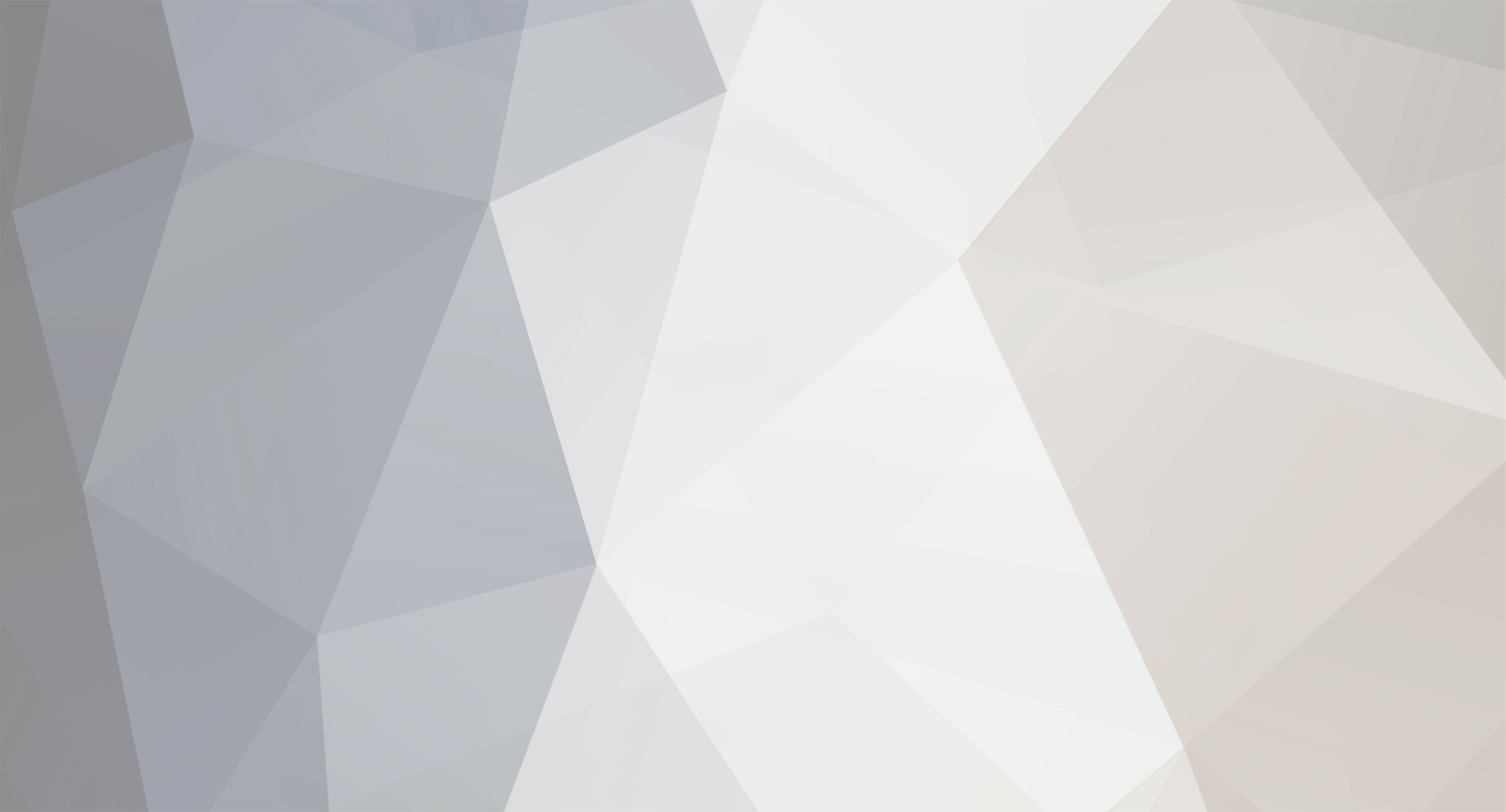
kscarbel2
Moderator-
Posts
18,539 -
Joined
-
Days Won
112
Content Type
Profiles
Forums
Gallery
Events
Blogs
BMT Wiki
Collections
Store
Everything posted by kscarbel2
-
Owner/Driver / May 21, 2015 Video - Return of International http://www.ownerdriver.com.au/events-news/1505/bts-15-return-of-international/
-
Ford Truck targets Middle East bound long-distance fleets
kscarbel2 replied to kscarbel2's topic in Trucking News
Here is a proud looking Mk 2 Trancontinental, again with the double-skinned roof (aka. roof heat shield) for Middle Eastern travel. The revised Mk 2s had the Cummins Big Cam Formula E (NTE) engines. . -
The New York Times / May 30, 2015 Inside the National Vehicle and Fuel Emissions Laboratory (http://www.epa.gov/nvfel/) here, a mammoth contraption, with steel rollers, advanced electronics and exhaust tubes, is nearing completion. The project — an enormous “truck treadmill” — is the new centerpiece of the Environmental Protection Agency’s complex. One of the largest vehicle testing centers in the world, the truck lab will play a crucial role in shaping and enforcing a major new environmental mandate by the Obama administration that could dramatically transform America’s trucking industry. This week, the EPA is expected to propose regulations to cut greenhouse gas emissions from heavy-duty trucks, requiring that their fuel economy increase up to 40 percent by 2027, compared with levels in 2010, according to people briefed on the proposal. A tractor-trailer now averages five to six miles a gallon of diesel. The new regulations would seek to raise that average to as much as nine miles a gallon. A truck’s emissions can vary greatly, depending on how much it is carrying. The hotly debated rules, which cover almost any truck larger than a standard pickup, are the latest in a stack of sweeping climate change policy measures on which President Obama hopes to build his environmental legacy. Already, his administration has proposed rules to cut emissions from power plants and has imposed significantly higher fuel efficiency standards on passenger vehicles. The truck proposals could cut millions of tons of carbon dioxide pollution while saving millions of barrels of oil. Trucks now account for a quarter of all greenhouse gas emissions from vehicles in the United States, even though they make up only 4 percent of traffic, the E.P.A. says. But the rules will also impose significant burdens on America’s trucking industry — the beating heart of the nation’s economy, hauling food, raw goods and other freight across the country. It is expected that the new rules will add $12,000 to $14,000 to the manufacturing cost of a new tractor-trailer, although E.P.A. studies estimate that cost will be recouped after 18 months by fuel savings. Environmental advocates say that without regulation, the contribution of American trucks to global warming will soar. “Trucking is set to be a bad actor if we don’t do something now,” Jason Mathers, head of the Green Freight program at the Environmental Defense Fund. But some in the trucking industry are wary. “I’ll put it this way: We told them what we can do, but they haven’t told us what they plan to do,” said Tony Greszler, vice president for government relations for Volvo Group North America, one of the largest manufacturers of big trucks. “We have concerns with how this will play out.” The E.P.A., along with the National Highway Traffic Safety Administration, began its initial phase of big truck fuel economy regulation in 2011, and those efforts have been widely seen within the industry as successful. But meeting the initial standards, like using more efficient tires, was not especially difficult by comparison. The proposed rules will ask much more of the industry. They will require more investment and innovation, like tweaking engines and transmissions, improving aerodynamics and using lighter materials. More disruptive options, like recycling engine heat to drive a secondary turbine, or moving away from diesel itself, are also under consideration. Already, some bigger fleets like that of the United Parcel Service have started outfitting some of their trucks with natural gas. To win over industry players, regulators say they have made efforts to engage companies up and down the supply chain. They have held hundreds of meetings and have tried to shape their proposal in a way that would help truck-related businesses. “Fuel is either at the top or near the top of truck operators’ costs,” said Christopher Grundler, director of the E.P.A.’s Office of Transportation and Air Quality. Reducing those costs, he added, was good for business and the environment. Mr. Obama led the cheerleading for his truck rules. In a speech last year signaling the rules, he said, “Because they haul about 70 percent of all domestic freight — 70 percent of the stuff we use, everything from flat-screen TVs to diapers to produce to you name it — every mile that we gain in fuel efficiency is worth thousands of dollars of savings every year.” John C. Wall, chief technical officer at Cummins, a leading manufacturer of truck engines, said his company had “tried to engage proactively in the development of the regulations” and had found federal officials to be open-minded about what the company thought could be achieved. Others in the industry, though, hold a different view. John Yandell Jr., president of Yandell Truckaway in Pleasant Hill, Calif., said that fuel is the second-highest cost for his family business and that he would love to get better mileage on his fleet, which operates short-haul regional routes. But, he said, he is skeptical that can be achieved in the near future in a way that is affordable for him, if at all. “Twenty years ago, my trucks were getting five miles per gallon; today they are getting around 6.2 to 6.4,” he said, but getting up to nine or 10 seemed like a pipe dream. “Talk is cheap, but I don’t see how they get there.” Getting there, however, is a priority for Mr. Obama. The administration also hopes that ambitious government targets can help drive the innovation needed to achieve them. After the 54.5 m.p.g. requirement for cars and light trucks was announced in 2009, a wave of new research and development happened in Detroit, as automakers rushed to develop new hybrid, electric and super-efficient gasoline engines. The new truck rules are intended to spur the same rush to innovation among the companies that build the 10-ton tractor-trailers that haul things as varied as timber, steel and frozen fish. But as with any new environmental rules, the details are complicated and will take time to sort out. The public will be asked to comment on the proposed rules before the final version is put in place sometime next year. Back at the testing lab, the truck treadmill was put through its paces. A semi truck was fastened down with thick chains secured to even thicker steel anchors. A driver started the engine, which roared as the truck sat atop enormous metal rollers that allowed the wheels to spin in place. Orange tubes, intended to collect the exhaust fumes when the formal testing begins, hung from the ceiling. “This was a hole in the ground before Christmas,” said David Haugen, director of the E.P.A. lab’s testing and advanced technology division. “Now we’re ready to make history.”
-
Australasian Transport News / June 1, 2015 New Zealand trucking corporation Mainfreight (http://www.mainfreight.com/global/en/global-home.aspx) has reported a record NZ$2.05 billion ($A1.9 billion) in revenues across its global operations. That fed into an earnings before interest, tax, dividends, and amortisation (underlying earnings) result of NZ$162.2 million (A$151 million). At home, the company saw increases in revenues and profits across both its transport and logistics divisions. Group managing director Don Braid says those gains were similar to the achievements built in the previous financial year. "Our New Zealand transport operations gained a number of new customers, and increased the number of consignments transported through our network by 150,000," his report to shareholders states. "This builds on similar levels of growth in the year prior." Across the Tasman, a shaky economy and competitive market subdued Mainfreight’s ambitions in Australia for the financial year that ended on March 31. Revenues increased by seven per cent to A$490.65 million, while underlying earnings improved 5.8 per cent to A$37.2 4 million. "Whilst these improvements may seem satisfactory, when compared to New Zealand’s level of growth and the relative size of the Australian market, we would have expected more," the commentary explains. While profitable, Mainfreight’s US operations also filed below-expectation results. The smaller European business achieved strong growth off a relatively low base. Total sales for the region rose by 3.6 per cent over the year to March 31, with underlying earnings up 33.5 per cent to €11.91 million (A$17 million). "Whilst the European economy remains turbulent, our own improved performance is providing confidence for the future." In Asia, Mainfreight had underlying earnings of US$4.99 million (A$6.5 million), up 41.6 per cent from what was also a low base. Braid says the forward outlook also remains positive. "A number of large multinationals can now be counted as loyal customers, and we are underway with attracting more," he says. "Their relative logistics spend is considerably larger than we have experienced before in the smaller markets of New Zealand and Australia [and] the potential [they] bring to our global business is exciting." .
-
Owner-Driver / May 29, 2015 A growing number of the trucking industry’s customers are trying to force operators to accept 120-day payment terms, the managing director of FBT Transwest says. Cameron Dunn told a recent road safety summit that 120-day terms are now a common feature in contracts put out to tender. This comes despite efforts by the Road Safety Remuneration Tribunal (RSRT) to improve the situation. It last year mandated 30-day payments for sub-contractors and owner-drivers. "It is more common now that contracts will come out that’ll push for 120 days," Dunn, whose business is involved in dangerous goods, says. "I’ve mentioned it to some people and they are aghast. Well that’s actually quite factual and more and more, as day goes by, end companies are pushing us out." Dunn says companies are employing logistics experts during the contract tendering process and ordering them to reduce transport costs — a move that has led Dunn to refuse work to avoid agreeing to harsh terms and conditions. "I won’t be pushed to not do the right thing," he says. Dunn’s comments caught the attention of federal Labor senator Glenn Sterle, who attended the summit which was organised by the Transport Workers Union (TWU). Sterle raised concerns about payment terms and says he knows of a large food manufacturer attempting to institute 90-day payments. "This is a monster and all this will do is crush competition and it will squeeze the living daylights out of a lot of operators," he says. While small-time trucking operators with limited cashflow stand to suffer from lengthy payment terms, Dunn says large transport firms are agreeing to 120 days. "Now why do you think the larger companies are saying yes? They’re saying yes because they’ve got the ability to be able to cover that cashflow with their other contracts," he says. "They have some of their contracts at 120 [days], some at 14, some at seven. But they also then push out payments to their suppliers, so it’s ever revolving. They’ll push the tyre supplier out, possibly, to 120 days. "It’s happening. It’s more and more. It’s certainly out there and its scary, it’s very, very scary." Dunn also touched on the addition of key performance indicators (KPIs) in contracts and the effect they are having on freight rates. He says contracts generally include KPIs relating to the environment, safety and tonnage and that if a trucking company does not meet them then the customer has the ability to reduce payments. "There are some contracts when you actually read them, you can actually start off carting for $1 a tonne and and up after two years at 80 cents because you failed to meet the different KPIs. And they are out there. That’s no bullshit, it’s happening." Dunn was a feature participant at the road safety summit, which was held in conjunction with the TWU’s National Council earlier this month. The day-long event discussed road transport safety and included representatives from Victoria Police, the RSRT, the Roads and Maritime Services (RMS) and Toll.
-
Peterbilt’s Model 579 EPIQ opening doors with large fleets
kscarbel2 posted a topic in Trucking News
Truck News / May 29, 2015 Peterbilt is feeling pretty good about its position in the marketplace – especially among large fleets – thanks to the success of its Model 579. And now with the addition of the EPIQ package, the company says it has never been better positioned to sell to large fleets in the US and Canada. Three quarters of the trucks Peterbilt builds are now aerodynamic models. “It has opened a whole new customer base for us,” Robert Woodall, assistant general manager, sales and marketing with Peterbilt, said during a press briefing at the company’s Denton truck plant. Woodall said the EPIQ package improves fuel economy over a base Model 579 by 4% and contends it’s the most advanced, fuel-efficient truck on the road. It’s certainly the most fuel-efficient truck ever produced by Peterbilt. Woodall said the EPIQ package is just now entering production and already fleets are making the transition, despite an upcharge he said is quickly recovered through fuel savings. “Most of the interest in EPIQ is going to be the big fleet guys, those guys who are all about fuel economy,” Woodall said. “That’s where EPIQ is playing out.” The EPIQ package consists of: a more complete aerodynamic fairing package; the Paccar MX-13 engine integrated with the Fuller Advantage Series automated manual transmission; a single horizontal exhaust; the SmarTire tire pressure monitoring system; low rolling resistance tires; and optimized software. New additions to the package include GPS-based predictive cruise technology to ensure engine and transmission are being optimally operated and neutral coast, which disengages the transmission while travelling downhill to save fuel. Also new is a Driver Performance Assistant, which coaches drivers on fuel-efficient driving techniques. The 579 EPIQ can also be ordered with the Cummins-Eaton SmartAdvantage. However, both the SmartAdvantage and the Paccar/Eaton pairing (dubbed APEX) are limited to a GCWR of 80,000 lbs, meaning this package won’t fit all Canadian needs. For the Canadian customers, a 16-speed Eaton UltraShift Plus LSE will be available, rated at up to 110,000 lbs, but they won’t be calling that an EPIQ, even when all the other aspects of the package are spec’d. It might be EPIQ, but it’ll still be a fuel-efficient option for fleets seeking the versatility to haul heavier Canadian payloads. Fleets running north-south with US-legal loads on the other hand, may be well served by the true EPIQ, straight out of the box. The Model 579 itself is the result of an exhaustive design process. Andrew Weiblen, director of product planning with Peterbilt, said the development process began by reaching out to customers to find out what they wanted in a truck. They visited truck stops with a mobile, adjustable cab and surveyed drivers on the ideal configuration. Most preferred a 2.1-metre cab width, which was adopted for the 579. “A 2.1-metre cab is the perfect width to give drivers ample space, without making them feel like they’re driving an RV down the road,” Weiblen said. Determining the market needs was the first in a five-step design process. Next came: ideation; concept; validation; and final design. As part of the ideation process, designers studied how customers use the truck. When they noted some were placing their cell phones in the cupholder, a special phone-sized storage slot was developed. The concept stage included the building of prototypes. Clay models were built in 20%, 40% and full-sized scale. Next, as part of the validation process, full-sized functioning prototypes were built and rollover and frontal impact testing was conducted. Peterbilt wanted to ensure the truck would last a million miles or more. The 579 is the foundation from which all other models – including vocational and severe-service trucks – are built, so it had to be constructed tougher than required for the on-highway linehaul applications it was intended for. Finally, in 2012, came production. The arrival of the 579 also necessitated a redesign of the production plant. About 55,000 sq.-ft. of floor space had to be reconfigured to accommodate the new production flow. A new robotic chassis paint system was installed as well as a non-contact laser alignment system, which Peterbilt said is the only one of its kind among truck manufacturers. The company is particularly proud of this piece of equipment. It ensures trucks are delivered to dealers and customers in alignment and reduces the need for fleets to align new trucks when they’ve arrived. The Model 579 drew inspiration from the Peterbilt/Cummins SuperTruck project. The chassis fairings and predictive cruise technology are a couple of the 579’s features that were first developed as part of the SuperTruck. Peterbilt 579 EPIQ Road Test: http://www.trucknews.com/test-drive/driving-peterbilt-model-579-epiq-2/ -
Commercial Carrier Journal (CCJ) / May 31, 2015 In April 2011, on-highway diesel broke the $4-per-gallon mark for the first time since the recession, double the low of $2-per-gallon just two years earlier. Fleet managers, still reeling from the effects of the economic downturn, were scrambling for answers. By 2012, there was no bigger buzzword in trucking than natural gas. Whether it was compressed natural gas or liquefied natural gas, OEMs and engine makers were ramping up for what was expected to be a game-changer for trucking efficiency. By that time, diesel had stabilized at about $4 per gallon, and no one thought it would drop soon. A handful of carriers were quick to react, converting some or most of their fleet equipment to more expensive natural gas-powered tractors to take advantage of the fuel’s comparatively low cost. Many other carriers followed suit, dipping their toes in the water and getting positive results, just as the fueling infrastructure was unfolding. Other carriers were pressured into natural gas adoption by customers with aggressive environmental sustainability initiatives such as Owens Corning and Procter & Gamble. By December 2013, Class 8 natural gas truck sales had risen from nowhere to account for 3.2 percent of the total U.S. and Canadian Class 8 truck market, according to FTR, an industry analyst firm that tracks equipment and freight trends. Some were calling for the natural gas truck market to skyrocket at that time, with Thomas O’Brien, TravelCenters of America president and chief executive officer, suggesting that one in four heavy trucks on the road in 2020 would be powered by natural gas. The diesel dip Over the next year and a half, diesel plummeted $1.25 per gallon, hitting a low of $2.75 in April of this year, according to the U.S. Energy Information Administration’s weekly retail price index. Lower diesel costs, coupled with strides made by OEMs and engine makers to improve the fuel economy of traditional diesel-powered trucks and engines, have combined to stymie the natural gas market. “We are seeing a leveling off in activity,” said Eric Starks, FTR president. “Demand for natural gas equipment is not growing, nor is it dropping. The trucking industry has been hoping for growth in this sector, and it clearly has stalled out and is not expected to make significant strides until the price of diesel fuel rises again.” Given the inherent volatility in diesel prices, it is unlikely the low-cost fuel will remain at current levels for a long period of time. T. Boone Pickens, speaking at ACT Expo in Dallas last month, said as U.S. producers throttle back production, he expects oil prices to recover to upwards of $70 per barrel by the end of this year and approach $90 per barrel by the end of 2016. “Since 1980, I’ve seen six of these collapses of half the price of oil, and I promise you it will be back up again,” he said, adding that U.S. producers, who at their peak had more than 1,600 rigs drilling for oil, are responsible for the decline in oil prices. But rig counts have been cut by more than half as prices fell. “We’re the one who oversupplied the market and caused it to drop $50 per barrel,” said Pickens, who then compared the volatility of natural gas and diesel markets. “If natural gas doubled to $6, it would increase your fuel cost 37 cents per gallon,” he said. “$100 oil in parity with natural gas is $16, and I’ve never seen that. I’ve said that in my lifetime, I don’t think I’ll ever see $10 natural gas again, but I do think we may see $8. But I think you’re looking at $100-plus oil forever.” Navigating today’s challenges The natural gas truck market has faced other headwinds during the last year and a half in addition to lower diesel prices. The added costs of natural gas-powered vs. diesel-powered tractors – between $40,000 and $60,000 depending on tank configuration – have been slow to come down. An uncertain future in the used truck market has many fleets sitting on the fence before investing in natural gas equipment. And while many regional and dedicated carriers have had great success with natural gas operations, the fueling infrastructure still is being built out, and many over-the-road carriers remain hesitant to test the waters. The natural gas truck market took another hit last month when the journal Environmental Science & Technology published the results of a study coauthored by the Environmental Defense Fund that claims methane emissions from the natural gas manufacturing process and supply chain could lead to greater global warming than carbon dioxide emissions from diesel-powered trucks. According to EDF, methane – the main component of natural gas – has 84 times the warming power of carbon dioxide over a 20-year timeframe. “Natural gas trucks have the potential to reduce overall climate impacts compared to diesel, but only if we clean up the highly potent greenhouse gas emissions from the systems that produce and deliver the fuel,” said Jonathan Camuzeaux, EDF senior economy analyst. “Otherwise the net warming effect is actually a negative one for 50 to 90 years after the fuel is burned.” Natural Gas Vehicles for America, a developer for market acceptance of natural gas vehicles, was quick to respond. “This study clearly demonstrates that there is a role for natural gas in addressing climate change,” said Matthew Godlewski, president of NGVAmerica. “We welcome all credible insight into paths for improving emissions, yet it’s confusing that the Environmental Defense Fund has chosen to conduct and release another study, outside of the cooperative work already underway.”
-
Heavy Duty Trucking / May 28, 2015 Two decades ago, Peterbilt was primarily known for its classic truck designs that appealed to owner-operators and small fleets. But as it showed reporters during its Technology Showcase Thursday at its plant in Denton, Texas, it has reinvented itself as a company on top of the latest technology and fuel economy. About 10 years ago, the Model 386 was Peterbilt's first ground up design of an aero product, said Robert Woodall, assistant GM, sales and marketing. "In 2013 we introduced the Model 579, helping redefine our company," he said. Of course, the company still has a tried and true offering for customers who prefer that traditional look, with the Model 389. With the Model 579 Epiq, Peterbilt took the truck to an even greater level of fuel efficiency, Woodall said, noting later that it "has opened a whole new customer for us. We're the most competitive we've ever been with the big on-highway fleet business." Large fleets already buying the Epiq include Walmart, Love's, TMC, Freymiller and Celadon. On top of that, he said, "we've got a new 58-inch [sleeper] box coming out in November for regional hauls, so that's going to open up another group of customers." Many of the technologies used on that truck came through the Cummins-Peterbilt SuperTruck project, a joint effort with the EPA to demonstrate freight efficiency possibilities. Some of the aerodynamic fairings were adapted from the SuperTruck and actually tweaked to offer the same performance with easier maintainability, explained Chief Engineer Scott Newhouse. New Predictive Cruise technology, which will be available on the Model 579 and 567 this summer, also made its debut on the SuperTruck. It uses GPS data to ensure the engine and transmission are operating in the most efficient mode, working in tandem with neutral coast technology that allows trucks to coast downhills at idle. Under the hood, he said, Peterbilt's work on integrating the engine and transmission on the Super Truck taught them things they were able to apply to the new Apex package. "Also not directly related, we learned things such as driver impact, which really led into a lot of the Driver Performance Assistant technology," he said. "You have to be able to manage the impact the driver may have on fuel efficiency." Woodall noted that just as important as new high-tech products is the growth of high-tech systems and tools to support those products once vehicles are in operation. New vehicle technology such as the 579 Epiq, the Apex powertrain and the Driver Performance Assistant are complemented by back-end and diagnostic tools such as in-cab diagnostics that alerts drivers whether fault codes need immediate attention or not, as well as SmartLinq remote diagnostics. The technology extends to the plant itself, which has higher levels of automation and robotics than ever before, according to Ron Augustyn, manager of the Denton plant. The plant's undergoing an expansion that will add a new high-tech parts storage and retrieval system in addition to more docks. "The launch of the 579 and 567 was the most significant product launch in our history," he said, and the plant underwent a major transformation in order to produce the trucks, completely rearranging 55,000 square feet of floor space. Part of that transformation is an automated cab build station, a critical element in the overall build quality of the product, he said. Another significant investment was a non-contacting laser alignment system. Augustyn said this is the first truck plant in North America to use this state of the art technology, which uses a drive through laser scanning system that integrates steering wheel alignment as well. The system, he said, has improved accuracy 10-fold and efficiency by 40%. "Total truck alignment has been a challenge for the entire industry," he said, noting the accuracy of this system can provide improved fuel efficiency and reduced tire wear for customers. And looking to the future, Peterbilt is continuing to work on development of technologies that could move to autonomous vehicles. It has worked with Walmart to design a working autonomous truck that it will show to reporters Friday. "We're always looking ahead to new opportunities," said Newhouse. Autonomous technologies such as lane keeping, GPS navigation and platooning "are all technologies we continue to advance." Looking even further out, Newhouse highlighted Peterbilt's entry in the LA Auto Show design challenge last year, taking on the theme, "Sensing the Future" to look at how vehicles and people will interact in 2029. Peterbilt's concept entry, called Symbiotux, featured the concept of platooning. The interior would use nanotechnology and biomonitoring to adapt the environment to the driver's needs. For instance, a smart seat could sense a tight muscle in a driver's leg or back and adjust the ergonomics of the seat to compensate. Supporting photographs and video: http://www.truckinginfo.com/news/story/2015/05/peterbilt-highlights-technology-transformation.aspx
-
Heavy Duty Trucking / May 31, 2015 Peterbilt showed off its take on autonomous vehicle technologies to reporters Friday during a Technology Showcase at the Texas Motor Speedway. Bill Kahn, manager of advanced concepts at Peterbilt, doesn't really like to call the two demonstration vehicles "autonomous," although they would qualify as a Level 3 autonomous vehicle under National Highway Traffic Safety Administration classifications. He characterizes the technology more as the "cruise control of the future" and a "stepping stone to autonomous vehicles." Peterbilt engineers have dubbed it "advanced driver assist systems." A bumper-mounted radar system, on one of the trucks, and a lidar camera on the other, are used to determine the distance from the truck to the vehicle or obstacle ahead of it. The lidar has the added advantage of not only being able to determine an obstacle ahead, but also a wider field of "view" and the ability to provide some data on the size and shape of whatever's there. For on-highway situations, these and a windshield-mounted camera provide data to keep the truck in the lane as the truck steers itself. Kahn said this lanekeeping technology is capable of taking 85% of the active steering out of the driver's hands, leaving him much more refreshed. Kahn characterized lanekeeping as a form of advanced cruise control, and noted that just as any cruise control, you wouldn't use it in bad weather or congested traffic. The radar/lidar is also used for adaptive cruise, which can keep the truck the right distance from the vehicle in front of it and bring it to a complete stop if necessary. In addition, the concept trucks featured a GPS-based autopilot system that would allow the truck to operate autonomously in urban environments – but only if the route was preprogrammed. The GPS system is accurate up to 5 centimeters. One truck can drive the route (with a human driver) and "map" it, then transfer that data to other trucks in the fleet. The other trucks then follow that preprogrammed course; driver intervention would be needed in some situations. In the case of platooning, that information transfer between the front truck and the ones behind would happen in real time. So far, testing of the GPS system has all been done on non-public courses set up to mimic city streets. The trucks have Dedicated Short Range Communications, or DSRC, radio antennas, a vehicle-to-vehicle communication system. DRSC is similar to Wi-Fi, but is not likely to be vulnerable to interference, and is an important part of the federal government's plans for "connected vehicles." Supporting photographs: http://www.truckinginfo.com/news/story/2015/05/peterbilt-shows-off-cruise-control-of-the-future.aspx
-
Platooning is closer than you think – just like the trucks
kscarbel2 posted a topic in Trucking News
Fleet Owner / May 29, 2015 For many fleet managers, platooning seems like a dream come true - two trucks traveling in line, very close to each other, saving fuel without sacrificing safety. Platooning saves fuel because two tractor-trailers traveling closely, usually 40 to 50 feet apart, set up air flows that help to 'push' both trucks forward. In Peloton Technology, Inc. tests with CR England, platooning saved 7% at 65mph – 10% for the rear truck and 4.5% for the lead truck. So far, Peloton has logged 14,000 miles in all of its tests. At the heart of platooning is a wireless electronic communications system, also connected to the internet, that tells the second truck when the first truck driver has braked. The second truck brakes almost instantaneously without driver intervention. In essence, both trucks brake at the same time. Fleet Owner talked to Josh Switkes, Founder and CEO of Peloton Technology about the technology aspects of platooning and Randy Mullett, Vice President for Government Relations and Public Affairs at Con-way and a board member of ITS America about the policy and regulatory aspects needed to get platooning on the road. 1. How does the braking system work? Switkes: With vehicle-to-vehicle communications, the rear truck knows exactly what the front truck is doing. We know how much engine torque it's applying, we know how fast it's going, and most importantly, we know when and how much the brakes are applied. We know all this almost instantly, about ten milliseconds between when the front truck's brakes are applied and when the rear trucks knows about it. 2. Is the second driver's view of the road impaired? Switkes: Your view of your lane ahead is blocked, but your view outside of that lane is fine off to the sides. We also help the second driver know what's coming up on the road through a video link. We take a camera that's looking forward from the front truck, and send that video feed to the rear truck through the wireless communication, so the rear driver sees the road ahead. You use it like another mirror. 3. Does the second driver get bored looking at the rear of the lead truck? Switkes: Unlike some platooning tests in Europe, like the Sartre project [in Europe], we use manual steering so the second driver has complete control. He or she is engaged all the time. We're not replacing the driver. We’re taking their skills and adding an extremely fast braking reaction. 4. How do you match up trucks and decide the following distance? Switkes: This is the job of the cloud-based Network Operation Center. Trucks are connected to the internet. We don't let the drivers choose [their position], and the reason we don't let them choose is because it's how we increase safety. We order the trucks based on their braking ability. Whichever truck can stop shorter is always going to be in the back of the two-truck platoon. We only platoon when it's safe depending upon the type of road, weather and traffic conditions. 5. How do trucks find each other? Switkes: Many fleets have multiple trucks leaving a distribution center or hub at the same time or very close to the same time. Not every fleet has these trucks together, but we've found a good number of fleets that do. We plan to deploy first with these fleets. It's important to realize that trucks do not have to be going to the same destination. The can platoon for a while then split in different directions. There's still a savings in doing that. 6. How much does it cost to outfit a truck? Switkes: We're not talking about that publicly. Most fleets tell us they expect payback in about seven months. We don't do anything to the trailer, only the tractor. We charge fleets a per-mile fee while their trucks are platooning and saving fuel. 7. What's it like to ride in a truck that's part of a platoon? Mullett: I rode in platoon vehicles last summer at the ITS World Conference in Detroit. Peloton had a demonstration, and we drove around interstates in Detroit. I'm confident that the technical issues have been surmounted, and that it can be done in a safe way. 8. What are some of the non-technical or policy and regulatory issues that still need to be addressed? Mullett: You might think that technology is the problem, but it’s the policy issues that need to be worked out. For instance, we need harmony on following distance, because there are minimum following distances in some states. Also, how do we keep cars from jumping in and out of the space between trucks? There also needs to be commonality about things like where to place the video screens so you don't confuse drivers using different vehicles. There are also mundane issues like what happens when one driver in a platoon needs to go to the bathroom. 9. What about driver acceptance? Mullett: It took some drivers a while to get used to new technology like automatic transmissions. There will be a little bit of an acceptance curve on platooning. 10. What non-technical issues concern fleet managers? Mullett: If the rear truck has better fuel economy, and the trucks are from different fleets, how do you to share the fuel economy in a fair way? 11. Will car drivers call police if they see trucks following so closely? Mullett: That's another issue that needs to be worked out. Trucks need some kind of signage telling other drivers that they're platooning and driving safely. 12. What's the overall biggest challenge to platooning? Mullett: I think that our biggest challenges are having our policymakers and the public be able to keep up with and accept the technology without killing the idea. I think we're about a year away from a serious pilot program. It may take another couple of years before we get enough density to see a large difference in [national] fuel savings. -
Ford Truck targets Middle East bound long-distance fleets
kscarbel2 replied to kscarbel2's topic in Trucking News
Thank you so much for sharing that link with everyone. Most Americans have no idea that Pacific Intermountain Express (PIE) operated in Europe and ran to the Middle East. Their DAF 2800s were quite a truck back then. Always great to see a Leyland Marathon. And this all falls back to the days when Mack F-models rubbed shoulders with MAN, Saviem, Scania and other European brands on the way to Western Asia. Most Americans can't imagine an F-model of all things in Europe much less Asia. (http://www.bigmacktrucks.com/index.php?/topic/30466-when-mack-roamed-europe-the-middle-east-africa-and-western-asia/) -
I lean towards Donaldson and Fleetguard nowadays, who are dedicated to the design and manufacture of high quality filters sold under their own brand. Many can benefit from buying the premium spec fuel and oil filters which have the more advanced filtering media (filters are so much cheaper than overhauls). For example, using the advanced Donaldson “Blue” filter range (http://www.donaldsonfilters.com/pages/products/extended_service.aspx). And Fleetguard’s “StrataPore” filtering media remains cutting edge (https://www.cumminsfiltration.com/html/en/products/lube/filtration.html). FYI, here’s a quick list of the filter manufacturers in the U.S. market. Affinia Group (Dana sold its filter business to Cypress Group subsidiary Affinia in 2004) Wix Napa Alliance (Freightliner aftermarket brand) Champion Laboratories (As a UCI Int’l subsidiary, Champion was acquired by New Zealand’s Rank Group in 2010 when it bought UCI) AC Delco Bosch Ford K&N Luberfiner Mobil 1 Mopar Napa STP Valvoline Clarcor (formerly J.L. Clark Manufacturing Co.) Baldwin (since 1981) Caterpillar-branded filters (since 2004) Hastings (since 1995) Cummins Filtration (always a premium product) Fleetguard Donaldson Company Inc. (Founded in 1915, Donaldson remains a profitable American company in today’s unforgiving global arena that delivers with superior products) Donaldson UCI-Fram (Honeywell International sold Fram to New Zealand’s Rank Group in 2011, who unsuccessfully tried to dump it in 2014) Fram Napa Mann+Hummel Mann+Hummel Purolator (ArvinMeritor sold Purolator to Bosch and Mann+Hummel in 2006. M+H bought out Bosch’s stake in 2013).
-
Ford Trucks Press Release / May 29, 1976 At Ford Motor Company, we’re serious about trucking. And proof of that is the new “Long Haul Cab” configuration now available for our popular Transcontinental heavy truck range. Targeted at Western European and UK operators with long-distance routes to the Middle East, Africa and Western Asia, the 32-item post-production ‘Long Haul Cab” SVO option includes four packages: Climatic Package – To combat the extreme temperatures encountered in hauling to/from the Middle East. Roof-mounted severe-service air conditioner Double-skinned roof to reduce the effects of the desert sun Tinted impact-resistant exterior sun visor Additional cab insulation Tinted and laminated windshield Tinted door windows Deleted side and rear bunk windows Long Haul Package – Features required to meet the rigors of long distance haulage. Two burner gas stove (gas bottle located behind passenger seat) Wash basin 22-liter (0.78 cu.ft.) thermostatically-controlled refrigerator Cloths Locker (wardrobe) Tinted and laminated windshield Tinted door windows Heavy-duty suspension Additional Storage Package – Enables drivers to operate for long periods fully self-contained. Under-bunk (lower) storage area Folding table with additional food storage container 10 liter (2.64 gallon) in-cab drinking water reservoir Three 20-liter (15.85 gallon total) drinking water containers in chassis-mounted and lockable carrier Door pocket racks Tape cassette holder Vacuum flask holder Security Package – Provides protection and warning against theft, vandalism and accidental damage. Lockable fuel tank cap, cab tilt mechanism and fifth wheel coupling release Fire extinguisher Front headlamp and rear tail lamp guards Horn-actuating intruder door opening warning system Interior door locks The passenger side dashboard lifts up to access the cab’s two burner gas stove and wash basin. A 22-litre refrigerator, centrally located between the seats with vibration-insulating floor mounts, can be operated engine-off for 12 hours. A generously sized fold-away table is centrally located between the driver and passenger for ease of use. A 10 liter (2.64 gallon) drinking water reservoir supplying the in-cab wash basin is supplemented by three plastic 20-liter drinking water containers carried in an external and lockable rack. An example of the Transcontinental’s superb chassis packaging, an oversize toolbox is efficiently mounted underneath the water container rack, this all behind the battery box on the left frame rail. Like all Transcontinental models, a two-bed sleeping arrangement is an available option. The sleeping area side and rear windows can be substituted with blanking panels that featured internal shelving, adding greatly to the Transcontinental’s in-cab storage space. Up to ten padlocks are provided for the battery box cover, external drinking water container rack, toolbox door and rear-stowed wheel chocks. A fuel efficient 14-litre Cummins NTC355 rated at 340 horsepower is standard equipment, paired with a 13-speed Eaton-Fuller transmission and Rockwell drive axle(s), and a 600 litre fuel tank suitable for long-distance transport. Ford Transcontinental – Maximum gross weight articulated and rigid trucks from the people that mean business in big trucks. Compare the Transcontinental with any other long-distance truck on the road today and you’ll quickly see why truck operators across Europe are switching to Ford. .
-
http://www.bigmacktrucks.com/index.php?/topic/32060-the-ford-w-1000-gas-turbine/
-
Triad Business Journal / May 28, 2015 Volvo Group on Thursday announced the grand opening of a facility in Advance, North Carolina for a subsidiary that recycles heavy-duty truck parts. The company held a ribbon-cutting ceremony today for the Dex Heavy Duty Parts facility after investing $2.6 million into the renovation of a 210,000 sq. ft. building at the site of a former textile storage facility. The facility is located on 38 acres at 2016 Cornatzer Road. The Winston-Salem Journal reported that Dex moved its headquarters to Advance from Virginia in August. "Volvo Group is pleased to open another facility in North Carolina," said Dennis Slagle, president of Volvo Group Trucks Sales North America. "Dex Heavy Duty Parts takes old trucks and recycles them – refurbishing some parts for resale and recycling others for reuse – which is not only a natural extension of our business, but perfectly exemplifies our core value of care for the environment." A Volvo Group subsidiary, Dex is a supplier of recycled, renovated and surplus medium- and heavy-duty truck parts that offers recycled and renovated parts to second- and third-generation truck owners. According to Darin Redmon, director of operations for Dex Heavy Duty Parts, “Since 2012, Dex has recycled more than three million pounds of material.” The company's facility adds to Volvo's presence in the Triad. Greensboro is home to the headquarters of Volvo Trucks North America, a maker of heavy trucks and engines, and its sister company, Mack Trucks. Both are subsidiaries of Sweden-based Volvo Group. Gov. Pat McCrory said: "It's always great to see companies move to North Carolina and we appreciate Dex Heavy Duty Parts’ commitment to our state and environment. Employers know North Carolina is a great place to invest because of our friendly business climate, infrastructure and talented workforce.”
-
Commercial Carrier Journal (CCJ) / May 28, 2015 Citing it as a way to improve aerodynamics and gain more flexibility in creating new technologies, Daimler Trucks North America, parent company of Freightliner and Western Star, has petitioned the U.S. DOT’s National Highway Traffic Safety Administration asking it to allow camera-monitor systems as a compliance alternative to rearview mirrors. Federal regulations currently require heavy-duty trucks to be equipped with rearview mirrors from the manufacturer. But, Daimler argues in its petition, modern camera-based systems can do the job just as good as rearview mirrors if not better, and it’ll allow truck makers to avoid the aerodynamic drag that comes with two awkwardly shaped chunks of metal and mirror hanging on each side of the tractor. Camera systems expand truck operators’ fields of view and give them better viewing angles of what’s happening around their vehicle, Daimler says. From its petition: “Camera systems can eliminate blind spots and furnish an unimpeded view in all directions, encompassing multiple lanes.” And the aerodynamic benefits, while improving fuel economy, also lower greenhouse gas emissions associated with fuel consumption. In the building of the Freightliner SuperTruck concept vehicle unveiled this year, Daimler said it hoped to not have to use rearview mirrors in the finished product. But to make the truck road legal — prior to NHTSA’s review of its exemption petition — Freightliner had to equip the rig with a small mirror on each side. However, as you can see in the photos below, they’re not really needed, as Freightliner also equipped the SuperTruck with the camera-monitoring system that could make rearview mirrors obsolete. Here are photos of both the SuperTruck’s rearview mirror setup and the one used in the Freightliner Inspiration, the company’s recently revealed semi-autonomous truck: Supporting photographs: http://www.ccjdigital.com/daimler-trucks-asks-dot-to-allow-it-to-use-camera-systems-in-lieu-of-rearview-mirrors-with-photos/
-
We had a lot of fun discussing Ford's highly advanced Big Red. http://www.bigmacktrucks.com/index.php?/topic/32038-fords-futuristic-gas-turbine-big-red/ One gentleman appeared claiming to own it, but................ Last year, one gentleman posted on the net: i know where it is.....and its alive and doin fine in my dads garage....my brother owns it....it is now fully restored with the original gas turbine engine.....tbr24333@yahoo.com And another gentleman posted: We were researching that vehicle in December. AACA Hornets Nest Region member and local editor Jerry Clemmons talked directly with Lee Holman. Lee siad tht after Ford was finished testing, it was being towed back to Detroit. Its tow rig broke down, so Holman Moody towed it back to Charlotte as a favor to Ford. Henry Ford II told HM to keep everthing since the Ford contract was over. HM retained the cab (cab and chassis less engine) for some time, but the trailers were sold to the "Miss Bardahl" racing team to haul boats. More recently a 1957 Thunderbird collector in North Carolina bought the cab. The turbine powerplant was an on-off deal, and parts were unavailable. The new owner installed an industrial turbine, bu it made the truck too heavy, and he couldn't get it tagged. Slick Owens, who worked at Holman Moody for 15 years, said the "cab had bath, sink and all kinds of stuff ... had maps of U.S. that could move like a movie, cab was as high as trailer and inside was smooth like a room." The picture below is visual proof that Bergdahl operated at least one of the Big Red Fruehauf trailers. A true piece of America's trucking history, it's regrettable that if the tractor is still actually in existence, it remains hidden away. It belongs in the Henry Ford museum. Or, Ford would impress if they rebuilt the truck to look as it originally did new, but installed a cutting edge turbine drivetrain based on the latest technologies. That is, like the Wal-Mart WAVE (http://www.bigmacktrucks.com/index.php?/topic/35200-walmart-debuts-futuristic-truck-at-mats/?hl=wave), create a modern hybrid drivetrain utilizing a micro-turbine. An updated Big Red would, like the 2017 Ford GT, would send the message that Ford continues to be at the cutting edge of vehicle innovation. .
-
Australasian Transport News / May 27, 2015 Fresh from a new cartage contract with global commodities giant Glencore, Lowes Petroleum Service (http://www.lowespetrol.com.au/) has formed a distribution joint venture with BP. The deal will see Lowes manage BP’s regional wholesale distribution network at particular regional locations in Queensland, New South Wales and Victoria. To be operational in September, subject to regulatory approval, Lowes expects the deal to provide "guaranteed supply, quality products, greater network coverage, a wider array of services and more depth of product choice incorporating BP card and fuels, and the BP and Castrol range of lubricants". Lowes general manager Bernie Morris tells ATN it will be business as usual for existing customers while his company gains a deeper understanding of what the agreement will mean operationally. At this stage, it was too early to determine how it will affect the Lowes’ fleet of Volvos, Macks, Kenworths and Ivecos across a range of configurations, Morris says. "We are taking time out over the next four weeks to visit each site and see what happens and how it happens," he says. "Our immediate attitude is that everything stays the same. "We will continue to service our customer base and make sure they are continually looked after in the same style as they have been in the past. "Our attitude as we move forward is to provide a more effective and more efficient delivery structure to that market place." Meanwhile, Lowes has tendered successfully for the carting of more than 100 million litres of product annually for Glencore from Newcastle into Glencore-owned coal mines in the Hunter Valley. "This is a three year contract and sees our company continue to grow and expand throughout the fuels and lubricants industry," Lowes says. "The new venture of contract cartage is a significant first for our company and sees the Goondiwindi-based business of Lowes Petroleum prove itself to be capable of meeting the stringent safety, quality and tight timeline requirements of Glencore, the world’s largest trading company. For its part, BP indicates that it and Lowes can be expected to pool their resources on the fleet front. "BP and Lowes Petroleum will be combining their trucks in the locations where the Lowes Petroleum Joint Venture will operate to continue delivering fuel to BP and Lowes’ customers," a BP spokesperson says. "There are over 100 trucks in the combined BP and Lowes Petroleum fleet." BP has also revealed a number of other initiatives aimed at restructuring it regional fuels business. These include agreements toward appointing Great Southern Fuel Supplies to operate BP’s depot and logistics business in Carnamah, Geraldton and Kewdale in Western Australia, and with Toll to outsource logistics operations in Tasmania. .
-
Uber-Like App "Cargomatic" bringing truckers more business
kscarbel2 posted a topic in Trucking News
USA Today / May 26, 2015 Cesar Lopez is one happy trucker. There's congestion at the ports, shipments are tougher to come by, and his days can be quite long. But now there's a new app that's bringing in more business. Way more business. Lopez, who runs his own independent trucking company, started using the Cargomatic app nearly a year ago to fill space on his truck with additional shipments. Business is up 35% since, he says. Asked to clarify, he says, "Over $100,000…no, more — $120,000." The extra bucks are coming in handy. Big trucks cost more than $150,000 to purchase, warehouses charge to use their services and it can cost as much as $1,000 to fill up a tank before heading down the highway. The app, from Jonathan Kessler and Brett Parker, is starting to catch on. Most of the 700 truckers working with Cargomatic are seeing $500 to $2,500 extra per shipments by working with the app, says company CEO Kessler. "We fill space on the trucks," says Kessler. "So Instead of being 50% full, now they're 75% full." Cargomatic, which currently operates just in southern California and New York, has been called the "Uber for truckers." Its app connects shippers with drivers looking for extra shipments to haul. Similar to Uber's founders, Kessler and Parker are trying to use technology to change an established business (in this case, a $70 billion business) with trade associations, unions and a long-established way of doing business. But Cargomatic isn't trying to replace established truckers and their rigs with a new set of drivers, Kessler says. "We're just trying to help them make more money." Still, there's some pushback. Weston LaBar, the executive director of the 6,000- member Harbor Trucking Association, which serves the Los Angeles and Long Beach ports, says his members are "skeptical" of the app , and none have signed up. "Anytime there's something new, there are people who don't understand it," Kessler says. The founders chose trucking as a business opportunity, they say, because of the huge impact it makes on all our lives. "Everything from the clothes on your body, furniture in your house, food in your refrigerator all comes on trucks," Kessler says. "Everything you use in your daily life will be on a truck at some point." Cargomatic is working with companies like Williams-Sonoma, Perry Ellis and Bass Pro Shops, offering lower-priced local shipments. When a new shipment comes in, it's broadcast to Cargomatic's network of truckers, along with the warehouse address and final destination. If the trucker is going that direction, he or she can select it in the app, and nab the job. "You don't have to call in, 'Where's my next dispatch?'" Lopez says. "Everything's at the click of one button. If it fits for you, you take it. Then you're done with it. " Kessler and Parker raised $11 million to get Cargomatic off the ground, and are still raising more money as they look to wider expansion in 2016. One investor is Volvo Group, which sold off its car business and now makes 70% of its profits from its fleet of trucks. Jonas Landstrom, investment director for Volvo Group Venture Capital, says Cargomatic is off to a "promising start, but it's early on their journey." Volvo invested, he says, because Cargomatic has "huge possibilities in terms of efficiency gains. But they have a lot of hard work ahead of them." Meanwhile, Lopez is happy with all things Cargomatic, except for one. He wants more business. "I wish they had more loads," he says. Related video: http://www.usatoday.com/story/tech/2015/05/21/uber-of-trucks-making-impact-in-los-angeles/27610727/ -
Australasian Transport News / May 27, 2015 The Arocs is a new vehicle that hasn’t graced Aussie shores until now. The Arocs is a severe-duty platform for high GCM and off-road work. In its native climes the big Benz is pitched as a construction and off-road vehicle. I recently got behind the wheel of Evaluation Unit 146, a 6x4 Arocs prime mover, before it was sent out to the back of beyond and the start of its test career. The team at Benz Australia reckons that this big banger may just have the right credentials to make it as a road train hauler. In Europe, the Arocs is available in a low tare weight variant called the Loader and the off-road variant called the Grounder. It’s fair to say that these clunky names probably won’t resonate very well in Australia and Benz is even considering dropping model names all together and reverting to the number based nomenclature of the past. Engine The 146 is a 6x4 Arocs prime mover, and under the blacked out cab sits a Euro 6 16-litre 630hp in-line 6 cylinder HDEP engine (model OM473, aka DD16). The big six also develops 3,000Nm (2,213 lb/ft) of torque and is equipped with a 475kW (637hp) of engine braking. The claim from Germany these days is that component life on the new range has been stretched out 20 per cent further than previous models. Another unconfirmed option is a water-based hydraulic retarder that adds another 400kW (536hp) of braking power to the engine. 875kW (1,173 horsepower) of retardation is certainly nothing to sneeze at. Transmission All of that circular motion gets to the back wheels via a 16-speed Powershift automated transmission, which uses a new dual plate organic clutch. Cab and controls The Arocs cab is quite imposing; this is the tallest cab in the range and this one was specced with a Bigspace sleeper cab. Through the matte black body wrap it was still possible to see the toothy grin of the rather distinctive Arocs radiator grille. This truck has a steer axle that sits further back than the Actros so time will tell how steer axle weights are going to play out, especially with the extra 150kg (331lb) of the Euro-6 (near EPA2010) driveline. But it also sits quite a bit higher off the ground. This particular truck can be equipped to work in roles of up to 170 tonnes (374,786lb) GCM, which explains the extra beef of the big Benz Banger. So far, the local engineering team has been able to get 1,150 litres of fuel on board this truck with the target being 1,300 litres (343 U.S. gallons). AdBlue (aka. DEF) capacity currently stands at 130 litres (34 U.S. gallons) with a target to increase this as well. Interestingly the batteries in the Arocs are mounted behind the cab at this stage and Benz has resisted the recent Euro trend of mounting batteries at the rear of the chassis to help with weight distribution. Getting to the cab is a long climb as this cab is significantly taller than any Benz I’ve driven in the past. Once inside in Mercedes-Benz Arocs, the environment is actually quite pleasant. Euro manufacturers often struggle to provide a decent sized bed, yet this truck has a respectable 750mm wide mattress that isn’t cut out around the seat. It also flips up to access the external locker boxes from inside the cab. These Aussie trucks have gained an extra 50mm of cab depth, which makes a world of difference but another interesting feature that’s available on the cab is the completely flat floor. The Arocs gets a black coloured dashboard as it’s expected to play in the dirt while the Actros will get a classier looking cream coloured one. This truck also had a rather nifty key fob that can be used to check lights, oil and coolant levels. The Mercedes-Benz Arocs uses a push-button start to fire the big 6 into life. Most other controls are fairly intuitive; my only gripe is that the transmission selector is tucked away a little too neatly under the steering wheel spokes. Performance Within minutes of rolling out of Mercedes-Benz’s Mulgrave headquarters, one thing was very clear: this was the most un-Benz like Benz I’d ever sat in. The Arocs’ engine sound had a harder edge and had urgency to it that the big lazy lugging old V engines never had. All that torque and horsepower wasn’t really getting much use as we only had one loaded trailer on board but the big Benz scooted though traffic quite well. Handling seemed firm and the whole cab seemed reasonably firm and stable in its ride. The in-line six seems to have better weight distribution than the old V engine, there’s less engine hanging forward of the steer axle. My experience with past Actros drives on public roads has generally seen me steering the cab through peaks and troughs like a yachtsman at sea. The Powershift transmission meandered through the various ratios with ease, happy to skip here and there at such a modest weight. This was also the first time I’d used the Benz EcoRoll freewheeling function, which kicked in nicely when coasting in traffic. There will be a steel suspension option for those who do want to drag road trains with this beast. And at this stage the trucks still use a hub-reduction drive. A hypoid drive option is currently under development. We took the Arocs for a drive on some country dirt; this is after all where it’s meant to be driven. The cab seemed well insulated with no squeaks or rattles at this early stage in its life. Verdict It’s the performance of the driveline that holds my attention the most. Vertical integration in the Daimler family has served this beast well so far and the Arocs is a very different kind of Benz as a result. Evaluation Unit 146 is being sent off to Western Australia where it will pay its dues in a road train role. Now that’s something I’d like to see. Specifications Make/model: Mercedes-Benz Arocs 6x4 (not finalised for release) Engine: 16-litre Mercedes-Benz OM473 Euro 6 Power: 466kW (625hp) @ 1,600 to 1,700rpm Torque: 3,000Nm max. @ 1,100rpm Transmission: 16-speed Powershift AMT Final drive: 4.33:1 GCM: Up to 170 tonnes (specification and approval dependent) Related video: http://www.fullyloaded.com.au/truck-reviews/1505/the-mercedes-benz-arocs/
-
Automotive News / May 27, 2015 General Motors sees "attractive" growth opportunities for diesel-powered vehicles in the U.S. and China. GM President Dan Ammann said sales of diesel cars will grow because diesels are an "intrinsically more efficient engine" than gasoline units. "We see attractive growth opportunities (for diesels) in the U.S. and, over time, also in Asia and specifically in China,” Ammann told reporters here on Tuesday. GM said it will expand its GM Powertrain Europe global diesel development center* in Turin, Italy. The center provides Opel/Vauxhall, Chevrolet and other GM brands with diesel technology. It grew out of GM’s failed partnership with Fiat at VM Motori** (2011-2013) and now employs about 650 people in a collaboration with Turin’s Polytechnic university. GM will add a new area to the center of about 2,500 square meters, dedicated to new labs and offices. Construction will start next year. The center developed GM's new 2.8-liter diesel engine that will be offered on the GMC Canyon and Chevrolet Colorado pickup trucks starting in the second half. It also engineered Opel's downsized 1.6-liter CDTI diesel which GM says is the quietest diesel in its class. * Founded in 2005 in Turin, Italy, GM Powertrain Europe is the center of innovation and development for diesel engines and related electronic control of GM globally and designs propulsion systems for Opel/Vauxhall, Chevrolet, and other GM brands. It was briefly part of Fiat-GM Powertrain during the entities’ 2011-2013 period. In late 2008, the R&D center relocated to the Polytechnic University of Turin, making GM the first automaker to become a physical part of a university campus. ** Noted Italian diesel engine maker VM Motori was acquired in 1995 by Detroit Diesel, then a 80/20 Penske-GM joint venture. In 2000, Detroit Diesel was acquired by DaimlerChrysler (1998-2007), who fitted many Toledo-built export Jeeps with VM Motori engines. Penske Corporation purchased a 51% stake in VM Motori in 2003 and acquired the remaining 49% from DaimlerChrysler in 2007. Penske then sold 50% of it to GM. Penske sold its 50 percent stake in VM Motori to Fiat Powertrain Technologies (FPT) in early 2011, resulting in an unplanned partnering of sorts between GM and Fiat. In late 2013, Fiat Group Automobiles acquired GM’s 50% stake in VM Motori.
-
As trucks of tomorrow take shape, two paths forward emerge
kscarbel2 replied to kscarbel2's topic in Trucking News
Platooning is a concept that Scania has already been working on for several years. DAF introduced their "EcoTwin" branded platooning concept this year. -
Reuters / May 25, 2015 Mario Enriquez says there's no real trick to getting great fuel mileage in a big truck. "Just take it easy," says the 61-year-old native of El Paso, who's driven an 18-wheeler for 11 years. "I don't gun the engine, I just gradually give it the gas." Enriquez averaged 9.74 miles per gallon from February to April in an International ProStar made by Navistar International Corp. For that, his employer, Mesilla Valley Transportation (MVT), awarded him a Nissan Versa compact car. Enriquez wasn't even the best of the company's drivers in the latest quarter, but no driver is allowed to win more than once and all those ahead of him were previous winners. The mileage performance Enriquez and truckers like him can achieve with current trucks is significant because it could influence how far the U.S. government pushes heavy truck makers to boost the average fuel economy of future Class 8 trucks - the over-the-road haulers like the ones MVT operates. Environmentalists want the Environmental Protection Agency to set a standard of 10 miles per gallon, up about 40 percent from current levels, as part of a broader effort to curb U.S. greenhouse gas emissions. Some truck manufacturers say that could be too aggressive. But owners of truck fleets such as MVT are running ahead of regulators and manufacturers, taking advantage of new technology and new ways of motivating drivers to cut fuel consumption. Their primary goal is cutting fuel bills, one of a trucking company's biggest costs. In the process, some truckers are already achieving mileage close to the target that green groups want the EPA to set. Brad Pinchuk, chief executive of Hirschbach Motor Lines, a midsize trucking firm, says some of his best drivers can get more than 10 miles per gallon out of their newest trucks today. In East Dubuque, Pinchuk is buying new trucks from Navistar International Corp that use automatic transmissions to boost mileage. Looking at the monthly fuel usage of a driver who recently switched to an automatic transmission truck, Pinchuk says the new model shows a mile-per-gallon improvement. Hirschbach also uses aerodynamic "sleds" and "tails" from startup SmartTruck, which attach to truck trailers and cut fuel usage by 10 percent by streamlining the flow of air around the trucks. Wabash National Corp offers a "skirts" and "tails" combination that provides similar savings. Wheel coverings from FlowBelow are another recent innovation, cutting fuel use by 3 percent, also by cutting the drag of air on the truck. Eaton is about to launch production of a dual-clutch transmission that it says will cut fuel consumption versus existing automatics by up to 12 percent. Engine maker Cummins Inc has a model in the pipeline that includes predictive GPS - which works out how to manage hills and valleys to use the least fuel. Klaus Kleinfeld, CEO of metals company Alcoa Inc, sees opportunities in the sector through increased use of aluminum to make trucks lighter. Daimler AG - the largest U.S. truck maker with 40 percent of the market so far this year last month showed off a Freightliner "SuperTruck" at an event in Las Vegas that has hit 12.2 miles per gallon in tests. Its latest production model gets close to 9 miles per gallon. Daimler is pushing fuel saving technology into current trucks. So far this year, 66 percent of its Class 8 trucks are equipped with some form of automated transmission, up from 33 percent in 2013. But company executives caution some SuperTruck innovations may not be marketable in 10 years' time. The EPA should consider different ways trucks are driven and set flexible standards, Wolfgang Bernhard, head of Daimler's global truck business, said in an interview. "There's all different kinds of traffic," Bernhard said. "So you need to say what you mean by 10 miles per gallon." An EPA spokeswoman said the agency intends to propose "performance-based standards that provide for multiple technological pathways to compliance." In other words, the agency wants to set a standard, and let truck makers and their customers decide what technology works best to hit the target. Kenny Vieth, president of ACT Research, which forecasts U.S. truck sales, says truck makers have reason to be wary of increasing costs. In 2005 and 2006, fleet owners splurged on new trucks to avoid buying 2007 models with expensive emission-reducing technology. "The whole industry has its fingers crossed that the EPA will focus on harvesting low-hanging fruit rather than home-run technologies that could prove expensive," Vieth said. At Hirschbach, Pinchuk has hired driver coaches to help improve driver efficiency. PeopleNet software in the trucks flags drivers for excessive repeated braking, which can indicate risky driving and also wastes fuel. Mesilla Valley Transportation CEO Royal Jones says many of his drivers average over 10 miles per gallon - though his fleet average is around 9 miles because short-haul drivers burn more fuel, since a truck can burn a gallon of diesel launching from a stop. MVT drivers have their top speed capped at 62 miles per hour using software, but any driver who gets over 8 miles per gallon is allowed to go up to 65 miles per hour. "If you're getting 10 miles per gallon, you're way ahead of the curve," Jones said. "But it is doable."
-
As trucks of tomorrow take shape, two paths forward emerge
kscarbel2 posted a topic in Trucking News
Commercial Carrier Journal (CCJ) / May 26, 2015 As OEMs and suppliers continue a rapid pace of new technology adoption into tractors, these truly are exciting times in the trucking industry. Perhaps the excitement was never more palpable than last month, when Daimler Trucks threw a press event for a group of international journalists and industry analysts and introduced the Freightliner Inspiration autonomous truck. Daimler touted the truck’s major advantages, including improved safety, lower driver fatigue and improved fuel economy. Perhaps as big of a news story as the truck itself is the fact that it now can operate legally in the state of Nevada, thanks to the Silver State’s issuance of the first-ever commercial autonomous vehicle license. The future of trucking clearly is coming quicker than most in the industry ever anticipated. But even as this huge hurdle in truck technology has been cleared, plenty of unsolved issues remain. An autonomous truck requires clearly painted lane and road markings in order to operate in autonomous mode. Limitations in forward collision mitigation cameras can’t discern certain objects; while they may detect traffic ahead, nonmetallic objects (a deer carcass, for example) remain invisible. Then there is the subject of the driver. Despite the misconceptions from many in the driver community after Daimler’s announcement that autonomous trucks would eliminate jobs, these new vehicles in fact still require a driver. Will fleets that eventually deploy autonomous trucks let less-experienced drivers operate a tractor that certainly will be priced at a premium above conventional tractors? After all, when a critical situation occurs and the driver suddenly has to reclaim control of the truck, don’t you want your best driver behind that wheel to prevent an accident? A week after Daimler’s announcement, Volvo Trucks North America took time during its Volvo Trucks Business Symposium to explain its vision for new truck technology that takes a decidedly different approach: platooning. Volvo believes so strongly in this technology that its Volvo Group Venture Capital subsidiary invested in Peloton Technology, a company currently developing a vehicle-to-vehicle technology relying on collision mitigation and active cruise control systems. Platooning would allow two or more tractor-trailers to link up on the interstate. The technology potentially would allow for platoon-capable tractors from separate trucking companies to link up on the road. The major benefit to platooning, according to Volvo, is fuel efficiency, as the two tractor-trailers traveling with only a small gap between them will decrease drag off the trailer of the first vehicle while improving draft for the second vehicle. The North American Council for Freight Efficiency recently published the results of an industry standard SAE Type II test, which showed a combined 14 percent reduction in fuel consumption – 4 percent for the front vehicle and 10 percent for the rear one. “Connectivity and new technology will help to avoid accidents in a far greater way going forward,” said Göran Nyberg, Volvo Trucks North America’s president. “Connectivity will be the next game-changer for the industry. Not in five or 10 years, but two to three years.” Susan Alt, senior vice president of public affairs for Volvo Group North America, added that widespread adoption of autonomous commercial vehicles might not be a reality during our lifetime. “Platooning will probably come to market first,” said Alt. “The technology exists today – we just need rules and regulations to allow it.” Major hurdles to platooning include working with states with strict limits on following distances to allow for the convoy to operate on the road without the rear vehicle being pulled over for tailgating. And if two separate trucking companies are linked in a platoon and an accident occurs, which company is liable for damages? These are just some of the many issues that will need to be addressed before autonomous or platooning trucks become an everyday occurrence. But when those questions ultimately are answered and public is more receptive to sharing the road with such trucks, trucking will look vastly different than it does today.
BigMackTrucks.com
BigMackTrucks.com is a support forum for antique, classic and modern Mack Trucks! The forum is owned and maintained by Watt's Truck Center, Inc. an independent, full service Mack dealer. The forums are not affiliated with Mack Trucks, Inc.
Our Vendors and Advertisers
Thank you for your support!