990 don’t have the capacity to add the technology. The government agencies involved will take public comment for 60 days, then determine the final limit and decide if the regulation should be put in place. To James Chapman, a big-rig driver from Spartanburg, S.C., 68 mph would be the best option and he’d accept 65. But 60 mph would be too big of a difference from cars that are traveling at 75 mph or more. “To me it would be a safety hazard unless it slowed everybody else down,” he said while refueling his truck Friday along Interstate 75 near Findlay, Ohio. The agencies said that limiting the speed of heavy vehicles to 60 mph could save as many as 498 lives annually. Limiting it to 65 mph could save as many as 214 lives, and limiting it to 68 mph could save as many as 96 lives. There are 3.6 million big rigs on U.S. roads. The agencies said the proposal is based on available safety data and the additional benefit of better fuel economy.
-
Production of V-8 Maxidyne under way by Mack Trucks
kscarbel2 replied to kscarbel2's topic in Trucking News
ENDT865 14.19L 325hp @ 2,100 1,491 N.m @ 1,350 Maxidyne (5 or 6-speed Maxitorque) ENDT866 14.19L 375hp @ 2,200 1,410 N.m @ 1,600 Conventional torque-rise for multi-speed transmission ETAZ1000 16.36L 400hp @ 1,900 2,060 N.m @ 1,230 Conventional torque-rise for multi-speed transmission ETAZ1005A 16.36L 400hp @ 2,100 2,060 N.m @ 1,230 Maxidyne (5 or 6-speed Maxitorque) EM9-400 16.36L 400hp @ 2,100 2,061 N.m @ 1,230 (55% torque rise) Maxidyne (5 or 6-speed Maxitorque) EM9-400R 16.36L 400hp @ 1,700 2,061 N.m @ 1,230 (23% torque rise) Eco-spec conventional torque-rise for multi-speed tranny E9-440 16.36L 440hp @ 1,800 2,027 N.M @ 1,300 (16% torque rise) Conventional torque-rise for multi-speed transmission E9-400 16.36L 400hp @ 1,900 1,796 N.m @ 1,300 (20% torque rise) Conventional torque-rise for multi-speed transmission E9-450 16.36L 450hp @ 1,900 2,027 N.m @ 1,300 (20% torque rise) Conventional torque-rise for multi-speed transmission E9-500 16.36L 500hp @ 1,900 2,251 N.m @ 1,300 (20% torque rise) Conventional torque-rise for multi-speed transmission The 865 was a high torque-rise Maxidyne spec V-8, and the 866 was set up for multi-speed transmissions. When the E9 first came out in the early 1980s (evolved from the ENDT1000/1005) at the same time Cruise-Liner production shifted from Hayward, California to Macungie, you had the EM9-400 Maxidyne V-8 governed at 2,100rpm (55% torque rise), the "Econodyne" spec EM9-400R for multi-speed transmissions governed at 1,700 rpm (23% torque rise), and the E9-440 V-8 for multi-speed transmissions governed at 1,800rpm (16% torque rise). The EM9-400R offered maximum fuel economy in a V-8, while the E9-440 was aimed at the owner-operator segment. Then in the mid-eighties, the Maxidyne spec V-8 was dropped, and the product range became the E9-400, E9-450 and E9-500 (US market) which all had a 20% torque rise. -
The former superb Mack Trucks Remanufacturing Center outside of MIddletown, Pennsylvania, established by the legendary Ross Rhodes, is now a Volvo branded facility. http://www.volvotrucks.us/about-volvo/facilities/reman-center/
-
In the old days, if they wanted to block off the puff limiter altogether, or install a 691GC218CP6 puff limiter (the version with the least affect....there's a Service Bulletin), I had no problem with that. But I never encountered a good customer experience from turning up the fuel.
-
Who designed/styled the Superliner?
kscarbel2 replied to sodly's topic in Antique and Classic Mack Trucks General Discussion
http://www.bigmacktrucks.com/topic/43658-21977-over-drive-cruiseliner-report/#comment-321468 The Cruise-Liner was a big step forward for Mack Western. It was the result of west coast truck engineers that Mack had hired. In theory, they could give us a leap forward with a true west coast design. In the eyes of many in headquarters, the original Hayward designed/produced Cruise-Liner was an engineering disaster. The freedom given the west coast engineers was revoked, and the 2nd gen Cruise-Liner was created in Allentown (fixing many of the shortcomings). The MH Ultra-Liner restored Mack's reputation as a designer of well-engineered COEs. The axle-mounted steering arrangement was a huge mistake. The telescoping steering shaft wore out prematurely (we sold thousands of replacements, averaging 2-3 over the life of a truck), as did the steering gears and pitman arms, becoming strong sellers in the parts department. (the output shaft splines and pitman arm splines were constantly wallowed out owing to the nature of the stupid design). The disconnecting (ball and socket) shift linkage, specifically the gears, rails, bushings and seals in the tower, also had unacceptably short life (the average truck's shift tower was rebuilt at least 3 times over its life). It was a terrible design, whereas the shift linkage on the MH Ultra-Liner was superb. I did prefer the original first generation Cruise-Liner instrument panel over the simplified second generation, however the center console had all the aesthetics of a plastic box. It was excessively large and the top (with the vents) frequently cracked and required replacement, a problem resolved with the second generation (It's pretty embarrassing when west coast Mack dealers have console covers hanging in their show room because they're such strong sellers). And then you had those expensive rubber riv-nuts that retained the grille constantly falling out. Here it is year 2016 and I couldn't possibly forget the part number, 68RU29301P5, because it was a hot issue. The Trico pantograph windshield wiper arms and their transmissions didn't hold up. All of these issues were covered in Mack Service Bulletins.............there were more service bulletins on the WS/WL Cruise-Liner than any other single model in the history of Mack Trucks. I found the cab was "beat" less with the 10,500lb front suspension. But dealers were accustomed to ordering the 12,000 front suspension, as they had for years with the heavier steel-cabbed F-model. The work ethic of the employees at the Hayward plant was terrible. They were "California casual" about showing up for work......one never knew how many people were coming in. The Allentown people sent out there were in constant frustration. The workers would install cab screws with their power tools until the threads were stripped. They didn't care. The idea of setting up a west coast plant for west coast truck production was logical. However, there was a people problem. This is all why the plant was closed, and the 2nd gen Cruise-Liner was built at Macungie.......with significantly better quality. I believe Peterbilt closed its plant at nearby Newark, California plant in 1986 for the same reason, issues with assembly quality. Caterpillar, Ford, GM and International Harvester abandoned the Bay Area as well. -
Any time one "turns up the fuel", they're simultaneously asking for trouble. If I had a dime for every time I've heard a version of this story.......
-
Who designed/styled the Superliner?
kscarbel2 replied to sodly's topic in Antique and Classic Mack Trucks General Discussion
I'm pressed for time just now, but I'm going to quickly tell you, the first generation frame that, yes, shared with the RWL/RWS and WL/WS, was NOT a good design. I've mentioned before, the axle-mounted steering gear was a disaster, as was the disconnect shift linkage design (WL/WS). And, it didn't use Mack's superb "body-bound bolts" which led to the same fastener headaches of the "assembled trucks". We gave the west coast engineers some leeway......and it didn't work out. When we fired many of them and brought the Cruise-Liner to Macungie, we "fixed it" as much as we could, to get by until the MH was launched. It still had those flaws, but it was a much better truck. On the other hand, the state-of-the-art Allentown-designed frame used on the MH and RWI, and the cutting edge break-away shifter design (MH), were as advanced as any truck today. And of course, the frame-mounted steering was trouble-free. Frankly speaking, the MH Ultra-Liner was the "best" truck we ever designed. -
Relax.......it's all just a show. Seriously, do you honestly believe that either Hillary Clinton or Donald Trump would actually be allowed to run America Inc. ?
-
Test Drive: Is International's HX620 the Driver's Vocational Truck?
kscarbel2 replied to kscarbel2's topic in Trucking News
I've always liked that cab. I don't dislike the CAT instrument panel, but I do like the old instrument panel. I'd like to see NAV offer both, which would please almost everyone. -
The Daily Mail (Hagerstown, Maryland) / October 12, 1970 ALLENTOWN, Pa. -- Mack Trucks, Inc., has added another chapter to the success story of its revolutionary "constant horsepower" Maxidyne engine with the production of an even more powerful model, a V-8 Maxidyne delivering 325 horsepower. Announcement of production of this newest turbocharged Maxidyne, which is coupled with the proven five-speed Maxitorque transmission, was made today by Walter M. May, executive vice-president of engineering and product, and Gerald F. Jones, executive vice-president of marketing. May and Winton J. Pelizzoni, chief engineer of power trains, developed the basic Maxidyne principle. Although production of the original 237-horsepower Maxidyne, a six-cylinder in-line engine, began only three years ago, it already accounts for more than 60 per cent of all Mack engines sold. May and Jones stressed that the V-8 Maxidyne, designated ENDT865, is designed to supplement, not replace, the original Maxidyne. "Mack's new V-8," they said, "is the perfect answer for the truck fleets and owner operators in need of an engine in the 325-horsepower range which provides all the advantages of the original Maxidyne, a drastic reduction in the shifting of gears, better operating efficiency, less driver fatigue and a reduction in maintenance costs." Zenon C. R. Hansen, Mack chairman of the board and president, said the newest Mack engine "will further entrench Mack in the Number One spot among all manufacturers of diesel-powered trucks. "Reports on the 23 prototypes we've had running in all sections of the nation for the last two years prove there is nothing else like the Maxidyne V-8. It's another 'first' for Mack, another quality power train from a company known around the world for the durability of its products," said Hansen. Development of the V-8 Maxidyne was under way when Mack introduced the in-line Maxidyne in 1966 and started production of that six-cylinder model the following year. A number of the V-8 prototypes, pulling up to 160,000 pounds gross combination weight, individually have logged more than 200,000 miles. Results showed the Maxidyne made the run with up to 83 percent less shifting of gears and finished about 11 hours ahead of one truck and close to six hours ahead of the other, and provided a substantial fuel economy advantage. The Maxidyne concept of constant horsepower over a broad working range of 1,400 to 2,400 revolutions per minute and a 56 percent torque rise in that range, make the difference. May and Pelizzoni slated: "Through most of its speed range, the Maxidyne actually puts out more power than higher rated engines, which exceed it for only the top 200 rpm. With a Maxidyne, the horsepower increases as rpm drop. Since the engine runs at lower rpm most of the time, it also consumes less fuel.
-
International Trucks Press Release / August 25, 2016 Best-in-Class Integrated Powertrain Warranty Package Now Available on New Orders of International DuraStar International Truck announced today the availability of the International DuraStar Integrated Powertrain Warranty Package, an exclusive, best-in-class, 4-year/unlimited miles and hours integrated powertrain warranty on new orders of its Cummins ISB-powered DuraStar model configured with Eaton’s “Procision” 7-speed dual-clutch automatic transmission, Dana Spiceraxles and driveshafts. International is offering this program to businesses in the pick-up and delivery segments as a testament of its confidence in the quality and performance of their medium-duty product. "The International DuraStar is one of the most reliable trucks in the medium-duty market," said Carl Webb, vice president and general manager, Medium-Duty Truck, International Trucks. "This new warranty is both a testament to the outstanding uptime this product delivers and also an example of our commitment to standing behind our products." The 4-year/unlimited miles and hours integrated powertrain warranty on the DuraStar features the most efficient engine ratings offered in the Cummins ISB6.7 diesel powered engine. The addition of the Eaton Procision dual-clutch transmission allows for safe, easy and fuel efficient operation of the truck for any driver. The DuraStar is the first truck in the industry to offer a powertrain that delivers outstanding drivability and high power density through high capacity gearing with the Dana E Series Steer and S140 Drive axle bundle. "Customers in need of a dependable truck that can handle the rigor of stop and go operation and withstand long idle times should strongly consider this specification of the DuraStar," said Webb. "It will deliver the efficiency they need with the peace of mind they require." To qualify for the DuraStar Integrated Powertrain Warranty Package, customers must either order or purchase a DuraStar from an International dealer between Aug. 22, 2016 and Dec. 31, 2016. Eligible truck applications include Dry Van, Refrigerated Van, Roll Back Recovery, Attic Van, Beverage (not tractor), Expedited Freight or Stake Flat with a max GVWR of 33,000 lbs. For more information, go to: www.InternationalTrucks.com.
-
Commercial Motor TV - sponsored by DAF Trucks / August 25, 2016 .
-
There's no doubt that Scania man Martin Lundstedt is feeling torn this week.
-
Key word: “athletic” Scania Group Press Release / August 25, 2016 One of the guiding principles in the development of Scania’s new generation of trucks was to create work vehicles for professionals, featuring the world’s best driver environment. The result, after a more than a decade of work, shows all the signs of setting a completely new industry standard. As Scania prepared to launch its R-Series in 2004, work had already begun on the next generation of trucks. Working within a number of new projects, the company’s designers sought a deeper understanding of the qualities that distinguished Scania as a brand and characterised its products. Customers and drivers in different segments and markets around the world were interviewed about what Scania meant for them. “We also looked at what assets from our own history could be developed and we studied how society might look over the coming the 5, 10, 20 or 50 years,” says Kristofer Hansén, Head of Scania’s Styling and Industrial Design division. Driver safety, vision, and interior space In parallel with these more theoretical studies, Scania’s designers conducted a number of projects involving experimenting with the layout and functionality of the cab. Based on in-depth studies from ergonomists, different conceptual ideas, and personas (imaginary typical customers), a number of proposals were developed for possible solutions for how the driver environment, sleeping area, storage and other features could take shape, design-wise, in the future. One particular important decision in terms of the design that was made very early on was to move the front axle 50 mm further forward in the next generation of trucks. This has allowed the driver’s basic position to be moved 65 mm closer to the windscreen and 20 mm out towards the side compared to earlier cab generations. “Above all, this allows for major improvements in terms of driver safety, vision, and interior space,” says Hansén. “We also got more space for seat adjustment, storage and the bed. Overall, it helped produce a truck that’s even easier to manoeuvre and has a whole new field of vision from the driver’s position.” The starting point for work on the next generation was that Scania is one of the best trucks to drive and use – and that is should become even better. A big part of the development work, therefore, involved creating an absolutely world-class driver environment. “With our work we aimed for what we sometimes called “masterful control of majestic power,” says Hansén. “It was a description of an outstanding driver environment. It’s what you, as a driver, feel when you have climbed up into the cab and have all that power under you. It communicates directly with you through the wheel, the interior, the sound, colours and functionality.” Hansén continues, “So, the new interior and the driver’s position don’t try to hide that this is a working environment for professionals. The feeling behind the wheel should be like steering a big, powerful premium car, while also simplifying and strengthening functionality through the new digital interface integrated into the driver’s position.” Well-crafted design Field test drivers, customers and other test personnel have, during development work, experienced a level of quality and design in Scania’s new truck cab that is completely new for the industry. Repeatedly heard comments include that the design is well crafted and well thought out, and that it gives the driver a strong sense of being well looked after. Hansén explains, ”Every part and every feature has been exposed to an intense process of questioning and evaluation, and we haven’t taken the easy option of using solutions that after a short period of use will be perceived as meaningless and irritating. When it comes to the new truck’s exterior, Scania has placed the greatest emphasis on aspects related to aerodynamics and, as a result, fuel consumption. All surfaces, including the front, the sides and even the underside, are optimised for the lowest conceivable drag. A powerful interior The exterior design of the new generation of trucks is also built on an approach of asking the question what the product stands for and what Scania wants to convey. But what can designers do with the square box that a truck cab literally is? ”Early on in the project, we determined that we were more agile in our expression than our competitors, and also in our way of looking at what we offer as a brand,” says Hansén. “It’s not just a truck, but rather a whole transport service. Hansén continues, “‘Athletic’ was another word that resonated early on, sometime around 2007. We shouldn’t be some big, strong lump – like a sumo wrestler – but rather a first-class race horse – a thoroughbred – without an ounce of extra fat around its muscles. This, of course, all corresponds with the fantastic engine that we’re known for.” The guidelines for Scania’s new trucks were, thus, to continue to emphasise the existence of the powertrain, with a clear, big front cover and the surfaces around the truck serving as the aerodynamic coverings to a powerful interior. “For this reason, the design language is now more controlled, with sharper lines but at the same time a more accommodating roundness, instead of extreme angularity or simpler, trendier, round areas, which it would have been significantly simpler to build up a design around.” Another goal for Scania’s designers was for the new truck to be a market leader in terms of aerodynamics while at the same time incorporating features that were previously applied separately, such as the sun visor or extra wheel trim. Avoiding huge dash units As part of the basic configuration, position lights and extra lights are now located within the chassis, without negatively impacting aerodynamics. This opened the way for using specific form elements that allowed for the integration of new types of lamps in the cab and chassis, something that heavily contributed to how the new trucks is perceived as a whole. The design of the new dashboard is also built on a desire to avoid the clumsy and huge dash units that are often found in trucks. “We have also tried to express a sense of ‘Agile Strength’ and ‘Flexible Power’,” says Hansén. “Seen from above, the instrument panel has a wing profile that clearly delineates the driver side from the passenger side, or living room if you like.” Hansén concludes, “The panel that the controls sit on is divided up into two segments, an upper and a lower part with an elegant horizontal step in the middle. This makes it easier to find what you’re looking for, you can support your fingers on it, and it makes selection easier and clearer than if we had used a big flat surface with the controls placed wherever.” No unnecessary fat Scania’s new generation of trucks has been designed and developed by the company’s own designers. The guidelines for the design of Scania’s new trucks were to continue to emphasise the powerful engines, but within a slimmer and more athletic form. “The new trucks communicate a sense of power, but in a new, more efficient and more flexible way than the previous generations,” says Anders Lundgren (left), Team Leader for Exterior Styling on the new generation of trucks. “There’s no unnecessary fat around the muscles – these are thoroughbreds.” Human touch Anna Selmarker leads Scania’s efforts in the field of Human Machine Interface (HMI) – the digital interaction between human beings and machines. One of Selmarker’s most important tools is a driver simulator that can simulate virtually any environment or situation that a driver might be exposed to. A good example of the results is the new dashboard, where drivers can simply and intuitively find the information they require. “Our vision is for Scania drivers to always be able to say that they perform best, because they have vehicles that support them in the best and most efficient ways,” she says. “That’s been the guiding principle in our work with the new generation of trucks.” Passenger car feel Christina Isomaa is Team Leader for Colour and Trim for the new truck generation. She and her team work on the colours, textures, and materials of a variety of different details, both within the cab’s interior and on its exterior. “There have been lots of changes in terms of colours and material choices in the new generation of trucks,” says Isomaa. “We have textiles and other materials that can withstand dirt and heavy wear, leathers with fantastic qualities, and small details that create that little bit extra like wood and metal. These are things normally only seen in exclusive passenger cars, so we’re really pleased and proud of these new features.” Passion for details Håkan Kåreby and the Appearance Approval team literally put on white gloves to examine Scania’s new trucks in detail. The team is responsible for the final quality check on all incoming articles. “We thoroughly investigate all parts to check that they are consistent with the idea and the vision that we have for the next generation of Scania trucks,” says Kåreby. “In practice, this means that we examine every visible item, about 2,600 parts. We work with our eyes, which are our primary work tool. We have digital verification tools, we use CAD and other support systems, but our eyes are always superior when it comes to judging colour and shape.” Driver’s best friend Scania’s Styling department has spent a lot of time improving ergonomics and the user-friendliness of the driver environment in every conceivable way. “We work with biomechanical ergonomics, adapting the driver environment to the driver’s bodily requirements and limits,” says Fredrik Pehrson at Scania’s Physical Vehicle Ergonomics division. “Typical questions were how the driver’s seat should be designed. But we also work with macro-ergonomics, adapting the entire cab environment to the drivers’ overall needs in terms of living in and moving about the cab.” “Over the years, we have met and interviewed many drivers to identify their needs in all aspects: direct and indirect sight, space within the cab, the work involved in getting in and out of the cab, the ability to sleep well and store their things, and so on.” Photo gallery - https://www.scania.com/group/en/key-word-athletic/
-
The Southern Illinoisan / August 25, 2016 The seven commercial tractors and two trucks that Navistar International Corp. has donated to Southern Illinois University are to the automotive technology student what the cadaver is to a medical student. This major donation to SIU’s Department of Automotive Technology, announced by school and company officials on Thursday morning, represents an opportunity for students to dissect the latest technology hitting the highways. Navistar additionally donated several engines, transmissions, driveline and emission control components. The availability of the trucks will allow students hands-on learning in the processes of diagnostic testing and code interpretation to determine where and what a problem is on a truck when things go wrong, said John McCuistion, Navistar's global powertrain and chassis engineering director. The most critical element of the availability of the trucks on SIU’s campus is that it provides access to the latest technology so that students are on the cutting edge when they graduate into the workforce. “This is the technology that is really going to be quite beneficial,” he said. The partnership additionally includes commercial truck and equipment retailer Rush Enterprises Inc., which has donated licenses to Diamond Logic Builder diagnostic software. Officials from SIU, Navistar International and Rush Enterprises officially celebrated the public-private partnership at an event held Thursday morning at SIU’s expansive Transportation Education Center located on the grounds of the Southern Illinois Airport near Murphysboro. Dozens of undergraduate automotive technology students attended the gathering. Aaron Weckhorst, a senior from Champaign, said that it’s a boon for students because it allows them to get closer to the advanced technology they will be working with post-graduation in the automotive industry. “It’s definitely a huge advantage to work on these (tractors and trucks) as opposed to what we used to have,” he said. “The new vehicles are a lot more advanced than the previous one that we had so it’s a big benefit.” Commercial truck technology is rapidly evolving. Advances are in large part driven by federal government regulations aimed at reducing greenhouse gas emissions and improving fuel economy standards, McCuistion said. SIU and Navistar officials did not have an exact dollar figure to attach to the donation, but it is significant, to the tune of several hundred thousand dollars, McCuistion said. Just one truck can sell for upwards of $100,000, though the trucks donated to SIU are not licensed for the roadways. SIU Chancellor Brad Colwell said students “expect and deserve no less than the best” and that the Department of Automotive Technology is an example of that commitment to excellence. As part of fulfilling that promise to students, Cowell said, “higher education also needs access to the greatest technology, technological advances and business practices.” And he said public-private partnerships such the one between SIU, Navistar International and Rush Enterprises give students that access. Colwell also took a moment to note the beauty of the beasts parked behind him as he spoke at the podium — one in particular sporting SIU’s colors. “I love this particular truck behind me. It’s got a great grill, dual-smoke stacks, and it’s maroon in color. And if you don’t mind, I’m going to take it home for just a quick test drive,” he said, laughing. “But it’s probably worth more than my annual salary so I won’t do that.” The event was attended by four state lawmakers — Sens. Gary Forby and Rep. Brandon Phelps, both Democrats, and Sen. Dave Luechtefeld, and Rep. Terri Bryant, both Republicans. During his turn at the microphone, Luechtefeld noted the dire financial situation facing the state and the uncertainty that has created at public universities including SIU. Given all the angst, Luechtefeld said it was nice to celebrate “good news.” Looking out at the automotive technology students in the audience, he said they are the people “who will absolutely lead this industry” into the future, and of the department, he said, “this may be as good as it gets” when it comes to educational programs in the field. Michael Behrmann, chairman of the Department of Automotive Technology, said students graduate from the program well prepared for a variety of jobs in the industry, in both government and the private sector. He said undergraduate students are trained in the latest technology, diagnostic techniques, and development of diagnostic procedures. As well, they are trained in soft skills that include management of technology and personnel, marketing and business practices. The program is pumping out some of the brightest in the industry, Behrmann said. He also noted that the program further opens opportunities for Southern Illinois to draw employers in the automotive industry to Southern Illinois that may be attracted by the proximity of a well-trained workforce, vast land resources and access to interstates and railways. Behrmann said he works closely with economic developers to market the region to decision-makers in the industry looking for places to start up or expand. “This region is primed for future development and expansion of these companies when they’re looking at opportunities and locations,” he said. “Southern Illinois is a prime location for them to consider.” .
-
Fleet Owner / August 25, 2016 Despite diesel fuel prices being in a trough last year, 17 North American fleets kept investing in a number of fuel-saving technologies for their trucks, and it's been paying off. Compared to national average fuel costs for over-the-road Class 8 trucks in 2015, the fleets saved what would break down to about $29.5 million apiece last year, the North American Council for Freight Efficiency (NACFE) reports in its latest Fleet Fuel Study. This is the fifth go-round of this study, with the first of its kind published in 2010. Participating fleets included Bison Transport, Cardinal Logistics, CR England, Challenger Motor Freight, Crete, Frito Lay, Maverick, NFI Industries, Nussbaum, Paper Transport, Prime, Ryder, Schneider, UPS and XPO Logistics (another two contributed data for past studies but couldn't for this 2016 report). All told, the study fleets collectively boast some 62,000 tractors and 217,000 trailers, and they saved a total of about $500.6 million in fuel costs, the study finds. NACFE develops these annual reports along with Carbon War Room, another nonprofit that was the brainchild of Sir Richard Branson, with their combined effort known as Trucking Efficiency. The study fleets employ various combinations of 69 fuel efficiency technologies reviewed in Trucking Efficiency Confidence Reports including truck chassis, idle reduction, aerodynamic, powertrain and tractor/ trailer advancements, operational changes and more. Last year marked the single biggest bump northward in average fuel economy the study fleets have seen — 3% — from 6.87 to 7.06 mpg. All told, that extra fuel efficiency helped the 17 fleets save a total of $500.6 million vs. national average Class 8 truck fuel spending; the national average fuel economy for those trucks was 5.83 mpg. That's not quite the full story, though, noted Dave Schaller, industry engagement director at NACFE, since 7.06 mpg is the collective average mpg for the study fleets, which keep their trucks an average of 5 yrs. 3 mos. "If you look at a five-year time frame, we're seeing some pretty substantial differences in fuel economy between the truck that's being traded in — say, our 2010 model year — and the new ones being operated now," Schaller said on a call with reporters Wednesday morning. "We're looking at close to a 16% gain in fuel economy between the trucks they're stepping out of and the trucks they're stepping into." In addition, although crude oil and correlating gasoline/ diesel prices remain low or middling, Schaller pointed out that those prices are volatile and could be agitated easily. "We've just experienced, as our little planet is revolving today, two earthquakes greater than 6.0 [magnitude]. If one of those happened to hit in a fuel oil-producing area, fuel prices could change pretty rapidly — and people that didn't buy these technologies might be sorry." Three points stood out to the 2016 study authors: • The study fleets varied in their choices of fuel efficiency technologies. • New greenhouse gas and fuel efficiency regulations set out a longer-term adoption of these technologies as opposed to that of the study fleets, which means fleets in general will likely need to see lower total cost of ownership/ quicker payback to make these technology investments. • After five years of these studies, the Trucking Efficiency team noticed that trucks are being driven fewer miles. Following the Great Recession that hit hardest in 2008, fleets began upping truck productivity, hauling more tonnage with fewer loads. "This continues and even widens in 2016," according to the study. On that last point, NACFE and Carbon War Room suggest some explanations for what's driving the productivity increase. Freight could be becoming denser/ more tightly packed; trucks could be hauling more pallets per trailer; private fleets have been reducing their empty miles; wider telematics adoption could be boosting carriers' equipment visibility and helping tighten up routing, etc.; and maybe 3PLs are getting savvier at what they do. Can't be bothered with some tech Mike Roeth, executive director of NACFE and operations lead for Trucking Efficiency, stressed that point in the study that the participating fleets have all gone in their own directions with technologies they put in their trucks. That goes for even similar technology such as strategies/ tech to reduce idle time, but certain technologies stood out in that particular instance. Overall, he estimated that the fleets have about a two-year ROI for their technology costs. And although the fleets have continued to invest in fuel efficiency technologies while fuel's been cheaper, some technologies haven't fared quite as well in adoption rates as others. Essentially, Roeth surmised, those tend to be the ones that involve manual processes or require some driver inputs, like trailer boat tails the driver has to fold out. Another example is 6x2 axle configuration on tractors, which can increase tire wear and reduce traction. "I would throw 6x2 adoption into the bucket of technology that drivers don't really like and appreciate. In a time where in 2015, tonnage was way up and it's tough finding drivers, fleets decided, 'For awhile, I'm just going to stop buying some of these technologies that require driver intervention and take that off the table when I'm trying to recruit and retain drivers,'" Roeth said. "Some others [among less-driver-favored technologies] would be tire pressure monitoring systems, maybe some collision-avoidance systems — which really aren't in our study — or trailer tails that require drivers to do something," he added. "All those technologies require some driver interaction. They do have fuel economy benefits, but in a time when fuel prices are down, they just fall into this bucket where fleets go, 'I'll just wait, and when fuel goes up more, I'll buy these things and I'll deal with any driver education and reaction to it then.'" A palette of fuel efficiency tech: Choose your paint Roeth also noted on the call that a new NACFE confidence report for fuel efficiency technology due out this fall will address platooning with two tractor-trailers. A number of other technologies are listed in a Carbon War Room video, including the following: • Chassis technologies: 6x2 axles; 4x2 tractors; synthetic axle lube; two-speed fan clutches; clutched water pumps • Idle reduction technologies: electronic engine controls; diesel auxiliary power unit (APU); fuel-operated/ diesel-fired heaters; battery HVAC; automatic engine start/ stop systems; AC power ports; truck stop electrification; thermal storage systems; insulation • Powertrain technologies: automated manual transmissions; automatic transmissions; downsized engines; direct-drive transmissions; synthetic transmission oil; synthetic engine oil; fuel additives; economic engine parameters; gear down protection; predictive cruise control; altered vehicle gearing; clutched air compressors • Operational practices: speed limiters; driver economy training; driver incentives; in-cab behavior notifications; routing optimization; maintenance; coasting before engine braking • Tire and rolling resistance technologies: tire pressure monitoring (tractor); tire pressure monitoring (trailer); tire pressure inflation (trailer); low rolling resistance duals; wide-based tires (tractor); wide-based tires (trailer); aluminum wheels (tractor); aluminum wheels (trailer); nitrogen-filled tires • Tractor aerodynamics: aerodynamic tractors; tractor chassis skirts; aerodynamic bumpers; aerodynamic mirrors; remove parts on tractors; roof air fairing; cab extenders; fixed fifth wheel; tractor-vented mud flaps; tractor wheel covers; tractor weight reduction • Trailer aerodynamics: trailer wheel covers; trailer-vented mud flaps; trailer skirts; undertray/ bogie fairing; trailer nose cones; vortex generators; boat tails; narrow mud flaps; double/ triple trailers; part removal/ relocation; tractor-specified weight reduction .
-
Heavy Duty Trucking / August 25, 2016 Chevron unveiled its new line of Delo 400 engine oils meeting the American Petroleum Institute’s new CK-4 and FA-4 heavy-duty diesel oil specifications, offering improvements in fuel economy and engine protection. These new API specifications, which go into effect Dec. 1, were requested by engine makers to help them protect modern engines while improving fuel economy. FA-4 engine oils are designed to provide optimized fuel economy and protection for the newest engines. CK-4 engine oils are backward-compatible but provide better protection for current engines than the previous CJ-4 category. Shawn Whitacre, Chevron senior staff engineer and chairman of the ASTM Heavy-Duty Engine Oil Classification Panel, called the rollout “one of the most significant new product introductions in our history, and the most extensive laboratory development program we’ve ever developed. “On top of the very significant laboratory test program, we’ve added to what I would say is the most rigorous, varied and exhaustive field testing program we’ve ever undertaken.” The new oils have been testing in close to 500 Class 8 trucks, as well as a broad variety of off-highway equipment such as cement mixers, construction equipment, mining and agricultural equipment. The oils feature what Chevron is calling Isosyn Advanced Technology, a combination of Chevron’t premium base oils, formulation expertise and additive chemistry. Officials note that Chevron is unusual in that it has its own company making the chemical additives necessary for engine oils today. (In fact, Chevron says, it was the first company to start adding chemicals to base oils back during WWII, allowing submarines to run longer between maintenance.) Chevron says the Isosyn Advanced Technology enables increased durability, through better oxidation control, anti-wear protection and piston control, while extending drain intervals compared to API CJ-4 oils. “We are seeing some of the longest drain intervals and best engine protection in our company history,” said Len Badal, global Delo brand manager. The technology also enables the company to offer lower-viscosity oils for better fuel economy. Badal pointed out that when the last oil category, CJ-4, was rolled out about 10 years ago, “We really only were worried about one viscosity grade, 15W-40. There was a little bit of 5W- 40 but that was a small part of the business. As you can see today we have a significantly wider range of products, and it’s getting bigger as new regulations come down, as we meet different customer applications.” In fact, Chevron predicts by the time the next oil category comes around, we will see even lower viscosity products. “You’re going to hear things about 0W-20s and 5W-20s and 0W-16s that today are not in the language of HD engine operators,” Badal said. As part of its product rollout, Chevron will launch an advisor service to help customers select the best products by assessing their business needs, analyzing their current lubricant choices and developing a customized action plan. For fleets that buy new trucks factory-filled with FA-4 engines but don’t want to handle two oils, Chevron said, it’s OK to use a CK-4 (or even a CJ-4 while they are still available), but there likely will be a trade-off in fuel economy and extended oil drain intervals. The 2017 Delo 400 Product Line The new Delo 400 product line will be available in a variety of viscosities and will support both API CK-4 and FA-4 categories. The first product to be available, starting in September, will be the Delo 400 XLE 10W-30 synthetic blend meeting API CK-4. It offers up to 1% fuel economy improvement for large trucks, deli says, and offers significant cost savings across entire fleets with maximum engine durability protection. Delo 400 ZFA 10W-30 is the new oil meeting the FA-4 category. Chevron says this 10W-30 offers the best fuel efficiency of the 10W-30s in its product line, with a 20% improvement over CJ-4 10W-30. Even though no engine makers have yet approved FA-4 oils for older engines, Chevron says in its own testing, this oil has performed well in EPA 2010 and EPA 2013 engines. Delo 400 XSP 5W-30 is a full synthetic meeting API CK-4. It offers up to a 2% fuel economy improvement for large trucks, excellent low-temperature performance, and the longest oil drain intervals in the Delo 400 lineup. It also can be used in a wide range of engines, from heavy-duty diesels to diesel Sprinter vans to gasoline vehicles. Delo 400 XSP 5W-40 is a full synthetic meeting API CK-4. Chevron says it offers 20% better oil oxidation resistance, extreme cold pumpability, high temperature protection, and a 50% reduction in wear vs. CJ-4 products. Delo 400 XLE 15W-40, a synthetic blend meeting API CK-4, offers up to 25% longer oil drain intervals over OEM published intervals, Chevron says. It features clean piston technology, meeting Mercedes Benz stringent MB228.51 piston cleanliness requirements. Delo 400 SDE 15W-40 is a premium conventional base oil meeting API CK-4. Chevron says it offers 38% better wear performance vs. a CJ-4 15W-40, up to 20% increase in total diesel engine life to rebuild, and excellent engine cleanliness performance. And depending on market demand, Chevron also has developed a ZFA 5W-30 full synthetic oil meeting FA-4. Because there are two separate oil categories, Chevron has paid attention to packaging and labeling to help customers differentiate between them. Specially labeled caps color coordinated labels and caps (red for CK-4, yellow for FA-4) are designed to make it easy to differentiate. In addition, full synthetics will be in light gray bottle. synthetic blends in charcoal gray bottle, and a new pearlized blue will designate the premium conventional product. For more information go to www.ChevronLubricants.com .
-
Cummins Adds 450-HP ISX12 Ratings Heavy Duty Trucking / August 25, 2016 Cummins Inc. announced the availability of two new 450-hp ISX12 ratings for linehaul and regional-haul truck markets. The 450 hp with 1650 lb.-ft. of peak torque and 450 hp with 1450/1650 lb.-ft. of peak torque are the newest ratings for the ISX12. The 450 hp with 1650 lb.-ft. of peak torque provides performance on the same level as 15.0L and 13.0L engines but at a much lighter weight, which means more payload capacity, according to Cummins. The 450-hp 1450/1650 lb.-ft. SmartTorque rating is ideal for such applications as tank and bulk haulers that transport heavy material on the way out, but return with a light or empty load. SmartTorque technology modulates torque output to deliver the adequate amount of torque needed for the work being done. Since its release in 2010, the ISX12 has performed well across a wide range of trucking applications, from regional-haul and bulk-haul to refuse and mixer. The engine, with its power take-off (PTO) capabilities, continues to benefit customers who demand more from their medium-bore engines. The ISX12 has been a dependable product for many customers across North America since its release, according to Cummins. Williams Tank Lines, based in California, hauls petroleum products and operates predominately ISX12-powered trucks. "The maintenance is a lot lower with the medium-bore ISX12, we've had [fewer] breakdowns, it's more dependable, more consistent. We have some that are approaching a million miles, and they haven't been overhauled," said Mike Williams, president of Williams Tank Lines. Along with these new ratings for regional-haul trucks, Cummins is continuing to work on expanded ratings for vocational trucks, to provide even greater productivity in ISX12-powered cement mixers, refuse, and vacuum trucks. The ISX12 will continue to be Cummins vocational and regional/bulk-hauling champion through 2017, and will be available through the end of 2018, with Cummins launching the next-generation X12 at the beginning of 2018.
-
Who designed/styled the Superliner?
kscarbel2 replied to sodly's topic in Antique and Classic Mack Trucks General Discussion
While the first generation RWL/RWS Super-Liner and WL/WS Cruise-Liner share the same Red Dot 210RD59301 grilledensor, they were two different design programs. FYI: We also offered it as a grille only without the condensor (still supplied by Red Dot), for customers who didn't spec air conditioning.....210RD59301P2.
BigMackTrucks.com
BigMackTrucks.com is a support forum for antique, classic and modern Mack Trucks! The forum is owned and maintained by Watt's Truck Center, Inc. an independent, full service Mack dealer. The forums are not affiliated with Mack Trucks, Inc.
Our Vendors and Advertisers
Thank you for your support!