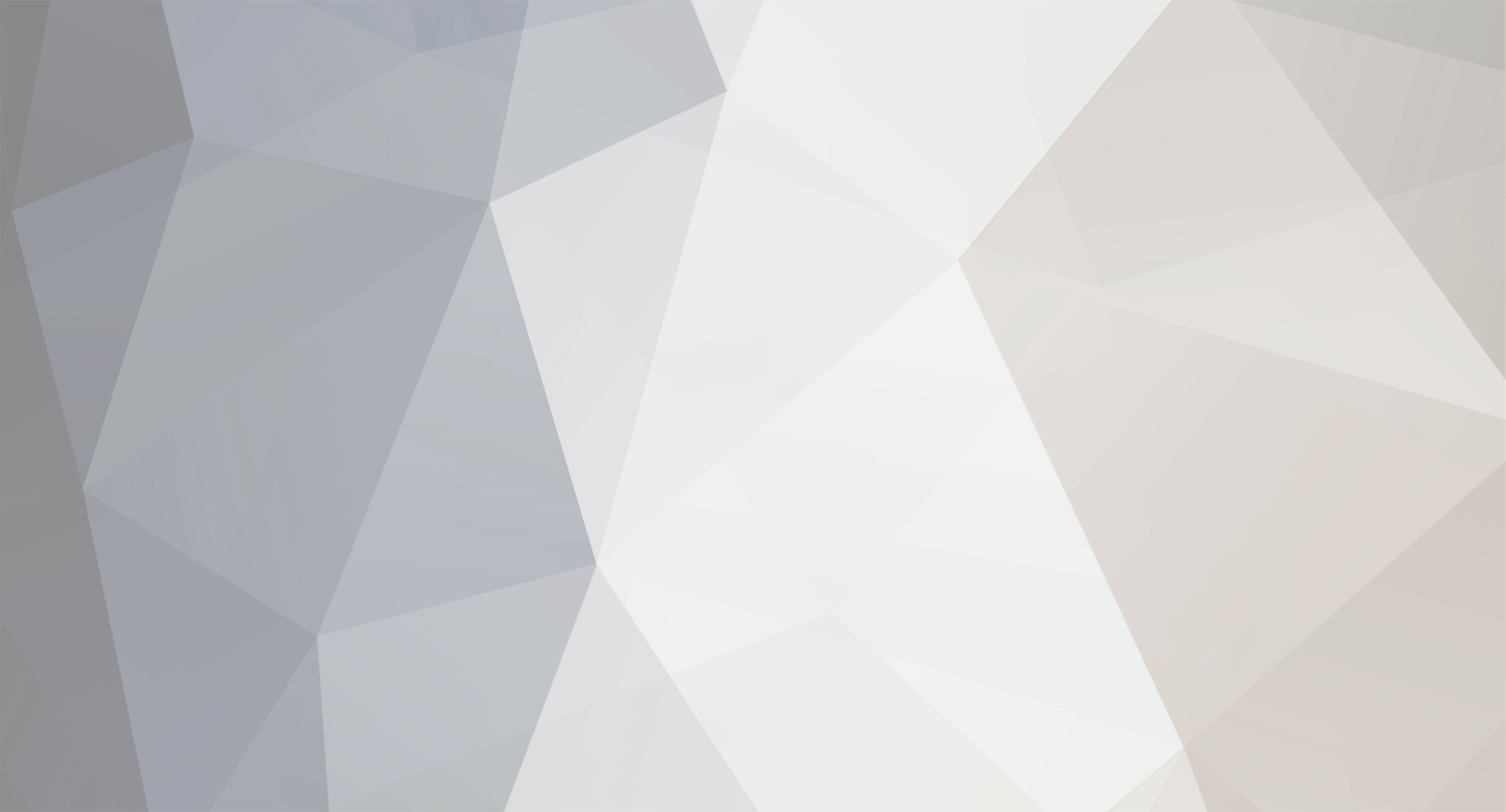
kscarbel2
Moderator-
Posts
18,535 -
Joined
-
Days Won
112
Content Type
Profiles
Forums
Gallery
Events
Blogs
BMT Wiki
Collections
Store
Everything posted by kscarbel2
-
Diesel News Australia / June 11, 2014 Cat Truck’s second model release for 2014, the high roofed CT630SC sleeper cab is based on the shorter CT630S released earlier this year. The Cat CT630SC retains the dimensions allowing the prime mover to fit inside the 26-metre (85.3 feet) 34-pallet B-double envelope, but with a full height sleeper cab. This latest release sees Navistar aligning its models to the Australian road rules and coming up with specifications closer to those required by the Australian trucking industry. By moving the cabin forward, when compared to the earlier models, and now developing an Australian designed and built high roof sleeper, a number of boxes have now been ticked, that weren’t in the past. Cat describes the SC sleeper as a 40 inch mid-rise design with an internal width of 2250mm (88.6 inches) and a 1975mm (77.8 inches) of standing room. The sleeper is fitted with a 711 mm (28 inch) wide innerspring mattress. This latest design also includes lockers on either side accessible from both inside and outside, something which has been missing from Cat product up until now. The SC sleeper is designed and built in Australia, and also includes a spacious storage compartment under the bunk (with room for an optional fridge), and a scalloped rear wall to optimize trailer clearance. “It was always part of our product planning that the SC would quickly follow the CT630S in the Cat Trucks model range,” said Kevin Dennis, Managing Director of Navistar Auspac (the new name for NC2 in Australia). “We already have the factory-fitted integral sleeper cab for shorthaul and regional roles but the SC is the critical addition to our range for linehaul B-doubles, and even B-triples.” “B-doubles dominate the linehaul freight industry and the need for a roomy, modern sleeper design that provides the driver with high levels of comfort and convenience yet maintains the ability to fit diverse trailer configurations within the 26-metre (85.3 feet), 34-pallet B-double envelope is more important than ever,” The two models released this year have shown Cat bringing the yellow engined trucks into line with Australian needs. In the past, the truck designs were simply adaptations of the Navistar designs sold in the US as Internationals, now a genuine Australian design focus is likely to better suit Aussie buyers. http://www.cattrucks.com.au/trucks/ct630sc/ .
-
The legendary ACCO – Designed and Built by Australians
kscarbel2 replied to kscarbel2's topic in Other Truck Makes
With operations in Australia since 1903, International Harvester established the Dandenong vehicle assembly plant in 1952. In continuous operation ever since, the facility has assembled over 225,000 trucks and bus chassis. International Harvester became International Trucks in 1989. Iveco purchased International Trucks Australia in 1992. Iveco being an unknown name down under, was allowed under the sale agreement to continue using the International name for 10 years in Australia and New Zealand. After the 1992 purchase, it was known as International Iveco Trucks Australia, and from 2001 as Iveco Trucks Australia. In early 2004, Navistar entered into a production agreement with Iveco resulting in International-branded trucks returned to the Dandenong production line in the form of 9900i and 9200i Eagle tractors. In recent years, Navistar had been importing trucks from North America and converting locally to right-hand drive. Navistar added the 7600 to Dandenong production in 2007. . -
The legendary ACCO – Designed and Built by Australians
kscarbel2 replied to kscarbel2's topic in Other Truck Makes
ACCO Walk-Around . http://www.youtube.com/watch?v=Z83mTwL8TiI -
The legendary ACCO – Designed and Built by Australians
kscarbel2 replied to kscarbel2's topic in Other Truck Makes
One of the advantages of the vehicles being fully manufactured in the one facility is that IVECO can work closely with the companies producing the machinery and bodywork that will be attached to the chassis in order to ensure the correct positioning of bolt holes and other fastening points. “We can be very responsive to our customers,” Reeman said. “We can build a one-off design or 100 copies of it and still be competitive in terms of price and time to manufacture.” ACCO trucks have almost become the de facto platform for the vocational market throughout Australia. Long popular as a mixer chassis, the ACCO’s strong and stable design allows it to withstand the stresses associated with having six to seven tons of concrete revolving on its back. The same characteristics also make it an ideal platform for mounting refuse bodies. The ACCO cab can be ordered with factory-installed dual steering to support front, rear and side-loading waste operations. The ACCO has long been ideal for customers looking for a sturdy, no-nonsense fleet vehicle. Over time, the robust reliability of the ACCO range has made the cost of ownership, combined purchase price and maintenance, repair and running costs, extremely economical. . -
The legendary ACCO – Designed and Built by Australians
kscarbel2 replied to kscarbel2's topic in Other Truck Makes
After International Harvester purchased English truckmaker Seddon Atkinson in 1974, a brand with a long presence in Australia, International introduced a Seddon Atkinson-badged version of the ACCO at Dandenong known as the F-4870 from 1980 thru 1989). The Seddon Atkinson F-4870 utilized a widened version of the Acco cab, and had an engine hump instead of a flat floor (International continued to build true Seddon Atkinson models in the UK). . -
The legendary ACCO – Designed and Built by Australians
kscarbel2 replied to kscarbel2's topic in Other Truck Makes
The ACCO (Australian Constructed Cab Over) was launched in 1972 as a modern replacement for the civilian model AACO. Over its long life, the basic shape of the ACCO has remained virtually unchanged. A unique feature of the truck is that every part of its cab-chassis design has been engineered, designed and made at the Dandenong plant. Through a diverse range of machining and shaping processes, raw sheet metal is converted into the components of the cabin. The Dandenong plant produces up to 650 ACCO trucks each year and it has produced more than 78,000 ACCO trucks since the model’s inception. Lloyd Reeman started as a mail boy with International Harvester in 1969, and then moved on to sales where he sold his first truck of the current ACCO design in 1972. Today, Reeman is Director Key Accounts, Sales Division for IVECO Trucks Australia – and still sells all ACCO models. The basic form of the ACCO range since the ‘70s has been a utilitarian cab-over-engine (COE) design. The design has a simplicity that was recognised from the start as a strong, robust and safe truck. “The early ones were pretty basic trucks, with few creature comforts for the operators,” Reeman said. Since the first truck rolled off the production line, more than 4,000 design modifications and additions have been made. “Many changes were implemented in response to customer requirements, but also the evolving health and safety legislation. We added air conditioning, different suspensions, insulation and power steering, among many other innovations to suit changing market requirements,” he said. . -
The legendary ACCO – Designed and Built by Australians
kscarbel2 replied to kscarbel2's topic in Other Truck Makes
The ACCO was born out of International Harvester’s desire to meet the vehicle needs of Australia’s military. The country was seeking to replace its World War 2 vintage GMC and Studebaker tactical trucks. The Australian Army told International engineers that they wanted a forward-control design like the Chevrolet “Blitz” produced during the Second World War for the Canadian military. The result was the International AACO (Australian Army Cab Over) tactical truck in both 4x4 and 6x6 configurations, first appearing on the drawing board in the early 1960s, and in prototype form in 1963. . -
The legendary ACCO – Designed and Built by Australians
kscarbel2 posted a topic in Other Truck Makes
Forty-two years ago, a legendary truck designed and built by Australians was born. Still in production today, the ACCO continues to improve with age. Born under the roof of International Harvester, the innovative ACCO combines real-world functionality with the ability to stand up to some of the harshest driving conditions in the world. The ACCO truck range is now owned by Iveco Trucks Australia, and continues to be produced at the same manufacturing facility in Dandenong, Victoria where it was born. The vast majority of the 2,000 Iveco-branded trucks that travel over three million kilometres every week are ACCOs. Active in every transport segment from food distribution to refuse, the ACCO has long been a part of Australia. . -
Scania Launches New 450hp Engine with SCR Only
kscarbel2 replied to kscarbel2's topic in Trucking News
The US does indeed need to join the rest of the world and use the "Euro" emissions standards, abandoning EPA2010 and adopting Euro-6. Currently, with or without EGR, a DPF is still needed to reach Euro-6/EPA2010 (we're VERY close to not needing it). But advances are being made which could change that. New forms of ultra-high pressure injection are in development, which could possibly eliminate the need for a DPF. So the possibility of a non-EGR engine with SCR, sans a DPF, is a future possibility. Of course, the entire powertrain continues to evolve as we speak. Keep an eye on Scania for leading edge developments in heavy truck diesel engine technology. -
Transport Topics / June 5, 2014 Navistar International Corp. announced June 5 that its fiscal second-quarter loss narrowed from a year ago as its Class 8 truck orders and market share improved. The maker of International brand trucks reported a loss of $297 million, or $3.65 per share, down from $374 million, or $4.65, a year ago. Navistar also boosted its Class 8 industrywide truck sales forecast to a range of 225,000 to 235,000, from a previous projection of 220,000 to 230,000. Its North American truck segment’s loss narrowed to $134 million, from $303 million a year ago. Revenue for the quarter ended April 30 rose 10% to $2.75 billion from $2.5 billion. “We have seen a number of encouraging signs this quarter, including improvements in our market share and strong order backlog, positive trends in our warranty expense and spend, and higher than expected structural cost reductions,” CEO Troy Clarke said. The period was the third consecutive quarter the truck maker has met or exceeded its guidance for earnings before interest, taxes, depreciation and amortization, Clarke said in a statement. Second-quarter EBITDA was $82 million after charges and adjustments, compared with its guidance of $25 million to $75 million. Orders and retail market share for both medium- and heavy-duty trucks improved sequentially and year-over-year. Navistar’s combined Class 8 retail market share was 14.9%, up from 13.9% in the previous quarter and 14.5% in the same quarter last year.
-
Exactly. Volkswagen AG has never expressed any interest in Paccar. However the company continues to consider Navistar from a distance. If you say it's been reported, where is the link to the news report?
-
Bloomberg / June 4, 2014 The 70-hour cap on a U.S. trucker’s workweek has a chance of being eased by Congress, undoing the result of a 15-year effort to reduce highway fatalities caused by drowsy long-haul drivers. The main federal regulation requiring truckers to take an extended break after reaching weekly time limits would be suspended under an amendment set for a vote in the Senate Appropriations Committee tomorrow. The new rule had taken effect in July 2013 and immediately drew criticism from the industry. The suspension, which would restore the industry’s 82-hour “workweek,” is intended to force the Transportation Department to address some of the regulation’s fallout, said Kevin Kelly, a spokesman for Senator Susan Collins, the Maine Republican sponsoring the amendment. The industry has said that the rule’s requirements for scheduling rest breaks at night forced more trucks onto the road during the daytime when traffic is most congested. “What has become clear during the past 11 months is that the new federal rules have presented some unintended consequences that may not be in the best interest of public safety, truck drivers and the businesses and customers who depend on their services,” Kelly said in an interview. The regulations took effect after more than 15 years of legal wrangling over sleep science, the role of fatigue in truck crashes, and how the costs of hiring more drivers to deliver freight would ripple through the economy. Truck Crashes “At the heart of this rule is an expectation to minimize the risk when tired drivers are behind the wheel of an 80,000 pound truck,” Anne Ferro, head of the Federal Motor Carrier Safety Administration, said in an interview. “The hours are exceedingly long.” The Senate amendment, if passed, would be attached to a broad transportation funding bill that would have to be approved by the full Senate and later reconciled with appropriations legislation in the House of Representatives. Truck crashes caused 3,912 fatalities in 2012, and the fatal-crash rate increased each year from 2009 through 2012, reversing a five-year trend. The hours-of-service regulation was expected to prevent 1,400 truck crashes a year, saving 19 lives and avoiding 560 injuries. 34-Hour Restart The trucking industry and business groups that rely on trucks to deliver their goods argue that FMCSA’s rest rules, which were made final in December 2011 and took effect July 1, 2013, have affected more companies than the agency projected. The American Trucking Association and its allies said regulators hadn’t done the research or analysis necessary to justify the changes, according to a letter they sent to Senate Appropriations Committee Chairman Barbara Mikulski, a Maryland Democrat, and Senator Richard Shelby of Alabama, the panel’s senior Republican. The trucking groups said they’re most concerned with the provision that forces drivers to take 34 hours off, which must include being off the road from 1 a.m. to 5 a.m. on two consecutive days during that period. This 34-hour “restart” requirement, which begins the clock ticking on a new work week, was intended to make sure drivers got enough sleep. The 34-hour restart only is required if a driver has reached the maximum weekly limits of 70 hours over eight days or 60 hours over seven days. Rush Hour There’s nothing in the regulation that forces drivers onto the road during rush hours, Ferro said. Drivers can set their own schedules and drive at night if they wish. There’s no requirement to get on the road the minute a 34-hour rest period ends at 5 a.m., she said. The vast majority of trucking companies don’t hit the 70-hour maximum, Ferro said. For 85 percent of drivers, it’s a non-issue, she said. The rules were written only after an extensive review of medical research on what human beings need to reduce fatigue, Ferro said. The agency held hearings across the country to gather industry input and reviewed more than 20,000 public comments, she said. Most of the companies that have been affected have already made the necessary investments to comply, through new agreements with shippers, reworking schedules and adjusting networks, Ferro said. Reversing the rules now would reward companies that have dragged their heels, while punishing those who have played by the rules, she said. Industry Cost The segment of the industry pushing the hardest for changes is relying on a system that shortchanges drivers, including forcing them to wait at loading docks, racking up hours of unpaid work, Ferro said. FMCSA won a U.S. Court of Appeals decision in August challenging the rules. The three-judge panel in Washington rejected most of the trucking industry’s arguments, describing them as “highly technical points best left to the agency.” That ruling capped years of wrangling over drive-time restrictions including two previous challenges before the appellate court. The court also ruled against groups including Public Citizen and the Truck Safety Coalition that said the rules didn’t go far enough. The final regulation was projected to cost about $470 million a year, with public safety and trucker health benefits of around $630 million. ‘Permanent Warfare’ Perhaps prematurely, the court said its decision would end the “permanent warfare” the regulatory battle had come to resemble. That was before trucking companies struggling to implement the regulations began complaining to Congress. None of the industry arguments ring true to Daphne Izer, the founder of Parents Against Tired Truckers, which has pushed for tighter rest rules for 20 years. The Lisbon, Maine, resident founded the group after her 17-year-old son, Jeff, and three of his friends were killed by a fatigued truck driver. Collins hasn’t spoken to her constituent as she has been crafting the Senate amendment, which Izer describes as a “back-door way of sneaking it in.” “This is fighting the battle all over again,” Izer said in an interview. “I’m mad, but I’m not doing this just to be angry. It’s hope for the future. It’s sparing others from going through what we’ve been through.”
-
Press Release / May 8, 2014 Italian truckmaker Iveco’s engine supplier, FPT, has launched the new Cursor 16. “We’re pleased to be able to reveal the engine to the public for the first time. Every now and then there is a massive leap in engine development and performance; FPT Industrial has achieved this with the Cursor 16,” said FPT Industrial’s Sales Vice President Massimo Rubatto. The new Cursor 16 offers best in class power and torque density, rated and max power as well as service intervals, crafted in a compact design to make it one of the smallest engines in its range. The Cursor 16 delivers 18-litre performance in a 13-litre package. It utilizes proven technology and represents the top level of the successful Cursor Series engine family, renowned for its reliability and flexibility. The 15.9-litre, six-cylinder in-line engine will be available in two versions: single stage turbo and dual stage turbo. The new engine is designed with the performance and durability to exceed the needs of heavy hauling applications, with the second stage version offering a fuel economy advantage in high load factor operations. The Euro-6 (EPA2010) emissions engine, with four valves per cylinder, delivers up to 764 horsepower (570 kW) with maximum torque of 2,449 lb-ft (3,320 Nm) at 1,500 rpm in its single stage version, and up to 845 horsepower (630 kW) with maximum torque of 2,581 lb-ft (3,500 Nm) at 1,400 rpm in its double stage version. The Cursor 16 is the first FPT engine to adopt a Compacted Graphite Iron (CGI) cylinder head, a high performance material providing high thermal and mechanical resistance. To be produced in FPT’s Bourbon Lancy plant in France, the Cursor 16 engine has been co-developed by FPT Industrial’s Research and Development teams in Arbon, Switzerland, and Turin, Italy. Combustion is optimized by the use of steel pistons, creating high peak cylinder pressure and, as a result, high power density and low Particulate Matter (PM) output. Combustion optimization is furthered with a FPT-developed double re-entrant combustion bowl, two different turbulent vortexes within the bowl allow for the accurate control of fuel and air mix to maximize performance and minimize emissions, while ensuring no residual fuel is left on the cylinder lining. The engine features a third generation ultra-high pressure common rail fuel injection system, of up to 2,200 bar, allowing a precise control of the injection process. The Cursor 16’s ball bearing turbocharger with wastegate further increases engine efficiency. FPT’s patented High Efficiency Selective Catalytic Reduction (HI-eSCR) technology is also utilized. Developed in-house to comply with Euro-6 emission regulations, the system reduces Nitrogen Oxide (NOx) emissions by more than 95%. With no PM after-treatment system and the high power delivery potential without a mandatory air handling system, the HI-eSCR system increases reliability and lowers maintenance cost, while reducing operating costs over the entire product lifecycle. The compact system allows for the optimization of space and minimizes the weight impact due to integrated components. In addition to its power and efficiency improvements, noise and vibration reduction has been achieved by the use of a rear geartrain timing system. Cursor 16 15.9 – Single stage (turbocharger) with wastegate Architecture: In-line 6-cylinder engine Injection – Ultra-high Pressure Common Rail (up to 2,200 bar) Valves per cylinder: 4 Displacement (l): 15.9 Unitary displacement (l): 2.65 Bore per stroke (mm): 141 x 170 Stroke/bore ratio: 1.21 Compression ratio: 16.5:1 Power range (rated hp): 644 / 691 / 764 Max torque (lb-ft @rpm): 2,205 (2,449 for 764hp rating only) @ 1,500 Dry weight (lb): 2,910 Dimensions (mm) L / W /H: 1,378 / 951 / 1,326 Cursor 16 15.9 – 2-stage (dual turbochargers) Architecture: In-line 6-cyliner engine Injection – Ultra-high Pressure Common Rail (up to 2,200 bar) Valves per cylinder: 4 Displacement (l): 15.9 Unitary displacement (l): 2.65 Bore per stroke (mm): 141 x 170 Stroke/bore ratio: 1.21 Compression ratio: 15.5:1 Power range (rated hp): 697 / 805 Power range (peak hp): 724 / 845 Max torque (lb-ft @rpm): 2,581 @ 1,400 Dry weight (lb): 3,197 Dimensions (mm) L / W /H: 1,378 / 1,010 / 1,326 .
-
Scania Launches New 450hp Engine with SCR Only
kscarbel2 replied to kscarbel2's topic in Trucking News
Scania’s new 450hp non-EGR powerplant meets Euro-6 (EPA2010) emissions levels using only SCR. As a result, the engine is inhaling 100 percent fresh air without any reduction in oxygen levels. Unlike engines with EGR, no percentage of fresh air intake is reduced, displaced by recirculated levels of exhaust gases (typically ranging from 18 to 30 percent). Without EGR (exhaust gas recirculation) piping, the “SCR only” powerplant realizes a weight savings of 88 pounds (40kg). Scania’s pure SCR solution also allows the use of a fixed geometry turbocharger rather than a more complex variable geometry unit. Exhaust aftertreatment remains the same, using a Tenneco-supplied module including an upstream NOx sensor, a diesel oxidation catalyst (DOC), a diesel particulate filter (DPF), AdBlue dosing module, two parallel selective catalytic reduction (SCR) catalysts with ammonium slip catalysts (ASC), and a downstream NOx sensor. Note that muffler and aftertreatment are brilliantly integrated into one compact module for efficient chassis packaging. While the folks in Gothenburg (Volvo) are toiling away at trying to extract and replicate the latest engine technologies of Daimler and MAN, the cutting edge engineers of the global truck industry at Scania continue a tradition of impressive innovation. Scania powertrain engineering truly is the benchmark for the global truck industry. . -
Press Release / June 3, 2014 Scania has now further broadened its already comprehensive range of Euro 6 (EPA2010) certified truck engines. Anyone who needs 450 horsepower, not least European customers with tractor-trailers, can now choose between two versions of Scania’s well known 13-litre engines at that power level. In its latest configuration it uses only SCR aftertreatment technology, and thus is expected to become a strong favorite among customers, especially long-haulage firms who prioritize low diesel consumption. “Our success with the 410 hp version of the 13-litre engine with only SCR has spurred us to go further down the road to reduce both complexity and diesel consumption,” says Joel Granath, Head of Product Management for Scania trucks. “Our customers now have a range of 18 different models of Euro 6 engines to choose from. This gives them unique opportunities to tailor their powertrains for optimal performance, regardless of driving conditions or application.” Because Scania engineers solved the puzzle of meeting tough Euro 6-emission requirements using only SCR – despite the high power range – customers now get increased freedom of choice with simpler solutions. The new Scania engine model – DC13 147 – requires neither a variable geometry turbocharger nor an EGR cooler. “Just as with the extremely fuel-stingy 410 hp model that appeared last autumn, this engine is ideal, especially for European long-haulage customers who prioritize low fuel consumption, but don’t want to give up torque or driver comfort,” states Granath. “According to our own calculations running a Scania Streamline, this results in a 1 percent fuel saving compared with the previous model using both EGR and SCR – everything else being equal.” Engines using only SCR technology require more AdBlue (DEF), on the other hand. In the case of Scania, this is normally an average of 6 percent of diesel fuel, while engines with EGR and SCR normally come up to 3 percent. For those who want to optimize their diesel fuel capacity, Scania offers a wide assortment of AdBlue tanks, including special solutions that use vacant space inside the frame in an intelligent way. The new engine model has, just like its predecessor, a very impressive torque: maximum torque is 2,350 Nm and is available right from 1,000 r/min, which assures very good driveability. “We are convinced that Scania’s 450hp engine with only SCR will become a popular workhorse out on the highway,” says Granath. “Using only SCR for aftertreatment has been shown to lead to lower consumption, and it also saves some weight.” “Euro 6 customers who have the advantage of being able to run on up to 100 percent biodiesel should look at the specially adapted version of Scania’s 450 hp engine range. That version uses both EGR and SCR for aftertreatment, just as before. http://www.scania.com/Images/wkr0006_tcm40-427362.pdf .
-
Claims Journal / May 1, 2014 The Department of Transportation (DOT) is seeking to mandate the use of speed limiters on trucks weighing over 26,000 pounds and traveling on roads with a speed limit of at least 55 mph. The department’s March 2014 “Report of Significant Rulemaking” states the new rule may take effect by October of this year. The DOT has not commented on the speed to which the heavy trucks would be limited, but previous proposals had included a limit of 68 mph. Advocates say that the rule would eliminate approximately 1,115 fatal crashes and require minimal investment by carriers since most heavy trucks already have limiters on board. The American Trucking Association (ATA) has asked for limiters on all new trucks, and the safety advocacy group Road Safe America (RSA) has proposed retrofitting all vehicles manufactured since 1990. Many fleets already limit the speed of their trucks with electronic governors. In the U.S., the National Highway Traffic Safety Administration (NHTSA) began looking at mandatory speed limiters on heavy-duty trucks in 2011. Two petitions for rulemaking were originally brought in 2006 by the ATA and the RSA, joined by nine motor carriers – Schneider National, Inc., C.R. England, Inc., H.O. Wolding, Inc., ATS Intermodal, LLC, DART Transit Company, J.B. Hunt Transport, Inc., U.S. Xpress, Inc., Covenant Transport, Inc., and Jet Express, Inc. The petition stated that a key strategy in preventing large truck fatal crashes is to reduce the top travel speed of the fleet. They cite studies showing that large trucks moving at high speeds have much longer stopping distances than the same trucks operated at lower speeds. Fatal crashes involving trucks are more prevalent on higher speed roadways, with 73 percent of traffic fatalities involving large trucks traveling on roads with a posted speed limit of 55 mph or higher. According to reports issued by the NHTSA and Federal Motor Carrier Safety Administration, and the Insurance Institute for Highway Safety (IIHS), large trucks are involved in fewer accidents than other types of vehicles per 100 million miles driven, but these accidents have a higher rate of fatalities. The DOT reports that: There were more than 1.1 million interstate motor carriers including for-hire, owner operators and private carriers (business fleets) as of December 2010.In 2007 (last available data), the Commodity Flow Survey reported that trucks hauled more than $8.3 trillion worth of goods.Approximately 11 billion tons of freight is moved each year.In 2009, 529 large truck occupants were killed in crashes.In 2009, 20,000 large truck occupants were injured.Annually, approximately 500,000 accidents involving trucks occur.In 2010, there were 1.1 fatal crashes per 100 million truck miles.Though the statistics vary depending on who is issuing the report, the commonality is that truck crashes are rising and often involve a fatality. The IIHS reports that in 2010: 286,585 million miles were traveled by trucks.3,413 people died in accidents involving large trucks.14 percent of the deaths were occupants in the truck.72 percent of the deaths were occupants in a different vehicle.13 percent of the deaths were people on motorcycles, walking, or riding bicycles.The number of fatalities rose by 8 percent compared to 2009.Large trucks accounted for 4 percent of registered vehicles but 9 percent of motor vehicle crash deaths.75 percent of truck accidents involving fatalities were tractor-trailers and 25 percent were single large trucks.The DOT did a detailed study called “The Large Truck Crash Causation Study” to analyze truck crashes occurring between 2001 and 2003. It reported that events that led to crashes included: loss of control of the truck after driving due to some event like a tire blowout;disabling or non-disabling vehicle failure – engine problem or hood flew up;another motor vehicle encroaching on the truck’s lane;poor road conditions due to poor road maintenance or weather;traveling too fast for road conditions;shifting cargo;lane drifting – either truck or passenger vehicle;driving off the edge of the road;improper truck maneuvering during events (turns and passing through intersections);coming upon a stopped vehicle;finding objects on the highway; anddriver fatigue.Reports show that 61 percent of fatalities occur on major roads other than interstate highways. Trucks often weigh as much as 30 times more than a passenger vehicle, so the smaller vehicle’s passengers are more likely to die in an accident involving a large truck. Tractor-trailers also require more stopping distance, especially when loaded, and need a correspondingly increased amount of time to react in order to avoid a crash. Many truck drivers are opposed to the new proposals. The Owner Operator Independent Drivers Association (OOIDA) has made excellent counter-arguments which boil down to, “Be careful what you wish for.” OOIDA argues that studies show that speed differentials lead to more collisions, so it’s safer to keep traffic moving at the same speed – something everybody who has pulled behind a truck traveling in the fast lane and trying to pass trucks in the slow lane traveling only 1-2 mph slower than their vehicle will attest to. Trucks all governed similarly won’t be able to pass each other. OOIDA also cites studies which say that car drivers (usually losing patience with slow-moving trucks) cause most of the collisions with big trucks when there is a fatality. OOIDA also notes that large trucks are not over-represented in fatal accidents. While they are only 3 percent of all vehicles, they drive 9 percent of all miles driven and are involved in about 11 percent of all fatal crashes. Lastly, OOIDA says that it is the states’ rights to set speed limits. According to the DOT the proposed speed limiter rule is slated to be sent to Secretary of Transportation Anthony Foxx for approval this month and then sent to the White Houses’ Office of Management and Budget in June. If it succeeds, the rule could be published as a Notice of Proposed Rulemaking in October. Fleets love them, and drivers hate them. But one thing is sure – the debate is not likely to end if the proposal is enacted. In fact, that’s when it will begin.
-
New Fee Structure for Pennsylvania Permits Starting July 1
kscarbel2 posted a topic in Trucking News
Heavy Duty Trucking / May 30, 2014 The Pennsylvania Department of Transportation will implement a new fee structure will be enacted July 1 for all types of permits, ranging from single trip/overdimensional, overweight, to annuals and seasonal permits, according to the Specialized Carriers & Rigging Association. Any increases in fees appear to be modest and this is the first change in the fee structure in over 20 years. The main impacts are an increase in the minimum overdimensional fee from $26 to $35 and an increase in the cost per ton mile from 3 cents per mile to 4 cents per mile. The new fee schedule is available from Pennsylvania’s Automated Permit Routing/Analysis System website. -
Russian truckmaker Ural has launched a new conventional truck model utilzing the cab from its GAZelle light commercial truck platform. http://trucks.autoreview.ru/_archive/section/detail.php?ELEMENT_ID=137796&SECTION_ID=7792 http://eng.gazgroup.ru/buyers/lcv/gazelle/
-
April activity points to Q2 seeing prices increase on resale and auction marketsFleet Owner / June 2, 2014 If April is any indication of how the used-truck market will perform in Q2, prices will be rising in both the resale and auction markets, according to the “Commercial Truck Monthly Report” for April on the vehicle-resale market prepared by The Truck Blue Book (TBB). The report states that April brought on price increases of 14% and 33% in those markets, respectively. What’s more, prices were higher than Q1’s average price by almost 4% and 2% in the resale and auction markets. “Heavy-duty prices increased 13% compared to Q1 in the asking-price market and medium-duty prices increased 11% compared to Q1 in the auction-price market,” the report’s author Jessica Carr, TBB’s associate analyst-- commercial trucks, told FleetOwner. She also noted that “volume fell in every market except medium-duty asking prices, where it rose 11%.” Carr also advised that “April showed positive change in asking and auction prices for the start of Q2.” And while asking prices increased across all five regions tracked, she said “volume was down drastically throughout April on the heavy-duty market.” Per Carr, April saw price increases across the board after the “minimal changes” seen during March. Key takeaways from the April report include: - Heavy-duty market recorded increases on both asking and auction prices at 15.7% and 30.8%, respectively - Medium duty saw a smaller change, however, it was also in a positive direction-- with 3.5% in asking price and 6.3% in auction prices - Volume on the auction market fell for both heavy and medium duty, at 42% for heavy and 66% for medium while the asking volume dropped for heavy at 22.6% and increased 12.3% on medium duty “As the market prepares for the usual sluggish spring and summer sales,” Carr observed, “prices are beginning to rise to compensate for the lesser number of sales at this time. “When focusing on commercial trucks between model years 2004 to 2014 in the U.S. with less than one-million miles, the average asking prices increased to the highest averages in 2014 so far for both medium- and heavy-duty trucks,” she continued. TBB found that overall Q1 asking prices were higher due to a significant increase in newer model-year (MY) volume, but the number of trucks on the market fell during April. Carr said the “significant drop” in trucks being sold was primarily driven by trucks falling within MYs 2008 to 2004 As for, medium- and heavy-duty trucks of MY 2010 and newer, all saw volume increases that drove the average asking prices on both markets upward. “We expect this trend to continue into the next few months as more of the new models enter the used market,” Carr remarked. “The largest volume increase from March to April was on the 2013 MYs, which is to be expected as they are more reasonably priced than a 2014 or a new 2013 while still having lower mileage than the 2011 or 2012s,” she continued. On the other hand, TBB discerned the largest decrease was for 2005 models, which dropped more than 50%. Heavy-duty trends spotted by TBB include: - Q1’s positive momentum for asking-price increases continued into April as asking - Prices increased 16% and auction prices rose 31%-- marking a much larger increase than the previous months - Q1 asking prices averaged higher than any quarter of 2013 and April started off Q2 even higher - Q2 auction prices increased as well, following the Q1 increase pricing higher than 2013 auction prices - As expected, prices on newer models have decreased since April of 2013 over 10% on MYs 2011 to 2014. However, those of MYs 2004 to 2006 saw increases year over year “The profound drop in truck supply on the used market has evidently caused prices to skyrocket in terms of the older models,” Carr pointed out. “The newer models are becoming more abundant in the more recent months as a larger number of 2013 and 2014 used trucks enter the market with competitive pricing,” she continued. Carr also observed that Q1 2014 started off the year with higher prices than Q1 of 2013. She said that “fed into the beginning of Q2 as April of 2014 saw a higher average asking price than 2013. This trend was caused by more volume on the newer model end.” Medium-duty trends spotted by TBB include: - Medium-duty market saw almost a 4% increase in asking prices and a 6% increase at auction during April - Large volume increases in newer trucks raised the overall average higher than - March. Even though the 2014s were stagnant, 2013s saw a 2% increase and 2012s decreased 6% during April - Medium-duty prices steadily inclined through Q1, showing higher average asking prices in March than January, while the increase in April brought prices 6% higher than January - Most model years saw minimum to no change in price during April - A number of MYs saw no change at all, including years 2014, 2009 and 2004 - Medium-duty asking prices were up 23% from April last year - Medium-duty volume is down immensely—year over year it was across the board with the exception of 2014 trucks; however, years 2008 to 2004 were impacted the most
-
Car & Driver / April 2014 At this year’s Detroit auto show, Ford’s F-150 nabbed headlines with its courageous move from steel to aluminum for the entire cab and bed, potentially saving hundreds of pounds. Equally courageous, but less reported, is Ford’s choice of materials for the 2015 F-150’s 2.7-liter twin-turbocharged “Nano” V-6 engine: It has a cast-iron cylinder block. Conventional wisdom says that iron is too heavy for modern cars and trucks. Ford’s first manufacturing genius, Charles “Cast-Iron Charlie” Sorensen, earned his nickname by integrating the Model T’s major engine and transmission components into just a few castings. But during the past two decades, engineers have systematically switched blocks and heads from iron to aluminum to save weight. So why the seemingly retrograde move to an iron block for the F-150’s 2.7-liter V-6, especially when this truck’s three optional engines all have aluminum blocks and heads? Because iron makes the most sense from an engineering perspective, and the most cents for the Ford Motor Company. In the 1950s, metallurgists began developing cast iron vastly superior to the Model T stuff. All cast iron is a mix of iron and graphite (carbon) with smidgens of other elements to fine-tune its physical properties. Basic gray iron is great for frying pans. Stronger malleable iron makes excellent crankshafts. Nodular iron has higher tensile strength and hardness, ideal for gears and camshafts. The best stuff is compacted graphite iron (CGI), which falls between gray and nodular iron in strength and stiffness while providing greater resistance to fatigue cracks. Graphite particles in CGI are shorter and thicker than those in gray iron. Under the gaze of an electron microscope, the graphite clusters in CGI look like coral tentacles. These entangled curlicues grip the surrounding iron matrix, in contrast to gray iron’s thin flakes and nodular iron’s spherical clumps. CGI also excels in thermal conductivity and internal-damping characteristics. The intrinsic damping helps minimize engine noise and vibration. When European high-speed trains suffered brake-rotor heat-checking and cracking, CGI saved the day. It’s the material of choice for exhaust manifolds, turbocharger housings, and flywheels. Hardworking turbo-diesel engines and NASCAR racers have had CGI blocks for years. Since iron is three times denser than aluminum, the F-150’s engine block is inevitably heavier than if it were cast from recycled beer cans, but there are offsets to consider. Since CGI is stronger and tougher, block walls can be thinner and main bearing saddles narrower, trimming overall engine length and weight. Engineers cleverly designed what Ford calls a two-piece block with the iron sandwiched between aluminum heads and a thick die-cast-aluminum “ladder frame.” The oil pan is molded plastic. No cylinder liners or expensive bore-surface treatments are needed inside the strong CGI, a significant cost savings. Because Ford is using CGI, its new V-6 is tougher, more compact, and less expensive than the all-aluminum alternative. In other words, this is an excellent way to counterbalance the extra cost of the F-150’s aluminum cab and bed. Cast-Iron Charlie would definitely approve. .
-
Diesel News Australia / May 29, 2014 The dirty diesel engine isn’t quite as bad as it is normally painted, according to a paper issued by the United Nations Economic Commission for Europe (UNECE), the body which develop the safety and emission standards for many parts of the world, including Australia. The report tells us only a small percentage of the particulate matter (PM) in the atmosphere we breath is caused by diesel engines in trucks, on the road. The paper is titled ‘Diesel Engine Exhausts: Myths and Realities’ and examines the effect of diesel in both Europe and North America. http://www.unece.org/fileadmin/DAM/trans/doc/2013/wp29grpe/GRPE-65-05.pdf The paper concludes 83 percent of the PM in Europe’s air comes from the commercial, institutional and household sectors. For the the USA this figure is even higher, at 97 percent. This leads the report to the conclusion, claims which say PM from diesels is the main cause for lung cancer in humans can be challenged. Attacking the major sources of PM in the economy will have a better health outcome than continuing to decrease PM limits for diesels. It is also noted the PM output of truck engines has been reduced by 90 percent in the past twenty years. Diesel engines are also vital to the economies in the 56 countries included in the study. Economic growth remains dependant on the distribution of goods and diesel is the fuel which makes this happen, and there are no serious alternatives on the horizon. “To improve the quality of air around us more attention must be given to the primary PM emitters,” said the paper. The report calls for a rethink of the way authorities look at pollution sources, concentrating on vehicles, and diesels in particular is not going to reap the kinds of rewards, in terms of better health outcomes, they are looking for. Better results will be had cutting pollution from industry and households.
-
R model rad opening molding
kscarbel2 replied to 85snowdog's topic in Exterior, Cab, Accessories and Detailing
So Volvo has stopped selling the 24RU516 R-model hood opening halves..........and replaced them with black rubber. Hmm. A not so subtle message is being conveyed here. -
May 13, 2014 Volvo announced on May 12 plans for the company’s new one million square foot Byhalia central parts distribution center in the Gateway Global Logistics Center, a new 1,500 acre industrial park located jointly in Fayette County, Tennessee and Marshall County, Mississippi. Suppliers from around the world will begin shipping every single Mack, Volvo, and UD truck part, Volvo Construction Machinery part and Volvo Penta marine part used for dealer repairs in the U.S., Canada and Mexico to the new Byhalia central parts distribution center. The facility, due to be completed in the fourth quarter of this year, is the keystone to Volvo Group's plans to consolidate its North American parts distribution network. It is located near Norfolk Southern's intermodal terminal in Rossville that opened nearly two years ago. At the same time, Volvo Group announced the closure of the company’s 196,786 square foot Memphis regional parts distribution center at 4903 Southridge in the Southeast Memphis industrial area. The new Byhalia central parts distribution center will eventually employ up to 250 people. Volvo Group is not yet ready to accept job applications, according to project manager Marcus Avenstam. Volvo Group said that suppliers will ship all Volvo’s “off-market” parts, to be sold for dealer repairs in North America, to the Byhalia central parts distribution center. Currently, parts are shipped from vendors to several warehouse locations across the continent. Avenstam said that Volvo Group chose the Mississippi location because, “It boiled down to a finite discussion of what is best for Volvo for a 30- to 40- year time frame.” Avenstam and the executive he reports to, Jan Lundegard, vice president of logistics operations, declined to discuss any incentives Volvo may have received from local or state government in Mississippi. Volvo determined the Mid-south was the place to be for its new, centralized strategy for distribution. “If you look at the continent of Canada, the U.S. and Mexico and if you look at the overall logistical structures that exist... we see this as a good spot to be. It’s also basically the parts distribution center for the United States.
-
Transport Topics / May 28, 2014 Con-way Truckload has purchased 550 new Kenworth, Volvo, Freightliner and Navistar tractors, 540 of which will be equipped with automated (AMT) transmissions and all with 6x4 axles. AMT transmissions Included in this purchase are the Eaton UltraShift, the Volvo I-Shift and the Detroit DT12 (Mercedes-Benz 12-speed G281-12 PowerShift 2 AMT). This purchase represents a significant increase of automated transmission trucks in Con-way Truckload's fleet, which previously was only operating 50 AMT-equipped trucks. Con-way says its decision was driven in part by driver requests for automatics, along with the company’s desire to lower the barrier of entry into a driving career. “We’ve found that many younger drivers looking to enter the industry prefer the automatic transmissions because it removes the perception that operating a truck is outside of their ability,” said Gretchen Jackson, recruiting manager at Con-way Truckload. “Truck driving is an essential role within the economy and, given the current driver shortage, we want to provide career opportunities for those who have an interest but may think the job is unattainable.” The new tractors will be on the road by December in a replacement cycle that will maintain the company’s 2,700-tractor fleet. Con-way Truckload is an operating company of Ann Arbor, Michigan-based Con-way Inc., which is ranked No. 3 on the Transport Topics Top 100 listing of U.S. and Canadian for-hire carriers.
-
The Volkswagen Worker’s “LT” cab is one of the most enduring designs ever produced. The cab was originally designed for the Volkswagen LT (Lasten Transporter, meaning cargo transporter) light/medium truck launched in the European market in 1975. Four years later, Volkswagen and MAN formed a joint venture to produce a series of commercial trucks ranging from 6 tons to 10 tons (13,228lb to 22,046lb). Dubbed the "G Series" under the VW-MAN partnership, it utilized a widened version of Volkswagen’s LT cab commonly referred to as the G90 cab, which was mounted on a MAN chassis fitted with a MAN drivetrain. The VW-MAN G-Series was produced from 1979 until 1993. Also in 1979, VW Brazil bought a 67 percent stake in Chrysler Brazil. One year later, VW bought the remaining shares of Chrysler Brazil. Though this ended Chrysler car production in Brazil, VW signed an agreement with Chrysler allowing the German company to continue production of Dodge D400 and D700 trucks at the former Chrysler Brazil plant in Sao Bernardo. When VW Brazil formed Volkswagen Truck and Bus in 1981, the new unit began with launching the 11-ton model 11.130 and 13-ton model 13.130 medium trucks which featured the G90 cab (wide width LT cab) mounted to a modified Dodge truck chassis. This marked the beginning of Volkswagen’s “Worker” series which remains popular to the present day. Up to last year, the Worker was available in 4x2, 6x2, 6x4 and 8x4 configurations from 7 tons to 35 tons (15,432lb to 77,162lb). However, the newer cutting edge Constellation has now replaced some models. The Worker remains available in 4x2 and 6x2 configurations rated from 13 tons to 24 tons (28,660lb to 52,911lb). https://www.man-la.com/produtos-volkswagen/modelos/worker-9 From 1990 to 1995, Volkswagen trucks and buses were built at the Volkswagen-Ford AutoLatina* joint venture utilizing Ford truck components. * Challenging economic conditions during the 1980s forced Volkswagen and Ford’s business units in both Brazil and Argentina to join forces and form a money-saving joint venture called AutoLatina in 1987 which lasted to 1995. VW and Ford trucks were produced together in Ford’s Ipiranga truck plant from 1990 to 1995. Due to the end the Autolatina joint venture with Ford, VW Truck and Bus had to withdrawal production from Ford’s Ipiranga plant and build its own truck plant in record time. In 1996, a new factory was built in Resende (west of Rio de Janeiro) in just 153 days at a cost of US$250 million. This also marked the beginning of self-designed proprietary Volkswagen commercial truck platforms. Innovative in design and management, Resende was the first truck plant in the world to adopt the “modular consortium” assembly process, in which the trucks are assembled by the supplier’s employees. Daimler, Ford, GM and Chrysler** went on to use supplier-assembled modules at their plants in Brazil as well. ** After an 18 year absence, Chrysler returned to Brazil in 1998 to produce the Dakota pickup. However, a Daimler-controlled Chrysler shut down Brazil production again in 2001. Fiat-Chrysler plans to open a plant in 2015. At one time, the Worker was sold in the U.S. market by both Kenworth and Peterbilt as the Mid-Ranger from 1987, until the Kenworth K300 and Peterbilt 270 utilizing a DAF 45 cab were introduced in 2000 (Paccar bought DAF in November 1996). Video - The Volkswagen Worker http://www.youtube.com/watch?v=1sbYaRQpMrk http://www.youtube.com/watch?v=FbsYBBt0Www http://www.youtube.com/watch?v=p781TbonEDk Video - The Resende Plant http://www.youtube.com/watch?v=pBWzYFho3wY&feature=related .
BigMackTrucks.com
BigMackTrucks.com is a support forum for antique, classic and modern Mack Trucks! The forum is owned and maintained by Watt's Truck Center, Inc. an independent, full service Mack dealer. The forums are not affiliated with Mack Trucks, Inc.
Our Vendors and Advertisers
Thank you for your support!