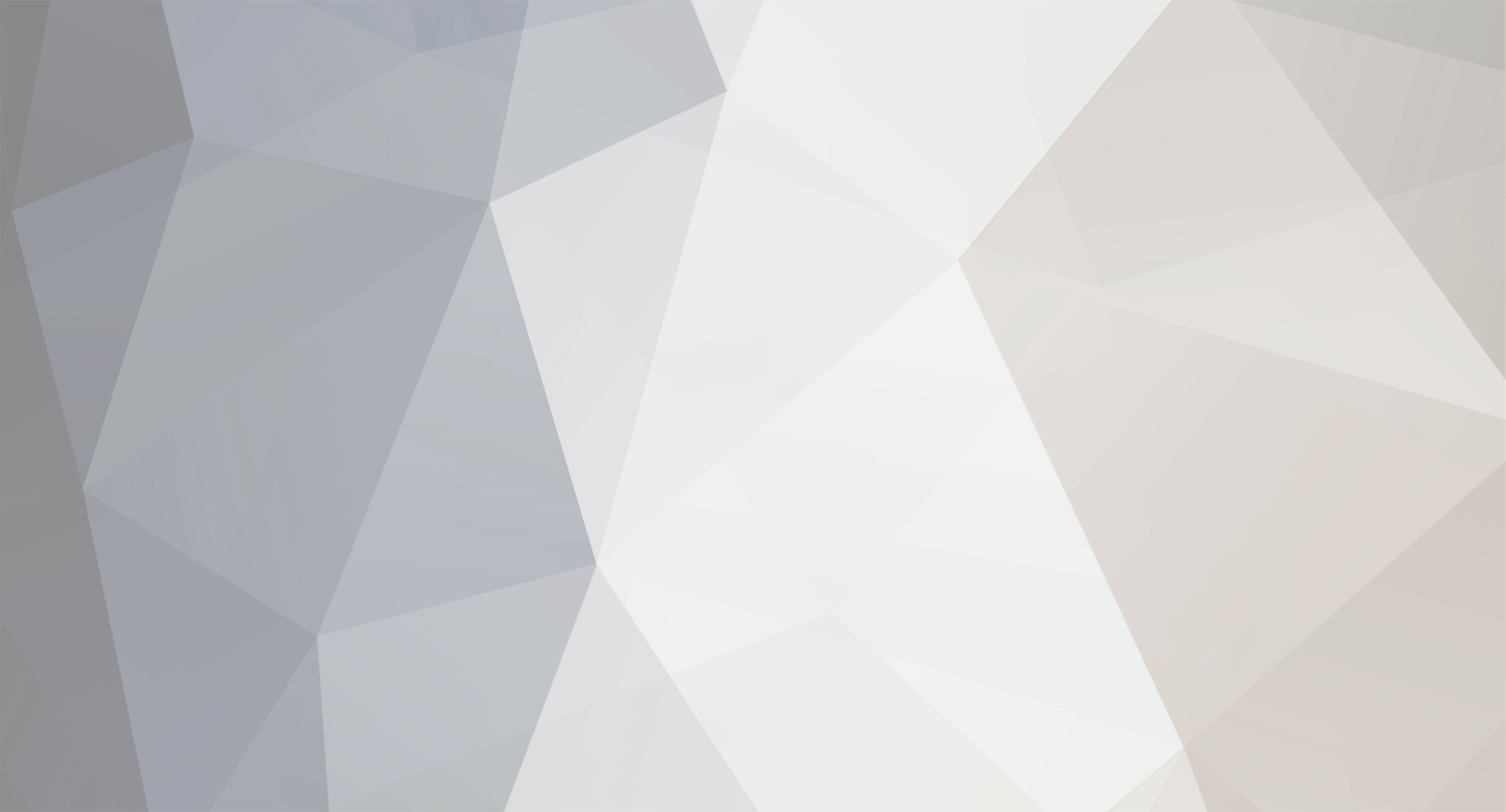
Geoff Weeks
Pedigreed Bulldog-
Posts
1,660 -
Joined
-
Last visited
-
Days Won
6
Content Type
Profiles
Forums
Gallery
Events
Blogs
BMT Wiki
Collections
Store
Everything posted by Geoff Weeks
-
this seams to imply that it was 18 volts before and after the regulator was replaced. Is that so? That would point to other problems Are you sure of your volt meter?
-
This is how I understand it: It was working fine, then it went to 18 volts, then the regulator was changed, then it stayed at 18 volts. If this is not the sequence than let me know what is. Two regulators being bad, is not as likely as one. There are resistor cards under the base of the regulator that cut the field current in stages. If one of these has failed it can not do its job. So there may be other reasons the regulators can't keep the alternator under control. Wiring and grounds are chief among them here. If it was working, then went to 18 volts, and the regulator was changed, and it went back to working for a while, then went back to 18 volts, then there are other suspects. The regulator works much like a single pole double throw relay. The top contact provides full battery voltage to the field. the field is connected to the movable contact. When the contact is neither touching the bottom or top contact, the field is fed power through the resistor cards, at a center tap. when the relay pulls all the way in and the moveable contact is touching the lower contact, the field is shorted to ground (no field current). In practice, the center contact is always dancing between the three positions, sometime touching the top sometime the bottom and most of the time in the middle, all based on the voltage supplied to the relay core. If one or more of the resistor cards are burnt too much current get to the field. If the regulator isn't well grounded, it may see only 11 volts between it and what it is attached too, even if the battery is seeing 16 volts, the regulator thinks it needs to raise the voltage when it really need to cut the voltage. This is what I mean by poor ground. The battery is often grounded to the frame, but the engine and body are often mounted in rubber bushings, so if you don't have good ground bonds, the voltage the body sees may be different than the voltage the engine sees, which may be different that what the frame sees. Good ground bonds are essential. If the field current is too high, because of a short in the field, or a 6 volt field being used as a replacement sometime in the past, because it looked right and fit, it could be burning the resister cards in the regulator, A check of the field current might give some answers, but I don't have the spec's. There are an awful lot of unknowns at this point. If you are working by yourself and aren't well versed in how to check these things, (often times it is much easier to show you than tell you how to run the checks) I would seriously have you consider a modern alternator set-up. There is also the rectifier situation, If you read the Wiki link I posted you will see that type of rectifier suffered from shorter life span and releases toxic fumes when it fails. I would hang onto the old set-up for show, but would suggest going with a modern unit for operation. When I get time, I am going to look into making a rectifier mount that will accept modern Leece Naville diode blocks, to mount on the rear of the alternator case, such that the cooling fan in the front of the alternator draws air over the diodes before it enters the rear of the alternator. The mount not only must hold the rectifiers blocks but also be electrically insulated from the alternator case, as well as being sturdy enough to take the vibration and heat in use. It must also protect from falling wrenches and such during maintenance. In modern alternators they are mounted inside the rear cover with insulating washers and feed throughs on the rear case. There isn't room for them inside the alternator case, I checked.
-
Replacing the rectifier is going to be a problem. There are remote rectifiers with a fan, as an assembly, but you are looking at several hundred dollars, and will not look like original. I think it is time to make the choice, original or retrofit? Nothing wrong with the original alternator, but the rectifiers are not the best, it was all that was available at that time. A replacement modern alternator, can equal or exceed what you have now, and all in the same footprint. I think I would either leave it be, or replace with a modern unit. Like I said, I have the same set up, only difference is your field is 12 volt and mine is 6 volts. If you go with a modern unit, it would eliminate the divorced regulator, the new ones are all self contained. So in short leave it as it is now, I wouldn't open it up unless you detect a bearing problem. The brushes and brush holder can break easily when you try to remove. Last I checked, they were still to be had, I have one stuck/broke one in my alternator and purchased are replacement brush holder. My brushes looked ok so am not going to replace. The other option, is to replace. Your choice.
-
Here is a simple test you can do. Get a test light, connect one end to a good ground, turn on the ign switch and touch the other end of the test light to each field terminal. It should light on one and not on the other. If it lights on both, you have a bad ground, if the doesn't light on both, either you have a bad regulator or it is set -up different than mine and regulates the ground side of the field (not likely, but can't rule it out.) Anything more and we are going to have to get deep into testing stuff that is hard to explain over the .net.
-
The two small wires on the back are field wires. One should go back to the field terminal on the regulator. Because your regulator is not identical to mine, I can't be sure where on the rectifier you connected the other will make a big difference. If i had to guess, I would guess the one field wire not connected to the regulator would go to ground, but without seeing the regulator and tracing out how it works, I can't be sure. The simplest course of action would be to replace with a modern "one wire" alternator, and do away with the troublesome rectifier and divorced regulator. It depends if you want period correct or not. You need someone who understands the system to guide you. This kind of work is very hard to diagnosis over the internet
-
Oil in the air tanks
Geoff Weeks replied to nam vet's topic in Antique and Classic Mack Trucks General Discussion
Just put on and fire it up. It doesn't fill with oil, oil is pressureized into the crank, which lubes the rod and mains , oil then drains back to the engine sump. -
Not so far in left, it depends on how well the regulator can clamp a light load. Normally, alternators of this size came about after the electronic regulators. Smaller output units, the battery can stabilize the highs and lows, Mechanical regs were primarily used when cars had 37- 45 amp units and trucks were no bigger than 60 amps. 100 amps, with a mechanical reg and resistor cards, were rare. I have not had the 100 amp 6 volt unit up and running on a vehicle so I don't know how well it clamps the voltage on a light load. That said 18 volts is way above the 14- 14.2 set point. I would expect it to be able to clamp better than that. A short in the field lead could burn a resistor card in the regulator and permanently damage the regulator. Finding replacement resistors would be hard. All that said, I wouldn't want the selenium rectifiers. That is what holding mine up/ I want to replace with modern diodes. Modern L/N diode packs would work well, but need to be cooled, so I need to fit them, isolated from case, in the air intakes on the back so cooling air gets drawn over the diodes. Just getting the time to get it done.
-
45mph w/ 5.13 rear ratio how can I go faster
Geoff Weeks replied to mack31's topic in Driveline and Suspension
Bet on it. 700 cid would be a whole lot of hurt if it came apart. -
In case anyone cares: Here is my 100 amp 6 volt unit, a bit different from his 100 amp 12 volt regulator. Output from the alternator is 3 phase delta wound stator. A three phase bridge rectifier that is isolated from the trucks wiring when the engine is off, via the big relay under the reg cover. On mine the voltage regulator controls the hot side of the field, but the alternator itself could be regulated by either hot or ground side. Note the grounding tab on the last picture to ground the rubber mounted regulator (common at the time to isolate the reg from the truck to reduce vibration induced problems. Rectifier is isolated when the truck is off to prevent leakage back through the windings and for safety, in case something falls on the rectifier when someone is working on the engine. Mine came from a 40's GMC tow truck.
-
Yeah, but a threaded pin does nothing to help remove the bushing, hanger still has to come out to replace the bushing if you don't have access.
-
Be aware the Selenium rectifiers used can "pop" releasing toxic vapor, which is why, I am looking to replace mine with modern diodes. https://en.wikipedia.org/wiki/Selenium_rectifier See above for more info
-
Interesting but a few things wrong. the KT was no longer than the 855, a bit taller and a whole lot heavier. it was one of the reasons for the weird fan drive, to keep the same envelope as the 855. I used to work at a place that rebuilt them for construction equipment. The main thing was that it was an inline, easier to fit between the frame rails that the big V engines. My IHC 9670 were fitted with 1500 sq" rad and could go up to 1800, so yeah 2000 was big
- 1 reply
-
- 2
-
-
Paul, Early alternator systems (talking 40's and 50's) had the rectifiers mounted separate a they didn't have high power diodes at that time. Remember, this is a time when most semi trucks had 50 amp generators. Fire trucks, and tow trucks could be fitted (at great expense) with L/N's alternators, Not only did they provide much more current, but could do so at lower speeds. Important for E vehicles. I have a 6 volt 100 amp set-up that is similar to the one here but not exact. Because the rectifiers were external, they were not kept connected to the battery like a modern alternator. The big regulator had a main relay inside that closed when the ign was turned on, and also a voltage regulator. (current regulation is not needed on an alternator as the winding are self regulating). The rectifiers have nothing to do with shop power, they are for the engine alternator. For some special application remote rectifiers are still used. My unit has the same rectifier set up. If he just wants to "get it running" then the whole system can be replaced by a modern (one wire) alternator. Alternators DO NOT get polarized, and in most cases generators don't lose there polarity, so only need to be polarized when a new unit is placed in service or an old unit is used on a different ground vehicle. Some fire trucks used the 3 phase output via transformers to provide 120 volt power for lights and universal motors for saws and the like. I'll have to look at my regulator and see if it is enough similar to his to be sure of the connections. Fairly sure the problem will come down to voltage drop in one of the circuits, either the ground or power side, or the field not being fed from the regulator like it should be, but cross shorted to the output wires some how. Without either being there or good photo's I can't tell what the problem is. Part of what sent this down the wrong road was saying it was a generator, that lead to the whole polarizing issue which has nothing to do with this. On the 1st thread started, I mentioned it might be an alternator and asked for pictures, which were not provided at that time.
-
Yes, that is a rectifier. and so it does have an early alternator system. Not a generator (dynamo). Yes, as I stated before, it could have a bad connection between the generator and regulator. Body could have a bad ground between it and the chassie, or frame. Technically, anything that produces DC is a generator, while anything that produces A/C is an alternator. But in automotive terms the two get mixed up a bit.
-
OK, this is going to be hard to sort out. It isn't the typical truck charging system, it is firetruck special. Not having the schematic on hand this is what I can say B goes to the ammeter or battery F to field Gen to armature ign to switched ign feed You didn't mention the terminal at the top G may or may not be ground A regulator is only as good as its connection to what it is regulating. If it is not making good connections it can't regulate. I still want a pic of the generator and associated wiring, it may still be an alternator, as I have a L/N set-up that looks very similar. You really are going to need someone who knows this type of equipment. Most truck people have no clue. With the ign feed, I suspect this is an alternator set-up with remote rectifier (big finned thing with three heavy wires coming from the "generator" and one heavy wire to to regulator) The early remote rectifier systems are weird in that the regulator dis connects them from the battery when the ign is off. This is how mine is set-up, it is similar but not exactly the same. It is a 100 amp L/N 6 volt alternator from the 50's. More pictures are needed.
-
BTW this is the 2nd thread on the same problem in the same section. don't start multiple threads on the same problem it gets confusing.
-
that said, polarizing will have no effect on the voltage setting. SO either you have a wiring problem, a regulator problem or a grounding problem. A regulator can only act on the voltage it "sees" so if the ground path is poor, it will "see" less voltage. I may be wrong, but didn't most have Delco generators? Lets get a picture of what you are working on.
-
Battery to Armature. Not to field. If in doubt, connect a jumper cable to the battery hot and touch the other end to the heavier of the two terminals on the genny.
-
I've got two sets but three engines for two trucks. So I am in no rush either. Here is another that show the contents https://www.mechanicsurplus.com/products/5698909517 Quite a jump in price, however. Think on it, the seller will not be around for a week. If by next weekend you still don't want it, I will likely decide its cheap enough to have on hand. Gasket sets and main bearing are the hardest thing to find for these engines. Oddly oil pumps seam to come up often either complete or kits. When I find cheap spares, I often get them. Finding some when you have a need can be hard and expensive.
-
One of us should jump on this: Only a head set but still https://www.ebay.com/itm/313126024114 I'll give you 1st refusal, if you decide you don't want or need it, I might grab it.
-
I think they were primed with Gasola or other orangish sealing primer and then a blue green top coat. Black for accessories. The lower left side of the block seams to be about the factory color. I think there are people re-popping the Donaldson air-cleaner decals. I think Jeep and/or Powerwagon used them.
-
Depends on how worn! 😄
-
20 years ago you could still get gasket kits, but no more. I suspect custom gaskets are going to be your only choice. Be sure to get the one between manifolds, as 'm sure you know, they have to bolted to the head with that connection loose, only tightened after the "assembly" is firmly attached to the head. Be sure not to loose the two "locating" ring in the intake manifold. Notice the "fuel pump" opening on the right side under the generator mount? That is a hold over from when there was a gear driven generator/distributor or Mag on the earliest engines. Victor set FS3031 would be the set, but it is for the bigger 282-308 really, works for the 269 also but as I say, NLA. Might find one NOS though.
-
Supposedly the pro's of threaded pins is it increases the surface area and grease contained. I never liked them myself. Plain pin in a bronze bushing, replace when worn is my choice.
BigMackTrucks.com
BigMackTrucks.com is a support forum for antique, classic and modern Mack Trucks! The forum is owned and maintained by Watt's Truck Center, Inc. an independent, full service Mack dealer. The forums are not affiliated with Mack Trucks, Inc.
Our Vendors and Advertisers
Thank you for your support!