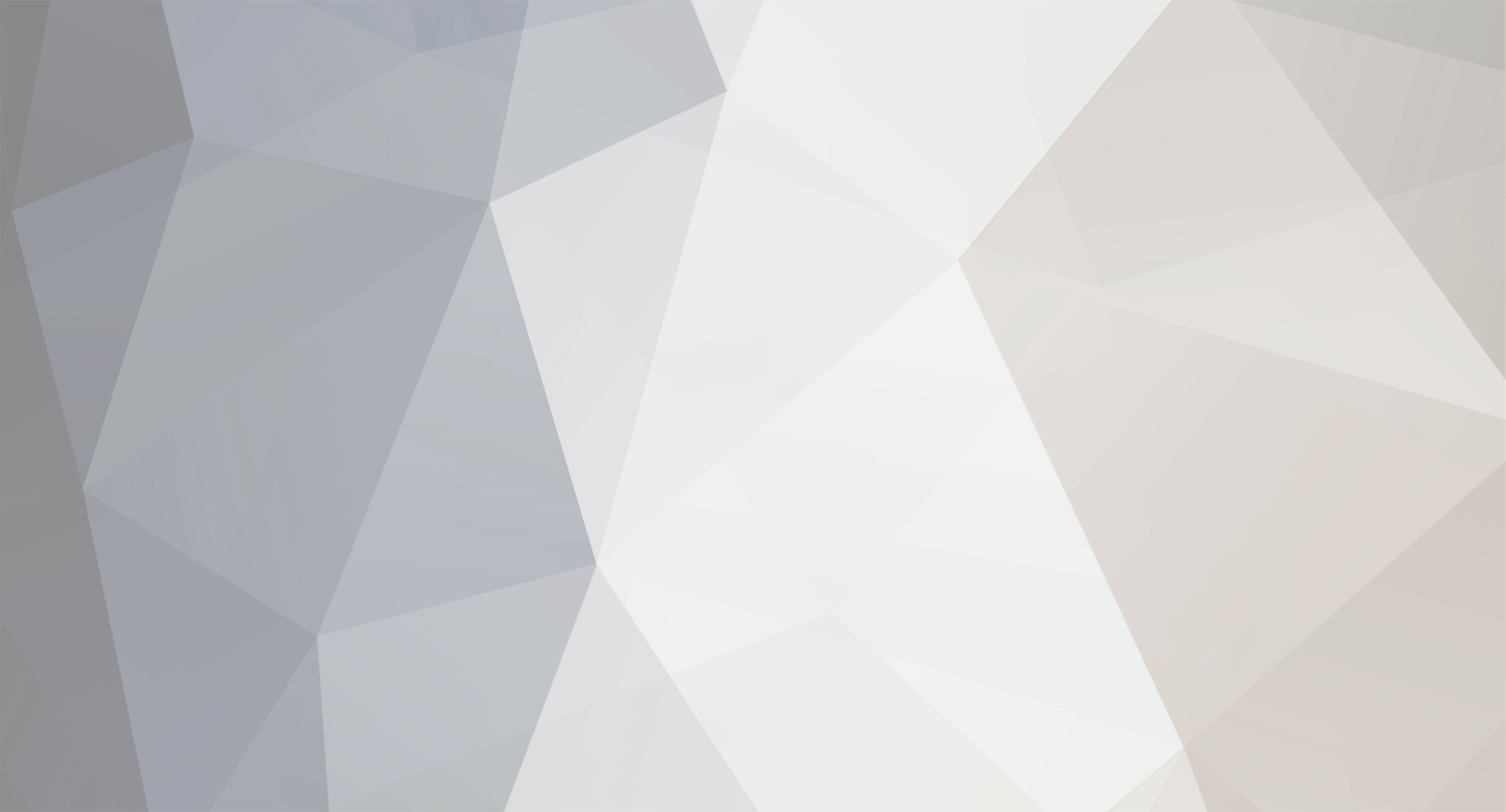
kscarbel2
Moderator-
Posts
18,539 -
Joined
-
Days Won
112
Content Type
Profiles
Forums
Gallery
Events
Blogs
BMT Wiki
Collections
Store
Everything posted by kscarbel2
-
The Daily Mail / July 4, 2015 The British trucker who blockaded the French! And, quelle surprise, they went squealing to the police. A rage-inducing dispatch from the Calais frontline. Doug Wilson told to off-load his cargo when caught Calais ferry protestHe was one of thousands caught in 30 mile queue caused by union strikeTurned tables - parked his own lorry to block workers from leaving meetingTook action at the start of Calais chaos which now shows no signs of improving Stuck in the worst cross-Channel chaos since World War II, one British lorry driver decided he had simply had enough. The port of Calais had been closed by striking French ferry workers who, for good measure, also blocked the alternative route to the UK by setting fire to the entrance to the Channel Tunnel. With queues of trucks up to 30 miles long outside Calais, Folkestone-based driver Doug Wilson, 57, was having a bad week in France. His client had given up waiting for his cargo of beer and had told Doug to off-load it. So he drove to the offices of the union whose members had started the tunnel blaze. The comrades had just gathered for a rally and, in a delicious moment of revenge, Doug parked his truck across the car park entrance and switched off his engine. ‘I blocked them in just like they’d blocked us in,’ he tells me. ‘They threatened me with a jack handle and I got pushed around a bit.’ His one-man blockade was lifted only when, with glorious irony, the strikers called the police. At least Doug had done something — which is more than can be said for the French authorities during a week of deplorable lawlessness bordering on anarchy at France’s busiest ferry port. For several days now, trapped lorry drivers have been besieged by migrants trying to hide on their vehicles and enter Britain illegally. The queue of lorries is stretching out of town and about to reach Belgium. There are feral gangs running everywhere — even though we are on the side of a motorway — and no police to be seen. A well-built Eastern European fumbles with the back of a lorry belonging to Express Trailers Ltd of Malta, pulls open the door and waves to a group of Afghan men squatting in the shade of a nearby tree. Three come running, but there’s room for only one inside. Never mind. He’ll have a crack at another lorry in a minute. One exasperated British lorry driver likens this week’s scenes in Calais to the post-apocalyptic thriller Mad Max. From where I’m standing — near the entrance to the Channel Tunnel freight terminal — I’d say it’s more like a David Attenborough wildlife documentary on the Serengeti. Stretching miles into the distance, vast, lumbering beasts crawl in the same direction while gangs of predators lie in wait, pounce on the more vulnerable prey and then move on. Their audacity is breathtaking — in every sense. They are not just risking life and limb as they leap between the moving parts of 44-ton trucks. They are brazenly breaking the law, sometimes with threats and violence, in broad daylight. And they do so under the gaze of bus-loads of French police. The gendarmes have little enthusiasm for arresting stateless migrants desperate to get out of France and into the promised land of the UK. Too much paperwork, Monsieur, and besides, there are too many to deal with. The police break up the larger gang assaults — and they don’t hold back with their batons — but then everyone is just sent on their way. There is nothing new about the people-smuggling racket in Calais. But this week, it’s busier than ever, thanks to militant French ferry workers objecting to the sale of the MyFerryLink line to Danish rival DFDS. And, just like the migrant gangs, they seem to enjoy immunity from prosecution. The tunnel arsonists received little more than a slap on the wrist, and there was not even a reprimand for another group who clogged the Calais car lanes by driving at a snail’s pace, a popular form of French protest known as ‘Operation Escargot’. As a result of all this, a 25-mile queue of freight traffic has been a sitting duck for ‘les clandestines’ all week. And the unions are promising more trouble to come. When schools break up in a few weeks, disruption and intimidation loom for millions of holidaymakers travelling to and from the Continent. Yet, disgracefully, the only people risking any sort of punishment are the drivers of lorries and coaches who face a fine of up to £2,000 per stowaway. Last week, Laurie Bourne, a coach driver from Essex, whose locked bus was ambushed by a gang of 30 outside Calais last autumn, was fined £2,000 by the UK Border Agency following the discovery of two migrants in a storage compartment. Although he had reported the stowaways to the port authorities, he was still quizzed for three hours and later punished. The migrants were given water and sent on their way. The situation is even more ruinous for lorry drivers with perishable loads. If a stowaway is found in a cargo of food, the whole lot must be jettisoned. A Home Office spokesman says the number of cross-Channel stowaways caught through security checks last year was 39,000 — more than double the number for the previous year and three times more than 2012-13. But officials refuse to divulge the number of fines issued. In this week’s chaos, there wasn’t time to check every load anyway. At one point, I watched a trio of French policemen wave a lorry through to the freight terminal with a man’s head clearly peeking out above the cab. Though the blockade has been lifted (for now), it will take days to return to normal. Until then, Britain continues to lose £250 million a day, according to the Port of Dover. Little wonder hauliers are demanding military intervention. ‘The UK and French governments must acknowledge their responsibilities and act,’ said Richard Burnett, of the Road Haulage Association, which represents 6,000 firms and 100,000 trucks. ‘If this means deployment of the armed forces, then so be it.’ Most of us will remember this week for the hottest start to July in history. Mr Burnett and his members will remember it for the worst blockade in living memory. ‘It’s not just lorry drivers who are suffering,’ he tells me. ‘There are supermarkets without food supplies and production lines on hold as they wait for components.’ He points out that on the British side of the Channel, Operation Stack — the emergency queuing system for lorries heading for Dover — went off the scale. Kent Police had never previously had to deal with a queue halfway back up the motorway to London. If that wasn’t bad enough, he explains, the migrant situation in Calais is now endangering the lives of hauliers as well as stowaways. Doug Wilson agrees: ‘People have been trying it on for years, but now they’re all armed — knives and worse.’ The smugglers’ usual tactic for slowing down lorries is to throw rubbish across roads — and even throw bricks at windscreens. In this sort of gridlock, they don’t need to. It’s a free-for-all for the marauders. Driving along the western approach to Calais, I am struck by the discipline of the lorry drivers. They form an orderly queue down the outside lane of the motorway, leaving the other lanes open for cars. Paul Joy, 49, from South London, is stuck here with 15 tons of German meat destined for a famous British supermarket chain, and says the whole lot will be worthless unless he gets it to his depot in the next 48 hours. Of all the places he drives to, he says Calais is by far the worst. ‘I reckon a few firms will go bust after this week,’ he adds. One Oxfordshire haulier has announced that he is giving up cross-Channel operations altogether. ‘There were always stowaways at Calais but now it’s a serious problem and it has cost us thousands,’ says Sir Adrian Cooper, 54. Arguably Britain’s poshest trucker, the 6th baronet delivers crops in a pair of 44-ton trucks. ‘Every time a gang cuts through the cover, it’s another £150 repair plus all the delay,’ he says. ‘These strikes have been the final straw. I’m sticking to the UK for now.’ Back outside the Calais freight terminal, the police are nowhere to be seen as an African gang crack open a P&O Ferrymasters container on the back of a Dutch lorry. Next, we stumble across an Afghan gang opening up a Romanian lorry operated by Vos Logistics. Another stowaway pops inside. A police car whizzes by without even slowing down. I find a party of Sudanese migrants sitting in the back of a Polish lorry carrying two German diggers. The door is wide open and they leap out when Mail photographer Mark Large starts taking pictures (a risky business, as the dents in his car testify). The driver, Jan Hajdecki, climbs from his cab and laughs. ‘All under control,’ he says, explaining that he deliberately leaves his truck wide open until he reaches the port. Only then does he bother clearing out any stowaways. He’d much rather they climbed in through the door than cut holes in his expensive curtain around the sides. Things are only going to get worse. As more migrants flee the horrors of IS and civil wars in the Middle East and Africa, more overcrowded boats are landing in Italy. From there, many will make their way to Calais where they will keep trying their luck. They may not be in mortal danger any more. But Britain, not France, is where they want to be. ‘Look, this is my home town,’ says Jamal, 32, a former garden centre manager from Daraa, Syria, producing his mobile phone to show me a picture of a pile of rubble. He has been sleeping in a tent on a Calais industrial estate for 45 days and has tried to jump on many lorries. Jamal wants to go to the UK because he has family there and because France is increasingly unpleasant. ‘I won’t go to the Jungle. It is not safe,’ he says. The ‘Jungle’ is the local name for the main campsite housing some 3,000 migrants in the dunes to the east of Calais. Jamal talks of drugs and gang wars. When I arrive mid-morning, most residents are sleeping after a long night of lorry-jumping. French charities provide a meal at 5pm every day and there is a standpipe and a row of grisly-looking portable loos. But the situation is not sustainable. Here I meet Masaret, 20, a business student from Keren, Eritrea. He speaks excellent English and explains that he has spent more than £3,000 getting this far, via Libya and a perilous voyage to Italy. ‘I have seen 15 people killed by IS and my home is a war zone. But there is nothing for us here in France. We want to go to Britain where there is potential. You have services for immigrants.’ His trousers are torn in several places after a botched attempt to climb under a train. ‘I am going to die or I am going to reach England.’ It is a tragic situation with no easy answers. But I can think of a few. After all, if I can stand here in broad daylight watching the smugglers at work, why can’t the French and British authorities have spotters doing the same? And the next time French militants set fire to the Channel Tunnel, is it too much to ask for them to be put on trial? This week, their leader, Eric Vercoutre, likened Tunnel security to ‘a sieve’ and has said he might do it again. If so, one thing is certain. The people who will really pay the price for this bedlam will not be the militants or the people smugglers. It will be the hauliers and coach drivers going about their work, the tourists heading off on holiday — and, ultimately, the British consumer. Photographs and video - http://www.dailymail.co.uk/news/article-3148953/The-British-trucker-blockaded-French-quelle-surprise-went-squealing-police-rage-inducing-dispatch-Calais-frontline.html .
-
General Motors Research Laboratories outlines the history of the diesel engine, including an explanation on how diesel engines work, and a comparison to gasoline-powered engines. https://www.gmheritagecenter.com/docs/gm-heritage-archive/historical-brochures/Innovation_and_Technology/Diesel-The-Modern-Power.pdf
-
Transport Topics / July 2, 2015 Rassini, a Mexico-based supplier of suspension and brake components, said it has expanded its offerings to include leaf springs for the North American commercial-truck market. The move extends the company’s reach beyond its established business in the North American light-truck and South American heavy-truck markets. “Entering the commercial truck market in North America was a natural progression for us, and we are already experiencing early success,” Rassini President Eugenio Madero said. The supplier said Ford Motor Co. recently awarded it a contract to supply the front suspension technology for the next-generation F-650 and F-750 work truck series built at Ford’s Ohio assembly plant. Rassini said it expects to provide heavy-duty suspension components for many North American truck brands. The marketing and sales operations for Rassini’s North American heavy commercial truck business are based in Plymouth, Michigan. Production, manufacturing, research and development are housed at the company’s facility in Piedras Negras, Mexico.
-
Daimler Press Release / July 2, 2015 Mercedes-Benz OM 471 (DD13) – the latest generation: Lower fuel consumption and CO2 emissions, more output and torque Consumption reduced, driving dynamics increasedNew: five output ratings up to 390 kW (530 hp)New: latest generation of the X-Pulse injection systemNew: high torque even from the bottom of the rev rangeNew: patented solution for exhaust gas recirculationNew: customised asymmetric turbocharger manufactured in-houseNew: even more robust thanks to the omission of sensors and pilot-controlled operation1100 litres of fuel savings a year and about three less tons of CO2 – two of the key benchmark figures for a long-haul tractor-trailer fitted with the latest-generation OM 471 13-liter engine from Mercedes-Benz, assuming an annual mileage of 130,000 km (80,778 miles). Four years on from the debut of the revolutionary OM471, the next evolution is here – and will allow the Mercedes-Benz Actros to broaden its lead in operating efficiency. Mercedes-Benz engineers have succeeded in squaring the circle, as fuel consumption has been reduced again, this time by up to 3%, while driving dynamics have been further enhanced by an increase in torque. The OM471 is spearheaded by a new 530 horsepower (390kW) power rating delivering 2600 Nm of torque. OM 471 in-line six-cylinder engine: a new era in engine manufacturing A perfect blend of economy and ecology: in spring 2011, in anticipation of the upcoming Euro-6 emissions standard and new Actros, Antos and Arocs heavy truck ranges for heavy-duty long-distance transport, short-radius distribution and construction, Mercedes-Benz unveiled an all-new generation of engines. The first member of the new engine family was the OM 471 (DD13). With its technical features and the resulting capabilities and qualities, the OM471 took engine manufacturing for heavy trucks into a new era. The 12.8-litre in-line six-cylinder unit made its mark with a robust design and technical innovations with significant benefits for the customer. Key features included the twin overhead composite camshafts, the singular common-rail injection system with X-Pulse pressure booster, the asymmetric exhaust gas turbocharger, the powerful engine brake and emission control based on SCR technology, exhaust gas recirculation and particulate filter in order to meet the stringent Euro VI emissions requirements. The engine left both business owners and drivers impressed The impressive fuel savings of the OM 471 caused a sensation from the outset with operators and drivers alike, further helped by outstanding aerodynamics. The OM 471 series sets new standards for heavy truck engines worldwide. Businesses benefit first and foremost from the low costs: low fuel and oil consumption, extremely long maintenance intervals of up to 150,000 km, as well as the engines' robustness and durability. Drivers, meanwhile, appreciate the spontaneous response from standstill, the tremendous pulling power even from low revs, as well as the drive units' refined operation and powerful engine brake. The OM 471 series engines have now built up a proven track record in practical operation in both the trucks and the buses and coaches from Mercedes-Benz and Setra. Including the closely related engines for overseas markets, production numbers have now reached the 250,000 mark – no other heavy-duty engine platform surpasses this figure or has proven itself so often. Systematic focus on low costs for the customer The engine development team has built on all the great qualities of the OM 471 with a raft of individual measures for the latest generation. The overriding goal for the engines' further development was to ensure they are systematically geared towards low operating costs. The latest generation of the OM 471 thereby succeeds in once again underlining the engines' quality. It brings about a further reduction in fuel consumption of as much as three percent, while the engines' robustness, which already verged on the proverbial, has been honed too. In addition to this, the engineers have achieved a substantial increase in torque at low rev speeds and expanded the line-up to a total of five output ratings with the addition of a new range-topping engine variant. New: five output ratings up to 390 kW (530 hp) The Mercedes-Benz OM 471 is now available in the following ratings: Output Torque 310 kW (421 hp) at 1600 rpm 2100 Nm at 1100 rpm 330 kW (449 hp) at 1600 rpm 2200 Nm at 1100 rpm 350 kW (476 hp) at 1600 rpm 2300 Nm at 1100 rpm 375 kW (510 hp) at 1600 rpm 2500 Nm at 1100 rpm 390 kW (530 hp) at 1600 rpm 2600 Nm at 1100 rpm The basic output variants delivering 420, 450 and 475 horsepower are complemented by three "top torque" versions, which offer an extra 200 Nm of torque on tap as required whenever the highest gear of the Mercedes PowerShift 3 automated transmission is engaged. This strategy has the effect of reducing the frequency of gear changes and increasing transportation speed without any negative impact on fuel consumption. This is further helped by the fast torque build-up at very low rev speeds, which has been optimised again in the latest generation of the engine. However the raw figures for the engines' maximum output and torque only tell part of the story: the peak output of all the new-generation engines is available virtually constantly over a wide rev range between 1450 and 1800 rpm. Maximum torque likewise stays at a nearly constant level from around 900 up to 1450 rpm. The result is excellent drivability with an exceptionally wide usable engine speed range. New: the latest generation of the X-Pulse (ACRS) injection system A key component of the new generation of engines is the latest-generation X-Pulse injection system (aka. Amplified Common Rail Fuel System) – the unique common-rail system with pressure booster in the injector and unrestricted flexibility for modelling the injection system. Maximum rail pressure has been increased from 900 to 1160 bar, resulting in a maximum injection pressure of 2700 bar. The injection nozzle is an eight-hole nozzle (previously seven holes), increasing the maximum flow rate by around ten percent. Additional modifications include the piston bowl geometry, the sizeable increase in compression ratio from 17.3:1 to 18.3:1, along with a reduced exhaust gas recirculation rate (EGR rate). All these measures add up to a further improvement in efficiency across the entire engine performance map. This in turn lowers fuel consumption significantly. The optimum values in the consumption characteristic map have followed the new torque curve towards lower rev speeds. Systematically configuring the engine for low fuel consumption means that untreated NOx emissions rise. This is countered by the SCR technology featuring an innovative and efficient SCR catalytic converter. AdBlue consumption is therefore on a par with earlier Euro V engines at around five percent of fuel consumption. The costs work out: the drop in fuel consumption of up to three percent comes at the expense of nothing more than a slightly higher quantity of the far cheaper AdBlue needed for emission control. To put it differently, assuming an annual mileage of 130,000 km in long-distance transport and a consumption of approx. 28.5 litres/100 km on a demanding route covered at full load capacity, every single Mercedes-Benz Actros with the latest-generation OM 471 engine would save around 1100 litres of fuel a year and emit about three tonnes less CO2. New: top-of-the-range engine with 390 kW (530 hp) The latest-generation X-Pulse system with its far higher injection pressure is also a vital prerequisite for the new top-of-the-range version of the OM 471 engine. It generates an output of 390 kW (530 hp) while delivering a sensational peak torque of 2600 Nm. Even from its idling speed of 600 rpm, the new engine produces a mighty 1600 Nm of torque. This takes the OM 471 into the sort of power output and torque ranges that were still the preserve of far larger engines and eight-cylinder units just a few years ago. The OM 471 is one of the most powerful diesel engines in its class. Special mention should be made of both the output of 30.5 kW (41.4 hp) per litre of displacement and the torque of 203 Nm per litre of displacement. Thanks to these exceptional figures, the new flagship engine is perfectly capable of handling even very demanding applications with gross combination weights of 40 tonnes and more. On top of this, operators also benefit from substantial weight and fuel savings when compared to larger engines with similar output ratings. New: high torque even from the bottom of the rev range The new injection system benefits not just the new range-topping version, but all other output variants of the OM 471 too. Although the nominal maximum output and torque figures for the engines remain unchanged, the output and torque curves at bottom-end revs rise far more sharply, endowing the engines with quite different performance characteristics. Now, all engine output ratings already muster up at least 2000 Nm of torque at just under 800 rpm. Depending on the output rating, close to peak torque is now already on tap between around 800 and 950 rpm. Consequently, the output curves of the new engines develop just as favourably. The rated output rev speed is now 1600 rpm, yet even at the previous speed of 1800 rpm, output is just one percent below maximum. Depending on the output variant, 95 percent of maximum output is already being generated at around 1300 to 1400 rpm. What this means in practice is outstanding drivability under all conceivable conditions across an extremely wide usable engine speed range of about 1000 rpm. At low rev speeds in particular, the already powerful engines now rank at least one output category higher than previously. New: longer final-drive ratio lowers engine speed Mercedes-Benz has capitalised on these new performance characteristics and used a longer standard final-drive ratio. A ratio of i=2.533 instead of the previous i=2.611 translates into a rev speed reduction of three percent. When fitted with 315/70 R 22.5 tyres, this results in an engine speed of around just 1150 rpm at a speed of 85 km/h. Thanks to the new output characteristics, this is not accompanied by any loss of performance. On the contrary: the engines now have significantly higher power reserves on uphill stretches. This extra power is not only apparent when driving on the motorway, but also on trunk roads and country highways. This is clearly exemplified by the highly popular Actros 1845. When travelling at a speed of 65 km/h in top gear, its engine speed is not even 900 rpm with the new axle. At this rev speed, the engine already generates close to its maximum torque of 2200 Nm and feels as if it still has plenty of power in reserve. With the previous engine and axle configuration, the Actros 1845 was running at a rev speed of just over 900 rpm when moving at the same speed in top gear, while its torque of just under 2000 Nm was already sloping off. To sum up, this all means that the latest generation of the Mercedes-Benz OM 471 combines notably higher performance with considerably lower fuel consumption. New: patented solution for exhaust gas recirculation The asymmetric turbocharger has been one of the special features of the OM 471 engine from the very start. In order to build up charge pressure fast with an equally brisk rise in output and torque, the exhaust gases from cylinders four to six are channelled straight to the turbine without any detours. A defined quantity of the exhaust gases from cylinders one to three, on the other hand, is diverted for the purpose of exhaust gas recirculation. This serves to reduce the NOx emissions. This fundamental solution has been retained, but the details have been refined to crucial effect. The previous EGR flap in the EGR path has now given way to an EGR flap repositioned much further forwards in the exhaust manifold, some distance before the exhaust gas enters the turbocharger. Whereas the distribution of the exhaust gases between exhaust manifold and turbocharger was previously partly dependent on the shape of the manifold and the geometry of the asymmetric turbocharger, distribution can now be infinitely and very precisely adjusted throughout the entire range of the engine performance map. This results in effective thermal management and a lower EGR rate in general with advantages for fuel consumption. Both the EGR rate and the exhaust gas flow to the turbocharger can be controlled in accordance with the engine's operating characteristics thanks to the flap's new position. This has therefore eliminated the need to monitor exhaust gas recirculation using a sensor in the venturi tube (the exhaust gas recirculation bypass) as well as a downstream EGR control system. The repositioning of the infinitely adjustable EGR flap furthermore opens up a whole new spectrum of asymmetry: the quantity of exhaust gases directed from the three donor cylinders to the combustion process can be varied exactly as required between zero and 100 percent – something which is unprecedented in engine manufacturing. The EGR flap thereby controls not just the flow of exhaust gas for exhaust gas recirculation, but also the turbocharger. New: asymmetric injection optimises emissions quality The asymmetric injection is another new feature. During normal driving, the injectors for all six cylinders in the OM 471 engine are supplied with an identical quantity of fuel. If regeneration of the diesel particulate filter is required at low loads, a high EGR rate of up to around 50 percent is set in order to raise the exhaust temperature. In order to prevent incomplete combustion in this situation which would result in a higher proportion of soot particles in the exhaust gas, the fuel quantity is smoothly reduced in cylinders one to three as the EGR rate rises and increased in cylinders four to six. In extreme cases, the injection quantity for the first three cylinders can be zeroed, while the other three cylinders operate as if at full throttle. Neither power output nor fuel consumption are affected by this reduction in fuel quantity down to complete cylinder shut-off, but emissions quality improves and soot particle levels drop. The asymmetric shift in injection is imperceptible to the driver. The same applies when the engine load is increased by depressing the accelerator and fuel injection becomes uniform for all cylinders again. New: supremely efficient turbocharger manufactured in-house A new asymmetric turbocharger is partly responsible for the swift and substantial increase in power delivery at low rev speeds. It was developed by Mercedes-Benz and is manufactured in the Mannheim engine plant. An in-house turbocharger ensures customised adaptation to the requirements of the OM 471. The turbocharger excels for its outstanding efficiency. Very tight production tolerances are a guarantee of supreme quality and durability. As before, the asymmetric turbocharger features a fixed-geometry turbine. From a technical standpoint, this variant is far less complex and thereby less prone to faults than a VNT turbocharger, for instance. It also does without a wastegate valve, further simplifying the design. This measure reduces the turbocharger's complexity and avoids a potential source of faults, such as leaks – another plus point as far as the robustness and durability of the OM 471 are concerned. New: even more robust thanks to the omission of sensors and pilot-controlled operation Besides a wastegate valve for the turbocharger, Mercedes-Benz has also dispensed with boost pressure control in the latest generation of the OM 471. Together with the elimination of the EGR sensor and EGR control, this means that operation of the engine with its meticulously optimised thermodynamics is purely pilot controlled. Controlling the engine in this way allows it to run even more efficiently. Precision pilot control of all variables results in an optimum efficiency factor without the added complication of individual control systems and their combination. The ingeniously devised emission control strategy, for example, replaces the individual control of exhaust gas recirculation and boost pressure that was customary in the past, and works far more effectively in this way. At the same time, the engine has become even more robust owing to the omission of numerous components and parts. The fundamental idea here is perfectly simple and makes perfect sense: anything that's not fitted in the first place can't cause a malfunction. Instead of using sensors with a linked system of control, Mercedes-Benz relies on various modes to assist with operation with, for instance, a cold engine, cold intake air or a cold exhaust aftertreatment system. Suitable modes have likewise been programmed for operation at medium and high altitudes, as well as for passive and active regeneration or regeneration when idling. With the exception of active regeneration, all the control modes are continuously variable, allowing the engine to be operated in an optimum efficiency range at all times. New: air conditioning saves fuel When it comes to the matter of TCO, fuel consumption and emissions, Mercedes-Benz considers every single vehicle component. The Actros and its siblings have been demonstrating this since 2011 with their regulated ancillary units and innovative fuel-saving air compressors. The latest optimisation measures include a new air conditioning system. Its refrigerant compressor works more efficiently, while the air management system impresses with its needs-based control of fresh air and air recirculation. The air conditioning thereby also helps to achieve the fuel savings in the heavy-duty trucks from Mercedes-Benz. Fuel consumption cut by 13 percent in just four years The advances are remarkable: since 2011, following the introduction of the new Actros with Euro VI emissions rating, the Predictive Powertrain Control (PPC) cruise control system and the new engine generation, average consumption has dropped by 13 percent compared to the predecessor Actros model. And it is important to note that the trusted Euro V Actros already ranked as one of the most economical trucks in Europe. By contrast, long-term improvements in consumption normally average out at around 1.0 to 1.5 percent a year in the commercial vehicle sector, which further underlines the exceptional technical expertise and innovative strength of Mercedes-Benz. Back in 2011, Mercedes-Benz eclipsed the competition when it brought out the first engines with a Euro VI emissions rating. The same is now set to happen again with the latest generation of the OM 471. The new generation of engines combine supreme economy on the one hand with extraordinary performance capabilities on the other. For the time being, they represent the fascinating pinnacle of development. Yet things will keep evolving, as the No. 1 in the heavy-duty truck segment and the No. 1 for fuel consumption never stands still. .
-
The events taking place in American society today are shocking.......and shameful. Child abuse is rampant across the country. No child brought into this world deserves to encounter such horror. The definition of “socially acceptable morals and values” is clear to any ordinarily prudent individual. However, unlike the automobile and truck which have “evolved forward”, from primitive machines into the highly sophisticated ones we know today, American society appears to be “regressing”, moving away from the signature morals and values that for decades defined America, and made our great country the envy of the world. The American government, I feel, inherently bears significant responsibility in guiding the positive forward development of American society. But just who am I pointing a finger of blame at? As a much admired President Lincoln once said, we are “a government of the people, by the people, for the people.” Daniel Webster said much the same, that the government is “the people’s government, made for the people, made by the people, and answerable to the people.” The American people are the U.S. government...........the U.S. government is the American people. Think about that. Thus, as our own self-appointed stewards, we have to blame ourselves for the decline of American society. Yes, one can argue I am not speaking of our reality. You are so right. Our government often does NOT appear to be functioning as “a government of the people, by the people, for the people.” Again, "we the people" of the United States are responsible for allowing our government to head off course, away from our control, and away from our country’s founding principles. Over the last 20 years, we have observed what to us in our youth was unthinkable. Who on this forum in their teenage years would have walked into a school and taken the life of another human being. The thought never crossed our minds. But the minds of recent generations are clearly different, indicating that we as a people and government combined are seriously failing in our responsibility to lead society. We have a responsibility to effectively raise the bar of morals and values for each new generation of Americans. However, and clearly so, society is plunging to a lawless state that in some aspects is already out of control. And yet, our government of the people does not speak of this crisis, nor address it. When tragic events occur, leadership utters politically correct words like "troubling" and "heartbreaking", and then resumes their normal routine. At some point several decades ago, the values that shaped our morals and values stopped being taught to a sizable portion of the masses, and we’re seeing the effects today in the form of senseless tragedies. Our government refuses to speak of (acknowledge) America’s crisis in society, apparently taboo in Washington, and has taken no steps to address it. An American society with strong moral principles and values is not an option........it is a necessity to safeguarding our future.
-
Mother tosses son off bridge, killing him KGW-TV / November 4, 2014 A 34-year-old woman is charged with throwing her son off the Yaquina Bay Bridge. Jillian McCabe of Seal Rock, Oregon., called 911 at about 6:25 p.m. PT on Monday to report that she threw her 6-year-old boy into the water. "I just threw my son over the Yaquina Bay Bridge," she told a 911 dispatcher. Before throwing her son to his death, she searched “not guilty by reason of insanity” on Google on her phone. McCabe told police that she heard voices telling her to throw the child off the bridge, which is 133 feet above the bay. She told the dispatcher her son, London, was gone in the water and described him and his clothing in detail. She then described herself as an officer approached her. She told several officers on the scene that she had thrown the boy into the water. The 6-year-old boy's body was found almost four hours later by the Coast Guard floating near a marina. McCabe was charged with aggravated murder, murder, and first-degree manslaughter and second-degree manslaughter and is being held on $1 million bail. Jillian McCabe appeared by video in Lincoln County Circuit Court in Newport, where she entered no pleas on the charges against her, the court reported. Two Portland attorneys were appointed to represent her. The aggravated murder charge, which carries a potential death penalty, was filed because the boy was under 14 years old. --------------------------------------------------------------------------------- Toddler thrown off Allentown bridge dies The Morning Call / May 10, 2015 A 20-month-old boy died Saturday morning, six days after his mother threw him into the Lehigh River from the Hamilton Street Bridge in Allentown. Zymeir Perry of Allentown died at 11:51 a.m. at Lehigh Valley Hospital-Cedar Crest, Lehigh County Coroner Scott Grim said. Authorities say the toddler's 19-year-old mother, Johnesha Perry, kissed her baby before pushing him over the rail and into the water, then jumped from the 52-foot-high bridge herself. Witnesses said Perry managed to walk to shore before collapsing, while Allentown police Officer Joseph Ianetta pulled Zymeir from the river about 700 yards downstream and performed mouth-to-mouth resuscitation. Witnesses told police that Perry said it was her time before she plunged into the water. Allentown police had charged Perry with attempted homicide before the baby's death. District Attorney Jim Martin said Saturday evening that Perry has been released from Lehigh Valley Hospital-Cedar Crest and moved to the Lehigh County Jail. Perry had previously been charged with two counts of aggravated assault and one count of endangering the welfare of a child. She was being held under $100,000 bail. --------------------------------------------------------------------------------- Father tosses 5-year-old daughter off Florida bridge to her death A 5-year-old girl is dead after her deranged father tossed her off a Florida bridge, and then calmly drove off as frantic rescuers tried to recover her body, police said. The girl plummeted some 62 feet to the Tampa Bay waters below while her father Nicholas Jonchuck took off, police said. Rescuers from Eckerd College found the girl in the water nearly two hours after the fatal plunge, about a mile from where she was tossed. She was pronounced dead at a hospital around 2:45 a.m., police said. Jonchuck has previous arrest for domestic violence dating to 2008, online jail records show, and he was busted for DUI and battery in 2013. Despite his checkered past, he had custody of his daughter.
-
ObamaCare started out as the 2006 RomneyCare Massachusetts health care insurance reform laws. Romneycare was a rationally thought out healthcare plan. But Washington gutted it, created an absolute mess called ObamaCare and dumped it on the masses. Having said all that, the U.S. insurance industry is one of the largest scams in our daily life (followed by the airline industry). The amount of money that Americans pay for all forms of insurance is shameful. For the first time in decades, we had a man qualified to be president running in 2012 - Jon Huntsman. But the establishment had the media keep the spotlight off him. The son of the founder of Huntsman Chemical, he wasn't about money. A Mormon, he had no tolerance for the status quo within the beltway around Washington and wanted to begin fixing America.
-
Failure of new U.S. weapons systems may be more than science fiction
kscarbel2 replied to kscarbel2's topic in Odds and Ends
As we've all learned in life, tomorrow's challenges more often come from where we least expected. We have a twisted relationship with many countries who are not our friends, Saudi Arabia being one of them. The lawless land directly under the U.S., aka. Mexico, should be a major security concern to all Americans. But note how Washington continuously sidesteps the issue. That our government on not one but two occasions has decided to grant amnesty to thousands of illegal immigrants from Mexico and Latin America is shocking. The U.S. has established immigration laws, which include procedures for legal immigration into the US. So, why does a British national have to endure our immigration process, when a Mexican national who illegally crossed our borders at night can stay and receive a green card, welfare and send his/her children to our public schools. It's all rather mind boggling why an illegal imigrant from Turkey is deported, but Latin Americans are invited to remain.....with benefits. What is the purpose of our immigration laws when our government arbitrarily enforces them? And, allowing illegal Latin American immigrants to stay in the US under amnesty programs, but not individuals desiring to immigrate from other global regions, is blatant discrimination. Last time I checked, the American values our government touts frown on discrimination. -
At the behest of the establishment, the media successfully discredited Perot. Yes, Perot was colorful, but he spoke the hard truth. For example, he told the American people the actual truth on NAFTA *. Not having ever heard someone running for government speak bluntly and directly about the issues, the brainwashed masses didn't know what to make of Perot, and were afraid to stray away from the established Washington Show. * The establishment's sales pitch for NAFTA to the gullible masses was a complete fabrication, a brilliantly played out distraction from the truth. NAFTA in fact was the idea of big business, a way for them to produce in low-labor-cost Mexico, and then import to the US without tariffs.
-
Their isn't one presidential candidate who is truly qualified to be president. As has been for decades, qualified Americans avoid the position. The theatrical Trump tells people the hard truth, but the masses aren't interested in realty. Thinking about our country's stewardship takes up too much time. The thought of Hillary being elected.......is very scary.
-
Reuters / July 2, 2015 A war between China and America is a favorite subject of armchair military analysts. Why would it happen? How would it play out? Authors have written thousands of pages online and off trying to answer these questions. That’s why Ghost Fleet, a new novel by national-security analysts August Cole and P.W. Singer, is fascinating. The book, set in the near future, is an account of a war between China and the United States written by two men whose day jobs are studying conflict and making policy recommendations. If anyone could get this scenario right, it’s these two military experts. Though it is fiction, the authors have taken great pains to keep their storytelling realistic. The novel particularly shines when the writers depict the failures of the Pentagon’s newest weapons systems. Over the past decade, U.S. taxpayers have poured trillions of dollars into fancy new weapons, such as the F-35 Joint Strike Fighter and the Littoral Combat Ship, though defense experts warned of their many failings. Lockheed Martin, the chief contractor on the F-35, attributes the planes many documented problems to its stage of development and promises that they all will be corrected by the time of deployment or shortly thereafter. Ghost Fleet imagines a war that begins with the Littoral Combat Ship and F-35 and ends with the United States relying on a reserve fleet of older, but more reliable, weapons moored near San Francisco. The Pentagon’s newest toys fail so spectacularly that Washington must fall back on their old, less technologically dependent weapons. The authors could be most prescient when describing the failings of recent U.S. military investments. They are less so when explaining why China picks a fight with the United States. Cole and Singer are so used to citing their military research that they’ve done it in their novel. Ghost Fleet has extensive footnotes. Don’t believe a passage about an emerging technology? The notes direct you to the Pentagon press release about it. Because of this, Ghost Fleet has a certain weight. Cole and Singer are so steeped in future wars that they depict the fighting — on the ground, in space and on the Internet –with an air of indisputable authority. Killer weapons and legacy systems The Pentagon’s current obsession with Swiss-army-knife-style weapon systems, which are able to do many different things, leads it to lose the first major battle against China in Ghost Fleet. In the novel, China kicks off its assault on the United States with an epic redo of Pearl Harbor. Faced with a surprise attack, Washington’s fleet of fancy Littoral Combat Ships and hangars full of F-35s can’t fight off Hainan’s troops. Part of this is due to the surprise attack, but much is due to the technology itself. The LCS and F-35s are largely untested weapon systems beset by ballooning budgets and horrifying problems. Worse, according to the authors, both rely far too much on computers. The F-35, in particular, is considered by many weapons experts to be a laughingstock. Its gun can’t shoot because Lockheed has yet to write the software for it; the $600,000 helmet required to fly the plane has yet to work as intended, and, in at least on case, the jet’s engine has caught fire. Despite these problems, the Pentagon is adopting the F-35 in all of its branches … and getting rid of battle-tested legacy systems. Ghost Fleet shows us the consequences of a U.S. military-industrial complex focused more on selling expensive new systems than on building quality weapons. Cole and Singer’s rendering of Pearl Harbor Two hinges on how shoddy the LCS and F-35 are. They’ve written a fictional version of the nightmare-scenario defense that many military journalists and analysts have long predicted would happen when the F-35 went to war. Following a series of sophisticated cyberattacks, the fancy jets barely fly, don’t carry enough ammo to effectively engage the enemy and are easily destroyed by Chinese fighters. In the end, it’s America’s ghost fleet that comes to the rescue. The Pentagon resurrects ships and planes retired by defense-contractor overreach and technological hubris. The old F-16s and A-10s still fly, and they’re ready and able to beat back America’s enemies. They are simple weapon systems, particularly when compared to the F-35 and the LCS. Better yet, they use outdated and simplistic computers that China can’t jam or hack. In Ghost Fleet, the old planes are the best planes. It’s vastly preferable to see the F-35′s failure in fiction than in real life, where real lives would be lost. Lockheed Martin, the manufacturer, says its product is reliable and able. “Here’s the truth about the F-35,” the company wrote in a recent statement about the jet responding to media criticisms of the weapon. “The jet has flown to the corners of the flight test envelope and it’s meeting or exceeding expectations in performance. There are no insurmountable obstacles to successfully completing the development program on schedule in 2016.” Clashing interests Ghost Fleet is full of wonderful moments. It’s got space pirates, drug-addled hackers out of a William Gibson novel and American insurgents fighting occupation in Hawaii. Cole and Singer make these fantastical elements work, and weave them into the story. But there’s a problem. The reasons behind the conflict feel far-fetched. The motivations of the Chinese antagonists feel more like the schemes of a Bond movie villain than the inevitable outcome of current geopolitics. There is a pernicious myth that the United States and China will never go to war because they are economically interdependent. But a closer look at history should worry everyone. China and America are closely linked economically. China sold the United States almost half a trillion dollars worth of goods in 2014, and Beijing holds trillions of Washington’s debt in U.S. Treasury bonds. But it’s quite possible that, as Ghost Fleet details, it is because of these economic ties — not in spite of them — that the two superpowers might come to blows. The authors debunk the idea that economic interests would prevent another world war within the first 30 pages of their novel. One character explains that imperial Germany was Britain’s largest trading partner before World War One. Japan, he says, was America’s biggest trading partner leading up to World War Two. The economic ties between Japan and America leading up to World War Two are more complicated than that. The island nation relied on U.S. oil imports to keep its military rolling. Washington, however, didn’t like Tokyo’s attempts to expand its territory into China. Congress attempted to sanction and blockade Japan to cut it off from its military’s main source of oil — the lifeblood of its dreams of empire. In Ghost Fleet, after a catastrophe in the Middle East, America becomes the world’s largest energy exporter. China’s Communist Party falls and a more militaristic, capitalist system replaces it. The two nominal allies expand their trading territory, and China imports most of its fuel from America. Then, Chinese scientists discover a massive natural-gas deposit in the Mariana Trench. This new source of energy means China can divorce itself from its old trading partner. Worse, the Chinese military establishment convinces the political leadership that China can no longer expand its trading territory without taking some away from its largest competition — the United States. So China attacks America to assert itself as a global power and establish more control over the Pacific Ocean’s trade routes. It’s an elegant and fictional way to get everyone fighting. But the world is far more complicated and chaotic. According to the Pentagon’s most recent report on China’s military, Beijing’s goals are “defending … territorial integrity, securing China’s status as a great power, and, ultimately, reacquiring regional preeminence.” These goals, especially the first and last, are key to understanding how a war between the superpowers might occur. The United States currently dominates the Pacific, but China has expanded rapidly to defend its increasing interests in the western Pacific. It is there, in the waters off the Chinese mainland, that I believe we’ll see the event that starts a war between the superpowers. It will probably be something ridiculous. Tensions between Washington and Beijing have escalated in recent years as China has asserted itself more and more beyond its borders. Beijing currently claims Taiwan and several islands scattered throughout the west Pacific as its territory, and it’s fielding more ships, planes and even building artificial islands to legitimize its claims. Washington holds treaties with Japan, Taiwan and the Philippines, and the U.S. Navy aggressively patrols the waters in these regions, often coming right up to the perceived border with China. If China ever invades Taiwan or pushes into the wrong island off the coast of Japan, the wronged country may go to war against Beijing. Such a conflict would test the value of a treaty with Washington and may drag it into a larger war. As tensions rise, both sides might also perceive tiny infractions as aggressive behavior. Both Beijing and Washington claim it would never throw the first punch, but we may soon see a day where an act of war is as simple as a U.S. jet crossing into Chinese airspace, or a Beijing drone crashing in Japan. The Chinese leadership in Ghost Fleet is aggressive and arrogant, ready to take what it wants at the edge of a sword. It begins the war for prestige and power. Often, wars begin for sillier reasons, and people later justify their actions as part of a larger scheme that never existed. In 1969, a World Cup qualifying match sparked a four-day war between El Salvador and Honduras. The fighting wasn’t about soccer; the match just ignited existing tensions. In 1914, a Serbian anarchist assassinated Austria’s archduke and set off a tidal wave of events that killed almost 40 million people. Wars often begin this way, when some small event pushes existing tensions to the fore. The United States and China just need another decade of tension and the right spark. It won’t take anything as contrived as a vice admiral’s dreams of a dominant China. Ghost Fleet is written by defense experts with a flair for fiction and a desire to document their sources. Their predictions of how and why the superpowers come to blows may not be plausible, but their vision of how the conflict would play out–in cyberspace and in the Pacific – seems so realistic that it’s frightening. Article - http://blogs.reuters.com/great-debate/2015/07/01/failure-of-new-u-s-weapons-systems-may-be-more-than-science-fiction/
-
Forget the casting number. When you called your Mack dealer, were they able to cross 8QE44 over to the Wagner number via part number supercession, or their old paper Mack-to-Vendor crossover book?
-
Yesterday, the Washington Navy Yard campus was placed on lockdown amid reports of gunshots in the same building where 12 people were killed during a shooting rampage in 2013. Gunshots make a distinctive sound. And federal official say a surveillance video showed two people jumping the fence next to the building a couple of minutes before the first report of the gunshots. But 12 hours later, all news of the event has been whitewashed from the headline pages of the online media. (you can google search it) Officials have since issued an "all clear", saying they haven't found any credible evidence of a threat. We are expected to believe that surveillance video showing people jumping the fence next to the building minutes before the first report of the gunshots is not suspicious, much less credible evidence of a threat. Peculiar?.........you be the judge.
-
Press Release / May 2015 Diamond Specialty Vehicles of Hershey, Pennsylvania, doing business as T-Line Specialty Vehicles, has displayed its new TCS vocational hood configuration and “Driver II” aluminum construction Diamond T cab. Website: http://tlinetrucks.com/ Related reading: http://www.bigmacktrucks.com/index.php?/topic/40010-t-line-successor-to-diamond-t-plans-return-to-market/?hl=t-line http://www.bigmacktrucks.com/index.php?/topic/39977-t-line-announces-summer-launch-for-raider-ii/?hl=t-line http://www.bigmacktrucks.com/index.php?/topic/39126-diamond-specialty-vehicles-announces-all-new-models/?hl=t-line .
-
- 2
-
-
Göteborgs-Posten / July 2, 2015 In the election campaign, Prime Minister Stephen Löfven promised an investment in an industry chancellor, who will lead the job of growing Sweden’s industrial base. But it will not be a single chancellor, rather it will be four: Ousted Volvo CEO Olof PerssonLisa Lindstrom, CEO of the digital design company DobermanPia Sandvik, Chairman of the Research Network RISEKarl Gustaf Ramstedt, CEO at embedded system and industrial IT company Prevas The four will support the government's job of developing Sweden into an even stronger industrial country.
-
STEMCO Acquires Goodyear Air Springs Business Trailer/Body Builders / July 1, 2015 Stemco, an EnPro Industries company, has acquired the manufacturer of Goodyear air springs, as well as Super Cushion and Spring Ride air springs, from ContiTech, a division of Continental Corporation. This business unit was part of the business called Veyance that was recently acquired by Continental. With the acquisition, STEMCO acquires the Super Cushion and Spring Ride lines of truck, trailer and truck cab suspension products, as well as cab seat springs. Also included in the acquisition are the Veyance manufacturing facility in San Luis Potosi, Mexico, the Veyance research and development operations in Fairlawn, Ohio, and all NAFTA related patents and applications. "The Goodyear air springs business carries with it a strong brand presence and premium product performance," said Todd Anderson, STEMCO president. "Customers will be able to count on the same consistent product performance and brand attributes, as the products will continue to be manufactured in the same facility and engineered by the same design team with the same support functions, in addition to gaining the support of the entire STEMCO team." He added, "We are looking forward to the air springs team joining the STEMCO family. Their record of success and growth potential make this an exciting addition to our business. STEMCO's commercial vehicle market focus, superior product technology and outstanding reputation for training and customer support make this acquisition a complement to the STEMCO business strategy." Air spring products are available now through the existing distributor network. For more information on the new STEMCO product lines, visit www.stemcoairsprings.com.
-
Child dies after running for hours carrying firewood, Grandmother and mother-in-law charged WYFF / March 10, 2015 An Alabama woman charged with capital murder in the death of her granddaughter forced the girl to run for more than three hours carrying sticks and firewood as a punishment for lying, prosecutors said Monday. Joyce Garrard is accused of forcing 9-year-old Savannah Hardin to run until she died as punishment for a lie about eating candy on the school bus. She could be sentenced either to death or life without parole if convicted. According to prosecutors, neighbors said Garrard yelled at the girl as she ran, forcing her to continue "like some kind of drill sergeant." A neighbor, Chad Jacobs, said he saw the girl running and carrying firewood and sticks over a two-hour period as he came and went from his home. "Joyce and Savannah were in the yard, and Joyce was telling Savannah to keep running," said Chad Jacobs. "She was just saying, 'Keep running, I didn't tell you to stop.'" Jacobs said he wasn't concerned at first but eventually saw the girl "on all fours" on the ground and vomiting with Garrard pouring water over her. Paramedics arrived within minutes, he said. When paramedics arrived, they found Savannah on the ground, "freezing cold to the touch," her clothes and shoes soaking wet, Reid said. Garrard never told the medics that the girl had been running; she said only that the girl collapsed in the yard, Reid said. Savannah wasn't supposed to eat candy because she was on medication for attention deficit hyperactivity disorder and had a bladder problem, but she had eaten candy on the school bus the day before she died. Garrard was angry that Savannah ate the candy "but she was more upset about the lie," Reid said. Surveillance video from a school bus shown to a jury showed Garrard talking with the bus driver, Raenna Holmes, about Savannah taking candy without paying from another student who was selling it. Garrard told Holmes: "She's going to run until I tell her to stop." The women then talk about a bladder condition the girl had and a procedure she had related to that condition. The driver then asks, "Is she OK?" Garrard replies: "She might be when I get about four more bottles of water in her." The girl's stepmother, Jessica Mae Hardin, is awaiting trial on a murder charge in the girl's death. Authorities said she failed to intervene while the older woman forced the girl to run.
-
Texas mom murdered daughter, 4, stuffed her in car trunk New York Daily News / June 22, 2014 A Texas mom facing an impending divorce murdered her innocent 4-year-old daughter and stuffed the body in the trunk of a car because she was jealous of the happy little girl, shocked family members say. Stacie Marie Parsons, 25, walked into the Athens, Texas police department just before 9 a.m. Monday and told officers she had murdered her daughter. Police found the badly beaten girl, with severe head and chest trauma, wrapped in a garbage bag in the trunk of the car along the 400 block of Martin Luther King Jr. Blvd. Investigators believe the woman drove to a bridge some five miles away and committed the horrendous act before driving the car back home and walking to the police station. Gary Wyatt, her common-law husband of six years, said he’d told the woman he wanted a divorce Sunday night, setting off a ferocious argument. Parsons and little Victoria were gone when he awoke Monday morning but that he assumed they had gone to sign up for prekindergarten. When she returned home, she wouldn’t talk to her 45-year-old husband or his friend, Randy Dyess. Instead, she turned with a dark stare and said, “I wouldn’t be in that car if I were you.” "Oh, God it was awful,” a weeping Wyatt told the TV station. “Foaming out of her mouth, her head was bashed in. My baby's dead, she killed my baby." Cops haven’t released a motive, but a bawling Wyatt said his wife resented Victoria, her own baby. “To be honest with you, I think she's been jealous of that little girl since the day she was born," he told KLTV. And family friend Dyess said the woman was always on edge, even before the recent dustup over the possible divorce. "She said I'd rather kill Victoria and spend the rest of my life in prison, than to put up with you," Dyess told the station. Parsons is held in jail in lieu of $2 million bond. She has no prior criminal history.
-
2 arrested in twisted, gruesome child abuse case; Corpse, starved teen and sick infant found Associated Press / April 8, 2015 Two people have been arrested in what authorities describe as a twisted, gruesome case of abuse involving a child's corpse hidden in a broken-down car, a starved baby living on water and a sheltered teenager impregnated by her stepfather. Jondrew Lachaux, 39, and Kellie Phillips, 38, turned themselves in after the three children were discovered, North Las Vegas police said. The two face child abuse charges. Lachaux is also charged with concealing evidence after the toddler's badly decomposed body was found in the garage. According to court documents, the man and woman took five of their children on a trip to Oakland, California, eight months ago. The couple left behind two daughters — a teen and a sickly 3-year-old toddler — in their suburban Las Vegas home because the rental vehicle was full. The teen is Phillips' biological child and Lachaux's stepdaughter. Authorities say Lachaux reportedly impregnated the teen, who gave birth at home without any medical care to a now 4-month-old girl. She struggled to care for herself while pregnant and her 3-year-old sister who had medical problems while they were home alone. But the teen said she was too scared to call for help even after the food and medication left by their mother ran out. "The totality of evidence is leading investigators to believe she was almost a prisoner in her home," police Sgt. Chrissie Coon said. "Fugitives can psychologically confine their victims without physically being present." The case first unraveled on April 1. The teen was seen at McCarran International Airport with a very sick baby. The infant was hospitalized in extremely critical condition for severe malnutrition and hypothermia from surviving on watered-down baby formula. In an interview with police, the teenager described abuse at home in detail, saying Lachaux raped her without her mother knowing. For the last five years, the family had lived in North Las Vegas, but the group of children rarely went outside and was homeschooled. The teen told police she has had braces on from five years ago but hasn't seen a dentist since. In late March, she said her stepfather came home to hide her sister's corpse and then kicked her out of the house in fear that her mother would find out about the pregnancy. She survived for a few days homeless in public places, including at the airport and on the Las Vegas Strip. The teen said the 3-year-old sister apparently had trouble breathing and died about a month ago. She called her parents for two weeks before Lachaux called back to learn of the death. Lachaux and the teen hid the badly decomposed body in the back seat of a broken-down Mercedes in the garage. The corpse was leaking fluids but was concealed in a box surrounded by blankets, plastic bags and pizza boxes, according to court records. The coroner's office said it has not yet positively identified the body or the cause of death. The teen is now being held in juvenile detention on a child abuse charge. The other five children -- ages 1, 3, 4, 7, 8 and 9 -- were found with Phillips in good health and have been put in protective custody.
-
The Next Frontier in Airline Travel - Tag Your Own Bags The Wall Street Journal / July 1, 2015 For decades, fliers have checked their bags the same way: hand them to an airline employee and trust that they will reappear at the destination. Now big changes to that model are coming as airlines look to streamline the airport experience—and pass more work to customers and machines. The airlines latest ideas includes having fliers tag their own bags, print luggage tags at home and track their bags on smartphones. Later this year, some fliers in Europe likely will begin using what could be the future of flying luggage: permanent bag tags that digitally update if flight plans change. Improved technology and loosened security rules are accelerating changes to baggage handling. The changes face hurdles, including opposition from unions, security rules and fliers who prefer a human touch. On a recent weekday at Chicago’s O’Hare International Airport, several fliers struggled to tag their bag and summoned airline employees for help. Still, carriers are plowing ahead. More than a third of global airlines now ask fliers to tag their own bags, compared with 13% in 2009. By 2018, more than three-quarters of carriers intend to offer the service. “I don’t work for the airline. Why should I do their job?” said Mark Sam Rosenthal, a television writer from New York who prefers to check bags with ticket agents. “If something goes wrong or I have a question, the self-tagging machine isn’t going to have an answer,” he said. Charlie Leocha, head of the flier-advocacy group Travelers United, predicted the new technology will shorten airport lines, but also warned it would eventually replace airline workers, frustrating fliers when storms or other disruptions hit. Airline unions generally oppose the new technology for the same reasons. Airlines say such technology isn’t intended to reduce staff, but instead free workers to handle customer problems. From 2004 to 2014, a period in which airlines added many self-service technologies like kiosks, the number of U.S. ticket agents fell about 13.5% to roughly 138,000, according to federal estimates. U.S. airline passengers increased 8.6% to 761 million over that period. The biggest of the coming changes is permanent bag tags, electronic devices that strap on to frequent fliers’ luggage and digitally display their flight information. The tags display bar codes like a traditional tag, allowing them to work with existing infrastructure. Fliers update the tags via Bluetooth from their smartphones, and the airline can also remotely update the tag if its owner gets rerouted. Officials expect similar technology to soon arrive in the U.S. “Home-printed and electronic bag tags are the low-hanging fruit for U.S. airlines,” said Stephanie Taylor, manager of passenger services at Airlines for America, the largest U.S. airline trade group. “We’re expecting multiple carriers to adopt these solutions by the end of the year.” Simpler bag-handling changes are becoming pervasive. It is now common for travelers to tag their own bags in Europe, and it is catching on in places like China, Africa and the Middle East *. * Here’s the airline industry paying off Rupert Murdoch’s WSJ to provide misinformation to Americans. I routinely travel across Europe, the Middle East and Asia on Lufthansa and other airlines, and have yet to observe self-tagging The Transportation Security Administration late last year changed its policy to make it simpler for U.S. airlines to offer self-tagging *. American Airlines Group Inc., United Continental Holdings Inc. and Alaska Air Group Inc. are adding self-tagging kiosks across the country. * The FAA, long accused of being too cozy with the airlines, is often cited as an example of "regulatory capture" - in which the airlines openly dictate to its regulators its governing rules, and arranging for beneficial regulation. During the Bush administration, the FAA actually called the airlines their “customers” and adopted a business model for evaluating its performance. Now, the FAA ironically calls the airlines "stakeholders." In the U.S., airlines still must staff bag-drop stations because security rules require employees to check identifications of passengers checking bags. Airlines for America* said it is lobbying the TSA to allow a biometric identification check, such as facial-recognition software or fingerprint readers, to remove humans from the process. The TSA said it “does not currently envision changes to bag security requirements.” * The top lobbyist for the leading U.S. airline trade association Airlines for America, Shelley Rubino, is since 2014 the girlfriend of Transportation Department chairmen. House Transportation and Infrastructure Committee Chairman Bill Shuster (R-PA)...........conflict of interest? Airlines also are moving to improve bag tracking ahead of a June 2018 deadline set by industry groups to install such technology.
-
US hands foreign companies tax advantage The Financial Times / September 25, 2014 The Obama administration has handed foreign companies an advantage over American rivals because they will not be caught by new rules governing access to offshore cash. The US this week unveiled proposals to discourage controversial mergers known as “inversions”, which American companies have used in part to gain tax-free access to earnings parked outside the US. A US Treasury official, referring to measures that make it harder to access offshore cash, told the Financial Times: “Our actions are specifically targeted to inverted companies.” They will not apply to foreign companies that acquire a US business and its cash pile. Some tax experts questioned why the two groups should be treated differently. “It seems unfair and inappropriate,” said Steve Rosenthal, senior fellow at the Tax Policy Center, a non-partisan think-tank. US companies have used inversions to establish addresses in countries with low tax rates, enabling them to access offshore cash without triggering US taxes that become payable when overseas earnings are repatriated. According to Moody’s, the rating agency, US non-financial companies hold about $950bn in overseas cash and liquid investments. As a result of the measures, a US company’s offshore cash would become cheaper to access if it were acquired by a European rival than if the US company did an inversion. Stephen Shay, a Harvard Law School professor and former Treasury lawyer, said: “It shouldn’t matter whether the new [corporate] structure comes in the form of a new foreign acquirer or an inverted transaction. The fact is there is attempted avoidance of US tax on the offshore earnings either way.” Inverting companies have been slammed by President Barack Obama for abandoning the US and eroding its tax base. On Monday, when Jack Lew, Treasury secretary, unveiled the measures, he praised “genuine” cross-border mergers done for business reasons for “encouraging foreign investment to flow into the United States”. European companies have spent $173bn so far this year on acquisitions of US businesses, according to Dealogic. The deals have been driven more by a desire for exposure to the faster-growing US market than by the attractions of offshore cash. The Treasury’s targeted steps were praised by a trade group for foreign businesses in the US, the Organization for International Investment. “They have tried to thread the needle, which was welcome,” said Nancy McLernon, its chief executive. But Mr Rosenthal, the tax expert, said: “US companies say: “If we invert, why should we be at a competitive disadvantage to a foreign multinational that acquires a US company and is not subject to these inversion rules?’” Even before Monday’s proposals, inversions did not allow US companies instant tax-free access to their accumulated overseas earnings. They first had to be moved out from under the US tax net using one of several complex techniques. The Treasury plans to eliminate three of the techniques, but the two most popular – known as “hopscotch loans” and “decontrolling” – will still be available to new foreign-based owners of US subsidiaries. In previous proposals for broader tax reform, which remain stymied by Congress, the Obama administration signalled a desire to curb tax avoidance on offshore cash by all companies, inverted or not.
-
Once upon a time, America led the world in innovation and industrial might. But as a result of government casting a blind eye to the fast declining state of American industry, a significant portion of U.S. industry is now under foreign ownership. In order for a major country like the United States to regain its position as a world leader, we must have a solid economy, which inherently requires a solid industrial foundation. Today, we no longer have that. Much has been allowed to go abroad, while the meager remnants remaining is being sold to foreign companies. - Germany's ZF has acquired TRW - Italy's Fiat owns Chrysler, Dodge and Jeep - China's Wanxiang has acquired over 20 U.S. businesses including battery maker A123, Dana’s coupled-products business, Neapco and D&R Technology. - Germany's Daimler acquired Freightliner, Western Star, Detroit Diesel and Thomas Built Buses - Sweden's Volvo acquired White, Autocar, GMC heavy truck and Mack Trucks - Germany’s Knorr-Bremse owns Bendix Commercial Vehicle Systems - Sweden’s Haldex acquired Anchorlok and the Neway suspension control valve business - Germany’s SAF acquired Neway air suspensions, and 5th wheel makers Holland and Simplex - Prestolite Electric, which includes the Leece-Neville brand, was acquired by Zhongshan, China-based Broad Ocean Motor Company and Beijing-based Ophoenix Capital. - Nexteer Automotive aka GM Global Steering Holdings LLC (formerly Delphi Steering and GM’s Saginaw Steering Division) was acquired by Chinese government-owned Pacific Century Motors - Korea's Doosan owns Bobcat - Aircraft and industrial engine maker Teledyne Continental Motors was acquired by Chinese government aircraft maker AVIC - Canada's Bombardier acquired Learjet Corporation - Mexico's KUO Group acquired Borg-Warner and Spicer transmissions - Italy's Fiat thru subsidiary CNH Global owns Case-IH and New Holland - Sweden's Volvo acquired the road construction equipment division of Ingersoll Rand - Japan's Bridgestone owns Firestone - France's Michelin owns Uniroyal and BF Goodrich - China’s Beijing West Industries acquired Delphi’s brake and suspension divisions - Netherlands-based Mittal Steel acquired (asset holder of Bethlehem Steel, LTV, Weirton Steel, Georgetown Steel and US Steel) - Mexico's Metalsa S.A. acquired 10 Dana plants that produce structural components for chassis and body structures in light and commercial vehicles - Germany's Siemens acquired Houston-based Dresser-Rand - China's Shuanghui owns Smithfield Foods - Belgium's InBev owns Anheuser-Busch - South African Breweries (SAB) acquired Miller Brewing - Germany's Merck KGaA acquired St. Louis-based Sigma-Aldrich - Switzerland's Nestle owns Gerber baby foods and Purina - Sweden's Electrolux owns the Frigidaire, Kenmore and Tappan brands - South Korea's LG owns Zenith - Netherlands-based Philips acquired Magnavox, Philco and Sylvania - China's Lenovo acquired IBM's personal computing division - Japan's Seven & I Holdings owns 7-Eleven - The UK's InterContinental Hotels Groups owns the Holiday Inn and Crowne Plaza hotel chains, and Candlewood Suites - China's Wanda Group owns the AMC cinema chain - The Venezuelan government owns Citgo - Mexico's Bimbo Group acquired Sara Lee's bakery business and the following brands: Arnold, Ball Park, Boboli, Brownberry, Cinnabon Bread, EarthGrains, Entenmann’s, Francisco, Freihofer’s, Marinela, Milton’s Bread, Mrs Bairds, Oroweat, Roman Meal, Sara Lee, Stroehmann, Sun-Maid Bread, Thomas’ and Tia Rosa. - The British-Dutch conglomerate Unilever owns Ben & Jerrys, Vaseline, Hellmann’s, Best Foods, Ponds, Good Humor and Breyers - Germany's Henkel owns Dial soap, Loctite, Orbseal and Bergquist - Germany's Bayer acquired Miles Laboratories and Cutter Laboratories (including Cutter insect repellent, Alka-Seltzer, One-A-Day, Flintstones vitamins and Bactine), and the consumer care business of Merck & Co. which included the brands Claritin (allergy), Coppertone (sun care), MiraLAX (gastrointestinals), Afrin (cold) and Dr. Scholl’s. - Bayer CropScience acquired biological company AgraQuest - Thailand’s Thai Union Frozen Products owns Chicken of the Sea and Orion Seafood International - South Korea’s Dongwon owns StarKist - The UK’s Lion Capital owns Bumble Bee Foods - Giant Carlisle (Martin's Food Markets, Ukrops), Stop & Shop and Giant-Landover supermarkets are owned by Dutch retailer Koninklijke Ahold N.V. - Food Lion and Hannaford supermarkets are owned by Belgium-based Delhaize Group - Colombia's Cementos Argos has acquired the cement and ready mix producing assets of Vulcan Materials and LaFarge - UK-based Tarmac PLC acquired the cement and ready mix producing assets of Stamford, Conn.-based Lone Star Industries (for many years the largest U.S. cement maker) - Two-wheeled electric people mover Segway has been acquired by China’s Ninebot The list, sadly, goes on and on. European companies have spent over $173 billion in 2014 on the acquisition of US businesses. Think about that.
-
Reuters / July 1, 2015 [in a rare sign of economic wisdom] The United States filed a lawsuit on Wednesday to stop Sweden's Electrolux AB, which owns the Frigidaire, Kenmore and Tappan brands, from buying General Electric Co's appliance business, the Justice Department said in a statement. It said the $3.3 billion deal would hurt competition, and consumers, by combining two of the three top makers of stoves, cooktops and ovens. Whirlpool Corp, which bought Maytag in 2006, is the third. Electrolux shares traded in the U.S. (ELUXY.PK) on the OTC Pink market fell 9.3 percent, with more than 40,000 shares exchanged. GE's share price was steady. GE, which also has the Hotpoint brand and sells almost exclusively in the United States, said in a statement that its goal remained to close the deal in 2015. "Electrolux and GE intend to vigorously defend the proposed acquisition," the company said in a statement. In its complaint, the Justice Department said that Whirlpool, GE and Electrolux had 90 percent of the U.S. market for stoves and ovens. Leslie Overton, a deputy assistant attorney general at the Justice Department's Antitrust Division, said the Electrolux deal would lead to higher prices for consumers. "This lawsuit also seeks to prevent a duopoly in the sale of these major cooking appliances to builders and other commercial purchasers," she added. But Electrolux disagreed. Its antitrust attorney Joe Sims argued that LG, Samsung and others were moving into the market to challenge the Big Three. "There is absolutely no barrier of any kind to any other manufacturer participating," he said. Sims said that the company and Justice Department had been in settlement talks. "We are rational and are therefore more than happy to come to a reasonable settlement if the DOJ (Justice Department) is. If not we're just going to have to win in court," said Sims, who said the deal could close by the end of the year. GE’s move to sell off its appliances business is part of a shift the U.S. conglomerate is making to sharpen its focus on manufacturing big-ticket industrial products such as jet engines and power turbines. To that end, GE in April announced it would exit $200 billion worth of finance assets, while it is seeking to acquire the power equipment unit of France’s Alstom. European regulators have expressed concerns that GE’s purchase of Alstom’s power unit would leave just two gas turbine companies in Europe, with GE only competing with Germany’s Siemens. GE has been working on concessions to save the planned 12.4 billion euro ($13.7 billion) purchase, which would be the biggest in the U.S. conglomerate’s history. GE on Tuesday warned that the appliances sale would not close in the second quarter because of an ongoing regulatory review, and expected an after-tax gain of roughly 5 cents to 7 cents per share should the deal close. GE is expected to earn $1.29 per share this year, according to Thomson Reuters I/B/E/S. The case at the U.S. District Court for the District of Columbia is United States v AB Electrolux and General Electric Co. It is No. 15-1039.
BigMackTrucks.com
BigMackTrucks.com is a support forum for antique, classic and modern Mack Trucks! The forum is owned and maintained by Watt's Truck Center, Inc. an independent, full service Mack dealer. The forums are not affiliated with Mack Trucks, Inc.
Our Vendors and Advertisers
Thank you for your support!