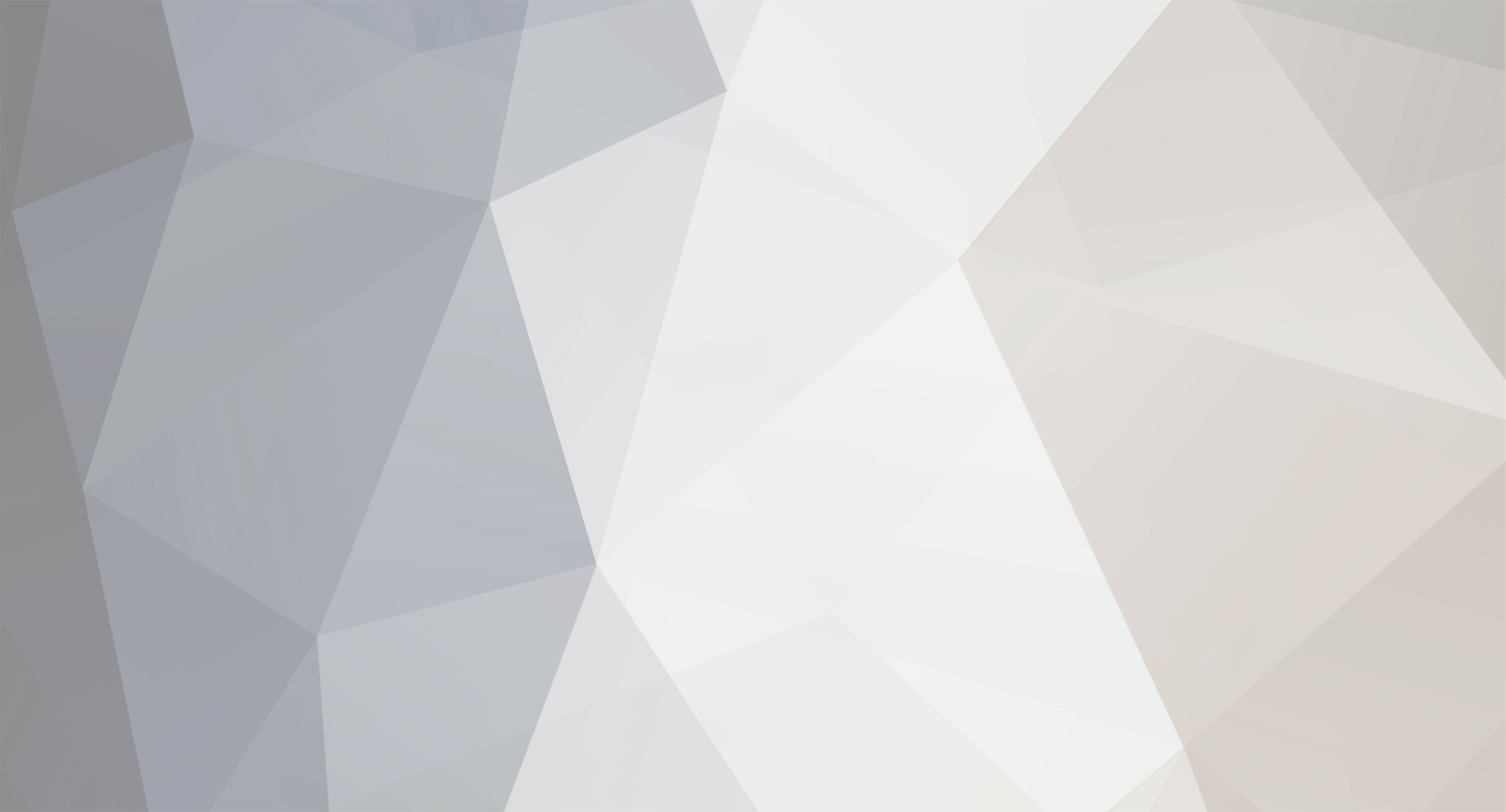
Mackpro
Pedigreed Bulldog-
Posts
2,991 -
Joined
-
Last visited
-
Days Won
10
Content Type
Profiles
Forums
Gallery
Events
Blogs
BMT Wiki
Collections
Store
Everything posted by Mackpro
-
Fuel level sensor/sending unit in tank low voltage or bad sending unit
-
Mack Truck CV713 Fault Codes
Mackpro replied to BBADA's topic in Modern Mack Truck General Discussion
First code is a MID-136 SID-4 FMI-2 which is right side drive axle ABS sensor. MID-142 SID-231 FMI-8 is Vechicle ECM J-1939 data link. MID-142 PID-177 FMI-3 is Transmission oil temp sensor. MID-136 SID-211 FMI-14 is an ABS fault but not in any of my books. -
If its fuse 41 and u have a air fan clutch, that fuse also feed some other things including the PTO plugin on top of the trans. Something else could be blowing it.
-
Possible Help With Default Code 9 2
Mackpro replied to awtfit's topic in Electrical, Electronics and Lighting
NUMBER: SB221032 DATE: 12/04/03 MODEL: ALL TITLE: 9-2 FAULT CODE DIAGNOSTICS AND REPAIR PROCEDURES <a name="s01">9-2 Fault Code Diagnostics and Repair Procedures (Not applicable to Mack Trucks Australia) (Supersedes bulletin SB-221-032 dated 3/20/03) A 9-2 fault code "Power reset without Key Switch" (Failure Mode Identifier [FMI] 4, Parameter Identifier [PID] S254 and Message Identification [MID] 128/142), will set with a MID 142 if the Vehicle Electronic Control Unit (VECU) senses a loss of battery without the key switch being turned off. A 9-2 fault code will set with a MID 128 if the Engine Electronic Control Unit (EECU) senses a loss of switched power without the key switch being turned off. Fault code 9-2 generally indicates a loss of power or ground connection to the VECU or EECU. Complete electronic diagnostic procedures for troubleshooting a 9-2 fault code are outlined in the V-MAC® III Service Manual, 8-211 (dated October 2001 or later). In addition to the diagnostic procedures outlined in the V-MAC® III service manual, when troubleshooting the cause of a 9-2 fault code, the investigation should include the following: The following procedures cover all chassis equipped with MACK engines and CL and CV model chassis equipped with Cummins engines. To avoid a repeat failure, do not stop performing the procedures outlined in this bulletin at the point where it appears that the problem may have been corrected. All steps (steps 1 through 8), plus the voltage drop tests, must be performed to ensure that the cause of the 9-2 fault code has been repaired. Inspect the batteries. Load test each battery. Check tightness of each battery connection. Clean and tighten as necessary. If the vehicle is equipped with a battery disconnect switch, check the connections for corrosion and tightness. Clean and tighten as necessary. Inspect the battery cable connections at the starter motor. Before proceeding, disconnect the negative battery cables from the battery. Remove the positive and negative battery cables from the starter motor. Note the tightness of the cable connections while they are being removed. Note any corrosion on the cable ends, then clean both sides of the cable terminal. Reinstall the battery cables and tighten the retaining nuts to 270 lb-in (31 N•m). [*] Inspect the left-side engine ground. Remove the bolt that secures the ground cable to the engine block (note the tightness of the ground bolt prior to removal). After removing the ground bolt, discard the star washer. Clean the ring terminals of all the ground wires, and also clean the ground bolt boss on the side of the engine block. Measure the length of the ground bolt, then measure the depth of the bolt hole in the engine block. Compare the measurements to be sure the bolt will not bottom in the bolt hole when tightened. Install the ground wire ring terminals onto the ground bolt, then install the bolt into the bolt hole in the engine block. Fan the ring terminals around the ground bolt so that the wire lugs are not on top of each other. Tighten the ground bolt to 120 lb-ft (163 N•m). [*] Inspect the left-side frame ground. Remove the bolt that secures the ground cables and wires to the left-side frame rail (note the tightness of the bolt prior to removal). After removing the bolt, discard the star washer (if equipped). Inspect the bolt and the wire ring terminals for signs of arcing or corrosion. Clean both sides of the ring terminals, making sure to remove all traces of the heat shrink sealant that may have oozed out during the heat sealing process. Clean around the ground bolt hole on both sides of the frame rail. Install the ground bolt, ground cable and wires, flat washer and nut. Fan the ring terminals around the ground bolt so that the wire lugs are not on top of each other. Tighten the nut to 37.5 lb-ft (51 N•m). DO NOT use a star washer. Spray paint the area of the frame rail around the ground bolt to prevent rust from forming. [*] Inspect the ground circuit breaker. Remove the retaining nuts that secure the cables to the terminals of the ground circuit breaker (note the tightness of the nuts prior to removal). Discard the nuts with the captured star washers. Clean both sides of the ring terminals, being sure to remove all traces of heat shrink sealant that may have oozed out during the heat sealing process. Install the wire ring terminals onto the terminal stud on the ground circuit breaker. Install a new nylock nut (part No. 21AX938) onto the terminal. Fan the ring terminals around the terminal stud so that the wire lugs are not on top of each other. Tighten the nut to 65 lb-in (6.16 N•m). [*] Inspect the left-hand side dashboard ground wire. Remove the instrument cluster and note the tightness of the ground bolt. Remove the ground bolt, discard the star washer and clean all the ring terminals. Sand or scrape to remove the paint from around the ground bolt hole. Install a flat washer over the ground bolt, then insert the bolt through the cross bar from the front side. Install another flat washer and secure with a prevailing torque nut. Install a flat washer over the bolt, then install the ground wire ring terminals, a flat washer and secure with a prevailing torque nut. Tighten the nut to 108 lb-in (12 N•m). [*] Inspect the right-hand side dashboard ground. Remove the "D" panel from the dashboard, then check the tightness of the ground bolt. Remove the ground bolt, discard the star washer and clean all the ring terminals. Sand or scrape to remove the paint from around the ground bolt hole. Install a flat washer over the ground bolt, then insert the bolt through the cross bar from the front side. Install another flat washer and secure with a prevailing torque nut. Install a flat washer over the bolt, then install the ground wire ring terminals, a flat washer and secure with a prevailing torque nut. Tighten the nut to 108 lb-in (12 N•m). [*] If the 9-2 code is logged in the VECU, proceed as follows: Remove fuse or circuit breaker No. 16 from the electrical equipment panel. Insert the purple male test lead adapter included in the Kent-Moore V-MAC® Test Lead Adapter Kit (tool No. J 38581) into the female terminal to check the tightness of the terminal. If the drag felt on the test lead is not sufficient, replace the female terminal end (part No. 925AM173). Remove power relay Nos. 1 and 2 from the electrical equipment panel. Check the terminal blades of the relays for deep scratches which indicated good contact between the female terminals and the male terminal blades of the relays. If deep scratches are not present, inspect the female terminals for damage or spreading. Replace the female terminals as required (part Nos. 2967-2807554 [Amp Industries part No. 280755-4] and 2967-422811 [Amp Industries part No. 42281-1]). Although the power relays may seem tight when being removed from the electrical equipment panel, this does not indicate sufficient contact between the male and female terminals. The only way of determining sufficient contact is by looking for deep scratches on the male terminals. [*] If the 9-2 code is logged in the EECU, proceed as follows: Remove fuse or circuit breaker No. 40 from the Engine Power Distribution Module (EPDM). Insert the purple male test lead adapter included in the Kent-Moore V-MAC® Test Lead Adapter Kit (tool No. J 38581) into the female terminal to check tightness of the terminal. If the drag felt on the test lead is not sufficient, replace the female terminal end (part No. 6031-12110844). Disconnect connector "B" from the EPDM. Inspect the connector terminals for corrosion and other damage, and check to make sure that each terminal is fully seated and locked in the connector body. Disconnect the engine-to-transmission transition connector. Inspect the terminals for corrosion and other damage, and check to make sure that each terminal is fully seated and locked in the connector bodies. Testing Voltage Drop Measuring voltage drop across a cable or a cable connection is useful in determining the integrity of the circuit. Cables or connectors should have no measurable, or only a fractional voltage drop. For a wire, cable or connector, voltage drop should be 0.1 volt or less, and for an insulated or ground circuit, voltage drop should be 0.5 volt or less. Voltage drop measurements greater than 0.1 volt for a cable or connector indicate the presence of high resistance that could be caused by a loose connection, dirt or corrosion. When diagnosing a 9-2 fault code, the following voltage drop tests should be performed, and the information gathered from these tests should be recorded on the "Voltage Drop Test/Battery Load Test Results" form included at the end of this service bulletin. The completed form can then be faxed to the Mack Trucks Electronic Service Engineering Department for analysis. Voltage Drop Test Procedures Voltage drop is measured by placing a digital multimeter (volt-ohm meter) in parallel with the component (wire, connection, etc.) as follows: Set the multimeter to the VDC function. Turn the vehicle ignition switch to the ON position. Long jumper wires with alligator clips on both ends may be used to facilitate performing the following tests. Measure voltage drop on the positive side of the battery by placing the positive meter lead on the positive battery post (terminal), then place the negative meter lead at the following test points: Measure voltage drop on the negative side of the battery by placing the positive meter lead on the negative battery post (terminal), then place the negative meter lead at the following test points: Battery negative post to battery negative cable end Battery negative post to starter ground terminal Battery negative post to frame ground Battery negative post to master ground circuit breaker Battery negative post to left-hand side dashboard ground terminal Battery negative post to right-hand dashboard ground terminal Battery negative post to alternator ground (G) terminal Battery negative post to left-hand side engine ground connection [*] Record the voltage drop measurements obtained at the above locations in the form provided with this bulletin. If voltage drop measurements are higher than specified, clean the connectors, terminals, etc., as required and retest. In addition to the above voltage drop tests, also perform an open circuit voltage test and load test of all the batteries. Include this information on the form provided with this bulletin. For information concerning voltage drop tests, battery open circuit voltage tests and battery load tests, refer to the MACK Electrical Troubleshooting Manual, 8-212. Battery positive post to battery positive cable end Battery positive post to starter solenoid battery ( terminal Battery positive post to starter relay battery ( terminal Battery positive post to power relays 1, 2, 3 and 4 Battery positive post to alternator positive ( terminal -
Possible Help With Default Code 9 2
Mackpro replied to awtfit's topic in Electrical, Electronics and Lighting
9-2 code is one or both of the ECM's loseing voltage. Check the black box ground breaker and aux starter solinoid mounted on the firewall ( on driver side of engine compartment) . Check all power and ground connections. The grounding bolt under the starter into the engine block. There is a Mack Service Bulletin on this but I can find it now. Check and see if your cab ECM (VECU) is facing up, ( connectors up) if so flip it over and clean connections. The R series cabs were bad about leaking water right on to the VECU. -
2010 Mack mp7 with a intake temp code?
Mackpro replied to popcorn501's topic in Modern Mack Truck General Discussion
We have a 2011 that has had 3 harness's on it in 16 months. At one time ,we were ordering 2 at a time for each truck down because it was a 50/50 shot of it being bad. At our last Mack school we had a big discussion about wiring harness'es, They are built by hand in various 3 world countries and take lots of man hours ti make hence they have a high failure rate. Somebody in class said why dont they build them here in the US. Think what a $850 russian made harness would cost if made here by a $30 an hour union worker ? $3,000? -
2010 Mack mp7 with a intake temp code?
Mackpro replied to popcorn501's topic in Modern Mack Truck General Discussion
i would unplug the sensor and see if the FMI changes from 2 ( data erratic)to 5 ( open circuit). If the FMI stays the same its the harness or connector ( my guess) . If the FMI changes to 5 then plug the sensor back up and clear all codes, with the key on/engine off does the code come on? Does the code come on after first starting up or do you have to drive it under a load to get the code to become active? -
2010 Mack mp7 with a intake temp code?
Mackpro replied to popcorn501's topic in Modern Mack Truck General Discussion
Here is a code listing and possible cause's for 2010 SCR engine's, your code is in there and shows possible causes. 2010 fault code list.pdf -
2010 Mack mp7 with a intake temp code?
Mackpro replied to popcorn501's topic in Modern Mack Truck General Discussion
Here is the sensor part# listing and location for most all 07 emission (non-SCR)MP engines sb273014.pdf -
Going to M-Drive class in the end of October in Atlanta. It's only a 2 day class and most everyone here at our shop has done been to it. I know anything more than a top cover, ECM or output shaft seal and you replace the complete unit. No tearing it down as of yet.
-
2010 Mack mp7 with a intake temp code?
Mackpro replied to popcorn501's topic in Modern Mack Truck General Discussion
The one you want to replace is the one that is mounted directly on the intake manifold. But to be 100% sure of the part # of the sensor, I need to know the exact model of the truck , CXU, CHU, GU, MRU or LEU. But If yor truck dosent have SCR/ Diesel exhaust fulid injection, the part # of the sensor you need should be #20524936. -
2010 Mack mp7 with a intake temp code?
Mackpro replied to popcorn501's topic in Modern Mack Truck General Discussion
If it is an MRU with an MP7, there are 2 sensors on the intake manifold, they both look exactly the same, the one towards the rear and mounted directly on the intake manifold is the boost temp sensor and thats the active code your getting. The part# is 20524936. The one mounted towards the front or on the intake maifold piping is the boost air pressure sensor. Same sensor part# is the same. -
2010 Mack mp7 with a intake temp code?
Mackpro replied to popcorn501's topic in Modern Mack Truck General Discussion
Forgot to ask , is it a GU713 or a MRU or what model? -
2010 Mack mp7 with a intake temp code?
Mackpro replied to popcorn501's topic in Modern Mack Truck General Discussion
When you change most anything on the engine you should do a "learn data reset" in VCADS. Whats the last 6 of the vin and ill look it up. -
2010 Mack mp7 with a intake temp code?
Mackpro replied to popcorn501's topic in Modern Mack Truck General Discussion
If the FMI is 5, it's an low voltage/open circuit . Make sure you have the correct sensor as the boost pressure sensor on the 07-09 DPF only engines are different that the ones on the 2010+ DPF/SCR engines. On the older MP engines the sensor is boost pressure only on the newer SCR engines its boost pressure and temp sensor all in one. They look exactly the same and will plug up but will derate and make codes appear. -
The "burp" was on the first orignal 2004 ASET turbos (631GC5171 series turbos) . The very first MP-8 turbos habe the same issue as well , a software update solved the MP-8's. When replacing the old style ASET turbo with the new style ASET turbos (631GC5176 series) there was a software update that should have been done. Pull the large hose on the front of the EGR cooler off ( going to the "S" shaped pipe that goes over the engine) and check for wetness/antifreeze. If dry its ok. The EGR valves on the early ASET's would sometimes break inside and cause EGR flow when there should be none but this would usually set a code for EGR issue.
-
I wonder if the VGT/wastegate is sticking. Take the stainless braided air line off the turbo actuator (VGT/wastegate) and lightly blow air into the wastegate and see if the rod moves down full stroke then springs back up when air is removed. The pivot pin can sieze up and the turbo will not work correctly. The pivot pin can be removed and cleaned and coated with hi-temp anti seize. An "E" clip holds it in. You might have to shoot a little air in the VGT to get the pin in and out. Dont put to much air to the VGT or you could blow the diaphram in it. I dont think the lower HP engines had the boost pressur relief valve in the intake manifold piping.
-
There is sometimes a "L" shaped bracket that goes from the cylinder head to the water pump housing. If this is missing it causes the assembly to vibrate and crack the water pump housing. Last 6 of the vin and i can maybe get u a parts pic and see if it wass equipped this way.
-
Our sister store sold a local fleet 15 CXU's with the MP8 and M-drive's. All the top drivers who are mostly oldtimers did not want to get out of their older CXU's with manual trans and climb into the new CXU's with the M-drives. Lots of bitching and groaning but the boss said just try them for a week. I not lying but the owner of the company/fleet said after a week , 100% of the drivers said to pass their older trucks on down the line and that their not giving up their M-drives. We have had no failures of any kind with the M-drives. I know one very very large dealership that had to replace 2 but it was by Macks request and just a drop in the bucket of the number of M-drives he had running around there.
-
Look at the tag on the turbo and see if the part# ends in something like 631GC5171M***. Hopefully you have the newer 631GC5176M** series turbos. The 5171 series had some weird issuses with them. You rarely see them much cause the had a high failure rate and probably have all bee replaced. Check for soot leaking around the exhaust manifolds and the EGR piping as the EGR piping actually had turbo boost pressure on it when under a load. Make sure this thing doesn't have an exhaust brake on it under the cab. Check the muffler for a broken baffle , rattling around and sometimes blocking air flow through the muffler. 8-3 code is the #3 EUP pump and shouldnt cause the noise and whistle issue.
-
2010 Mack mp7 with a intake temp code?
Mackpro replied to popcorn501's topic in Modern Mack Truck General Discussion
If under warranty send it to the dealer, otherwise throw parts at it. Extended warranties dont sound so bad after all (with these new engines). There are no troubleshooting books on the 07 emission MP engines and newer. The only troubleshooting guides are in the VCADS/PTT software that u can buy from a Mack dealer and put in your laptop. Sadly, with the MP engines, we dont even try to "fix over the phone" as it would take hours to explain and then without all the special tools and breakout boxes your wasting your time. With the older engines we could scan and fax pages out of the manual to the customer and help him that way but with the new stuff its impossible. By the way whats the FMI of the code and does the engine have SCR/ DEF injection on it? -
Low coolant sensor fault, with the FMI of 3 its probably not low of coolant but looks mor like a electrical/ wiring issue or a bad sensor. Unplug the sensor and put a paper clip jumping the two wires together and see if the light goes out, hopefully it does , if not unplug both engine ECM connections and check for oil or antifreeze in the engine ECM and harness.
-
On top of the dash in the fuse box look at fuse # FU53 its a 10 amp and powers the compressor. Also fuse # FU72 powers the complete AC/heater unit. And also check FU25 as well ( its a square shaped fuse )
BigMackTrucks.com
BigMackTrucks.com is a support forum for antique, classic and modern Mack Trucks! The forum is owned and maintained by Watt's Truck Center, Inc. an independent, full service Mack dealer. The forums are not affiliated with Mack Trucks, Inc.
Our Vendors and Advertisers
Thank you for your support!