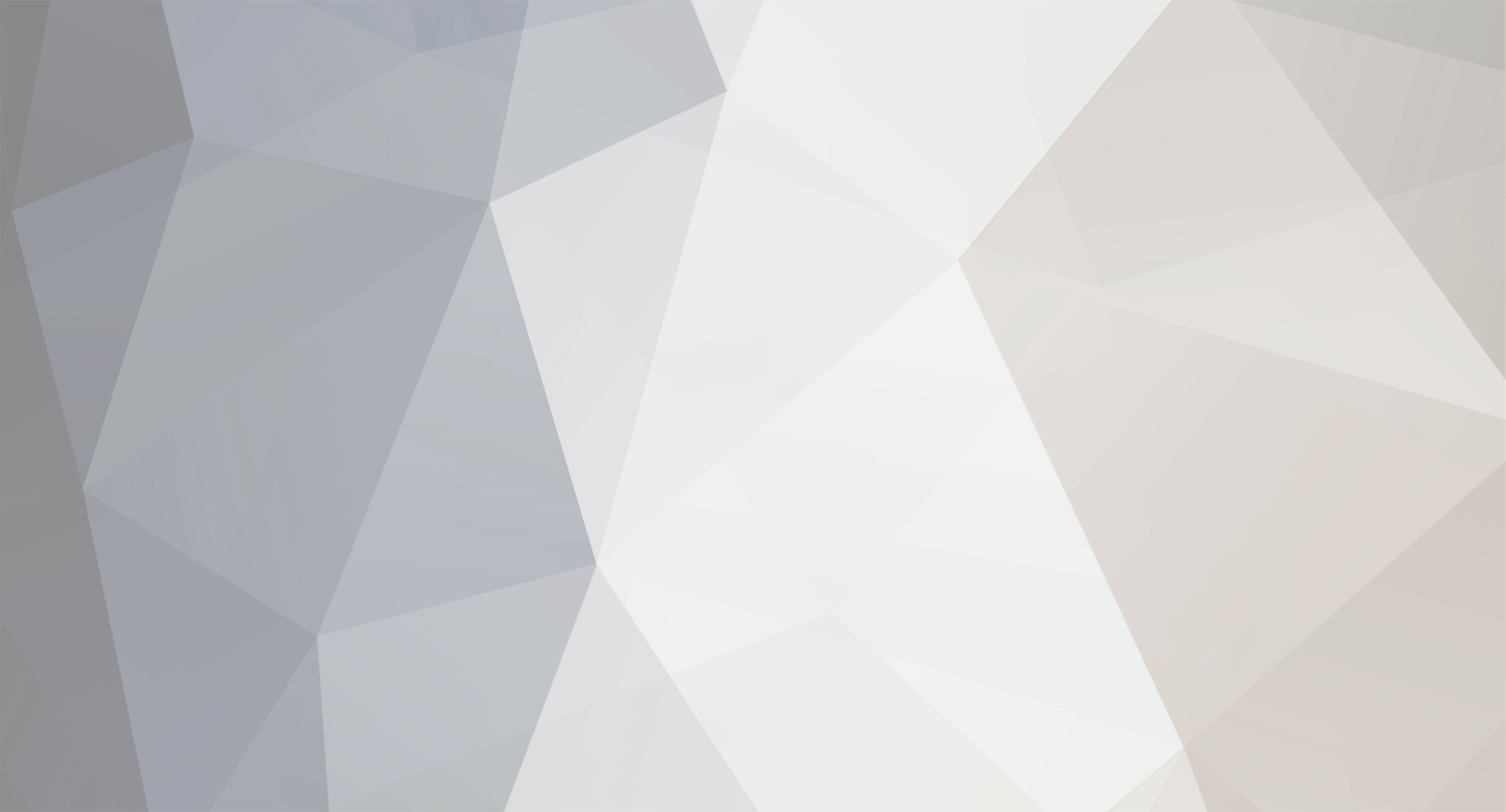
kscarbel2
Moderator-
Posts
18,743 -
Joined
-
Days Won
114
Content Type
Profiles
Forums
Gallery
Events
Blogs
BMT Wiki
Collections
Store
Everything posted by kscarbel2
-
Street Insider / April 6, 2016 Rush Enterprises, Inc. announced the implementation of a plan for consolidation of its Navistar Division dealership network that is intended to allow the company to significantly reduce expenses while still providing efficient service to its customers in the affected areas of operation. The plan includes closing Rush Truck Centers in the following locations on May 1, 2016: Kankakee, Decatur, Ottawa, Mount Vernon and Grayslake, Illinois; Ontario, Oregon; Findlay, Ohio; and Statesville, North Carolina. Rush Truck Centers formerly located in Brazil, Indiana; and Helper, Utah, were closed in the first quarter of 2016. Additionally, as a result of [dealer] acquisitions, the company currently has two locations in each of Augusta and Tifton, Georgia, which will be consolidated into one location in Augusta and one location in Tifton on June 1, 2016. The company also consolidated its Peterbilt location in Alice, Texas, into its newly constructed Corpus Christi, Texas, location in the first quarter of 2016. In total, the company expects to close 13 Rush Truck Centers in the first half of 2016. “It’s never easy to make the decision to close a Rush Truck Center,” stated W.M. "Rusty" Rush, Chairman, Chief Executive Officer and President of Rush Enterprises. “However, as we acquired dealership groups across the country in recent years, we acquired a number of small dealerships located in close proximity to one another. Many of these dealerships have been in existence for a long time, but with changes in technology and, in certain cases, the local markets, there is no longer an economic justification for the affected dealerships to operate in such close proximity to our other dealerships,” explained Rush. “Unfortunately, there are a lot of great employees who have worked hard for this Company at each of the affected Rush Truck Centers. We are hopeful that many of these employees will accept positions at nearby Rush Truck Centers,” Rush continued. “The 13 Rush Truck Centers we intend to close contributed approximately $55 million in revenue in 2015,” stated Rush. “We expect that we will be able to retain approximately 55% of the revenue from these locations through consolidation into other nearby locations. However, we anticipate that the closures will result in annual expense reductions of approximately $11.0 million. Importantly, we believe these expense reductions will be achieved without any significant reduction in our ability to service customers in our areas of responsibility,” Rush concluded. The facility consolidations are expected to result in a restructuring charge estimated at approximately $4.0 million to $6.0 million. A significant majority of the charge will be taken in the first quarter of 2016, with the remainder expected to occur in the second quarter of 2016. The charge is expected to consist of approximately $400,000 in severance and related benefits, plus $3.6 million to $5.6 million in facility exit costs, including impairment charges to certain fixed assets and the value of the real estate underlying the locations that will be classified as held-for-sale. Approximately $750,000 of the severance and related benefits and facility exit costs are cash costs, a significant majority of which are expected to be paid during fiscal year 2016. In addition, the company plans to classify certain excess real estate as held-for-sale, which will result in impairment charges of $4.9 million in the first quarter of 2016. “Over the years, we have accumulated some excess real estate as a result of acquisitions and our construction of new dealerships. We plan to sell this real estate, none of which is encumbered with debt, over the next 12 months and deploy the proceeds in a manner that creates long-term value for our shareholders,” explained Rush. “Consolidation of our dealership network is an important part of our plan to reduce expenses in 2016. As always, we remain committed to meeting the needs of our customers, and I commend our employees for maintaining excellent customer service while reducing costs across the organization,” concluded Rush.
-
Roush Offers Propane Fuel System for Ford F-750
kscarbel2 replied to kscarbel2's topic in Trucking News
It’s hard for Alkane, with its propane PSI 8.8-liter (GM big block) in a Chinese Foton, to compete with Ford-backed Roush. http://alkanetruckcompany.com/trucks/ -
Heavy Duty Trucking / April 6, 2016 Roush CleanTech has developed a propane autogas fuel system for the Ford F-750 chassis and its 6.8-liter V-10 engine. The model was created in response to the growing demand for an autogas-fueled medium-duty chassis for bobtail applications, cylinder delivery trucks, and larger tank setters and box trucks, said Todd Mouw, vice president of sales and marketing. “Now fleet managers can purchase an F-750 that not only costs less (than diesel) initially, but also saves money at the pump and uses a clean-operating, American-made fuel,” he said. With the Roush system, the Ford F-750, rated at up to 33,000 pounds, comes with a 50-usable-gallon fuel tank, located on the driver side for ease of fueling. An extended tank option is available for those in need of more mileage. Victory Propane, a supplier in Michigan, is one of the first to purchase the new Ford F-750 with the system. “Victory Propane already has 25 Ford F-650s equipped with the Roush CleanTech fuel system,” said Gregg Falberg, the firm’s president. “We will increase our autogas fleet with Roush’s first two Ford F-750s, and 13 more have been ordered.” Historically, propane autogas costs up to 40% less than gasoline and 50% less than diesel, Mouw said. Each Ford F-750 equipped with this fuel system will emit about 120,000 fewer pounds of carbon dioxide over its lifetime compared to conventionally fueled counterparts. The engine meets Environmental Protection Agency and California Air Resources Board certification requirements. As a Tier 1 supplier and Ford Qualified Vehicle Modifier manufacturer, Roush CleanTech outfits propane autogas vehicles that retain all Ford performance characteristics, such as horsepower, torque and towing, while maintaining the OEM factory warranty. . For more information, click here.
-
France 24 / April 6, 2016 The Spanish foreign ministry has summoned France's ambassador after French farmers hijacked Spanish trucks at the border and drained their cargo of wine. The farmers attacked several Spanish trucks on Monday at a toll barrier at Le Boulou in southern France in what they said was a protest against unfair competition. "We are protecting our products" from cheap wine coming from Spain and Italy, Frederic Rouanet, the president of the Aude winemakers' union, told AFP, vowing to continue the protests. The Spanish Federation of Freight Transportation, which represents truckers, said French police had allowed the demonstrators to "act with impunity". In July, Madrid issued a similar protest after French farmers ransacked Spanish trucks carrying milk and meat. French farmers have been furious over falling food prices, which they blame on foreign competition as well as supermarkets and distributors. .
-
Navistar adds RollTek seat option to ProStar
kscarbel2 replied to kscarbel2's topic in Trucking News
-
Transport Topics / April 6, 2016 As shareholders at truckmaker Daimler AG approved the biggest dividend in the company’s history, two investors got into a fight at its annual general meeting over complimentary sausages. The world’s largest truckmaker was forced to call police after one shareholder began packing away multiple sausages from the buffet. A woman intervened, and the two got into a verbal altercation. Daimler served about 12,500 wursts to the 5,500 shareholders who attended the meeting in Berlin, spokeswoman Silke Walters said. Buffets that can cost far more than one share of stock are part of the culture of European shareholder meetings, which can drone on the better part of a full day as investors chow down on everything from hearty pretzels and bratwurst to coffee and cake. Daimler shareholders approved a dividend of 3.25 euros per share on April 6, enough for a double-pack of sausages at German discounter Aldi. Daimler Chairman Manfred Bischoff said the company clearly needs to do more to satisfy their hunger. “Either we need more sausages, or we’ll have to get rid of the sausages entirely,” Bischoff said.
-
Navistar adds RollTek seat option to ProStar
kscarbel2 replied to kscarbel2's topic in Trucking News
-
Fleet Owner / April 6, 2016 Seat system better protects drivers in a roll over Navistar is now offering IMMI’s RollTek seat as an option on its International ProStar Class 8 on-highway trucks; an optional feature available immediately, the OEM said.. The RollTek safety system (http://www.imminet.com/products/rolltek/) combines advanced seat belt technology and side airbag protection to significantly reduce the potential for death or serious injury in a rollover. A sensor located behind the seat constantly monitors the angular position of the vehicle, activating a series of safety systems if it detects an imminent rollover. When activated, the RollTek seat system deploys side-roll airbags, tightens the safety belt and lowers the seat to help reduce injury risk and maximize safety for operators “Incorporating the advanced RollTek protection system into our heavy truck portfolio is a reflection of our listening to our customers and providing them with an option when a collision is unavoidable, said Bill Kozek, president of Navistar Truck and Parts, in a statement. “Today’s trucking companies are increasingly looking for smart technologies that can deliver an added margin of safety and productivity,” added Steve Gilligan, Navistar’s VP-product marketing. “The RollTek safety system provides best-in-class protection that contributes to drivers’ safety and peace of mind.”
-
The Guardian / April 6, 2016 The term tax haven may evoke images of exotic locales, but Panama actually ranks as the 13th most attractive spot for hiding assets, while the US lies third One of the surprises about the Panama Papers – the largest leak from an offshore tax adviser in history – is how few Americans have so far been exposed. The reason? It may be because creating a shell company in the US is easier than obtaining a library card. About 200 people with US addresses have so far been revealed as clients of Mossack Fonseca, the firm at the center of the Panama Papers leak. Compared with countries such as China, Switzerland, Russia and the United Kingdom, the number is small. The anomaly may be because it’s so easy to create a vehicle to hide your money and your identity in the US that there’s no need to mess with Panama, according to Shruti Shah, vice-president of programs and operations at Transparency International, an anti-corruption organization. “You don’t really have to go to Panama or other tax havens. They are not the only ones making it possible for corrupt officials and other criminals to launder their money. You can do it in every state in the US,” explained Shah. “In every state in the US, you can incorporate an LLC – [a limited liability company] – or another legal entity and you don’t have to disclose who the beneficiary on it is. In fact, Delaware is so synonymous with anonymous companies and ghost corporations that it was named in Transparency International’s Unmask the Corrupt campaign as one of the most symbolic cases of corruption.” The term tax haven usually evokes an image of some faraway place like Belize or the Cayman Islands. Yet in 2015, in a ranking of tax havens most attractive for those looking to hide assets, the US came in third – surpassing Cayman and Singapore. The two places that were even better suited as tax havens for the rich were Switzerland and Hong Kong, according to the Tax Justice Network that published the ranking. What was Panama’s ranking? It was 10 spots behind the US, at 13. Welcome to Delaware A while back, Shah sent her husband to return an overdue book she had borrowed from the library. When he returned, he told her her library card was expired and that to renew it she would have to bring her driver’s license showing her current address or a utility bill with her address. “If I were to open a shell company, I wouldn’t require any of those things. I would actually need less information to open a shell company in the US than I would need to get a driver’s license or a library card,” pointed out Shah. Is this in every state or just some like Delaware where the majority of US companies are incorporated ? “No state in the US requires beneficial ownership information. So it’s practically everywhere,” explained Shah, who lives in Virginia. “Some states are easier than others. In some states it’s more money than others, because they also have tax-friendly laws. Delaware and Nevada and Wyoming are infamous – or famous, however you look at it – [for their tax laws]. Texas and Florida are equally easy.” There is nothing illegal about setting up a shell company. US states are proud of their business-friendly policies. Delaware, for example, prides itself on being the incorporation capital of the US. “More than 1,000,000 business entities have made Delaware their legal home,” claimed the state’s Division of Corporations website. “More than 50% of all publicly-traded companies in the US including 64% of the Fortune 500 have chosen Delaware as their legal home.” In the wake of the Panama Papers, the number of shell companies incorporated in the US could grow. Instead of stashing their cash in Belize, Panama or the Cayman Islands, the companies and individuals could turn to the US. “They certainly could,” said Heather Lowe, director of government affairs at Global Financial Integrity. “Given the lack of action in the US to address this issue compared to, say, the European Union, it may seem like a safe bet right now.” Shell companies have their uses; they can be used to buy land anonymously, for example, without tipping off the competition. To create an entity to protect future business rights, or a holding company for various businesses. They can also be used to, legally, make political contributions anonymously. Just because some people or companies have chosen the state to form shell companies and hide assets does not mean the entire system should be to blame, argued Charles Elson, director of the John L Weinberg Center for Corporate Governance at the University of Delaware. “Delaware really is not a tax haven. Delaware is a place where most US companies are incorporated, because of a very intelligent corporate law regime,” he said. “Obviously, some companies that are problematic come here, too, but that’s not the design of the system. That’s a collateral effect … If someone uses the corporation for nefarious purposes, I don’t think that’s the fault of the corporate statute, but of the individual.” Shell companies, whether created abroad or at home, make it easy for people to hide assets and commit crimes, said Shah. For example, in the mid-2000s, former Louisiana congressman William Jefferson had created eight different shell companies to hide hundreds of thousands of dollars of bribes. Viktor Bout, an infamous arms trafficker known as the Merchant of Death, had at least a dozen shell companies incorporated in Delaware, Texas and Florida to cover up his weapons trafficking operation. There is no reason, said Shah, why creating such shell companies should be easier than obtaining a library card. Her group Transparency International has called on the US Congress to pass the Incorporation Transparency and Law Enforcement Assistance Act introduced by congresswoman Carolyn Maloney and Senator Sheldon Whitehouse. If enacted, the bill would require states to collect, maintain and update information about beneficial ownership of all companies created in the US. “Bipartisan legislation has been introduced in the House since 2008, but it has never seen the light of day. It’s never been enacted into law. Maybe now is the time,” said Shah. Elson remains skeptical as to whether such a law would actually work. “I don’t know how fixing the beneficial ownership rule would fix this. If someone is devious enough to game the system in this way, they would work their way around any single regulatory change. These are very clever people,” he said. In order for any legislation to pass, the US business community would have to come out in support of it, pointed out Lowe. “The US Chamber of Commerce has long opposed legislation to end anonymous companies, and they must reverse that position and begin to support honest and open business practices,” she said.
-
Lars Stenqvist joins Volvo Group management Volvo Group Press Release / April 6, 2016 Lars Stenqvist has been appointed member of the Volvo Executive Board and Executive Vice President of Volvo Group Trucks Technology, the Volvo Group’s technology and product development organization for trucks. He will also hold the title of Volvo Group Chief Technology Officer. Lars Stenqvist was born in 1967 and has been active for many years in the heavy vehicles industry, with several years of international experience. Currently, he is working for the Volkswagen Group as head of research and development for trucks and buses. Previously, he worked with Swedish truckmaker Scania. Lars Stenqvist replaces Torbjörn Holmström, who will be employed as the Volvo Group’s senior advisor on research and development. He will assume his new assignment in October, 2016.
-
In addition to Volvo Group CFO Jan Guander and executive board appointee Hakan Samuelsson, both long-time Scania veterans, Martin Lundstedt will now be working with another old Scania colleague at Volvo. Lars Stenqvist, has agreed to leave Volkswagen Truck & Bus and become head of Volvo R&D. Martin Lunstedt and Lars Stenqvist grew up together from the age of kindergarten in the city of Mariestad. After high school, they served their two years of compulsory military service together and went on to attend college at the renowned Chalmers University of Technology in Gothenburg where Volvo is headquartered. Both men joined Scania in 1992 after graduating. Last September, Volkswagen Truck & Bus head Andreas Renschler removed Stenqvist from his position as Senior Vice President and head of Vehicle Definition at Scania, and gave him a new assignment as head of R&D at VW’s truck & bus unit. (Volkswagen Group managed to acquire enough shares of Scania in May 2014 so as to take control) Like Lundstedt, Stenqvist was unhappy with the new German control of Scania. Born in 1967, Stenqvist began his Scania career by working at several of the company’s production units. From 2002 to 2004, he served as head of Scania’s chassis assembly operations in the Netherlands. From 2004, Stenqvist worked within Scania's R&D unit. In 2007, he was appointed Senior Vice President and Head of Vehicle Definition. .
-
V8 – Power in style Launched at the end of the 1960s, Scania’s first V8 engine was Europe’s most powerful truck engine and it held this distinction for many years. Scania is continuing this tradition with its latest top-of-the-line V8, which has the highest torque and power ratings of any V8 truck engine. But it’s not just about power. The V8 also meets the requirements of all the different Euro (and equivalent) standards, and stands ready to meet future environmental standards. The Scania 730 hp V8 in many ways represents the beginning of a new era, a new reign in the kingdom of high-output engines. The V8 is based on Scania’s modular engine platform, introduced in 2007 on inline engines. It features a completely new design, yet it shares fundamental architecture and many components with its siblings in the Scania engine dynasty. http://www3.scania.com/en/New-V8-truck-range/Line-up/ http://www.scania.com/group/en/section/solutions/trucks/v8/
-
Prime Mover Magazine / April 6, 2016 The last weekend has been an eventful one for the Australian trucking industry, with the Road Safety Remuneration Tribunal’s (RSRT) much-criticised minimum payment scheme being stopped less than 48 hours before it was supposed to come into effect. After a heated debate over the Easter break, it seemed like the RSRT’s intricately named Contractor Driver Minimum Payments Road Safety Remuneration Order (RSRO) would come into effect as planned when Australia closed for business last Friday, with the Tribunal stating it would not to agree to a delay. A last minute appeal by NatRoad to the Federal Court in Brisbane, however, still managed to stop the Order from going ahead, with the Court formally granting a stay of the Order until further notice. “This means that the Contractor Driver Minimum Payments RSRO that was to apply to tens of thousands of contractor drivers across Australia from 4 April will not commence until further order of the Court,” NatRoad announced Friday evening. This week, Employment Minister, Senator Michaelia Cash, now followed up with an announcement that the Government will be introducing legislation to ensure that orders setting mandatory remuneration rates for truck drivers cannot commence before 1 January 2017. Minister Cash said the new legislation, if passed by the Senate, will provide certainty for the trucking industry while reform options for the Road Safety Remuneration system are considered by the Government. She explained, “Today I also announce that given the urgency of this matter, consultations with key industry stakeholders for reform options for the system will commence this week. “This is a priority for the Government as owner-drivers are the lifeblood of the economy. Anything which threatens their viability will have significant implications across the country – this is not something we will tolerate. “If the payments order was to come into effect as planned it would be devastating for thousands of owner-drivers and consumers alike.” What also became clear over the course of last weekend and during the following debate was that industry will use the delay to lobby for the abolishment of the RSRT itself. Responding to new reports by PwC and Jaguar Consulting that assess the impact of the RSRO on the Australian economy, ATA Chair Noelene Watson said the Tribunal failed to have any appreciable impact on road safety. “In particular, the Jaguar Consulting report points out that the tribunal’s prescriptive approach is at odds with the best practice general duties approach to heavy vehicle safety recently agreed to by transport ministers following advice from the ATA,” she explained. “Until now, the ATA has had no mandate to be involved in the Tribunal. However, the definitive findings of [the new] reports make it clear that the Act and Tribunal are a threat to the viability of more than 20,000 small trucking operators, and to our economy generally.” The Australian Logistics Council’s (ALC) Managing Director, Michael Kilgariff, had made the same call last week, stating “the abolition of the RSRT is the only real way to avoid the duplication, confusion and costs that this order, and others like it, will inevitably create. “The ALC believes the best way to achieve safety improvements in the heavy vehicle industry is through achieving greater compliance and enforcement of Chain of Responsibility (part of the Heavy Vehicle National Law, ed.).”
-
HGVUK / April 5, 2016 Goodyear is reinventing the truck tyre with the launch of a completely new industry size: the low profile Goodyear KMAX S steer tyre in the dimension 375/45R22.5. In addition to this industry innovation, the leading tyre manufacturer further broadens its portfolio with another low profile tyre: the Goodyear KMAX D drive axle tyre in size 315/45R22.5. The new versions of Goodyear´s high mileage truck tyres play a crucial role in optimizing freight efficiency for fleet operators as they allow volume capacity of more than 100 m3 for semi-trailers. The new low profile truck tyres are the result of collaboration with leading truck maker DAF on their special Low Deck tractor and initially will be available only as OE fitment for the DAF CF and XF Low Deck tractors. The new tyres are the Goodyear KMAX S steer tyre size 375/45R22.5 and the Goodyear KMAX D drive axle tyre size 315/45R22.5. The size 375/45R22.5 is new to the industry and has been added by the European Tyre and Rim Technical Organisation (ETRTO) to the official list of sizes. The two new Goodyear low profile truck tyres are an important step for the freight segment, where improvements in ton per kilometer are continually pursued, while respecting the height limitation imposed on vehicles. In order to maximize load capacity of more than 100 m3, many fleets operate megatrailers with an internal height of 3 meters. The new tyre combination overcomes the issues that often make optimizing such trailers difficult if not impossible. This is another example of Goodyear leading the way by reinventing the tyre. The new KMAX D drive tyre reduces chassis deck height, lowering the fifth wheel by 5 to 6 centimeters to 91 centimeters, and the innovative KMAX S steer tyre lowers front axle height by approximately 2 to 3 centimeters This further allows a sufficient gap to be maintained between the tractor and trailer during maneuvering. This means that, within the maximum vehicle height of 4 meters, trailers with an internal height of 3 meters can be used, allowing volumes of more than 100 m3 for maximum transport efficiency. The tyres also permit axle loads of 8 and 11.6 tonnes respectively and is an alternative for 355/50R22.5 steer tyres and 295/55R22.5 drive tyres. The new tyres will initially be supplied to DAF for original equipment fitment and soon after as replacements. The combination of low aspect ratio with high load index made the development of these tyres a technological challenge. To do this, Goodyear employed a mixture of engineering methods and technologies. These include tuning the width of the KMAX S steer tyre’s shoulder ribs along with the geometry and sequence of the sipes. A 6-rib design has been adopted and the IntelliMax Ribs (circumferential ribs that link laterally) have been specifically adapted. Specific optimization was also carried out on the V-shape tread design of the KMAX D drive tyres. Both steer and drive tyres feature the Interlaced Strip Technology in their construction. Interlaced Strip Technology is patented by Goodyear and is an innovative belt reinforcement in the crown area of the tyre. This allows the tyre to carry more load as well as giving a better wear profile for increased mileage potential. .
-
6 Truck Makers to Participate in European Platooning Challenge
kscarbel2 replied to kscarbel2's topic in Trucking News
-
Volvo New River Plant Workers Ratify 5-Year Contract
kscarbel2 replied to kscarbel2's topic in Trucking News
Volvo Trucks North America and UAW Agree on Five-Year Contract Volvo Group Press Release / April 5, 2016 Volvo Trucks North America today announced that employees represented by the United Auto Workers have ratified a new five-year agreement covering about 2,000 members of UAW Local #2069 at the New River Valley, VA, plant. The new contract is effective March 17, 2016, and will expire on March 16, 2021. “Our positive working relationship with the UAW was in evidence throughout negotiations, and helped us reach an agreement that ensures the plant’s competitiveness, while continuing to offer our employees a great quality of life,” said Franky Marchand, NRV vice president and general manager. “NRV builds every truck we sell in North America,” said Göran Nyberg, president of Volvo Trucks North America, "and this agreement gives us the stability we need to keep building on the momentum we established during our record 2015.” -
Class 8 orders continue falling Fleet Owner / April 5, 2016 By contrast, medium-duty demand continues to rise. Orders for Class 8 trucks continued to decline in March, according to preliminary data, while orders for medium-duty remained on a growth track. North American Class 8 truck net orders fell for the third consecutive month to 15,800 units in March – the lowest level for Class 8 orders since September 2012. March orders were 12% below February and down 37% year-over-year, which is the weakest month of March in six years, and are expected to remain under 20,000 units for the next few months as the market bottoms out. The decline in Class 8 orders in March results from a weak freight rate environment, weakness in late-model used truck values, and excessive new vehicle stocks. Fleets are being very cautious in the current uncertain economic environment, as freight has slowed due to a “manufacturing recession.” Some fleets are also delaying replacing older units until conditions improve. There are very few dealer stock orders, since inventories are sufficient and OEM lead times are short. As a result, OEMs continue to reduce production rates in response to an expected 26% drop in build this year. Inventories remain high and retail sales have moderated, so order rates should remain subdued in the short-term. Manufacturing is expected to improve soon and this is expected to increase freight levels and stabilize truck demand. In the case of medium-duty truck demand, a decent jobs market and rising incomes continue to support discretionary spending and improved housing activity. For medium-duty trucks, the slow but steady rise in the order trend remained evident in March, with orders rising 4% against a tough year-over-year comparison. Medium-duty order strength through the first quarter continues a period of meaningfully stronger orders which began last September.
-
FDA Previews Final Food Safety Transportation Rule Transport Topics / April 5, 2016 The U.S. Food and Drug Administration on April 5 previewed its final rule that creates new requirements for the sanitary transportation of human and animal food by truck and rail to ensure that transportation practices do not create safety risks. “Practices that create such risk include failure to properly refrigerate food requiring temperature control for food safety, the inadequate cleaning of vehicles between loads and the failure to otherwise properly protect food during transportation,” the agency said in its rule scheduled for publication in the April 6 Federal Register. The rule establishes requirements for sanitary transportation practices applicable to shippers, loaders, carriers by motor vehicle and rail vehicle, and receivers engaged in food transportation. “Due to illness outbreaks involving human food and animal food that became contaminated during transportation, and incidents and reports of insanitary transportation practices, there have been concerns over the past few decades about the need to ensure that food is transported in the United States in a sanitary manner,” the rule said. “Consumers deserve a safe food supply, and this final rule will help to ensure that all those involved in the farm-to-fork continuum are doing their part to ensure that the food products that arrive in our grocery stores are safe to eat,” Michael Taylor, FDA’s deputy commissioner for foods and veterinary medicine, said in a statement. The rule specifically addresses requirements related to vehicles and transportation equipment, transportation operations, training, records and waivers. Businesses would be required to comply with the new regulation one year after publication of the final rule, with smaller businesses having two years to comply with the new requirements. Jon Samson, executive director of American Trucking Associations’ Agricultural & Food Transporters Conference, said he generally was pleased with the final rule. “There were some pretty significant changes made on the positive side,” Samson told Transport Topics. Samson said the final rule will allow a food receiver to make the call whether the food was adulterated or not, if for example, a proper food temperature stipulated in a contract was not precisely maintained during transport. The proposed rule would have automatically required that the food be declared as adulterated, Samson said. “Also, they’re backing off on any sort of prescriptive requirements for temperature monitoring or continuous monitoring,” Samson said. “That was another big one because sometimes it isn’t necessary, especially if you’re doing shorthaul movements to constantly be monitoring the temperature.” Some of the changes the agency made in its 283-page final rule to its 2014 proposed rule include: • Simplified definitions for parties covered by the rule to make them all activity-based and added a definition for “loader” as a new party covered by the rule. • Amended the definition of “transportation operations” such that additional transportation activities are not covered by the rule, including transport of food completely enclosed by a container, except food that requires temperature control for safety, food contact substances, and human food byproducts transported for use as animal food without further processing. • Changed the provisions of the rule to focus on food safety concerns and not additionally adulteration as a result of spoilage or quality defects. • Removed prescriptive requirements for temperature-monitoring devices and continuous monitoring of temperature during transport and replaced these provisions with a more flexible approach, which allows the shipper and carrier to agree to a temperature-monitoring mechanism for shipments of food that require temperature control for safety. • Removed the provision requiring the carrier to demonstrate temperature control to the receiver for every shipment requiring temperature control. • Revised the rule to require that if a person subject to the rule becomes aware of an indication of a possible material failure of temperature control or other conditions that may render the food unsafe during transportation. • Revised the requirements of the final rule to make it clear that its requirements account for the fact that the intended use of the vehicle or equipment with respect to the type of food that is being transported is relevant in establishing the applicable sanitary transportation requirements. • Revised the rule to primarily place the responsibility for determinations about appropriate transportation operations on the shipper. The FDA said it received 240 comments on the proposed rule from individuals, industry and trade associations, consumer and advocacy groups, academia, law firms, professional organizations, federal and state, tribal and foreign government agencies and other organizations.
-
FDA releases final food transportation safety rule Fleet Owner / April 5, 2016 Regulation marks the sixth major rule under FDA Food Safety Modernization Act The U.S. Food and Drug Administration finalized a new food safety rule Tuesday that will help to prevent food contamination during transportation. The rule, under the FDA Food Safety Modernization Act (FSMA), will require those involved in transporting human and animal food – shippers, loaders, carriers and receivers – to follow best practices for sanitary transportation, such as properly refrigerating food, adequately cleaning vehicles between loads and properly protecting food during transportation. “Consumers deserve a safe food supply and this final rule will help to ensure that all those involved in the farm-to-fork continuum are doing their part to ensure that the food products that arrive in our grocery stores are safe to eat,” said Michael R. Taylor, the FDA’s deputy commissioner for foods and veterinary medicine. The rule is the sixth of seven proposed since January 2013 and is part of a larger effort to focus on prevention of food safety problems throughout the food chain, and the rule implements the Sanitary Food Transportation Act of 2005 (SFTA). The seventh rule, which focuses on mitigation strategies to protect food against intentional adulteration, is expected to be finalized later in 2016. The new rule will apply to food transported within the United States by motor or rail vehicle, whether or not the food is offered for or enters interstate commerce. It was proposed in February 2014 and takes into consideration more than 200 comments submitted by the transportation industry, food industry, government regulatory partners, international trading partners, consumer advocates, tribal organizations and others. “We recognize the importance of education and training in achieving widespread compliance, and we are committed to working with both industry and our government partners to ensure effective implementation of all of the new food safety rules under the Food Safety Modernization Act,” Taylor said. Businesses would be required to comply with the new regulation one year after publication of the final rule, with smaller businesses having two years to comply with the new requirements. Key requirements include: Vehicles and transportation equipment: The design and maintenance of vehicles and transportation equipment to ensure that it does not cause the food that it transports to become unsafe. For example, they must be suitable and adequately cleanable for their intended use and capable of maintaining temperatures necessary for the safe transport of food. Transportation operations: The measures taken during transportation to ensure food safety, such as adequate temperature controls, preventing contamination of ready to eat food from touching raw food, protection of food from contamination by non-food items in the same load or previous load, and protection of food from cross-contact, i.e., the unintentional incorporation of a food allergen. Training: Training of carrier personnel in sanitary transportation practices and documentation of the training. This training is required when the carrier and shipper agree that the carrier is responsible for sanitary conditions during transport. Records: Maintenance of records of written procedures, agreements and training (required of carriers). The required retention time for these records depends upon the type of record and when the covered activity occurred, but does not exceed 12 months.
-
Commercial Carrier Journal (CCJ) / April 5, 2016 The federal government’s Food and Drug Administration released April 5 a Final Rule that sets new sanitation-related standards for food haulers and others in the supply chain, like shippers, who deal in the transportation of food products. The rule does, however, have a notable exception for small companies: Carriers, shippers and receivers who bring in less than $500,000 in total annual revenue will not have to abide by the rule’s new procedures. The rule’s key requirements for carriers include: (1) That carriers and drivers ensure their refrigerated trailers are pre-cooled prior to loading food, carriers/drivers provide upon request by shippers and receivers proof they’ve maintained the appropriate temperature for the food they’re hauling and (3) carriers develop and implement procedures that specify their practices for cleaning, sanitizing and inspecting their equipment. The new rule also requires that shippers inspect carriers’ trailers prior to loading food products and requires any entity subject to its requirements, such as carrier personnel and drivers, to “take appropriation action to ensure that the food is not sold” if they become aware of any indication that a shipment of food was not kept at the proper temperature throughout its shipment. Shippers will now also be required to give carriers written sanitation requirements for their vehicles and require shippers to keep records showing they’ve done as much. The FDA says the rule likely won’t change carrier and shipper practices, saying it essentially only codifies already existing best practices for food shipments. The rule will take effect a year following its April 6, 2016-scheduled publication date in the Federal Register.
-
Volvo New River Plant Workers Ratify 5-Year Contract
kscarbel2 replied to kscarbel2's topic in Trucking News
UAW and Volvo agree to new contract at Dublin plant The Roanoke Times / April 5, 2016 The union for Volvo’s only truck-making plant in the United States has OK’d a labor contract with the company that will run until March 16, 2021, according to a Volvo news release. Negotiations on the agreement began in February, the same month that the truck manufacturer began layoffs of approximately 600 plant workers. Before the layoffs were announced in December, the plant had 2,800 employees. UAW Local 2096 has not returned repeated requests for comment, but the union has unveiled contract highlights on its website. From the online documentation, the plant’s union employees would be entitled to $2,000 signing bonuses and general wage increases over the next five years. For example, employees hired between March 17, 2011, and March 16 of this year would receive a $2,000 signing bonus and a 50-cent hourly raise from the second to fourth year of the contract. Those employees would then get a 73-cent raise during the contract’s fifth year. The five-year agreement Volvo and the union reached in 2011 was set to expire this year. When the union ratified the previous agreement in 2011, Volvo rehired about 700 workers who had previously been laid off. The union ratified the contract agreement Sunday, according to the union’s Facebook page. Various sectors involved in the vote, including hourly and salaried employees, approved the contract by more than 80 percent in favor. -
Volvo New River Plant Workers Ratify 5-Year Contract
kscarbel2 replied to kscarbel2's topic in Trucking News
Volvo Employees OK New Contract The New River Dispatch / April 5, 2016 Workers at the Volvo plant in Dublin have overwhelmingly approved a new contract with the truck maker. According to a post on the UAW Local 2069 Facebook page, workers ratified the agreement by a ‘YES’ vote of 88% of the votes cast. The five-year agreement gives employees a pay raise, increases in medical, vision, dental benefits, increases in pension benefits, and a hunting holiday. Retirees will also get yearly lump-sum increases. The Dublin plant, which currently employs more than 1,750 people, laid off more than 600 workers in February. No change in their status was indicated. Details of the agreement can be found on the UAW Local 2069 website. UAW – Volvo Trucks Proposal Highlights Link - https://drive.google.com/file/d/0BzigbY3lbz_eU2NHc3B3SDNCUXc/view?pref=2&pli=1 -
Transport Topics / April 5, 2016 Volvo Trucks North America announced that United Auto Workers union members at its New River Valley (NRV) plant in Virginia have ratified a five-year contract. The terms of the agreement that extends from March 17, 2016 until March 16, 2021 weren’t released. The vote count also wasn’t disclosed. “Our positive working relationship with the UAW was in evidence throughout negotiations, and helped us reach an agreement that ensures the plant’s competitiveness, while continuing to offer our employees a great quality of life,” said Franky Marchand, vice president and general manager of the plant known as NRV that is located in Dublin, Virginia. “NRV builds every truck we sell in North America,” said Göran Nyberg, president of Volvo Trucks North America, “and this agreement gives us the stability we need to keep building on the momentum we established during our record 2015.” Related reading: http://www.bigmacktrucks.com/topic/42910-volvo-trucks-to-lay-off-734-workers-at-its-virginia-plant/#comment-313858 http://www.bigmacktrucks.com/topic/42949-union-authorizes-volvo-strike/#comment-314157
-
The Wall Street Journal / April 5, 2016 Dealer inventories of unsold heavy trucks are at their highest level since before the financial crisis as weak freight demand sidetracks new orders from trucking companies Orders for new big rigs plunged and inventories of unsold trucks soared to their highest levels since just before the financial crisis, as uncertainty about future demand and a weak market for freight transportation weighed on truck manufacturers. About 67,000 Class 8 trucks are sitting unsold on dealer lots, after sales in March dropped 37% from a year earlier to 16,000 vehicles. Inventories haven’t been this high since early 2007. At present, there are too many trucks chasing too little freight. Companies that placed large orders in late 2014, only for customers to move less freight than expected last year, are reluctant to buy more vehicles now. Last month, it was reported that spot market rates for dry vans fell 18% between February 2015 and February 2016, an indication of weak demand. Fleets are being very cautious in the current uncertain economic environment. Freight has slowed due to the manufacturing recession, so they have sufficient trucks to meet current demand. Aaron Tennant, owner of Simplex Leasing Inc., a trucking company in Jamestown, N.D., said that last June, anticipating market growth, he placed an order of 115 new Navistar International trucks to replace 75 trucks and expand his fleet to 245 vehicles. But that growth has not come. “Once this order is complete, I’m probably not going to consider buying any new trucks until at least October or November,” he said. “It’s definitely coming from caution. The market has softened in the last year.” Analysts say the backlog of Class 8 trucks appears to be about six months, and truck and truck component manufacturers like Paccar, Navistar and Meritor are likely to see further pressure on their share prices and earnings. They believe the companies most closely tied to the Class 8 vehicle production cycle will likely have a difficult time exceeding expectations this year.
BigMackTrucks.com
BigMackTrucks.com is a support forum for antique, classic and modern Mack Trucks! The forum is owned and maintained by Watt's Truck Center, Inc. an independent, full service Mack dealer. The forums are not affiliated with Mack Trucks, Inc.
Our Vendors and Advertisers
Thank you for your support!