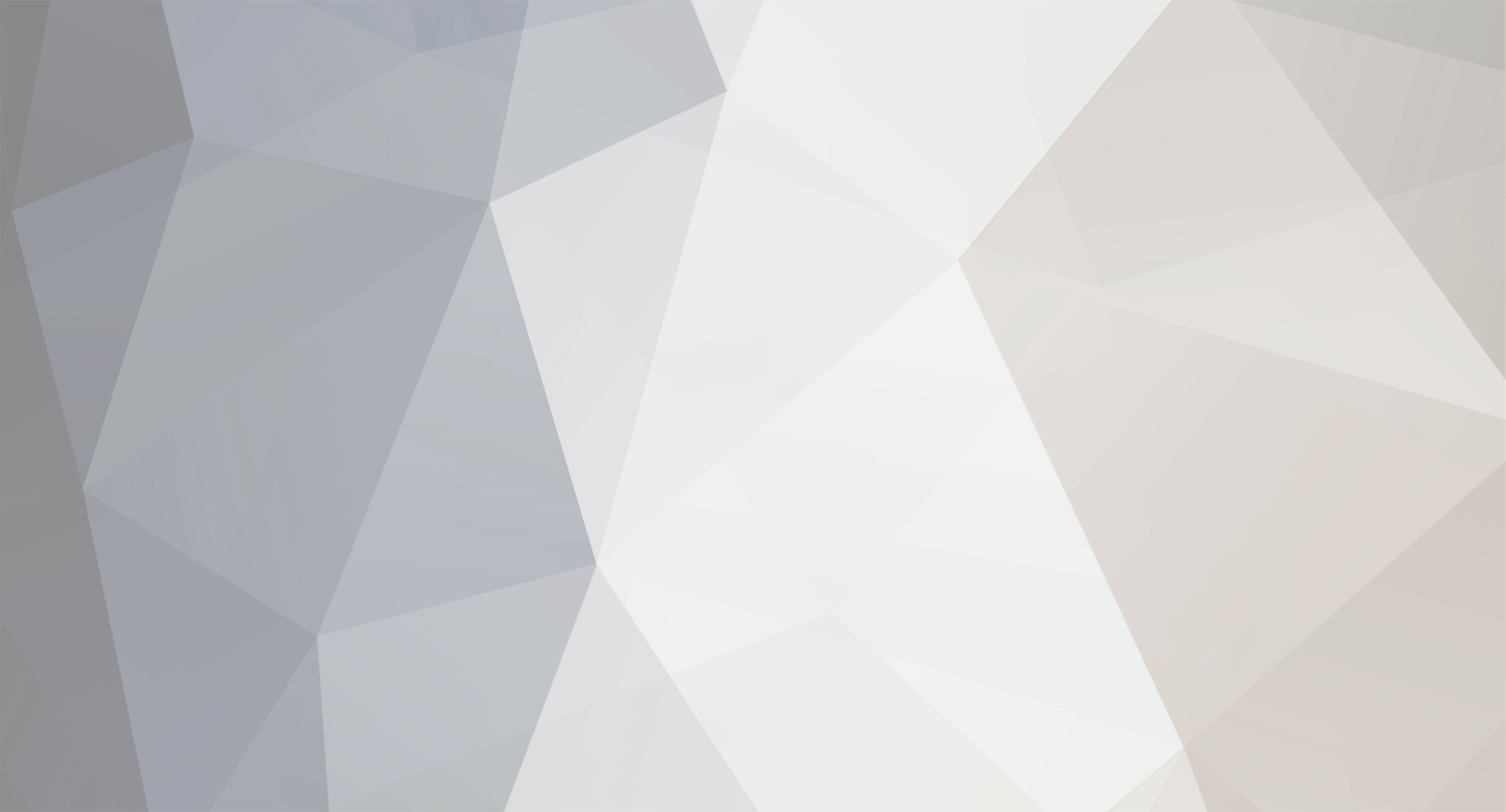
kscarbel2
Moderator-
Posts
18,539 -
Joined
-
Days Won
112
Content Type
Profiles
Forums
Gallery
Events
Blogs
BMT Wiki
Collections
Store
Everything posted by kscarbel2
-
Surely they're joking...................????? Reuters / March 17, 2020 The Native American [Indian] gaming industry on Tuesday requested $18 billion in U.S. federal aid as it shut casinos that are [allegedly] the sole source of commercial revenue for dozens of tribes in a bid to slow the coronavirus epidemic.
-
After working around the globe, I personally want any 85,000 lb (38,555 kg) bogie to have planetary hub reduction axles.
-
Bloomberg / March 17, 2020 The Trump administration is discussing a plan that could amount to as much as $1.2 trillion in spending -- including direct payments of $1,000 or more to Americans within two weeks -- to blunt some of the economic impact of the widening coronavirus outbreak. Treasury Secretary Steven Mnuchin pitched $250 billion in checks to be sent at the end of April with a second set of checks totaling $500 billion four weeks later if there’s still a national emergency. “Americans need cash now, and the president wants to give cash now. And I mean now, in the next two weeks,” Mnuchin said Tuesday at a White House briefing alongside President Donald Trump. “It is a big number,” Mnuchin said. “This is a very big situation in this economy, we put a proposal on the table that would inject $1 trillion into the economy.” The administration had been discussing a total aid package of $850 billion, but discussions later included spending as much as $1.2 trillion. The cash payments would be part of a stimulus plan Mnuchin is negotiating with Congress. The administration hasn’t decided on how much to send Americans, but wants the checks to exceed $1,000. Mnuchin’s proposal included $300 billion for small business loans, $200 billion in stabilization funds, $250 billion in cash payments and a possible second round of checks. Including tax deferrals, that would bring the cost of the plan to around $1.2 trillion. Mnuchin said the administration will aim not to send checks to millionaires but stressed the need for urgency. The checks will be subject to some kind of income test. Mnuchin also said the government intends to keep stock markets open. Plunging stock prices and the abrupt drop-off of consumer spending during a time of social distancing has crystallized the need for Congress to act quickly and boldly. The Federal Reserve has already used much of its toolbox to shore up the economy, leaving policymakers to dull the extent of the damage with fiscal stimulus. News of stepped-up government efforts to offset the financial damage caused by the outbreak prompted a rebound in U.S. stocks. The S&P 500 jumped as much as 7% before paring back to 4%, continuing a streak of volatility last seen during the Great Depression. The Dow Jones Industrial Average notched a 2% gain. The Senate on Tuesday was poised to take up a House-passed economic relief measure. That package, negotiated by Mnuchin and Pelosi last week and endorsed by the president, pays for virus testing, bolsters unemployment and food assistance and will send tens of billions in fresh aid to states. Its centerpiece gives workers at companies with fewer than 500 employees up to 12 weeks of paid family and sick leave to deal with issues involving the coronavirus, including staying home to care for children home from school. The tax credits for paid family, sick and medical leave in the virus bill would cost nearly $104.9 billion. The idea of issuing checks to Americans has been endorsed by lawmakers across the ideological spectrum. But it may not be practical to get money to Americans as fast as Trump desires. When Congress sent stimulus checks in 2009 to combat the financial crisis it took more than two months from the signing of the bill to checks hitting the mail. It’s quickest and simplest for Congress to send the same amount to every individual person, but still will take months to happen. If lawmakers decide to give more money to lower-income workers, it becomes even more complicated. In a further move to relieve financial stress on average Americans, Mnuchin said that individual taxpayers can get a deadline extension on paying taxes of up to $1 million and corporations can defer tax payments of up to $10 million. The deferments can total as much as $300 billion, Mnuchin said, up from $200 billion he proposed last week. The 90-day delay gives taxpayers additional time to pay their outstanding tax liabilities without interest or penalties. The White House is encouraging taxpayers to still file by April 15 if they don’t owe the IRS any money.
-
No mention of it on the website..................https://www.macktrucks.com/powertrain-and-suspensions/axles/
-
If you mean the Federal Reserve dropping interest rates to zero on Sunday, that scares the heck out of me because now the Fed is out of ammunition should things get worse down the road.
-
Heavy Duty Trucking (HDT) / March 16, 2020 Mack Trucks introduced the Mack S852, an 85,000-lb. gross axle weight rating of its proprietary tandem drive axles, which is available for order now. Customers can spec it for specialized severe-duty or heavy-haul applications on Mack Granite models. For extreme loads at slow speeds, the S852 tandem drive axles have a creep rating of 105,000 lbs. Today’s Mack drive axles are engineered with a double-reduction design and include several design advantages implemented through continuous research and development efforts, according to Mack, such as the use of Durapoid bevel and helical gears. This design provides favorable gear tooth geometry that helps eliminate localized stress and loading on the gear tooth end, providing enhanced strength and longer gear life. Frictional losses are also reduced in this gear design, allowing Mack axles to deliver up to 1.5% improved fuel efficiency. “Low-traction situations can be a challenge for truck drivers, seriously impacting their productivity,” said Roy Horton, Mack Trucks director of product strategy. “To help address that issue, we offer standard inter-axle and optional inter-wheel power dividers that automatically distribute torque between the slipping and non-slipping axle or wheel respectively.” The axles also feature a top-mounted carrier design that is not only less prone to main seal leaks, but also provides more than two inches of additional ground clearance. An additional benefit of Mack’s top-mounted carrier design is improved driveline angles between the drive axles. Instead of a three and a half to eight-degree angle, Mack’s prop shaft angle is just one to two degrees. This maximizes universal joint life, allows for greater axle articulation and reduces vibrations for a smoother ride. It also reduces torque losses for improved efficiency. The new rating comes as Mack celebrates 120 years of drive axle design, engineering and manufacturing this year. “Mack has a long and rich history of engineering and manufacturing its own powertrain components, including drive axles, as it fits with our philosophy that components designed to work together, simply work better,” said Horton. “We welcome the new S852, which will broaden the applications our trucks are built to handle.” .
-
I would like to see a 180 day deferral (6 months), and we very well might before all is said and done.
-
This just in from the White House: MarketWatch / March 17, 2020 Treasury Secretary Steven Mnuchin on Tuesday said President Trump has authorized the deferral of $300 billion in payments to the IRS. Mnuchin said if individuals owe a payment, they can defer up to $1 million, and corporations may defer $10 million. The deferrals will be penalty-free for 90 days as the U.S. grapples with the coronavirus crisis.
-
Croatia is ahead of the game! All countries should do this. ------------------------------------------------------------------------- Reuters / March 17, 2020 Croatia’s government proposed on Tuesday to postpone tax payments for at least three months and make loans available to struggling business in response to the fallout from the coronavirus pandemic. “The goal of our economic measures is to save jobs and secure sufficient liquidity,” Prime Minister Andrej Plenkovic told a cabinet session. Parliament is expected to approve the measures this week. The postponement of tax payments on profit and income, as well as other salary contributions, will be extended for an additional three months if needed. Finance Minister Zdravko Maric said at the end of the six-month period, taxpayers would be able to pay overdue taxes in up to 24 monthly installments without any interest.
-
CNN's grossly biased headlines and dramatized reporting of the news should all be a crime.
-
S&P Global's economists today forecast a global recession this year. They now estimate global GDP growth in 2020 at just 1.0%-1.5%, with risks remaining firmly on the downside. IHS Markit now expects a recession to begin in the second quarter, and predicts the downturn will last through the end of the year. They see unemployment rate rising to 6% from the current 50-year low of 3.5%, a large increase that would hinder a recovery. Saudi Aramco Chief Executive Amin Nasser said on Monday that he is “very comfortable” with $30 oil. Goldman Sachs says oil consumption is down by 8 million barrels a day. The bank expects West Texas Intermediate (WTI) to trade higher than Brent this quarter, and cut its Brent forecast for the second quarter to just $20 a barrel.
-
Wall Street Journal / March 14, 2020 U.S. highway-safety regulators are suspending rules that limit daily driving hours for truck drivers moving emergency supplies such as medical equipment, hand sanitizer and food in response to the nationwide coronavirus outbreak. The Transportation Department’s Federal Motor Carrier Safety Administration announced the nationwide exemption late Friday, following President Trump’s declaration of a national emergency over the pandemic. The move “will help America’s commercial drivers get these critical goods to impacted areas faster and more efficiently,” FMCSA Acting Administrator Jim Mullen said. It comes as hospitals report shortages of medical masks and as retailers and manufacturers are straining under surging demand for everything from hand sanitizer to staples such as toilet paper and rice. As anxious consumers stockpile goods, grocers have turned to rationing, imposing purchase limits on disinfectant wipes, cleaning supplies and other high-demand products. The move is the first time the FMCSA has issued nationwide-wide relief from hours-of-service regulations, although regional declarations have waived those rules in response to disasters such as hurricanes. Federal regulations limit most commercial truck drivers to 11 hours of driving time in a 14-hour workday, restrictions intended to reduce accidents caused by highway fatigue. The national emergency declaration applies to carriers providing direct assistance to relief efforts tied to the coronavirus pandemic, such as moving medical supplies and equipment to test, diagnose and treat Covid-19. It also applies to those hauling goods to help prevent its spread, including masks, gloves, hand sanitizer and disinfectants. Drivers transporting “food for emergency restocking of stores” are also covered by the declaration. It also applies to motor carriers moving medical and emergency services providers, people needed to set up and manage temporary housing and quarantine facilities, and people being moved for medical, isolation or quarantine purposes, the agency said. The declaration doesn’t apply to routine commercial deliveries or truckers hauling mixed loads that include essential supplies. Drivers that inform motor carriers they need immediate rest must be permitted at least 10 consecutive hours off duty.
-
Coronavirus vaccine test opens with 1st doses Associated Press / March 15, 2020 SEATTLE — U.S. researchers gave the first shots in a first test of an experimental coronavirus vaccine Monday, leading off a worldwide hunt for protection even as the pandemic surges. With careful jabs in the arms of four healthy volunteers, scientists at the Kaiser Permanente Washington Research Institute in Seattle began an anxiously awaited first-stage study of a potential COVID-19 vaccine developed in record time after the new virus exploded out of China and fanned out across the globe. The Associated Press observed as the study’s first participant, an operations manager at a small tech company, received the injection in an exam room. Monday’s milestone marked just the beginning of a series of studies in people needed to prove whether the shots are safe and could work. Even if the research goes well, a vaccine would not be available for widespread use for 12 to 18 months, said Dr. Anthony Fauci of the U.S. National Institutes of Health. At a news conference, President Donald Trump praised how quickly the research had progressed. Fauci noted that 65 days have passed since Chinese scientists shared the virus’ genetic sequence. He said he believed that was a record for developing a vaccine to test. This vaccine candidate, code-named mRNA-1273, was developed by the NIH and Massachusetts-based biotechnology company Moderna Inc. There’s no chance participants could get infected because the shots do not contain the coronavirus itself. It’s not the only potential vaccine in the pipeline. Dozens of research groups around the world are racing to create a vaccine against COVID-19. Another candidate, made by Inovio Pharmaceuticals, is expected to begin its own safety study next month in the U.S., China and South Korea. The Seattle experiment got underway days after the World Health Organization (WHO) declared the new virus outbreak a pandemic because of its rapid global spread, which has infected more than 169,000 people and killed more than 6,500. Starting what scientists call a first-in-humans study is a momentous occasion for scientists, but Jackson described her team’s mood as “subdued.” They’ve been working around-the-clock readying the research in a part of the U.S. struck early and hard by the virus. Still, “going from not even knowing that this virus was out there ... to have any vaccine” in testing in about two months is unprecedented, Jackson told the AP. Some of the study’s carefully chosen healthy volunteers, ages 18 to 55, will get higher dosages than others to test how strong the inoculations should be. Scientists will check for any side effects and draw blood samples to test if the vaccine is revving up the immune system, looking for encouraging clues like the NIH earlier found in vaccinated mice. “We don’t know whether this vaccine will induce an immune response or whether it will be safe. That’s why we’re doing a trial,” Jackson stressed. “It’s not at the stage where it would be possible or prudent to give it to the general population.” Most of the vaccine research under way globally targets a protein aptly named “spike” that studs the surface of the new coronavirus and lets it invade human cells. Block that protein and people cannot get infected. Researchers at the NIH copied the section of the virus’ genetic code that contains the instructions for cells to create the spike protein. Moderna encased that “messenger RNA” into a vaccine. The idea: The body will become a mini-factory, producing some harmless spike protein. When the immune system spots the foreign protein, it will make antibodies to attack — and be primed to react quickly if the person later encounters the real virus. That’s a much faster way of producing a vaccine than the traditional approach of growing virus in the lab and preparing shots from either killed or weakened versions of it. But because vaccines are given to millions of healthy people, it takes time to test them in large enough numbers to spot an uncommon side effect, cautioned Dr. Nelson Michael of the Walter Reed Army Institute of Research, which is developing a different vaccine candidate. “The science can go very quickly but, first, do no harm, right?” he told reporters last week. The Seattle research institute is part of a government network that tests all kinds of vaccines and was chosen for the coronavirus vaccine study before COVID-19 began spreading widely in Washington state. Kaiser Permanente screened dozens of people, looking for those who have no chronic health problems and are not currently sick. Researchers are not checking whether would-be volunteers already had a mild case of COVID-19 before deciding if they are eligible. If some did, scientists will be able to tell by the number of antibodies in their pre-vaccination blood test and account for that, Jackson said.
-
Trump said Monday that the novel coronavirus outbreak in the United States could last until July or August. “People are talking about July, August, something like that … could be longer than that.”
-
Salt Lake City Police Department (SLCPD) March 14, 2020 "Due to the confirmed case of #COVIDー19 from community spread, SLCPD is asking all criminal activities/nefarious behavior to cease until further notice. We appreciate your anticipated cooperation in halting crime & thank criminals in advance. We will let you know when you can return to your normal criminal behavior. #SocialDistancingNow #behaveyourself Also, find more information about #coronavirus here: https://www.slc.gov/mayor/covid-19/" https://www.facebook.com/slcpd/posts/3115773975102552?_fb_noscript=1
-
Britain asks Ford to produce lifesaving hospital ventilators Reuters / March 16, 2020 Britain has asked Ford Motor Company to help make health equipment including hospital ventilators to cope with the coronavirus outbreak. Ford said it was assessing the situation. The U.S. automaker operates two engine factories in Britain, which made just under 1.1 million engines in 2019. One of the two sites, in Bridgend in Wales, is due to close this year. It was not immediately clear how a manufacturer of cars could turn to producing specialist medical equipment, which international parts would be needed or what certification would be required. One option could be to adopt defense industry rules which can be used to order certain factories to follow a design to produce a required product quickly. British industry has the capability to do that but is unlikely to make the electronic components that would also be required. Robert Harrison, professor of automation systems at the University of Warwick in central England, said it would be a significant task, perhaps taking many months, for engineering companies to manufacture ventilators. "They would have to tool up production lines and train workers to assemble and test the product," he said. Sourcing the parts, for example, electronics, valves and air-turbines, quickly could be difficult, Harrison said. The ventilators are sophisticated devices. "It is crucial that they work correctly in order to keep the patient alive, as these are life-critical pieces of equipment," he said. Different approach Many countries are trying to buy ventilators, used to keep people with coronavirus alive if they struggle to breathe. Britain, which has reported 35 coronavirus deaths and 1,372 cases, has taken a different approach to some European countries that have imposed stringent lockdowns to try to slow the spread of the disease. Prime Minister Boris Johnson will speak to manufacturers to seek support for the production of "essential medical equipment” for the National Health Service, a spokesman for his Downing Street office said. "He will stress the vital role of Britain's manufacturers in preparing the country for a significant spread of coronavirus and call on them to step up and support the nationwide effort to fight the virus," the spokesman said.
-
Goldman Sachs has downgraded U.S. GDP forecasts and said a recession was on its way. The investment bank’s economic research team, led by Jan Hatzius, said economic activity would “contract sharply” for the rest of March and April as consumers and businesses cut back on spending. They expected a recovery after April, though that was uncertainty, but said their new forecasts “probably” met the criteria for a recession. They expected real GDP growth of 0% in the first quarter and a contraction of 5% in the second quarter. “This takes our 2020 GDP forecast down to +0.4%(from 1.2%). The uncertainty around all of these numbers is much greater than normal.” The team said the prospect of a recovery and strong growth in the second half were dependent on whether social distancing and warmer weather reduces the number of virus cases, how quickly reduced infections will bring a return to normality and how effective fiscal and monetary policy turns out to be. Goldman Sachs chief equity strategist David Kostin said, in a separate note, the S&P 500 could fall to as low as 2,000 points if the economic impact of the virus worsens but expected the index to reach 3,200 by the end of 2020.
-
Jack's not in the truck business, but he's a brilliant businessman and a heck of a nice guy.
-
Here's a new twist. Chinese billionaire Jack Ma (actually a good guy), via his Jack Ma Foundation and Alibaba Foundation, is donating 500,000 Coronavirus testing kits and one million surgical masks to the United States. He has already donated supplies to other countries including Japan, South Korea, Italy, Iran and Spain, with two million protective masks destined for distribution across Europe. The first consignment of 500,000 masks and other medical supplies such as test kits (pictured below), which was destined for Italy, arrived in Belgium on Friday. .
-
Fed Slashes Interest Rates to ZERO LinkedIn / March 15, 2020 The Federal Reserve cut interest rates to zero Sunday, saying "the coronavirus outbreak has harmed communities and disrupted economic activity." In addition, it is introducing a $700 billion program to shield the U.S. economy from the impact of COVID-19. It's the "largest single day set of moves" the Fed has ever taken. The low interest rates, which aim to make borrowing cheap for Americans and businesses in crisis, will likely remain until the economy recovers from the coronavirus downturn. Futures trading on Sunday pointed to an impending stock-market decline on Monday. The Fed's board of governors, who had been set to meet this Wednesday, were widely expected to cut rates to zero at that meeting, after they cut rates to a half a percentage point in another emergency cut on March 3. Sunday's latest emergency action suggests the Fed was concerned that waiting even three more days could be too late to prop up the economy. The Fed will no longer meet later this week. ------------------------------------------------------------------------------------------------------------------------------- MarketWatch / March 15, 2020 The Federal Reserve on Sunday threw in the proverbial kitchen sink to lessen the expected blow to the U.S. economy from the coronavirus. In a rare Sunday decision that comes three days before a scheduled formal meeting, the central bank slashed its benchmark interest rate to zero and implemented a bond-buying program, known as quantitative easing (QE), of at least $700 billion. “The virus presents significant economic challenges,” said Fed Chairman Jerome Powell. “Measures to stem the spread of the illness will have a significant effect on economic activity in the near term,” he added. Powell acknowledge the Fed can’t help businesses or workers who are hurt by the broad shutdown of normal day-to-day activity. That is the role for Congress and the administration, he said. The Fed’s job is to make sure financial markets are not dysfunctional and credit is flowing, he said. Powell said the economy would be weak in the April-June quarter, with a likely decline in output. What happens after that depends on developments with the pandemic, he said. The Fed cut its key benchmark rates by 100 basis points to a range of zero to 0.25%. That’s the “zero lower bound” for rates. Powell repeated that the central bank doesn’t intend to push the benchmark rate into negative territory, as some foreign central banks have. The vote to slash rates was not unanimous. Cleveland Fed President Loretta Mester dissented, saying she preferred a half-point cut. The new round of QE will consist of open-ended purchases of $500 billion of Treasury securities and $200 billion of agency mortgage-backed securities. Powell said the asset purchases were designed to restore smooth Treasury market functioning so credit could flow to households and businesses. Some of the crises-era bond-buying programs were controversial with lawmakers. Powell used stark language to defend the new QE. The Treasury bond market is the foundation of the U.S. financial system, and the mortgage-backed securities market is closely aligned with that. “If they don’t function well, that will spread, Powell said. In a sign of a dovish stance, the Fed stressed rates would stay near zero for a long time. Specifically, the Fed said it expected to keep rates near zero “until it is confident the economy has weathered recent events and is on track to achieve its maximum employment and price stability goals.” That means rates will stay low as the Fed expects inflation to hit 2%. That has only happened a few times since the 2008 financial crisis and never for a sustained period. The Fed is “willing to be patient,” Powell said. Dow futures sank after the announcement Sunday. The Fed said it was willing “to use its full range of tools” to support the flow of credit in the markets, again pledging to do whatever it takes to keep short-term lending markets liquid. The Fed lowered the rate charged to banks for short-term emergency loans from its discount window to 0.25% from 1.75%, and eliminated reserve requirements for banks and said it would urge banks to tap their liquidity and capital buffers to lend to clients. To help foreign firms and banks who need dollars , the Fed activated dollar swap plans with the Bank of Canada, the Bank of England, the Bank of Japan, the European Central Bank and the Swiss National Bank. Powell stressed that he didn’t think the Fed was out of tools after today’s actions. He said Sunday’s decision was in lieu of a the meeting set for Tuesday and Wednesday. The Fed won’t release a “dot plot” showing the expected path of interest rates over the next few years or an economic forecast until June, he said
-
Some years later, Scania had reached another technical cross-roads: how would they fit in the new injection technology that was required for the engine to comply with the new Euro 3 emissions legislation? To solve the challenge, Scania’s engineers started the development of a completely new engine set-up: a V8 with a narrower, 72-degree angle. Around 12 prototypes were built, of which a couple still exist in less-visited corners of Scania’s R&D department. But it was at this point that a certain senior engineer stepped in: Bengt Gadefelt. “He warned that the 72-degree engine would have a very complex layout, especially the crankshaft. Finally, with another injection solution chosen, we chose to develop a totally new 90-degree 16-litre engine instead,” recalls Håkan Fransson, a retired former Scania Chief Engineer. Pictured - One of the prototypes of a 72-degree angle V8 that was developed to succeed the original 14-litre V8. It stayed a prototype and was never used. .
-
Scania Group Press Release / March 11, 2020 Polish Elmex Logistics Group recently took delivery of the first ten of 20 liquefied gas Scania R 410 trucks. Elmex operates a fleet of more than 200 vehicles in providing transport services throughout Europe. The network of liquefied filling stations in Europa is rapidly expanding and currently numbers around 250, of which five in Poland. .
-
Scania Group Press Release / March 13, 2020 This historical film tells the story of why Scania developed the first Scania V8 engine, the DS14, in the 1960s. When the Swedish authorities raised the speed limit and maximum gross weight permitted for heavy trucks, it created the need for a new, more powerful engine. Scania's engineers met that need with the now-legendary 350 horsepower V8 engine. More than half a century later, the Scania V8 remains a powerful tool for the most demanding transport operations. This is where that legend began. Learn more about the development of the first Scania V8: http://bit.ly/ScaniaV8History .
-
- 1
-
-
Scania Group Press Release / March 10, 2020 Today, the tenth of March, is International V8 Day, a time for the V8 engine to be celebrated around the world. And the perfect day to make a visit to Charles Russell Transport in Cheltenham in the South West of England. Charles Russell Transport is where the past, present and future come together. Besides a fleet of 35 Scania trucks (of which 20 are V8s) that handle today’s tough transportation tasks, it keeps a unique collection of vintage V8s. And both the company and its exhibition space are going for growth. On entering the gates of Charles Russell Transport’s premises in Cheltenham in the South West of England, you might be fooled into thinking you were on a farm. Yet the picturesque rural setting of this haulage business is home to an amazing collection of Scania V8s: an exhibition featuring every model ever produced, all presented in an increasingly crowded space. The latest addition to the company’s “Scania V8 museum” is a 1986 R142, which has been stripped down to component level. Now waiting to have its cab installed, it is then due to be refurbished and repainted to get it back into pristine condition, just like all the other trucks in the collection. Classic truck enthusiast and founder of the company Charles Russell has his own personal favourite: the 1972 140 Super. “That’s because of the iconic status of the model,” he says. Restoring vintage vehicles Having now taken a step back from the day-to-day operations of the business he founded in 1969, Russell still takes great pleasure in lovingly restoring his vintage vehicles, and spends as much time as possible on each project himself. Ever the businessman though, he always tries to minimize the cost of refurbishment. For his latest R142 project, he bought a similar V8 for parts and sold on the cab for more than he had spent on the entire vehicle. “I display my vehicles at classic-truck shows, and even I display some on behalf of Scania in Great Britain,” he says. Russell’s interest in collecting all things V8 and Scania started in a modest way in the 1980s with a series of posters and memorabilia. But it was without doubt his love of the engine that sparked his passion: “In my opinion, the Scania V8 is the best diesel engine ever produced.” Classic Scania V8 collection Rather like the business itself, his V8 collection is starting to outgrow the company’s current premises, so they are investing heavily to support expansion for the next generation. One reason that the company has survived and thrived is the fact that it takes a specialist approach to haulage. The handling of industrial machinery accounts for 80 per cent of the business, while the rest involves abnormal and interesting loads including large sculptures, boats and aircraft. Coming from a farming background, Russell started out transporting livestock to local markets. As the business grew, he moved into transporting industrial machinery, which is when he acquired his first crane truck so he could load and unload on site at customers’ factories. As this side of the business grew, in 1980 Russell started transporting industrial machinery to various parts of Europe. “Then I decided to offer customers an additional service: installing their machinery. That way, with our complete package, they’d only have one company to deal with.” One-stop shop for transport and installation The concept of a one-stop shop has since become the bedrock of the business. Customers’ requirements are assessed, and the manpower and equipment needed are organised so that all the work can be carried out without the help of any subcontractors. Assignments might involve anything from the transportation and installation of a single machine to the relocation of a complete factory. Russell’s son Ben, who works as Operations Director, says: “We operate a tailor-made IT system that is designed for abnormal loads and machinery. Customer demands have increased and timescales have shortened so we have to respond rapidly.” Indeed, the company carries out 20 to 30 jobs a day, and ensuring that the trucks are fully loaded as much of the time as possible is key. Quality customer care Customer care is a strong feature of the business. When tendering for his first major customer (one he has retained until the present day), Russell said, “If we don’t get it right, you don’t need to pay us.” The customer has never had any cause for complaint. Quality customer care is something that Charles Russell Transport has in common with Scania, which makes them a good fit. Russell bought his first Scania 141 for the company in 1983. “I kept it for three years and sold it for more money than it cost,” he says. “As a young businessman I thought that was a great deal. That day, I became converted to Scania for the reliability, the day-to-day running costs and the residual value of their trucks.” Runs a fleet of 35 Scania trucks Today, the company runs a fleet of 35 Scania trucks, 20 of which are V8s, with the new generation of vehicles due to be delivered in 2019. Along with their acquisition of new vehicles, Charles Russell Transport provides workforce training in the new technologies and features that the new trucks have. The company also runs its own apprenticeship scheme to prepare the next generation to support the business. While transporting industrial machinery accounts for most of the company’s business, helping out in the art world is probably the most fun and most demanding of their activities. They work with some of the most prestigious names in the large-sculpture domain, though they are very discreet about their clientele. Charles Russell Transport has been involved in installing works in locations as diverse as New York, Hong Kong, Mexico and Paris. Monumental sculptures to Doha One of the company’s most challenging art projects to date was transporting a series of monumental bronze sculptures from a foundry in the UK to Doha in Qatar. In total the sculptures weighed more than 200 tonnes, each one weighing up to 29 tonnes. They ranged in height from five to 15 metres, with a width of up to seven metres. During this three-year project, Charles Russell Transport’s full range of services were enlisted, including the instalment of the sculptures at the Sidra Medical and Research Centre in Doha. .
BigMackTrucks.com
BigMackTrucks.com is a support forum for antique, classic and modern Mack Trucks! The forum is owned and maintained by Watt's Truck Center, Inc. an independent, full service Mack dealer. The forums are not affiliated with Mack Trucks, Inc.
Our Vendors and Advertisers
Thank you for your support!