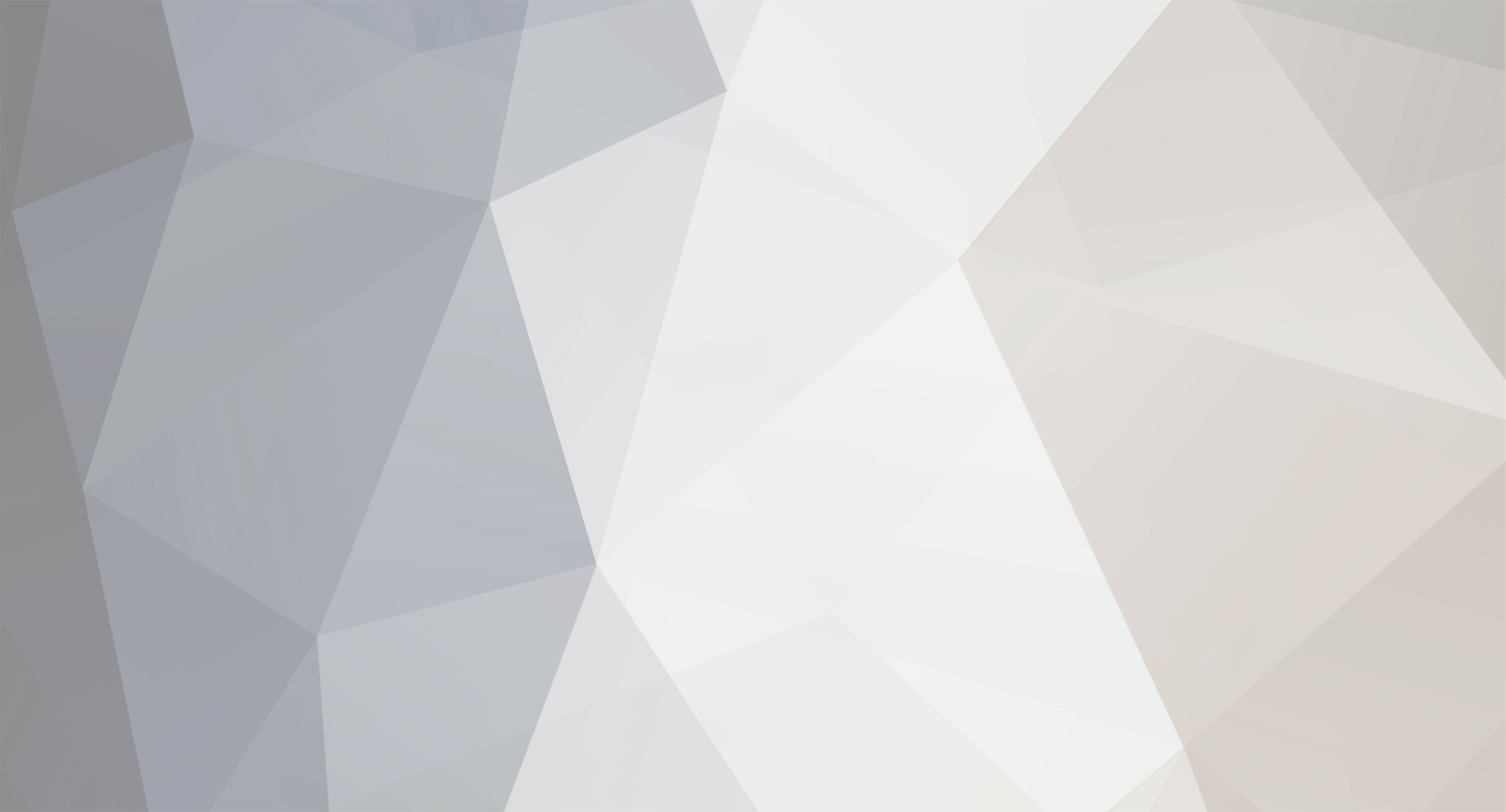
kscarbel2
Moderator-
Posts
17,891 -
Joined
-
Days Won
86
Content Type
Profiles
Forums
Gallery
Events
Blogs
BMT Wiki
Collections
Store
Everything posted by kscarbel2
-
Facing a lack of skilled technicians, UK to recall BC Mack........details at 11.
-
Trailer/Body Builders / January 22, 2016 UK truckmakers are gaining confidence for 2016 after registrations increased 27% in 2015 to 44,063 units, according to the Society of Motor Manufacturers and Traders (SMMT). Senior industry executives remain confident that demand is now at a healthy and sustainable level after a disappointing 2014 in which registrations were depressed by the impacts of Euro-VI introduction and European Community Whole Vehicle Type Approval. Stuart Webster, Iveco Managing Director, said, “Inflation is low and under control, the deficit continues to fall, growth is going generally in the right direction, unemployment is at its lowest level for almost a decade and oil prices are low and likely to go even lower. Interest rates remain low and look set to remain that way well into 2016.” Webster predicts that between 42,000 and 43,000 trucks will be registered this year. Although that would be below 2015’s total, Webster describes it as “the real market norm.” Ian Mitchell, MAN Sales Director, is more optimistic than Webster. He said, “We see the market for 2016 being broadly in line with 2015 at around 44,000 units.” Ray Ashworth, DAF Managing Director, is bullish too. He said, “With the single exception of the Euro-VI ‘pull-through’ year of 2013, not since 1988 has the heavy end of the market been in such rude health. We’re certainly looking good for 2016.” DAF was overall CV market leader once again in 2015, with a 26% market share, ahead of Mercedes-Benz and Scania. Scania’s result was a 48.9% increase on its 2014 performance, and it is off to a flying start in 2016. It has won an order for more than 2,000 trucks from Eddie Stobart and its associated companies; the manufacturer’s largest ever European order. Martin Hay, Scania UK Sales Director, said, “We expect the confidence in the industry to continue, and do not expect to see any significant changes in the size of the market from 2015.” The tractor unit market soared ahead by nearly 36% in 2015, with Mercedes-Benz finishing on top ahead of Scania. A record number of 6x2s made up the vast majority of registrations in the sector. The buoyant tractor unit market results contrasted with far more muted growth for 7.5-tonners, which increased by only 2.9% last year. Keith Child, Isuzu Managing Director, thinks that the market for 7.5-tonners will increase during 2016. He said, “We may see demand for 7.5-tonners grow as some major fleets turn over existing vehicles as part of their scheduled replacement cycle.” A vigorous construction industry helped push sales of multi-axle rigids upwards by over 20% in 2015, to 8,522 units. DAF led the way overall, although Scania registered more four-axle trucks. Whilst the strength of the construction industry has been a boon, manufacturers are wary of any slowing in the marketplace. Ian Mitchell said, “It will be interesting to see if demand for four-axle rigids continues at the same level this year.” One factor that might affect rigid registrations in coming months is a bottleneck in getting chassis bodied. “Body builders have been hit by the double whammy of recession – when they lost people and skills – and the advent of European Community Whole Vehicle Type Approval,” said Stuart Webster. “They’re short of resources and finding it difficult to respond, which means restricted capacity and lengthened delivery times, particularly for tippers and other construction industry trucks.” Manufacturers are also concerned that a lack of drivers will limit sales, as operators won’t buy trucks if they have nobody to drive them. Webster said, “The industry is getting desperately short of drivers, and too little is being done to encourage new and younger drivers in. The working conditions put many of them off, and the legislation that rules their lives is deterring them from entering the sector. “This is a crisis waiting to happen; and the time has come for the powers that be to take action at all levels.”
-
Commercial Carrier Journal (CCJ) / January 21, 2016 Cummins announced Jan. 21 it too will forgo exhibiting at the 2016 edition of the Mid-America Trucking Show (MATS), joining all major truck manufacturers in opting to skip the annual trucking trade event. It will, like the others have announced, return to the show in 2017, the diesel engine maker said in its announcement. Cummins and the other manufacturers have signaled they intend to participate in the show on a biennial basis from here on, exhibiting in odd-numbered years and skipping even-numbered ones. Daimler was the first to announce its intentions to skip, and Volvo, Mack, Peterbilt, Kenworth and International later announced the same. Some truck makers say they’d like to see the show itself move to a biennial format, as to avoid the conflicts of the biennial IAA commercial truck show that takes place every other year — even-numbered years — in Hanover, Germany. Mid-America organizers have maintained they intend to continue the show as an annual event.
-
Fleet Owner / January 21, 2016 Automatics and AMTs predicted to gain big ground in trucking Automated manual transmissions (AMTs) and their fully-automatic brethren are projected to gain significant ground in the North American truck market over the next decade, according to new research conducted by global consulting firm Frost & Sullivan. The firm predicts that AMTs and automatics will experience a compound annual growth rate (CAGR) of 3.9% and 2.9%, respectively, through 2025, while manual transmission demand will shrink by 2.7% over the same time period. By 2025, Frost & Sullivan expects the market share for manual transmissions among North American medium- and heavy-duty trucks will decline to 43.5%, while AMT market share will climb to 29.4%, with automatics at 27.1%. “The market is on fire,” Sandeep Kar, global VP of the firm’s automotive & transportation research practice, told Fleet Owner. “AMTs used to have less than 5% to 6% market share and they are now in the double digits. Economies of scale are shrinking the price difference [with manuals] and the benefit of higher efficiency is attracting more fleets.” Silpa Paul, the researcher in charge of the study, explained to Fleet Owner that fuel savings and driver recruitment/retention benefits are the two factors driving higher adoption of AMTs and automatics among trucking companies – with more demand for AMTs at the moment. “Fuel costs can account for 50% to 65% of a fleet’s operating costs, making it the highest cost component for fleets,” she said. “Studies show that adoption of AMTs and ATs can improve truck fuel efficiency in varying degrees depending on truck operating duty cycle [with] AMTs especially beneficial in drive cycles with high idling time in comparison to MTs [manuals transmissions and conventional ATs [automatic transmissions].” Paul added that as truck drivers from the baby-boomer generation retire and are replaced by millennials, training and retention costs are escalating because younger drivers lack basic familiarity with manuals, especially in North America, where passenger cars are now largely equipped with automatics. Fleets are also looking to leverage telematics to gain more benefits as well, she pointed out. “Manual transmissions are not ‘smart’ devices,” Paul said, noting that as AMTs and automatics are electronically controlled transmissions (ECTs), they can now be “integrated” with telematics to gain more performance data from the truck. “This is a great value-add for fleets,” Paul emphasized. Other data revealed by Frost & Sullivan’s global truck transmission study includes: - The medium-duty truck premium for AMTs averages $600-$3,000, increasing to $1,000-$5,000 for heavy-duty units. - The medium-duty truck premium for fully-automatic transmissions averages $3,000-$6,000, rising to $6,000-$10,000 for heavy-duty units. - Where newer dual clutch automated transmissions (DCTs) are concerned, the medium-duty premium averages $3,000-$5,000, while the heavy-duty premium averages $5,000-$10,000. - Those high incremental costs versus the potential fuel savings is the primary factor presently inhibiting mass adoption of ECTs as a group, the firm noted. - Globally, AMTs are expected to experience the highest rate of adoption over the next decade with a CAGR of 12.5%, while ATs will experience a CAGR of 7.7%. - Downspeeding, engine downsizing, and the increasingly “vertical integration” of truck transmissions in North America, Europe, and Asia is “catalyzing” the adoption of ECTs. Truck OEMs in particular are using ECTs to meet the higher torque requirements downspeeding places on powertrains. - European truck manufacturers already offer AMTs as “standard fitment” in both medium- and heavy-duty trucks; their market share topped 55.4% among European Union trucks last year. - However, the manual transmission will still dominate in trucks with gross vehicle weight ratings (GVWRs) exceeding 16 tons, Frost & Sullivan stressed as the fuel economy benefits of ECTs aren’t as yet conclusively proven. - That being said, manual transmissions will still experience a decline in global heavy-duty truck market share from 81.4% currently to 65.5% by 2025.
-
Mack Buses
kscarbel2 replied to 41chevy's topic in Antique and Classic Mack Trucks General Discussion
-
Mack and Scania
kscarbel2 replied to dogg rescue's topic in Antique and Classic Mack Trucks General Discussion
http://www.bigmacktrucks.com/index.php?/topic/34624-mack-scania-cooperation/?hl=ds8 -
Mack Buses
kscarbel2 replied to 41chevy's topic in Antique and Classic Mack Trucks General Discussion
Mack had some large western bus operators, including San Francisco of course, and Portland. I always liked that Volkswagen advertisement. A lot to be said about flattery. . -
Cummins Press Release / January 11, 2016
-
Lawn equipment maker Ariens at odds with Muslims workers
kscarbel2 replied to kscarbel2's topic in Odds and Ends
That is troubling. There's a time and place for everything, and school time is for learning. Western countries are going to regret not revising their thought processes on immigration. The situation of today is FAR different from when their policies were originally formed. -
Owner/Driver / January 21, 2016 Todd Malycha is a big Mack fan, especially the 2005 Titan he drives for Corbet’s Timber Haulage around the pine plantations of Central Queensland. In 2014 Cyclone Marcia carved its way through the Queensland coast, laying acres and acres of pine plantations around Byfield, an hour or so up from Rockhampton. Today, there are around 40 trucks running 24 hours a day, five days a week, salvaging the pine before it rots. Andrew Corbet has nine trucks hauling pine, one of which is a 2005 Mack Titan with an enthusiastic Todd Malycha behind the wheel. The Titan has been recently rebuilt and refurbished in Corbet’s Timber Haulage own workshops. "They just don’t make trucks like this," Todd says. "The Cummins and its 600hp in this Titan are just awesome." Corbet’s trucks are doubled shifted, keeping them running around the clock from Monday to Friday with Todd sharing the Titan with another driver, Barry Merchant. The pine is hauled from Byfield down to the port of Gladstone where the majority is chipped for export. There is a regular "log jam" during school days however, with a curfew taking place around the Byfield School from 6am to 9am and again from 2pm to 4.30pm. "We’ve got two years of work here hauling out millions of tonnes of timber. Each shift you do a trip and a half, so you don’t get bored. It’s a pretty good job!" The fold-up B-double Kennedy trailers were built in 2002 and have since been refurbished. Although Todd is no stranger to hauling logs, he admits operating the Elphinstone fold-up B-double takes some getting used to. "I think I’m going to do some damage but no, they are great, well designed and easy to operate," he says. Todd has driven mainly Kenworths or Volvos over the past 20 years, apart from the occasional Mack, including a Super-Liner out of Mount Gambier. Todd later moved to South Australia’s Riverland district before relocating to Queensland, which is where he’s been for the past couple of years. His career has included road trains, hauling triples to Darwin for ABC Transport and over to Perth for HPS Transport. However, it’s the Titan that maintains Todd’s level of driving enjoyment, with its V8 underneath. "The rig looks great, a little bit of scroll work and a few stickers and it looks a million bucks," he says. "Why drive a new truck when you can drive one as good as this?" Photo gallery - http://www.ownerdriver.com.au/industry-news/1601/salvaging-pine-from-a-cyclones-carnage/
-
Burrumbuttock Hay Runners applauded for heroics
kscarbel2 replied to kscarbel2's topic in Trucking News
Burrumbuttock Hay Runners promise April convoy Australasian Transport News / January 20, 2016 Convoy founder says they will be finishing off the job they started earlier this month Just weeks after organising the transportation of over 5,000 bales of hay to struggling farmers in Queensland, Riverina-based farmer and Burrumbuttock Hay Runners founder Brendan Farrell has announced the job isn’t finished. In a post to the convoy’s Facebook page, Farrell says only half the farmers received hay in the first hay run to Ilfracombe, and another run will be taking place on April 1. "There's 120 truck drivers at the moment screaming ‘let's get this show on the road’," Farrell says. "So, let's do what we do and drop some more hay off." He is even promising a bigger convoy than the 125-truck convoy that travelled the 1,860km journey in January. "It's going to be huge – bigger than the last one, trust me," he says. "So April 1 we will be there and all we're doing is keeping the dream alive." Farrell’s hay convoy, which has run on ten occasions in the last two years, has received a surge of praise over the past fortnight from farmers and concerned members of the community, attention that the founder shrugged off. "People need to realise I’m just a bloke with a truck," Farrell says in an earlier video post. "You don’t have to be famous to help people. "You don’t need to have a million dollars to help people. "You put your hand up and you just get on and do it." While he is currently on a holiday in Fiji, Farrell says he will be organising the next run on his return, creating a committee and allocating area managers to drought-affected zones. For truck drivers, he says they should get in contact but stay patient. For those looking to donate, he says they can send funds to the Rotary Club of Sydney, details of which are on the Facebook page, or to Drought Angels. -
The Engineer / January 20, 2016 UK-based automotive contract engineering firm Ricardo has received two contracts to produce natural gas engines for heavy commercial trucks that would operate under California’s tight emissions environment. The contracts will see Ricardo partnering with the Gas Technology Institute, a US organisation headquartered near Chicago, devoted to energy and environmental technology development. The project aims to develop alternatives to diesel engines for medium and heavy commercial trucks to reduce NOx emissions and improve fuel efficiency. Some funding is coming from the Southern California Gas Company (SoCalGas). In one project, Ricardo is to test two ignition systems that can be used with natural gas-fuelled engines – high-frequency discharge and pulsed nano-plasma – to measure and evaluate their effect on engine performance. The other project is aimed at developing an ultra-low emission engine for class 4-7 medium and heavy duty trucks, whose current diesel engines are in the top ten sources of NOx emissions in the Southern Californian Basin and are projected to remain major polluters even as the current fleet is replaced by newer vehicles meeting the most recent emissions standards, set in 2010. The new engines would produce 90 per cent less NOx than even the best-performing current diesel engines, Ricardo claims, adding that their performance “would approach the regional NOx emissions associated with operating an equivalent all-electric heavy-duty vehicle, when the emissions associated with the electricity production are taken into account.” According to Ricardo president Clive Wooton, “trucks such as these are not as amenable to the type of electrification and hybridization approaches that have been applied very successfully in the passenger car and SUV sector. However, the substitution of diesel with natural gas as a transportation fuel for these classes of vehicle offers some attractive potential benefits in reducing NOx emissions.” Related reading: http://www.arb.ca.gov/msprog/tech/techreport/ng_tech_report.pdf http://www.ricardo.com/en-GB/News--Media/Press-releases/News-releases1/2016/Ricardo-to-help-develop-technology-for-ultra-low-emission-natural-gas-heavy-truck-engines/
-
TATRA PHOENIX – successfully premiered at the 2016 Dakar Rally! Tatra Truck Press Release / January 20, 2016 The crews of the TATRA BUGGYRA RACING team contributed to the thirty-year celebrations of the TATRA brand at the world's toughest long-distance rally with the excellent finishes at the 2016 Dakar Rally. Jaroslav Valtr finished eighth with his Phoenix truck, and Martin Kolomy sixteenth with his Fat Boy. The key goal of the new TATRA PHOENIX vehicle was to finish the race. And to test and tune the truck for the next one. Having switched to the TATRA from Liaz, Jarda Valtr got the feeling soon after the race started that he could let the Phoenix "fly" and battle for the top positions. After the initial "tuning" and some bad luck for the Phoenix, he fought his way from the 33rd starting position to the second ten, and from there repeatedly made a play for the "podium". "I came back after a year's break, and now we have the result of a lifetime. We had problems primarily at the beginning of the race and it cost us an even better finish. The race was fantastic. We showed several times that both the Fat Boy and new Phoenix belong to the absolute best and that our vehicles are ready to fight for the Bedouins," said Valtr. His teammate, Josef Kalina, who stood at the start of the TATRA vehicle with Karel Loprais 30 years ago, added after Stage 13: "It was a perfect stage for our Phoenix. He was flying today! But we had some mistakes in navigation, and it cost us valuable time. But we have another top ten finish as a result and we're defending eighth place overall, which is an excellent outcome." Martin Kolomy strove for the highest positions and turned in a fantastic ride during the whole competition, illustrated by his victory in the 3rd stage, but unfortunately he had bad luck for a moment in the seventh stage when a stone jammed his steering, resulting in the truck crashing into a riverbed bank, causing fairly extensive damage to it. With new TATRA-brand servicing tools and technology on hand, the mechanics of the TATRA BUGGYRA RACING team managed to repair everything. Martin then tested the robustness and resilience of the TATRA 815 Fat Boy vehicle by getting back into the top ten from the depths of the starting field, where he dropped back to due to delays from the crash, and once again he put up a fight for a stage "podium", but finally ended up only in fourth. "This year's Dakar was very hard, because we had an accident and some technical problems. One truck fared better and the other worse, but I'm excited. Both our crews finished and are healthy. It's a marathon contest, difficult to prepare for. The stages were difficult but nice, and I hope that we shall get together here in a year's time again and do even better, maybe get the best possible results. Even after today's stage, I know there is no better brand to start with," the sixteenth-place Martin Kolomy said in praise of his Tatra at the finish line. The TATRA trucks of another Czech team – Bonver Dakar Project – also didn't do too badly with their international crews but were held back in the race by some minor accidents and defects rather than any fundamental technical problem. Arthur Ardavichus from Kazakhstan also had excellent results with an 11th place finish overall. Team boss and driver Tomas Vratny finished in 17th place and handicapped driver Andorran Alberto Llovera in 35th. With a Tatra truck adapted for manual steering, he became the first handicapped truck driver to finish the race and huge thanks go to both him and the whole Bonver Dakar Project team that enabled him to achieve this result and fulfil the TATRA brand's motto – "TATRA takes you further..." Photo gallery - http://www.tatratrucks.com/about-the-company/press-and-media/news/tatra-phoenix-successfully-premiered-at-the-2016-dakar-rally/
-
Lawn equipment maker Ariens at odds with Muslims workers
kscarbel2 replied to kscarbel2's topic in Odds and Ends
Life in a western country, including the United States, is completely different from countries under Islamic Law (Shariah). If one chooses to [legally] immigrate to the United States, then one needs to make a conscious decision about adapting to the American way of life. The U.S. is a global symbol of diversity; however we have norms, just as every country does. You can’t expect to put a square peg into a round hole. Live in the countries where your beliefs fit in.- 21 replies
-
- 10
-
-
Daimler Investing $22.7 Million to Expand Facilities at FCCC
kscarbel2 replied to kscarbel2's topic in Trucking News
Daimler invests $22.7M to expand Freightliner Custom Chassis Fleet Owner / January 20, 2016 Daimler Trucks North America (DTNA) announced it will invest $22.7 million in Freightliner Custom Chassis Corp (FCCC) to expand facilities and improve operations in South Carolina. “The investment will positively impact a number of key business operations for FCCC, including the construction of a new logistics center, as well as expansions of the current office building, employee parking lot, completed chassis parking and loading/delivery operations,” according to DTNA. Daimler added that the investment will drive implementation of a new line side delivery process, which will utilize nearly 60% more component kitting. “The investment shows our commitment to the employees in Gaffney, our customers and to the future of FCCC,” said David Carson, president, Freightliner Custom Chassis Corp. “We will continue to build the best chassis with the best features and customer support, and this investment will ensure we are well positioned for future growth. I’d like to thank the officials from the state of South Carolina and Cherokee County for their help in making this project possible.” According to DTNA, in addition to the logistical and process improvements, the investment will provide an expansion to the current office building, which will provide a 25% increase in personal work stations, increase the training room capacity from 25 to 100, double the amount of available team work space and increase the cafeteria capacity from 15 to 119. “The leadership team at DTNA wants to ensure we have the tools and facilities we need to continue delivering the best chassis for all of our customers across all of our product lines,” Carson added. -
Fleet Owner / January 20, 2016 Dual-stage design streamlines replacement process, OEM says. Ford is introducing a new “dual-stage” replacement turbocharger for vehicles equipped with its 6.4-liter Power Stroke diesel engine, shortening the replacement process and lowering costs as well. “The new dual-stage turbocharger allows installers to provide one repair at a lower cost that also includes peripheral parts like an oil supply line and an installation kit that would otherwise need to be purchased separately,” said Dan Goering, Ford’s diesel product manager, in a statement. “Customers and installers now have options in terms of replacement, and the dual-stage choice definitely saves time and money.” He added that replacing the high- and low-pressure turbochargers on the 6.4-liter Power Stroke used to be a two-step process with two distinct costs. Thus this new dual-stage turbocharger creates a one-stop option addressing the need to replace both turbochargers at the same time, Goering noted. Ford pointed out that recent analysis shows that 33% of high pressure turbocharger repairs also include a low pressure turbocharger. Moreover, replacements of just the high or low turbocharger may soon be followed by replacement of the other – causing inefficiencies, especially for fleet vehicles when time off of the road is critical. On top of that, the OEM said its new the dual-stage unit comes fully assembled, saving labor costs while still coming in at a lower price. Customers can order the dual-stage system from their Powertrain Distributor or Ford dealer using part number 8C3Z-6K682-CRM for 6.4-liter Power Stroke engines 2008, 2009 and 2010 Ford F-250s through F-550s.
-
Trailer/Body Builders / January 20, 2016 Daimler Trucks North America (DTNA) announced the investment of $22.7 million in Freightliner Custom Chassis Corp (FCCC) to expand facilities and improve operations in Gaffney, South Carolina. The investment will positively impact a number of key business operations for FCCC, including the construction of a new logistics center, as well as expansions of the current office building, employee parking lot, completed chassis parking and loading/delivery operations. In addition, the investment will drive implementation of a new line side delivery process which will utilize nearly 60 percent more component kitting. “The investment shows our commitment to the employees in Gaffney, our customers and to the future of FCCC,” said David Carson, president, Freightliner Custom Chassis Corp. “We will continue to build the best chassis with the best features and customer support, and this investment will ensure we are well positioned for future growth. I’d like to thank the officials from the state of South Carolina and Cherokee County for their help in making this project possible.” In addition to the logistical and process improvements, the investment will provide an expansion to the current office building, which will provide a 25 percent increase in personal work stations, increase the training room capacity from 25 to 100, double the amount of available team work space and increase the cafeteria capacity from 15 to 119. “The leadership team at DTNA wants to ensure we have the tools and facilities we need to continue delivering the best chassis for all of our customers across all of our product lines,” Carson added.
-
Associated Press / January 20, 2016 After refusing to allow its Muslim workers special prayer breaks, Wisconsin lawnmower manufacturer Ariens was forced to act in order to prevent a $1 million loss for the company each year. Fifty three Muslim employees have walked off the job, claiming Ariens changed work practices which insulted their devout faith. Dan Ariens, chairman and CEO of Ariens, a company which makes lawn mowers and snow blowers, says he will refuse to allow the disgruntled employees back to work unless they accept his decision to ban extra prayer breaks. Ariens, whose family set up the business more than 80 years ago, denies he was being insensitive to their religious needs and warns they may lose their jobs if they do not accept his terms. He says the company’s non-Muslim workers complained to him about the exceptional time given to the 53 Islamic staff to be able to meet their religious obligations during working hours. “It just throws 800 people in disarray. Think of the unfairness. Everybody gets two ten minute breaks, but some additional 50 people are getting more breaks of maybe five or twenty minutes, ‘ said Ariens. The banned Muslim workers now claim they were technically forced out of their jobs and insulted by the company's management. An Imam who leads prays at his Mosque with many of the workers said Ariens, if allowed, was setting a dangerous precedent which might lead businesses around the US to review the procedure of allowing Muslims time during work to pray. Ariens employs 2,000 people including 800 at its Brillion, Wisconsin plant. The company expects its Muslim employees to limit their prayer time to the two ten minute breaks allowed to all employees working eight hour shifts. But the 53 Muslims, mostly from Somalia and arrived at the plant last summer, say they cannot ignore the religious requirements which specifies the times that they must turn towards Mecca and prostrate to Allah. They have to have clean bodies and carry out the prayers at daybreak, noon, mid-afternoon, sunset and evening and each prayer lasts five minutes. But Ariens says some prayer breaks took key workers away from production assembly lines for up to twenty minutes. Ariens, speaking in the boardroom of the company's Wisconsin headquarters, said: “We know those breaks aren't always (taking) five minutes for prayer because you can't physically walk to one end of the plant. It is 365,000 square feet so it may take you ten, fifteen and we know in some cases twenty minutes. If they were to stay with those five minute breaks, it would cost us about a million dollars per year. Let's say an assembly line has ten people on it, if two walk off the job, the other eight are standing there because they work in a sequence. It is impossible and it is not a free for all. We work as a team.” He insists the resentful employees, who have walked out and have until January 25 to return to work or face losing their jobs, knew from the day they joined of the company's allotted break times. “I am not a Muslim. I am not aware of the Muslim prayer times. I know that there is a faith. But I am not aware of the practice. But I do know that they were made aware of break times when they joined the company,” said Ariens. Ariens, who is a Catholic, was asked why he wasn't aware that Muslims were required to pray five times a day. He said: 'Do you know how many rosaries I do a day?' One Muslim worker, Ibrahim Mehammed, 32, claims he and his fellow Muslims are being forced to choose between work and faith. “They are not respecting our values and religion. The Koran says we have to pray five times a day and at what times this has to be done. These prayers are very important to us as we have to fully respect Allah and when they refuse us to pray at these times, we have no choice but to lose our jobs. Since most of us arrived in Brillion last summer, we have been treated very well and we get on with our non Muslim colleagues. They would step in for us when we went to pray and it was all OK. Nobody had any trouble at all until the company called us together last week and told us we couldn't pray anymore when we had to. It is crazy to ask us to pray out of the times that we have to. It wouldn't mean anything to us or to God. Now they have given us letters which tell us where to get help with unemployment. As far as I am concerned, I have been fired from my job over my religion,” Mehammed said. His colleague Dhar Mahed, 37, says, “We are hard workers and we get on very well with everybody. Nobody complained to us about our prayers. People take breaks to go to the bathroom and nobody says anything about that. They can go as many times as they like. It is a shame that we are being put away from our jobs only because we are sincere and respectful Muslims and simply want to pray.” The problem began soon after the influx of Somalian Muslims last summer who found work at Ariens through an employment fair and applied online. Until that time, there were only a handful of Muslim employees leaving the production lines to pray. But with over 50 additional Muslim workers demanding time to pray during work time, Ariens management said the situation became extremely difficult and they were not expecting new staff to make such demands. One of the longest serving Islamic workers says some of his fellow Muslims were using the prayers as an excuse to avoid work. Bashir Mahamed, 67, who has worked at Ariens for nearly ten years, says: 'There was no problem when there was just three or four of us. “But when these large numbers came, I could see that the work was being affected. I know that some of the people were taking the time not to pray as they were not really practicing Muslims. But I am very happy with my job and I will carry on working there, says Mahamed. His Imam Mohamed Abdelazim of the Appleton Mosque, however, disagrees with him and says the workers took time only to pray. “They have to pray at the designated times. The prayers are called Fajr, Dhuhr, Asr, Maghrib and Isha. If a Muslim does these prayers he is rewarded by God, but if he does them at times different from the Muslim calendar, then his rewards are less and less. They have to be on time. It is not good to try and tell these Muslim brothers and sisters to pray during their lunch breaks as these prayers will not be correct and acceptable,” says the Imam. Another Imam Hassan Abdi of the Green Bays Mosque, claims: “This company has changed its policy towards Muslims after employing them. We do not understand why. 'Most of these brothers and sisters worship at my mosque and I believe they are in this situation because their employer wants to get rid of its Muslim workers. The times to pray are in the Koran. They have to do it. If this company does this, other bosses around America could see this as an excuse to get rid of its employees. This is a dangerous situation for us in this country.” But Ariens denies he is using the controversy over prayers as an excuse and says he is angered over claims on social media that his company's actions amounted to racism. He says: 'They don't know us and they are baseless and wrong. They do not know us as a family business that has been here eighty years. 'We have all kind of diversity here in North East Wisconsin and we hire anybody who wants to come and work and be part of this family. We are not going to discriminate not hiring someone based on their faith. We don't do research to say that we shouldn't hire them because they are Somali or because they are Irish Catholics. That is discrimination. We are absolutely not discriminating because we are saying that we have seen they have relocated and looking for a job and we have a job open... let's see if we can put those two things together,” says Ariens. He insists the latest batch of Muslim workers have been treated fairly and professionally. 'We put them through orientation and training. So these 53... we have invested in them and trained them. We have brought them some skills and they have become good manufacturers and we would like this not to cause them to voluntarily leave us and quit.' He said if the 53 workers left their jobs, the replacements could be Muslims as long as they understood there were only two ten minute break times. “I will feel bad if they leave. We are a business... we are not a non-profit business. We are as family and a team. No one is fired.” The CEO estimates $1 million would be lost per year if the prayers were allowed to continue when the workers wanted. The Equal Employment Opportunity Commission states that employers do not have to accommodate a religious practice if it causes 'undue hardship' to the company by decreasing 'workplace efficiency. The dispute has to be resolved by Sunday as that is the deadline Ariens has laid down for a return to work, otherwise the 53 will be deemed to have left their jobs on their own accord.
-
NHTSA chief vows action this year on cybersecurity
kscarbel2 replied to kscarbel2's topic in Trucking News
This news relates to the evolving nature of heavy trucks. The telematics systems now being used by the truckmakers, which allow ECU updates via WiFi networks, are vulnerable. Most people fail to keep their router firmware updated, making it easily vulnerable to hackers. And even when updated, WiFi by nature is still vulnerable. After that, the truckmakers are talking about over-the-air updates through a cellular network, another easily hackable situation. -
Automotive News / January 19, 2016 The nation’s top auto safety regulator said his agency will take action this year to address automotive cybersecurity issues, as the spread of connectivity technologies threatens to expose vehicles to new paths of attack. The National Highway Traffic Safety Administration (NHTSA) currently lacks regulations for the security protocols governing the roughly 100 million lines of software code used to control many functions in modern cars [and commercial trucks]. As Wi-fi hotspots, satellite radio and other network connections to vehicles become more common, NHTSA administrator Mark Rosekind said, the agency must define its role in how the security of those systems should be managed, and what tools it needs to ensure the safety of connected vehicle systems. Rosekind says the effort has the backing of Transportation Secretary Anthony Foxx, though it’s still unclear what type of action the agency will take. “I don’t know if there’s going to be regulation or standards, or what that’s going to look like,” Rosekind said on the sidelines of a NHTSA cybersecurity event today, “but I don’t think there’s any question that we have to get action on cybersecurity this year.” Auto cybersecurity was thrust into the spotlight last summer when researchers Charlie Miller and Chris Valasek, working with a magazine reporter, exploited a network vulnerability in the infotainment system of a Jeep Cherokee to demonstrate that they could remotely take control of functions such as its steering and brakes. Automakers fear that NHTSA regulations for cybersecurity could take years to formulate, and may stifle innovation in the meantime. At the same time, they don’t dispute that security is a critical issue as vehicles become increasingly connected to the Internet, and as autonomous driving technologies enter the marketplace. Potential threats At today's meeting, panelists identified a variety of potential threats, including so-called ransomware, or malicious software designed to extort money from vehicle owners by crippling the vehicle’s software controls until a ransom is paid. Another topic of discussion was how to patch vulnerabilities in vehicle infotainment systems -- the gateway used in Miller and Valasek’s Jeep hack -- and whether features should be disabled until security updates can be installed. Rosekind said NHTSA organized the daylong event to bring together automakers, suppliers, government officials and researchers, in part to help define the agency’s role in overseeing auto cybersecurity. “Clearly we are the agency that could create mandates if they were needed,” he said. Safety-critical issues He acknowledged the concerns about barriers to innovation but said safety was a paramount concern. For safety-critical issues where industry-wide adoption is required, “that’s where you need regulation,” he said. “In some areas of safety, you need 100 percent adoption.”
-
More Air Force drones are crashing than ever as new problems emerge The Washington Post / January 19, 2015 A record number of Air Force drones crashed in major accidents last year, documents show, straining the U.S. military’s fleet of robotic aircraft when it is in more demand than ever for counterterrorism missions in an expanding array of war zones. Driving the increase was a mysterious surge in mishaps involving the Air Force’s newest and most advanced “hunter-killer” drone, the Reaper, which has become the Pentagon’s favored weapon for conducting surveillance and airstrikes against the Islamic State, al-Qaeda and other militant groups. The Reaper has been bedeviled by a rash of sudden electrical failures that have caused the 21/2-ton drone to lose power and drop from the sky, according to accident-investigation documents obtained under the Freedom of Information Act. Investigators have traced the problem to a faulty starter-generator, but have been unable to pinpoint why it goes haywire or devise a permanent fix. All told, 20 large Air Force drones were destroyed or sustained at least $2 million in damage in accidents last year, the worst annual toll ever, according to a Washington Post investigation. The Pentagon has shrouded the extent of the problem and kept details of most of the crashes a secret. The aircraft losses pose another challenge for the Air Force as it struggles to provide sufficient drone coverage for counterterrorism operations in Iraq, Syria, Afghanistan, Somalia, Yemen, Libya, Mali and Cameroon, among other countries. Despite a surge in requests from field commanders, the Air Force last year had to curtail its drone combat missions by 8 percent because of an acute shortage of pilots for the remote-controlled aircraft. Things have gotten so bad that the Air Force is offering retention bonuses of up to $125,000 to its drone pilots, who have long complained of overwork. The Air Force also has contracted out more drone missions to private companies to meet what one general called “a virtually insatiable appetite” from military commanders for airborne surveillance. While Air Force leaders have publicly bemoaned a lack of personnel and resources, they have said little about the high number of drone crashes, a long-standing vulnerability that worsened substantially last year. Ten Reapers were badly damaged or destroyed in 2015, at least twice as many as in any previous year, according to Air Force safety data. The Reaper’s mishap rate — the number of major crashes per 100,000 hours flown — more than doubled compared with 2014. The aircraft, when fully equipped, cost about $14 million each to replace. The Air Force’s other primary drone model, the Predator, also suffered heavy casualties. An older and less capable version of the Reaper, the Predator was involved in 10 major accidents last year. That’s the most since 2011, when the U.S. military was simultaneously surging troops into Afghanistan and withdrawing ground forces from Iraq. Although the Defense Department has a policy to disclose all major aircraft mishaps, it did not publicly report half of the 20 Reaper and Predator accidents last year. In five other cases, U.S. military officials provided confirmation only after local authorities reported the crashes or enemy fighters posted photos of the wreckage on social media. According to the military, only one drone was downed by hostile forces: a Predator that was hit by Syrian air defenses near Latakia on March 17. All but one of the 20 Air Force drone accidents last year occurred overseas. Six drones crashed in Afghanistan. Four crashed in the Horn of Africa, near a U.S. military base in Djibouti. Three crashed in Iraq. There were also crashes in Kuwait, Turkey, Syria and Libya. In two cases, Air Force officials would not identify the country where the mishaps occurred. In addition to the Air Force, the Army operates its own drone fleet. It is preparing to expand the number of combat missions it flies to help compensate for the Air Force’s cutbacks. Last year, the Army reported four major drone crashes, each involving the Gray Eagle — a model identical to the Predator. Three of the Army’s accidents occurred in Afghanistan. One happened in Iraq. Although the military’s drone programs are largely unclassified, the Obama administration rarely discusses details of the key role they fill in its counterterrorism strategy. The CIA runs its own drone operations on a covert basis, and the secrecy surrounding those missions often seeps into the Pentagon. Lt. Gen. Robert P. Otto, the Air Force’s deputy chief of staff for intelligence and surveillance programs, acknowledged in an interview that there has been a spike in Reaper accidents. Many cases remain under investigation, but Otto and other Air Force officials blamed the Reaper’s flawed starter-generator for causing at least six major crashes since December 2014. “We’re looking closely at that to determine what is the core issue there,” Otto said. Although the drone pilot shortage has compelled the Air Force to reduce the number of combat missions, Otto said the aircraft mishaps have not forced additional cuts. The Air Force has enough replacement drones on hand, he said, and already had orders in place to buy dozens more Reapers over the next few years. “Any impact to operations has been negligible to barely noticeable,” he said. Field commanders, however, have long complained of a drone deficit. In March, the four-star commanders of U.S. forces in the Middle East and Africa both told Congress that the Pentagon has provided less than one-quarter of the drones, other aircraft and satellites that they need for reconnaissance and surveillance missions. “The Predator has been our most effective weapon in our campaign against the global jihadists,” said Michael G. Vickers, the Pentagon’s former top civilian intelligence official, at a House Armed Services Committee hearing Jan. 12. But he cautioned that the size of the drone fleet “will remain a critical limiting factor in the conduct of our campaign.” Drones going ‘stupid’ Military drones have been dogged by persistent safety and reliability problems since the first Predator was deployed to the Balkans on a combat mission two decades ago. Of the 269 Predators purchased by the Air Force since then, about half have been destroyed or badly damaged in accidents, records show. Air Force officials describe the Predator as an experimental aircraft that was rushed into war zones, particularly after the U.S.-led invasion of Afghanistan in 2001. They say it has lasted much longer than expected and that, at a cost of$4 million apiece, is relatively expendable in the event of a crash. The Air Force has about 140 Predators left and plans to retire them all by 2018. They are gradually being replaced by the Reaper. Introduced in 2007, the Reaper can fly twice as far as the Predator and carry more bombs and missiles. Until recently, it also had a much better safety record. Over the past three years, however, some production models of the Reaper have been hobbled by an outbreak of electrical failures. Investigators and engineers have traced the problem to the starter-generator. It powers the drone but is prone to conking out, for reasons that remain unclear. The Reaper carries an emergency battery backup system. But the batteries last only for about one hour. If a malfunctioning drone needs more time than that to reach an airfield, it is in trouble. In such emergencies, the drone pilot usually has no choice but to intentionally crash the aircraft in a remote area, such as a mountainside or a waterway, to avoid striking people on the ground. No one has died in a military drone accident, though many catastrophes have been narrowly averted, documents show. “Once the battery’s gone, the airplane goes stupid and you lose it,” said Col. Brandon Baker, chief of the Air Force’s remotely piloted aircraft capabilities division. “Quite frankly, we don’t have the root cause ironed out just yet.” The Reaper and the Predator are both manufactured by General Atomics Aeronautical Systems, a San Diego-based defense contractor. In addition to the Air Force, other customers who have purchased the Reaper include the Department of Homeland Security, NASA, and the British, French and Italian armed forces. The CIA also flies Reapers. General Atomics officials declined requests for an interview or to provide data on the Reaper’s history of starter-generator failures. In an emailed statement, General Atomics spokeswoman Kimberly Kasitz said the firm “stands behind the proven reliability” of the Reaper. She added that Reapers have recorded more than 2.2 million flight hours and have “been very effective for multiple customers.” The Reaper’s starter-generator is built by Skurka Aerospace of Camarillo, Calif. Skurka executives referred requests for comment to their parent corporation, Transdigm Group of Cleveland. A Transdigm spokeswoman did not respond to phone calls or emails. Averting disaster Government agencies other than the Pentagon have also run into problems with their Reapers. Shortly before midnight Jan. 27, 2014, an unarmed Reaper was flying a surveillance mission near San Diego for U.S. Customs and Border Protection. Suddenly, an alarm sounded, signaling that the starter-generator had stopped working. The crew flying the drone from a remote-control ground station in Corpus Christi, Tex., inputted commands to restart the generator, but their attempt failed. The pilot made quick calculations and concluded that the Reaper lacked enough battery power to make it back to its launch point, at Fort Huachuca, Ariz., according to an aircraft accident report by Customs and Border Protection. Worried that the Reaper might otherwise crash into a heavily populated part of Southern California, the pilot commanded the drone to head out to sea, where it was ditched about 23 miles west of Point Loma, Calif. The drone sank about 4,200 feet to the ocean floor. Ten days later, most of the wreckage, including the intact starter-generator, was recovered from the depths by a Navy salvage team. According to the accident investigation report, it was the 18th time in nine months that a starter-generator had failed on a Reaper. Disaster was averted in most cases, but in three of the incidents, the drone crashed. Working with engineers from General Atomics, investigators identified three parts of the starter-generator that were susceptible to breakdowns. But they couldn’t figure out why they were failing. No pattern was apparent. Older units had failed, but so had brand-new ones. There was no correlation with operating locations or conditions. The Customs and Border Protection investigation blamed an “unknown factor” that was “likely external.” The report noted that, unlike most aircraft, the Reaper lacked a backup, or redundant, power supply system. Calling it a “design weakness,” the report recommended that Reapers be equipped with a permanent backup electrical supply. Two days after the crash near San Diego, General Atomics issued an alert bulletin to its customers, advising them to limit “non-essential” Reaper operations to keep the drones within one hour’s flight of an air base in case of an emergency. The bulletin, however, did not apply to combat missions. Crashes pile up General Atomics engineers made little headway in identifying the mechanical gremlin that was plaguing the starter-generators. Meanwhile, Reapers kept crashing. On Dec. 12, 2014, a Reaper armed with missiles and bombs experienced a starter-generator failure about 90 minutes after it took off from Kandahar Air Base in Afghanistan. As the batteries drained, the crew intentionally flew the drone into a mountain. The wreckage was not recovered. “I thought it was a very prudent place to ditch it, onto a high mountain top,” the unidentified mission crew commander told Air Force investigators, according to the accident-investigation report. “Our deal is we try to do it into high mountain tops.” Less than two months later, on Feb. 4, 2015, an Air Force Reaper had to cut short a surveillance mission over Somalia when its starter-generator died. The flight crew tried to rush the drone back to its base in Djibouti. But with about 30 miles to go, the battery ran out and the Reaper was ditched in the sea, according to the Air Force’s accident investigation report. In an appendix to the report, General Atomics noted that it had completed the development of a “more robust” starter-generator in response to the string of mishaps. The appendix, which was heavily redacted, did not give further details. In March, the Air Force’s program manager for its Reaper fleet filed a report with the Pentagon noting that there had been “a dramatic increase” in starter-generator failures since 2013. Col. William S. Leister informed Pentagon officials that investigators from the Air Force, General Atomics and Skurka had investigated the problem for more than a year. The team, he said, had identified “numerous manufacturing quality issues” yet had been unable to determine the exact cause of the failures. “But, I am pleased to report that we may have light at the end of this dark tunnel,” he added, promising unspecified “corrective actions in the very near term.” He declined to comment further for this article. Other Air Force officials said the service began installing a secondary generator on its Reapers in July that can provide up to 10 extra hours of electricity in case the first one fails. The Air Force determined that 60 Reapers in its fleet were carrying the buggy starter-generators. So far, the new backup part has been installed on 47 of those aircraft, according to Baker, the colonel in charge of the drone capabilities division. Since then, Baker said, there have been 17 “saves” — or incidents in which the primary generator failed mid-flight. In each case, he added, the backup generator kicked in and the drone was able to land safely. .
-
Reuters / January 19, 2015 China National Heavy Truck Company, also known as CNHTC and Sinotruk, saw its export truck sales rise 16.6 percent in 2015, despite a sluggish global economy, the company said Tuesday. The Shandong, China-based truck manufacturer received export orders for over 40,000 heavy trucks in 2015, making it China’s largest exporter of commercial vehicles for the 11th consecutive year. Company officials said burgeoning Southeast Asian and African markets contributed to the growth. The Hong Kong-listed truckmaker has six overseas assembly plants and representation in 40 countries. .
-
Date: March 1-4 Location: Indianapolis Presently known major participants: Cummins Ford Commercial Vehicles International Kenworth Mack Mitubishi Fuso Ram (Dodge) Commercial Website: http://www.ntea.com/worktruckshow/
-
MAN Truck & Bus Press Release / January 19, 2016 MAN showcases integrated solutions for the construction sector at BAUMA* 2016 MAN will use five exhibits in hall B4, stand 225, to showcase its expertise in the construction sector. The display on the stand will include a crane tipper from the TGL series, a two-axle MAN TGS with HydroDrive as a semitrailer tractor, a payload optimized truck mixer on a four-axle MAN TGS, a MAN TGS designed for 33 tonnes for the mining industry and a three-axle MAN TGX tipper with the new 560 hp D38 engine. Four other vehicles will also be located in an open space in front of hall B4 at the exit next to the stand. Here, MAN plans to exhibit a MAN TGX 41.640 heavy-duty semitrailer tractor with the D38 engine, a five-axle MAN TGS designed for a gross permitted weight of 50 tonnes, a MAN TGS with triple-axle arrangement provided as standard, and a MAN TGM in all-wheel drive version. The needs of the user provide the focus for the MAN product range - true to the trade fair motto, “You can count on MAN”. MAN's sector-specific focus is evident in many areas, for example in the choice of three possible all-wheel drive technology variants. The optional all-wheel drive is the premier choice for occasional driving on more challenging terrain. The permanent all-wheel drive is ideal for use where a high-level of traction is often required as well as under widely varying road holding conditions. The MAN HydroDrive, an optional hydrostatic drive in the front axle, is an ideal addition if the vehicle travels predominately on sealed road surfaces and only occasionally needs additional traction. A success story continues: MAN HydroDrive The launch of the MAN Hydrodrive in 2005 represented the introduction by MAN of a new drive technology variant on to the market. The technical solution of a hydrostatically driven front axle to increase traction when required and to deliver a strong braking effect on steep offroad slopes was welcomed in many sectors with great interest. HydroDrive is thus available on the market in a wide range of drive configurations for two-, three- and four-axle vehicles. MAN has continued to develop this system and improve its operation in practice for users. The routing of the hydraulic lines has been optimised and the clearance around the wheels increased making larger rim and tyre widths possible - even with tyre chains attached. MAN is to announce an extension to its range of drive configurations at bauma 2016. MAN HydroDrive in combination with an automated gearbox is likely to be available to order from IAA 2016 onwards. A plus for payload: new light hypoid tandem axle At bauma 2016, MAN is to launch a new light hypoid tandem axle unit for payload-sensitive transport tasks. In comparison to fitting a planetary axle, this weighs in at approximately 280 kilogrammes lighter. Compared to normal hypoid axles currently available with a 13-tonne load capacity, a weight advantage of 180 kilogrammes is achieved. In terms of truck mixers, this means for example that it is possible to transport 180 kilogrammes more concrete or water. The requirement for the use of thermo-insulated bodies when transporting asphalt adds additional weight. The operator is now able to compensate for this payload loss with a lighter axle unit. This tandem axle unit also has other advantages besides the payload argument: Slightly less diesel is used compared to vehicles fitted with planetary axles. In a direct comparison of hypoid axles, the new axle construction - designed for a payload of 11.5 tonnes - also offers additional ground clearance of approximately four centimetres. This means that, also with hypoid axles, MAN now meets the authorisation criteria for an offroad vehicle (N3G) of medium-high design height and with 315/80 R22.5 tyres. The new axle unit is available for vehicles up to 480 hp in normal height design for leaf-leaf and air-leaf suspension versions of the TGX 6x4, TGS 6x4 and 8x4. This also includes the TGM in 6x4 drive configuration. The TGX 6x4 and TGS 6x4 and 8x4 also benefit from this equipment alternative in the medium height version with leaf-leaf suspension. Construction flagship: the MAN TGX with D38 engine MAN is showcasing the powerful D38 engine in the TGX series for the first time at bauma. This combination represents the perfect vehicle for heavy-duty traction operation. With high engine power over 500 hp, you can transport heavy loads and also achieve high average speeds. Typical applications include tilting articulated trains or 6x4 tippers frequently used with trailers, as well as heavy-duty roll-off skip loaders. In construction traffic, for example, if low loader trailers with heavy-duty construction machines need to be pulled, then the TGX D38 with 520 and 560 hp can move up to a gross train weight of 120 tonnes with ease - depending on the driveline design. In line with sector requirement, MAN is adding the TGX D38 in normal as well as in medium design heights and with tough steel bumpers to the product range. The two-stage turbochargers characteristic of MAN engines means the 6-cylinder in-line engine with 15.256 ccm displacement reaches its nominal torque of 2700 Nm at 930 rpm. The full torque can also be used in a wide torque range of 930 to 1350 rpm. This means that in traction applications, this top-of-the-range model draws upon its great tractive power at low speeds, changes gear at an early stage and keeps the engine torque high in high gears. In summer 2015, MAN switched the TGX D38 series over to the new TipMatic TX gearbox generation. Its direct-drive version is designed for the high torque of 2500 to 2700 Nm produced by the D38 engines. This TX gearbox provides the customer with a number of convenience functions. The following functions from the catalogue are particularly suited for use in the construction industry. Gradient sensor: Thanks to the integrated gradient sensor, the TGX D38 takes the current topography into account when selecting a gear. The driveline always finds the right gear for moving off – whether driving uphill, with an empty vehicle or with full loads. Rocking free: On a snow-covered carriageway for example, or on lightly compressed ground on construction sites, this function on the TGX D38 makes it easier for trucks which are stuck to pull away. If the rocking free function is activated, the clutch opens very quickly, so long as the driver has lifted off the accelerator. If the accelerator is pressed again the clutch closes, allowing the driver to carefully rock the vehicle free. A suitable gear is selected automatically here in order to reduce the torque to the drive wheels and thus avoid wheel spin. Manoeuvring feature: The interaction between the accelerator position and clutch controls has been designed to function even more smoothly so that the driver can manoeuvre more accurately at the loading ramp or in confined construction sites.The aim of other functions available on the TipMatic TX gearbox is rather fuel saving. They therefore contribute positively in terms of the TCO of the MAN TGX D38. The new EfficientCruise GPS cruise control with EfficientRoll “sailing” function were brought into this series along with the TipMatic TX. The combination of both factors provides potential savings. The system utilizes the 3D map material of the terrain to anticipate the course taken by the road and adapts the speed accordingly. At the same time, EfficientCruise anticipates gear selection and shifts down into the appropriate gear before uphill sections. The aim is to manage the uphill section without tractive force interruption. For short inclines, the vehicle completely prevents downshifts if possible. With the knowledge of the topography of the course of the road ahead, the vehicle shifts up a gear at an early stage if this is likely to have a positive effect in fuel saving. This is where the speed shifting functions play their part. Thanks to the specific coordination of engine, clutch and gearbox control, it shifts even more quickly between the three highest gears – 10th, 11th and 12th. This means, for example, that the gearbox can shift down more quickly when going uphill and the torque for tractive force interruption is shortened. This in turn means that greater momentum is maintained, saving on the vehicle's fuel. The Idle Speed Driving function uses the high torque of the 15.2 litre engine at low speeds which provides greater comfort when driving slowly and saves fuel. This is particularly practical in stop-go traffic or when coasting up to a roundabout. In such situations, the vehicle will continue to move forward with the engine at idling speed and the clutch closed, as long as the driver does not brake. For the heavy load: MAN TGX heavy-duty transporter The MAN TGX with D38 engine provides top performance for heavy-duty transport. The four-axle MAN TGX 41.640 8x4/4 combines the most powerful version of the D38 engine and the MAN TipMatic TX with the standard converter-clutch unit. Thanks to the strong torque of 3000 Nm, even heavy-duty transport of 250 tonnes can be moved smoothly and powerfully. The converter-clutch unit allows for particularly precise shunting in tight spaces, on inclines and with heavy loads. The launch of the MAN TGX D38 was the reason to extend the range of models in the heavy-duty transport segment. As regards cabs, there is a choice between all widths XL, XLX and XXL, and now also right-hand drive ex-works. Important for heavy-duty transport operators: the wheelbases on the new Euro 6 version with the D38 engine are the same as the current Euro 5 design with the V8 engine. This means that the cornering characteristics of the towing vehicle and the connected trailer or semitrailer remain the same. The existing reports continue to be valid without alteration. In addition to the premium 640 hp class, MAN is adding further models to the product range for heavy-duty transport. Gross train weights of up to 180 tonnes are possible with the 560 HP and 2700 Nm D38 engine. Tailored to the sector in every respect: partially raised exhaust system MAN offers four-axle chassis from the TGS series with a two-part exhaust system. The diesel particulate filter is fitted between both front axles, and the SCR-cat is positioned on a frame behind the cab. The extension to the variant range is new for bauma 2016: This version is now also available with the 8x4 drive in combination with the longer L and LX cabs. It has so far only been offered with the M cab in drive configurations 8x4, 8x6, 8x8 and 8x6H. The advantages of this arrangement are the avoidance of dust turbulence by means of an exhaust tailpipe which discharges downwards, and the increased space provided in the frame between the second and third axles. This free space can be used for a larger fuel tank or for additions needed by the body. Alternatively, a vehicle with a shorter wheelbase may be chosen to increase manoeuvrability. This emission control system configuration is also available for the standard five-axle, created by attaching an 8x4 to a steered trailing axle. A tough operator in mining: MAN TGS WorldWide For mining and gravel extraction operations, MAN offers the tough and resilient MAN TGS chassis from its WorldWide product family in markets outside Europe. The vehicles are optimised to meet sector requirements: The tandem axle unit on the MAN TGS 33.480 6x6 BB - an exhibit at bauma - now has a longer wheelbase of 1500 millimetres. This means that large format 16 R 20 tyres can be fitted. If the ground conditions require them, 24 R 20.5 format tyres also fit on the tippers. The MAN TGS dumper truck, designed for a gross permitted weight of 33 tonnes, is therefore ideal as an alternative to the articulated dumper which is significantly more expensive to purchase. The MAN TGS WorldWide, designed by the Munich based commercial vehicle manufacturer, represents a truck to cope with challenging road situations as well as extreme climatic conditions such as icy temperatures, snow and extreme heat. The heat retention function, which remains active in neutral, has proven itself in Arctic climatic regions and in frosty winters. It ensures operational capability of the vehicle in temperatures of up to minus 40°C. The MAN TGS 40.540 6x6 BBS from the TGS WorldWide series is available for the toughest of transportation tasks. The combination of the three-axle towing vehicle with 540 hp engine, MAN TipMatic automated gearbox with converter-clutch unit (WSK), leaf-sprung planetary axle and additional radiators for engine, gearbox, WSK and transfer case is ideal for gross train weights of up to 250 tonnes at maximum traction. This vehicle is designed for worldwide operations. It is available as both a left and right-hand drive vehicle and also in emission categories Euro 4 and Euro 5. Air intake as well as exhaust tailpipe are raised for rough operating conditions; it has a steel bumper and tyre formats 325/95 R24 and 14.00 R20 may be selected. Heavy duty equipment ex-works is a tradition at MAN. Components such as two-stage trailer hydraulics, register coupling, heavy-duty trailer coupling at normal and low mounting positions, sliding device for fifth-wheel coupling and support plate for swan neck can of course also be supplied by MAN with this towing machine. The Euro 5 exhaust classification is increasingly gaining in importance in markets outside Europe. MAN is therefore introducing common rail engines to the TGS Worldwide series from the D20 and D26 series for the first time in this exhaust classification. These come from the D20 engine series with 320, 360, 400, and 440 hp. The D26 covers the 480 hp and 540 hp versions. All the engines are 6 cylinder in line engines. MAN image database - http://bildarchiv.man.de/index.php/main?level=0&catId=11651&mainCatId=530&catName=bauma+2016〈=en * Held every three years in Munich, Germany, BAUMA (International Trade Fair for Construction Machinery, Building Material Machines, Mining Machines, Construction Vehicles and Construction Equipment) is the world's largest trade fair in the construction industry.
BigMackTrucks.com
BigMackTrucks.com is a support forum for antique, classic and modern Mack Trucks! The forum is owned and maintained by Watt's Truck Center, Inc. an independent, full service Mack dealer. The forums are not affiliated with Mack Trucks, Inc.
Our Vendors and Advertisers
Thank you for your support!