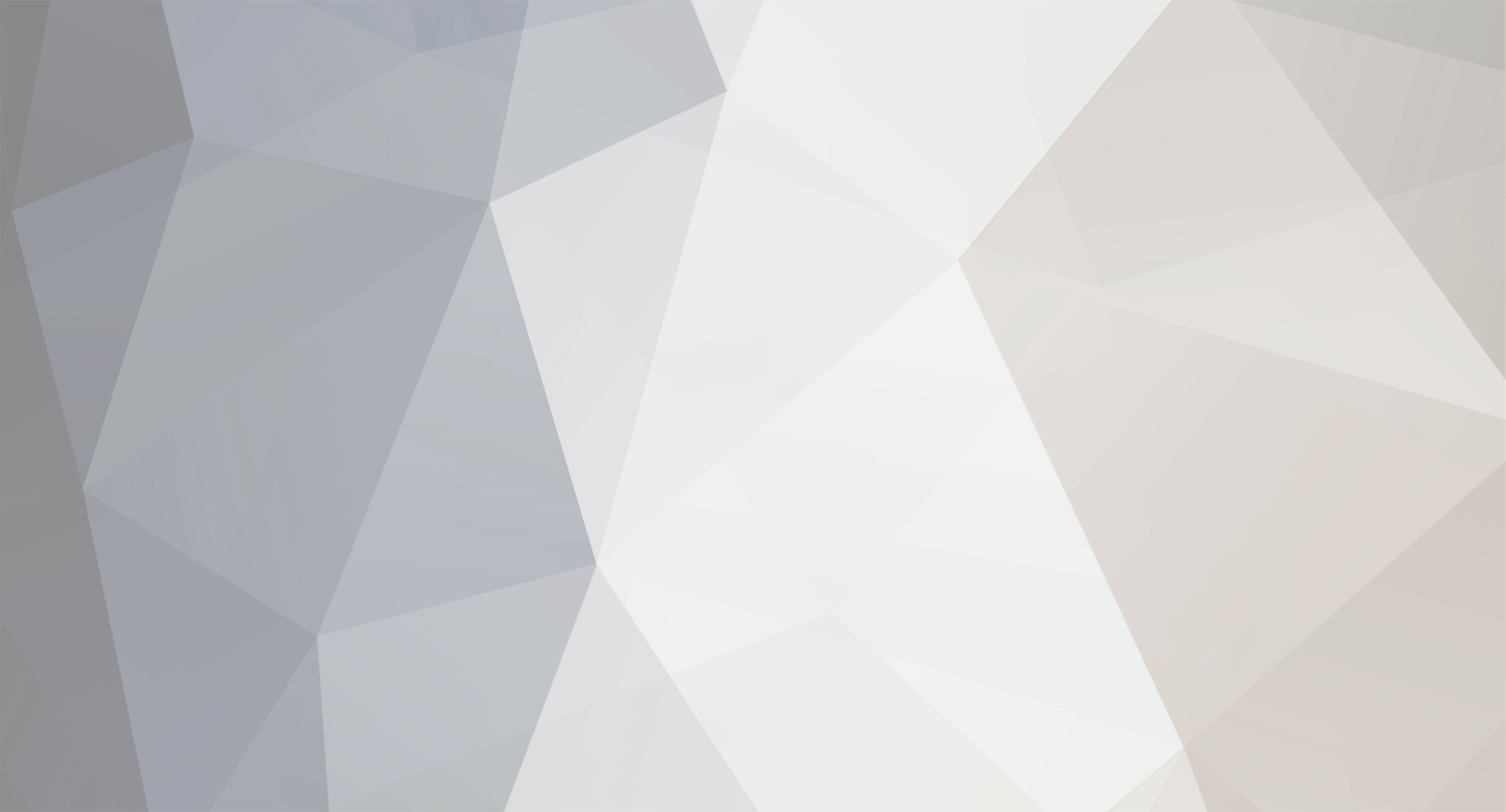
kscarbel2
Moderator-
Posts
18,541 -
Joined
-
Days Won
112
Content Type
Profiles
Forums
Gallery
Events
Blogs
BMT Wiki
Collections
Store
Everything posted by kscarbel2
-
-
Volvo Trucks Press Release / December 10, 2019 Following on from the launch of our electric trucks 2018 for urban distribution and refuse collection, we’re ready to explore the potential of electrification in more demanding segments too. So our two latest concept vehicles are designed for the conditions of urban construction and regional distribution. .
-
Scania Group Press Release / January 12, 2020 Scania’s rollover side curtain airbags targets one of the most critical consequences of rollover accidents, where drivers or passengers are injured in a collision or fatally crushed by their own vehicle. This unique solution deploy and protect those travelling in the cab if the truck rolls over. .
-
Ford Trucks has delivered its 1000th truck in Romania…
kscarbel2 replied to kscarbel2's topic in Trucking News
Bill Ford's heavy truck people are on a roll ! -
Ford Trucks International Press Release / December 25, 2019 Ford Trucks has sold 1000 vehicles in Romania in two years! Romania is one the most important markets in Eastern Europe for Ford Trucks, Ford Automotive's heavy commercial vehicle brand. To celebrate the delivery of the 1000th vehicle, a ceremony was arranged at the offices of Cefin Trucks, the local distributor, in Bucharest. During the ceremony, Ford Trucks International Markets Director Emrah Duman outlined Ford Trucks’ progress during the past two years. “In only two years in Romania, we’ve reached 8% market share in the heavy vehicle sector. We’re the market leader in the construction sector, with a 27% market share, as well as being in second place in the road trucks sector with 24% of the market share.” Ford Trucks has used its more than 60 years of engineering experience to emerge at the forefront of global competition in the heavy commercial vehicles sector. In Romania, one of the leading export markets in Eastern Europe, its 1000th truck was recently delivered. On Thursday, 28 November, Ford Trucks International Markets Director Emrah Duman and Eastern Europe Regional Manager Selim Yazıcı attended the ceremony. At Ford Trucks, the market leader of Romania's construction sector Ford Trucks first entered the Romanian market in May 2017, when they appointed distributors. In his remarks, Ford Trucks International Markets Director Emrah Duman noted that: As an EU member with a quickly developing economy, new construction projects, and state investments, Romania is in a position of focus for us. As an EU member with a quickly developing economy, new construction projects, and state investments, Romania is in a position of focus for us. At Ford Trucks, we’re very happy that we’ve been able to deliver 1000 trucks in such a short time. This success in Romania is due to our partnership with our distributor Cefin Trucks, the quality of our products and their suitability for the European market, our excellent engineering talent, the power of our research and development departments, and our technology. Our F-MAX truck, winner of the 2019 International Truck of the Year award, plays a very important role. We've now completed our infrastructure in all of Romania's big cities. At 12 locations, we provide sales, after sales service, and spare parts. By the end of this year, we’ll have 14 locations. The result of all this hard work is that, at the end of 2 short years, we’ve reached 8% of Romania’s market share for heavy commercial vehicles. Noting that Romania’s construction sector is growing rapidly, Duman said that “We’ve become the market leader in Romania’s construction sector, with 27% of market share. Also, we have the second largest market share in the trucks sector, with 24%. All of this success was achieved in only 2 short years.” The 2019 ITOY-winning F-MAX will continue to grow in Romania Commenting that the F-MAX’s ITOY award win would accelerate growth in Romania, Emrah Duman continued: “Following the ITOY award, we revised our plans for growth due to the heavy demand coming from Europe, and rearranged our international organizational structure. By opening country and regional offices in more than 10 countries, we aim to grow much more quickly in Europe.”
-
Ford Trucks International Press Release / December 25, 2019 Ford Trucks, Ford Automotive's heavy vehicles brand, has made a rapid entrance into the Western European market with back to back openings of dealerships in Portgual and Spain. European expansion has stepped up a gear… Emphasizing that Ford Trucks has reached significant market shares in countries such as Romania, Ukraine, Georgia and Kuwait, Ford Trucks Deputy General Manager, Serhan Turfan, said "We’re quickly trending upward in markets where we’ve only very recently begun operating. We’ve just expanded into Portugal and Spain, and our preparations to open in Italy will be finished by the end of this year. Our aim is to spread across all Europe, to Germany, France, the Netherlands, Belgium and Luxembourg.” Ford Trucks has used its more than 60 years of engineering experience to emerge at the forefront of global competition in the heavy commercial vehicles sector. With the F-MAX winning the 2019 International Truck of the Year Award, a new page is turned in the company's plans for global expansion. Following the ITOY award, Ford Trucks revised its growth plans due to the heavy demand coming from Europe and rearranged its international organizational structure. The company has appointed country and regional directorates in more than 10 countries and aims to grow rapidly in Europe. "We've completed our preparations for a sustained and potent growth in Europe" With the opening of dealerships in Portugal and Spain signalling Ford Truck’s expansion into Western Europe, Ford Trucks Deputy General Manager, Serhan Turfan, provided this assessment of the company’s global expansion plans: With our award-winning F-MAX, our global expansions plans have reached a very important threshold. Continuing its success after winning the ITOY award, the F-MAX was chosen as 'Truck of the Year' in Russia, Austria and Slovenia as well. In Europe and elsewhere, the demand for F-MAX and Ford Trucks is growing. "Our goal is to complete our expansion in Western Europe by 2023" Explaining that the company is trending upward in markets they have only recently entered, Turfan continued: "In countries such as Romania, Ukraine and Georgia, we aim to hit the same numbers that we have in other markets in Europe. We've recently expanded into Portugal and Spain and our preparations to operate in Italy will be complete by the end of the year." Our goal is to spread across Europe: to Germany, France, the Netherlands, Belgium and Luxembourg. Our target is to complete our Western European expansion by the end of 2023 and be present in more than 80 countires. We're ready to prove ourselves in the European market." In 2019, Ford Trucks continued to rise in the Turkish market Despite a tight market in Turkey for heavy vehicles, Ford Trucks was able to increase its market share, going from 28.5% in 2018 to more than 30% by the end of October 2019. Ford Trucks has seen uninterrupted growth for 10 years, and has doubled the market share it held in 2008 (14.7%), and now has the highest market share of the last 25 years.
-
DAF Trucks Press Release / December 18, 2019 150,000 fully electric kilometres - almost four times around the earth. That is the extensive practical experience that DAF has now gained with its CF Electric at several customers. The sophisticated vehicles with VDL E-power-technology are used on a daily basis by customers for the transport of for example food and containers. The DAF CF Electric was named Green Truck Logistics Solution 2019 in June, a prestigious award for the deployment of promising, emerging technologies for innovative, sustainable logistics in Europe. More and more cities are expressing their intention to only allow emission-free and almost completely silent vehicles in their city centers in the near future. The DAF CF Electric is an answer to that. Sales in limited numbers It is one year ago that the first CF Electric was delivered and in the past period DAF gained lots of experience with in total six fully electric trucks. Among other things, this has resulted in a version that is internally referred to as 'Phase 2' and has a new generation of software and a new dashboard. "We have now reached the point where we can start to sell the CF Electric in limited numbers," said Richard Zink, member of the Board of Management and responsible for Marketing & Sales. "Think of a few dozen units on an annual basis. In order to guarantee excellent quality, we start up production in a controlled way. Simultaneously, we can thoroughly build up our service network, step-by-step. The CF Electric tractor unit is now available for customers in the Netherlands, Belgium and Germany's North Rhine-Westphalia. Depending on the local battery charging infrastructure and after-sales possibilities, sales in other parts of Europe will be considered." Business case The use of the CF Electric has helped customers to determine the business case of an electric truck and experience what its use means in daily practice. Where in the first few weeks, they only used a limited part of their CF Electric’s 100 kilometres of range, some transport operators now drive around 250 kilometres a day with the vehicle. "It is a matter of planning your trips cleverly," said Richard Zink. "The ability to quickly charge the batteries - with the right equipment fully charged in just over 30 minutes - means that additional kilometres are available quickly if required. 18 hours per day, 7 days a week DAF customers Jumbo, Simon Loos and Tinie Manders Transport from the Netherlands and Rhenus Group from Germany all have a CF Electric in their fleet. Also at Tinie Manders, the electric truck is used very intensively: the tractor has already done more than 30,000 kilometres and runs seven days a week from six in the morning until midnight. Most are short trips in the Eindhoven region. “The CF Electric is as reliable as any other DAF truck", says Eveline Manders, co-director of Tinie Manders Transport. "Planning and driving an electric truck requires a different mindset. You have to make sure that the route fits the truck - and not the other way around. Moreover, in order to optimally use the truck, it is important that you can charge the batteries during loading and unloading. If you take these two matters into account, the electric truck can be a great alternative for urban distribution." Recently, DAF and VDL Groep announced that four fully electric, three-axle CF Electric refuse collection trucks will become operational, for the 'zero emissions' collection of residual products in urban areas. About the DAF CF Electric The DAF CF Electric is a fully electric 4x2 tractor, developed for distribution applications in urban areas with single or double-axle trailers and GVWs up to 37 tonnes. The truck is based on the DAF CF - 'International Truck of the Year 2018' - and operates fully electric, thanks to VDL's E-Power Technology. The core of the intelligent powertrain is a 210 kilowatt electric motor, which receives its energy from a lithium-ion battery pack with a total capacity of 170 kilowatt-hours. The CF electric has a range of approximately 100 kilometres, making it suitable for transporting high volumes within urban distribution. DAF CF Electric — Technical specifications Weight tractor: 9,700 kg Electric motor: 210 kW Torque: 2,000 Nm Battery capacity: 170 kWh Range completely charged vehicle approximately: 100 km Fast-charging batteries 35 minutes (bij 300kW) .
-
Cummins Press Release / January 8, 2019 Add life to ISX engines with tiered CLASSIC, PRO, or ELITE overhaul kits. These overhaul kits are currently available for ISX15 and ISX12 EPA 2010 (CM2250) | EPA 2013 (CM2350) engines. .
-
2020 Ford Super Duty plow package boasts best-in-class rating Trailer-Body Builders / January 10, 2020 The 2020 Ford F-Series Super Duty will tackle winter’s worst weather with the heaviest snow plow rating in the segment, Ford says. With the available Snow Plow Prep Package, Super Duty features a maximum 1,400-pound snow plow rating accounting for mounting hardware, which is best-in-class for gasoline-powered trucks in the segment1, and maximum 1,290 pounds which is also best-in-class for the diesel segment2. “Super Duty is a real workhorse in the snow removal industry,” said Mike Pruitt, Ford F-Series Super Duty chief engineer. “With our new Snow Plow Prep Package, we’re really delivering for folks who clear the way after a big storm. Being able to safely hook up bigger plows means roads, driveways and parking lots are cleared quickly and drivers can move on to the next job.” The new Snow Plow Prep Package, available for 4x4 pickups, includes heavy-duty springs specific to each configuration and an up-rated alternator to deal with heavy electrical loads. According to a study conducted by the Snow and Ice Management Association and Wolfworx/Singer Consulting, clearing the white stuff is an $18 billion industry in the US, one growing at a rate of about 3% annually. It’s comprised of more than 22,000 commercial contractors and more than 75,000 sole proprietors. The 2019 SIMA survey data indicates F-Series is the overwhelming choice, with nearly 50% of market share in an industry that values reliability, service network and, of course, rated plow weight, according to Ford. Owners will also appreciate other new features such as a windshield wiper de-icer, which pre-heats the windshield under the wipers to keep blades free of ice, as well as available heated steering wheel and heated front and rear seats. Optional white or amber LED strobe lights on XL, XLT or Lariat series trucks take a step out of the upfitting process. Deep Snow/Sand drive mode is available on models equipped with the all-new 10-speed heavy-duty TorqShift automatic transmission. The special drive mode changes throttle mapping and traction control settings to allow for added control and greater confidence in snowy or slick conditions. Plow operators can rely on the quality and craftsmanship of a high-strength steel boxed frame and high-strength, military-grade, aluminum-alloy body that provide a sturdy backbone, Ford adds. Customers have a choice of engines, including a standard 6.2-liter gas V8, an available all-new 7.3-liter gas V8 with best-in-class 430 horsepower and 475 lb.-ft. of torque and an available third-generation 6.7-liter Power Stroke diesel V8 with best-in-class2 475 horsepower and 1,050 lb.-ft. of torque. Ford F-Series Super Duty is built at Kentucky Truck Plant in Louisville, and Ohio Assembly Plant in Avon Lake, OH. Trucks are shipping to dealers now.
-
CNN / January 11, 2020 Twenty-one Saudi servicemen training at US military installations will be expelled from the United States after a review that followed the deadly shooting last month at a Naval Air Station in Pensacola, Florida. The Saudis are not accused of aiding the 21-year-old Saudi Air Force second lieutenant who killed three American sailors in the December shooting, but some have connections to extremist movements. Seventeen of the expelled cadets were found to have possessed online terrorist material. Fifteen, including some of the 17 who possessed online terrorist material, had images of child pornography.
-
Looking for info on the E9 marine engine
kscarbel2 commented on Macktitan 525's blog entry in Macktitan 525
https://www.bigmacktrucks.com/topic/50389-truck-to-boat-engine-swap/?tab=comments#comment-374249 https://www.bigmacktrucks.com/topic/34624-mack-–-scania-cooperation/?tab=comments#comment-231636 -
Sharing this post from Curbtender celebrating and acknowledging our mutual customer, West Tex Disposal in Odessa. Great chassis/body combo! We appreciate the business and look forward to continuing to support West Tex Disposal throughout the ownership experience. #Autocar #AutocarTruck #AutocarTrucks #AutocarSolutions #AlwaysUp #uptime #itsallabouttheuptime #Curbtender #TrashTrucks #TrashHauling #WasteCollection #GarbageTruck #FEL #FrontLoader #disposal #westtexdisposal This Curbtender Titan was mounted on an Autocar Trucks chassis and sold by Jer and the great team at Harrison Truck Centers. West Texas Disposal will be driving this green giant for years to come. #Curbtender #GarbageTruck #FrontLoader #AutocarTrucks #AlwaysUp
-
Scania Group Press Release / January 9, 2020 In Hull, United Kingdom, the Humberside Fire & Rescue Service has taken a Scania L-series low-entry fire truck into operation. The vehicle carries an aerial ladder platform, which at 45 metres is the joint highest in the country. To achieve Humberside’s overall on-road height requirement of 3.55 metres and provide maximum manoeuvrability and a high level of visibility for the driver, the vehicle has been specified with a low-height Scania L 360. The compact and lightweight Bronto Skylift aerial ladder platform stows to less than 12 metres overall length for transport. Its cage can raise 500 kilos vertically with the load monitored automatically. There is an integrated, space-saving 3,800-litre per minute capacity water nozzle. “We operate a 65-strong all-Scania fleet of heavy fire appliances and continue to specify Scania for their build quality and longevity,” says Andy Day, Fleet and Operational Equipment Manager for Humberside Fire & Rescue Service. “Our experience is that we see up to five extra years of service from Scania chassis compared to others we have operated in the past.” The L-series fire truck is based in Hull, where its height means it will be capable of reaching the top of every residential building in the city. .
-
Scania Group Press Release / January 7, 2020 The Upper Austrian Provincial Fire Brigade, Landes-Feuerwehrverband Oberösterreich, has recently begun using a Scania Interlink HD coach for logistical and tactical operations. The coach serves as a mobile command post and staff unit as well as a transport vehicle. “For over three decades, we have used a coach for transporting passengers and for accident and disaster relief operations,” says Fire Inspector Markus Mayr, Head of the Civil Protection Department of Landes-Feuerwehrverband Oberösterreich. In addition to standard features, the coach is equipped with blue light bars, blue flashing lights and a siren. However, the vehicle’s speed has been limited to 110 km/h. The Interlink coach has 35 seats and four tables, which if needed can easily be removed via a quick release mechanism. It also has a kitchenette, toilet and luggage room. “Replacing the bus with five to six smaller vehicles was out of the question,” says Mayr. “An important consideration was to obtain a spacious layout. This is definitely the case with the Scania coach.” .
-
Scania Group Press Release / January 2, 2020 All too often, an unhappy driver finds the cap broken and the fuel tank dry. Scania therefore introduces the Fuel Theft Alarm, with an installed sensor that monitors the fuel level, initially for single tanks and very soon also for the more common double tanks. “Although the loss of valuable fuel is bad enough, it is perhaps worse that the truck cannot carry out the day’s scheduled deliveries as planned and may be liable to penalties,” says Product Manager Eric Ljunggren, Scania. The fuel alarm monitors for up to 65 hours If the fuel level drops significantly, the alarm is activated and emits a high-pitched sound, which it shares with the normal theft alarm system. When activated, the alarm system monitors the fuel level for up to 65 hours, provided that the truck’s master battery switch is activated. The customer will also receive an e-mail, text message and a warning notification in their Scania Fleet Management Portal if they have the Control Package. One French fleet owner says that stolen diesel and ancillary costs annual set him back 12,000 euro. Although his depot yard is fenced and equipped with CCTV, thieves continue to plague him. “A large sum of money goes up in smoke each year but additionally the thieves break and pierce fuel tanks,” he says. “This requires repairs and the truck is immobilised. It’s all very, very annoying and now we’ve decided never to refuel on Fridays so that tanks are empty when we park for weekend.” Deterring presumptive thieves Perhaps the greatest advantage of the Fuel Theft Alarm is in deterring presumptive thieves. A sticker on the tank warns miscreants that the fuel is protected. Even if the fuel in the tank is saved, attempts may still cause grief since a broken cap might require time-consuming and costly repairs. “The owner and driver will be alerted if the vehicle is being tampered with and the consequences of having fuel stolen can be avoided or at least mitigated,” says Ljunggren. .
-
Japan throws stones at Ghosn from a glass house Commentary – Philip Nussel, Automotive News / January 11, 2020 As the Carlos Ghosn scandal unfolds with Hollywood-level kinds of drama and intrigue, it's refreshing to see the Japanese government launch its resources to rein in this fugitive from justice with all the righteous indignation of a nation that truly values international business ethics. It's quite an about-face for a business culture that allowed the Takata exploding-airbag scandal that has claimed at least 24 lives, injured some 300 people and generated the largest safety recall in the history of the global auto industry. Another 10 million airbags were recalled in the U.S. last week, in fact. But even more enlightening is how the prosecution and post-escape pursuit of Ghosn runs contrary to the Japanese practice of protecting its own business fugitives from justice, particularly when they stand accused by other countries of crimes that might not be considered serious in Japan. Supply chain corruption In the Takata scandal, the company in January 2017 agreed to pay a $1 billion U.S. criminal fine for its fraudulent conduct stemming from the lethal airbag defect. Three of its executives were charged with crimes in the U.S., but they stayed in Japan and never faced justice here. "Warrants were issued at the time of the indictment and are still active," a U.S. Justice Department spokeswoman said in an email to Automotive News, declining further comment when asked about extradition efforts. Perhaps more troubling is that for many years, dozens of Japanese auto suppliers systematically ripped off their customers — including their own affiliated Japanese automakers — in the U.S. and other countries. These suppliers allowed their sales executives to collude with competitors on the price of everything from ball bearings to wire harnesses. This institutional corruption resulted in countless billions of dollars in costs built into the price of light vehicles. The antitrust arm of the Justice Department spent much of the past decade, during the Obama and Trump administrations, prosecuting these crimes. As of 2018, U.S. antitrust regulators said their work yielded $2.9 billion in fines and convictions of 46 suppliers and 32 executives. The vast majority of them are Japanese. And while the companies themselves pleaded guilty and ponied up massive U.S. fines, as many as 20 individuals charged with crimes stayed in Japan, where they were protected from extradition. Some even kept their jobs. It's unclear whether the U.S. even attempted extradition — and very unlikely that it did. Japanese officials would have to cooperate in such a process. To this day, these Japanese executives carry the same international fugitive status as Carlos Ghosn. Ultimate irony The ultimate irony here is that Ghosn was blamed, in part, for creating this culture of corruption in the Japanese supply chain when he saved Nissan in 1999. Back then, Ghosn helped cut Nissan's costs by dismantling the automaker's insular supplier "keiretsu". He had the audacity to demand competitive bidding. As my former Automotive News colleague Dave Guilford suggested during an interview with Ghosn in 2014, suppliers responded to Ghosn's demands by fixing prices. "So it's my fault?" Ghosn responded, laughing. "That's a most original explanation." "I had nothing against keiretsu," Ghosn added. "It was working for our competitors. But it wasn't working for us." For the past year, Ghosn has been accused of a variety of economic crimes that, if true, might have cost Nissan tens of millions of dollars. If true. Yet Japan harbors fugitives who cost the entire auto industry far more, not to mention the loss of 24 lives, most of them in Hondas. Japanese authorities may have very good reasons for their bitter, relentless pursuit of Ghosn and his family, but they might be wise to take a look in the mirror and stop protecting their own business fugitives from justice.
-
Navistar MaxxForce engine class-action settlement finalized at $135 million Matt Cole, Commercial Carrier Journal (CCJ) / January 8, 2020 A federal judge has approved Navistar’s proposed $135 million settlement that will be paid out to owners of certain International trucks equipped with defective model year 2011-2014 MaxxForce 11- or 13-liter engines. Judge Joan Gottschall of a U.S. District Court for the Northern District of Illinois granted the final approval on Jan. 3. The judge concluded that the class action settlement is a “fair, reasonable and adequate resolution” of the truck owners’ claims. The approval follows an objection filed in October by four large fleets. As part of the settlement, those who purchased or leased International trucks with the defective engines can choose from three forms of relief for each affected truck they owned or leased. They can choose to receive up to $2,500 in cash, up to a $10,000 rebate on a new Navistar truck with proof of ownership/lease, or up to $15,000 in repayment for repair costs. The order states that Navistar will contribute $85 million to fund claims for the cash payout and repair repayment options. The remaining $50 million will be used for rebates. Owners and lessees of affected trucks have until May 11 to file their claims for any of the three options, according to the law firm Lieff, Cabraser, Heimann and Bernstein, which represented the class in the settlement. More information on the settlement and filing a claim can be found here.
BigMackTrucks.com
BigMackTrucks.com is a support forum for antique, classic and modern Mack Trucks! The forum is owned and maintained by Watt's Truck Center, Inc. an independent, full service Mack dealer. The forums are not affiliated with Mack Trucks, Inc.
Our Vendors and Advertisers
Thank you for your support!