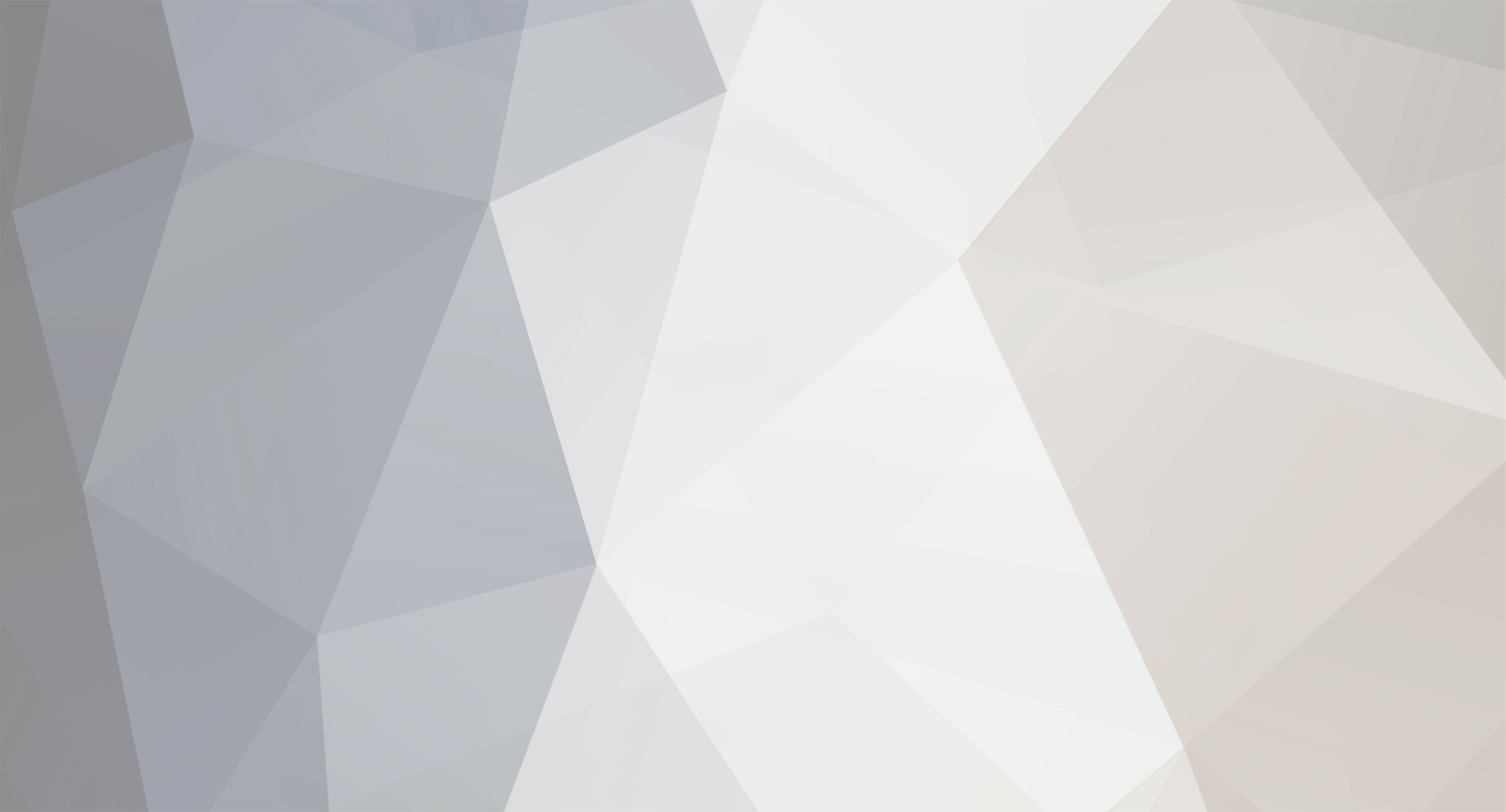
Geoff Weeks
Pedigreed Bulldog-
Posts
1,689 -
Joined
-
Last visited
-
Days Won
6
Content Type
Profiles
Forums
Gallery
Events
Blogs
BMT Wiki
Collections
Store
Everything posted by Geoff Weeks
-
We've been over this, time and time again. There is no "tubeless" 24" truck tire. There is no tubeless replacement for 24" tube type tires. There are Mfg in the far east that make tube type 24" tires. Cruiseliners tire shop is mistaken, they don't want to admit it, but if you look at the MFG tire catalog for the tire they claim to be "tubeless" RIGHT IN THE CATALOG it is listed as a TT or TUBE TYPE! I'm sorry to get so adamant about it, but it is right there in black and white from the mfg of the tires. To my knowledge, there isn't nor has there ever been a tubeless 24" truck tire in the sizes we are talking about The reason tubeless tire are "half sizes" I.E. 22.5" and 24.5" is because there has to be a "gutter" or drop center in the rim base so the tire can be fitted over the one piece rim. Without that drop center it would be impossible to mount a tire, you can not "stretch" the tire over the rim, there must be a smaller section of the rim base to provide the "slack" , so the edge of the bead can be worked over the edge of the rim.That make the center of the rim smaller or the same size at the center as the tube type it replaces. so a 22.5 rim measures the same at the drop center as a 20"flat based rim, same for the other tubeless replacements. a 15" TT trailer tire can be replaced by a 17.5" tubeless, a 20" TT tire can be replaced by a 22.5 tubeless, and a 22" TT truck tire can be replaced by a 24.5. THERE IS NO 26.5" tire to replace a 24"TT So for the last time, if you want to replace 22" and I can see why, then 24.5 is the answer if you want to replace 24" then you need to get another 24" and use a tube! For the people with 24" rubber, I am no longer going to answer, I have stated what I know time and time again, and the question keeps coming up with hand wringing and hopes for a unicorn that doesn't exist.
-
Ok, I'm trying to wrap my mind around what you are saying. SO is there separate wires in the box for back-up, stop and turn combo for left rear truck, and stop and turn combo for right rear truck plus tail, and separate turn and brake for the trailer 7 wire? Seams like too much for a single JCT box. Trailer turn (7 wire) are connected to the FRONT turn signals on the truck, while being supplied a brake light feed that is independent of the combo feed from the turn signal/brake combo the truck uses. That is a lot to stuff in a Jct box.
-
Is that JCT box for the 7 wire trailer or for the truck tail lights? I can see the 7 wire being in the cab but the lights on the rear of the truck generally run down the frame rail. You need wires for reverse lights that will not be on the 7 wire trailer cable, plus they generally only have two lights on the rear of the truck, so need a different feed from the turnsignal switch to incorporate the brake light function as well.
-
You used to be able to get bias tubeless, bias and radial are ply construction, tube or tubeless is another matter.You can and I do have tube type radials, and I have a bias tubeless. 22" is more of a problem than either bias, radial tube. the 22" size is hard to find, for that reason alone I would say go 24.4 tubeless. 20" used to be a lot easier to find, and a lot more choices when you did find them. I guess they are getting harder now.
-
Beats 6 mpg on a 6.9 Ford. Heck the L-10 semi would get 6. Just needs to get you where you needed to go. The less you spend getting to and from the job, the more that ends up in your pocket!
-
I put an engine in one of those, it had an exhaust brake (didn't work at the time and the owner didn't want to fix). What kind of fuel usage did the 4 cyl diesel give? I thought they would make a better service truck than the Superduty Fords I had.
-
Just wait, it will happen so often you loose the embarrassment. Remember "A mind is a terrible thing to loose"
-
I know! It is a CRS (can't remember S$%^) engine!
-
Look along the frame rail, there should be a 4 or 5 wire cable for the lights. Unless someone has totally ripped this truck apart, that is where the factory would have run the cable. I have diagrams for 1973 but not newer. They might tell you the color codes for the wires as those tend not to change much over the years.
-
Mack quantum with 18 speed Eaton has by itself split down in top gear
Geoff Weeks replied to Gorilla's question in Mack Truck Q & A
I thought/think he is refering to the "peanut valve" in the splitter cover. I don't know if they still use it, but it could be part of the problem. B11 in your picture -
New bearing installed, but ran into a snag, My soldering irons aren't big enough to heat the slip ring to get a good solder joint. I got them to release with a torch being very careful, and could likely get them back on the same way, but the stator bars need to un soldered and re soldered to wires. That is also going to require more heat than my electronics soldering iron can provide. Too much copper to dissipate the heat. So I'm off to buy some good old fashion irons in the 100 watt range. I took pictures of the slot and wooden "wedge" that goes under the bearing to hold the wires. Got the 1st slip-ring back on. I also took a picture of a JB series rectifier lay'd on the rear housing. If you could make the metal "can" to surround the rectifier and used Lexan sheet to insulate it from the rear casting, I think you could duplicate what I have. You need the "can" to direct air flow over and around the rectifier so it will cool. The next problem to solve is: The truck wiring is not up to 100 amps of charge. The ammeter is 50 amps, and that is about all I want to put through it. I don't want a shunt type modern ammeter as it will detract from the truck's originality. I have the L/N 100 amp regulator, which looks internally like a normal generator regulator with the current regulator removed. There is a place for 3 bobbins but only two are installed. I have found some manuals that suggest that a current regulator was used on some installs.The current curve rises and then flat-lines at 55-60 amps. Other current/speed curves show it continuing on up to the full 95 amps the unit is capable of. I think the chances of finding one of these regulators is about as good as finding another update kit! I can see no reason I can't use a 50 amp Delco, Ford or Autolite regulator in place of the L/N. I have done that before on alternators that I couldn't get regulators for. One step at a time. I'll first get this back together then decide on how to control it. I don't need 95 amps of 7.2 volts. 50 would be more than enough. I think L/N also felt that way, but wanted the high output at low speed that an alternator can provide (unlike a generator).
-
Well, I got the slip-rings and rear bearing off. P/S pulley puller got the outer slip ring, then I grabbed the rear bearing, but didn't realize there was a tiny snap ring between the bearing and inner slip ring (hidden behind a fiber washer and 75 years of crud) once that was off the inner slip ring and bearing came off together. Everything other then the bearings can be re-used. Hardest part will be re-soldering the slip ring wires.
-
Messy bench time: Puller arrived today, and although the paperwork that came with the kit shows a 3 jaw puller, I think the correct 2 jaw might work better. Came apart HARD, but likely hasn't been apart in 75 years. Good news is the kit will mate the rear bearing with no mod's. Bad news is the rear bearing really should be replaced. It is dry and I could possibly clean and re-lube, on the other hand I have it this far apart. As stated earlier, the bearing is inboard of the slip-rings, so they would have to come off to get at the bearing. Not sure I could get them off in one piece. Interesting construction, the rotor is made in three parts front and rear shell and shaft. Big nuts hold the shells on the shaft and allow field replacement of the field coil, and even voltage changes by changing the field coil itself. Something not seen on modern units. Stator is bar wound and very stout. I'll likely pick up new bearings in town, then see if I can remove the slip rings in one piece, even the manual says that isn't always possible. If it seams like there is a problem, then I'll order two new rings and make sure they are correct before I go further.
-
Somewhere on the .net there used to be a site where a Swiss trucker posted all his pic's from years of running from Europe all over the middle-east and even one trip to Pakistan via the Kiber pass (sp?). Almost all done in K100 KW with Detroit 2 stroke power. 1000's of pictures and stories to go with. I had it bookmarked on an old computer but somehow it got lost? All in the days of real film, so much harder than today with digital photo's I don't know if it is still all out there in cyber-land somewhere.
-
The alternators themselves date back to the 40's at least. Looking at the kit, it could be easily reproduced. The original rear cover could be machined, the hardest part would be the new stamped steel cover that would have to be made fairly accurately so to clear the electrical parts while still ducting cooling air over the diode blocks. I checked, the JB series will fit but are "backwards" in that the solid part of the block covers the cooling air duct,These have the diode toward the outside, and the JB has the diodes toward the inside.
-
Rather than get further off topic, I started a new thread here:
-
Rather than clutter up the Fire Truck thread, I thought I'd post here. Today I got the N.O.S. Leece Neville kit to update old selenium rectifier units to enclosed diodes like a modern unit. Very well made, and very serviceable. Scanned Document.pdf 2.pdf Scanned Document3.pdf I never even knew these existed, and 75 years on must be scarcer then hens teeth. For 12 volt I likely wouldn't bother, but for 6 volts, there aren't too many alternators available and this one is "from the period". I would have been happy with a 48 amp Delco generator in 6 volt, but those don't come up often either. This kit was along the lines of what I was going to try and make. Using Lexan to insulate JB2500 series rectifiers on the back case. Comes with everything including new brushes and a new ID tag!
-
What is the best method to clean out the coolant system?
Geoff Weeks replied to Gorilla's question in Mack Truck Q & A
-
Good reason to look up the parts book, and see what is required. I think the parts will be different for Mack rears vs. Eaton but am open to being corrected.
BigMackTrucks.com
BigMackTrucks.com is a support forum for antique, classic and modern Mack Trucks! The forum is owned and maintained by Watt's Truck Center, Inc. an independent, full service Mack dealer. The forums are not affiliated with Mack Trucks, Inc.
Our Vendors and Advertisers
Thank you for your support!