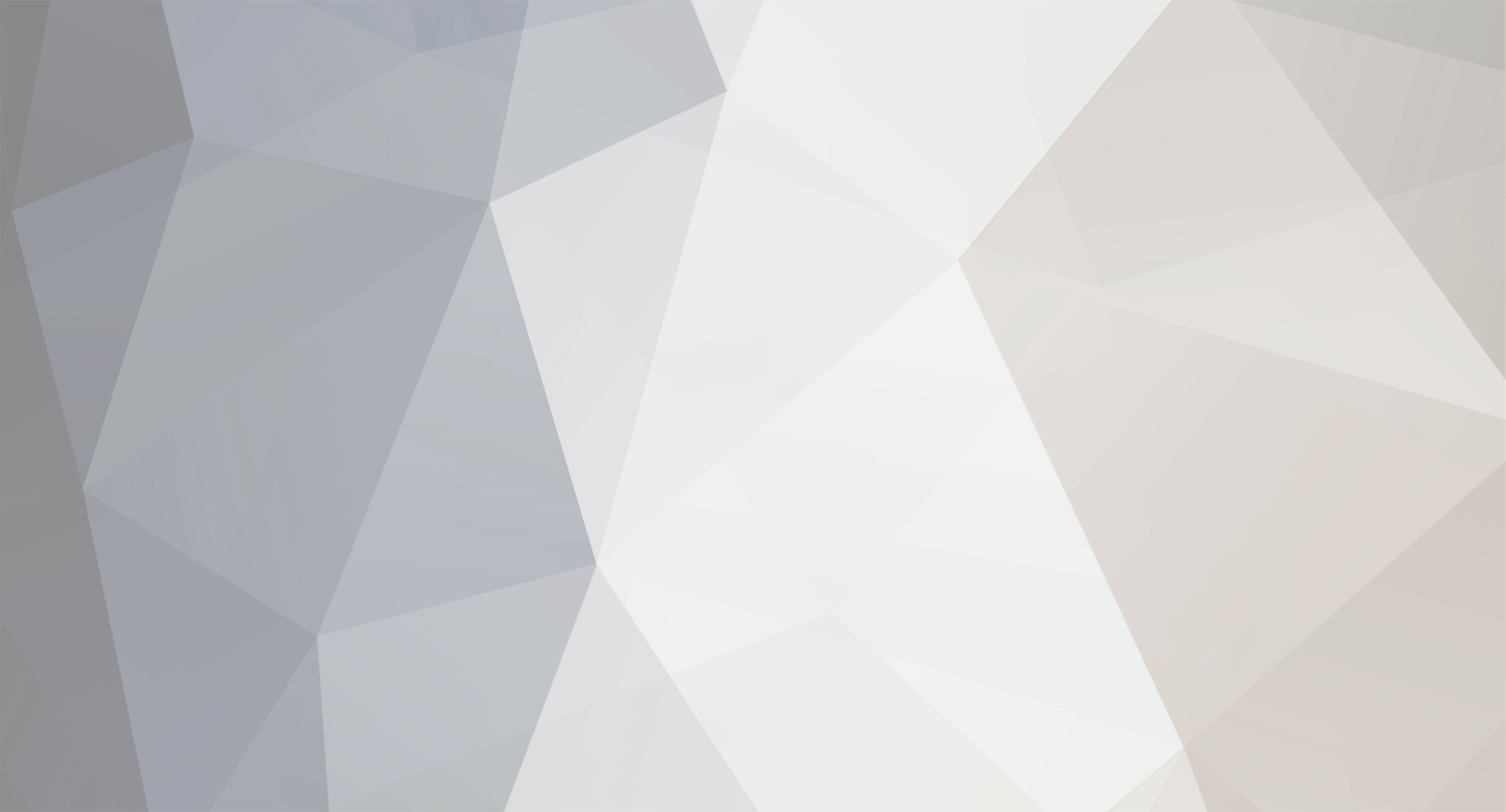
kscarbel2
Moderator-
Posts
18,541 -
Joined
-
Days Won
112
Content Type
Profiles
Forums
Gallery
Events
Blogs
BMT Wiki
Collections
Store
Everything posted by kscarbel2
-
Insight on one of Mack Trucks great leaders -------------------------------------------------------------------- Opportunity Belongs To The Prepared, Says Retiring Mack Chairman Pelletier November 10, 1985 / The Morning Call Mack Trucks Chairman Alfred W. Pelletier, 64, who concluded a 34-year career with the company on Friday, relaxed in his spacious World Headquarters office in Allentown last week and told an interviewer, "Everybody who wants to advance should be ready for opportunities when they come along." But Pelletier really couldn't say he was consciously ready in 1962, when he was Ontario service manager of Mack Trucks Canada, Ltd. A combination of happenstance, common sense and company loyalty opened a door that eventually led to executive suite. On that day in 1962, Toronto native Pelletier traveled to Thunder Bay, Lake Superior, to resolve some engine problems for a Mack dealer. When he arrived, the man had his suitcases packed and was leaving on vacation. He nonchalantly tossed a packet of papers into Pelletier's lap. "This is a tender for the purchase of 10 Mack diesel trucks. Aren't you going to submit a bid?" asked an incredulous Pelletier, as the disinterested dealer shrugged and headed toward the door. Contacting Dominion Tar & Chemical, the company that solicited the bids, Pelletier was advised that he had only 24 hours to turn in Mack specifications and prices on logging trucks to be used for feeding the company's paper mills. But that was not the only problem. Pelletier was a master mechanic who had never sold as much as a fuel pump. Sales was not his line. "Mack had the best darn logging trucks in the industry. Dominion was going to buy gasoline-engine trucks and I urged them to consider Mack diesels," recalled Pelletier, who made a hurried call to Mack's sales office in Toronto. Staying on the phone for an hour, Pelletier nervously compiled the specifications on a sheet of paper, listed all of the prices, came up with a total and drove the bid to the Dominion office 100 miles to the south. Three weeks later, while on a business call in Quebec City, Pelletier received a telegram from Mack's office in Toronto. It read, "Congratulations. We got the order for the 10 diesel trucks." Pelletier's superiors did not overlook his enterprise. "If I had not taken advantage of that opportunity, I might still be up in Canada in Mack's service division," he remarked. Pelletier often tells the Thunder Bay story when he travels across the United States, speaking to teen-agers and young adults enrolled in one of his major volunteer activities: Vocational Industrial Clubs of America (VICA). On one goodwill tour this year, he told a discouraged vocational student, "This country will always need doctors, dentists and lawyers. But it also will need people with skilled trades and experience. Learn a skill that's in demand and you'll be able to make a living with it." Elaborating on that point last week, Pelletier said, "The manual skills have declined in thiscountry; labor has become too complacent. VICA is the kind of organization that will bring them back. Young people are very enthusiastic because somebody cares about them." Scores of his acquaintances and associates in the Lehigh Valley know much more about Alfred Pelletier the Mack chairman, United Way president, Minsi Trails Council scout leader and benefactor of the Parkette National Gymnastic Center than they do about the young Canadian who came out of World War II and got a job in 1945 as a diesel mechanic with the Toronto Transportation Commission. His experience servicing and repairing the commission's 10 Mack transit buses won him a job with Mack Trucks Canada as a journeyman mechanic in 1952. "I knew how to take a diesel engine completely apart and put it back together. That gave me confidence," Pelletier remarked. Pelletier's "diesel school" was the Canadian Royal Navy, which he served in combat 1941-45 with punishing convoy trips across the oft-stormy North Atlantic. Based in Halifax, Nova Scotia, Pelletier was assigned to a Bangor- class escort vessel or a corvette. To this day, he still regards Nicholas Monsarrat's "The Cruel Sea" as the finest war novel ever written about men of the anti-submarine forces. Shortly after the corvette received its first radar system, concerned crewmen alerted the captain to a "blip" in an ocean combat zone. Two radio demands for the "blip" to identify itself went unanswered. Finally, after a third "this-is-it" demand, this reply was received, "All right, captain, keep your little boat on course and everything will be just fine." The terse message came from HMS George V, a British battleship large enough to capsize the corvette with the flushing of its bilge tanks. Coming from a poor family - his father was a French Canadian who grew up in a New Brunswick French village and married a British war bride - Pelletier learned the value of a dollar early on. Only the family's history was rich: A tracing of roots revealed that the Pelletiers were indirectly descended from French explorer Samuel de Champlain. Over the years, Pelletier has boated and fished many times in Champlain's "little lake" in New York. If Pelletier's rise through the ranks of Mack Trucks Canada was not meteoric, it certainly was impressive. In the same year he joined the Canadian subsidiary (1952), he became shop foreman of the Toronto branch. A year later, he was promoted to service manager for all of Ontario. Pelletier was branch manager at Toronto, 1966-67; general manager Mack Trucks Canada, 1970, executive vice president, 1971, and was appointed president of Mack's whole Canadian operation in 1974. While Pelletier was president of Mack Trucks Canada, the company had record sales, but the economy was good. A recession hit in 1975. When Mack Trucks' board met in Allentown in 1975, it was decided to kick President Henry J. Nave upstairs to chairman and select an executive from within Mack's ranks to be president and chief executive officer. Officials of Signal Companies, Inc., then Mack's parent corporation, agreed with the Allentown brass that Pelletier was the best man. "The job wasn't offered to me. I was told to report to Allentown," said Pelletier, who was taken by surprise with a phone call. "At first I was shocked. Then I was on Cloud Nine; I couldn't believe that I was going to Allentown where many of the giants of the truck industry, the engineering brains, had worked. But I did take it as a challenge." One aim of Mack directors was to promote a person from within who could provide the company with at least 10 years of leadership. "I have fulfilled that requirement because it is 10 years almost to the month that I assumed the presidency," said Pelletier, who will be feted at a testimonial dinner at the Holiday Inn West on the night of Dec. 11. Between now and the dinner, which is by invitation only, Pelletier will be saluted by the Parkette staff and members at their center on Nov. 23. While Pelletier had the highest respect for Henry Nave's abilities, he remembered with some amusement that Mack staffers had a psychological problem regarding Nave's long association with rival White Trucks. They never seemed totally comfortable with the "White Knight" in their midst. "Nave was a good truck man and a great guy," said Pelletier. "No question about it, he was a gentlemen. But you can't take a fella who for 25 years was your arch enemy and put him amongst the Mack staff. It was just not good for morale. That's why Signal decided to appoint as president someone within the company for the first in 33 years." Even today there exists a bitter rivalry between Mack and the now Volvo-White Co. in the heavy truck industry. When a reporter inadvertently referred to Mack's chrome-laden long-haul Superliner as White's "Freightliner,' ' Mack Vice President William McCullough almost jumped down his throat with both feet. Loyalty, dedication and pride are not demanded of Mack's administrative corps - these qualities just seem to come naturally. Pelletier, who owns thousands of Mack Trucks shares and intends to keep them, sees a great future for the company despite foreign competition in the Class 8 truck market that is growing steadily. What's the most significant aspect of Mack as he looks back over his long career? "Mack has a great product line and the name. And we have the most dedicated group of distributors and employees in the industry. They believe in that Bulldog. We sell so much under that Bulldog name," Pelletier replied. "Our parts service has improved dramatically in the last five years. We can give a customer delivery of 92 percent of his order in less than 24 hours; the balance in 48 hours." He added, "This is no criticism of the guys who ran the company years ago because we didn't have computers like we have today. The information systems we have now makes it possible to give you this kind of performance." Pelletier praised the contributions of former Mack Chairman Zenon Hansen, who built the World Headquarters, raised a faltering company to new heights and made the Mack Bulldog a symbol of quality around the world. And he expressed full support for John B. Curcio, current president and CEO, who must keep Mack competitive with the construction of a state-of-the art assembly plant to replace the outmoded 5-C complex in South Allentown. Curcio, Pelletier noted, also must continue the cost-cutting programs that will make Mack a lean machine through the end of this decade. Among other observations that Pelletier made in a lengthy, often reminiscent, interview were these: - When Pelletier arrived in Allentown and told 600 employees at a sales meeting that he would visit every Mack dealer and facility in the nation, there were snickers in the audience. He and executive Gardner Davis did not realize it would taken them five years, traveling three days a month, to meet Mack's 240 distributors and representatives. - Pelletier saw immediately that he had to cut operational costs. Brockway, the truck-manfacturing company that Mack owned at Cortland, N.Y., had to be liquidated. Two Mack executive jets at Queen City Airport were sold off, but the helicopter was kept to shuttle customers and VIPs back and forth. Pelletier began running a much tighter ship as he'd done in Canada. - Mack's assembly plant at Hayward, California, site of the old Chris-Craft boatworks, also was closed. About 70 percent of the materials used at Hayward was being shipped in from east of the Mississippi River and roughly 75 percent of the assembled trucks were being shipped to the eastern market. It made no sense logistically. - Under his 10-year administration, Mack has had a reasonably good relationship with the United Auto Workers, even though a UAW strike shut the Allentown and Macungie plants for more than a month in 1984. "They try to do their best for their brothers and sisters, and there are some things that we feel we must have. So these issues have to be negotiated." Although Pelletier became involved in community activities shortly after he was named president and CEO, he was able to spend more time in civic leadership after Curcio took over those posts and shared the administrative responsibility. Pelletier spearheaded the public campaign that initially raised $250,000 for the Parkette Center that developed into a $750,000 building, then hit $1 million when air-conditioning was installed. But it is one of the finest gymnastic facilities in the nation used by Olympic stars, on occasions, for workouts. Pelletier, never a Boy Scout in his youth, was introduced to the organization when he chaired the Eagle Scout recognition dinner. Later he became a district chairman for the Explorer scouts and now has Mack sponsoring six Explorer units. On Jan. 20, he will complete his third and final year as Minsi Trails Council president. When he retires to his new home in Toronto with his wife Patricia, Pelletier will assist Canadian scouters in establishing an Explorer program, the first for Canada, in the Greater Toronto region. After serving as a division chairman for the United Way in Lehigh County, Pelletier accepted the campaign chairmanship in 1983 and headed a team that attained a record goal. He was a member of the Muhlenberg College Board of Associates and found time to promote the purchase of U.S. Savings bonds. Pelletier said that he was able to accomplish so much as a busy executive only with the help and support of his wife, who is an outstanding tennis player and tournament winner. Their son Douglas is a computer specialist for IBM Corp. in Bethlehem. Their two married daughters, Janet and Nancy, reside in the Toronto area. The couple has three grandchildren. Up at the strike of six every morning, Pelletier sleeps an average of only five hours a night and has conditioned himself to long, hard days. "I have the unusual ability to take catnaps during the day and awake refreshed. I nap on airplane trips when nobody else can," he chuckled. Just when friends expected Pelletier to unbuckle his seatbelt and put 47 years of the truckindustry behind him, Pelletier stunned many of them when he disclosed last month that he has accepted the post of president and CEO of Junior Achievement of Canada. Based in Toronto, he will work full time and use all of the experience he has gained while working with youth groups during his Mack tenure in Allentown. "If I had nothing to do in retirement, I would go nuts," Pelletier allowed. But do the Junior Achievement kids in Canada know that their new logo will be miniature bulldog?
-
Alfred W. Pelletier, 86, Dies – Former Mack Trucks CEO October 22, 2008 / The Morning Call Alfred W. Pelletier, age 86, slipped away peacefully in the early hours of October 21, 2008, after a long and brave struggle with Alzheimer’s disease. Born January 22, 1922, Al grew up in Toronto with his sister Lillian, his twin brothers Bernie and Leonard, and his mother, affectionately known as Chick. After graduating from the Danforth Technical School in Toronto in 1939, he joined the Toronto Transportation Company as an apprentice mechanic. In 1941, he volunteered for service in the Royal Canadian Navy. He remained in the service for the duration of World War II, with over three years on convoy escort duty in the North Atlantic aboard the H.M.C.S. Digby and H.M.C.S. Granby. Released from active duty as a chief petty officer in 1945, he rejoined the Toronto Transportation Company as a journeyman mechanic, and subsequently was promoted to shop foreman. In 1952, Al went to work for Mack Trucks Canada as the shop foreman of the Toronto factory branch. His hard work resulted in a promotion to district service manager for all of Ontario. After serving as the Toronto branch manager in 1966 and 1967; he rose to the position of general manager Mack Trucks Canada in 1970, executive vice president in 1971, and ultimately was appointed as president of Mack Trucks Canada in 1974. A natural leader, Al went on to become President, CEO and Chairman of the Board of Mack Trucks, Inc. He and his wife, Pat, and daughter, Nancy, moved to Allentown, where they lived for 10 years. During his tenure in Allentown, Al served as Chairman of the Minsi Trail Council, Chairman of the United Way of the Lehigh Valley, and Chairman of Vocational Clubs of America, where he was recognized by Ronald Reagan for his service to young people. He worked tirelessly to raise the funds needed to build the Allentown Parkettes Gymnasium. And he received Distinguished Citizenship Awards from both the Minsi Trail Council and the United Way, and he received an Honorary Doctor of Humanities from DeSales University. After 34 years in the trucking industry, rather than retire, Al accepted the post of President and C.E.O. of Junior Achievement of Canada. Al brought his strengths in management and visions of entrepreneurship to many aspiring young men and women. Al and Pat retired to Naples, Fla., where they enjoyed golf and tennis with their many friends. Among his many lifetime community contributions, Al spent every Thursday building homes for Habitat for Humanity in Florida. Summers were spent with the family at Lone Pine on beautiful Lake of Bays in Muskoka. Survivors: Al leaves his wife Pat; daughters, Janette (Carl Corter) and Nancy Bowen (John); son Doug (Kelly); grandsons Jason (Angela), Ryan, Randy, Scott and Brad; and step-grandchildren David (Gabriella), Arden, Tony, Annie. Al will be remembered for his warmth and generosity, his many invented catchphrases, and above all, his love of family. .
-
Reuters / October 20, 2015 AB Volvo said on Tuesday it signed a letter of intent with HCL Technologies to sell its external IT business. The deal is expected to raise Volvo’s operating earnings by about US$108.5 million (900 million Swedish crowns). The Swedish company said about 2,600 Volvo staff would be affected by the transaction and offered employment at HCL. The deal is expected too close during the second quarter of next year. "Not only will our cooperation with HCL Technologies provide significant cost-savings. We will also make a capital gain when the contract is signed," Volvo's acting chief executive Jan Gurander said in a statement. The sale of Volvo's external IT operations is part of sweeping efficiency measures aimed at cutting 10 billion crowns of structural costs at the truckmaker. In October 2012, Volvo sold its aerospace division, Volvo Aero, to British engineering group GKN for US$1.05 billion (6.9 billion Swedish crowns). Volvo Press Release - http://www.volvogroup.com/group/global/en-gb/newsmedia/_layouts/CWP.Internet.VolvoCom/NewsItem.aspx?News.ItemId=151137&News.Language=en-gb
-
adding air ride cab on a RD822sx
kscarbel2 replied to m16ty's topic in Exterior, Cab, Accessories and Detailing
The answer is yes. And there's a Mack service bulletin that lays out the parts required and installation. Now whether or not those parts are still available thru the Volvo parts distribution system is another matter. -
Kenworth Offers Two-Hour Truck Repair Diagnosis
kscarbel2 replied to kscarbel2's topic in Trucking News
Kenworth Dealers Add New Facilities, Extended Hours Trailer/Body Builders / October 20, 2015 Kenworth dealers have invested nearly $500 million in new and relocated facilities in the past five years, according to Jason Skoog, Kenworth assistant general manager for sales and marketing. “That is reflected in a 20 percent growth rate for dealership locations,” he said. “We now offer over 360 locations in the United States and Canada, and nearly 75 percent of those locations are full-service stores.” Skoog said the growth is in response to the change in the industry, and to be ready for future needs of customers. “With a strong truck market over the past few years, along with improving retail market share, there are more Kenworth trucks on the road than ever before,” he said. “And, as trucks become more complex and computer-based, dealers become an integral part for service. Downtime is no longer an option in our industry. Uptime is what it’s all about, which is also driving us to expand to be closer to where our customers need us. The partnership between customers and Kenworth dealers will only become stronger. Our dealers are there for full vehicle support, from cradle to grave. They’re the backbone.” Skoog offered some examples of recent dealer expansion. “Wisconsin Kenworth recently broke ground on a 75,700-square-foot facility just outside Madison. They’ll include Kenworth PremierCare ExpressLane bays for 2-hour diagnostics and estimates, which is part of new Kenworth’s PremierCare Gold Certified program that we’ve just announced,” he said. “What’s more they’re building a specially equipped area to service CNG powered units.” “This new state-of-the-art facility will ensure that we are able to meet the technological demands of an ever-evolving industry and allow our dedicated employees to continue to deliver Kenworth quality service to new and existing customers," said Jim Moeller, CEO of CSM Companies, which is the parent company of Wisconsin Kenworth. “We’re growing and building along with other Kenworth dealers throughout the country.” MHC Kenworth has been rapidly expanding its dealership network, growing from 37 locations in 2010 to 67 locations in 2015. This year alone, the dealership group added 10 new locations. “We are in constant pursuit to support customers with convenient locations and service points,” said Tim Murphy, CEO of MHC Kenworth. “This year MHC expanded into its 16th state and opened its 67th location.” According to Murphy, all MHC dealerships locations are open extended hours, with 21 open 7 days a week, 24 hours a day. “MHC continues to invest in its dealerships by renovating and building new, state-of-the-art facilities,” added Murphy. “This is to provide customers access to more services and amenities, while decreasing the time their trucks are off the road.” In Alberta, Edmonton Kenworth made a major investment on a 16-acre parcel in Leduc near the Edmonton International Airport. Just opened, it features an 111,500-square-foot main building with an indoor showroom large enough for customers to view up to four Kenworth trucks out of the elements. The main building also offers several specialty bays to provide service for fabrication, component rebuild and liquefied natural gas-powered commercial vehicles, plus four triage bays to provide customers rapid diagnostic reports. Here are the 25 dealerships that have invested more than $1 million in facility improvements in 2015 - Bayview Kenworth - Woodstock, New Brunswick; Central Illinois Trucks - Green Oaks, Ill.; Custom Truck Sales - Swift Current, Saskatchewan; Edmonton Kenworth - Leduc, Alberta; Inland Kenworth - Phoenix; Kenworth Northeast Group - Brockton, Mass.; Kenworth of Cincinnati - Cincinnati, Ohio; Kenworth of Pennsylvania - York, Pa.; Kenworth of South Florida - Fort Myers, Fla.; Kenworth of South Louisiana - Bossier City, La.; Kenworth Quebec - Saint-Georges, Quebec; Kenworth Sales Company - Salina, Utah; Kenworth Toronto - Kitchener, Ontario; MHC Kenworth dealerships in Denver, Colo.; Macon, Ga.; Cedar Rapids, Iowa; Kansas City, Mo.; Kingsport, Tenn.; and South Fort Worth, Texas; New England Kenworth - Southern Maine; Performance Kenworth - Beaumont, Texas; Truck Enterprises - Hagerstown, Md.; Wichita Kenworth - Dodge City, Kansas; Wisconsin Kenworth - Madison, Wis.; and Worldwide Equipment - Prestonsburg, Ky. -
Heavy Duty Trucking / October 20, 2015 Kenworth is rolling out a service program for its trucks at certified dealers that would provide a full diagnostic analysis and repair estimate within two hours, the company announced at the American Trucking Associations' (ATA) Management Conference and Exhibition in Philadelphia. The service would be offered under the Kenworth PremierCare Gold Certified program as a way to reduce truck downtime for commercial customers. Kenworth Gold Certified dealers would provide the servive at their Kenworth PremierCare ExpressLane with dedicated technicians that can provide the quick diagnosis and estimate repair time and cost, according to Kenworth. "The goal is to do away with trucks sitting in the queue and drivers waiting for an estimate," said Jason Skoog, Kenworth's assistant general manager for sales and marketing. "And that's critical to our customers, especially when the repair may be very simple and can be completed within hours. Knowing what’s happening, quickly, will help customers make the decisions needed to keep their deliveries on schedule." The program also includes an around-the-clock roadside assistance program supported by a call center to help drivers and fleet managers work through the issue. The dealers also offer extended evening hours on weekdays and the weekends. Diesel technicians at Kenworth Gold dealers will have "achieved the highest levels of certification." In addition, new Kenworth Class 8 trucks with the PACCAR MX-13 engine are now standard with Kenworth TruckTech+. The system enhances vehicle diagnostics by providing information on engine health to the customer and dealer.
-
Fleet Owner / October 20, 2015 At the American Trucking Associations Management Conference & Exhibit at the Philadelphia Convention Center on October 19, Mack Trucks announced the creation of certified uptime centers, a new dealer service certification dedicated to maximizing customer uptime. Mack stated that its certified uptime centers are the latest extension of Mack’s commitment to keeping customers’ trucks and operations at peak productivity. “Thanks to standardized workflows and service processes, as well as redesigned service bays, certified uptime centers will enable faster and more efficient service and repair,” the company said. “The revisions will also offer more transparent information to the customer, helping them to make quicker decisions for their business.” “This certification goes beyond just improving diagnostic times,” said President Stephen Roy. “We’re increasing customer uptime by changing our approach to the service process, ensuring our customers’ trucks are diagnosed and repaired efficiently and returned back to them as quickly as possible.” Certified uptime centers will feature “uptime bays” reserved specifically for trucks with service and repair tasks requiring less than four hours of work. Customers with vehicles needing a quick repair will be rapidly diagnosed, serviced and returned to work, increasing efficiency at the dealership and improving a customer’s ROI, Mack said. Mack’s Uptime Solutions, including Mack GuardDog Connect telematics and Mack ASIST service management system, will be built into the new Mack Certified Uptime Centers’ workflows. Mack’s recently announced integration of Truck Diagnostics System (TDS) and Mack ASIST will also support certified uptime centers. Mack is currently piloting the certification at 21 locations throughout the U.S. and Canada. “The certified uptime centers pilot has significantly reduced the amount of time we’re spending on diagnostics and has also allowed an increase in technician productivity,” said Jon Miller, service manager at Vanguard Truck Center of Phoenix, one of the pilot locations. “Our customers have noticed they’re getting their trucks back more quickly, as the new workflows are helping us be more efficient and move trucks through the repair process faster.” Mack will continue its certified uptime centers pilot through 2015, and will begin the rollout of the certification to the Mack Trucks dealer network in 2016.
-
- 1
-
-
Fleet Owner / October 19, 2015 The goals for the next round of federal truck fuel efficiency requirements will be achievable, says the head of the country’s largest truck maker—he’s just not sure yet what the solutions are going to be. And all bets are off if the EPA’s Phase 2 greenhouse gas (GHG) reduction program strays from the preliminary standards proposed earlier this year, Daimler Trucks North America President and CEO Martin Daum told trucking media representatives during a roundtable discussion here. That proposed target is a 24% improvement in heavy-duty fuel efficiency by 2027, which Daum concedes is “a lot.” The good news is the company has “ideas for the first steps,” but where those steps will lead is to be determined. “You can’t have this for nothing. You have to invest and you have to start today thinking about how,” Daum said. “I’m confident we can reach it, but I don’t know how.” While DTNA is generally supportive of the program’s goals, Daum objected to a possible engine-only standard separate from the vehicle requirements. “I’ve never seen an engine alone running down the road,” he quipped. “We need all the pieces to fit together to optimize [fuel efficiency]. But the higher the engine standard, the less room we have for optimization.” He does credit EPA with being “fully aware of the complexity” of the rulemaking, and for working with the industry as well as with environmental advocates and state and local air quality agencies to develop the plan. DTNA also would like to see a single national standard, but the real concern is for the possible development of a new, lower NOx regulation. His concern is that the GHG rule will be finalized and manufacturers will begin to work toward meeting the requirements, and then EPA will set another NOx limit. And that will cause an industry "disruption" similar to 2006. “Don’t touch NOx,” Daum said. “Our entire positive-challenge outlook is off, the moment we get a NOx rule. A NOx rule won’t benefit our customers, it will just make trucks more expensive. This would be very short sighted.” Indeed, some 3 billion gallons of fuel are wasted due to congestion each year, outweighing many times over the projected fuel savings for the Phase 2 rule, according to DTNA. So Daum suggests that policy makers should focus first on relieving traffic bottlenecks, which account for 40% of that wasted fuel. Sean Waters, DTNA director of compliance and regulatory affairs, added that’s he’s “optimistic” the EPA leadership will listen to the recommendations of the agency engineers rather than be swayed by emotional appeals and political considerations. He suggested that both the 24% improvement and the 2027 timeline likely will be features of the final rule. But he admitted to being somewhat “worried” about the date's being moved up due to a “campaign of sorts” that generated some 150,000 “generic” comments from individuals calling for a speedier implementation. “We don’t think moving the 2027 standards to 2024 is possible because we don’t have time to invent the technology,” Waters said. “It’s hard to speculate what they’re going to do, but EPA and NHTSA are data-driven organizations—and the four truck OEMs have jointly stated that it’s not possible.” As to NOx, Waters too explained that there are “far better” and “less disruptive” solutions for improving air quality other than imposing a new standard on trucks, although California specifically is looking for tighter regulations “NOx and CO2 are inextricably intertwined in the engine—that’s a physics problem we can’t overcome—but if you use less fuel you will also end up with less NOx,” Waters said. “The number one thing California could do would be to accelerate fleet equipment turnover. The vast majority of trucking companies are still using pre-EPA10 trucks and, given the NOx reduction since 2010, getting new trucks on the road would the fastest way to achieve better air quality standards.”
-
Car & Driver / October 20, 2015 Todd McCann started driving big rigs in 1997 and covers about 125,000 miles a year on America’s highways. In other words, he knows driving. (He also runs the hilarious Trucker Dump podcast.) It’s hard to imagine anyone with a better perspective on the best and worst of highway driving than a guy who spends every day, week after week, sitting high up behind the wheel of his rig, watching cars ahead, behind, and alongside. We asked him to tell us what mistakes he sees again and again, and how we can all be better drivers. This should be obvious: Pay attention. People don’t pay attention. They are in their own worlds because of cell phones. That’s why they get caught riding on the right side of the road. That’s why at the last-second they realize they are about to miss their turn. About 75 percent of the time when they are trying to merge onto the highway and are trying to push me over—which is ridiculous in itself—it’s because they are looking up at the last second from their cell phone. They realize that they should worry about merging and you see the cell phone vanish. They put the phone down and look up at you like, “You didn’t see that.” I’m not one of these guys who thinks that if you’re texting going down the road, you’re a danger to everybody. If it’s a quick text, I don’t see it as being much more dangerous than fiddling with your radio station, as long as there isn’t a bunch of traffic around. But I’m in Jersey right now and I see it on I-95 all the time where there’s a ton of traffic and there are people cruising by on their phones. That’s just amazing[ly dumb]. Stop hanging out along my side. Have you ever seen the signs on the back of trucks that say, “If you can’t see my mirrors, I can’t see you?” I get what they are trying to do with that, but that rule is not entirely true. It’s true that you shouldn’t tailgate a truck but the sides are just as bad. I had a car riding on my right side the other day, just hanging out. That’s the worst thing any driver can do. We have a huge blindspot over there. I almost ran this guy off the road because I couldn’t see him. He was riding right in my tractor tires. According to that rule, he was okay because he could look up and see my mirror. But I couldn’t see him. He was nowhere to be found. I didn’t see the car until he popped up in another mirror as he was going off on the shoulder. He was right along my right-hand side. What can I do? Personally, I don’t understand why anyone would want to ride beside a truck at all. When I’m in my car, even before I was a trucker, I would get around those trucks as soon as possible. The tires are almost as tall as your car. If there’s a blowout, it’ll tear your car up. It just makes no sense to me. The old three-lane pass is a big problem. That’s when a car is way over in the left-hand lane and passes right in front of you at the last second to hit an exit ramp. You just dove over three lanes! And you have no idea what’s over there on the other side of me. A crotch rocket could have been whipping by me at 90 mph and you would have just killed him dead. It blows my mind, especially when you see it’s a soccer mom with a van full of kids. At least if they are doing that around a car, it makes more sense. At least you can see around a car. You can’t see around a truck. That’s just insane. Stupid is everywhere. It really is. Some areas are worse than others. I think LA has taken the Fast and Furious movies seriously. They drive crazy out there, especially when the bars are getting out. It’s nuts. You see crotch rockets going by you at 100 miles-per-hour, weaving in and out of traffic. The little souped-up cars do that, too. But the East Coast is bad, too. People in the Midwest seem to be more relaxed. The more crowded the area, the more stupid things you see. Construction areas are especially scary. If you get a construction area, no matter where you are, people are doing something stupid. Here’s the thing that makes me the maddest during construction: I’ll be cruising along in the left-hand lane of a two-lane highway going 50 mph because that’s what the signs say to do. I have people driving around me on the right-hand side, which is about the only time they should be doing that, but they are flipping me off. You can see the road rage because I’m in the left lane going 50. They could be doing it while they are passing the sign that says, “Trucks, left lane only. 50 mph.” They are just not paying attention to the signs. They think truckers are bad drivers. We are not. Two-thirds of accidents between a truck and a car are caused by the car. People think we are the safety hazards. But we’re not. We know how to drive defensively. If we drove like car drivers, changing lanes as quickly and as non-nonchalantly as they do, and slamming on the brakes, there would be a lot of accidents out on the road. There would be a lot of deaths. Be consistent with your speed. The fluctuating speed thing causes so many problems. People just don’t pay attention to how fast they are going. They take their foot off the gas and then put it back on. For a truck, that’s the worst, but it causes problems for everybody. I was coming up from Richmond, Virginia yesterday. There was a small Winnebago that was going 10 mph under the speed limit. It was causing all kinds of problems. One vehicle was backing up three lanes of traffic. I wish people would just pay attention. If a trucker is tailgating you, you’re probably going too slow. If you see a truck in your rearview, the first thing you need to do is put down your phone. The second thing you need to do is look at your speedometer. The majority of the time, if a trucker is tailgating you, you’re doing something wrong. My truck is limited at 64 mph. If I’m tailgating you because you’re going too slow, that’s a problem. I’m not talking tailgating like getting one car length behind them and flashing my lights. I’m talking three or four car lengths. Just enough to make them want to cuss me real bad. If they scoot over and get out of the fast lane, mission accomplished.
-
So your engine, E7-250, is governed at 1950 rpm. I wouldn't turn up the rpms. No Mack single axle has a 4.30 axle ratio. Maybe you misread the last digit. What's the axle model? If it's a Mack rear, it begins with "RA"
-
Why haven't these murderers been summarily sentenced to death? They savagely ripped away a 5-year-old child's god-given right to a lifetime on earth. Where is the justice? If you intentionally and criminally take a life, you lose your own. ------------------------------------------------------------------------------------------------------------- Three Milwaukee men murder 5-year old girl Reuters / October 20, 2015 Three black Milwaukee men accused of targeting the wrong house in a revenge shooting last year were charged on Tuesday in the death of a 5-year-old white girl as she sat on her grandfather's lap watching television, police said. Arlis Gordon, 23, and Carl Barrett, 20, were charged with first degree reckless homicide and Paul Farr, 24, was charged with two counts of harboring and aiding a felon in the fatal shooting of Laylah Petersen in 2014, according to a criminal complaint filed in Milwaukee County Circuit Court. Milwaukee Police Chief Edward Flynn told a news conference the men were seeking revenge for a jury's acquittal in November 2014 of a man who was accused of killing Gordon's step-brother. After the verdict, Farr drove Gordon and Barrett to a house where they thought the defendant's girlfriend lived, Flynn said. Gordon and Barrett got out of the car four blocks from the intended target and fired into the wrong house, he said. The barrage of gunfire fatally wounded Petersen while she was sitting on her grandfather Robert Fogl's lap watching television in the living room, the complaint said. Flynn pulled a large button with a photograph of the girl from his shirt pocket in announcing the charges on Tuesday. "I've been carrying something around with me, and it's Laylah," Flynn said. "I'd like to think we can put her to rest now." Barrett and Gordon could be sentenced to up to 60 years in prison if convicted and Farr up to 10 years in prison. The men were arrested over the past week after police heard stories linking the three to the shooting. They are now in custody. .
-
Arizona father drowns wife, 3 toddler children Associated Press / October 19, 2015 The deaths of two adults and three young children who were in an SUV that plunged into an Arizona lake are being investigated as a murder-suicide as police said Monday that the father of the toddlers deliberately drove the vehicle into the water. Police spokesman Lt. Mike Pooley said 27-year-old Glenn Edward Baxter purposefully drove himself, his estranged wife and their children into Tempe Town Lake just after midnight Sunday. A surveillance video from a nearby condominium complex showed the car being driven into the lake. The video shows Baxter getting out of the SUV, walking down to the lake, then getting back in the driver's seat and driving the vehicle "at a high rate of speed" before it hits a curb and flips over into the water. "This was not an accident. Mr. Baxter took deliberate action," Pooley said. "It's absolutely horrific what happened to those little kids and their mother." Witnesses and officers jumped into the lake in a bid to rescue Baxter, 25-year-old Danica Baxter, and their three children, 1-year-old Zariyah, 2-year-old Nazyiah and 3-year-old Reighn. The children's great-grandfather had expressed his doubts earlier that the deaths were accidental, saying the children's mother had declined her estranged husband's attempts at reconciliation because he hadn't addressed his anger management problems. George Britt said it doesn't make sense that the early-to-bed-early-to-rise mother would take her children out for a ride just after midnight. "She is never up at that time of the night," Britt said. "Never, never." Investigators believe Baxter and his wife met late Saturday night to talk about their children and an argument ensued. Police found a handgun in the SUV, but it's unclear if Danica Baxter was being held against her will at the time of the incident. The couple married in April 2012, and relatives said they separated several months ago. Tamika Franklin, an aunt of Danica Baxter, described her as an excellent mother who adored her children. "Everything she did was for her kids. Her kids were her life. She would never do anything to hurt her kids," she said as she began to cry. The parents and the two youngest children were pulled from the vehicle and brought to a hospital, where they later died. Investigators then determined the couple's oldest child was missing, and divers later retrieved the child's body from the still submerged vehicle.
-
Missing 11-year-old child found in freezer Associated Press / October 19, 2015 The body of an 11-year-old girl who had been missing since August 2014 was found on Sunday inside a locked freezer owned by her mother. Officials from Child Protective Services (CPS) visited the West Bradenton, Florida, apartment of Keishanna Thomas last Friday, expecting to find five children between the ages of 2 and 15 years old. Instead, they only found four: Missing was 11-year-old Janiya Thomas, who had not been seen since August of 2014. Keishanna Thomas would not divulge her daughter's whereabouts – even after being arrested and appearing before a circuit court judge. For her alleged refusal to cooperate, she was held on a contempt of court charge. After noting her disappearance, police began an investigation to find Janiya. At 7 p.m. Sunday, we received a phone call from a family member of Janiya Thomas, telling us the location where she might possibly be located," says police spokesman Lieutenant James Racky. "We went to that location and were told there that the body of the child may be in a freezer." Keishanna Thomas and a male friend had previously moved the locked freezer to the home of Janiya's aunt and grandmother. After Thomas' arrest, they broke the lock on the freezer and found the girl’s body. Janiya had intestinal issues making her unable to control her digestion and bowel movements. It was quite serious – and could ultimately have been fatal. "That medical condition is the same one that killed her father," said Racky. Authorities say that Keishanna Thomas was annoyed by her daughter's condition and locked her in the bathroom rather than allowing her access to other parts of the apartment. Janiya was pulled from school in 2013. That same year, her mother told CPS that she had begun homeschooling the girl. When asked how the girl celebrated her birthday last year, the child said Janiya just stayed in the bathroom. One child said the mother used a belt and punched Janiya. One child told police that Thomas punished Janiya for soiling herself by leaving her inside a bathroom for long periods of time. When asked how long, the child said it was a week or so, with Janiya even eating in the bathroom. He said his mother slept in the front room so she could catch Janiya if she tried to sneak out at night. The siblings of a missing 11-year-old Florida girl told child welfare investigators that they went to school one day and never saw their sister again, and one boy told them, "I think she is dead or something." --------------------------------------------------------------------------------------------------- Update: Associated Press / October 27, 2015 The mother of a girl found dead in a freezer was accused of beating her five children for years in a home that at times was filled with rats and roaches, according to documents released Tuesday. The documents, released by the Manatee County Sheriff's Office, show child welfare investigators visited the home of Keishanna Thomas 10 times amid allegations that she beat one of her children with an electric cord leaving welts, burned another child with bleach so badly her skin was discolored and left another child with 22 scars. Despite evidence of abuse, investigators wrote in their reports that the children were not in imminent danger. One of the children was removed from the home in 2004, but she was later returned to her mother, whose criminal history includes arrests on charges of battery and drug possession, the documents say. Details about when and why that child was returned were not clear. In September, another call came to the state's child abuse hotline, claiming Thomas beat her 12-year-old son for stealing candy. It was then that they discovered no one had seen her 11-year-old daughter Janiya for more than a year. Her siblings told investigators they came home from school one day, and she was gone; they presumed she was dead. A padlocked freezer was left by Thomas and another man at the home of Janiya's grandmother, she and the girl's aunt told authorities. Inside was a body that officials confirmed on Monday was that of Janiya. The grandmother and aunt say they didn't realize what was inside. Janiya's mother had initially been jailed on contempt and child abuse charges because she refused to talk about the girl's whereabouts. The contempt charge has been dropped, though she is jailed on a charge of abuse of a corpse. It's unclear how the child died. Police say they need to do more testing. The Department of Children and Families has removed Janiya's four siblings, and Secretary Mike Carroll said his agency is investigating whether anything could have been done differently to prevent Janiya's death. The sheriff's office is in charge of child welfare investigations in the area and handled the Thomas case for years. The agency did not immediately return emails seeking comment Tuesday. But the documents released by the agency portrayed a violent family life, including six cases alleging physical injury to the children and two cases of family violence, as the single mother struggled to control her anger and appeared to take it out on the children. "The mother is consistently uncooperative with (investigators), and she does not follow through with services when they have been offered and put in place. The children have become increasingly fearful of their mother and frequently feel unsafe in their home environment," investigators wrote after visiting the home last month. But for years, investigators dismissed safety threats. In 2004, one of the children had 22 scars and said her mother beat her. A few years later, a child who cannot use one arm had been hurt in a fall and appeared to have scratches on her face. But the girl was afraid to talk to investigators and said only that she fell. Investigators came to the home again in 2012 after one of the children had burns on his arms and legs, but officials wrote "there are not negative implications based on signs of present danger." Last year, one of the children said his mother pulled down his pants and beat him with an electric cord. A doctor who examined the child also found the marks were "abusive and consistent with being hit with an electrical cord." Thomas said she hit the child with her hand and said the child had been lying and stealing. Investigators again filled out paperwork alleging the children were not in imminent danger. Most recently, the girl's siblings told investigators Thomas punished Janiya for soiling herself by leaving her inside a bathroom for long periods of time. When asked how long, they said it was a week or so, with Janiya even eating in the bathroom. The mother slept in the front room so she could catch Janiya if she tried to sneak out at night. When asked how the girl celebrated her birthday last year, the child said Janiya stayed in the bathroom. Another child said the mother used a belt and punched Janiya.
-
What's your rear axle ratio and tire size?
-
Scania Group Press Release / October 19, 2015 Sustainability needs to be much more than a corporate vision of a distant future. Action speaks louder than words, and Scania's sustainable transport solutions are ready here and now.
-
Well, there you go. You're driving a piece of proud Mack history.
-
Great. All any Mack dealer needs to hear is RD822SX - 1100, and they can research the truck parts you need. Mack trucks sold to the military still have normal model and VIN numbers. Only once in a great while was a truck missing from the Mack parts system, or the information in the system was incomplete. I suspect your truck was one acquired to meet a "war emergency" requirement for Operation Desert Storm (http://www.bigmacktrucks.com/index.php?/topic/34637-mack-people-and-trucks-tackle-the-eye-of-a-storm/?hl=stockertown), and was later turned over to the National Guard. It was a civilian model, and most likely repurchased from a dealer by Mack Trucks for the short-notice requirement.
-
Truck Sales Australia / October 20, 2015 The 300th Kenworth for Lindsay Transport was handed over at the Kenworth Bayswater plant recently, celebrating a relationship that goes back almost 45 years. Lindsay Brothers first began carting produce in the Coffs Harbour area in 1953, when Tom Lindsay and his late brother Peter bought three trucks from their father, Victor, and started transporting bananas. Today, Lindsay Australia Limited, has grown into an Australian Stock Exchange-listed transport, logistics and rural supply company, and runs a fleet of more than 250 prime movers operating out of 33 stores and depots from Adelaide to Mareeba. From its head office in Brisbane, Lindsay Australia employs over 1,100 people and generates revenue of approximately $310 million per year. The company has also diversified its operations, now hauling fresh and frozen produce, as well as general and express freight from Adelaide to Lakeland Downs (near Cooktown). Currently, the Lindsay Transport fleet travels over 57 million kilometres each year. Lindsay’s Kenworth stable comprises a mix of cabover and conventional models for B-Double and 19-metre line-haul applications. One of Kenworth’s major advantages is the ability to spec trucks for a variety of high utilization applications, which often sees a truck travel more than 500,000 kilometres a year. At the handover event, Kim Lindsay, Managing Director of Lindsay Australia said: “We have been working with PACCAR and the Brown and Hurley Group now for many years. They understand our trucking needs – and deliver outstanding sales, service and support Australia wide. PACCAR’s commitment to quality and innovation has helped Lindsay Transport to grow and maintain a large and diverse fleet so we can deliver our service promise to our customers.” The milestone T409 will go into 26-metre B-Double line haul service hauling refrigerated produce on interstate routes. The vehicle, powered by a 15-litre, Cummins ISX e5 engine with an Eaton Ultrashift Plus transmission, has a number of distinctive features, including gold coloured logos, personalised exhaust shields, a stainless-steel light bar and a specially embossed interior highlighting the 'Lindsay Transport 300th Truck', just to name a few. Related reading - http://www.kenworth.com.au/trucks/t409/ .
-
Heavy Duty Trucking / October 19, 2015 Detroit Connect has introduced new features for its Virtual Technician remote diagnostic system, including a new portal that lets users dig deeper into the data, and for some 2017 models the ability to "flash" software updates and parameter changes to the truck over the air. “Intelligent connectivity is at the core of what we are offering to drivers and fleet managers,” said Matt Pfaffenbach, director, telematics for Daimler Trucks North America. “By adding new technologies that provide more meaningful insights and visibility, we are further contributing to increased uptime, safety and efficiency.” A new portal will provide Detroit Connect users additional information about overall fleet health, as well as enable them to take a deeper dive into specific fault events communicated via Virtual Technician. The portal, available on all Freightliner and Western Star models with Detroit engines, will also allow users to view and archive Detroit Diesel Engine Control (DDEC) reports, which use diagnostics to further analyze driver and vehicle performance. The portal, which will serve as the access point for all services offered by Detroit Connect, will also include options for communications, reporting and subscription management customization. Detroit Connect is piloting the portal with select customers beginning now, through early 2016, with an anticipated rollout to all customers by spring 2016. “Every customer has different concerns and ways of analyzing and acting on fault information, so we developed the portal to specifically make the fault information as manageable and consumable for every priority,” said Pfaffenbach. Over-the-air updates Farther down the road but perhaps more exciting, DTNA is developing a new telematics platform that will be available on select truck models in 2017. The platform will have new connected vehicle communications hardware that can be used globally. This will enable integration with third-party applications, and will reduce the need for additional hardware. The new telematics platform – which will use cellular service connectivity – will mark the introduction of flash over-the-air capabilities for Detroit, including remote vehicle parameter settings, remote downloading of DDEC reports, and remote flashing of firmware for electronic controllers. "To me this is overdue," said DTNA CEO Martin Daum. "You don’t go to the Apple Store every time you update an app, so why expect it from the truck?" Pfaffenbach noted that fleets will also have the ability to do parameter updates, such as changing the mph limit on speed govenors. "i also hear from fleets that they want confirmation that the vehicle in operation is as it was configured, that someone has not messed with the paramaters, and this technology will give them the ability to do that," he said. “Vehicle connectivity is going to continue to have a significant impact on how customers do business, and DTNA will continue to push the envelope to be part of that evolution,” said Pfaffenbach.
-
Fleet Owner / October 19, 2015 Look for 2016 truck sales to fall somewhere between the exceptionally strong numbers of 2015 and those seen in 2014, according to Martin Daum, president and CEO of Daimler Trucks North America (DTNA). With production plans essentially in place through the end of the year, Class 6 through 8 sales in North America should top 435,000 trucks, he said during a press conference at the American Trucking Assns. Annual conference. That would be 13.4% above 2014 sales, which totaled 384,000. With fleets now in the middle of their ordering cycle, Daum said, “I’m fairly confident that [Class 6-8 sales] will be lower than 2015, but better than 2014.” While the new year’s truck totals might suffer in comparison with the strong 2015 numbers, “2014 was a good year,” he said. “Everyone had happy faces then, so why not again.” October and November order intake for delivery in 2016 will be significant lower than last year, which Daum characterized as “not normal,” and driven by fleets rushing to reserve production slots in anticipation of a strong truck sales year. “Don’t be fooled [by the lower order intake]. Compare it to Q4 2013, not to Q4 2014, which would be misleading.” Focusing on the U.S., Daum expects Class 8 sales to reach 262,000 trucks by the end of the year, compared to 220,000 in 2014 for an 18.8% gain year over year. Classes 6 and 7 will finish out 2015 at 114,000 units, which is well above the 106,00 recorded in 2014, but still below what DTNA considers a normal annual volume of 135,000. “We’re seeing a slow and steady recovery [in Classes 6 and 7], and expect that trend to continue in 2016,” Daum said. In other news, Daum said DTNA was “tiptoeing at full speed” into extending remote connectivity for its trucks. During ATA the company announced that it was launching remote software updating for its trucks, and Daum said the company was committed to accelerating development in the area of connectivity “even though it is a big challenge in uncharted territory.” Daum also hinted that DTNA would be introducing it’s next generation heavy truck later in 2016, but declined to give more details.
-
Commercial Carrier Journal (CCJ) / October 19, 2015 And then there were none. Peterbilt on Monday announced its plans to join every other major North American truck OEM in sitting out the 2016 Mid-America Trucking Show (MATS) in Louisville, Ky. “After carefully considering our marketing strategies for next year and beyond, Peterbilt has decided to exhibit at the Mid-America Trucking Show on a bi-annual schedule,” Peterbilt Public Relations Manager Derek Smith says. “We wish MATS success in 2016 and we look forward to participating in the 2017 show.” Pete’s sister company Kenworth made its plans to skip MATS next year known this weekend at the American Trucking Association’s Management Conference & Exhibition in Philadelphia. Daimler Trucks North America, the first to pull out of the show, cited its preference to see the annual MATS show adjust its cycle to odd-numbered years, a move that would relieve conflict for global truck OEs also attending the IAA Commercial Vehicle Show in Hannover, which is held on even numbered years. A sentiment, Smith says, Peterbilt’s parent company echoed. “Peterbilt is a Paccar company, a global leader in the manufacturer and support of commercial vehicles, and the bi-annual MATS show strategy will be complemented by Paccar’s participation at IAA, held every other year in Hannover, Germany,” he adds. Navistar, Mack Trucks and Volvo Trucks North America have each also previously announced they would skip MATS in 2016.
-
Heavy Duty Trucking / October 19, 2015 As Navistar continues to make progress putting the “dark days” of its failed EPA 2010 emissions strategy behind it, the truckmaker will re-brand its product lineup as it rolls out new models starting next year. In an interview during the American Trucking Associations’ annual Management Conference & Exhibition, Jeff Sass, senior vice president for truck sales and marketing, said he thinks truck sales overall next year will be good for International as well as for the industry overall. Looking ahead to 2016 expectations, “I think it’s going to be strong,” said Sass, who joined Navistar about four months ago after a 20-year career at Paccar. “It probably won’t be as high [as 2015] in the on highway sector, maybe down 5%. The vocational sector will be flat to up a little bit and we feel medium-duty will be up.” As far as International trucks specifically, Sass sees "nothing but upside” next year. “We’ve gained a couple points of [market] share in medium this year, and we plan to gain a couple more points in medium next year. We think we’ll see an uptick in market share for our on highway product as well. and with the introduction of our new vocational product I think we’ll see growth there.” The new vocational product, which will replace the PayStar, will be unveiled in February during the World of Concrete event in Las Vegas. It is scheduled to start rolling off the line in April, just in time for the construction season. The “star” nomenclature will be retired in favor of a letter-and-number system. The vocational truck will be referred to as HX, followed by a 3 digit code signifying whether it’s long or short hood and set-forward or set-back axle. Next up will be a replacement for the ProStar, which will be called the LT series. It’s scheduled to be introduced in a late summer time frame, and will feature the new configurations to meet 2017 greenhouse gas regulations. The upcoming Class 4/5 product being co-developed with GM also will use the same naming style: CV, for commercial vehicle. The Chevrolet version will have some different styling and a different name. Why the move to a different naming convention? “It’s just time,” Sass explained. “We have a chance for rebranding and an opportunity to provide the customer with a new experience with Navistar in their International products.”
-
Fleet Owner / October 19, 2015 A recently released study from the National Resource Council of Canada determined that the combined use of a rear fairing and trailer skirt provides a 10% increase in aerodynamic efficiency above the sum of the individual products. The review, conducted from 2012 to 2015, used products comparable to the Stemco TrailerTail and EcoSkirt in a 30% scale wind tunnel to evaluate the benefits attainable by a variety of commercial trucking aerodynamic devices, Stemco said. According to Stemco, the study revealed that “side-skirts and boat-tails provide the greatest drag reductions” among the devices studied. The findings, the company stated, determined that users can save nearly 1,400 gallons (5,300 liters) of fuel per truck, per year by using both a rear fairing and side skirt. "In our study, we were excited to see that adding skirts and tails were actually mutually beneficial at multiple yaw angles," said Brian McAuliffe, senior research officer at the National Research Council of Canada. "We hope our study will help North American trucking fleets become more fuel efficient and better understand the aerodynamic benefits of current and future technologies." Stemco said the NRC test also confirmed research completed by the company, which indicated that a 4-sided, 4-foot-long TrailerTail 4x4 delivers slightly more drag reduction than the 3-sided, 3-foot-long TrailerTail Trident. However, combined with Eco-Skirt, both TrailerTail 4x4 and TrailerTail Trident models meet the Environmental Protection Agency’s proposed GHG Phase 2 regulations, according to Stemco. "The NRC study further validates that a TrailerTail and EcoSkirt should be essential elements in modern fleet operations," says Al Smith, director of sales for Stemco Innovative Tire & Mileage Solutions group. "Companies could be losing over a thousand dollars in fuel costs per trailer per year by only using one or the other." .
BigMackTrucks.com
BigMackTrucks.com is a support forum for antique, classic and modern Mack Trucks! The forum is owned and maintained by Watt's Truck Center, Inc. an independent, full service Mack dealer. The forums are not affiliated with Mack Trucks, Inc.
Our Vendors and Advertisers
Thank you for your support!