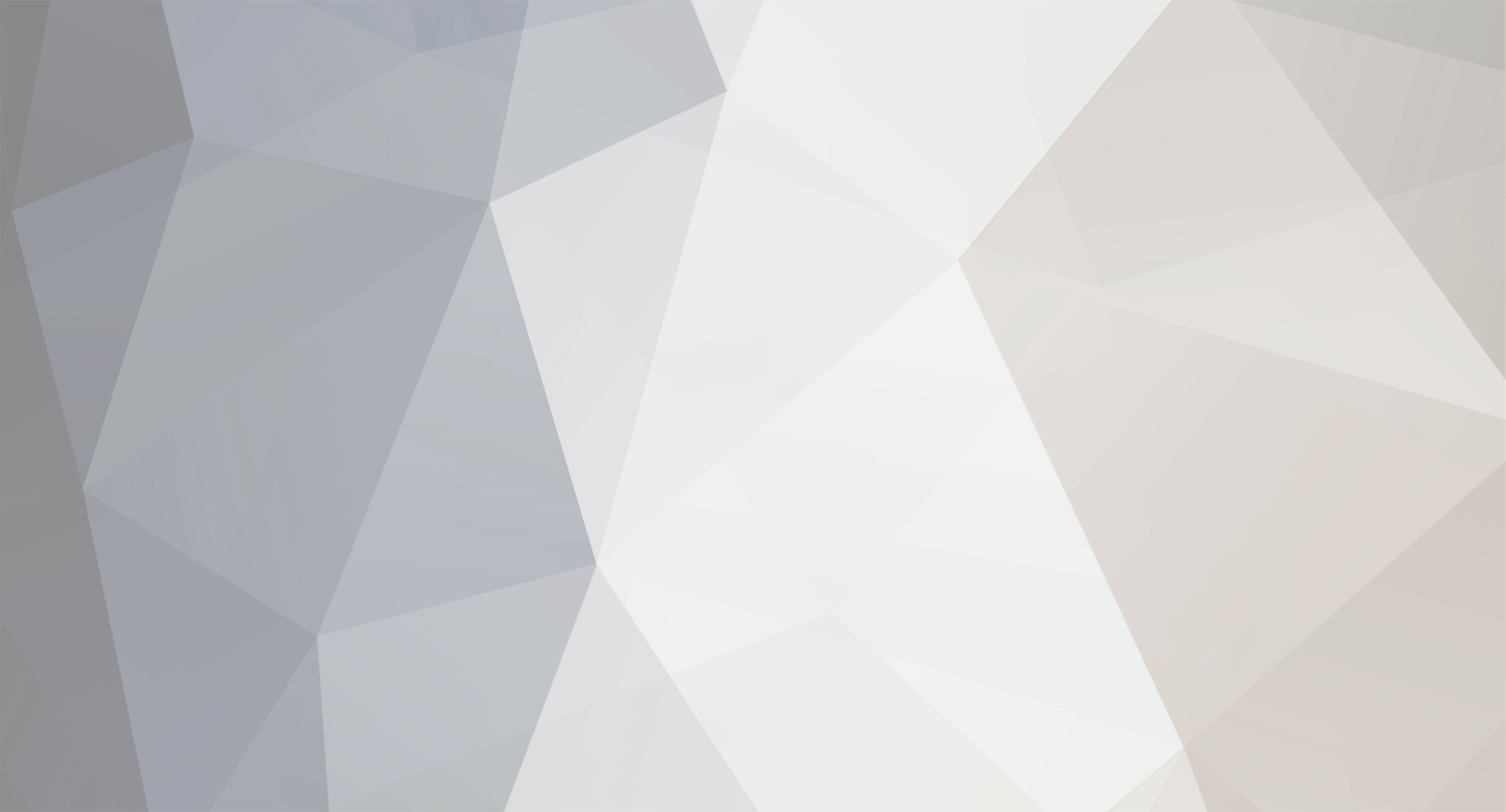
Nickdieselz
Puppy Poster-
Posts
11 -
Joined
-
Last visited
Content Type
Profiles
Forums
Gallery
Events
Blogs
BMT Wiki
Collections
Store
Everything posted by Nickdieselz
-
DieselLink or NexIQ adapter?
Nickdieselz replied to JoeH's topic in Electrical, Electronics and Lighting
Check out this laptop, it works great and does everything we need it to. I had other laptops before that all broke within months but we've had this one for around 2 years. https://dieselscanners.com/products/diesel-diagnostic-laptop-scanner-tuner-truck-repair -
I recommend this laptop, we use it all the time at my shop and it works great. No complaints and works on every truck that comes in, would recommend you look into it. https://dieselscanners.com/products/diesel-diagnostic-laptop-scanner-tuner-truck-repair
-
It sounds like your Mack CXN612 might be experiencing a fuel delivery issue, particularly on the high-pressure side of the fuel system, given the symptoms of surging before parking and the engine not staying running despite starting fluid helping it crank. Here are a few things to check: 1. Fuel Supply Pump: While you've got pressure leaving the filter, it's possible that the fuel supply pump is not maintaining enough pressure beyond that point. A weak or failing supply pump can allow enough fuel to reach the filter but not sustain enough pressure to the injectors. Check the fuel pressure after the pump to ensure it’s in spec for your ASET engine. 2. Air in the Fuel Lines: Since you replaced the filter, there could be air trapped in the fuel lines, which can cause a no-start or rough running condition. You may need to manually prime the system or check for leaks in the fuel lines, especially between the tank and the supply pump. Even a small leak can cause air to get into the system. 3. Fuel Return Line: A blockage or restriction in the return line could cause fuel pressure to drop, preventing the injectors from receiving adequate fuel. Ensure that the return line isn’t clogged or restricted. 4. Fuel Pressure Regulator: If the fuel pressure regulator is faulty, it may be preventing the system from maintaining the correct fuel pressure, which would result in the engine not getting enough fuel to stay running. 5. Injector or Injector Pump Issues: If the injectors or injector pump are failing, they might not be delivering fuel properly, even if there’s pressure up to that point. You can perform a cylinder cut-out test or have a professional test the injectors to ensure they’re functioning correctly. 6. Electrical/Fuel Pump Relay Issues: Check the electrical connections to the fuel pump and the relay. A faulty relay or bad wiring could cause intermittent power to the fuel system, explaining why it cranks but won’t stay running. Given the surging before the truck was parked, it seems likely that something in the fuel system is beginning to fail. Checking the fuel pressure at different points, from the tank to the injectors, should help narrow down whether it's a supply, air, or injector-related issue.
-
It sounds like the issue you're experiencing with the MDrive transmission and jake brake could be related to how the transmission control module (TCM) is programmed to handle engine braking at higher speeds. Since it briefly downshifts but then returns to the higher gear, it may be trying to balance engine RPMs and load under certain conditions, which can result in this behavior. Here are a few considerations: 1. Transmission Software Calibration: Some MDrive systems are set up to avoid excessive downshifting at higher speeds to prevent over-revving the engine. It might be a built-in safety feature, but since you've had this issue since new, it's possible that the programming could be fine-tuned by the dealer or a service center. Updating or reprogramming the TCM could solve this. 2. Load and Speed Conditions: The transmission may prioritize maintaining a higher gear at speeds like 70 km/h and above if it detects that downshifting would result in engine overspeed or excessive braking force. At lower speeds, it might allow more aggressive downshifting. 3. Jake Brake Settings: Some systems have different levels of engine braking (e.g., Stage 1, 2, or 3). At maximum, the system could be trying to provide more braking force through the engine but still limits downshifting under certain conditions. Double-check that you're in the correct mode for your intended braking. 4. Manual Intervention: Since you are manually downshifting to compensate, it may indicate that the automatic control logic isn’t calibrated to your driving style or conditions. Sometimes manual control is preferred in hilly or high-speed braking situations, but it shouldn’t be a constant necessity. I recommend having the dealer or service center check the transmission’s software and calibrations to see if there's an adjustment that can be made for better jake brake performance, especially if this has been a persistent issue since you got the truck. They can perform a diagnostic to see if the downshift logic can be adjusted to better match your driving conditions.
-
It sounds like you're dealing with a challenging diagnostic issue, especially given that the customer has already replaced multiple components. Based on the information you provided: 1. Unit Pump Codes: If you're seeing every unit pump code when it runs briefly on starting fluid, it's likely pointing to a fuel system issue. If even one of the unit pumps (individual cylinder fuel pumps) is shorted or malfunctioning, it could cause a no-start condition or erratic behavior across the entire fuel injection system. Since you're not seeing any exhaust smoke, it suggests fuel is not making it into the cylinders, further pointing to a possible fuel injection issue. 2. Single Unit Pump Shorting: Yes, a single shorted or faulty unit pump can disrupt the operation of the whole system. These pumps are often wired in series or share common circuits, and if one is shorting, it could cause the ECU to shut down the whole fuel injection system for protection, resulting in a no-start condition. 3. RPM Signal & Crank Mode: Since you’re getting an RPM signal in crank mode and have replaced the flywheel and cam sensors, it suggests that the basic engine management sensors are functioning properly. The issue seems more isolated to fuel delivery beyond the fuel supply pump, especially since you're not getting any injection happening (no exhaust smoke). Things to Consider: - Unit Pump Electrical Checks: You can check the wiring and resistance of each unit pump individually to see if one is shorted or out of spec. Compare readings to what’s expected for the system. - Fuel Injector Control Module (FICM): If the unit pumps seem fine, the issue could also be in the FICM or another component of the fuel control system. The FICM controls the fuel injectors and could be malfunctioning. - Injector Solenoids: Ensure the injector solenoids aren't stuck or faulty. A solenoid short or malfunction can also cause issues like this. - Fuel Rail Pressure Sensor/Regulator: Though you've tested the fuel pressure during cranking, it’s worth double-checking that the rail pressure sensor and regulator are functioning correctly to avoid inconsistent pressure. Since the truck runs briefly on starting fluid, it confirms spark and basic engine mechanics are working, so focusing on the fuel delivery and control system is key here. Checking wiring for shorts or grounding issues in the fuel system might lead you to the culprit.
-
Diagnostics tools, code scanners?
Nickdieselz replied to Sturgill's topic in Modern Mack Truck General Discussion
I recommend these laptops, we use them at my shop and they work amazing. No issues with them, they never caused us any issues and works on every truck that comes in. You should look into them, they have been god-sent for us. https://dieselscanners.com/products/diesel-diagnostic-laptop-scanner-tuner-truck-repair -
Mack TE 64 Diff Lock Alarm
Nickdieselz replied to jcutler's topic in Modern Mack Truck General Discussion
It sounds like your TE 64 Cab Over is experiencing an electrical issue with the differential lock alarm, particularly related to the instrument cluster or its wiring. Since unplugging and replugging the 4-wire harness temporarily stops the alarm, it suggests a connection or signal issue. Here’s where to start troubleshooting: 1. Check the Cluster Harness and Connections: Inspect the 4-wire harness going to the cluster gauge. Look for any loose, corroded, or damaged wires or connectors. Cleaning the connectors and ensuring a secure connection might solve the problem if it’s just a loose contact. 2. Inspect the Instrument Cluster Itself: The issue could be within the cluster gauge itself, as it’s possible there’s an internal fault that triggers the alarm falsely. Consider testing or replacing the cluster gauge. 3. Check for Electrical Shorts or Grounding Issues: Look for any potential shorts or grounding issues in the wiring between the diff lock system and the cluster. An intermittent ground fault could cause the alarm to trigger. 4. Pneumatic System Verification: Since the diff lock is pneumatically disconnected, ensure the pneumatic system isn’t sending any false signals or leftover pressure. Double-check any pneumatic sensors related to the diff lock to make sure they are not faulty. 5. Diagnostic Scan: If possible, hook up a diagnostic tool to check for any fault codes or signals related to the diff lock system. The alarm might be linked to an electronic control module (ECM) detecting a fault. If you need a diagnostic tool recommendation, I would highly suggest you look in this laptop https://dieselscanners.com/products/diesel-diagnostic-laptop-scanner-tuner-truck-repair By focusing on the wiring, connections, and the cluster gauge, you should be able to identify the root cause of this alarm issue. If the problem persists, it might be necessary to test the entire diff lock circuitry. -
It sounds like you're dealing with a combination of shifting and acceleration issues on your 2014 Mack Pinnacle MP8 with the mDRIVE transmission. The behavior you're describing—jerking in low gears and RPM locking in 12th gear—suggests there may be a problem with the transmission control system or related sensors. Here are a few areas to check: 1. Transmission Control Module (TCM): The TCM could be malfunctioning, causing improper gear changes or locking the RPM. Try performing a reset or updating the TCM software if available. 2. Clutch Calibration: mDRIVE transmissions rely heavily on clutch calibration. If the clutch calibration is off, it could cause jerking or inconsistent shifting. 3. RPM/Speed Sensors: A faulty sensor could provide incorrect data to the transmission, leading to improper gear shifting or locking in a specific gear. Check the speed and RPM sensors for proper function. 4. Wiring and Connectors: Since this issue happens intermittently, there could be a loose or damaged wire, especially around the TCM or transmission. Inspect all connections and wiring harnesses for wear or poor connections. 5. Hydraulic System (if applicable): If the transmission relies on hydraulic actuation, ensure that there is proper hydraulic pressure and that no leaks are present. 6. Fault Codes: Even if the dashboard isn’t showing active fault codes, plug in a diagnostic tool to check for any stored or pending codes that could give more insight into the issue. If the problem persists or worsens, you might want to consider taking it to a specialized shop that deals with Mack transmissions for a thorough diagnostic.
-
Alternator voltage 16.5
Nickdieselz replied to David Wakeman's topic in Modern Mack Truck General Discussion
It sounds like your 2016 Mack Pinnacle is experiencing a serious electrical issue, likely related to voltage regulation or grounding problems. The symptoms you're describing—high voltage (16.5+ volts), electronic malfunctions (radio blanking out, hill assist malfunctioning, transmission shifting erratically), and overheated wires behind the master switch—are classic signs of an overcharging problem or a significant electrical fault. Here are some possibilities to investigate: 1. Alternator Overcharging (Regulator Issue) - Overvoltage: If your alternator is putting out 16.5+ volts, it’s overcharging the system. The normal charging voltage should be around 13.8 to 14.6 volts. Anything higher than that risks damaging sensitive electronic systems. - Voltage Regulator: Many trucks have an external voltage regulator, but some alternators have built-in regulators. If the regulator is faulty, it could be allowing the alternator to output excessive voltage. - Test the Alternator: Have the alternator and voltage regulator tested to ensure they are functioning correctly and not overcharging the battery or electrical system. 2. Battery Condition - Battery Health: If your battery is damaged or its internal resistance is too high, it can affect the overall electrical system and cause erratic voltage fluctuations. - Check Battery Terminals: Ensure the battery terminals are clean and tightly connected. Corrosion or loose connections can also cause voltage irregularities. 3. Grounding Issues - Bad Grounds: If the truck’s grounding system has corrosion or loose connections, it could cause intermittent power surges, voltage spikes, or erratic electrical behavior. A bad ground can make it seem like there’s an overcharging issue because power is not properly distributed or dissipated. - Check Ground Straps: Inspect all ground connections, especially the ones between the engine, frame, and body, for corrosion or damage. Tighten any loose connections and clean any corrosion. 4. Master Switch Wiring (Short or High Resistance) - Overheating Wires: The fact that the wires behind the master switch are getting too hot to touch suggests a short circuit or high resistance in that wiring. This could be drawing too much current and causing the electrical system to malfunction. - Check for Shorts: Inspect the wiring for signs of damage, fraying, or exposed wires that could be shorting out. Heat can also come from loose connections, so check the connections at the master switch for tightness. 5. ECM/GuardDog Electrical Interference - Electronic Malfunctions: Overcharging can cause electronic control modules (ECMs) to behave erratically. The GuardDog system and hill-hold assist may be malfunctioning because they aren’t receiving stable voltage. - Scan for Codes: Even though this might seem like a voltage issue, scanning for diagnostic trouble codes (DTCs) may give you clues about specific systems affected by the voltage spikes. 6. Transmission and Shifting Problems - Electronic Shift Control: The transmission relies heavily on stable voltage and clean electrical signals. If the voltage is too high or erratic, the transmission may not shift properly or could get stuck in a specific gear. - Inspect Transmission Wiring: Check for any damaged wiring related to the transmission control module (TCM), as voltage spikes can interfere with the shifting logic. What You Can Do Next: 1. Test the Alternator: Use a voltmeter to check the alternator's output at the battery terminals while the engine is running. If the voltage consistently exceeds 14.6V, the alternator or voltage regulator is likely the issue. 2. Inspect Battery and Grounds: Check battery voltage with the engine off (should be around 12.6V) and with the engine running (should be around 14.0-14.6V). Also, verify that all ground straps and connections are clean and secure. 3. Check and Replace Master Switch Wiring: If the wires are overheating, you may have a short or high resistance. Carefully inspect the wires for any signs of damage and repair or replace them as necessary. Fixing this issue soon is important to avoid further damage to your truck's electrical components. If you're unsure about testing the alternator or electrical systems yourself, it might be worth taking the truck to a professional mechanic or electrician specializing in heavy trucks. Let me know how it goes or if you need further clarification on any of these points! -
Suspension clunk when braking
Nickdieselz replied to annmax's topic in Modern Mack Truck General Discussion
The loud clunk you're hearing from the front suspension of your 2021 Mack Granite when pressing the brake pedal could be due to several possible causes. Here's a list of things to check that might help pinpoint the issue: 1. Loose or Worn Suspension Components: - Control Arms: If the bushings in the control arms are worn out or if the bolts are loose, they could be shifting under the braking force, causing the clunking sound. - Ball Joints: Worn ball joints can also cause clunking, especially under load when braking. Check for any play or wear. - Sway Bar Links or Bushings: These components help stabilize the suspension and can make a clunking noise if they're worn out or loose. 2. Brake Components: - Caliper Bolts: Ensure that the brake calipers are tightly secured. Loose caliper bolts can cause movement when the brakes are applied, resulting in a clunk. - Brake Pads: If the brake pads are loose in their mounting brackets, they can shift when braking, causing noise. Check for excessive movement or wear in the pad hardware. - Steering Knuckle or Hub Assembly: If there's wear or looseness in the knuckle or hub assembly, it can cause a clunk during braking. 3. Steering Components: - Tie Rod Ends: Worn or loose tie rod ends can result in a clunking sound, especially when the vehicle's weight shifts during braking. - Steering Gearbox: Ensure the steering gearbox and linkage are securely mounted, as movement in these areas can create noise during braking. 4. Shock Absorbers or Struts: - Worn or damaged shocks/struts can clunk when they compress or extend under the force of braking. Check for oil leaks or signs of damage, and ensure that all mounting bolts are tight. 5. Frame or Body Mounts: - Loose or worn body mounts or frame bolts can cause noise as the body shifts relative to the frame under braking forces. 6. Suspension Bump Stops: - If the suspension bump stops (which prevent excessive suspension travel) are damaged or missing, the suspension may bottom out under hard braking, causing a clunk. 7. Axle or Driveshaft: - Check the front axle or driveshaft for any movement or wear, especially around the U-joints or CV joints, which could contribute to a clunking noise during braking. Diagnostic Tips: - Check for Play: With the vehicle on a lift, have someone apply the brakes while you check for play or movement in the suspension or steering components. - Inspect Under Load: Sometimes, a noise like this only appears under load, so a thorough inspection with the vehicle's weight on the suspension (on ramps or a drive-on lift) may be necessary. By systematically going through these components, you should be able to narrow down the source of the clunk. Let me know if you discover anything specific, and I can provide more guidance from there! -
Blower motor not working on level 4
Nickdieselz replied to Cpitt32's topic in Modern Mack Truck General Discussion
It sounds like you're on the right track by replacing the blower motor resistor, but since it didn’t resolve the issue, here are a few other components to check: 1. Blower Motor: The motor itself could be failing. Even though it may work on other speeds, the highest speed (level 4) often bypasses the resistor and runs directly through the motor. If the motor is faulty, it might struggle to handle the higher current load needed at level 4. 2. Blower Motor Relay: On some vehicles, the highest fan speed uses a separate relay to bypass the resistor. If this relay is faulty, it could prevent the fan from running on the highest setting. Check your fuse box or wiring diagram for the location of the relay. 3. Wiring and Connections: Inspect the wiring and connectors to the blower motor and resistor. A loose or corroded connection might only affect the fan at higher speeds due to the increased current. 4. Blower Control Switch: The HVAC control switch that changes fan speeds could also be the culprit. If the switch isn't working correctly, it may not be sending power to the blower motor on the highest setting. Here's a quick way to diagnose: - Test the blower motor directly by supplying 12V to the motor to see if it runs at full speed. If it works, the problem could lie in the relay, switch, or wiring. - Use a multimeter to check for voltage at the blower motor on the highest speed. If no voltage is present, trace it back to the relay and switch. Let me know how the testing goes, and I can help with further steps!
BigMackTrucks.com
BigMackTrucks.com is a support forum for antique, classic and modern Mack Trucks! The forum is owned and maintained by Watt's Truck Center, Inc. an independent, full service Mack dealer. The forums are not affiliated with Mack Trucks, Inc.
Our Vendors and Advertisers
Thank you for your support!